OPTIMIZATION
blog & article
read our latest newsletter
Whether you’re curious about material selection, product design, mold design, mold making and injection molding, feel free to ask us anything. Our team is ready to provide the guidance and insights you need.
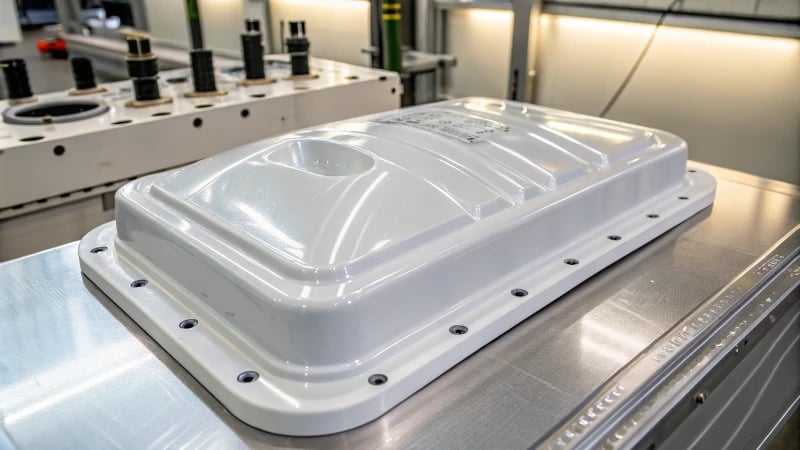
What Are the Best Techniques to Minimize Parting Line Traces in Injection Molded Products?
Parting lines can mar the appearance of injection molded products. To minimize these traces, focus on optimizing mold design by carefully positioning gates and avoiding rounded corners. Adjusting injection molding parameters like temperature and pressure is crucial for better material ...
OPTIMIZATION
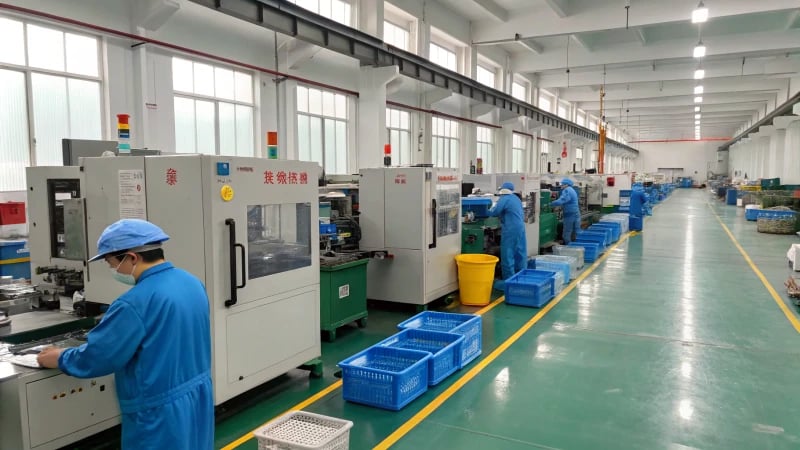
How Can You Enhance Production Efficiency in Injection Molding Machines?
This article explores strategies to enhance production efficiency in injection molding machines. Key techniques include optimizing process parameters like injection speed and cooling time, utilizing quick mold change systems, adopting hot runner technology, upgrading to high-performance all-electric machines, and implementing ...
OPTIMIZATION
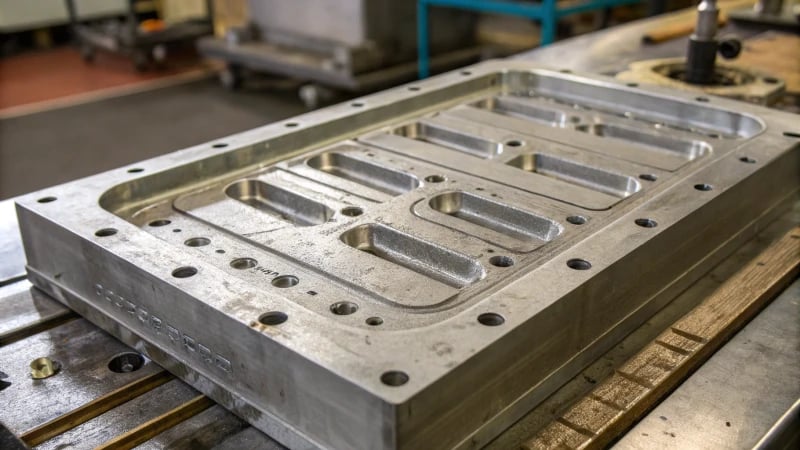
What Are the Best Ways to Enhance the Toughness of High Hardness Die Steel?
This article explores effective methods to enhance the toughness of high hardness die steel. Key strategies include alloying with elements such as nickel, molybdenum, and vanadium to refine grain structure and improve strength. Heat treatment processes like tempering and deep ...
OPTIMIZATION
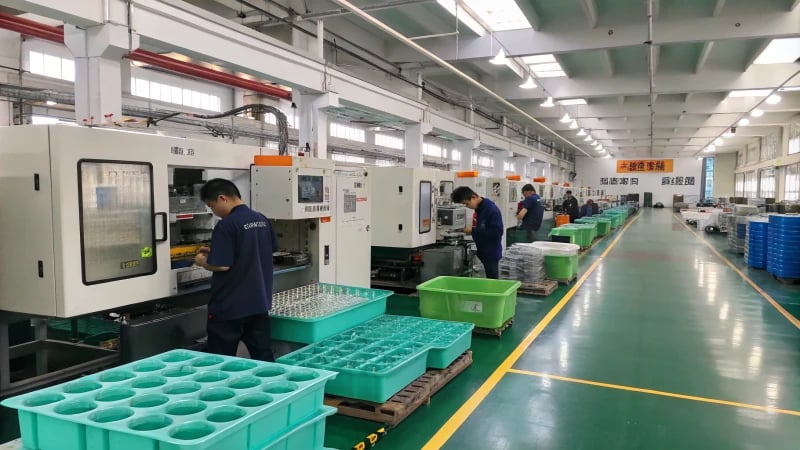
What Are Effective Ways to Reduce the Cost of Injection Molding Machine Products?
