Navigating the world of PVC injection molding can feel daunting, especially when scorching issues arise. Let me share my journey with you—because I’ve been there too!
To effectively resolve PVC injection molding material scorching, adjust process parameters like barrel temperature, injection speed, and pressure. Optimize mold design with improved exhaust and gate adjustments, choose stable materials, and maintain equipment regularly.
While these initial adjustments provide a solid foundation for resolving scorching issues, delving deeper into each area can yield even more effective results. Let’s explore these strategies in detail to enhance your understanding and application in real-world scenarios.
High barrel temperatures cause PVC scorching.True
Excessive heat leads to premature PVC decomposition, resulting in burning.
What Are the Common Causes of PVC Scorching in Injection Molding?
Understanding the root causes of PVC scorching in injection molding is crucial for maintaining product integrity and minimizing waste.
PVC scorching in injection molding is primarily caused by high barrel temperatures, fast injection speeds, excessive pressure, poor mold exhaust, and unsuitable materials.
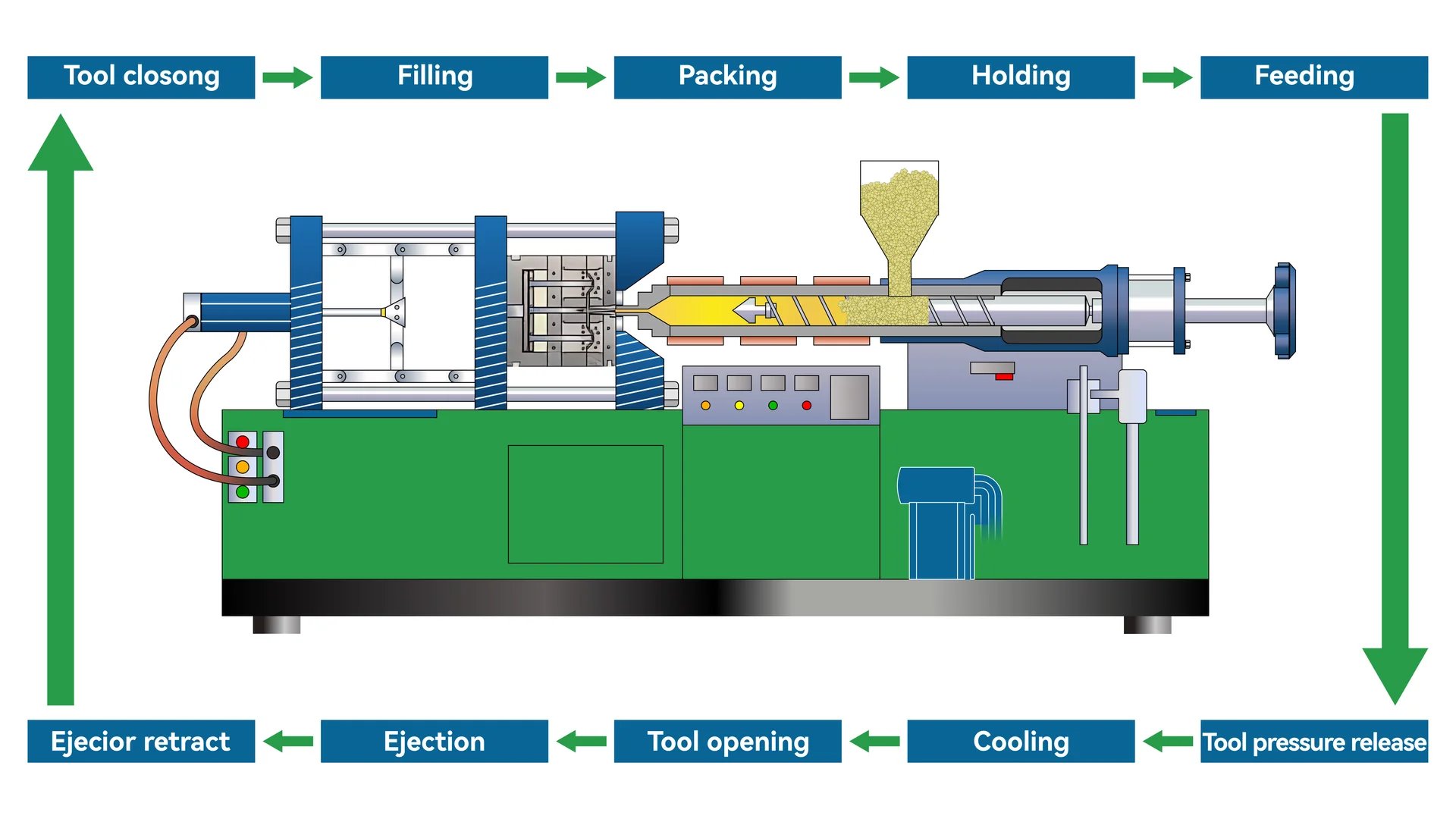
High Barrel Temperatures
One of the most common causes of PVC scorching is excessively high barrel temperatures. When the temperature is too high, it can lead to premature decomposition of the PVC material inside the barrel, resulting in burning.
