In the competitive world of manufacturing, maximizing efficiency is key to staying ahead. For those in the injection molding industry, maintaining equipment health is a top priority.
A well-planned injection mold maintenance schedule boosts production efficiency by reducing downtime, preventing costly repairs, and ensuring consistent product quality. Regular maintenance tasks such as cleaning, inspection, and lubrication keep molds in optimal condition, supporting uninterrupted operations and longevity.
While this overview provides a glimpse into the benefits of a structured maintenance plan, diving deeper into specific maintenance strategies can offer insights that are both practical and transformative for your production environment. Read on to discover how each element of the schedule plays a critical role.
Regular mold maintenance reduces production downtime.True
Routine checks prevent unexpected breakdowns, ensuring continuous operations.
What Are the Key Benefits of Injection Mold Maintenance?
Effective maintenance of injection molds is crucial for optimizing production and ensuring long-term equipment reliability.
Key benefits of injection mold maintenance include extended mold lifespan, reduced downtime, cost savings, and enhanced product quality. Regular maintenance ensures molds operate efficiently, preventing defects and improving overall production consistency.
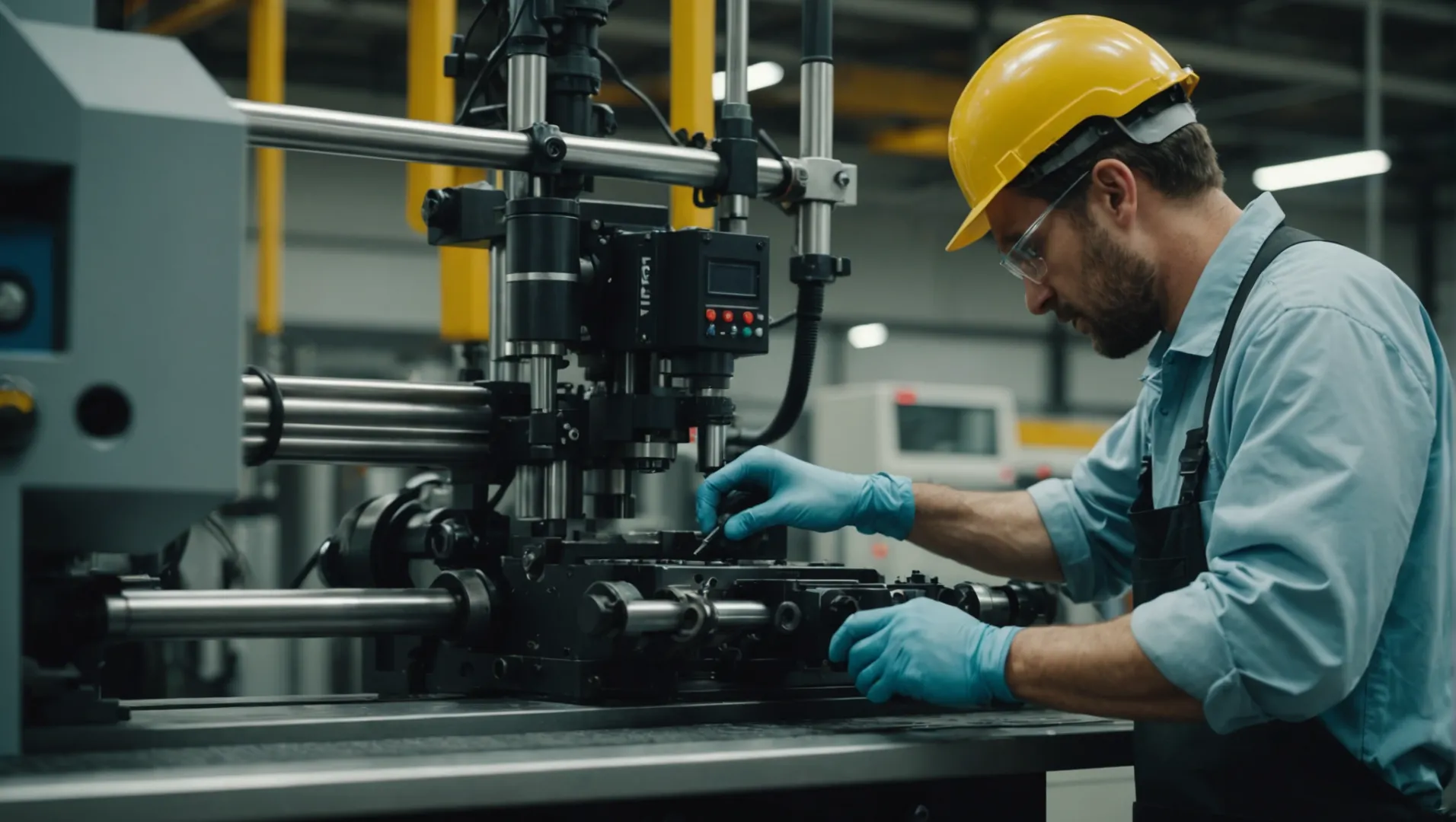
Extending Mold Lifespan
Regular injection mold maintenance1 significantly extends the lifespan of molds by preventing wear and tear. Daily tasks such as cleaning mold surfaces and checking lubrication systems help maintain operational integrity, reducing the likelihood of costly replacements. Over time, these practices save both time and resources for manufacturers.
