Do you ever think about the hidden heroes of plastic molding? Let’s explore the really interesting world of runners!
In plastic molding, the runner directs molten plastic from the injection machine to the mold cavity, impacting production speed and final product quality, making its design crucial for efficient and effective molding processes.
I still remember when I first saw a runner in action during my early days in product design. It was mesmerizing. This important channel guided molten plastic from the machine directly into the mold. The runner is more than just a path. It is the lifeline for a smooth process. Designers need to understand its details, from main runners to gates. This knowledge is essential. It is very important for anyone wanting to improve their designs. Mastering this part transforms your creations and really improves production efficiency. It changes everything!
The runner channels molten plastic to the mold cavity.True
This statement is true as the runner's primary function is to transport molten plastic from the injection machine to the mold, ensuring proper filling.
Runner design has no impact on production efficiency.False
This claim is false; the runner's design significantly affects both production efficiency and product quality in plastic molding processes.
What are the Different Types of Runner Systems?
Have you ever thought about how the magic of injection molding works? Let’s explore the amazing world of runner systems. Runner systems help this process become very efficient and effective.
Injection molding uses three runner systems: main runners transport plastic melt to the mold, branch runners distribute it within the mold, and gates direct it into the mold cavity, ensuring consistent quality.
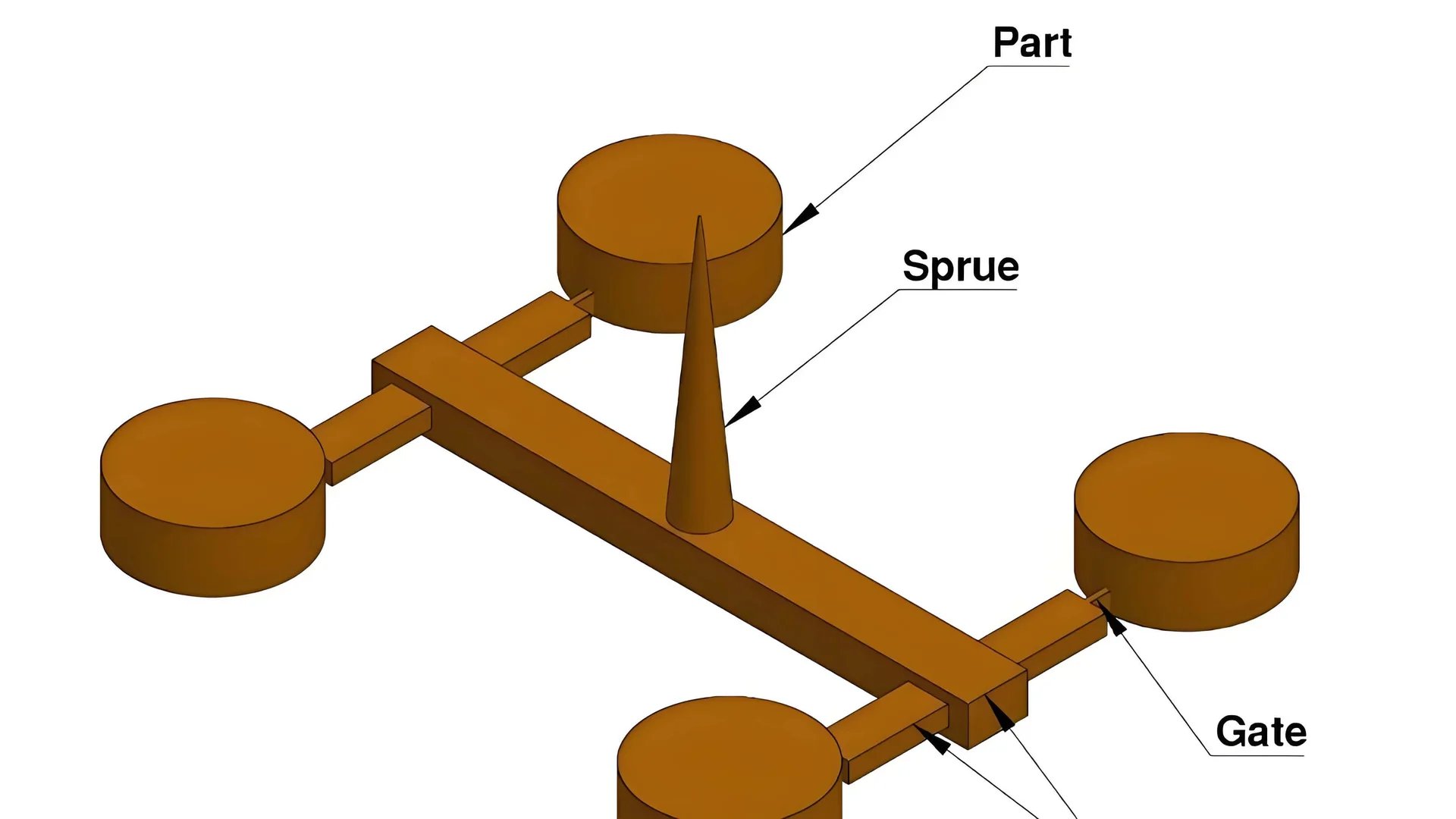
Understanding Runner Systems
In injection molding, the runner system plays a crucial role in determining the efficiency and effectiveness of the molding process. It consists of various components that ensure the smooth flow of plastic melt from the injection molding machine to the mold cavity. Let’s explore the different types of runner systems:
Main Runner
The main runner is where it begins. Think of it as a highway connecting the injection molding machine’s nozzle to the branch runners. Its design is very important; it helps reduce pressure loss and maintains stable temperatures. Typically conical, it has a taper between 2° – 6° to facilitate smooth flow.
Characteristic | Details |
---|---|
Diameter | Matches machine nozzle |
Shape | Conical |
Purpose | Ensure efficient plastic melt flow |
