Have you ever wondered how those perfect plastic flowers come to life?
Injection molding machines create plastic flowers by injecting molten thermoplastic into detailed molds, carefully designed to capture every aspect. Precise mold design, material selection, and accurate operation result in lifelike floral components.
As I dive into the world of mold design, I often recall my first attempt at creating something intricate—a plastic rose. It was fascinating to see how a simple piece of thermoplastic transformed into a work of art, all thanks to the carefully designed molds that captured every vein and petal texture. But it’s not just about the mold; selecting the right thermoplastic is crucial too. I remember experimenting with various materials like polypropylene and ABS, each offering different levels of rigidity and flexibility.
Once the material and mold are ready, the real magic happens. The injection molding machine heats the plastic until it’s molten, then injects it with precision into the mold cavities. Watching those flower parts emerge, ready to be assembled into a complete bloom, is nothing short of mesmerizing. And for those extra special designs, a bit of post-processing—like painting or texturing—can truly elevate the final product, making it look almost as real as nature itself. Every step in this process not only challenges but also inspires me to push the boundaries of what’s possible with injection molding.
Injection molding uses thermosetting plastics for flowers.False
Injection molding typically uses thermoplastics, not thermosetting plastics.
Mold design affects flower detail accuracy.True
The mold design determines how accurately flower details are captured.

How Does Mold Design Shape the Creation of Plastic Flowers?
Have you ever marveled at the lifelike appearance of plastic flowers and wondered what magic goes into crafting them?
Mold design is crucial for crafting realistic, durable plastic flowers by capturing intricate details such as petal veins and leaf textures, ensuring each flower’s authenticity and longevity.
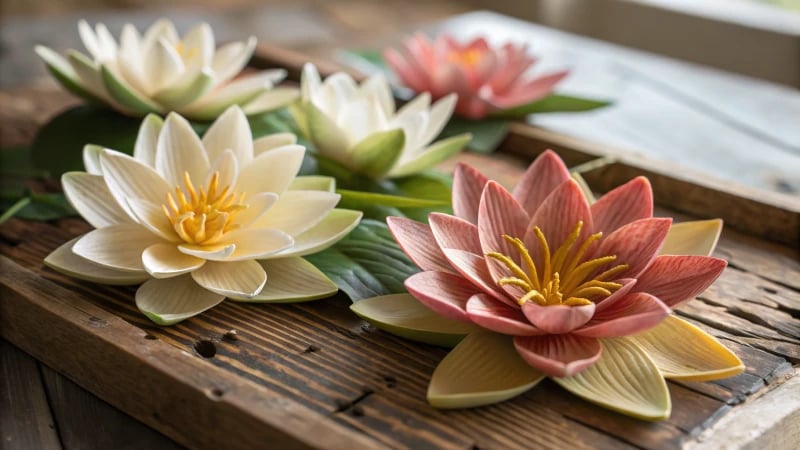
The Art of Mold Design
Let me take you on a journey into the fascinating world of mold design—a craft where creativity meets engineering precision. As someone who has spent years immersed in the nuances of design, I can tell you that crafting plastic flowers is all about capturing nature’s beauty in the finest detail. It’s like painting a masterpiece, where each stroke is a vein on a petal or a texture on a leaf, meticulously crafted with custom-designed molds1.
Key Considerations in Mold Design
I remember the first time I realized the importance of detail orientation in mold design. It was during a project where we had to replicate the intricate veining on rose petals. This required the use of advanced CAD software and a keen eye for detail—skills that I’ve honed over years of designing products that balance beauty and functionality.
-
Detail Orientation: Every mold needs to reflect the delicate intricacies of real flowers, from veins to textures, which is why skilled designers are indispensable.
-
Material Compatibility: Choosing the right material, like polyethylene or ABS, is crucial. These materials need to flow perfectly into the mold cavities to create parts that are as durable as they are beautiful.
Material Characteristics Polyethylene (PE) Flexible, durable, and easy to mold Polypropylene (PP) Stiff, resistant to chemicals ABS Tough, impact-resistant, and aesthetic -
Process Efficiency: Precision and speed are vital in the molding process. The injection molding machine heats the plastic to a liquid state before it’s injected into the molds—a process that must be finely tuned to maintain quality.