Reducing Downtime
Maintenance schedules are designed to minimize production interruptions. By routinely inspecting critical components like cooling and electrical systems, potential issues are identified early, preventing unexpected breakdowns. This proactive approach means fewer delays in production, allowing businesses to meet deadlines consistently.
Cost Savings
Investing in a comprehensive maintenance plan reduces long-term costs. While there is an upfront investment in labor and materials for maintenance activities, this pales in comparison to the expenses associated with major repairs or new mold fabrication. Regular checks also help in catching minor issues before they escalate, avoiding costly emergency fixes.
Enhancing Product Quality
Consistent maintenance ensures molds remain in optimal condition, directly impacting the quality of finished products. Clean and well-maintained molds produce parts with fewer defects, such as flash or surface blemishes. This leads to higher customer satisfaction and reduces waste from rejected parts.
Supporting Continuous Improvement
A well-documented maintenance schedule allows for continuous improvement2 in production processes. Data gathered from routine checks can be analyzed to improve mold designs or adjust operational parameters, driving efficiency and innovation within the manufacturing setup.
Through these strategies, businesses not only preserve their assets but also enhance overall productivity and competitiveness in the market.
Regular mold maintenance extends lifespan by preventing wear.True
Maintenance prevents wear, extending mold lifespan and saving costs.
Skipping maintenance reduces product quality and increases defects.True
Lack of maintenance leads to defects, impacting product quality.
How Does Each Maintenance Interval Contribute to Efficiency?
Each maintenance interval in injection molding plays a unique role in ensuring efficiency and preventing downtime.
Daily, weekly, monthly, quarterly, and annual maintenance intervals each contribute to injection molding efficiency by addressing specific operational needs. Regular upkeep prevents wear, optimizes performance, and extends the lifespan of molds, thereby enhancing overall production efficiency.