Solution: Gradually reduce the temperature settings of each section of the barrel, the minimum melting temperature of PVC is 170 °C, particularly around the nozzle, by increments of 5-10°C. Observe changes in product quality to find an optimal temperature range.
Fast Injection Speeds
Fast injection speeds generate significant shear heat within the mold cavity, increasing the risk of scorching. This shear heat arises from the rapid movement of PVC through the narrow confines of the mold.
Solution: Slow down the injection speed to reduce shear heat. Adjust these parameters incrementally and continuously monitor product quality to prevent defects while minimizing burning risk.
Excessive Injection Pressure
Too much pressure can cause the PVC material to flow too quickly, generating excessive friction heat. This excess heat leads to scorching as the material cannot dissipate the generated heat efficiently.
Solution: Lower the injection pressure gradually based on product structure and size. Ensure any adjustments maintain product standards while reducing scorching risks.
Poor Mold Exhaust
If a mold doesn’t allow air and volatiles to escape efficiently, these elements can react with PVC at high temperatures, causing burning.
Solution: Improve mold exhaust by enlarging or increasing the number of exhaust grooves. Consider placing these grooves strategically on parting surfaces or utilizing vacuum exhaust methods for enhanced efficiency.
Unsuitable Materials and Additives
The choice of materials significantly influences the risk of scorching. PVC with poor thermal stability is more prone to degradation under heat.
Solution: Opt for PVC with superior thermal stability. Consult suppliers for thermal stability indicators and conduct small-batch tests to verify material suitability. Adding heat stabilizers like lead salts or organic tin can also enhance stability and reduce burning.
By addressing these key areas, manufacturers can significantly reduce the incidence of scorching in PVC injection molding, leading to higher quality products and more efficient production processes. Learn more about optimizing injection molding parameters1.
High barrel temperatures cause PVC scorching.True
Excessive heat decomposes PVC, leading to burning.
Fast injection speeds reduce PVC scorching risk.False
Rapid speeds generate shear heat, increasing scorching risk.
How Can Process Parameter Adjustments Prevent Scorching?
Process parameter adjustments are crucial in preventing scorching during PVC injection molding, ensuring product integrity and consistency.
Adjusting process parameters such as barrel temperature, injection speed, and pressure can significantly reduce the risk of PVC material scorching. By fine-tuning these variables, manufacturers can prevent premature decomposition, minimize shear heating, and maintain optimal flow dynamics within the mold.

Adjusting Barrel Temperature
One of the primary causes of scorching in PVC injection molding is excessive barrel temperature, leading to premature decomposition of the material. To mitigate this, manufacturers should gradually reduce the temperature2 across different sections of the barrel. The nozzle area requires particular attention, as it directly influences the material’s entry into the mold. A recommended adjustment range is between 5-10℃ to avoid abrupt changes that might affect product quality. Observing the finished product’s quality after each adjustment helps determine the optimal temperature settings.
