Did you ever have problems with your injection molding projects? Let’s explore how Mold Flow Analysis might transform everything for you!
Mold Flow Analysis optimizes injection molding by adjusting gate location, runner systems, injection pressure, and cooling time, enhancing manufacturing efficiency and smoothness.
I think about my journey in product design. I remember the many hours I spent fixing problems in the injection molding process. I discovered Mold Flow Analysis at that time. This tool became a lifeline for me. I optimized parameters like gate location and injection pressure. I began to notice very impressive improvements. Adjusting the gate location helped me avoid short shots and air traps in complex parts. Pieces fit together like a puzzle!
Mold Flow Analysis improves injection molding efficiency.True
This claim is true as Mold Flow Analysis helps optimize parameters, leading to better manufacturing efficiency.
Gate location does not affect product quality in molding.False
This claim is false because gate location significantly impacts the flow and quality of the molded product.
- 1. What is Mold Flow Analysis and Why is it Important?
- 2. How Does Gate Location Impact Injection Molding?
- 3. How Do Runner Systems Impact Filling Quality in Injection Molding?
- 4. How Can Injection Pressure Optimization Reduce Defects?
- 5. How Can I Improve My Cooling Time Management?
- 6. How Can Mold Flow Analysis Enhance Production Efficiency?
- 7. Conclusion
What is Mold Flow Analysis and Why is it Important?
Have you ever wondered how manufacturers check that every plastic part they create is perfect? Mold Flow Analysis holds the answer. This tool optimizes the injection molding process. It also guarantees quality. Efficiency improves with its use. This really matters!
Mold Flow Analysis (MFA) uses computer simulations in injection molding to optimize gate placement, runner systems, and cooling methods, ensuring high-quality products and reducing defects.
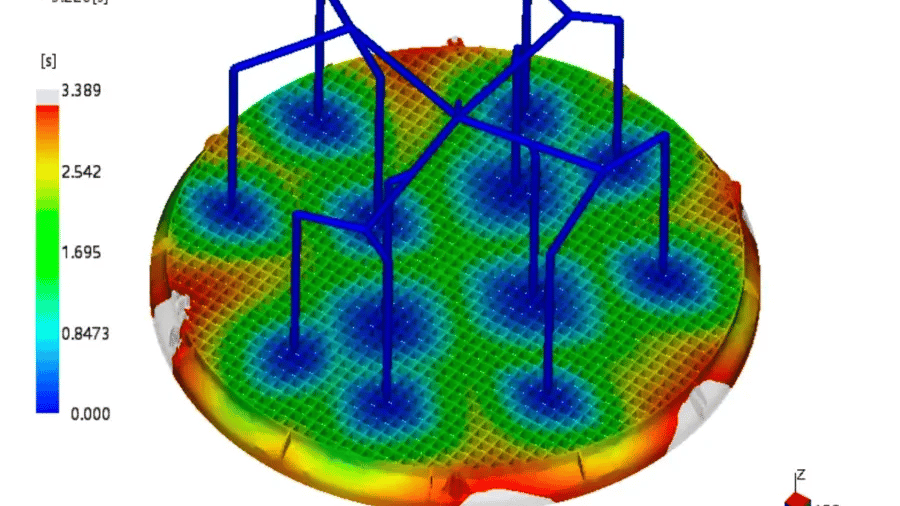
Mold Flow Analysis (MFA) is a simulation technology that plays a pivotal role in the injection molding process. It allows designers to predict how molten plastic flows through a mold, ensuring optimal filling, cooling, and solidification. Understanding MFA can significantly enhance production quality while reducing costs.
Importance of Gate Location and Number
One critical aspect of MFA is determining the gate location and number. An optimized gate location ensures that the melt fills the cavity evenly, especially in complex geometric shapes. For example, when producing a plastic part with both thin and thick sections, placing the gate close to the thin-walled area helps achieve better flow.
In one project, I placed the gate near a thin section of a plastic part. This gave us perfect flow and really improved the outcome.