This article explores effective ways to reduce the cost of injection molding machine products. Key strategies include selecting cost-effective raw materials, optimizing mold designs, enhancing production processes, and managing energy consumption efficiently. By making small adjustments in material choices and ...
OPTIMIZATION
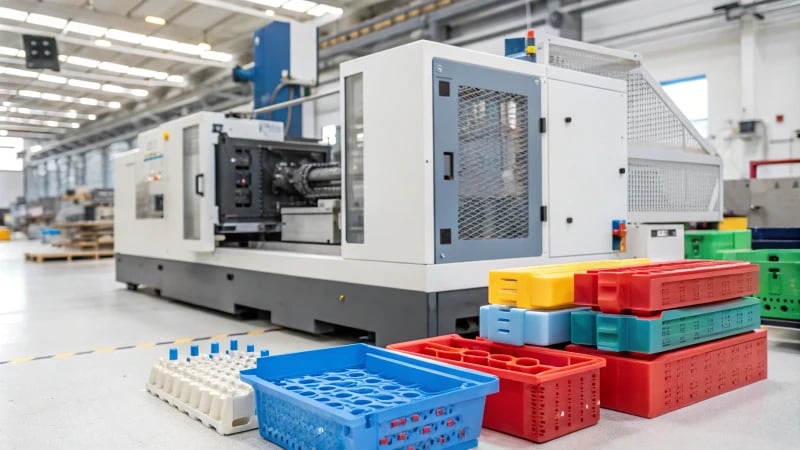
How Can You Solve Warpage Defects in Injection Molded Parts?
Warpage in injection molded parts can significantly impact product quality. This article outlines key strategies for addressing this issue, including optimizing cooling systems to ensure uniform temperature distribution, adjusting gate designs for even melt flow, and carefully selecting materials with ...
OPTIMIZATION
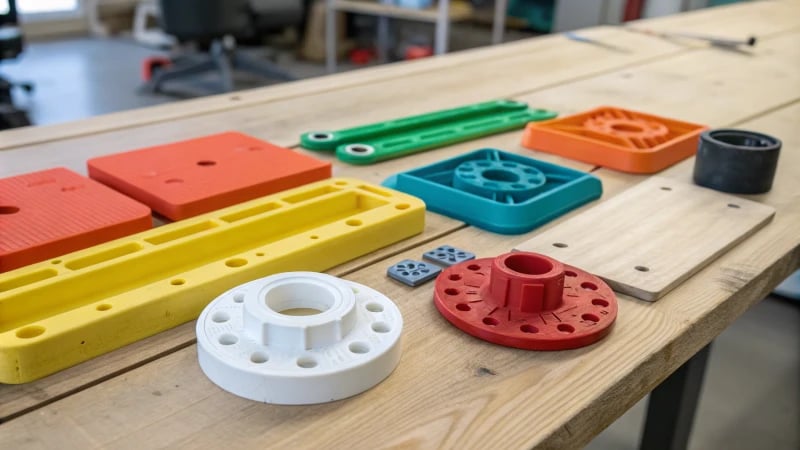
What Are Effective Methods to Solve Sink Mark Defects in Injection Molding?
Sink marks can significantly affect the appearance and strength of injection-molded parts. This article outlines effective methods to address these defects by optimizing product design through uniform wall thickness and rib placement, adjusting injection molding parameters like holding pressure and ...
OPTIMIZATION
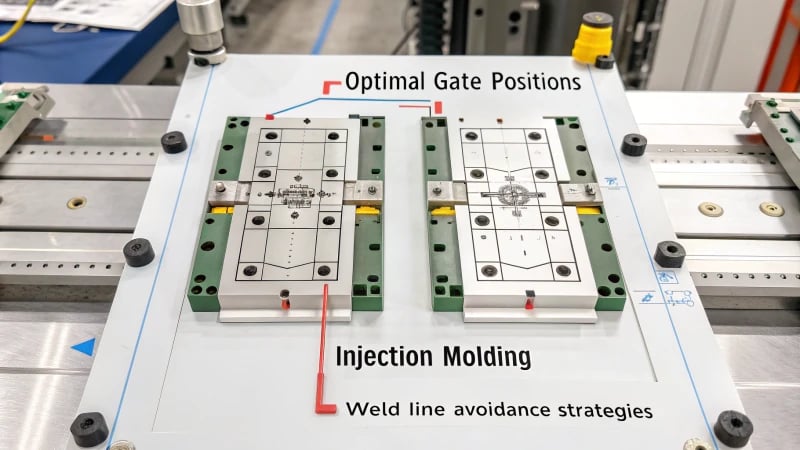
How Can You Prevent Weld Lines by Optimizing Gate Position in Product Design?
Weld lines can significantly affect the appearance and strength of molded products. This article explores how optimizing gate positions during injection molding can prevent these defects. Key strategies include placing gates symmetrically to ensure even melt flow, using sequential gating ...
