Do you sometimes feel puzzled when calculating injection mold cooling time? You are not alone.
I discovered that figuring out the cooling time for an injection mold needs different methods. These methods include calculations using heat conduction equations. Empirical formulas help, too. Other ways are trial molds and mold flow analysis software. Each method has its own advantages and drawbacks. They offer customized solutions for various production needs.
When I started with injection molds, it felt like solving a puzzle. Understanding each method helps choose the best for my projects. Let me explain how I tried different techniques for better manufacturing.
Theoretical Calculations: At first, these seemed complex with many heat equations. But once I learned the basics, it was clear. Different plastics, like polystyrene and polypropylene, have unique cooling times. They vary because of thermal properties.
Empirical Formulas: I often use empirical formulas for fast estimates. It’s like a shortcut. Picking the right numbers is very important for being correct. With polycarbonate, changing a number based on experience helped greatly.
Preliminary Trial Molds: Testing trial molds showed me how helpful experiments are. Adjusting cooling times felt like a dance. Watching product quality change until it all fit was rewarding.
Mold Flow Analysis Software: Lastly, I used mold flow software for precise needs. This software suggests cooling times close to what happens in real life. But, these suggestions still must be checked in actual production.
Each step helps me get closer to mastering injection molding. Finding the perfect balance is truly satisfying. It’s like completing a puzzle.
Fourier's law calculates mold cooling time.True
Fourier's law is used in theoretical calculations for mold cooling time.
Empirical formulas are always more accurate than simulations.False
Simulations often provide more accurate cooling times by considering detailed mold and flow factors.
How Do You Calculate Cooling Time Using Theoretical Methods?
Do you ever think about how engineers find the best cooling time in injection molding?
The method to estimate cooling time uses the principles of heat movement. It considers plastic density, volume, specific heat capacity and thermal properties. The formula, t = (ρVcp△T)/(hA△Tm), calculates cooling time under perfect conditions. This guides precise temperature control in manufacturing. The method is based on Fourier’s law.
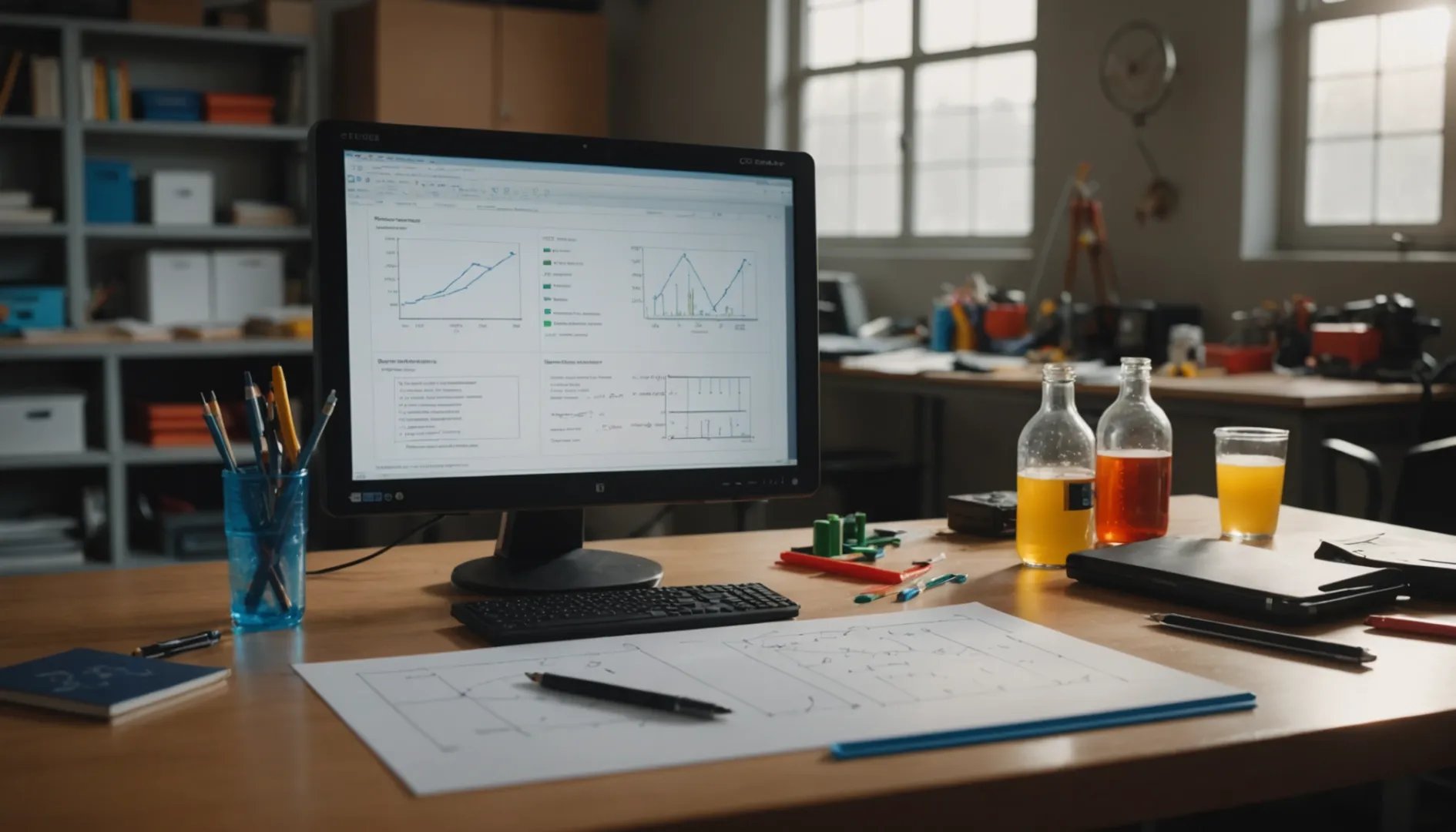