In addition to location, MFA can also indicate whether multiple gates are needed. For instance, a car dashboard may require several gates to ensure uniform filling throughout its large cavity. This optimization ultimately results in reduced defects and better product quality.
Runner System Parameters
The runner system plays a significant role in the flow of plastic material. MFA assists in selecting the right runner shape and size, which affects flow resistance. A round runner typically has lower resistance compared to trapezoidal or U-shaped runners.
Runner Shape | Flow Resistance | Suitable Applications |
---|---|---|
Round | Low | General purpose |
Trapezoidal | Medium | Complex parts with varying thickness |
U-shaped | High | High volume production |
Moreover, MFA ensures that runner designs are balanced in multi-cavity molds, helping to achieve simultaneous filling of each cavity. I recall a project involving plastic bottle caps where maintaining uniformity was essential; we needed them to fill all at once.
Injection Pressure and Speed Optimization
MFA also enables injection pressure optimization by analyzing flow resistance within the mold cavity. If the pressure is too high, issues such as flash and demolding challenges can arise, while too low pressure can lead to short shots. Optimizing injection pressure is another important lesson from MFA; setting the correct pressure was crucial for thin-walled electronic cases.
Furthermore, controlling injection speed is vital for achieving high-quality finishes on products. Different speeds affect the flow front; for visually appealing parts like those in cars, MFA simulations advised me on speeds for perfect surfaces without flaws.
Putting Pressure and Time
The holding stage after filling is critical for compensating for cooling shrinkage. After mold filling, this stage compensates for shrinkage during cooling; I’ve used insights from MFA numerous times to reduce shrinkage marks in precise parts like gears by predicting necessary holding pressure.
Determining appropriate holding time is equally essential; based on wall thickness and material properties, MFA calculates optimal times ensuring integrity without unnecessarily lengthening production cycles.
Cooling Time and System Parameters
Lastly, MFA optimizes cooling time by analyzing temperature distribution during cooling processes. This step has been critical in enhancing production efficiency while preventing part deformation; reducing cooling times greatly increased output while maintaining quality during one toy project.
MFA also aids in designing cooling systems by evaluating layout, diameter, and flow rate of cooling pipes to ensure even cooling throughout large parts—an effective cooling system prevents warping which I learned through previous project challenges.
By integrating Mold Flow Analysis into our design and production processes raises product quality while reducing waste and boosting overall efficiency.
Mold Flow Analysis improves injection molding efficiency.True
MFA optimizes processes by predicting plastic flow, enhancing efficiency and reducing defects in production.
Multiple gates are unnecessary in Mold Flow Analysis.False
MFA often indicates the need for multiple gates to ensure uniform filling in large cavities, crucial for quality.
How Does Gate Location Impact Injection Molding?
Did you ever think about how the position of a gate in injection molding changes the process? It’s really interesting! Let’s explore how this important detail impacts our tasks and the quality of what we produce.
Gate location in injection molding affects melt flow, filling efficiency, and defect rates. Optimizing it enhances part quality and minimizes production issues.

Understanding Gate Location in Injection Molding
Gate placement in injection molding shapes our molded parts. I remember a project where gate position changed the final product entirely. The right gate affects melt flow, filling efficiency, and defect rates a lot. Good optimization improves part quality and minimizes production issues. This is what every designer wants.
Optimizing the gate location ensures even flow and avoids defects like short shots or air traps. Once, I worked on a complex part with both thick and thin sections. Putting the gate near the thinner area helped with quick filling, avoiding annoying trapped air pockets.
Importance of Gate Number Adjustment
Sometimes, one gate isn’t enough, especially for large or complex shapes. Mold flow analysis plays a vital role in deciding whether multiple gates are necessary.
Consider a car dashboard where achieving uniform melt filling is crucial. This often requires an increased number of gates to ensure consistent quality throughout the entire mold. The following table illustrates this concept:
Part Type | Recommended Gates | Reason for Multiple Gates |
---|---|---|
Car Dashboard | 2-4 | Ensures uniform melt filling |
Plastic Bottle Caps | 1-2 | Simplified shape allows single gate |
Runner System Parameters
The design of the runner system matters a lot as it dictates how effectively the melt travels from the gate to the cavity. The shape and size of runners impact flow resistance and pressure loss. Generally, round runners are preferred for their lower flow resistance.
