Have you ever felt like understanding the quality of injection molds is like unraveling a well-hidden mystery?
You probably judge injection molds’ quality by examining the materials used and how they perform. Checking if they are accurate during production is also important. Assess whether the design is good and practical. Trial results must be evaluated. The mold’s durability matters. Mold durability is very important.
I remember the first time I had to look at an injection mold. I felt both excited and nervous. Our product’s success depended on this choice. It was like a complicated puzzle where each piece had to fit perfectly.
Understanding mold materials was key. I learned to study inspection reports very carefully, much like a detective looking for clues. Tiny surface defects seemed small but could cause big problems in production.
Checking manufacturing accuracy was my next task. I became very interested in measuring tools – calipers, micrometers and others. Structural design was also important. Parting surfaces and demolding systems needed perfect coordination.
Trial runs felt like an exciting event. We needed to succeed on the first try. Seeing the first successful batches was a thrill. Our hard work paid off.
Thinking about the mold’s service life made me thoughtful. It was not just about how long it could last, but about lasting without damage. Each mold had its own story, showing strength over time.
These moments taught me that mold evaluation is an art. It mixes technical skills with intuition and patience.
Material composition affects injection mold quality.True
The materials used in molds determine durability and performance.
Service life is irrelevant to mold quality.False
Longer service life indicates better durability and efficiency.
How Does Mold Material Affect Product Quality?
Picking the right mold material shapes your product’s quality and strength. It resembles choosing the best ingredients for a dish. When done correctly, something extraordinary comes to life.
Mold material impacts quality. It controls how strong, smooth and intact the final product is. P20 and H13 steel grades are very durable. They provide superior hardness and resist wear. This gives precision. It brings long life to manufacturing processes.
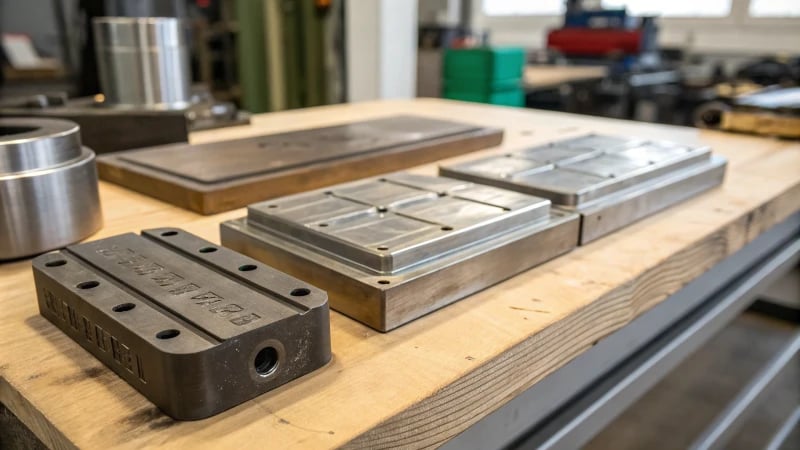
Importance of Material Composition and Performance
The quality of mold material1 is crucial. It’s like picking the right base for a house. My top choices have been P20 and H13 steel due to their hardness and resistance. For instance, on a project with H13 steel, its toughness stood out, even in high heat.
Material | Hardness (HRC) | Properties |
---|---|---|
P20 Steel | 30-36 | Wear-resistant, durable |
H13 Steel | 48-52 | High strength, toughness |
Toughness matters.
Surface Quality of Mold Material
Surface quality plays a quiet yet vital role in mold production. Tiny flaws, like cracks and pores, can quickly lead to major problems. Techniques such as magnetic particle flaw detection helped me spot these issues with great precision. A smooth surface is not just for looks; it keeps the mold strong.
Influence on Manufacturing Accuracy
Dimensional accuracy separates a perfect fit from a bad mismatch. In my early days, I learned how crucial tools like calipers and micrometers are for ensuring that the mold dimensions meet exact specifications. Picture spending hours designing a part, then it doesn’t fit due to a minor error.
For complex shapes, laser scanning2 now helps me check curvature errors with great ease. Precision is everything.
Role in Structural Design Efficiency
Good structural design sets the stage for success. Misaligned parting surfaces or demolding mechanisms lead to a bad experience. I faced cooling issues in a design until we set the channel distance to between 15-25 mm from the cavity surface.