Understanding Fourier’s Law for Cooling Time
Fourier’s law of heat conduction forms the backbone of the theoretical calculation method for cooling time. This approach primarily calculates the heat transfer process of the plastic melt within a mold cavity. The formula is expressed as t = (ρVcp△T)/(hA△Tm), where each parameter represents critical physical characteristics of the material and process.
Here, t denotes the cooling time, crucial for ensuring the product achieves its intended form without defects. The density ρ, volume V, and specific heat capacity cp of the plastic are pivotal because they determine how quickly heat dissipates from the plastic melt. This is why understanding thermal properties1 is essential in molding applications.
Effects of Plastic Properties
Plastics cool in their own unique ways. If you use polystyrene (PS) and polypropylene (PP) for similar items, you see that they do not cool the same. Their thermal diffusivity is different. In my early experiments, I was amazed by how small differences changed cooling times. Correctly using these values in the formula improves your cooling time estimation2.
For example, materials like PS may cool faster than PP under identical conditions due to these inherent differences.
Combining Theory with Practice
Theoretical calculations are helpful but not complete. In my early work, I saw how factors like melt flow dynamics and mold design intricacies change results. That’s why combining real-world tests with theory gives better predictions.
By exploring tools such as mold flow analysis software3, engineers can simulate various scenarios to anticipate potential deviations and refine their calculations accordingly. This ensures that the cooling process aligns closely with actual production needs, reducing waste and improving efficiency.
Cooling time depends on plastic's thermal diffusivity.True
Thermal diffusivity affects how quickly heat is conducted through the plastic.
Empirical formulas for cooling time are always accurate.False
Accuracy depends on selecting appropriate empirical coefficients for materials.
How Do Empirical Formulas Estimate Cooling Times?
Have you ever thought about how manufacturers figure out the cooling time for materials?
Empirical formulas use simple equations to guess cooling times. They come from old data. The formulas look at the material’s type and thickness for fast results. These formulas are very useful. However, they are not very exact. They work best for rough guesses rather than precise forecasts.
