Do you often find yourself deeply involved in the complicated world of injection molding, struggling to adjust those tricky parameters for a flawless finish?
To improve product quality in injection molding, adjust things like mold temperature, injection speed and holding pressure. Higher mold temperature probably increases surface shine. Changing injection speed and pressure maybe reduces defects and keeps size correct.
The first time I saw a stubborn flow mark on a prototype was unforgettable. I felt puzzled until I saw that the injection speed ran too fast. Slower speed and adjusting the gate position helped the melt fill the cavity without issues. This process is like a puzzle. Every part – temperature, pressure, speed – must fit perfectly to craft a flawless product. Pure joy comes from everything falling into place, especially when it means stronger and more reliable products.
Increasing mold temperature improves surface gloss.True
Higher mold temperatures allow the plastic to flow better, enhancing gloss.
Reducing injection speed increases product defects.False
Slower injection speeds can reduce stress and prevent defects.
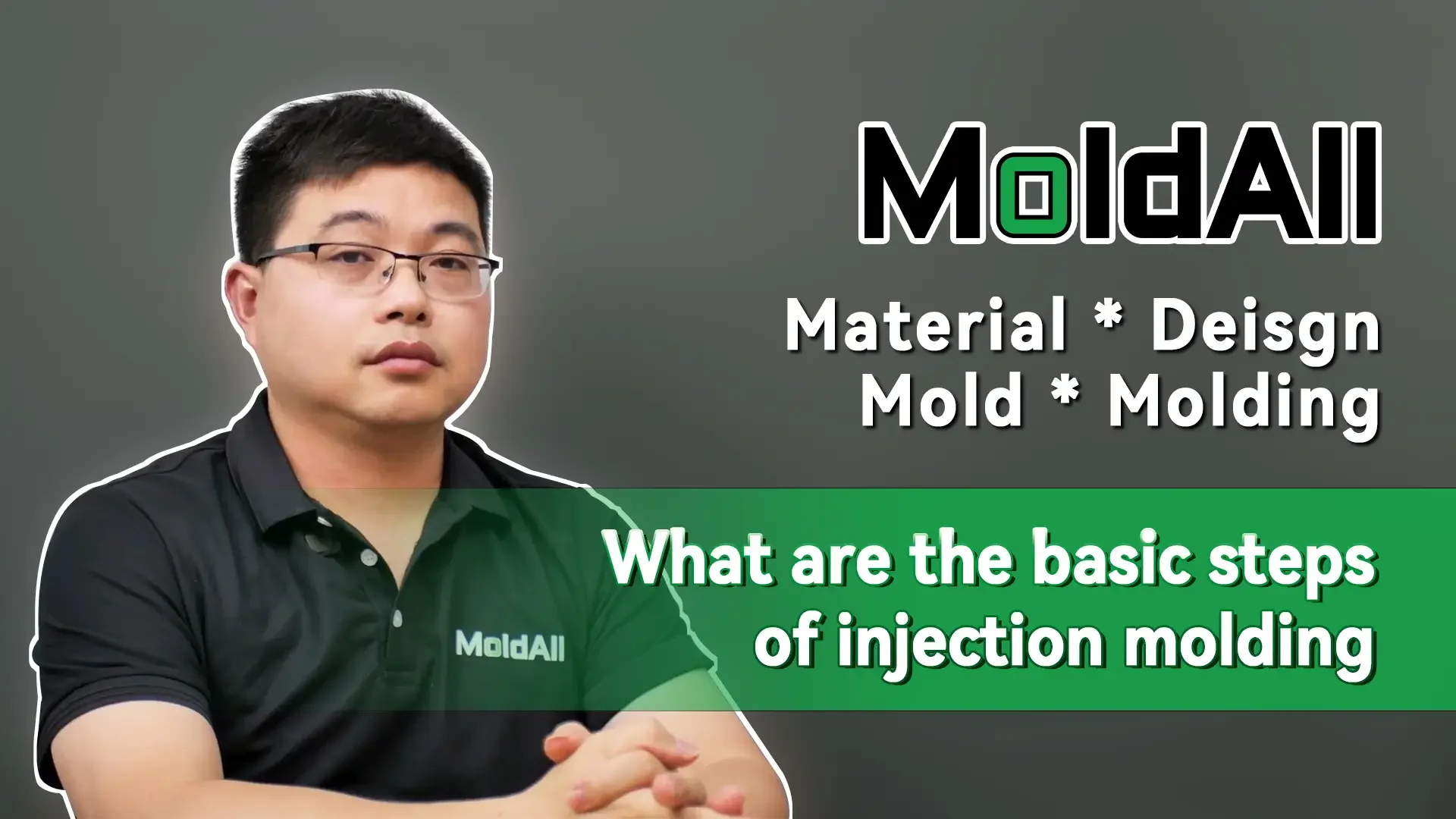
How Does Mold Temperature Affect Product Quality?
