Dimensional differences in molds resemble tiny gremlins. These gremlins disrupt manufacturing quality. Every detail matters. Product fit may suffer. Longevity might reduce. Really important facts.
Dimensional deviation changes mold quality by affecting the precision of mold spaces and centers. These changes result in size mismatches, causing problems when assembling parts. Product lifespan and consistency suffer due to these issues. Manufacturers face huge challenges because they prioritize accuracy. Accuracy is very important to them.
When I began designing molds, I didn’t realize how big a problem small errors could be. Imagine you have carefully designed a mold for a smooth electronic part, but the pieces do not fit because of a tiny mistake. It’s really annoying!
Size differences mess up the accuracy of the mold’s cavity and core, which is a huge problem for precise items like small electronic pieces. Even a tiny error of ±0.01mm can make parts useless. With molds that have multiple cavities, incorrect positioning is like trying to fit puzzle pieces that don’t belong together.
Initial fitting is not the only concern. Errors also complicate assembly. I remember spending long hours adjusting parts to fit properly, only to create more mistakes. This raises expenses and can wear out molds faster, shortening their lifespan.
Even worse, these problems affect the final products. Think about making car parts where exact size is very important. Any slight change can impact assembly and performance – like driving a car with misaligned wheels.
Understanding these effects is vital for anyone who seeks to keep mold quality high. It’s about learning the skill of precision – something I have learned over time and now value a lot in my work.
Dimensional deviation increases mold production costs.True
Correcting deviations requires additional resources, increasing overall costs.
Dimensional deviation has no effect on product assembly.False
Deviations can lead to misalignment, affecting assembly accuracy.
- 1. What Are the Key Factors Influencing Dimensional Deviation in Molds?
- 2. How Does Dimensional Accuracy Impact Mold Assembly and Performance?
- 3. How Does Dimensional Deviation Impact Mold Service Life?
- 4. How Can Dimensional Deviation Affect Molded Product Quality?
- 5. How Can I Minimize Dimensional Deviation in My Manufacturing Process?
- 6. Conclusion
What Are the Key Factors Influencing Dimensional Deviation in Molds?
Have you ever thought about why some molded products just don’t fit well? Small, almost invisible differences in the molds cause this problem. These molds sometimes have very tiny flaws. Maybe they seem small, but they really matter. Tiny deviations affect the whole product. Little errors lead to a big issue.
Material properties, equipment performance, design details and environmental conditions influence dimensional deviation in molds. Addressing these factors probably improves mold precision. This action simplifies assembly issues. Mold longevity might also increase, really extend its use over time.
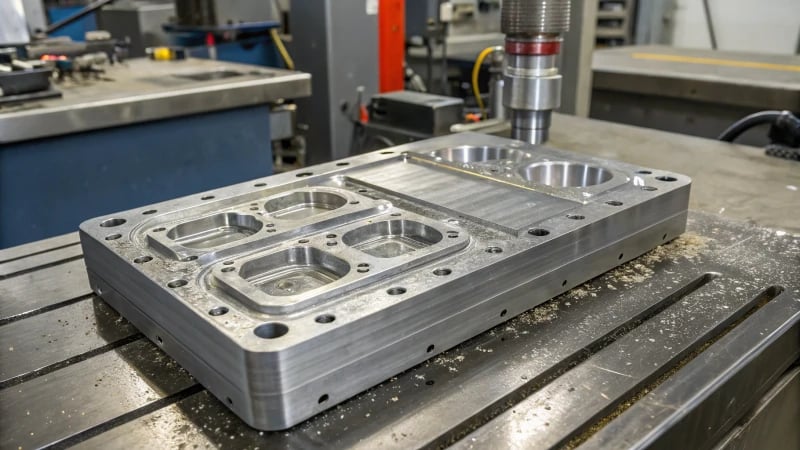
Material Properties
Material choice really matters in mold work. Variations in thermal expansion, elasticity, and shrinkage rates can lead to dimensional deviations. Once, I worked with a polymer that looked great on paper but grew unexpectedly with heat, messing up the size we planned for.
Property | Impact on Deviation |
---|---|
Thermal Expansion | Can cause size changes with temperature |
Elasticity | Affects the mold’s ability to return to its original shape |
Shrinkage Rate | Leads to size reduction post-cooling |
Equipment Performance
Machine precision is vital here. Misalignments or wear in machines can lead to inaccuracies in mold dimensions. I learned this tough lesson when a CNC machine we used needed regular checks but didn’t get them. This led to poorly aligned parts.
