Let’s dive into the world of injection molds! Optimizing their insulation is key to improving efficiency and quality in manufacturing.
To effectively insulate injection molds, one should use suitable materials like ceramic coatings, insulating paints, or rubber gaskets, combined with proper application techniques and regular maintenance.
While this overview provides a solid foundation, there’s so much more to explore! Understanding specific methods and materials can help you tailor your insulation process to fit your unique needs.
Ceramic coatings are the best for high-temperature mold insulation.True
Ceramic coatings withstand extreme temperatures, offering excellent insulation.
What Are the Best Insulating Materials for Injection Molds?
Choosing the right insulating materials for injection molds is critical for ensuring operational efficiency and longevity. Discover which materials stand out in providing optimal insulation.
Ceramic coatings, insulating paints, and rubber gaskets are the top insulating materials for injection molds. They provide superior thermal resistance, insulation, and flexibility essential for various operational environments.
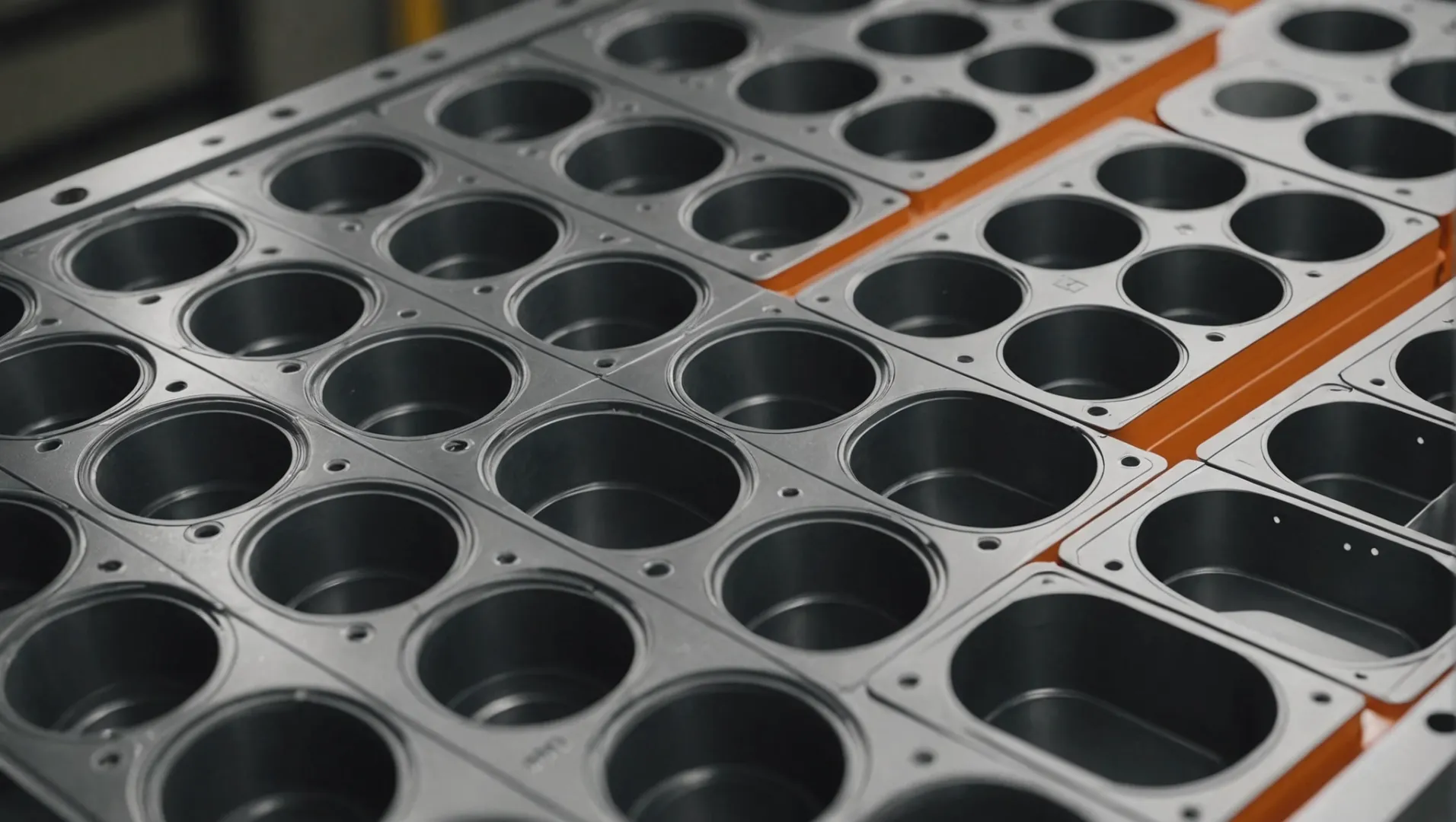
Ceramic Coatings: The High-Temperature Champion
Ceramic coatings are renowned for their ability to withstand extreme temperatures. This makes them particularly effective in high-temperature and high-pressure environments often encountered in injection molding. Beyond temperature resistance, ceramic coatings offer excellent electrical insulation and wear resistance, thereby extending the service life of molds. These properties make them ideal for molds with stringent insulation requirements.
Advantages:
- Exceptional temperature resistance
- High hardness and wear resistance
- Effective electrical insulation
Ideal Uses:
Ceramic coatings are best suited for environments where molds are subjected to severe thermal conditions and electrical insulation is paramount.