I remember learning about main runners and how their simple design impacts the final product’s quality. A well-designed main runner reduces defects and maintains consistency. Truly, a game-changer.
Branch Runner
The branch runner serves as a network of roads off the main highway. It spreads the plastic melt evenly to each gate, making sure every mold part gets what it needs. Shapes vary widely, including circular, semicircular, trapezoidal, or U-shaped, each with benefits:
- Circular: Offers low flow resistance but is complex during mold processing.
- Trapezoidal & U-shaped: Easier handling and usually provide better melt flow.
Selecting the right shape depends on factors such as plastic type, product size, and process conditions. Shorter branch runners usually perform better; they reduce pressure loss and temperature changes.
Gate
Finally, the gate is the last stop before entering the mold cavity. It manages speed and direction; this part is crucial in our system. Different gates suit various uses:
- Side Gate: Good for small to medium products; it allows smooth side entry.
- Point Gate: Best for aesthetic products; however, it needs higher injection pressure because of its size.
Gate Type | Application | Advantages |
---|---|---|
Side Gate | Small/Medium products | Smooth entry |
Point Gate | High appearance products | Minimal marks on surface |
Understanding these systems is essential for designers like me who aim to balance functionality with aesthetics while ensuring efficient production processes. Those interested in learning more should explore advanced mold design techniques1 or best practices in runner system configuration2. We constantly refine our craft to deliver exceptional results.
Main runners are conical to minimize pressure loss.True
Main runners in injection molding are designed conically to reduce pressure loss, ensuring efficient plastic melt flow from the machine to the mold cavity.
Branch runners can only be circular in shape.False
Branch runners can have various shapes, including circular, trapezoidal, and U-shaped, each offering different advantages for melt flow distribution.
How Does Runner Design Affect Injection Molding Efficiency?
Have you ever thought about how a runner, which looks simple, affects the whole injection molding process? Different runner designs really change efficiency. They reduce costs. Product quality gets better with these designs.
Efficient runner design in injection molding minimizes pressure loss, maintains melt temperature, and shortens cycle times, reducing waste and production costs while enhancing product quality.