Have you ever thought about how your mold’s temperature affects your product’s quality?
Mold temperature is very important for product quality. It affects how smooth the surface is, how exact the size is and how strong the product is. Adjusting mold temperature really changes how a product looks, fits and lasts. This adjustment really helps achieve high quality in manufacturing. Quality is key.
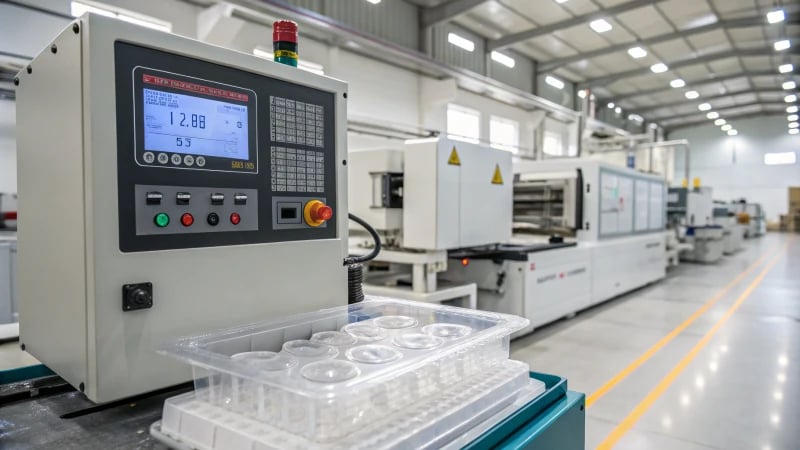
Product Appearance Quality
Surface Gloss:
In my early days in the molding industry, I remember facing surface gloss issues. It taught me how important mold temperature1 is. Raising the mold temperature for ABS plastic from 40-60℃ to 60-80℃ greatly improved surface finish. A dull product became shiny, just by changing the temperature settings.
Plastic Type | Original Temp (℃) | Adjusted Temp (℃) |
---|---|---|
ABS | 40-60 | 60-80 |
Surface Defects:
Surface flaws, such as flow marks or silver streaks, are annoying. Once, adjusting the injection speed fixed everything. Slower speed allowed for better material flow and reduced flaws, as if the material needed time to settle perfectly. A proper temperature adjustment2 helps mitigate these defects by ensuring even distribution and reducing moisture content.
Dimensional Accuracy
Oversized Products:
Oversized products posed another challenge for me. Reducing the injection volume and extending cooling time helped a lot. Adjusting the screw stroke felt like finding the perfect ingredient, using just the right amount to avoid oversized parts.
Issue | Solution | Adjustment |
---|---|---|
Oversized | Reduce Injection Volume | Screw Stroke: 70mm |
Small Size Issues:
Handling small-sized products was also hard. They often required more injection volume and higher holding pressure. It made me think of baking bread; with too little dough, you get a tiny loaf that doesn’t meet expectations.
Increasing both the injection volume and holding pressure can compensate for shrinkage, improving dimensional accuracy.
Product Physical Properties
Strength and Toughness:
Adjusting mold temperature improved product strength and toughness significantly. Watching higher temperatures improve molecular alignment during cooling was really fascinating. For PP plastic, adjusting mold temperature from 30-50℃ to 50-70℃ led to a noticeable difference.
A well-adjusted mold temperature3 enhances the strength and toughness of products.
By understanding these details has been crucial in my career, teaching me how important it is to get mold temperature right. It’s like tuning a musical instrument to achieve top product quality. Each adjustment moves me towards mastering the art of injection molding.