Modulating Injection Speed
High injection speeds can cause increased shear heat within the mold cavity, escalating the risk of scorching. By lowering the injection speed3, manufacturers can decrease shear forces and subsequent heat generation. This step involves carefully adjusting the machine’s speed settings and observing changes in product fill and quality. It’s crucial to balance speed reduction with maintaining adequate mold filling to prevent defects.
Controlling Injection Pressure
Excessive injection pressure can induce fast material flow, generating friction heat and potential burning. Reducing the pressure ensures that the material flows steadily without excessive friction. Manufacturers should adjust the pressure settings4 according to product size and design complexity, ensuring that product quality remains uncompromised while minimizing scorching risks. Careful observation during this process is essential to find a balance that meets product requirements without burning issues.
By focusing on these key process parameters, manufacturers can effectively prevent scorching during PVC injection molding, safeguarding product quality and consistency. These adjustments form a pivotal part of a broader strategy to combat scorching, alongside mold design optimization and material selection.
Reducing barrel temperature prevents PVC scorching.True
Lowering the barrel temperature minimizes premature decomposition of PVC.
Increasing injection speed reduces scorching risk.False
Higher speeds increase shear heat, raising the scorching risk.
Why Is Mold Design Crucial in Reducing PVC Scorching?
Mold design plays a pivotal role in mitigating PVC scorching during injection molding, impacting exhaust efficiency and material flow.
Effective mold design minimizes PVC scorching by enhancing exhaust systems and optimizing gate positions and sizes, ensuring even material flow and temperature control.
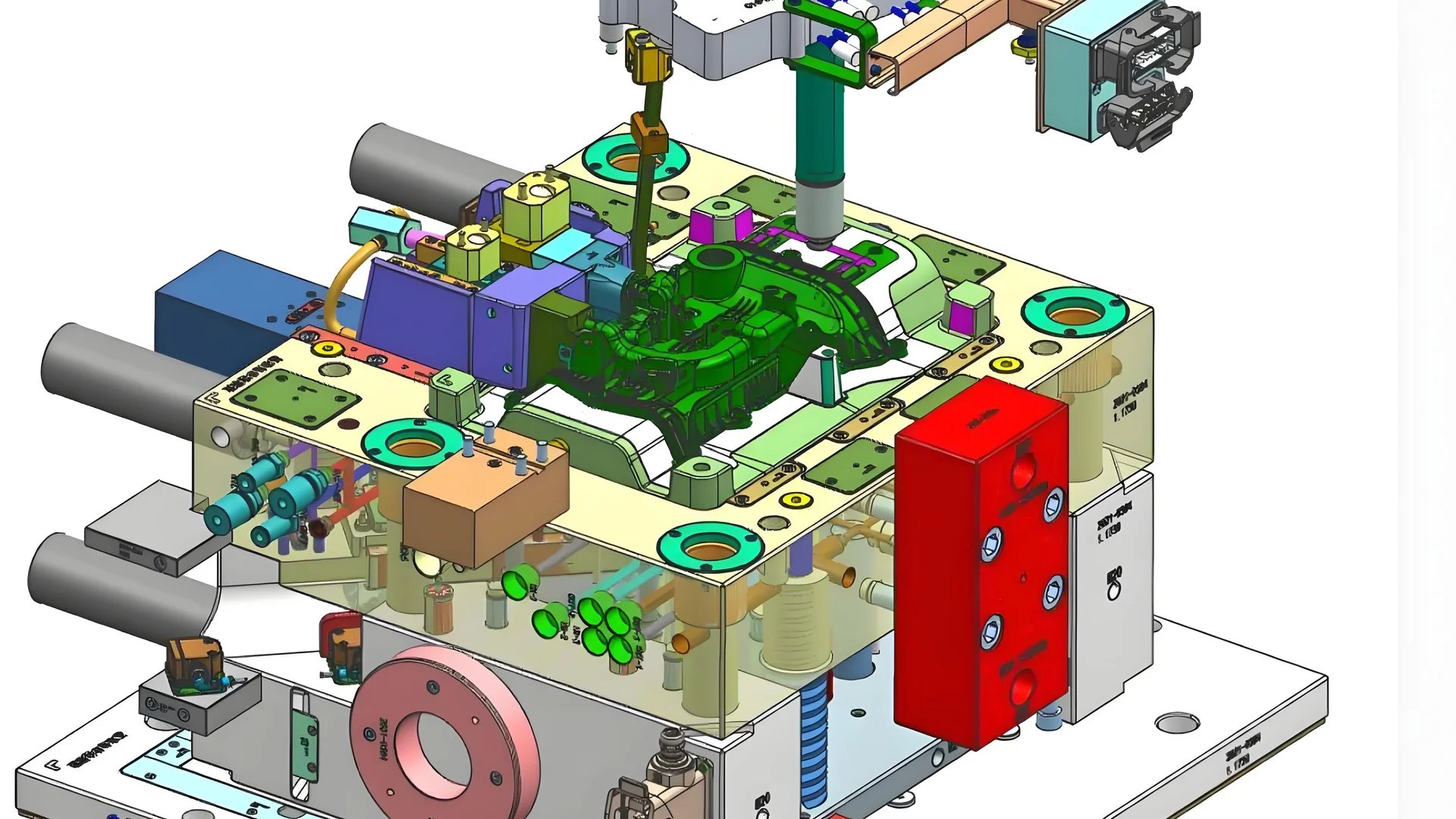
Enhancing Mold Exhaust Systems
One of the primary roles of mold design in reducing PVC scorching is enhancing the mold’s exhaust capabilities. Inadequate exhaust can trap air and volatile compounds within the mold cavity, which can lead to reactions at high temperatures, causing material scorching. To combat this, increasing the number and size of exhaust grooves can significantly improve airflow. Position these grooves on strategic parts of the mold like the parting surface, sliders, and inserts. Employing auxiliary methods such as vacuum exhaust can further ensure efficient removal of air and volatiles.