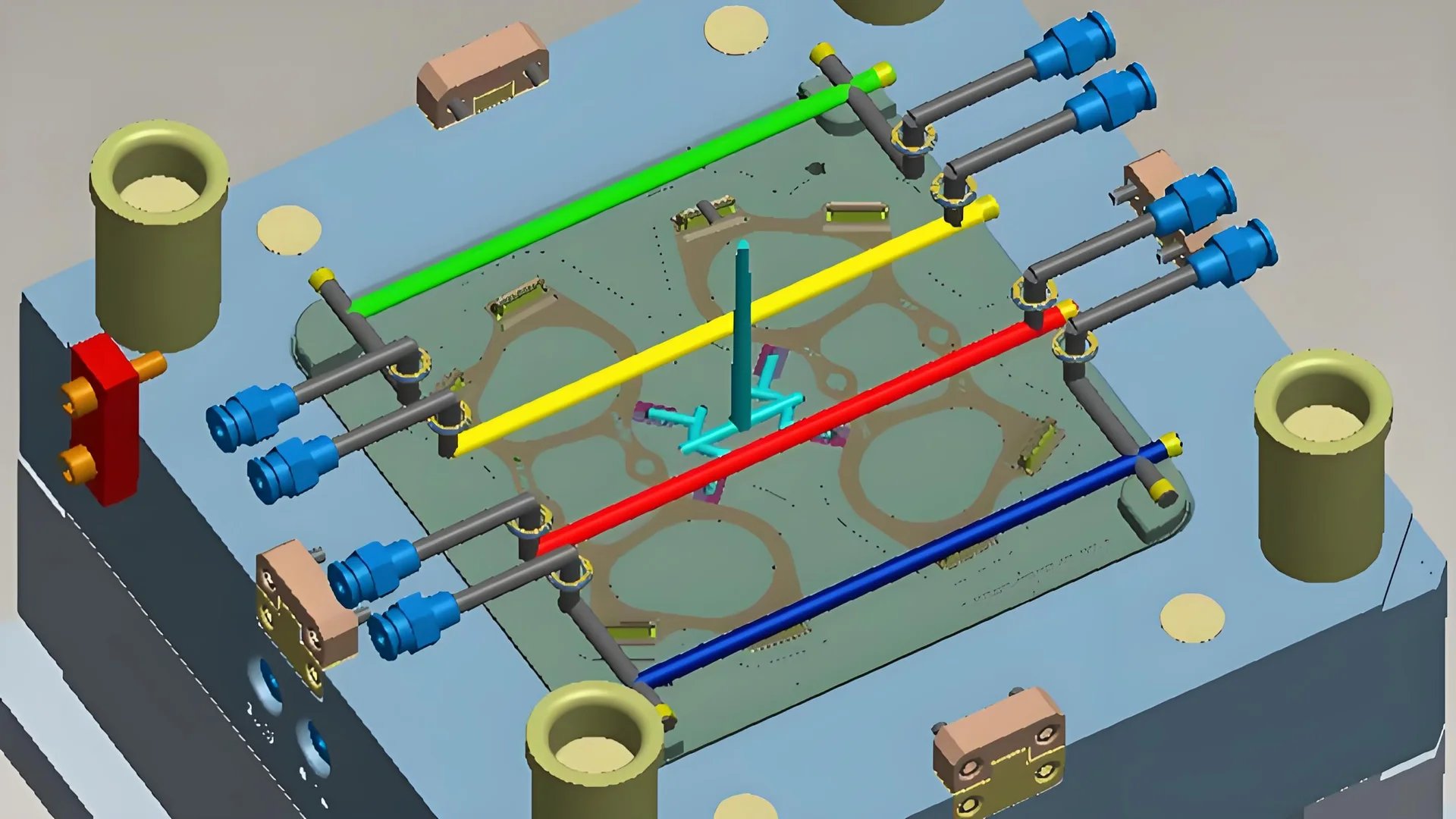
The Role of Empirical Formulas
Empirical formulas play a pivotal role in estimating cooling times by leveraging historical data and patterns from past manufacturing processes. They provide a streamlined approach, especially when precise measurements aren’t feasible. One common formula used is t = C× S², where t represents the cooling time, S stands for the average wall thickness of the plastic product, and C is a material-specific coefficient. For instance, polycarbonate might have a C value ranging from 1.5 to 2.0.
Understanding Material Specificity
Different materials exhibit unique thermal behaviors, which significantly impact cooling times. For example, plastics with higher thermal diffusivity tend to cool faster than those with lower values. Therefore, the empirical coefficient C must be carefully chosen based on the material’s properties. For instance, polystyrene and polypropylene might require different coefficients due to their varying thermal diffusivity4 characteristics.
Tailored Formulas for Specific Products
In some cases, empirical formulas are further refined to cater to specific types of injection-molded products. For example, thin-walled container products may have formulas that incorporate parameters such as diameter alongside wall thickness. These tailored formulas are derived from extensive production experience and provide more accurate estimates for similar products, thereby enhancing manufacturing efficiency5.