Insulating Paints: Versatile and Cost-Effective
Insulating paints offer an affordable and flexible solution for mold insulation. Their ease of application allows them to cover even complex mold shapes effectively. This versatility ensures a comprehensive insulating layer that reduces the risk of current conduction through the mold.
Advantages:
- Easy to apply via spraying or brushing
- Low cost
- Forms a solid insulating film
Ideal Uses:
These paints are particularly effective for complex mold surfaces where uniform coverage is essential. They offer a practical solution for general-purpose insulation needs.
Rubber Gaskets: Flexible and Resilient
Rubber gaskets bring flexibility and resilience to mold insulation. They adapt to various shapes and sizes, providing stable insulation and preventing current leakage. Additionally, their buffering properties help reduce wear and tear on molds during operation.
Advantages:
- Excellent elasticity and flexibility
- Effective current leakage prevention
- Provides cushioning to reduce wear
Ideal Uses:
Rubber gaskets are commonly utilized in movable parts such as sliders and ejectors, where both insulation and mechanical flexibility are required.
Understanding these materials’ specific properties helps manufacturers tailor their approach, ensuring each mold benefits from optimal insulation1 tailored to its unique operational demands.
Ceramic coatings provide excellent electrical insulation.True
Ceramic coatings are known for their effective electrical insulation properties.
Rubber gaskets are unsuitable for movable mold parts.False
Rubber gaskets are ideal for movable parts due to their flexibility.
How to Properly Apply Insulating Materials to Molds?
Applying insulating materials correctly to molds is crucial for maintaining efficiency and durability in manufacturing processes.
Proper application of insulating materials involves choosing the right material, surface preparation, correct application techniques, and ensuring thorough drying and curing.