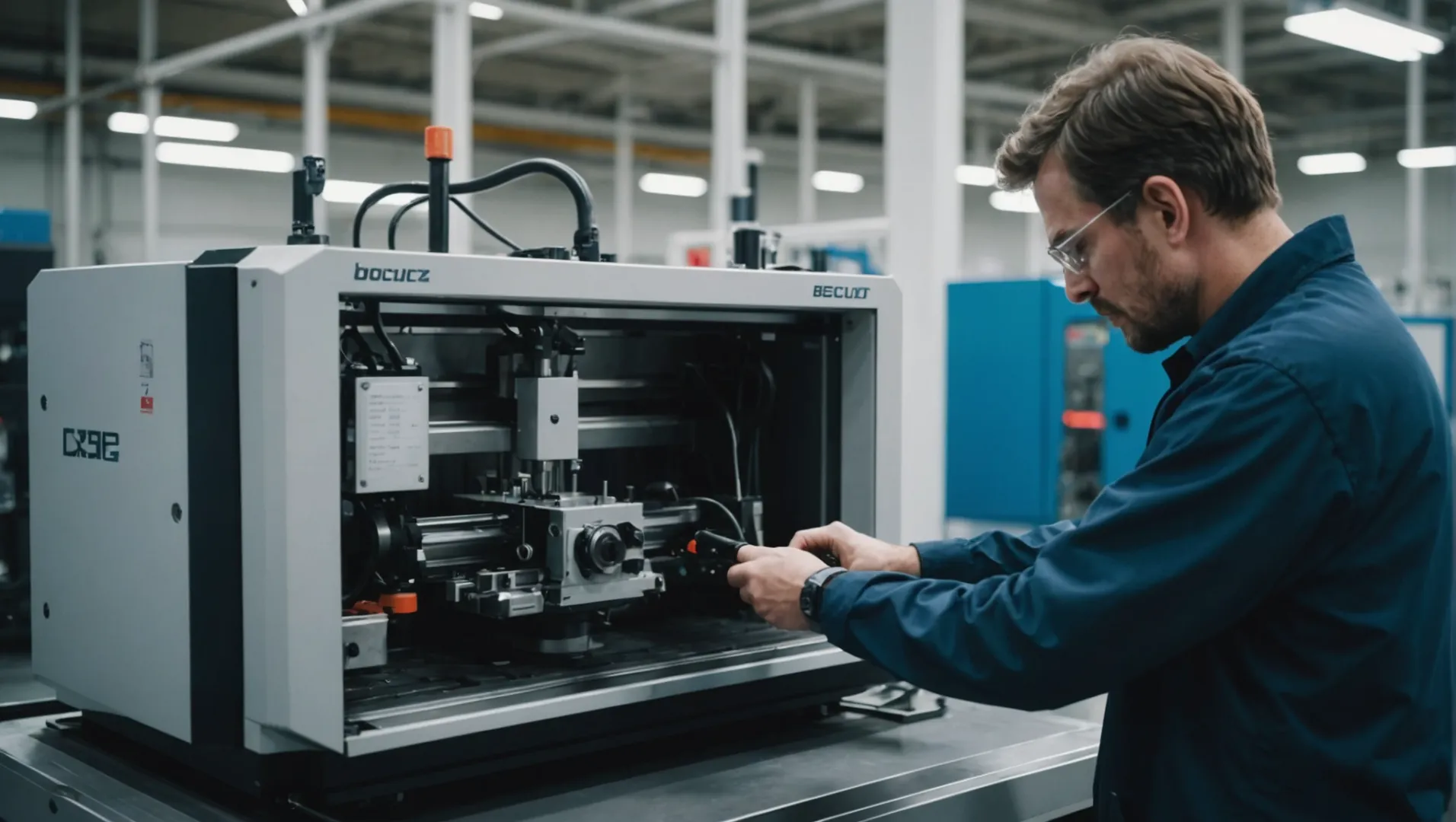
Daily Maintenance: The Foundation of Consistent Operations
Daily maintenance is crucial as it involves routine tasks that ensure the mold remains in peak condition day in and day out. By cleaning the mold surface regularly and checking systems like cooling and lubrication, potential issues can be caught early3. This daily upkeep minimizes the risk of sudden breakdowns and ensures that the mold functions smoothly throughout each production cycle.
- Cleaning: Prevents buildup that can cause defects.
- Cooling Checks: Ensures efficient thermal management.
- Lubrication: Reduces friction and wear on moving parts.
Weekly Maintenance: In-Depth Inspections
Weekly maintenance focuses on more detailed inspections, enabling the identification of wear or damage that daily checks might miss. This interval allows for the replacement of worn components such as ejectors or guide pins, ensuring they do not affect the mold’s performance.
- Part Inspection: Ensures key components are not compromised.
- Fastening Bolts: Secures the mold structure against deformation.
- Exhaust System: Prevents defects by maintaining clear air channels.
Monthly Maintenance: Thorough Cleaning and Calibration
Monthly maintenance involves disassembling and thoroughly cleaning the mold, providing an opportunity to measure wear and adjust accordingly. This helps maintain dimensional accuracy and prevents long-term degradation.
Task | Purpose |
---|---|
Thorough Cleaning | Removes deep-seated residues |
Wear Measurement | Identifies changes in dimensions |
Electrical Check | Ensures reliable system operation |
Quarterly Maintenance: Comprehensive Overhaul
Every quarter, a comprehensive overhaul is conducted to assess the mold’s structural integrity and performance. This is when professional maintenance personnel perform detailed analyses to address any underlying issues.