Exploring Advanced Techniques
Sometimes, to achieve that lifelike appearance, we go beyond simple molding. I’ve seen firsthand how post-processing techniques like painting or surface detailing can elevate a flower’s aesthetic appeal. Imagine a team of skilled artisans adding color and texture—each stroke bringing the flower closer to its natural counterpart.
But it’s not just about looking good. Mold design also influences how these flowers hold up over time. Choosing appropriate thermoplastic materials2 ensures they are as resilient as they are beautiful.
By delving into these aspects, designers like myself can push boundaries, creating artificial flowers that not only meet functional and aesthetic needs but also inspire innovation in plastic component design3.
Mold design captures intricate petal details in plastic flowers.True
Custom molds are used to replicate delicate petal details accurately.
Polyethylene is unsuitable for molding plastic flowers.False
Polyethylene is flexible, durable, and easy to mold, making it suitable.
Why is choosing the right material for injection molding so important?
Ever stared at a perfectly molded plastic flower and wondered about the magic behind it? It all starts with choosing the right material.
Selecting the right material for injection molding is vital for achieving desired quality, durability, and cost-effectiveness, ensuring essential properties such as strength, flexibility, and aesthetics are met for successful product outcomes.
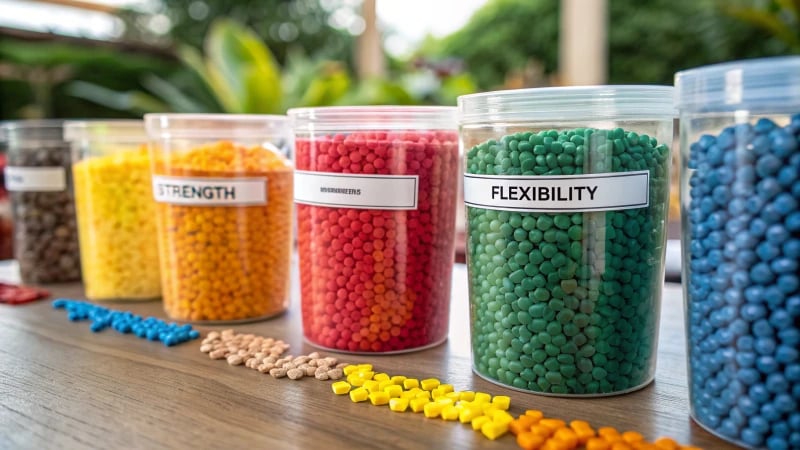
Understanding Material Properties
I’ve always been fascinated by how the right material can make or break a product. Imagine this: I once worked on creating a new line of plastic flowers. The choice of material was pivotal. We needed something with high tensile strength to ensure our flowers wouldn’t wilt under pressure—literally! Selecting a material that could handle heat without losing shape was also crucial since we wanted them to withstand sunny window sills.
The choice of material in injection molding can greatly influence the product’s mechanical properties4. For instance, selecting a material with high tensile strength ensures the product can withstand significant stress without deforming. Likewise, a material with good thermal resistance can prevent product degradation in high-temperature environments.
Compatibility with Mold Design
It was like solving a complex puzzle where every piece mattered. The mold design had to capture the delicate veins and textures of real flowers. That’s why we turned to polyethylene and polypropylene. These materials flowed beautifully into the intricate cavities of our molds, perfectly replicating every petal and leaf detail.
Material selection must align with the mold design to ensure the intricate details are accurately captured. When creating a plastic flower, materials like polyethylene or polypropylene can be excellent choices due to their excellent flow characteristics5. These properties allow the molten plastic to fill complex mold cavities, ensuring detailed flower features are accurately reproduced.
Cost Implications
Balancing the budget was another juggling act. I remember poring over material charts, weighing cost against performance. Here’s a snapshot of what that looked like:
Material | Cost | Strength | Flexibility |
---|---|---|---|
Polyethylene | Low | Medium | High |
ABS | Medium | High | Medium |
Every choice had its trade-offs, and finding that sweet spot between quality and expense was key.
While certain materials offer superior qualities, they may also increase production costs. A balance between cost and performance is essential.
Environmental Considerations
As someone passionate about sustainability, I always push for eco-friendly materials. By opting for recyclable bioplastics, we not only met environmental goals but also tapped into consumer demand for greener products.
Environmental impact is another crucial factor. Using recyclable materials like bioplastics can align production processes with sustainability goals. Exploring eco-friendly options6 not only benefits the environment but also meets consumer demand for sustainable products.