This change brought uniform cooling:
Parameter | Ideal Range |
---|---|
Cooling Channel | 15-25 mm from cavity |
Cooling was then solved.
Impact on Mold Longevity and Wear Resistance
Quality materials protect mold life by reducing wear and fatigue. Seeing less than 0.05mm wear after 100,000 cycles feels like hitting gold:
Wear Tolerance |
---|
<0.05 mm after cycles |
It’s not only about extending life; it’s about keeping high standards.
By understanding these factors, I’ve chosen mold materials wisely. This really improves quality and efficiency, reducing defects and creating long-lasting molds.
H13 steel reaches 48-52HRC after quenching.True
H13 steel indeed reaches 48-52 HRC after quenching and tempering.
P20 steel is more wear-resistant than H13 steel.False
H13 steel is generally more wear-resistant than P20 due to higher hardness.
Why Is Manufacturing Accuracy Important for Molds?
Precision in mold manufacturing matters a lot. Mold manufacturing creates the very foundation for many products. Exact measurements and details lead to high-quality items. Precision reduces waste and errors, saving resources. Industries demand reliable and accurate molds for consistency. Slight errors in molds can really result in flawed products. High standards in mold creation improve overall product quality.
Precise mold production helps each item match exact requirements. Waste stays low and quality gets better. This affects the size and shape accuracy of plastic products. They probably fit and work as planned.
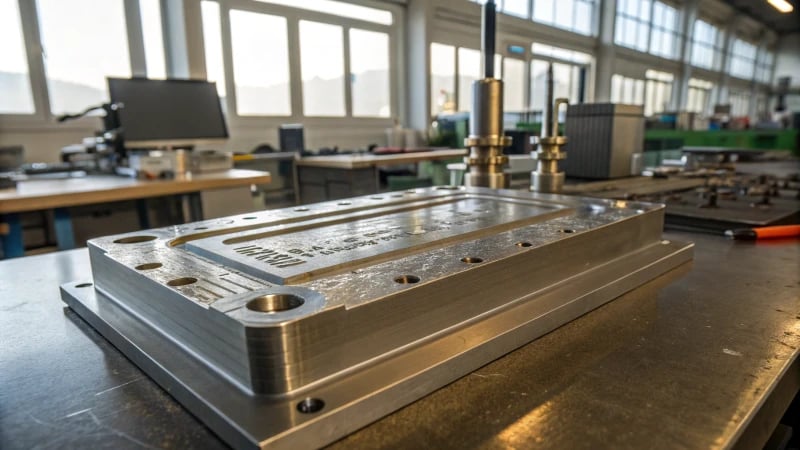
Dimensional and Shape Precision
I recall the first moment I held a perfectly shaped plastic piece. Each curve and edge was flawless. It was magical. Yet the true secret behind this magic is accuracy. Precision forms the core of mold creation. It affects every tiny detail and the overall product function.
Imagine building a house. A slight error in the foundation makes the wall crooked. Molds work the same way. Every sector, from cars to electronics, depends on exact measurements to ensure products function properly. Molds must be precise; otherwise, parts simply don’t fit.
For instance, in precision injection molds, maintaining tolerances within ±0.01mm ensures minimal size deviation in products.
Measurement Tools | Description |
---|---|
Calipers | Measure small distances accurately |
Micrometers | Offer precision measurement |
CMMs | Coordinate Measuring Machines for complex shapes |
Material Quality and Surface Finish
Material quality holds equal importance. Strong mold steels like P20 or H13 act as unsung heroes. These materials endure high temperatures and pressures without weakening.
Learning to check material composition through inspection reports showed me how these steps help prevent mold damage using tools like magnetic particle flaw detectors to identify surface defects that could lead to mold damage.
For example, H13 steel, after quenching and tempering, maintains its strength at high temperatures.
Explore mold material quality3
Structural Design Rationality
Correct design is key to smooth functioning. Accurate manufacturing ensures that mold design elements—like parting surfaces and cooling systems—are precise and functional.
I once spent days on a cooling system problem, later finding out the channels were poorly placed. A good cooling system not only improves efficiency but also lets each part cool evenly.
A rational cooling system is crucial for efficient production, affecting both product quality and cycle time by reducing cycle times significantly.
Understand mold cooling systems4
Trial and Wear Performance
I remember the nerves before my first mold trial—a successful trial brings relief and signals a good design. Manufacturing accuracy determines how well a mold performs during trials.