Limitations of Empirical Approaches
Despite their convenience, empirical formulas are not without limitations. They often rely on generalized assumptions and may not account for complex interactions in the molding process, such as melt flow or mold structure intricacies. This makes them more suitable for preliminary estimates rather than precise predictions. In practice, empirical methods are often complemented by theoretical calculations6 or simulation software to achieve better accuracy in estimating cooling times.
Theoretical Calculation Method
Theoretical methods delve deeper into scientific principles to calculate heat transfer using Fourier’s law. These methods involve complex equations that consider factors like density and specific heat capacity to provide accurate results.
Preliminary Trial Mold Method
When starting with a new mold design, initial trials set conservative cooling times while closely observing product quality outcomes. Adjustments based on these observations help find an optimal balance between quality and efficiency.
Using Mold Flow Analysis Software
Modern technology enhances our ability to predict cooling processes through mold flow analysis software that simulates real-world conditions considering mold structure and melt flow dynamics.
Cooling time is determined by Fourier's law.True
Fourier's law calculates cooling time using heat conduction equations.
Empirical formulas are more accurate than theoretical methods.False
Empirical formulas are simpler but less precise than detailed simulations.
Why is the Preliminary Trial Mold Method Essential?
Have you ever thought about why early trial molds really change the game in manufacturing? I want to share the amazing reasons why this step is so important.
Preliminary trial mold methods are crucial for adjusting cooling times in injection molding. These methods improve product quality before large-scale production. Testing molds in different situations helps find the best settings. This process lowers defects. Manufacturing becomes very efficient.
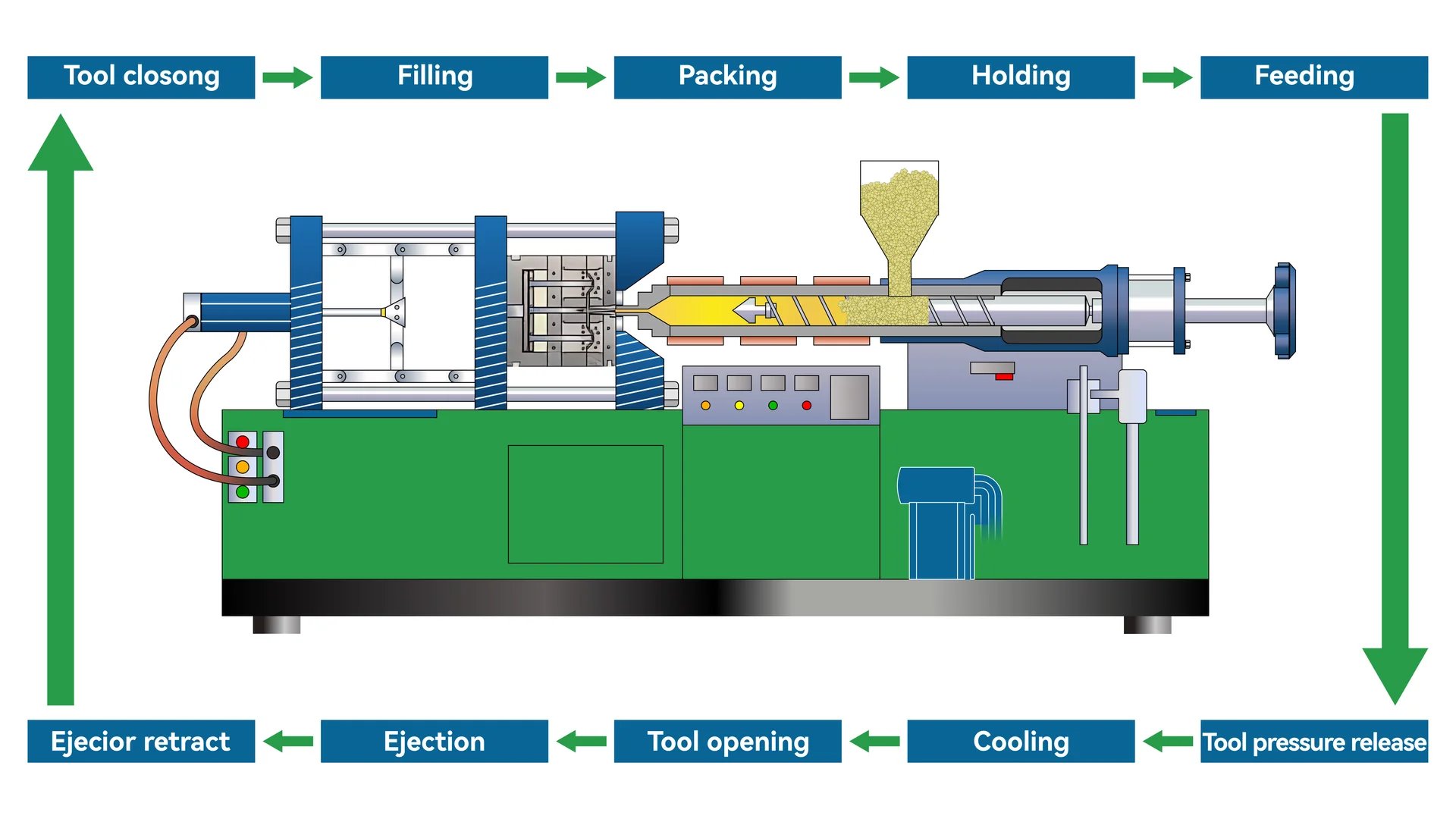
Understanding the Preliminary Trial Mold Method
The preliminary trial mold method plays a pivotal role in the world of injection molding by allowing manufacturers to test their molds before proceeding to full-scale production. This method provides an opportunity to evaluate product quality7 under various cooling times, ensuring that each item is properly cooled and cured without defects.