Post-Processing and Finish
Finally, the post-processing phase! Achieving that realistic look often required a bit more work, like painting or adding surface details. Not all materials play well with these processes, so this step was crucial in our decision-making.
Some materials require additional post-processing to achieve the desired finish. For a realistic plastic flower, post-processing steps like painting might be necessary to enhance appearance. This adds another layer of consideration when selecting materials as not all materials respond well to such processes.
In summary, material selection in injection molding isn’t just about picking what works—it’s about crafting something exceptional by balancing all these factors seamlessly.
High tensile strength materials prevent product deformation.True
Materials with high tensile strength withstand significant stress, reducing deformation.
Polyethylene is not suitable for intricate mold designs.False
Polyethylene's excellent flow characteristics suit complex mold cavities.
How Does the Injection Molding Process Operate?
Ever wondered how those incredibly detailed plastic flowers are made? Dive into the intriguing world of injection molding with me.
Injection molding melts thermoplastic material, injects it into a mold, and solidifies it to form shapes like plastic flowers upon cooling and ejection.
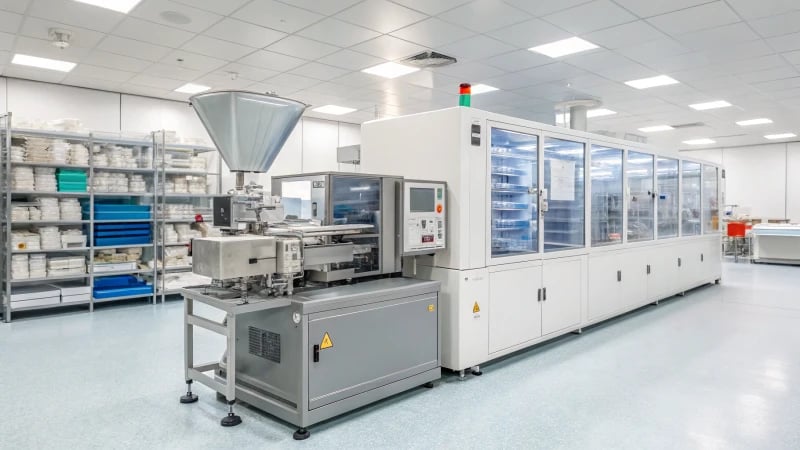
The Basics of Injection Molding
I remember the first time I saw an injection molding machine in action; it was like watching a choreographed dance. This technique involves injecting molten material into a mold to create parts, and it’s usually done with thermoplastics because they can be melted and solidified multiple times without losing quality.
Key Components
-
Injection Molding Machine: A marvel of engineering with parts like the hopper, barrel, screw, and mold. Each plays a pivotal role in shaping products.
-
Mold Design: Custom-designed molds capture intricate details. For example, when making something as delicate as a plastic flower, the mold design must capture every petal vein and leaf texture.
Component | Function |
---|---|
Hopper | Feeds raw plastic into the machine |
Barrel | Heats and melts the plastic |
Screw | Moves melted plastic into the mold |
Mold | Shapes the final product |
Step-by-Step Process
- Material Selection: Picking the right thermoplastic is crucial. I once worked with polyethylene for its flow characteristics, which allowed us to create finely detailed molds for flower parts.
- Heating and Injection: We heated the plastic until it melted, then used a screw to inject it into our custom mold under high pressure.
- Cooling and Ejection: After filling the mold cavities, we waited for it to cool and solidify before opening the mold to reveal our creation.
Applications and Considerations
When I helped design a line of decorative plastic flowers, we had to be meticulous about our material choices and mold designs to avoid defects like warping. Post-processing steps like painting were sometimes necessary to achieve the desired look.
Advanced Techniques
Creating complex designs can be challenging but fascinating. I’ve seen techniques like using multiple molds or adding details post-processing to bring intricate visions to life. For more insights on advanced mold design7, there are countless resources offering guidance on optimizing molds for specific applications.
Injection molding uses only thermoplastics.False
While typically using thermoplastics, injection molding can use other materials.
The screw in the machine moves melted plastic into the mold.True
The screw's function is to push molten plastic from the barrel into the mold.
Where Can You Find Reliable Injection Molding Machines for Flower Production?
Finding the perfect injection molding machine for making plastic flowers feels like searching for a needle in a haystack. But fear not, I’ve been there, and I’m here to guide you through it.