OPTIMIZATION
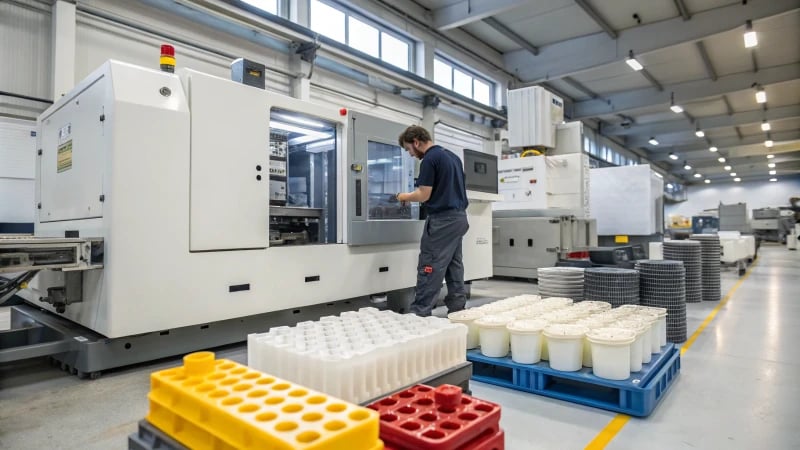
How Can You Adjust Injection Pressure for Optimal Plastic Product Performance?
This article explores the importance of adjusting injection pressure in plastic molding to achieve optimal product performance. It highlights how different factors such as mechanical requirements, dimensional accuracy, and appearance quality influence the necessary pressure settings. For high-strength products like ...
OPTIMIZATION
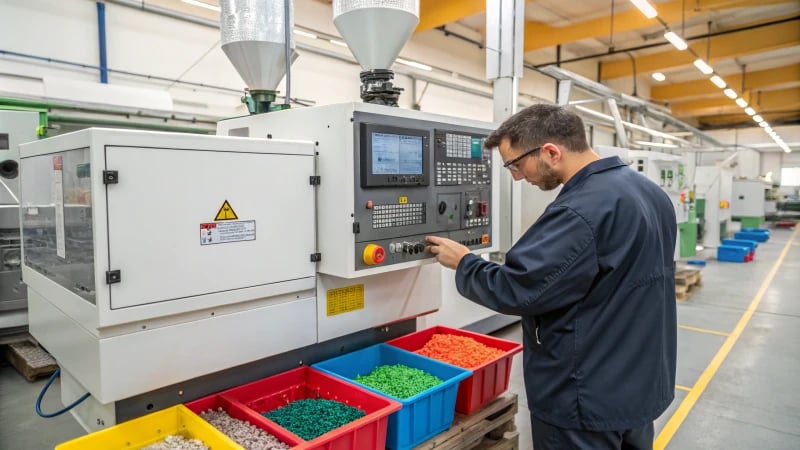
What is the Best Way to Determine Optimal Injection Pressure for Plastic Products?
This article explores the best practices for determining optimal injection pressure in plastic molding. It emphasizes the importance of understanding material properties such as viscosity and heat sensitivity, along with product structure considerations like wall thickness and complexity. Mold design ...
OPTIMIZATION

How Do You Choose the Best Reinforcement Materials for Plastic Products?
Selecting the right reinforcement materials for plastic products is crucial for enhancing their mechanical properties. Options like glass fiber, carbon fiber, and aramid fiber offer unique benefits depending on application needs. For automotive parts requiring high strength, glass fiber significantly ...
OPTIMIZATION
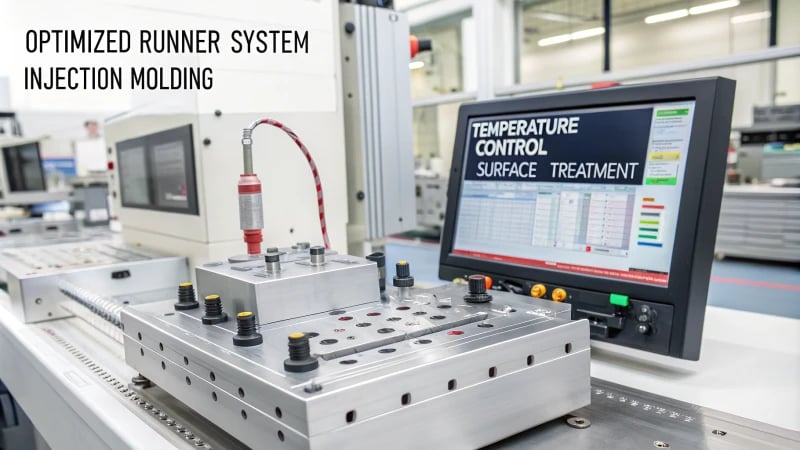
How Can You Optimize a Mold’s Runner System for a Balanced State?
This article discusses how to optimize a mold's runner system for balance in injection molding. Key strategies include maintaining uniform runner sizes, implementing gradual transitions, and utilizing CAE software like Moldflow for simulations. Temperature control is crucial in hot runner ...
OPTIMIZATION
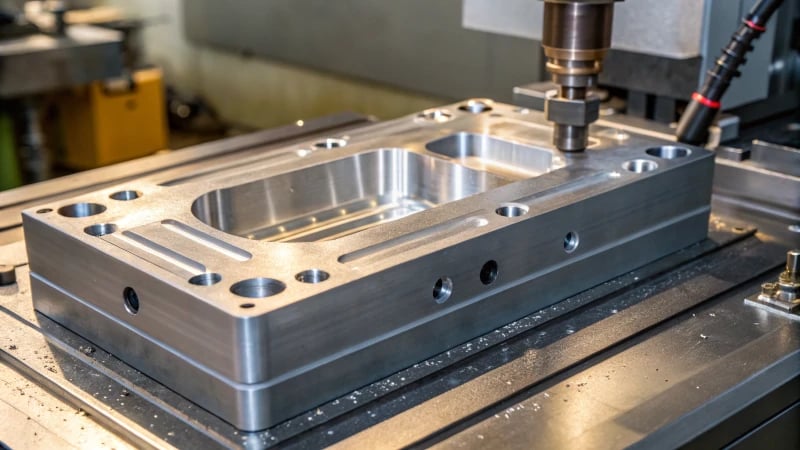
How Can You Enhance the Precision of Injection Molded Products by Optimizing the Parting Line?