I remember a key moment in my career when I faced the preliminary trial mold method for the first time. My project struggled—it hit a problem. The products changed shape after being removed from molds. It was very frustrating. The preliminary trial mold method was my solution. By testing molds first, we adjusted things until they worked well. This testing allowed us to try different cooling times, ensuring every product was cooled correctly and had no defects.
During the initial trial phase, manufacturers often start with a conservative cooling time, approximately 1.5 to 2 times longer than what theoretical or empirical calculations might suggest. By doing so, they can assess whether the product cools completely and maintains its intended shape post-demolding. For instance, if there’s noticeable deformation, it signals that adjustments in cooling time are necessary.
Fine-Tuning Cooling Times
One of the main benefits of the preliminary trial mold is the ability to gradually refine cooling times. After observing the initial trial results, adjustments are made incrementally. For example, if a product exhibits slight deformation, increasing the cooling duration might resolve this issue. This iterative process continues until achieving a balance between minimal cooling time and high-quality product output.
This method complements both theoretical calculations and empirical formulas8. The theoretical approach, grounded in Fourier’s law of heat conduction, considers plastic properties such as density and thermal diffusivity. Meanwhile, empirical formulas provide a simpler estimation based on material coefficients; however, these calculations are often just starting points due to the complexities of the injection molding process.
Enhancing Efficiency with Mold Flow Analysis Software
To further optimize the process, mold flow analysis software simulates the cooling process and provides more accurate suggestions for cooling times. By inputting parameters like plastic properties and mold structure into this software, manufacturers gain insights that account for real-world variables such as cooling channel layouts and plastic melt flows.
Although these software recommendations are highly accurate, they still require validation through actual production trials to ensure that any theoretical assumptions align with practical manufacturing conditions. By integrating software analysis with preliminary trial molds, manufacturers can significantly enhance their production efficiency while maintaining high standards of product quality.
Through a combination of these methodologies—the preliminary trial mold method remains essential in refining manufacturing processes and ensuring successful outcomes in injection molding projects.
Theoretical method uses Fourier's law for cooling time.True
Fourier's law is used to calculate heat transfer in the theoretical method.
Empirical formulas are more accurate than simulations.False
Simulations account for mold structure and flow, offering more accuracy.
How Does Mold Flow Analysis Software Enhance Accuracy?
I never imagined feeling so interested in mold flow analysis software. Yet, here we are. This tool seems crucial for exact injection molding tasks. It helps a lot.
Mold flow analysis software improves accuracy in injection molding. It simulates how plastic melts flow and cools. This software studies mold structure and material properties. It gives precise suggestions on cooling times. This approach cuts down on trial and error. Mold design gets better and product quality rises.