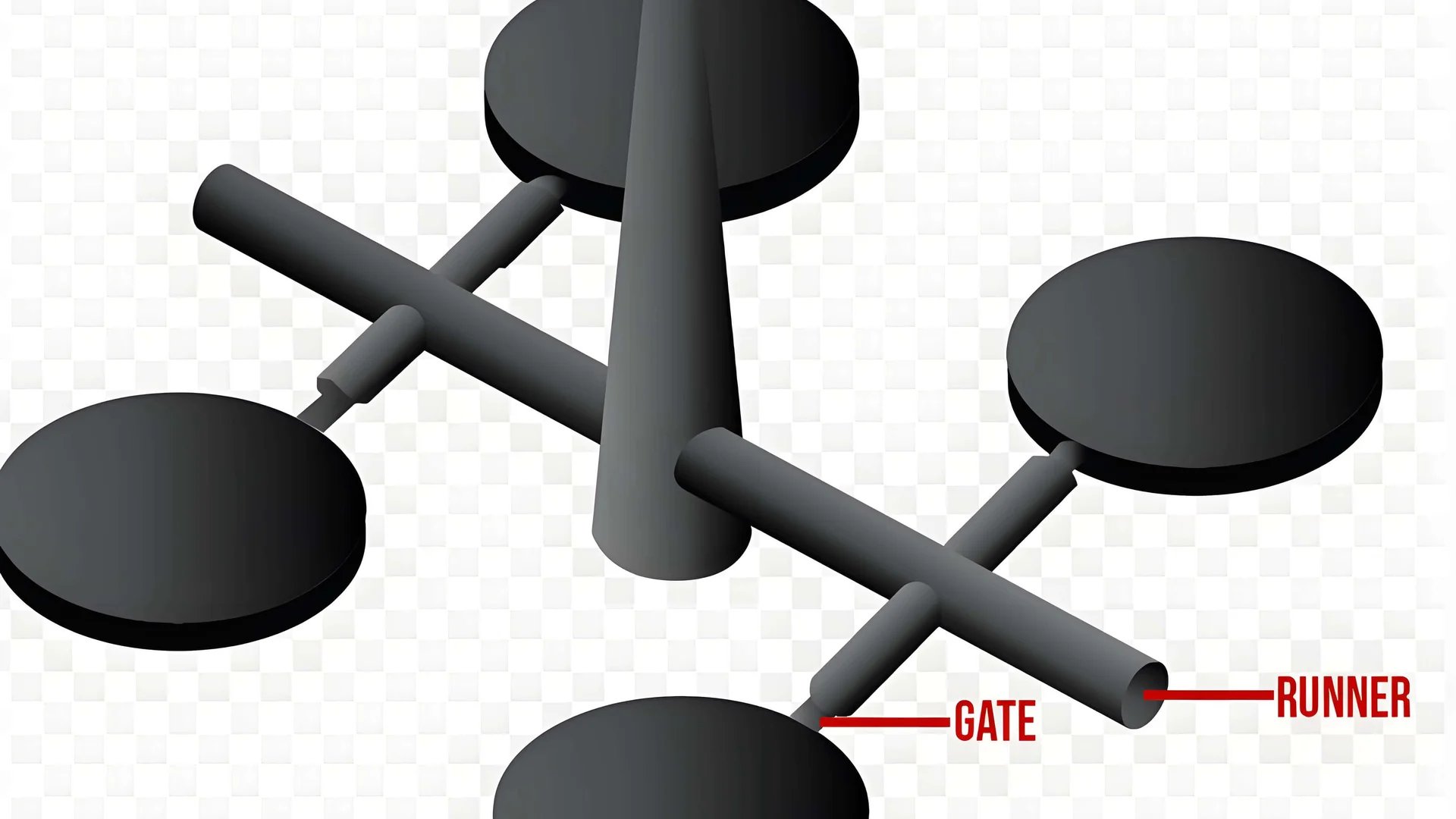
Understanding Runner Design in Injection Molding
When I began learning about injection molding, I quickly noticed the runner system’s importance. It’s the path where molten plastic flows from the injection machine into the mold. This part must be correct because it significantly impacts production efficiency.
A well-designed runner can significantly enhance the efficiency of the injection molding process by minimizing pressure loss and ensuring uniform melt distribution. The key aspects of runner design include the main runner, branch runner, and gate.
Main Runner Characteristics
The main runner connects the injection machine to the mold’s branch runners. Its design is crucial for maintaining the flow characteristics of the plastic melt.
- Conical Shape: The cone-like shape, usually tapering between 2° – 6°, allows a smooth flow. It’s like giving the plastic a gentle nudge along its path.
- Diameter Matching: The small end’s diameter matches that of the nozzle to minimize turbulence and ensure an efficient transition. This match feels like watching a perfect race – everything flows very smoothly.