Mold flow analysis helps in selecting optimal runner parameters for smooth transitions without pressure loss. This is important, especially in multi-cavity molds where equal filling rates are key.
Injection Pressure and Speed Control
Gate location also influences injection pressure and speed used during the molding process. Analyzing flow resistance at different points allowed me to optimize pressures to prevent defects like flash or demolding difficulties.
Adjusting the injection speed is also crucial; when creating high-quality parts, like car interiors, controlling injection speed prevents unsightly flow marks.
Hold Pressure and Time Settings
After filling, correct hold pressure is crucial. I worked with high-precision gears where predicting hold pressures helped minimize shrinkage marks and dimensional issues.
Setting appropriate hold times is a balancing act; too short causes visible shrink marks while too long stretches cycle times unnecessarily. The following table outlines optimal hold times based on wall thickness:
Wall Thickness (mm) | Recommended Hold Time (seconds) |
---|---|
< 1 | 5-7 |
1-3 | 8-10 |
> 3 | 12-15 |
Cooling Time Optimization
Lastly, cooling time and system parameters matter a lot. Did you know that gate location affects cooling efficiency? I designed cooling pipe layouts for uniform cooling to enhance efficiency without losing quality?
Optimizing cooling times through mold flow analysis can significantly enhance production efficiency without compromising part integrity.
For example, small plastic toys may benefit from reduced cooling times while ensuring proper quality.
In conclusion, knowing how gate location impacts many factors is essential for optimizing part quality and production efficiency. To learn more about effective gate placement strategies, explore this detailed guide1.
Gate location affects melt flow patterns in injection molding.True
The placement of gates directly influences how molten material fills the mold, impacting overall part quality and efficiency.
Multiple gates are unnecessary for complex mold designs.False
In complex geometries, multiple gates may be essential to ensure uniform filling and minimize defects during the injection process.
How Do Runner Systems Impact Filling Quality in Injection Molding?
