Navigating the RoHS compliance maze in injection molding feels like solving a complex puzzle with ever-changing pieces.
The RoHS Directive bans hazardous substances in injection molding, prompting a shift to safer materials, fostering innovation, and affecting production costs.
Remember when we used to rely on traditional materials without a second thought? The RoHS Directive has turned those days upside down, pushing us to rethink every step of our material choices. For me, it’s been like adapting to a new language in design—challenging but rewarding. Suddenly, those trusty pigments and stabilizers we’ve counted on for years are off the table, nudging us towards greener, often more expensive alternatives. It’s not just about compliance; it’s about crafting a sustainable future.
The shift has also sparked an unexpected wave of innovation. Companies are racing to create eco-friendly materials like bio-based plastics, which not only meet stringent standards but often bring surprising benefits in performance and flexibility. But let’s be honest, this transformation isn’t without its headaches. Testing costs have climbed as we ensure every product ticks all the right boxes, and managing supply chains has become more intricate than ever.
Yet, in the midst of these hurdles, there’s a silver lining. Products that align with RoHS standards don’t just stay clear of regulatory issues—they carve out a ‘green’ advantage in the market. I’ve seen firsthand how consumer preferences lean towards environmentally conscious products, boosting brand image and competitiveness. Embracing these changes is our ticket to thriving in a world that’s increasingly prioritizing sustainability.
RoHS Directive bans all heavy metals in injection molding.False
RoHS restricts, but does not ban all heavy metals. It limits specific ones.
RoHS compliance affects material costs in injection molding.True
Compliant materials often cost more due to restrictions on hazardous substances.
How does RoHS impact injection molding materials?
Ever wondered how the RoHS Directive reshapes injection molding? It’s all about cutting out hazardous substances, which impacts everything from design to cost and sparks innovation.
RoHS impacts injection molding by restricting hazardous substances, prompting changes in material selection, cost hikes, and encouraging eco-friendly innovations.
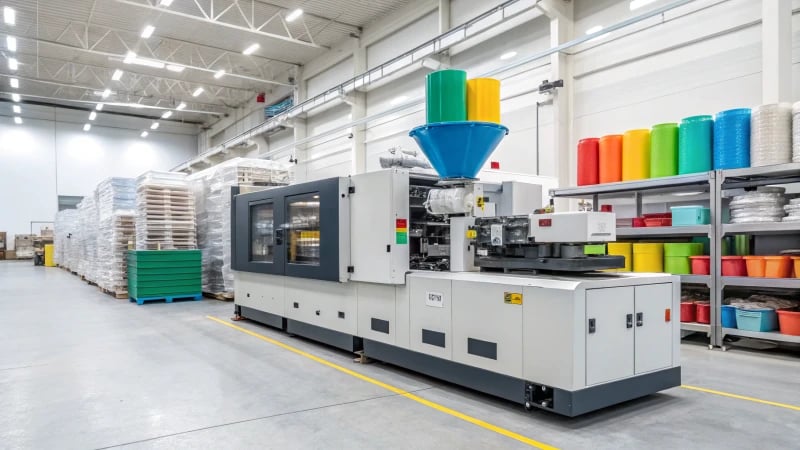
Material Composition Restrictions
I remember when the RoHS Directive1 first came into play, and it felt like a tidal wave hit the manufacturing world. Suddenly, we had to rethink our entire material strategy for injection molding. Heavy metals like lead, mercury, and cadmium were now off-limits, which meant hunting down lead-free pigments and cadmium-free stabilizers. I must admit, it wasn’t easy on the wallet at first, as these alternatives definitely spiked costs. But the silver lining? It pushed us towards cleaner, safer materials, which was a win for everyone.
Restricted Substance | Common Use | Alternatives |
---|---|---|
Lead | Pigments | Lead-free pigments |
Cadmium | Stabilizers | Cadmium-free stabilizers |
Brominated Flame Retardants | Electrical equipment housings | Non-halogenated flame retardants |
Range of Material Options
The transition wasn’t without its hiccups. With RoHS compliance, our go-to materials were suddenly out of the picture, which meant delving into new territory with bio-based and degradable plastics. I recall a project where we explored these alternatives; it was like opening Pandora’s box of possibilities! These greener options not only met environmental standards but often offered better performance than their predecessors. These innovations are gaining traction as they align with green manufacturing trends2.
Quality Control Challenges
Ensuring everything was up to snuff with RoHS standards was another story. We had to ramp up testing on raw materials and finished products. This meant investing in new testing equipment and training—adding a whole layer of complexity and cost. I found myself constantly checking in with suppliers to make sure our supply chain stayed compliant. Let me tell you, it was a balancing act keeping everything in line while not breaking the bank.