This article explores how optimizing the parting line in injection molding can significantly enhance the precision and aesthetics of molded products. Key strategies include thoughtful mold design, selecting appropriate parting positions to minimize visible seams, utilizing advanced mold structures like ...
OPTIMIZATION
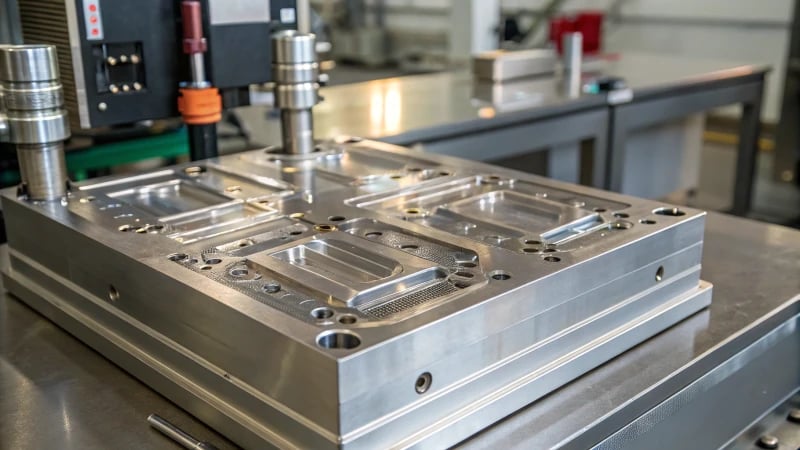
How Can Mold Adjustments Enhance the Strength of Injection Molded Products with Low Injection Pressure?
This article explores how adjusting injection molds can significantly enhance the strength of injection molded products. Key strategies include optimizing gate systems, improving runner designs, enhancing exhaust systems, and controlling mold temperatures. By increasing gate sizes and repositioning them for ...
OPTIMIZATION
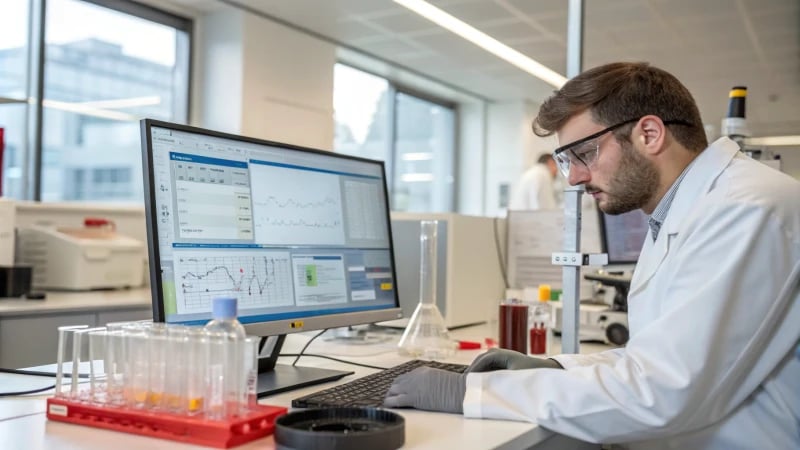
What Are the Best Methods to Determine the Appropriate Processing Temperature Range for Materials?
Determining the appropriate processing temperature range for materials is crucial in manufacturing. This article discusses the significance of analyzing material properties such as crystallinity and thermal stability, alongside utilizing reliable supplier data. It emphasizes the need for hands-on experimentation and ...
OPTIMIZATION
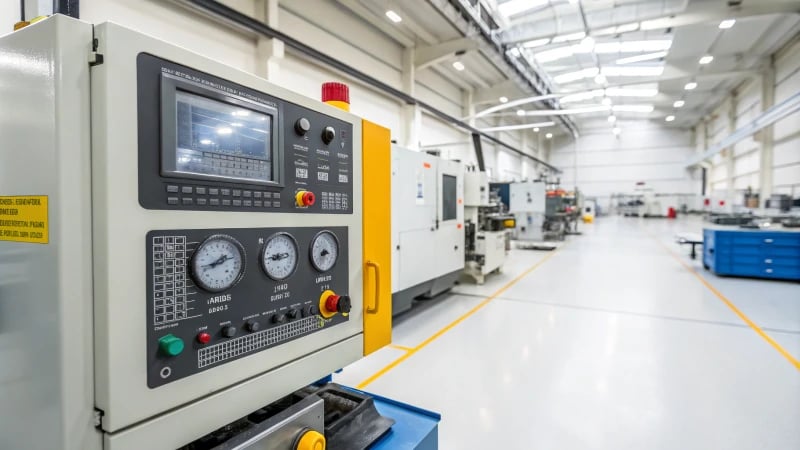
How Can You Adjust the Temperature of an Injection Mold?
Adjusting the temperature of injection molds is crucial for product quality. This article explores various methods such as modifying water or oil temperatures, adjusting heating power based on material needs, optimizing mold structure for uniform heat distribution, utilizing temperature sensors ...