Have you ever thought about how a small part might really change the quality of your molded pieces? Let’s look into runner systems and see how important they are in injection molding. These systems help fill the molds properly.
Runner systems in injection molding influence material flow, pressure distribution, and cooling. Proper gate placement, runner shapes, and injection settings are essential for high-quality parts with fewer defects.
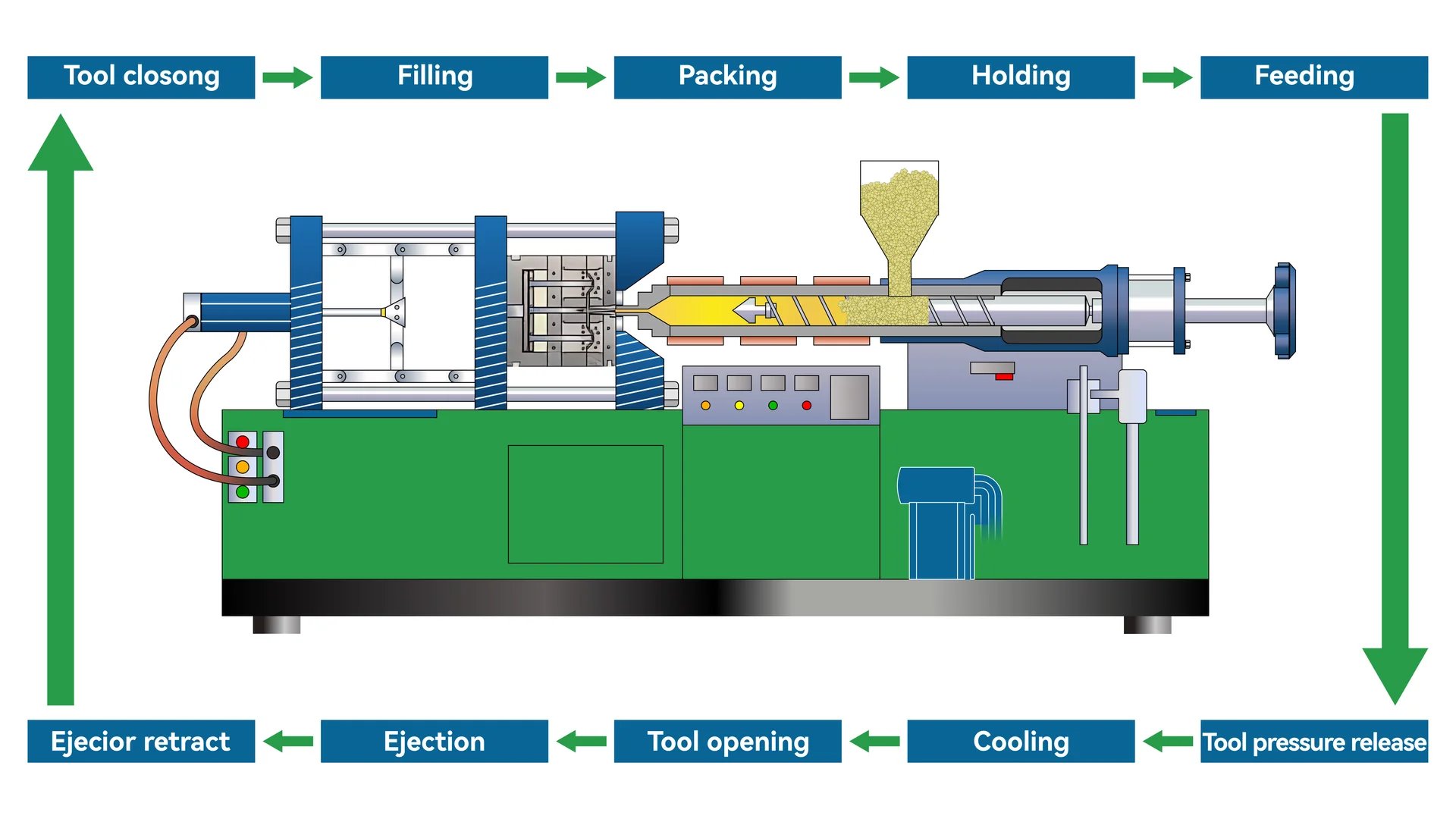
Understanding Runner Systems
Runner systems are critical components in the injection molding process that play a significant role in ensuring the melt fills the mold cavities efficiently and effectively. The design of the runner system can influence the overall filling quality of plastic components.
1. Gate Location and Number
Optimizing the gate location is essential for even melt distribution. For complex geometries, mold flow analysis can determine the best entry points for the melt.
- Example: In a thin-walled section of a part, placing the gate near this area ensures quick filling, reducing the chances of defects like short shots or air traps.
- Gate number: Increasing the number of gates may be necessary for large parts to achieve uniform filling.
2. Runner System Parameters
The shape and size of runners affect flow resistance. Runners can be designed in various shapes:
Runner Shape | Flow Resistance | Efficiency |
---|---|---|
Round | Low | High |
Trapezoidal | Moderate | Moderate |
U-shaped | High | Low |
Choosing the right size is equally important. A runner that is too narrow can lead to pressure loss, while one that is too wide might waste material.
3. Injection Pressure and Speed
Using mold flow analysis, designers can optimize injection pressure to avoid issues like flash or demolding difficulties.
- Injection Speed Control: The right speed is crucial for maintaining surface quality, particularly for aesthetic parts like automotive interiors. Analyzing flow fronts at various speeds helps in determining the optimal speed to avoid defects such as flow marks.
4. Holding Pressure and Time
After the cavity is filled, holding pressure compensates for cooling shrinkage. Here’s how:
- Holding Pressure Determination: Utilizing mold flow analysis, designers can predict necessary holding pressures to minimize shrinkage marks.
- Holding Time Setting: The calculation of optimal holding time ensures effective pressure compensation during cooling, balancing efficiency and cost.