Properly designed main runners reduce pressure losses, which in turn lowers cycle times and increases overall production efficiency.
Branch Runner Functionality
Branch runners distribute molten plastic evenly to each gate. Their design affects not only flow rate but also product quality. Over time, I’ve discovered common shapes that meet different needs:
Runner Shape | Advantages | Disadvantages |
---|---|---|
Circular | Lowest flow resistance | Difficult to open during mold processing |
Trapezoidal | Easy to process, good flow performance | Moderate resistance |
U-shaped | Balanced flow and processing ease | Requires more space |
Choosing the right shape based on the product’s requirements and type of plastic can enhance efficiency.
Gate Design Considerations
Let’s discuss the gate – the final checkpoint before the plastic enters the mold. Its design controls the flow of melt:
- Side Gate: This one is versatile! It fits small to medium parts and ensures a smooth entry from the side.
- Point Gate: If appearance matters, this gate leaves tiny marks but needs higher injection pressure, which affects cycle time and energy use.
Impact on Injection Molding Efficiency
Reflecting on my experiences, I’ve realized how much runner design impacts injection molding efficiency. Here are some factors I always consider:
- Pressure Loss: A smart runner design reduces pressure drop, ensuring efficient filling and shorter cycles.
- Temperature Maintenance: Keeping the melt’s temperature right during its journey is vital; poorly designed runners can lose unwanted heat – trust me, I’ve seen it!
- Material Utilization: Efficient runners generate less waste, reducing material costs and supporting sustainability. Every bit helps!
For anyone curious about how different runner types affect production, check out different runner types3 or explore gate functions4. Learning about runner design has opened my eyes and I hope it brings you clarity as you improve your processes!
Well-designed runners minimize pressure loss in molding.True
Efficient runner design reduces pressure drop, enhancing flow and cycle times in injection molding, leading to better production efficiency.
Circular runners are the best for all injection molding processes.False
While circular runners have low resistance, they can be difficult to open during processing, making them not universally ideal for all applications.
What Challenges Can Arise with Runner Systems?
Exploring the world of runner systems in injection molding presents many challenges. These challenges influence production efficiency. They also impact the quality of the final products. Let’s dive into these issues together!
Runner systems in injection molding face challenges like gate blockages, flow imbalances, temperature issues, and pressure loss. Understanding these is crucial for maintaining production efficiency and product quality.
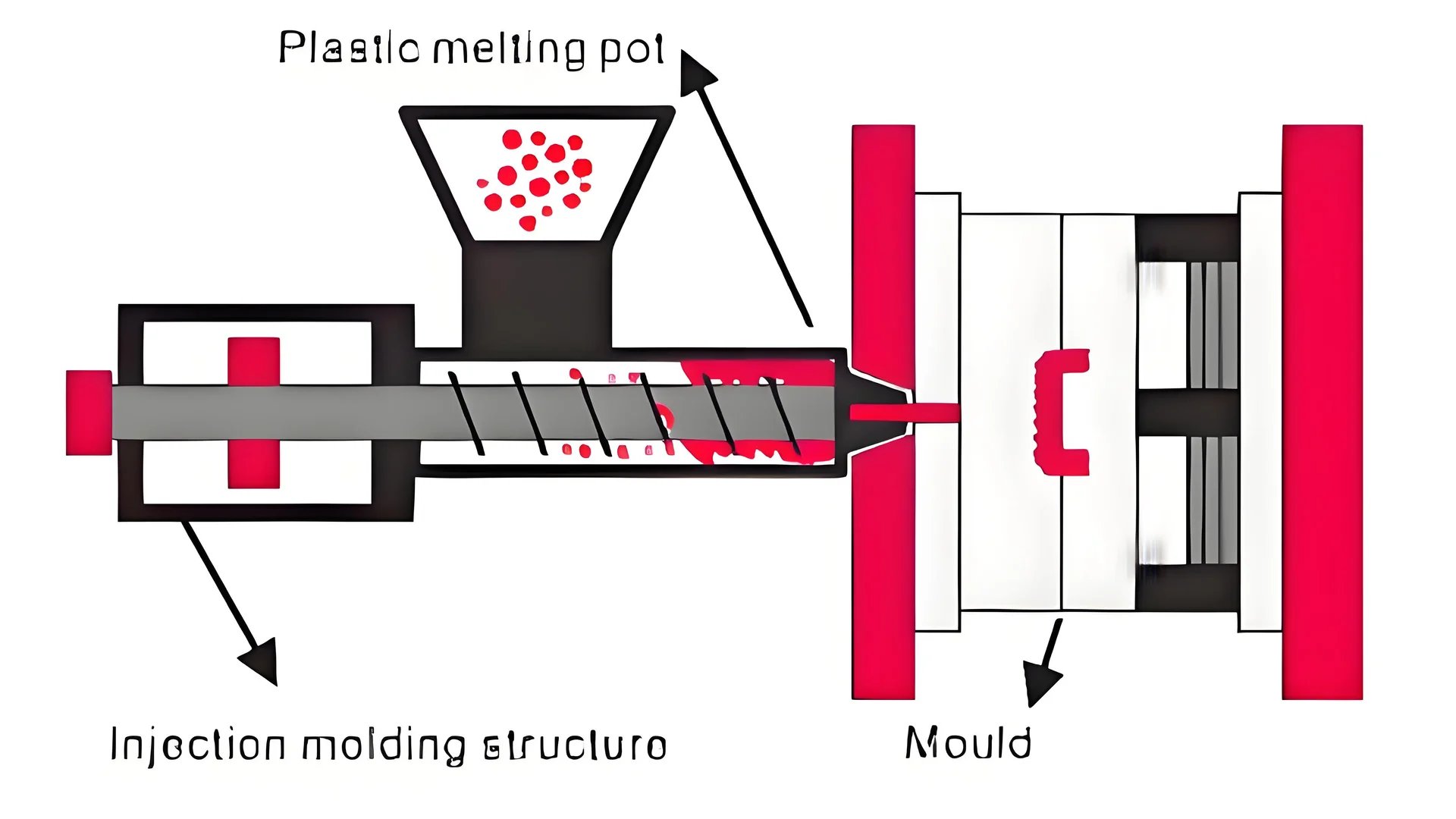
Understanding Runner System Challenges