OPTIMIZATION
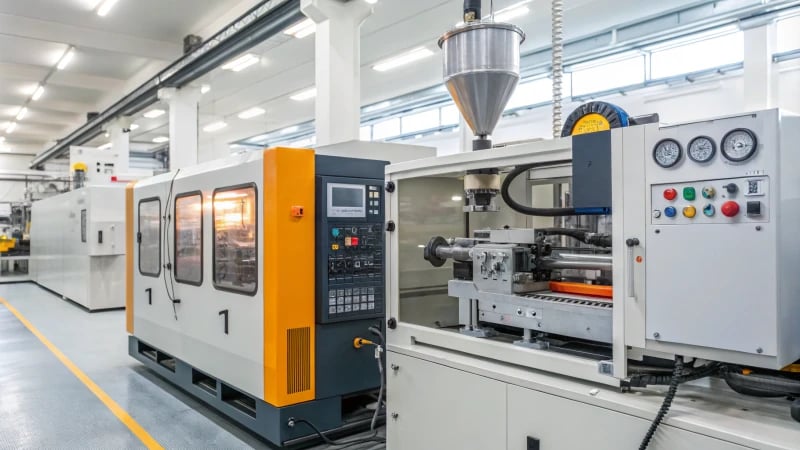
How Can You Adjust Injection Molding Process Parameters to Enhance Product Quality?
This article explores how to enhance product quality in injection molding by adjusting key parameters such as mold temperature, injection speed, and holding pressure. Higher mold temperatures improve surface gloss while optimizing injection speed reduces defects like flow marks. Proper ...
OPTIMIZATION
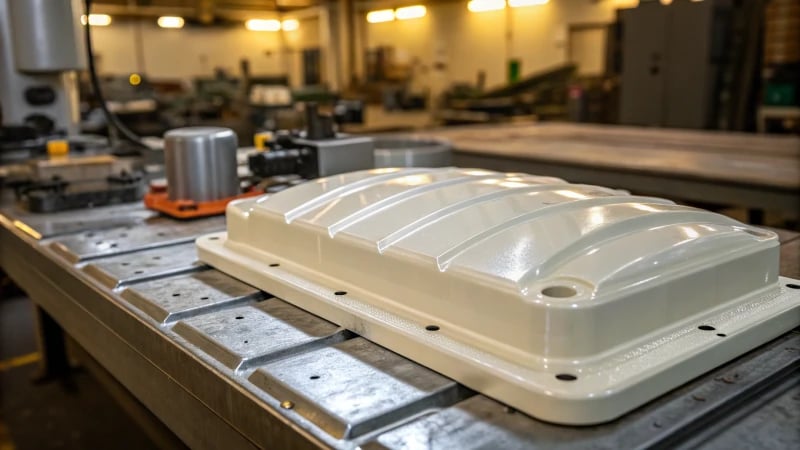
How Can You Enhance the Strength of Injection Molded Products?
This article explores effective strategies to enhance the strength of injection molded products. Key factors include careful material selection, optimization of injection molding process parameters such as pressure and speed, and improvements in mold design. Materials like polyamide (PA), polyoxymethylene ...
OPTIMIZATION
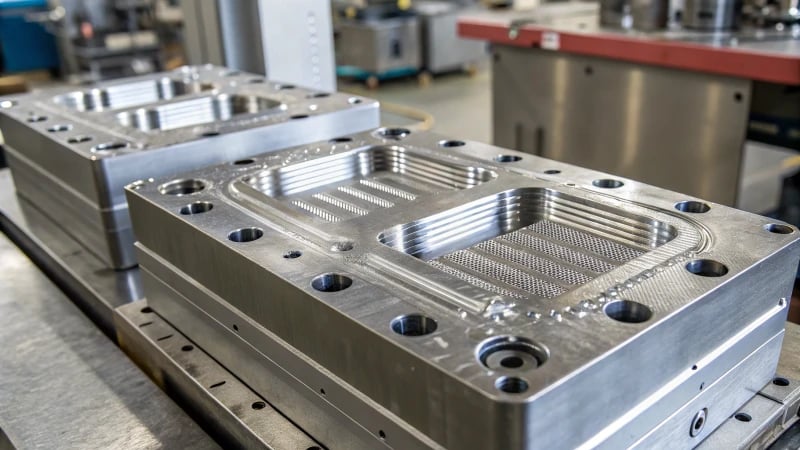
How Can You Achieve the Optimal Balance Between Hardness and Toughness?
Balancing hardness and toughness in mold design is essential for optimal performance. Small precision molds require high hardness (50-54HRC) for accuracy, while large complex molds prioritize toughness (8-10J/cm²) to withstand stress. Material characteristics also play a significant role; highly filled ...
OPTIMIZATION

What Are Effective Solutions for Insufficient Mold Filling?
This article explores the impact of insufficient mold filling on product quality in injection molding, detailing defects such as short shots, surface roughness, and dimensional deviations. It offers effective solutions including optimizing runner systems, improving gate design, enhancing exhaust systems, ...
OPTIMIZATION
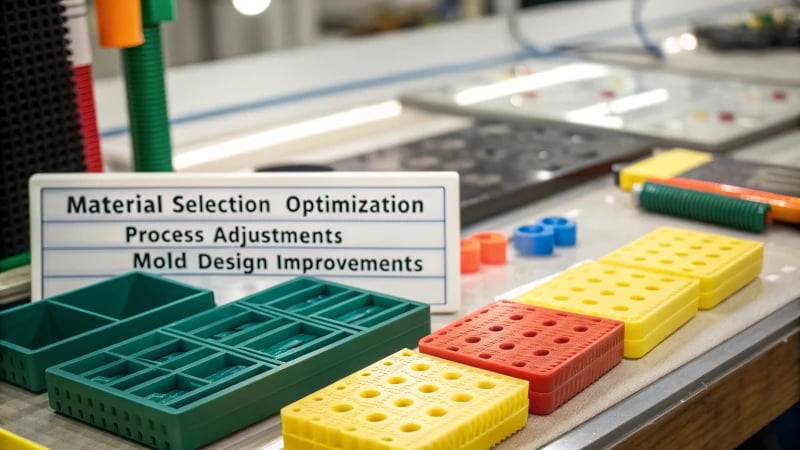
How Can You Effectively Handle Gate Marks from Point Gates?