5. Cooling Time and Cooling System Parameters
Cooling time directly impacts production efficiency:
- Cooling Time Optimization: Shortening cooling time through precise temperature distribution analysis can enhance productivity without sacrificing quality.
- Cooling System Parameter Adjustment: The layout and flow rate of cooling pipes must be carefully designed for uniform cooling to prevent warping.
In summary, runner systems play a pivotal role in determining the quality of filled molds by influencing various factors such as melt flow, pressure distribution, and cooling efficiency. By optimizing these elements through careful analysis, designers can significantly enhance product quality while minimizing defects.
Runner systems directly affect melt flow in injection molding.True
The design of runner systems is critical for ensuring efficient melt flow, impacting the filling quality of molded parts.
Increasing gate numbers always improves filling quality.False
While more gates can help, they may not always improve filling quality and can lead to inefficiencies if not optimized correctly.
How Can Injection Pressure Optimization Reduce Defects?
Have you felt upset because defects spoiled your perfectly designed product? I have felt that too. Reducing defects truly matters. Optimizing injection pressure very much improves product quality. This change probably helps in minimizing annoying defects.
Optimizing injection pressure in molding ensures consistent melt flow and controlled pressure, reducing defects like short shots and surface imperfections, thereby enhancing product quality. Adjusting cooling times is crucial for these improvements.
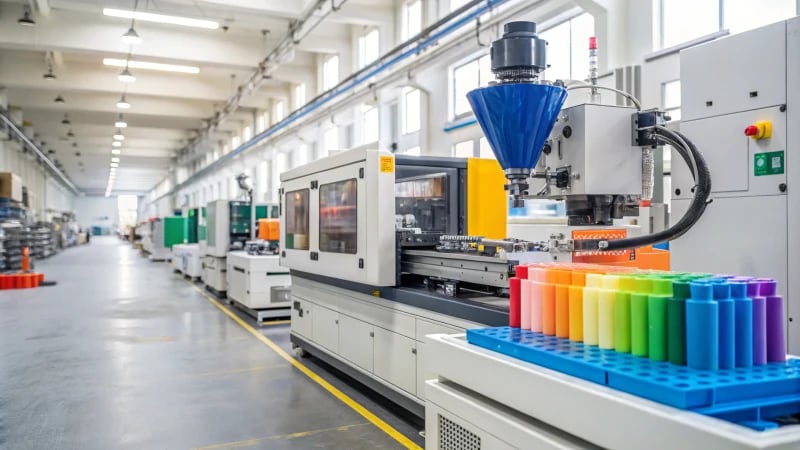
Understanding Injection Pressure Optimization
Optimizing injection pressure is very important to reduce defects in the injection molding process. By carefully analyzing and adjusting the pressure at which molten plastic is injected into the mold, manufacturers can achieve better fill patterns and reduce common defects such as short shots, voids, and warping.
For instance, applying the right injection pressure ensures that the melt fills the mold cavity evenly, especially in complex geometries. In cases where parts have both thin and thick walls, I learned to place the gate near thin areas to enable efficient filling. Mold flow analysis tools became my secret weapon in identifying these optimal locations.
Key Factors Impacting Defect Rates
- Injection Pressure
Finding the right pressure is crucial. Too much pressure causes flash and problems during removal. Too little pressure results in short shots and voids.
Pressure Level | Possible Defects |
---|---|
Too High | Flash, Demolding Difficulties |
Too Low | Short Shots, Voids |
-
Injection Speed Control
The speed of injection is very critical. Incorrect speed caused flow marks when working on car interior parts. Adjustments based on mold flow analysis improved this by creating smooth finishes that satisfied our clients. -
Holding Pressure and Time
After filling, correct holding pressure is essential for controlling shrinkage as it cools. Too little pressure gives shrink marks while too much raises cycle times and costs.- Optimal Holding Pressure: Keeps the right pressure to prevent defects during cooling.
- Calculated Holding Time: Allows enough cooling time without delaying production unnecessarily.