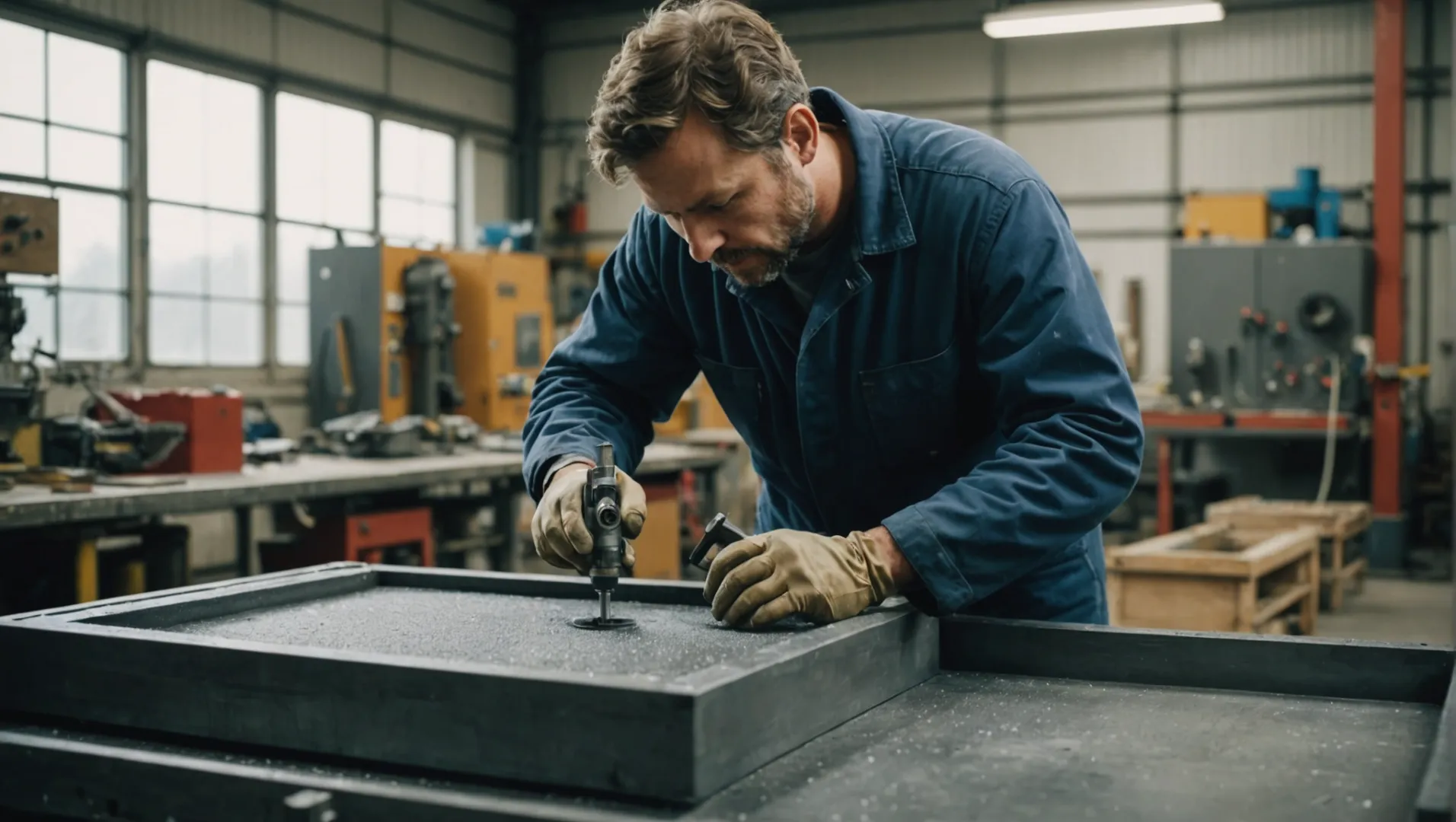
Selecting the Appropriate Insulating Material
Choosing the right insulating material is the foundation of effective mold insulation. Depending on your specific needs and the operating environment, different materials offer various advantages:
-
Ceramic Coating: Perfect for high-temperature environments, ceramic coatings offer superior temperature resistance and insulation, preventing electrical currents from passing through the mold. Their hardness and wear resistance also contribute to prolonging the mold’s lifespan. Consider ceramic coatings for molds used in extreme conditions, where both thermal and electrical insulation are critical.
-
Insulating Paint: This material is user-friendly, often applied through spraying or brushing. Insulating paints dry to form a solid, protective layer that provides comprehensive coverage even on complex mold shapes. Given its cost-effectiveness and ease of application, insulating paint is ideal for molds with intricate designs that demand complete insulation coverage.