Runner systems in injection molding are crucial for delivering the plastic melt to the mold cavities efficiently. However, several challenges can arise during this process that may affect the final product’s quality and production efficiency.
1. Gate Blockages
One of the most common issues is gate blockages. Imagine this: the mold is ready, but the gate is blocked during injection. The plastic can’t move properly into the mold cavity, causing incomplete fills and defects such as short shots. To mitigate this issue, designers should consider optimizing gate design5 and ensuring proper melt flow.
2. Flow Imbalance
Flow imbalance occurs when the plastic melt does not distribute evenly across multiple cavities. On one project, the plastic didn’t spread evenly across cavities, leading to variations in wall thickness and overall product inconsistency. Using advanced simulation tools can help predict flow patterns and adjust runner dimensions accordingly to achieve uniform melt distribution6.
3. Temperature Control Issues
Maintaining optimal temperature within the runner system is vital. Temperature fluctuations can lead to premature solidification or degradation of the plastic material, affecting mechanical properties. Effective temperature management strategies include using temperature control units7 and monitoring thermal profiles throughout the injection cycle.
4. Pressure Loss
Pressure loss along the runner system can severely impact injection performance. Once, a poorly designed runner caused significant pressure drops; it felt like a constant struggle. The design of both main and branch runners should minimize pressure drops by considering aspects such as diameter and length. Implementing streamlined designs can significantly reduce resistance to flow, ultimately enhancing production efficiency.
Challenge | Description | Mitigation Strategies |
---|---|---|
Gate Blockages | Blockage of the gate preventing proper fill | Optimize gate design and check material flow properties |
Flow Imbalance | Uneven distribution across cavities | Use simulation tools for predicting flow |
Temperature Control | Fluctuations affecting material properties | Utilize temperature control units |
Pressure Loss | Loss of pressure impacting injection performance | Design runners with optimized geometry |
5. Material Variability
Material variability complicates runner design as different plastics have unique flow characteristics. Testing materials under expected conditions helps identify potential challenges early on; it saves hours of troubleshooting later on when you test materials8.
By addressing these challenges through careful design and testing, manufacturers can improve operational efficiency and product quality in their injection molding processes.
Gate blockages can cause incomplete fills in injection molding.True
When gates are blocked, the plastic melt can't enter the mold, leading to defects like short shots.