Maintaining a compliant supply chain is essential, which involves auditing suppliers and creating a robust traceability system. This complexity can increase supply chain management costs3.
Impact on Production Costs
It’s no secret that going green comes with a price tag. RoHS-compliant materials were pricier than the old ones, which hit our production costs hard. We had to tweak our processes to accommodate these new materials since they behaved differently during molding due to differences in fluidity or molding shrinkage.
Market Competitiveness
Navigating these challenges wasn’t just about staying within the law—it was about gaining a competitive edge too. In markets like the EU, being RoHS-compliant wasn’t optional; it was necessary to avoid export restrictions. Plus, positioning ourselves as eco-friendly helped us tap into the green consumer market by adopting sustainable practices4. Ultimately, embracing these changes has been a game-changer for us in staying ahead in the competitive landscape.
RoHS bans lead in injection molding pigments.True
RoHS restricts hazardous substances like lead, requiring safer alternatives.
RoHS compliance reduces production costs in injection molding.False
RoHS increases costs due to pricier materials and compliance testing.
What Are the Challenges of Ensuring RoHS Compliance?
Trying to navigate RoHS compliance is like untangling a ball of yarn while juggling flaming swords—tricky and demanding!
Ensuring RoHS compliance involves managing restricted materials, navigating complex supply chains, facing higher costs, and staying updated with changing regulations, requiring careful planning and R&D investment.
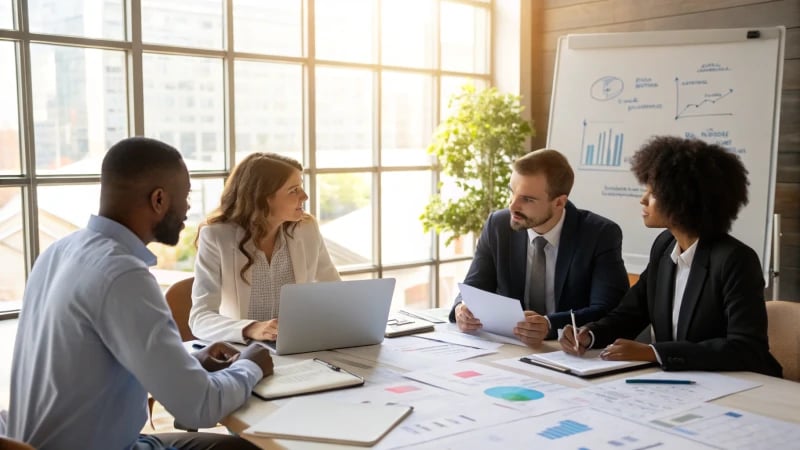
Material Composition Restrictions
I remember the first time I had to deal with the RoHS Directive; it felt like my usual toolkit was suddenly off-limits. The directive’s restrictions on heavy metals like lead and cadmium meant that I had to find new pigments and stabilizers. It wasn’t just about replacing materials; it was about maintaining the quality and performance we were known for. I found myself diving into research, searching for alternatives that wouldn’t compromise our standards. And let’s not forget the brominated flame retardants, which needed replacing with phosphorus-based options—each switch felt like stepping into uncharted territory, impacting both costs and production methods.
Substance | Traditional Usage | RoHS Restriction |
---|---|---|
Lead | Pigments | Prohibited |
Cadmium | Stabilizers | Prohibited |
PBB/PBDE | Flame Retardants | Limited |
Supply Chain Management
Ensuring every part of our supply chain met RoHS standards was like piecing together a massive puzzle. I had to set up rigorous auditing systems5 to trace every component back to its source. This meant a lot of late nights poring over supplier reports and data sheets. It was a daunting task, but knowing we were avoiding potential compliance issues—and hefty fines—was worth every sleepless night.
Increased Testing Costs
Testing for compliance wasn’t just a checkbox on a to-do list—it was an entire operation. Investing in the right equipment, training staff, and scheduling regular tests all added up. But each test reassured me that we were on the right track, preventing any nasty surprises down the line.
Market Competitiveness
Complying with RoHS opened up new market opportunities for us, giving our products a "green advantage." However, non-compliance could result in export restrictions that might tarnish our reputation and shrink our market presence.
Production Cost Fluctuations
Switching to compliant materials sometimes felt like trading my trusty old tools for new ones I wasn’t familiar with. The new materials often came with higher costs and altered production dynamics. This required us to rethink our processes entirely, aiming to balance efficiency with compliance.