-
Rubber Gaskets: Known for their elasticity and adaptability, rubber gaskets are excellent for insulating moving parts of molds such as sliders or ejectors. Their stability in insulation performance and ability to absorb shocks make them indispensable in ensuring the longevity and functionality of these components.
Preparing the Mold Surface
Before applying any insulating material, thorough surface preparation is essential. This process involves:
- Cleaning: Use organic solvents or appropriate cleaning agents to remove oils, dust, and other contaminants from the mold surface.
- Surface Treatment: Techniques like grinding or sandblasting enhance the adhesion properties of the mold surface, ensuring that the insulating material bonds effectively.
Applying Insulating Materials
With the surface ready, proceed with applying the chosen insulating material using methods best suited for each type:
- For ceramic coatings, consider spraying or thermal spraying for even distribution.
- Insulating paints can be applied using a spray gun or brush.
- Rubber gaskets should be precisely cut to size and carefully adhered to the intended areas.
Application Techniques at a Glance:
Material Type | Application Method |
---|---|
Ceramic Coating | Spraying or Thermal Spraying |
Insulating Paint | Spray Gun or Brushing |
Rubber Gasket | Cutting and Adhesion |
Ensuring Proper Drying and Curing
The final step is critical for solidifying the insulation layer:
- Follow the specific drying and curing requirements of the chosen material. Conditions such as temperature and humidity play a crucial role in this phase.
- Allow sufficient time for curing to achieve optimal insulation performance.
By adhering to these guidelines, manufacturers can ensure that their molds are properly insulated, resulting in enhanced operational efficiency and product quality. For further insights into specific insulation techniques2 or maintenance strategies, explore additional resources tailored to your manufacturing needs.
Ceramic coatings prevent electrical currents in molds.True
Ceramic coatings offer superior insulation, preventing electrical currents.
Insulating paint is ideal for high-temperature environments.False
Ceramic coatings, not insulating paint, are ideal for high temperatures.
Why Is Regular Maintenance Crucial for Insulated Molds?