It’s fascinating to see how manufacturing accuracy affects wear resistance too; molds retain quality even after thousands of cycles by consistently producing good parts.
Assessing wear after production cycles ensures the mold’s longevity; if wear on cavity surfaces remains below 0.05mm after extensive use, the mold is deemed durable.
Precision molds reduce production costs.True
Accurate molds minimize errors, leading to less waste and rework, lowering costs.
H13 steel is unsuitable for high temperatures.False
H13 steel maintains strength at high temperatures after quenching and tempering.
What Makes a Mold Structure Design Rational?
Picture entering a workshop where every mold is flawless. Each mold shows careful design and skilled engineering.
Rational mold structure design needs choosing the right materials. Manufacturing must be precise. Parting surfaces are strategic. Efficient demolding mechanisms are essential. Cooling systems require optimization. Successful trial results remain crucial. The goal is durability. Efficiency matters. Product quality is very important.
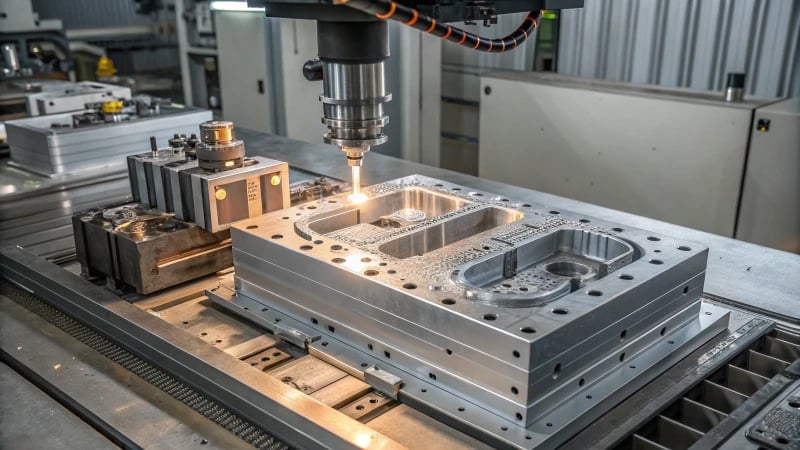
Material Quality and Selection
Choosing the right material is like picking the best tool for work. I often use steels like P20 or H13 for their hardness and toughness. They last long, like a good friend in production. Checking material composition and surface quality early helps catch potential problems. Early detection saves trouble.
Material | Hardness (HRC) | Features |
---|---|---|
P20 Steel | 28-32 | Good toughness, easy machining |
H13 Steel | 48-52 | High strength and toughness |
Inspecting material composition and surface quality helps ensure durability. Techniques like magnetic particle flaw detection can identify potential issues early.
Manufacturing Accuracy
Precision means more than just numbers; it’s like art. Tools such as calipers and laser scanners help achieve exact standards. Tight tolerances within ±0.01mm matter in the end product. Precision truly makes a difference.
Using tools like calipers and laser scanning instruments ensures dimensional and shape accuracy5. Tolerances should be within ±0.01mm for precision molds to guarantee consistent product dimensions.
Parting Surface Design
A well-designed parting surface is like puzzle pieces fitting perfectly. The design should match the largest contour of the product, allowing easy demolding. This is crucial, especially with undercuts.
The surface should align with the product’s largest contour, particularly vital for products with undercuts where the parting surface must work with sliders or inclined ejectors6.
Demolding Mechanism
Picking the right ejection method feels like a trick in engineering. For thin pieces, using a large push plate spreads force and stops warping. Small mistakes here can cause breaks—best to avoid them!
Evaluate if the mechanism distributes force evenly to avoid local ruptures7.
Cooling System Efficiency
The cooling system is the quiet hero of mold design. Cooling channels close to the cavity surface help cool evenly, reducing cycle time significantly—it’s like finding harmony in a machine.
Cooling channels should be near the cavity surface for uniform cooling, typically 8-12 mm in diameter and 15-25 mm from the surface.
Trial Mold Success
Nothing feels better than when a mold works perfectly on its first test—success shows a strong design! Dependable molds keep size and looks consistent across batches; it’s like winning big in mold design.
The success rate of initial trials indicates the rationality of a mold’s design.
Key Metrics
- First Trial Success Rate: High success means strong design.