Temperature fluctuations do not affect product quality in molding.False
Inconsistent temperatures can degrade materials, impacting mechanical properties and product quality.
How Can Optimizing Runners Improve Product Quality?
Did you ever think about how a small design change probably leads to a big improvement in product quality? Let’s enter the interesting world of injection molding runners. We will explore how optimization creates a really significant difference.
Optimizing runners enhances product quality by improving melt flow, reducing cycle times, and minimizing defects. Critical elements include proper design of main and branch runners and precise gate specifications.
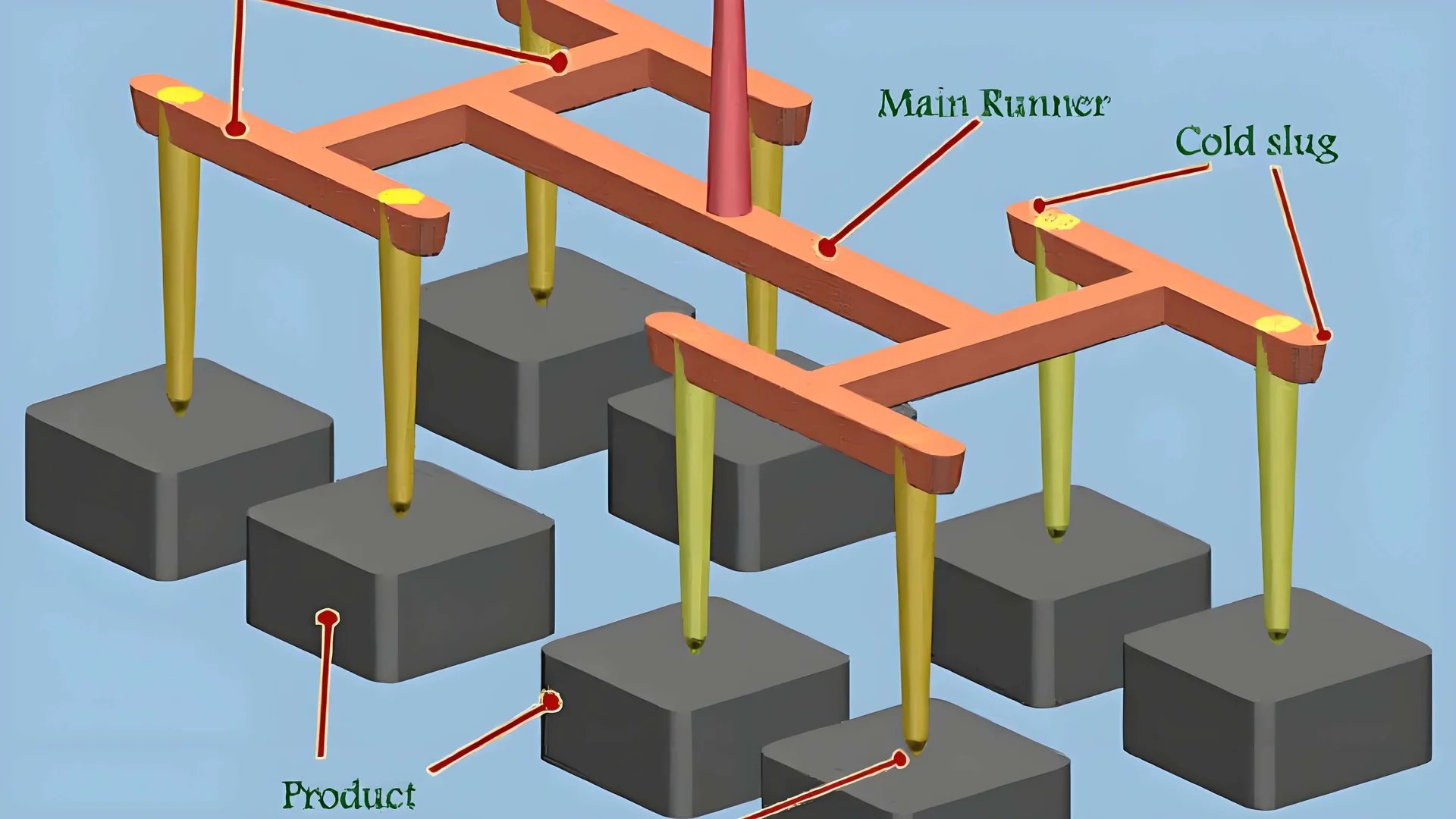
Understanding Runners in Injection Molding
As someone who has spent years working in product design, I know that understanding injection molding is crucial for better product quality. Runners guide molten plastic from the machine nozzle to the mold cavity. These runners often go unnoticed, yet they are truly important. Optimizing them improves production and product outcomes.