Regular maintenance of insulated molds ensures optimal performance, extending their lifespan and maintaining high-quality production standards.
Regular maintenance of insulated molds is vital for preserving their insulating properties, preventing costly downtime, and ensuring consistent production quality. Without it, molds risk damage from wear, resulting in insulation failure and compromised product integrity.
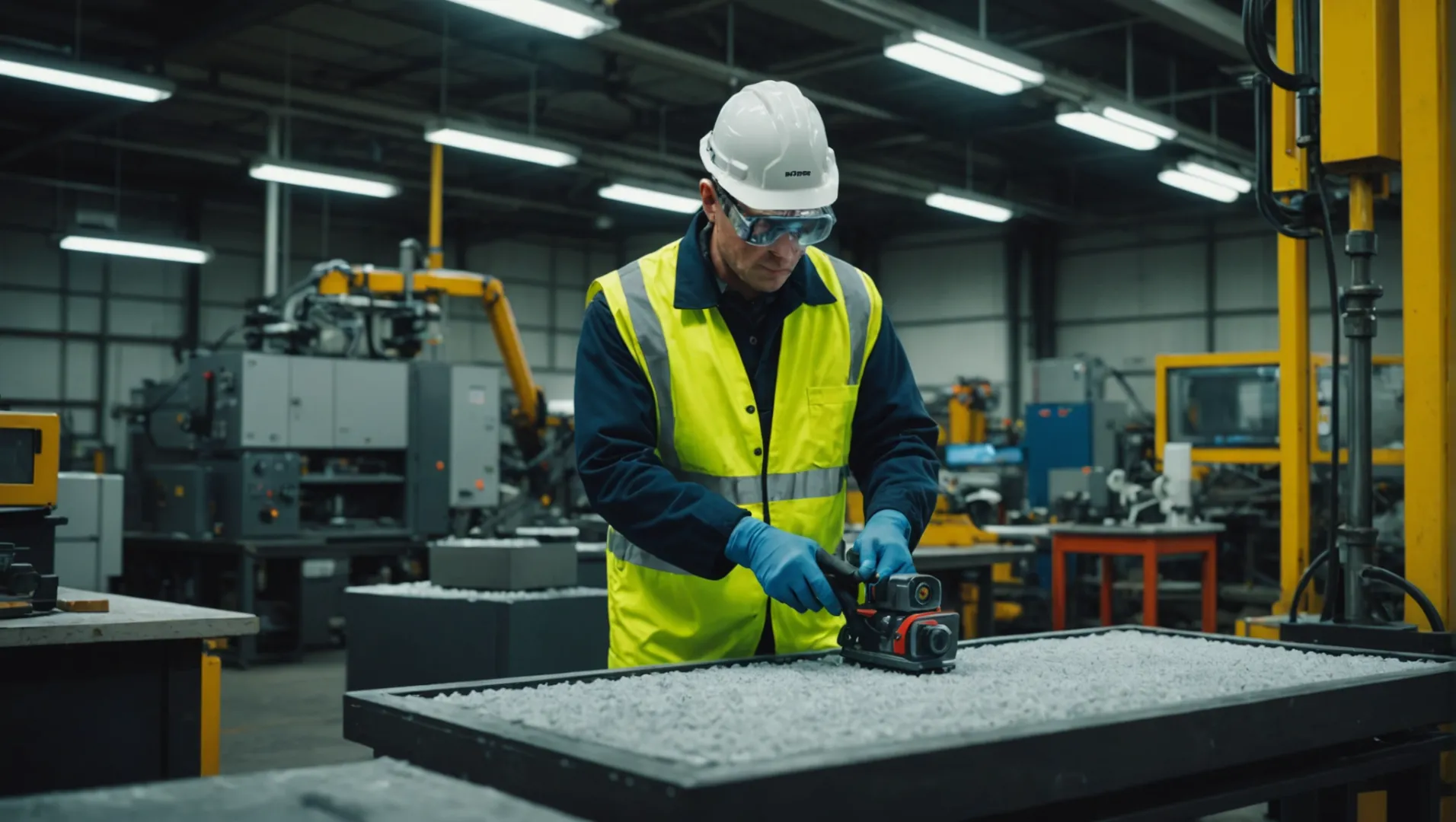
The Role of Regular Inspections
Regular inspections are the backbone of maintenance for insulated molds. By examining the appearance of the insulation layer3, manufacturers can identify signs of wear such as damage, peeling, or cracking. Timely detection allows for immediate repairs, preventing more significant issues that could halt production.
Conducting Insulation Performance Tests
Utilizing specialized testing instruments to evaluate the insulation performance is a critical maintenance step. Conduct these tests periodically to ensure that the insulation retains its effectiveness. If tests indicate a decline in performance, it might signal the need for further maintenance actions4 or material replacements.
Importance of Correct Maintenance Procedures
To preserve the integrity and functionality of insulated molds, it’s crucial to follow precise maintenance procedures. Begin by disconnecting the mold from power sources before inspections or testing, thereby safeguarding against electrical hazards.
- Cleaning: Remove any debris or contaminants that could affect the mold’s surface and insulation.
- Repairs: Address any visible damage immediately to maintain insulation integrity.
- Reapplication of Insulating Materials: Over time, materials like ceramic coatings or insulating paints might require reapplication5 to restore their protective qualities.
Long-Term Benefits of Routine Maintenance
Routine maintenance not only extends the lifespan of molds but also ensures consistent product quality. This proactive approach can prevent unexpected downtimes and expensive repairs, ultimately saving resources and enhancing operational efficiency.
By maintaining a schedule of regular inspections and upkeep, manufacturers ensure that their insulated molds remain in peak condition, supporting continuous production and reducing energy consumption6. Investing in regular maintenance translates into substantial long-term benefits, both in cost savings and in maintaining competitive production standards.