- Dimensional Accuracy: Steady through many tests.
- Surface Finish: No defects in production cycles.
P20 steel is preferred for its hardness and wear resistance.True
P20 steel is known for good toughness and easy machining.
Cooling channels are typically 5-8 mm in diameter.False
Cooling channels are usually 8-12 mm in diameter for efficiency.
How Can Trial Outcomes Reveal Mold Quality?
The small details of trial outcomes probably show a lot about the quality of injection molds. These details are like reading the first pages of a novel. They really set the tone for the future.
Trial results show the quality of molds by checking the success of the first trial, how the product stays the same over time and how long it lasts. These checks show how precise and efficient the manufacturing and design are.
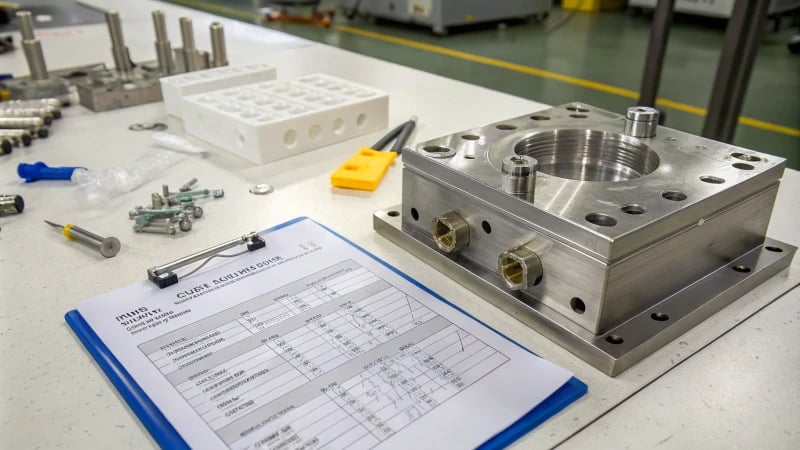
Evaluating First Trial Success
I remember my first major project in mold design. Nervous excitement filled the air as we started the initial trial. This moment shows whether all our work was worth it. When the first batch came out perfectly, it felt like winning a prize. A successful first trial confirms that the time spent on design and production was not wasted. For instance, in car parts, getting the right size and look from the start shows that the mold is very reliable.
Consistency in Quality
Consistency is crucial. One successful batch isn’t enough; keeping that standard over time is essential. Consistent size and smooth finishes without flaws matter. Take electronic shell molding, for example. If each piece has the same wall thickness and perfect finish, the mold is ready for mass production8. It really is ready.
Quality Aspect | Indicator |
---|---|
First Trial Success | Meets strict standards initially |
Product Quality Stability | Consistent across trials |
Mold Wear | Minimal after extensive use |
Long-term Mold Strength
Time and repeated use test a mold. I worked with a mold that was great at first but wore out quickly. This taught me about the need for durability. A strong mold should last through many cycles with little wear. Seeing less than 0.05mm of wear after 100,000 uses shows excellent durability.
Accurate Manufacturing and Smart Design
Precision matters. Tools like calipers help achieve perfect dimensions. I recall learning to maintain cavity size within ±0.01mm – it felt like an art. Not only is precision important, but smart design also counts. Clever cooling designs probably improve how fast and well a mold performs.
Complete Analysis
Considering all these factors offers a clear view of mold quality through trial results. Exploring material make-up, surface condition, and structural design really upgrades mold efficiency and durability.
For those seeking higher mold quality through trials, using industry guidelines is key. These resources reveal methods to optimize the manufacturing process for better outcomes.
First trial success indicates mold quality.True
A successful first trial suggests high standards in design and precision.
Mold wear over 0.05mm is acceptable after 100,000 cycles.False
Good wear resistance is shown by wear under 0.05mm after 100,000 cycles.
What Influences Mold Service Life?
Picture standing in a busy factory. The sound of machines fills the air. Each machine relies on one unsung hero꞉ the mold. Its journey is about precision. Its journey is about endurance.
Mold usage time depends on several things. Material quality really plays a role. Manufacturing accuracy matters too. Design needs to be solid. Successful trials are crucial. Resistance to wear is important. Fatigue strength must not be overlooked. Regular upkeep really matters. Careful handling truly increases lifespan.