- CNC Machines: Require great precision to stay accurate.
- Injection Molding Equipment: Needs constant pressure and temperature.
Regular calibration and maintenance are essential to minimize such dimensional deviations1.
Design Complexities
Complex designs excite and challenge me. More details increase the risk of mistakes. Especially with multi-cavity molds, keeping them all the same is tough. A multi-cavity mold project showed me that minor placement errors can create big issues.
- Intricate Details: Might cause errors if not managed carefully.
- Multi-Cavity Molds: Need careful setup for cavity consistency.
Mold makers need to account for potential position accuracy problems2.
Environmental Conditions
I’ve also witnessed how conditions like humidity and temperature changes affect materials and machines. High humidity made materials swell, changing our planned sizes unexpectedly.
- Humidity: Swelling or shrinking may happen.
- Temperature: Control is needed to avoid thermal changes.
Ambient conditions such as humidity and temperature can exacerbate dimensional errors3.
Learning about these factors has helped me achieve accurate and well-performing molds. Using strict quality checks addresses these issues, making molds better and last longer.
High thermal expansion leads to mold shape issues.True
Materials with high thermal expansion rates can distort mold shapes when heated.
Humidity has no effect on mold dimensional accuracy.False
Humidity can cause material swelling, affecting mold dimensions.
How Does Dimensional Accuracy Impact Mold Assembly and Performance?
I remember my first big task in putting together molds. Getting the sizes just right was a challenge.
Dimensional accuracy is very important so mold parts fit exactly. This prevents problems like faster wear and poor product quality. Even small mistakes cause assembly challenges. Minor deviations cause performance issues too. Molded parts depend on accuracy. Reliability depends on it.
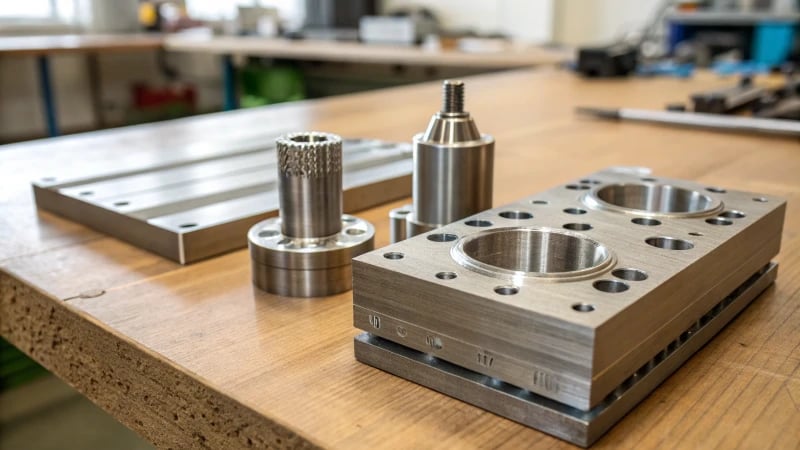
Importance of Dimensional Accuracy
I remember feeling overwhelmed when I started in mold design. Back then, every detail had to align correctly. Dimensional accuracy is not just a technical task; it’s the core of building a reliable mold. Tiny errors matter. Even a small mistake, like ±0.01mm, might mean failure in precision injection molds.
Dimensional accuracy is pivotal in mold assembly, impacting both the cavity and core dimensional accuracy4. Deviations can lead to oversized or undersized parts, compromising the product’s ability to fit within specified tolerance ranges.
For instance, in precision injection molds, deviations exceeding ±0.01mm can render electronic components non-functional. Similarly, deviations affect the shape and position accuracy of molds, especially those with complex curved surfaces.
Effects on Mold Assembly
-
Parts Matching Problems: I once found that guide pins did not line up due to dimensional error. Tight fits damage parts while loose fits lower accuracy.
- Tight fit: Increases mold wear
- Loose fit: Reduces guiding accuracy
-
Harder Assembly: Errors forced extra fixes like grinding, which made things cost more and brought new mistakes.