-
Cooling Time Optimization
Cooling solidifies everything; it must be right! I once rushed this step and saw parts warp! Using mold flow analysis told me the perfect cooling times that kept parts accurate and improved efficiency.- Shortened Cooling Time: Increases production speed.
- Even Temperature Distribution: Reduces deformation risk.
Practical Applications of Optimization Techniques
Applying these techniques improved product quality significantly. For example, in designing car dashboards, multiple gates were crucial for achieving uniform filling and avoiding defects from uneven pressure distribution.
In summary, focusing on injection pressure optimization changed my view on injection molding. It’s amazing how these strategies cut defect rates while improving product quality significantly. For more insights on how to implement these strategies effectively, check out injection molding techniques.
By constantly checking each parameter related to injection pressure, speed, and cooling, I have streamlined our processes allowing us to deliver high-quality plastic parts very efficiently.
Optimizing injection pressure minimizes short shots in molding.True
Properly adjusting injection pressure ensures even melt flow, significantly reducing the occurrence of short shots during the injection molding process.
High injection speed always improves surface quality.False
High injection speeds can cause turbulence, leading to surface imperfections rather than improving quality, making this claim false.
How Can I Improve My Cooling Time Management?
Managing cooling time is very important in manufacturing. This is especially true for injection molding. I want to share some best practices. These not only improve how quickly production happens but also improve the quality of products. Let’s explore these ideas together!
Optimize cooling time in manufacturing by improving gate locations, adjusting runner settings, controlling injection parameters, accurately setting holding pressure and time, and refining cooling systems.
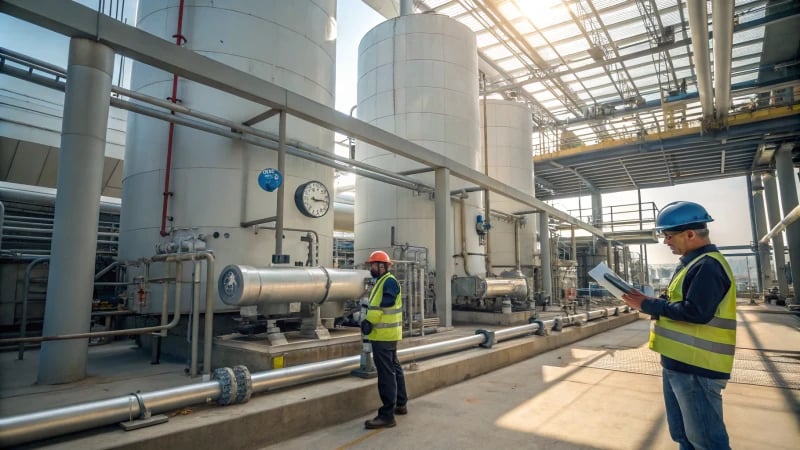
Understanding Cooling Time Management
Cooling time management is not just a technical need. It’s a key part of creating top products I’ve learned to value as a designer. I ignored it once and later saw how much it impacted my work. Good cooling raises efficiency and product quality. Manufacturers like us manage to reduce production times and save money without losing quality.
To get good at cooling time management, a few best practices really help:
1. Optimize Gate Location and Number
Gate placement and count in the mold are crucial for proper cooling.
-
Gate Location Optimization: Mold flow analysis showed me the best gate spots. It ensured even filling of the mold cavity. For complex shapes, placing gates near thinner sections allowed easy filling and fewer defects.
-
Gate Number Adjustment: Sometimes big parts need more than one gate. While working on a car dashboard, we used multiple gates to ensure even filling. This approach significantly cut cooling variations, keeping our products consistent.
2. Adjust Runner System Parameters
Runners guide melted plastic into molds. Their design greatly affects cooling time.
Runner Shape | Flow Resistance | Recommended Applications |
---|---|---|
Round | Low | Most applications |
Trapezoidal | Medium | Complex shapes |
U-shaped | High | Large parts |
- Balanced Design: In multi-cavity molds, a balanced runner system is crucial for filling all cavities at once. Mold flow analysis helped adjust runner designs, which was vital for making uniform bottle caps.