Regular maintenance extends mold lifespan.True
Routine upkeep prevents wear and damage, prolonging mold life.
Skipping maintenance doesn't affect insulation quality.False
Neglect leads to wear and damage, compromising insulation quality.
What Are the Environmental Benefits of Mold Insulation?
Mold insulation not only enhances manufacturing efficiency but also significantly benefits the environment. Discover how optimizing mold insulation contributes to a sustainable future.
Mold insulation reduces energy consumption, minimizes waste, and prolongs mold life, thus decreasing environmental impact. Using efficient insulating materials and methods ensures better thermal management and sustainability in manufacturing processes.
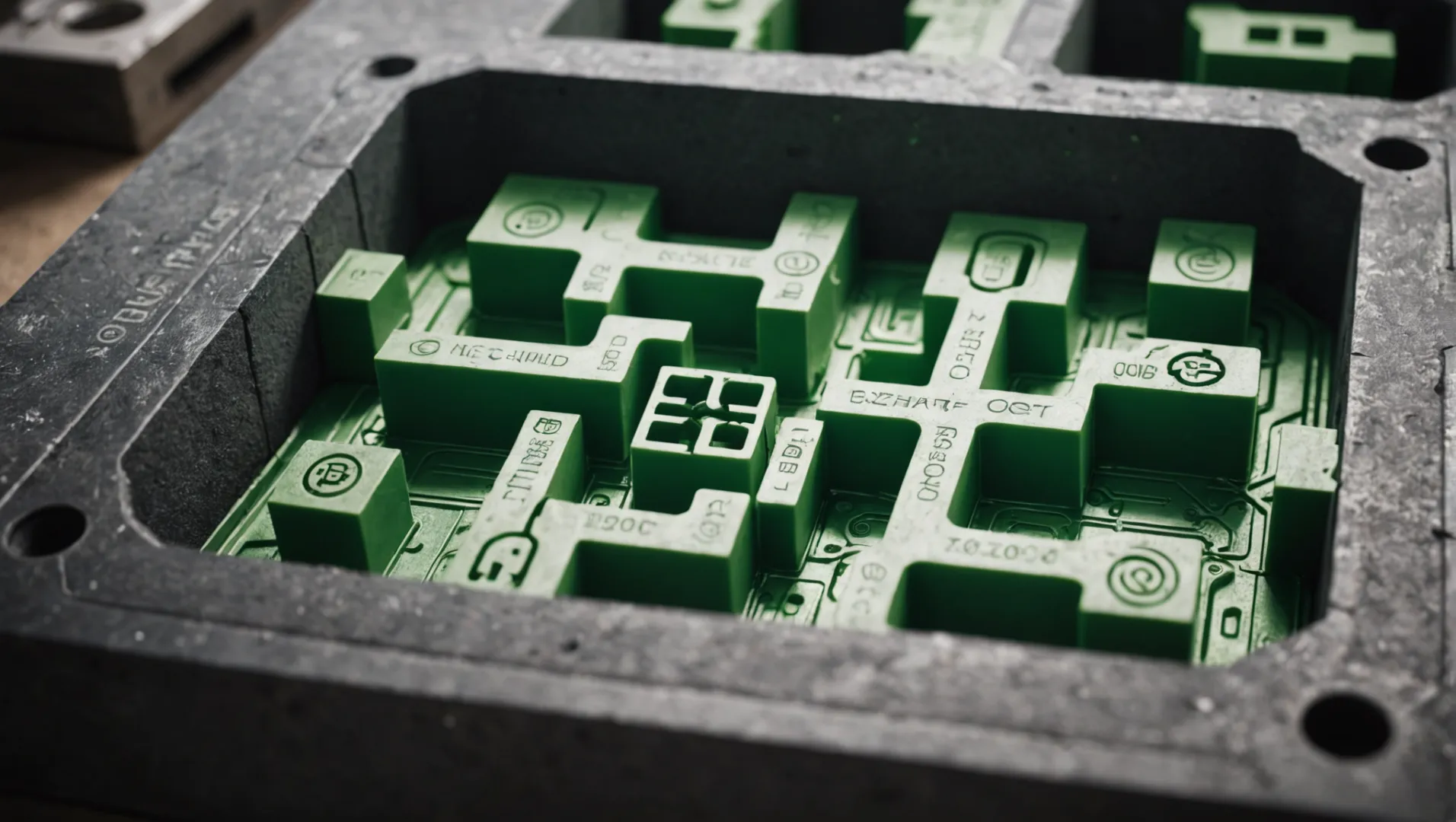
Reduction in Energy Consumption
One of the primary environmental benefits7 of mold insulation is its ability to significantly reduce energy consumption. By maintaining consistent temperatures within the mold, less energy is required to heat or cool the mold during production cycles. This not only leads to cost savings but also decreases the reliance on non-renewable energy sources, thereby reducing the carbon footprint of manufacturing processes.