Issue | Impact |
---|---|
Tight fit | Increases mold wear |
Loose fit | Reduces guiding accuracy |
Influence on Mold Performance
Dimensional errors work quietly like hidden troublemakers. Wear and tear increase without warning. Stress from these errors leads to early mold breakdowns.
Dimensional deviations influence mold performance by increasing wear and reducing fatigue strength. Uneven stress distribution from deviations can result in premature failure of molds due to fatigue cracks.
For moving parts such as the ejection mechanism, abnormal friction accelerates wear, necessitating frequent maintenance.
Impact on Product Quality
Keeping dimensions steady is crucial for quality in large-scale production. I’ve watched car part sizes change due to dimensional issues affecting both assembly and performance.
Dimensional stability is key to maintaining consistent quality in mass production. For instance, deviations in automotive parts can affect assembly quality and performance.
Errors show up as ugly flash or shrinkage, hurting a product’s look:
- Appearance Quality: Flash or shrinkage issues
- Dimensional Stability: Fluctuating product dimensions
Dimensional deviation5 at the parting surface might cause flash during injection affecting aesthetics. For functional products, mismatched parts reduce performance efficiency and accuracy.
Learning these lessons taught me to focus on details in mold design—accurate dimensions bring better product trust and improve function. Precision is key.
Dimensional deviations cause mold assembly difficulties.True
Deviations require extra work, like grinding, increasing assembly time and errors.
Dimensional accuracy does not affect mold performance.False
Inaccuracies increase wear and reduce fatigue strength, impacting performance.
How Does Dimensional Deviation Impact Mold Service Life?
Have you ever thought about why some molds do not last very long? The reason could be those tricky dimensional changes!
Dimensional deviation affects the life of molds. It leads to more wear and reduces fatigue strength. Misalignments cause extra friction. More friction means more wear. Uneven stress lowers fatigue strength. This speeds up mold breakdown.

Increased Wear
Dimensional deviations often lead to poor fits between mold parts, such as sliders and guide rails. A loose fit causes parts to shake during operation, leading to accelerated wear and tear. I remember the first time a mold wore out too quickly; parts didn’t fit tightly—they shook during operation. This shaking led to faster wear.
For instance, the contact surface6 between a slider and a guide rail may wear faster if the dimensional accuracy is compromised.
Part | Effect of Deviation |
---|---|
Slider | Increased shaking, wear |
Guide Rail | Faster wear |
For mold parts with relative motion, like the ejection mechanism, any dimensional deviation might result in abnormal friction. Frequent adjustments were necessary due to this abnormal friction. This friction not only speeds up wear but also increases maintenance frequency, impacting overall mold longevity.
Reduced Fatigue Strength
Dimensional changes mess with how stress spreads across mold parts. Uneven wall thickness leads to greater stress on thinner sections during injection pressure application. Consequently, these areas may develop fatigue cracks over time.
A table showcasing stress distribution:
Wall Section | Stress Level |
---|---|
Thicker | Lower |
Thinner | Higher |
Stress imbalance weakens fatigue strength. This leads to early failures after fewer injection cycles than expected. I discovered this when a mold developed fatigue cracks after just a few cycles due to uneven wall thickness putting extra stress on thinner sections.
This underscores the importance of maintaining dimensional accuracy7 during manufacturing to ensure optimal stress distribution and prolonged mold life.
Impact on Injection Molded Products
Mold precision affects product stability. The dimensional stability of injection-molded products is directly linked to mold precision. Once, deviations caused dimension changes in automotive parts, which messed with assembly quality.
Moreover, dimensional deviation might cause appearance quality issues such as flash or shrinkage on injection-molded products. For example, deviations led to appearance issues like flash on some products occurred at the mold parting surface8, affecting aesthetic appeal.
By understanding and addressing these dimensional deviations, manufacturers can extend mold service life and ensure consistent quality of their products through careful design considerations and adherence to precision standards in mold manufacturing processes.
Dimensional deviations increase mold wear and tear.True
Loose fits cause shaking, accelerating wear and tear on mold parts.
Even stress distribution reduces mold fatigue strength.False
Uneven stress distribution, not even, reduces fatigue strength.
How Can Dimensional Deviation Affect Molded Product Quality?
Ever thought about how small mistakes in measuring might change a product’s whole life?
Dimensional deviation affects the quality of molded products. This happens through errors, difficulties in assembly and extra wear, leading to reduced performance. Accuracy during mold production is necessary for the best outcomes.