3. Optimize Injection Pressure and Speed
Pressure and speed of injection impact not only filling but also cooling rates.
-
Injection Pressure Optimization: In one project, assessing flow resistance helped set optimal injection pressures. High pressure caused defects like flash; low pressure led to incomplete fills. For thin-walled electronic parts, precise tweaks mattered.
-
Injection Speed Control: Controlling injection speed is key for great surface quality. It’s crucial to adjust this speed to avoid flaws while maintaining function.
4. Determine Holding Pressure and Time
After filling the cavity, holding pressure becomes crucial to prevent shrinkage.
-
Holding Pressure Determination: Mold flow analysis predicts needed holding pressures. This is vital for reducing shrinkage marks on precision pieces like gears; correct pressure is key for keeping dimensions accurate.
-
Setting Holding Time: It’s important to find the perfect holding time; too short causes defects while too long raises cycle times. I often check wall thickness and material properties for accurate adjustments.
5. Cooling Time and System Parameter Optimization
Optimizing cooling times greatly elevates productivity.
-
Cooling Time Optimization: Detailed analysis helped calculate the shortest cooling times while keeping quality high; when molding small toys, shorter cycles boosted efficiency without losing integrity.
-
Adjust Cooling System Parameters: Changing the layout, diameter, and flow rate of cooling channels helps in even temperature distribution; I saw how smart design prevents warping during cooling.
For more insights into refining your processes, check out advanced cooling techniques or best practices in mold design2. I’m fond of sharing my experiences – together, let’s improve our craft!
Optimizing gate location improves cooling efficiency in molding.True
Strategic gate placement ensures even melt distribution, reducing defects and enhancing cooling efficiency during the injection molding process.
Multiple gates are unnecessary for small molded parts.False
For larger components, using multiple gates is essential to achieve uniform filling and consistent cooling, preventing quality issues.
How Can Mold Flow Analysis Enhance Production Efficiency?
Do you ever think about how factories adjust their injection molding methods to be perfect? Mold Flow Analysis (MFA) is truly fascinating. It changes the industry. This tool allows factories to improve production efficiency better than ever. Let’s explore this amazing tool together!
Mold Flow Analysis enhances production efficiency by optimizing gate locations, runner systems, injection pressures, and cooling times, reducing defects, improving cycle times, and ensuring high-quality outputs in manufacturing.
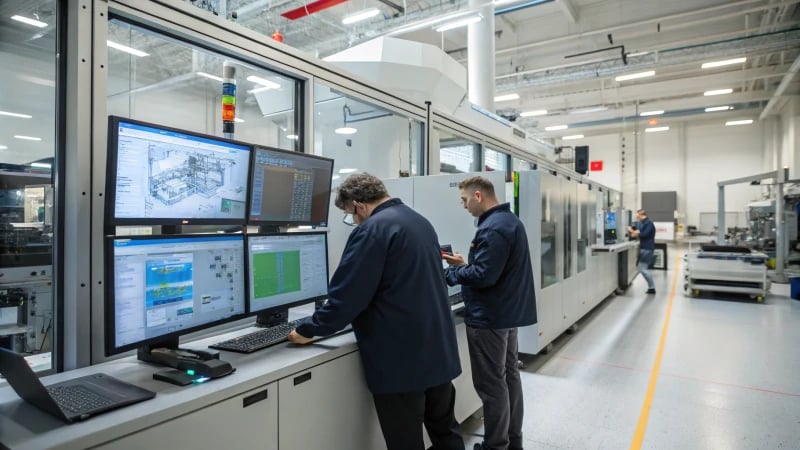
Understanding Mold Flow Analysis
Mold flow analysis (MFA) is a powerful tool that allows manufacturers to simulate the injection molding process before actual production begins. This technique helps in identifying potential defects and optimizing the design parameters to enhance production efficiency.
By utilizing MFA, designers can analyze various factors such as melt flow, cooling times, and pressure distribution within the mold. This predictive capability leads to more informed decision-making in the design process.