Dealing with gate marks in injection molding can be challenging. This article explores various methods to effectively manage these imperfections, including manual and mechanical grinding techniques, chemical treatments like solvent wiping and polishing, advancements in hot runner technology, and strategic ...
OPTIMIZATION
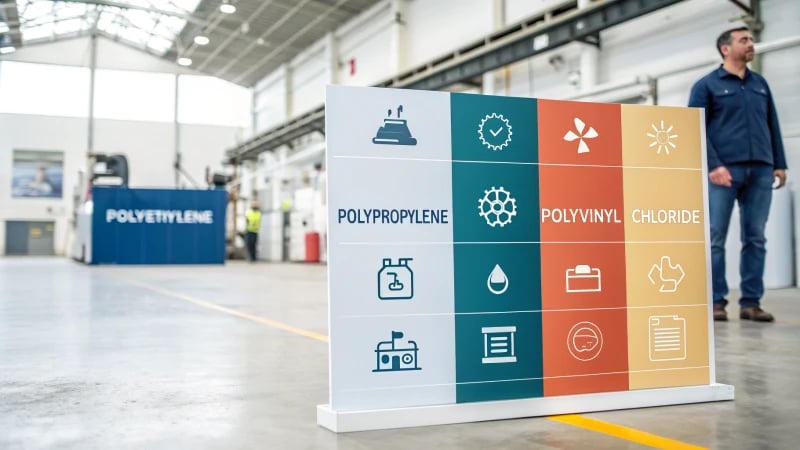
What Are the Optimal Processing Temperature Ranges for Various Plastic Materials?
This article explores the optimal processing temperature ranges for different plastic materials including polyethylene (LDPE and HDPE), polypropylene (PP), polystyrene (PS), polyvinyl chloride (PVC), polycarbonate (PC), nylon, and ABS. It emphasizes the importance of precise temperature control in achieving high-quality ...
OPTIMIZATION
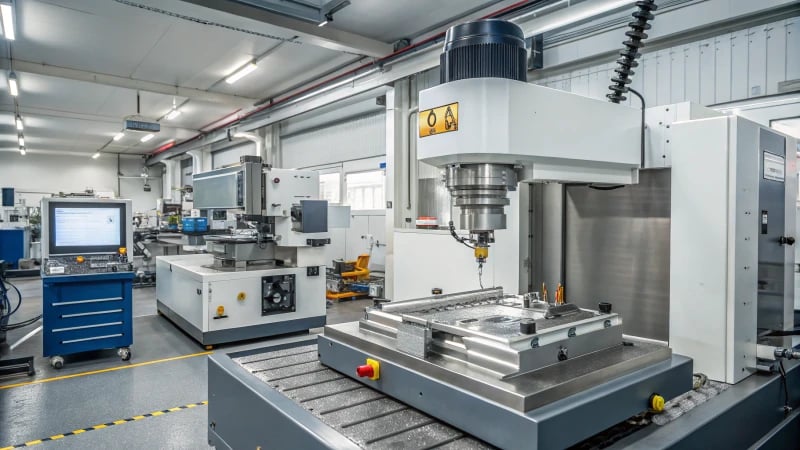
What Are the Best Ways to Reduce Dimensional Deviation in Mold Manufacturing?
Reducing dimensional deviation in mold manufacturing is crucial for achieving high precision and quality. Key strategies include regular maintenance of equipment like CNC machines, careful selection and monitoring of tools, optimizing processing parameters, and thoughtful mold design. Implementing rigorous quality ...
OPTIMIZATION
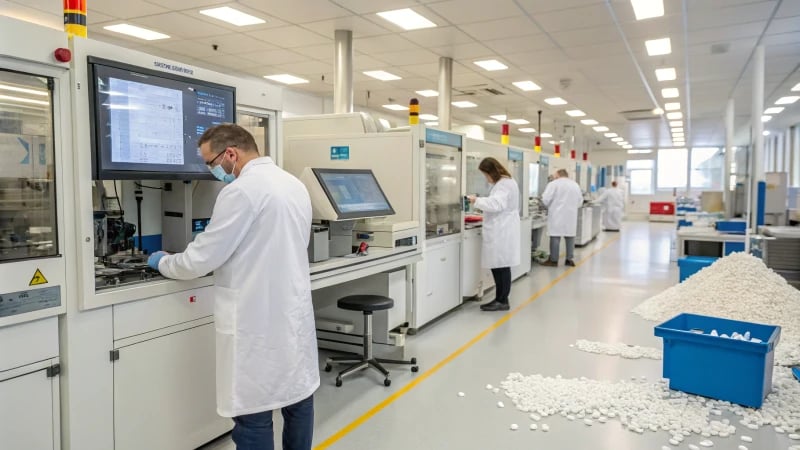
How Do You Determine the Optimal Processing Temperature for Plastic Materials?
This article explores how to determine the optimal processing temperature for plastic materials by examining key factors such as melting points, thermal stability, viscosity, hygroscopicity, and the effects of additives. Understanding these characteristics is crucial for achieving efficient production and ...