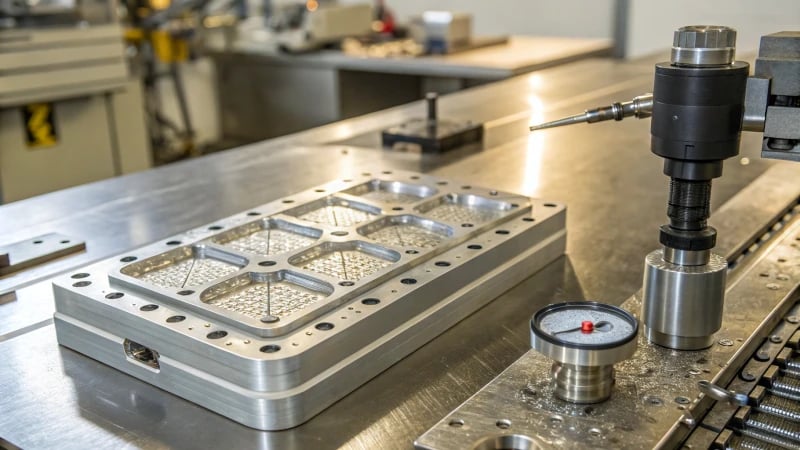
Impact on Mold Accuracy
I recall a moment when we worked on a project needing extreme precision. Even a small size error could lead to failure. Picture making a mold with a cavity slightly too big; the matching part might not fit, potentially ruining the whole setup. I quickly learned that even tiny shifts like ±0.01mm could be vital, especially with detailed electronics. It’s like assembling a jigsaw puzzle where each piece must perfectly align or none will fit.
Dimensional deviations can lead to reduced cavity and core9 accuracy. If a cavity is oversized, corresponding parts may exceed design tolerances, affecting assembly.
Aspect | Effect |
---|---|
Cavity Size | Larger parts may exceed tolerance |
Position Accuracy | Inconsistent dimensions in mass production |
Impact on Mold Assembly
Challenges continue during assembly. Dimensional precision is key here, too. I once faced a faulty guide pin. It was either too tight or too loose, causing chaos in mold operations. It felt like trying to zip a jacket with mismatched teeth – very frustrating and not effective.
Poor dimensional accuracy can cause mismatches between mold parts. Deviations between guide pins and sleeves may lead to tight or loose fits, affecting mold operation.
Impact on Mold Service Life
Also, consider the mold’s lifespan. I’ve seen how misaligned parts face extra friction, cutting the mold’s life short. Think of running a car with misaligned tires – it might move, but not for long.
Dimensional deviations increase mold wear and reduce fatigue strength. Misaligned parts experience abnormal friction, shortening mold life.
Impact on Injection Molded Products Quality
Problems appear in final products as well. I remember size errors causing unequal parts in a batch of car parts. It’s like baking cookies without weighing the dough – some come out well, others not so much.
Size errors at the parting surface10 can lead to poor mold closure, causing flashes that ruin both look and function.
For precision parts like transmission components, this is really unacceptable.
In summary, controlling size errors in every step of mold creation is not merely a task; it’s an art that keeps the final product’s quality and strength.
Dimensional deviations can cause mold parts to misalign.True
Misalignment due to deviations affects mold operation and assembly quality.
Dimensional deviations do not affect mold service life.False
Deviations increase wear and stress, reducing the mold's lifespan.
How Can I Minimize Dimensional Deviation in My Manufacturing Process?
Have you ever felt upset when a project does not fit perfectly? I have as well. Let’s explore some ways to handle those irritating size differences.
I rely on precise measurement tools to reduce size errors. Regular maintenance of equipment keeps everything in good shape. Advanced CAD software helps design accurately. Quality control processes check and confirm the work. These methods result in better accuracy in manufacturing. They truly do.