- Structure Analysis: Ensures no hidden damage.
- Replacement of Worn Parts: Critical for maintaining precision.
- Performance Review: Aligns operations with production goals.
Annual Maintenance: Strategic Improvements
Annual maintenance goes beyond mere repairs, often involving technological upgrades that keep the mold aligned with industry advancements. Whether it’s adopting hot runner technology or enhancing automation features, these updates are vital for maintaining competitive efficiency levels.
By adhering to these meticulously planned intervals, manufacturers can enjoy enhanced efficiency, reduced downtime, and prolonged mold life, ultimately supporting a robust production environment. For more insights on how maintenance impacts overall efficiency, consider exploring advanced maintenance techniques4.
Daily maintenance prevents sudden breakdowns in injection molding.True
Regular cleaning and checks catch potential issues early, reducing breakdowns.
Quarterly maintenance involves only minor inspections.False
Quarterly maintenance includes comprehensive overhauls and structural assessments.
What Tools and Techniques Enhance Mold Maintenance?
Ensuring the longevity and efficiency of molds requires precise tools and techniques. Discover how to enhance your maintenance routines.
Tools and techniques such as ultrasonic cleaners, mold cleaning sprays, and advanced lubrication systems enhance mold maintenance by ensuring thorough cleaning, preventing corrosion, and reducing wear. Implementing these strategies helps maintain optimal mold condition, improving efficiency and extending mold life.
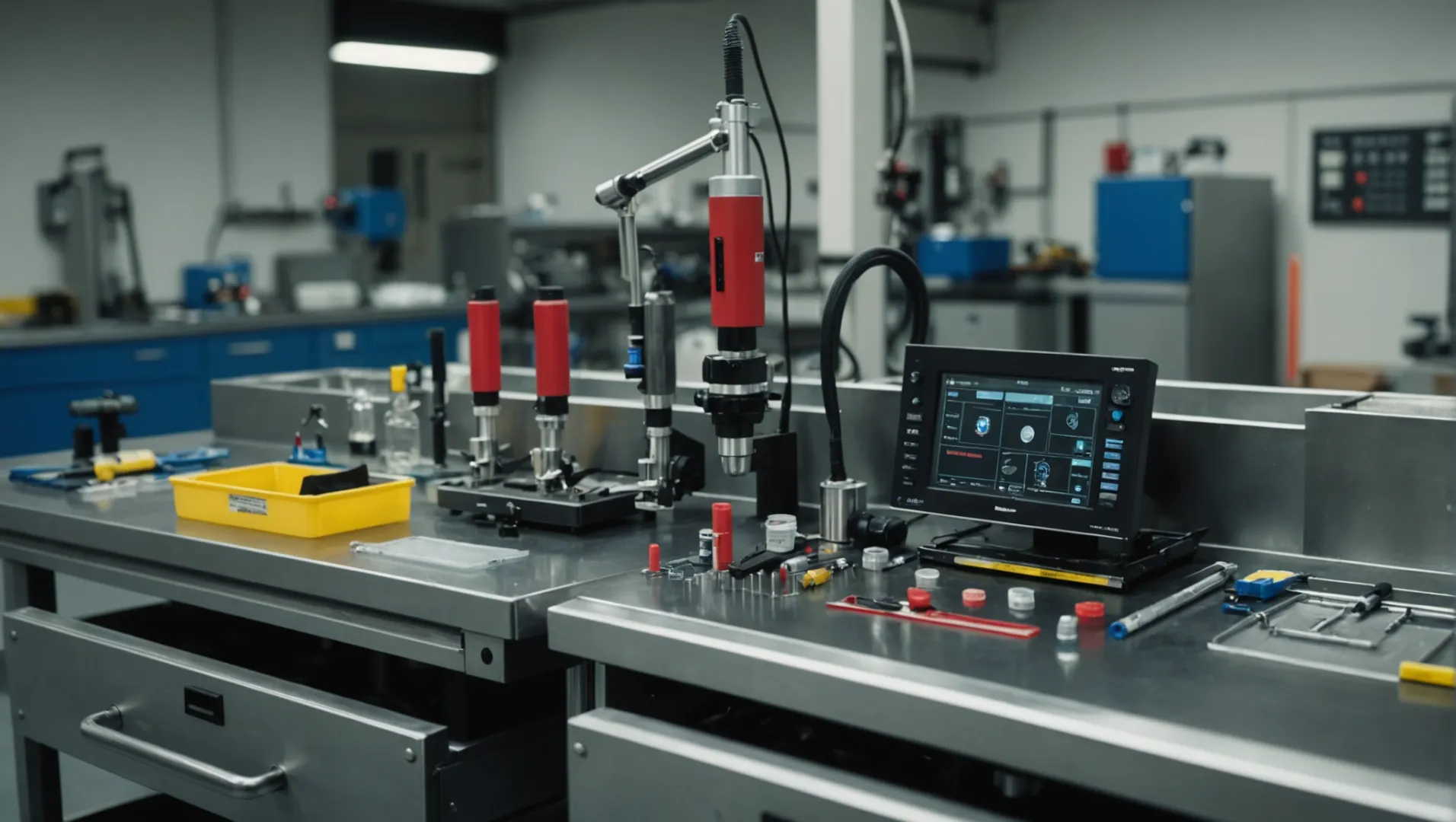
Ultrasonic Cleaners: Precision Cleaning
Ultrasonic cleaners are invaluable for maintaining molds, providing thorough cleaning without causing damage. These devices use high-frequency sound waves to create microscopic bubbles that remove dirt and residue from even the most intricate mold parts. This method is especially useful for cleaning molds with complex geometries or those that are difficult to disassemble.
Benefits
- Thorough Cleaning: Reaches tight corners and small crevices.
- Non-Abrasive: Prevents surface damage.
- Time-Efficient: Quickly removes contaminants.
For businesses seeking a comprehensive mold cleaning process5, ultrasonic cleaners offer a robust solution to maintain cleanliness and efficiency.
Mold Cleaning Sprays: Quick Solutions