Factor | Impact |
---|---|
Alternative Material Cost | Increased production |
Production Efficiency | Potential decrease |
Understanding these challenges isn’t just about keeping up with regulations; it’s about maintaining the quality and reliability our customers expect while navigating this ever-evolving landscape. It’s a continuous learning curve but one that’s crucial for staying ahead in the game.
RoHS compliance increases material costs.True
Switching to alternative materials often results in higher costs.
Non-compliance with RoHS has no market impact.False
Non-compliance can lead to export restrictions and affect reputation.
How Do RoHS Directives Influence Production Costs?
Navigating the maze of RoHS directives can feel like a financial jigsaw for manufacturers. But understanding its impact on production costs is key to staying competitive and compliant.
RoHS directives impact production costs by necessitating material substitutions, rigorous compliance testing, and stringent supply chain management, resulting in increased expenses.
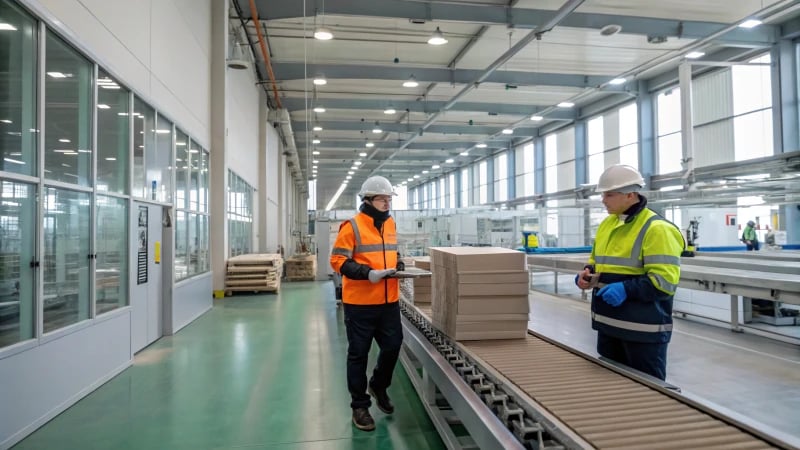
Material Restrictions and Alternatives
I remember the first time I had to deal with RoHS compliance—it felt like diving into the deep end without floaties. The directive enforces tight controls on harmful substances like lead and mercury, which sent me scrambling to find lead-free pigments and cadmium-free stabilizers. Sure, they are better for the environment, but boy, did it come with a price tag! The research and development needed to find these alternatives put a noticeable dent in our budget.
Traditional Material | Alternative | Cost Implication |
---|---|---|
Lead-based Pigments | Lead-free Pigments | Increased R&D Costs |
Cadmium Stabilizers | Cadmium-free Stabilizers | Higher Material Costs |
Impact on Material Options
Imagine you’re all set for a big project only to find out half your materials are off-limits! That’s what RoHS did to us. Suddenly, our choices for injection molding were drastically limited. We had to rely heavily on suppliers innovating compliant materials like bio-based plastics. It’s a bit like waiting for your favorite band to drop their new album—not always fast enough, but worth it in the end.
Promoting material innovation6 is crucial, pushing us towards materials with better environmental benefits.
Quality Control Challenges
Quality control under RoHS is no walk in the park. It involves extensive testing of both raw materials and finished products. I remember having to justify every penny spent on testing equipment and personnel training to my boss. Enhancing supply chain audits for compliance added another layer of complexity—and cost—to our operations.
Production Efficiency Concerns
Switching to alternative materials felt like trading in a trusty old car for a new model with quirks we had to figure out as we went. Differences in properties like fluidity and molding shrinkage meant adjusting processes, which initially slowed down production efficiency, leading to increased costs.
Market Competitiveness Factors
Despite the hurdles, complying with RoHS gave us a leg up in market competitiveness. Our eco-friendly products resonated with environmentally conscious consumers and improved our brand image. Embracing these green advantages7 can be a game-changer in the global market, turning compliance from a chore into a chance to shine.
RoHS increases production costs due to material restrictions.True
Complying with RoHS requires using alternative materials, raising costs.
RoHS directives do not affect market competitiveness.False
RoHS compliance enhances market competitiveness by appealing to eco-conscious consumers.
How Does RoHS Drive Material Innovation?
Ever wondered how a regulation could spark creativity and innovation in an entire industry? That’s exactly what the RoHS Directive is doing for electronics.
RoHS stimulates material innovation by promoting eco-friendly alternatives to hazardous substances, leading to advancements in bio-based plastics and non-toxic flame retardants, thus enhancing sustainability and technological progress.