Higher mold temperature improves surface gloss of ABS products.True
Increasing mold temperature for ABS from 40-60℃ to 60-80℃ enhances gloss.
Lower mold temperature increases strength and toughness of products.False
Higher temperatures allow slower cooling, enhancing molecular alignment and toughness.
How Can Injection Speed Affect Surface Defects?
Have you ever been curious why that shiny surface on a molded item sometimes slips away?
Injection speed greatly influences the surface quality of molded items by affecting how the plastic melt moves inside the mold. A quick speed leads to flow marks. A slow speed results in a poor finish. Finding the perfect speed is crucial to reaching the best quality.
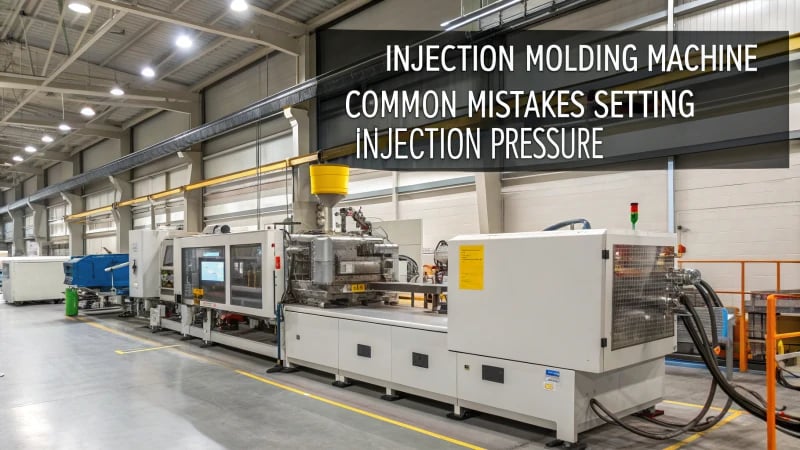
The Role of Injection Speed in Surface Quality
Injection speed in molding reminds me of tempo in music. Too fast or too slow can cause issues, impacting the product appearance quality4, including surface gloss and smoothness. This is vital for product look, especially the shine and smoothness of surfaces. I worked on some electronics cases once. Everything was fine, but the shine wasn’t good enough. Then I realized, the injection speed needed adjustments.
Surface Gloss and Defects
- Flow Marks: Getting a smooth surface sometimes leaves flow marks. These marks appear when speed is too high, making the plastic rush and show lines.
- Solution: Lowering the speed from 50-70mm/s to 30-50mm/s solved this problem. It worked wonders.
Parameter | Original Value | Recommended Value |
---|---|---|
Injection Speed | 50-70 mm/s | 30-50 mm/s |
- Silver Streaks: Annoying streaks occur when materials are too wet. During rainy months, our PA6 materials caused trouble.
- Solution: Dry materials to keep moisture below 0.2% for PA6.
Dimensional Accuracy and Injection Volume
Accurate dimensions are crucial. Once, we faced trouble with oversized parts.
- Oversized Products: Adjust injection volume by adjusting screw stroke from 80mm to 70-75mm saved the day.
- Small Size Products: Slightly increase volume and holding pressure for a perfect fill by increasing it by 10-15% to ensure proper filling.
Influence on Physical Properties
Speed also affects physical properties5 like strength and toughness:
- Insufficient Strength: More pressure compacts the melt well, improving strength by increasing injection pressure by 10-15%.
- Poor Toughness: Lowering screw speed lessens shearing, which enhances toughness from 100-120 r/min to 80-100 r/min.
Controlling injection speed changes product quality significantly. It really cuts defects and meets high beauty and function standards everyone wants.
Fast injection speeds cause flow marks.True
High speed causes turbulence, creating visible flow lines.
Slower injection speeds improve surface gloss.True
Reducing speed allows smoother filling, enhancing gloss.
Why Is Holding Pressure Crucial for Dimensional Accuracy?
Some molded parts turn out perfect. Others fall short. Accuracy matters a lot. Perfect parts do their job well. Imperfect ones might not fit right. Quality control is really important in molding. This decides the finished product. Quality control is key.