Mold cleaning sprays are essential for quick, on-the-spot maintenance. Designed to remove surface grime and residue effectively, they are ideal for daily maintenance routines. These sprays are formulated to be non-corrosive, ensuring they do not damage the mold surfaces while enhancing operational efficiency.
Advantages
- Fast Application: Ideal for quick clean-ups during production.
- Non-Corrosive: Safe for all mold surfaces.
- Residue-Free: Leaves no harmful deposits.
Utilizing effective mold cleaning sprays6 can significantly reduce downtime during production runs, ensuring molds remain in top condition.
Advanced Lubrication Systems: Reducing Wear
Lubrication is a critical aspect of mold maintenance, as it reduces friction and wear on moving parts such as sliders and guide pins. Advanced lubrication systems automate this process, ensuring consistent application of lubricants where needed. This not only extends the life of the mold but also maintains product quality by preventing wear-induced defects.
Features
- Automated Application: Ensures precise lubricant distribution.
- Consistent Coverage: Reduces human error in manual application.
- Extended Mold Life: Minimizes friction and wear.
Implementing automated lubrication systems7 can drastically improve the efficiency of maintenance schedules, leading to reduced maintenance costs and enhanced production reliability.
Visual Inspection Tools: Detecting Wear Early
Regular visual inspections with tools like magnifying glasses or borescopes help detect early signs of wear or damage. Identifying issues early can prevent larger problems, reducing repair costs and extending the lifespan of the mold. These tools allow maintenance teams to pinpoint areas needing attention before they lead to significant downtimes or defects.
- Magnifying Tools: Provide detailed views of surface conditions.
- Borescopes: Access hard-to-reach areas inside molds.
- Digital Cameras: Document conditions for ongoing assessments.
Incorporating advanced visual inspection tools8 into regular maintenance routines is crucial for proactive management of mold health.
Ultrasonic cleaners damage mold surfaces.False
Ultrasonic cleaners are non-abrasive, ensuring no surface damage.
Advanced lubrication systems reduce mold wear.True
They ensure consistent lubricant application, minimizing friction.
How Can Technology Transform Mold Maintenance Practices?
In an era where technological advancements redefine industrial standards, the injection molding sector must embrace innovation to enhance mold maintenance.