Gate Location Optimization
Gate location and number play a critical role in the injection molding process.
- Gate Location: Optimizing the gate location ensures that the melt fills the cavity evenly, preventing issues like short shots or trapped air. For instance, placing the gate close to thin-walled sections improves filling efficiency. I worked on a project where placing the gate was vital for even melt filling. Putting the gate near thin parts of our item stopped short shots and trapped air. I learned this lesson the hard way!
- Gate Number: In cases of large or complex parts, it may be necessary to use multiple gates. For example, designing a car dashboard once showed me that one gate was insufficient. MFA helped me see that several gates were needed for even melt spread, greatly improving the outcome.
Runner System Parameters
The runner system is essential for controlling how the melt flows into the mold cavities.
Parameter | Description | Impact on Production |
---|---|---|
Runner Shape | Different shapes (round, U-shaped) affect flow resistance. | Round runners typically have lower resistance, aiding smoother flow. |
Runner Size | Diameter impacts pressure drop; too narrow causes excess pressure loss. | Proper sizing is crucial for maintaining efficiency in flow rates. |
A balanced runner design ensures that all cavities fill simultaneously, which is vital in multi-cavity molds. I clearly remember changing runner settings in a multi-cavity bottle cap mold; each cavity filling at the same time felt like conducting a perfect symphony!
Injection Pressure and Speed Control
Another key area where mold flow analysis enhances production efficiency is through optimization of injection pressure and speed.
- Injection Pressure: Analyzing flow resistance helps determine optimal injection pressure, balancing risk of defects like flash against ensuring complete filling. By examining flow resistance, I discovered best injection pressures for different projects; too much caused defects while too little resulted in short shots.
- Injection Speed: The flow front advancement can be simulated at various speeds to ensure high-quality surface finish, particularly important in parts with strict aesthetic requirements like automotive interiors. An automotive interior project needed specific speed to avoid surface flaws; MFA allowed me to test different speeds and achieve a perfect finish.
Holding Pressure and Time Settings
Determining proper holding pressure and time after filling is crucial for maintaining dimensional accuracy and reducing defects.
- Holding Pressure: Adequate holding pressure compensates for shrinkage during cooling, crucial for high-precision components like gears. When working with high-precision parts like gears, I used MFA to find right holding pressure to avoid shrinkage; seeing it fit perfectly was very rewarding.
- Holding Time: The calculated holding time ensures that parts cool uniformly without warping or shrinkage marks appearing. Finding ideal holding time is tricky; if too short defects appear while if too long costs rise. With MFA, I calculated designs to reach best results.
Cooling Time and System Parameters
Mold flow analysis also contributes significantly to optimizing cooling times and systems.
- Cooling Time Optimization: MFA predicts temperature distribution and allows designers to calculate shortest necessary cooling time thereby improving cycle times. Optimizing cooling times once transformed my cycle for small plastic toys; calculating shortest cooling time really increased efficiency while keeping parts’ quality intact.
- Cooling System Layout: The layout and size of cooling channels can be adjusted to ensure even cooling preventing warping. Adjusting cooling channel layouts became natural with MFA; even cooling can stop warping especially in larger pieces.
In conclusion, employing mold flow analysis in production processes not only identifies potential issues but also paves way for enhancements that lead to increased efficiency and reduced costs. For further insights on best practices in mold design, check out advanced techniques3.
Mold flow analysis helps prevent defects in injection molding.True
By simulating the injection process, mold flow analysis identifies potential defects, enhancing the overall quality of produced parts.
Optimizing gate locations increases production cycle times.False
Correct gate positioning improves melt flow and reduces cycle times, leading to more efficient production processes.
Conclusion
Mold Flow Analysis enhances injection molding by optimizing gate locations, runner systems, injection pressures, and cooling times to improve efficiency and product quality.
-
This link provides in-depth analysis on optimizing gate locations for better mold design outcomes. ↩
-
Discover expert insights and strategies on effective cooling time management practices to enhance your production efficiency. ↩
-
Discover how MFA can significantly improve your manufacturing processes and reduce costs effectively. ↩