Holding pressure in injection molding is essential to fight material shrinkage. Parts need to keep precise dimensions and superior surface quality. This phase stabilizes the molten plastic as it cools. It prevents defects and achieves really accurate results.
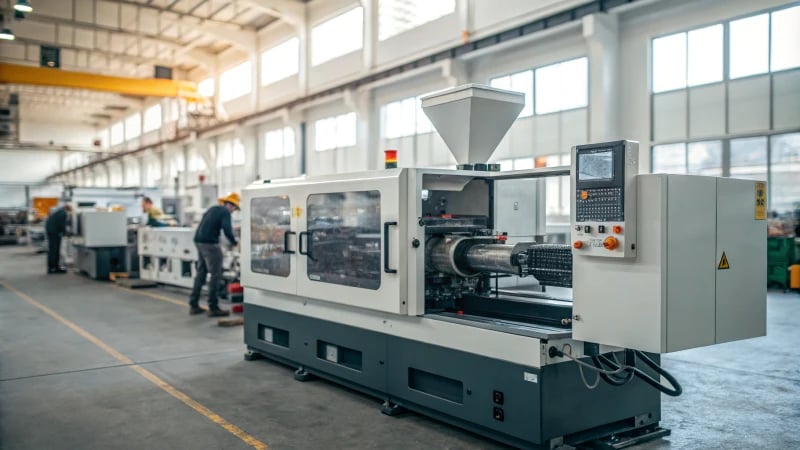
Understanding Holding Pressure
I remember my early days in mold design when I first learned about holding pressure, which my mentor called the "secret sauce" of injection molding. Holding pressure begins once the mold fills up. It keeps the plastic melt tight against the mold walls while cooling, balancing shrinkage, which is very important as it affects the final product’s precision.
Impact on Product Appearance Quality
Seeing a perfectly glossy surface on a finished part feels great. Early in my career, I saw some of my designs lacked shine because the mold temperature was too low and the holding pressure was off. Adjusting these settings—like raising temperature for ABS plastic from 40-60℃ to 60-80℃ and boosting holding pressure by 10-20%—resulted in that beautiful gloss and fixed unpleasant flow marks and silver streaks.
Effect | Action |
---|---|
Surface gloss | Increase mold temperature and holding pressure |
Surface defects | Adjust injection speed and gate position |
A small change goes a long way. For instance, increasing holding pressure by about 15% greatly improved both appearance and dimensional accuracy.
Ensuring Dimensional Accuracy
Dimensional accuracy holds vital importance in our field. Sometimes parts don’t fit because they are too large due to too much injection volume or not enough cooling time. Lowering the screw stroke or extending cooling time from 10-15 seconds to 15-20 seconds changes things significantly.
Key Adjustments:
- Oversized Parts: Reduce injection volume and ensure proper cooling time.
- Undersized Parts: Increase injection volume and holding pressure by about 10-15%.
Issue | Solution |
---|---|
Oversized | Adjust screw stroke, enhance cooling |
Undersized | Increase holding pressure and injection volume |
Influence on Physical Properties
Holding pressure affects more than size; it matters for strength and toughness too. Low pressure leads to weak products. Raising injection pressure by about 10-15% and extending holding time from 3-5 seconds to 5-8 seconds strengthens the product’s internal structure and total durability.
Physical Property | Adjustment |
---|---|
Strength | Increase injection pressure |
Toughness | Optimize mold temperature |
Getting these settings right feels like a small win every time. I know each part meets both dimensional and physical standards. Understanding these details not only improves product quality6 but also really increases our efficiency and success in the industry7.
Holding pressure affects dimensional accuracy.True
Holding pressure stabilizes the melt during cooling, ensuring precise dimensions.
Increasing holding pressure reduces surface gloss.False
Increased holding pressure enhances surface gloss by filling mold cavities.
How Can I Improve Product Strength and Toughness?
Ever wondered how products become tougher and more resilient? Let’s explore some clever techniques that increase both strength and quality. Maybe these methods are very useful for many industries. Improving these features often leads to better results. Increasing resilience matters a lot.
Increasing the product’s strength and toughness involves methods like setting the right mold temperature, changing the holding pressure and controlling how fast the injection happens. These steps help materials flow better and line up at a molecular level. This leads to really strong and durable products. Yes, very durable.