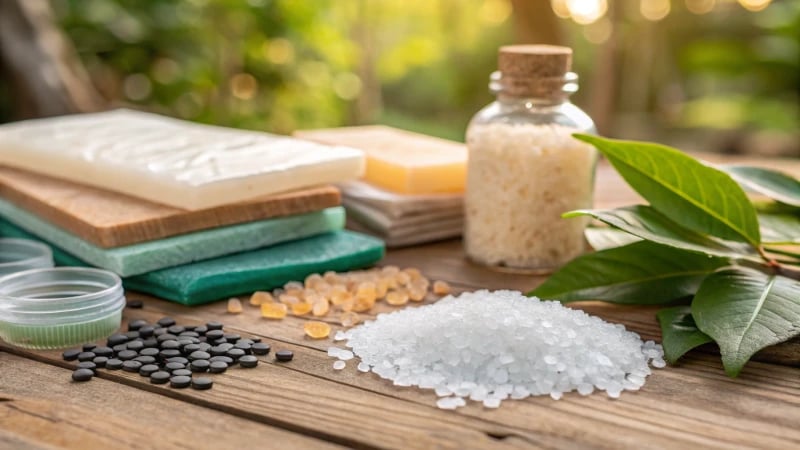
Material Composition Restrictions
When I first heard about the RoHS Directive, I thought it was just another regulatory hurdle. But then, as I dove deeper into my work, I realized its potential for sparking innovation. For instance, the restrictions on heavy metals in injection molding materials meant that we had to bid farewell to some vibrant lead pigments I used to love. But this challenge also opened doors to discovering lead-free alternatives that are not only safer but sometimes even more vibrant. This pivot encouraged increased research and development8, pushing us to think outside the box.
Restricted Substance | Traditional Use | Alternative Solution |
---|---|---|
Lead | Pigments | Lead-free pigments |
Brominated Flame Retardants
The restrictions don’t stop there. Remember the days when brominated flame retardants like PBB and PBDE were the go-to for electronic equipment housings? Those days are long gone. Now, we’re experimenting with phosphorus-based or nitrogen-based alternatives. Sure, they come with their own set of challenges, such as cost differences and performance tweaks, but they drive necessary process optimization9.
Plasticizer Restrictions
Plasticizers were another area where we faced limitations. Finding alternatives like citrate plasticizers forced us to rethink our product formulations and production processes, ensuring that we not only comply but also innovate.
Range of Material Options
Initially, I felt boxed in by the reduced choice of traditional materials due to hazardous content restrictions. But this challenge turned into an exciting opportunity to explore bio-based and degradable plastics. These innovations are not just eco-friendly; they promise better performance and processability, crucial for sustainable industry growth10.
Difficulty in Quality Control
Ensuring compliance with RoHS can be daunting. The rigorous testing required can spike costs and complicate supply chain management. I’ve learned that investment in equipment and training, alongside robust supplier audits, is essential to maintain directive compliance.
Challenge | Impact |
---|---|
Increased Testing Costs | Investment in equipment and training |
Supply Chain Management | Need for traceability systems |
Production Cost Changes
Eco-friendly alternatives often come with a price tag that can make anyone hesitant. However, I’ve found that while these materials might initially increase production costs, the long-term benefits of efficiency adjustments often outweigh these hurdles.
Market Competitiveness
Aligning with RoHS can be a game-changer in terms of market competitiveness. It not only opens up international markets but also appeals to environmentally conscious consumers. In my experience, this alignment significantly boosts brand recognition and positions us favorably through green innovation11. Whether we like it or not, these standards are reshaping our industry for the better.
RoHS restricts the use of lead in pigments.True
RoHS limits hazardous substances like lead, prompting alternatives.
RoHS compliance decreases market competitiveness.False
Adhering to RoHS offers a competitive edge through innovation.
How Can Companies Boost Market Competitiveness Through RoHS Compliance?
Ever wondered how following rules could actually make your business thrive?
RoHS compliance enhances market competitiveness by reducing export risks, promoting eco-friendly practices, and driving innovation, thereby meeting global standards, improving reputation, and expanding market reach.