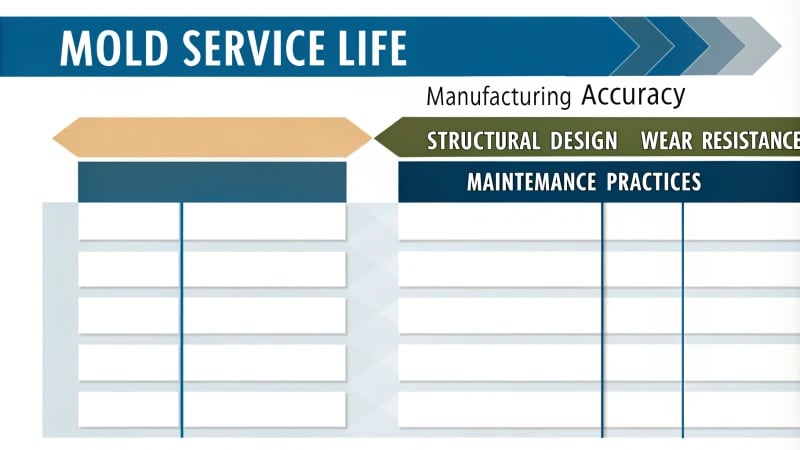
Material Quality
The right mold material9 really affects its durability. Imagine using top-notch mold steels like P20 or H13. These offer not only great hardness and wear resistance but also really good reliability under heat. It’s like picking the right ingredients for your best recipe; without them, the dish fails.
Material | Hardness (HRC) |
---|---|
P20 Steel | 28-32 |
H13 Steel | 48-52 |
When I first saw P20 steel, its perfect surface amazed me – no cracks or pores meant less worry about early breakdowns.
Manufacturing Accuracy
Once, I spent an afternoon with an experienced engineer. A tiny millimeter error could mean mold success or failure. Accuracy in measurements and shapes is very important. Tools like calipers and micrometers are crucial for precision.
For precision molds10, every small size difference counts, with cavity size tolerance ideally within ±0.01mm.
Measurement Tool | Application |
---|---|
Calipers | Dimensional checks |
Micrometers | Precision measurements |
Structural Design
Design involves more than appearance; it deals with usefulness. A smart cooling system or demolding setup makes a big impact. I saw a mold with a brilliant cooling channel design – like observing a master chef, making sure every dish cooks perfectly.
- Cooling Channel Parameters:
- Distance to cavity: 15-25 mm
- Diameter: 8-12 mm
Trial Mold Performance
First trials are crucial. A mold that performs well initially shows its true quality. Watching consistent trial mold products11 is like seeing a talented orchestra, each instrument blending smoothly with the next.
High success rates indicate reliable design and manufacturing processes.
Wear and Fatigue Strength
Checking wear and fatigue strength is like a mold’s regular health exam. If wear stays low after 100,000 cycles (below 0.05mm), the mold shows its strength. It’s comforting to know ejector pins handle millions of movements without failing, showcasing good fatigue strength.
Bringing all these factors together probably gives molds a long, successful life, letting production stay strong with ease. It’s amazing how every part connects, similar to the gears in a very smooth-running machine.
P20 steel has a higher hardness than H13 steel.False
H13 steel has a hardness of 48-52 HRC, higher than P20's 28-32 HRC.
Dimensional accuracy affects mold service life.True
Precision in dimensions ensures correct formation and longevity of molds.
Conclusion
Key indicators for judging injection mold quality include material composition, manufacturing accuracy, structural design, trial success rates, and mold service life.
-
Learn about how specific compositions enhance mold durability and product quality. ↩
-
Discover how precision in mold materials ensures high-quality product dimensions. ↩
-
Learn about the benefits of using high-quality materials like P20 or H13 steel in mold manufacturing. ↩
-
Discover how a well-designed cooling system can enhance efficiency and product quality. ↩
-
Understanding dimensional accuracy’s role ensures precision in final products, highlighting its critical nature in mold design. ↩
-
This link explains how sliders assist in demolding complex shapes, crucial for products with undercuts. ↩
-
Discover various ejection techniques suitable for thin-walled items to prevent deformation during demolding. ↩
-
Understand the requirements for molds suitable for large-scale production. ↩
-
Discover why choosing the right mold material is vital for durability and performance. ↩
-
Learn about essential tools for ensuring precision in mold manufacturing. ↩
-
Explore why initial trial success is crucial for evaluating mold quality. ↩