Reliable injection molding machines for flower production can be sourced from reputable manufacturers and distributors specializing in high-quality, precision equipment tailored for intricate designs.
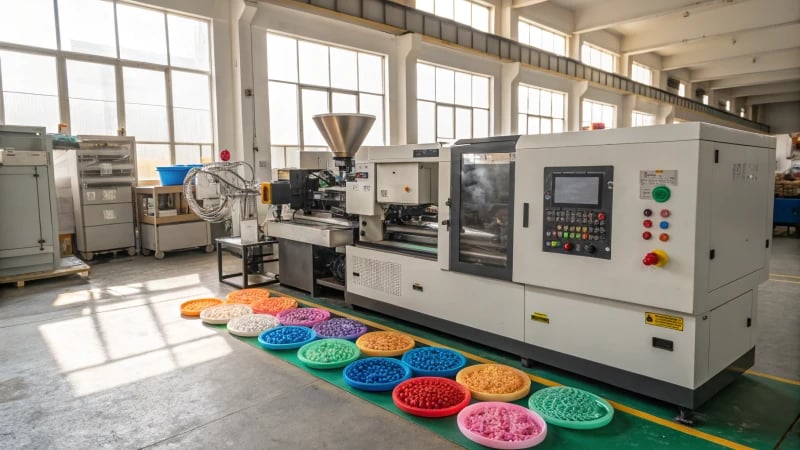
Understanding Injection Molding for Flowers
I remember when I first dove into the world of injection molding for flowers. It was a maze of options and technical jargon. But once I understood the basics, it all started to make sense. Injection molding allows you to create detailed designs, like the delicate veins on a flower petal or the textures of a leaf, using custom-designed molds. This process begins with mold design, where each cavity is crafted to bring your floral vision to life.
Key Manufacturers
When I first started looking into this, ENGEL8 and Arburg9 were the names that kept coming up. They’ve carved out a reputation for creating machinery that can handle the finesse required for flower molds.
Manufacturer | Specialty |
---|---|
ENGEL | High precision, versatile applications |
Arburg | Custom solutions, energy-efficient machines |
What to Consider When Purchasing
- Material Compatibility: In my experience, choosing the right material is crucial. Materials like polyethylene or ABS are often used because they mold well into detailed shapes and hold up nicely.
- Machine Specifications: Equally important are the machine specifications. You want something with excellent pressure and temperature control to ensure every detail of your mold is perfectly captured.
Where to Buy
I found that certified distributors offer not just machines but also much-needed after-sales service10 and support. Websites like Alibaba or ThomasNet are goldmines for finding suppliers globally.
The Role of Technology
Incorporating technology like real-time monitoring and automation has been a game-changer in my production process. It not only boosts efficiency but also helps maintain consistent quality.
Final Tips
Before sealing the deal, I always check customer reviews and the supplier’s delivery track record for reliable delivery11. Aligning your purchase with your production goals and budget is essential to balance quality and cost-effectiveness.
By following these steps, you’re set to find reliable machines that will enhance your flower production capabilities, just as they did for me.
ENGEL specializes in high precision injection molding machines.True
ENGEL is known for producing versatile, high-precision machinery.
Arburg offers energy-efficient machines for flower production.True
Arburg provides custom solutions with a focus on energy efficiency.
Conclusion
Injection molding machines create plastic flowers by injecting molten thermoplastic into custom molds, capturing intricate details and ensuring durability through precise material selection and post-processing techniques.
-
Exploring this link provides insights into how custom molds shape product aesthetics and functionality. ↩
-
Discovering this information helps in selecting materials that ensure durability and realistic aesthetics. ↩
-
Clicking this link uncovers trends and innovations shaping the future of plastic component design. ↩
-
Explores how different material properties affect injection molding outcomes, providing insight into selecting suitable materials. ↩
-
Offers guidance on materials with optimal flow characteristics, crucial for detailed mold designs. ↩
-
Discover sustainable material options for injection molding to align with environmental goals. ↩
-
Explore this link for in-depth guidance on optimizing molds for specific applications, enhancing both functionality and aesthetics. ↩
-
Discover why ENGEL is a leading choice for precision injection molding needs. ↩
-
Explore Arburg’s offerings in custom injection molding solutions. ↩
-
Understand the significance of after-sales services in maintaining machinery efficiency. ↩
-
Find strategies to ensure timely and secure delivery of your equipment. ↩