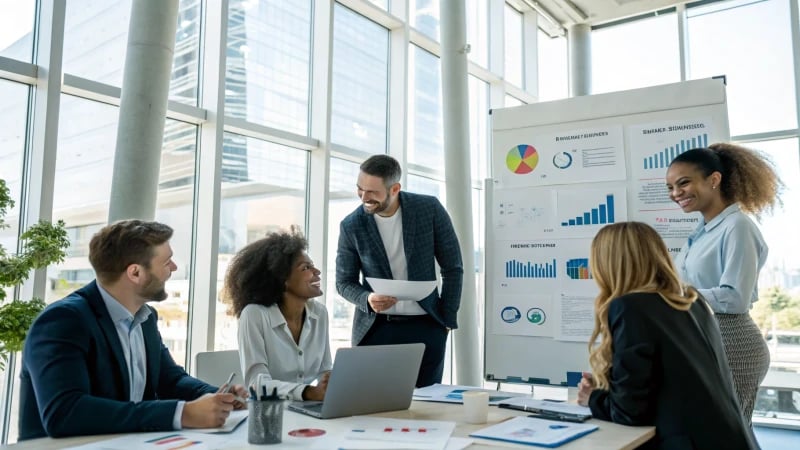
The Strategic Role of Material Composition Restrictions
When I first heard about RoHS compliance, it seemed daunting. As someone deeply involved in injection molding, I was used to relying on traditional materials like lead pigments for vibrant colors and cadmium stabilizers for enhanced stability. But with RoHS, I had to pivot. I remember diving into research and development to find alternatives that met the directive’s requirements. It was tough at first; costs went up, and the learning curve was steep. However, this challenge spurred innovation. Discovering bio-based plastics not only complied with regulations but also enhanced sustainability12. It’s like finding a hidden gem in a sea of compliance standards.
Material | Traditional Use | RoHS-Compliant Alternative |
---|---|---|
Lead Pigments | Bright Colors | Lead-Free Pigments |
Cadmium Stabilizers | Stability Enhancement | Cadmium-Free Stabilizers |
Navigating Market Limitations and Opportunities
Initially, the market seemed restricted due to the limited availability of compliant materials. I felt the pinch of fewer choices. But this scarcity nudged suppliers to innovate, crafting new materials that met RoHS standards. These advancements led to superior performing materials that caught the eye of environmentally conscious consumers. As I adapted quickly, I found myself riding the green wave, appealing to a growing base of eco-friendly customers.
Companies that adapt quickly can capitalize on the green advantage13, appealing to a growing base of eco-conscious consumers.
Quality Control Challenges and Solutions
Ensuring compliance meant rigorous quality control—testing raw materials and finished products meticulously. I had to step up supply chain audits and establish traceability systems to ensure we avoided export restrictions, especially in stringent markets like the EU. The initial costs were significant, from testing equipment to personnel training, but these steps were vital in securing our place in international markets.
- Testing Costs: Significant due to equipment and personnel training.
- Supply Chain Management: Enhanced auditing and traceability systems are necessary.
Impact on Production Costs and Efficiency
Embracing RoHS-compliant materials initially hit my wallet hard. They were pricier, pushing me to rethink production techniques. Yet, as I streamlined processes for these new standards, long-term efficiency gains became evident. It wasn’t just about compliance; it was about transforming challenges into opportunities for growth.
By aligning with RoHS directives, I’ve mitigated risks and positioned myself as a leader in sustainable practices. This proactive approach has significantly boosted our reputation and market standing14 globally.
RoHS compliance reduces production costs.False
RoHS compliance can increase initial costs due to research and testing.
RoHS compliance enhances market competitiveness.True
Compliance attracts eco-conscious consumers and meets international standards.
Conclusion
The RoHS Directive impacts injection molding by restricting hazardous substances, driving material innovation, increasing costs, and enhancing market competitiveness through eco-friendly practices and compliance.
-
Discover the specifics of the RoHS Directive to understand its material restrictions. ↩
-
Learn how sustainable materials are influencing the plastics industry. ↩
-
Find strategies to manage supply chains under RoHS regulations. ↩
-
Uncover how adopting sustainable methods enhances market competitiveness. ↩
-
Discover effective systems to enhance supply chain transparency and ensure compliance. ↩
-
Discover how material innovation aids compliance and offers new opportunities. ↩
-
Learn about the benefits of RoHS compliance on brand image and market position. ↩
-
Discover alternative lead-free pigments that comply with RoHS standards to enhance color vibrancy without environmental harm. ↩
-
Explore non-halogenated flame retardants that comply with RoHS and improve safety and environmental impact. ↩
-
Learn about bio-based plastics that offer sustainable solutions for injection molding under RoHS compliance. ↩
-
Understand how green innovation under RoHS compliance boosts brand image and market competitiveness. ↩
-
Explore how bio-based plastics contribute to sustainability and innovation in material development. ↩
-
Learn why having a green advantage is crucial for gaining consumer trust and improving market presence. ↩
-
Understand the impact of regulatory compliance on improving a company’s reputation and competitiveness. ↩