Technology transforms mold maintenance by introducing predictive analytics, automation, and advanced cleaning techniques, leading to more efficient and accurate upkeep of molds.
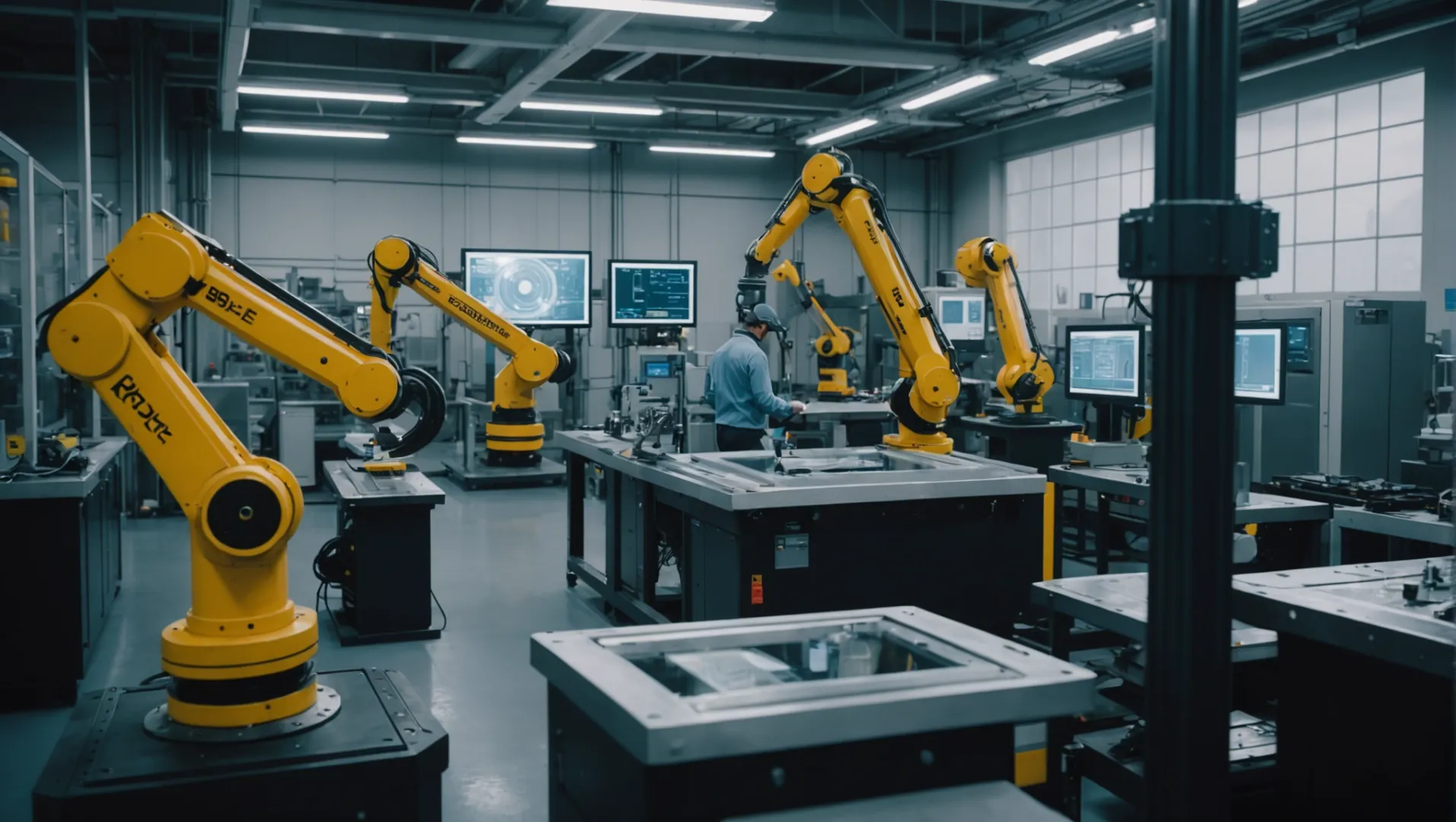
Harnessing Predictive Analytics for Proactive Maintenance
Predictive analytics leverages data to forecast potential mold issues before they occur, minimizing unexpected downtimes. By using sensors and IoT-enabled devices, real-time data on mold conditions can be collected and analyzed. This technology allows operators to predict wear and tear, facilitating timely interventions. Implementing predictive maintenance strategies9 can significantly reduce unscheduled repairs, thus optimizing production schedules.