Minimization of Industrial Waste
Insulating materials such as ceramic coatings and rubber gaskets help prevent mold wear and tear, extending their lifespan. This prolongation means fewer molds need to be produced, leading to less industrial waste. Additionally, when molds are insulated correctly, there is a reduction in defective products which otherwise would have contributed to waste.
Prolonged Mold Life
Proper insulation methods, including surface treatment and regular maintenance, ensure that molds are protected from external damages and chemical reactions. This increases their longevity and reduces the frequency of mold replacements. As a result, fewer raw materials are consumed over time, aligning with sustainable manufacturing practices.
Insulating Material | Energy Efficiency | Waste Reduction | Longevity Impact |
---|---|---|---|
Ceramic Coating | High | Moderate | High |
Insulating Paint | Moderate | High | Moderate |
Rubber Gasket | Moderate | Moderate | High |
Contribution to Sustainable Manufacturing
Implementing mold insulation is a step towards more sustainable manufacturing. By adopting environmentally friendly insulating methods, companies can demonstrate their commitment to reducing ecological impact while still meeting production goals. This approach not only supports regulatory compliance but also enhances corporate responsibility towards a greener planet.
In summary, mold insulation offers numerous environmental benefits by improving energy efficiency, reducing waste, and extending the lifespan of molds. These advantages highlight the role of effective insulation in promoting sustainable industrial practices.
Mold insulation reduces energy consumption by 30%.False
The context states it reduces energy but doesn't specify 30%.
Ceramic coatings improve mold longevity.True
Ceramic coatings are noted to have a high longevity impact.
Conclusion
By choosing the right insulation materials and techniques, you can greatly enhance production efficiency and product quality. Regular maintenance will ensure your molds perform optimally for years to come.
-
Learn how ceramic coatings improve mold efficiency and lifespan.: Choosing the right coatings for injection molds is crucial for extending mold life, improving part quality, and reducing maintenance costs. ↩
-
Explore advanced methods for optimizing mold insulation.: The rubber, plastics and wood panel industries work with heated tooling when material is pressed directly between hot platens. If a platen or … ↩
-
Learn why inspecting mold insulation prevents major production issues.: There are three main reasons we care about insulation in an attic when conducting a mold inspection. First, the insulation is often blocking the soffit venting, … ↩
-
Guides on performing insulation tests to ensure mold efficiency.: There are three commonly used methods for testing insulation resistance: spot reading test, time resistance test, and step voltage test. ↩
-
Find out when mold insulation needs reapplication for best results.: Mold growth on insulation is predominately caused by moisture buildup. When insulation becomes wet, it causes mold to survive on it. ↩
-
Explore how routine mold maintenance can save costs and improve efficiency.: The benefits they offer are multi-faceted, encompassing early detection, health protection, property preservation, legal compliance, and the immeasurable gift … ↩
-
Explore deeper insights into energy-saving benefits of mold insulation.: Insulation can help to maintain indoor temperature conditions which can help to control factors leading to mold growth so not having it where it counts can be … ↩