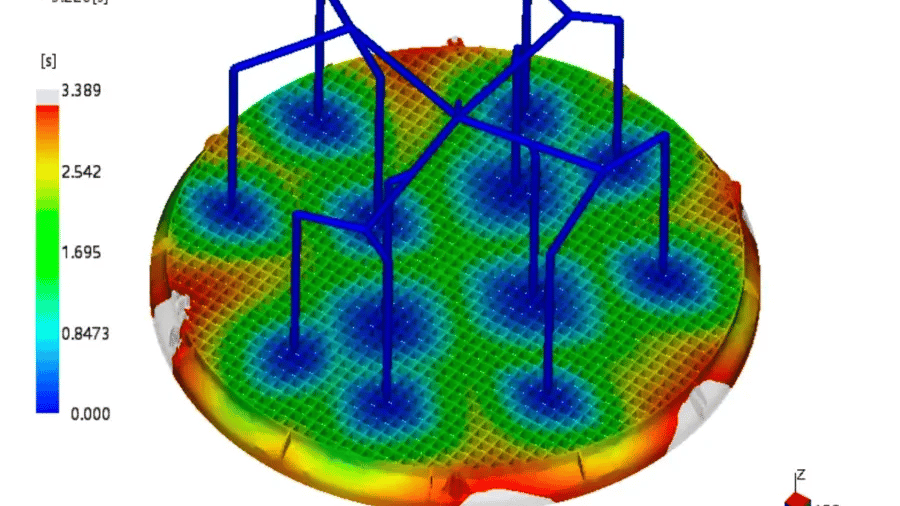
Simulation of Cooling Process
I remember the first time I used mold flow analysis software. It was like opening a new world. This tool shows how plastic melts cool down, like a futuristic movie playing in real-time. By inputting a 3D model of the product, the plastic material’s properties, and mold specifications into the software, engineers can visualize how everything flows and cools. This process involves setting various parameters such as cooling medium temperature and flow rate. The software then performs complex calculations to predict the behavior of the plastic melt, offering a realistic simulation of the actual molding process. During college, I guessed these values; now I saw potential problems before they were expensive mistakes.
Improved Cooling Time Predictions
In the past, I used theories and formulas and often felt like guessing. But mold flow software changed that by providing accurate predictions of cooling time crucial for optimizing production cycles in injection molding. Traditional methods rely on theoretical calculations based on Fourier’s law of heat conduction or empirical formulas that may not fully account for mold complexity or variations in material properties. Mold flow analysis software provides a more precise alternative by simulating heat transfer within the mold. It takes into account factors such as mold design and cooling channel layout9, offering cooling time suggestions that are more aligned with real-world conditions. These suggestions help reduce unnecessary trial and error, ensuring that products meet quality standards without extended production times.
Consideration of Material Properties
Each new plastic is like meeting a new character; different plastics exhibit unique thermal properties impacting how they cool and solidify. For example, materials like polystyrene (PS) cool faster than polypropylene (PP). Understanding this is crucial as it affects their thermal diffusivity rates. Mold flow analysis software allows specific material data input such as density, specific heat capacity, and thermal diffusivity settings to tailor simulations accurately to reflect how a particular material will behave during molding. This precision helps in selecting materials confidently, potentially reducing waste and improving product quality.
Optimization through Simulation
Mold flow analysis is not a one-time thing; it enables iterative testing where engineers can experiment with different designs or settings before starting production virtually before actual production begins. Changing mold structure10 or trying various cooling strategies is possible to enhance product outcomes without incurring additional costs or delays during physical trials. The insights gained from these simulations lead to creative ideas making products more durable and aesthetically pleasing.
Overall, mold flow analysis software represents my trusty partner—a powerful tool in modern manufacturing—allowing better decision-making based on detailed simulations of the injection molding process while streamlining production with high-quality output.
Mold flow analysis software offers more accurate cooling time.True
It considers mold structure and plastic flow, enhancing accuracy.
Theoretical calculations are more accurate than simulations.False
Simulations account for real-world complexities, improving accuracy.
Conclusion
This article explores methods for determining cooling time in injection molding, including theoretical calculations, empirical formulas, preliminary trial molds, and mold flow analysis software.
-
Explore various plastics’ thermal behaviors crucial for molding processes. ↩
-
Learn to apply thermal diffusivity in calculating cooling time. ↩
-
Understand how this software aids in precise cooling time prediction. ↩
-
Learn how thermal diffusivity affects material cooling rates. ↩
-
Discover how tailored formulas enhance production speed. ↩
-
Explore detailed calculations for precise cooling time predictions. ↩
-
Understand how product quality impacts manufacturing success. ↩
-
Discover how empirical formulas guide cooling time estimations. ↩
-
Learn how cooling channel design influences mold efficiency and product quality. ↩
-
Understand how mold structure impacts injection molding outcomes. ↩