Automation in Routine Maintenance
Automation simplifies daily maintenance tasks, such as cleaning and lubrication. Automated systems can be programmed to perform repetitive tasks with precision and consistency, reducing human error. For instance, automatic cleaning systems can ensure that mold surfaces are free from residues without manual intervention. This not only enhances efficiency but also extends the lifespan of the molds by ensuring consistent upkeep.
Advanced Cleaning Techniques
Traditional cleaning methods might not suffice for modern molds that require intricate detailing. Technologies like ultrasonic cleaning and laser cleaning have emerged as superior alternatives. Ultrasonic cleaning uses high-frequency sound waves to remove contaminants from mold surfaces without causing damage, while laser cleaning offers a contact-free solution that can effectively remove rust and residues. Both methods ensure thorough cleaning, which is crucial for maintaining mold integrity.
Digital Twin Technology
The concept of digital twins involves creating a virtual replica of the mold. This replica can be used for simulations to test different maintenance scenarios and predict their outcomes without physical trials. Digital twins provide insights into potential maintenance challenges and allow for strategic planning to address these issues proactively.
Integrating Artificial Intelligence (AI)
AI can enhance decision-making processes in mold maintenance by analyzing vast amounts of data to recommend optimal maintenance schedules. Machine learning algorithms can identify patterns in mold usage and suggest tailored maintenance plans that align with specific operational needs. This targeted approach ensures that molds receive the right level of attention at the right time, improving overall efficiency.
By integrating these technological innovations into mold maintenance practices, businesses can achieve higher efficiency, reduce operational costs, and enhance the quality of their molded products. Embracing technology not only transforms how maintenance is performed but also paves the way for more resilient manufacturing processes.
Predictive analytics minimizes mold downtime.True
Predictive analytics forecasts issues, reducing unexpected mold downtimes.
Traditional cleaning methods outperform ultrasonic cleaning.False
Ultrasonic cleaning is superior, removing contaminants without damage.
Conclusion
By implementing a structured mold maintenance schedule, you can significantly enhance efficiency and reduce costs. Regular upkeep ensures long-term operational success and continuous improvement.
-
Explore detailed insights into maintaining molds effectively.: Regular, careful injection mold maintenance can prevent part failures and lower the overall cost of your injection molding program. ↩
-
Learn how ongoing improvements boost efficiency and innovation.: Continuous improvement is a method of identifying and acting on areas of inefficiency (or error) in a manufacturing process. ↩
-
Explore why daily checks are crucial for preventing operational issues.: A well-designed and regularly maintained mold is key to designing high-quality, consistent injection molded parts. The cooling effect of the … ↩
-
Learn about cutting-edge methods to enhance mold longevity and efficiency.: This should include cleaning the mold regularly to remove debris and buildup, lubricating the mold to help prevent wear and tear on the moving … ↩
-
Learn about ultrasonic cleaners for efficient mold maintenance.: Ultrasonic cleaning uses a process called cavitation – the implosion of billions of micron-sized vacuum air bubbles – against surfaces immersed … ↩
-
Explore top-rated mold cleaning sprays for quick solutions.: Best Overall: RMR Brands RMR-141 Disinfectant at Amazon $26 ; Best for Bathrooms: · Clorox Tilex Mold and Mildew Remover at Amazon · $10 ; Best … ↩
-
Discover how automated lubrication systems enhance efficiency.: Automatic lubrication systems primarily help reduce wear and tear of device components, reduce energy consumption, decrease the amount of heat … ↩
-
Find essential tools for detecting mold wear early.: Fiber lasers offer a simplicity, speed, control and portability, minimizing mold cleaning risks. Read More · Are You a Moldmaker Considering 3D … ↩
-
Learn how predictive analytics minimizes unscheduled repairs in injection molding.: We introduce a generalized framework for implementation of predictive maintenance in injection molding process by integrating a variety of different data … ↩