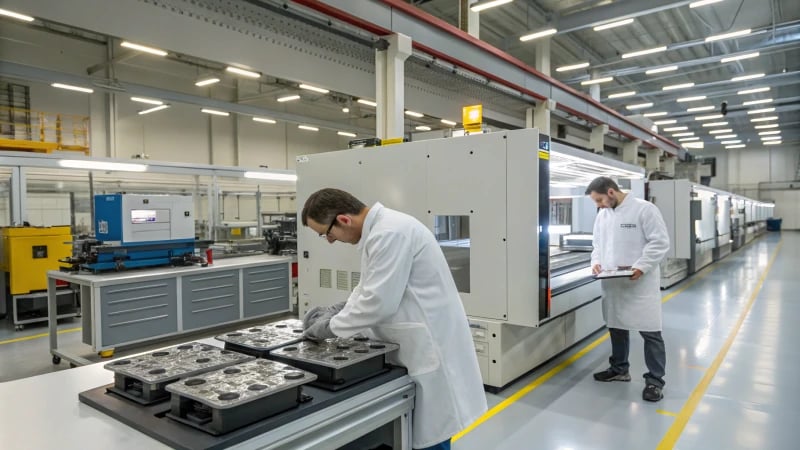
Setting Mold Temperature
Mold temperature acts like a sweet spot for plastic items. Adjust it perfectly, and products shine with a glossy surface and become tough. Once, when working with ABS plastic, we raised the mold temperature from 40-60°C to 60-80°C. The outcome? A surface smooth like glass, due to better plastic flow8.
Changing Holding Pressure
Holding pressure is like a gentle squeeze on the plastic melt. It helps fit the mold perfectly while cooling down. Increasing the holding pressure by 10-20% allowed us to reduce shrinkage. This led to better surface quality and stronger products.
Managing Injection Speed
Sometimes, fast injection causes visible flow marks. So, reducing the speed from 50-70mm/s to 30-50mm/s allows the material to fill the cavity better. This provides a smooth finish. Slower is better sometimes; it’s a bit like enjoying a scenic route instead of speeding through.
Keeping Size Accurate
Size accuracy is vital, especially for me since I love details. For large products, reducing injection volume and extending cooling time from 10-15 seconds to 15-20 seconds solved issues well.
Dimensional Issue | Solution |
---|---|
Oversized | Reduce injection volume, extend cooling time |
Small size | Increase injection volume, adjust holding pressure |
Improving Physical Qualities
Sometimes, a product just feels off. By raising injection pressure by 10-15%, every mold corner got filled. This increased density and strength. Prolonging the holding time from 3-5 seconds to 5-8 seconds also stabilized the inside structure.
Lowering screw speed from 100-120r/min to 80-100r/min helped too. This stopped too much shearing during molding and kept molecular chains9 intact. Tough materials like polypropylene needed this.
By tuning these elements, I personally saw manufacturers really sharpen the strength and toughness of their products. It’s a bit like cooking: get the mix and timing right, and it results in a masterpiece.
Increasing mold temperature enhances surface gloss.True
Higher temperatures improve plastic flow, enhancing surface smoothness.
Reducing injection speed increases flow marks.False
Lower speeds allow smoother filling, preventing flow mark defects.
Conclusion
Adjusting injection molding parameters like mold temperature, injection speed, and holding pressure enhances product quality by improving surface gloss, dimensional accuracy, and physical properties such as strength and toughness.
-
Explores how precise control of mold temperature can affect the finish and quality of molded products. ↩
-
Provides techniques to resolve common surface defects in molded products. ↩
-
Details the relationship between mold temperature adjustments and the mechanical properties of products. ↩
-
Explore how varying injection speeds impact product gloss and surface defects, providing insights into optimal settings. ↩
-
Discover how injection speed variations can alter the strength and toughness of plastic products during molding. ↩
-
Explore how holding pressure influences surface gloss and overall appearance quality in molded products. ↩
-
Learn about strategies to optimize injection molding settings for better dimensional accuracy and product quality. ↩
-
Exploring mold temperature effects provides insights into achieving better surface gloss and product aesthetics. ↩
-
Understanding molecular chains helps comprehend how material toughness is affected during manufacturing. ↩