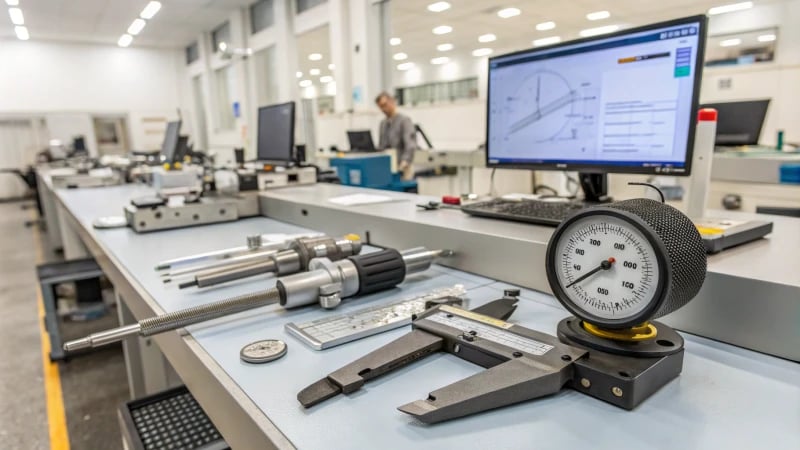
Use Accurate Measurement Equipment
I discovered that high-precision tools, such as coordinate measuring machines (CMMs), really change outcomes. These instruments give precise measurements for complex shapes, helping reduce dimensional deviations11. Regular calibration is crucial for consistent results. I remember a project where a small measurement error caused a chain reaction of mistakes. That was the moment precision’s importance hit me hard. It’s a big deal.
Maintain Equipment Regularly
Machines need to stay in great condition, saving me from endless problems. Routine checks reveal wear and tear, keeping parts within safe limits. This drastically lowers errors from mechanical breakdowns. Once, a tiny maintenance slip nearly messed up a whole production. Lesson learned.
Use Advanced CAD Software
Modern CAD software12 is like my safety net. It allows detailed design plans and minimizes chances for mistakes. Features like simulation and virtual prototyping help catch issues early. I have witnessed how this foresight prevents expensive errors in final products. Avoiding such costs is crucial.
Strong Quality Control Methods
Strict quality control is essential to find errors early. Statistical Process Control (SPC) is especially effective for tracking production changes, ensuring parts meet specifications consistently. Once, implementing SPC helped catch a defect that could have caused huge product recalls. It’s that important.
Implement Real-Time Monitoring Systems
Real-time monitoring gives immediate feedback on production conditions, allowing quick adjustments. This lowers the chance of unnoticed dimensional deviations over time. It’s like having extra eyes on every production step—vital.
Train and Develop the Workforce
Skilled workers are critical for reducing errors. Regular training keeps operators updated on the latest techniques and technologies in precision manufacturing. A well-trained team improves the entire process’s flow—it really does.
Strategy | Key Benefit |
---|---|
Accurate Measurement Equipment | Precise geometry measurements |
Regular Equipment Maintenance | Reduced mechanical failure-related deviations |
Advanced CAD Software | Enhanced design precision |
Strong Quality Control Methods | Early deviation detection |
Real-Time Monitoring Systems | Immediate production adjustments |
Workforce Training | Enhanced operator skill set |
Each strategy benefits reducing dimensional deviation in manufacturing processes significantly by improving overall production quality.
CMMs are essential for reducing dimensional deviations.True
Coordinate Measuring Machines provide precise measurements, crucial for minimizing deviations.
Advanced CAD software increases room for design error.False
CAD software reduces errors by allowing detailed design and virtual prototyping.
Conclusion
Dimensional deviation in mold manufacturing significantly impacts mold quality, affecting accuracy, assembly, service life, and product performance, ultimately leading to increased costs and reduced reliability.
-
Discover why regular equipment calibration is vital for maintaining dimensional precision in molds. ↩
-
Explore common position accuracy problems in multi-cavity molds and solutions to address them. ↩
-
Understand how environmental factors like humidity and temperature impact mold accuracy. ↩
-
Explore this link for a detailed understanding of how dimensional accuracy affects mold cavity outcomes. ↩
-
Learn more about how dimensional deviations affect injection molding processes and product quality. ↩
-
Explore how poor fit between mold parts accelerates wear and shortens mold lifespan. ↩
-
Understand why maintaining dimensional accuracy is crucial for mold durability. ↩
-
Learn how misalignment at parting surfaces affects product quality. ↩
-
Discover detailed insights into how precise cavity and core dimensions affect mold accuracy. ↩
-
Learn how deviations at the parting surface can lead to product quality issues like flash. ↩
-
Discover how CMMs help achieve precise measurements and reduce manufacturing errors. ↩
-
Learn how advanced CAD features optimize design accuracy and production efficiency. ↩