To optimize product quality in injection molding, it is essential to understand what runners are. The runner is the flow channel for the plastic melt, starting from the nozzle of the injection molding machine and leading into the mold cavity. By optimizing the runner system, manufacturers can ensure a smooth and efficient flow of plastic.
Key Characteristics of Runners
- Main Runner: This is the main path from the nozzle to the branch runner. It must be designed to minimize pressure loss and temperature drop during injection. A typical taper angle for the main runner is between 2° – 6°, which aids in maintaining the melt’s forward movement. I remember a project where changing the taper angle from 4° to 5° greatly improved production efficiency.
Feature | Description |
---|---|
Function | Connects nozzle to mold, minimizes pressure loss |
Taper Angle | Typically 2° – 6° |
Design Considerations | Must accommodate melt flow and minimize heat loss |
- Branch Runner: These channels connect to gates and spread the plastic evenly. Various shapes, such as circular and trapezoidal, can affect flow performance significantly. I’ve found that trying different shapes can change flow performance a lot; each shape has unique benefits and drawbacks.
Importance of Gate Design
The gate is crucial as it is the last point before plastic enters the mold cavity. Its size and shape affect surface finish and structural strength. For example:
- Side Gate: Suitable for small to medium products; allows smooth entry from the side.
- Point Gate: Ideal for high-quality appearance products; requires higher injection pressure but leaves minimal surface marks.
I worked on a product where changing from a side gate to a point gate improved looks and reduced surface marks significantly.
Gate Type | Suitable For | Advantages |
---|---|---|
Side Gate | Small/Medium Products | Smooth entry, fewer flow disruptions |
Point Gate | High Appearance Products | Minimal surface marks, better aesthetics |
Benefits of Runner Optimization
Here is why runner optimization matters:
- Improved Flow Efficiency: A proper runner system reduces pressure loss ensuring smoother mold cavity filling. I’ve seen this improve performance in my projects.
- Reduced Cycle Times: Good runners shorten production cycles by decreasing delays from flow issues; I recall how a basic redesign cut our cycle time by nearly 20%.
- Consistent Products: With refined runners, differences in size and quality drop resulting in uniform products which designers aim for.
- Less Waste: Optimized runners not only upgrade quality but also reduce waste benefiting both cost and sustainability; I am always enthusiastic about being more eco-friendly in manufacturing.
To dive deeper into specific techniques for optimizing runners, explore advanced runner design techniques9. This resource provides insights into practical approaches that can be implemented in modern manufacturing processes.
Optimizing runners reduces pressure loss in injection molding.True
Effective runner design minimizes pressure loss, ensuring efficient melt flow and improved product quality during the injection molding process.
Branch runners do not affect plastic flow performance.False
The shape and design of branch runners significantly impact how evenly plastic flows, affecting the overall quality of the molded product.
Conclusion
Runners in plastic molding are essential for efficient melt flow, affecting production speed and product quality. Understanding their design can significantly enhance manufacturing outcomes.
-
This link provides an in-depth exploration of runner systems, enhancing your understanding and application in design processes. ↩
-
Explore best practices for configuring runner systems to improve efficiency and product quality in your projects. ↩
-
Learn how optimizing runner design can improve your manufacturing processes, saving time and costs while enhancing product quality. ↩
-
Explore detailed examples of different gate designs and their effects on production to enhance your understanding. ↩
-
This link provides insights into common problems faced in injection molding runner systems and solutions to optimize performance. ↩
-
Learn how to achieve uniform melt distribution with effective runner designs. ↩
-
Understand best practices for maintaining temperature control in runner systems for improved outcomes. ↩
-
Discover how to minimize pressure loss in runner systems to enhance production efficiency. ↩
-
This link offers advanced insights into runner optimization techniques that can significantly enhance your manufacturing processes. ↩