OPTIMIZATION
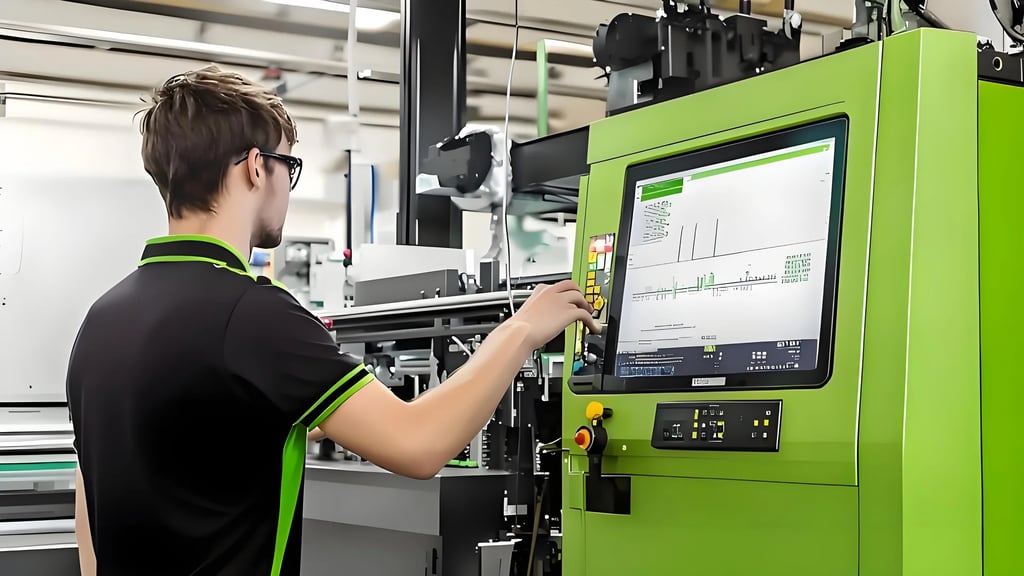
How Do You Optimize Injection Speed and Pressure for Better Performance?
Optimizing injection speed and pressure in molding is essential for achieving high-quality products. Understanding material traits and product designs allows for precise adjustments. Systematic testing helps identify flaws early, ensuring consistent results. Operators should familiarize themselves with machine controls and ...
OPTIMIZATION
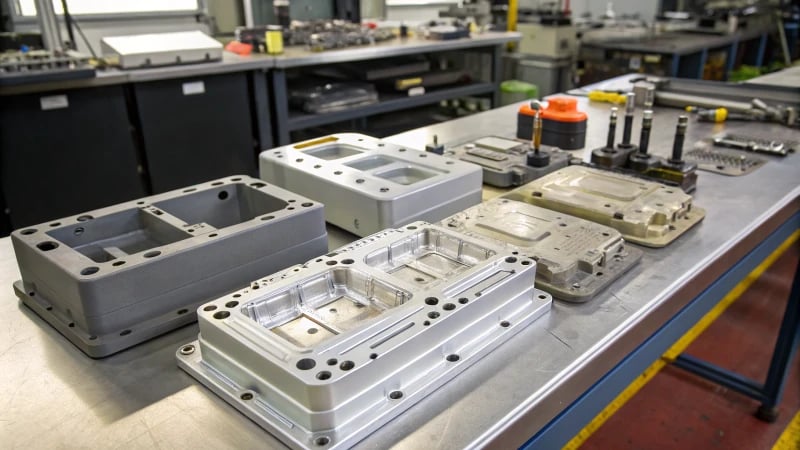
What Are Effective Ways to Reduce Appearance Defects in Injection Molded Products?
Injection molding can lead to various defects like flash, shrinkage, weld marks, flow marks, and silver streaks. This article outlines effective methods for reducing these appearance defects through optimized mold design, careful material selection, and precise adjustments in the injection ...
OPTIMIZATION
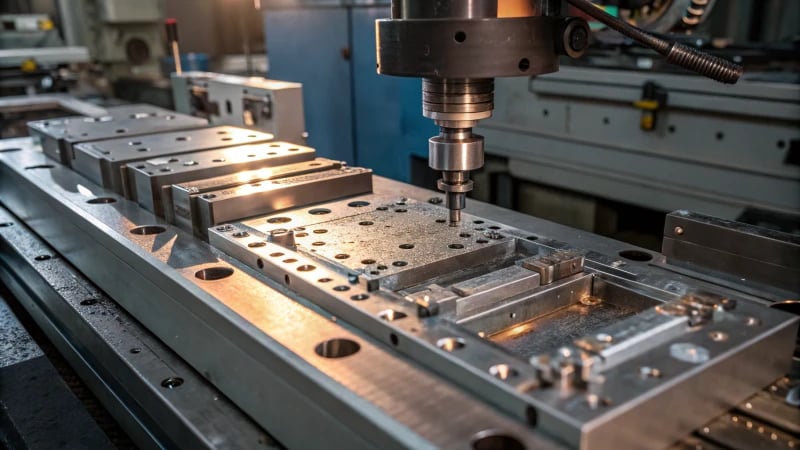
How Can You Increase Ejection Force by Enhancing Mold Structure?
This article explores effective strategies for increasing ejection force in injection molding. Key methods include optimizing the mold design, enhancing ejector mechanisms, strengthening guiding structures, and adjusting demolding angles. By implementing these techniques, manufacturers can achieve smoother product releases, minimize ...
OPTIMIZATION
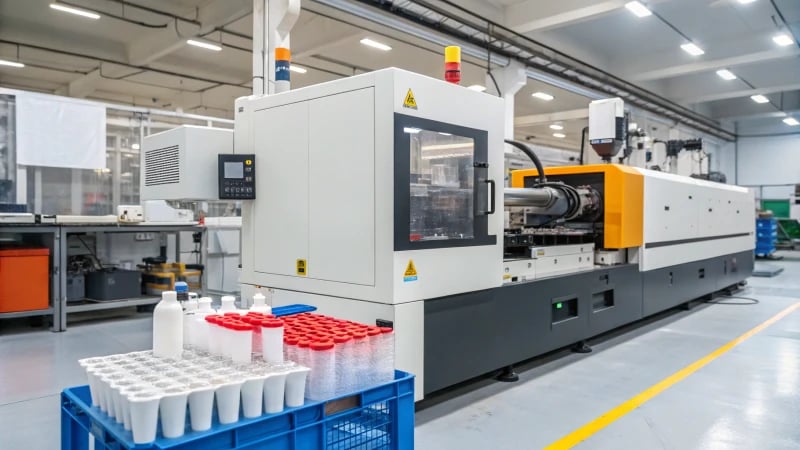
How Does Ejection Force Impact Molds and Plastic Products?
Ejection force plays a critical role in injection molding, affecting both the quality of plastic products and the longevity of molds. Excessive ejection force can lead to surface damage, dimensional inaccuracies, and internal structure failures in molded products, while insufficient ...
OPTIMIZATION
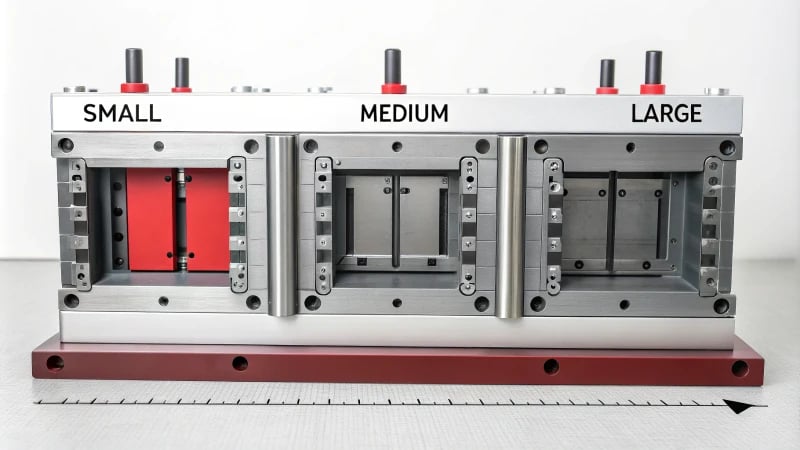
What Is the Best Method to Determine Film Gate Width for Specific Product Size and Wall Thickness?
In injection molding, selecting the correct film gate width significantly impacts product quality and efficiency. This article outlines guidelines based on product size—small (50%-100% of width), medium (30%-70%), and large (20%-50%)—and wall thickness considerations. For thin-wall products, wider gates (40%-80%) ...
OPTIMIZATION
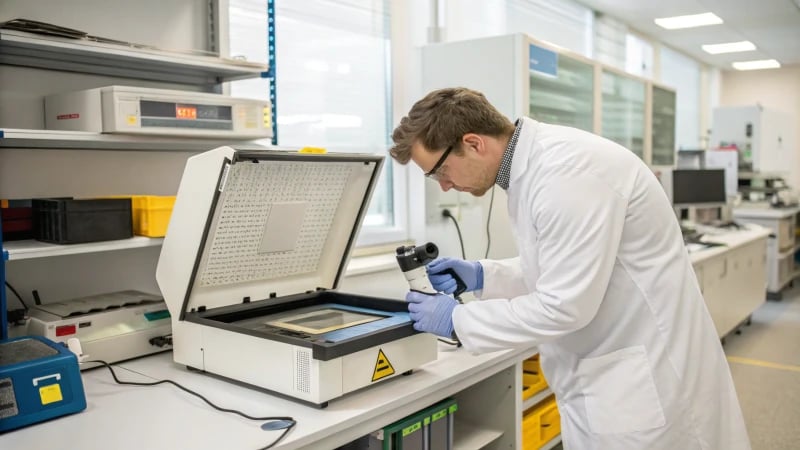
How Do You Choose the Right Processing Temperature for Your Material’s Properties and Application Needs?
Selecting the appropriate processing temperature is essential for achieving desired material properties and product quality. This article explores how factors like crystallinity, thermal stability, flowability, and application requirements influence temperature settings. Crystalline materials require temperatures above their melting points for ...
OPTIMIZATION
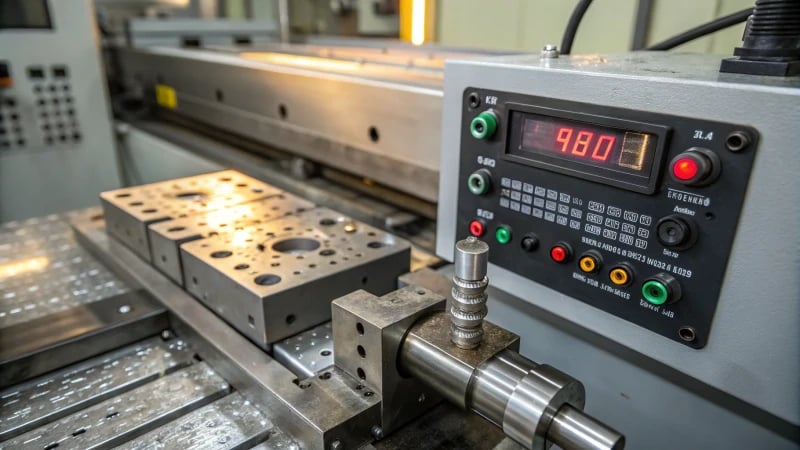
How Does Mold Temperature Impact the Strength of Injection Molded Products?
Mold temperature plays a crucial role in determining the strength and toughness of injection molded products. Proper control of mold temperature enhances melt fluidity, allowing for better filling of complex designs and promoting optimal molecular chain orientation. For materials like ...
OPTIMIZATION