For example, consider a case where a manufacturer encountered persistent scorching due to poor mold exhaust. By redesigning the mold to incorporate larger and more numerous exhaust channels, they observed a substantial reduction in scorching incidents.
Optimizing Gate Position and Size
The positioning and size of gates also play a critical role in preventing local overheating and scorching. When gates are poorly positioned or sized, it can cause uneven material flow, leading to hotspots where scorching is more likely to occur. By carefully designing gate locations to ensure uniform flow throughout the mold cavity, scorching risks can be minimized.
Utilizing designs such as multi-point or fan-shaped gates can enhance material fluidity and distribute heat more evenly. For instance, a study showed that adjusting gate sizes according to the product’s geometry reduced overheating and improved the final product quality significantly.
Case Study: Implementing Design Changes
In a practical application, a company facing severe scorching issues revamped their mold design by focusing on exhaust improvements and gate optimization. These changes resulted in reduced cycle times and enhanced product quality, showcasing the importance of thoughtful mold design.
-
Before Design Changes
- High incidence of scorching
- Inconsistent product quality
- Long cycle times
-
After Design Changes
- Significant reduction in scorching
- Consistent product quality
- Reduced cycle times
The case underscores that even minor adjustments in mold design can lead to substantial improvements in the manufacturing process. Implementing these strategies can make a significant difference in both productivity and quality in PVC injection molding.
By adopting these mold design techniques, manufacturers can not only reduce the risk of PVC scorching but also enhance overall production efficiency. For further insights on this topic, consider exploring injection molding exhaust systems5 and gate design optimization6.
Mold exhaust systems reduce PVC scorching risk.True
Enhanced exhaust systems improve airflow, preventing overheating.
Poor gate design increases PVC scorching.True
Incorrect gate positioning causes uneven flow and hotspots.
What Role Do Materials and Additives Play in Combating Scorching?
PVC injection molding is a widely used manufacturing process, but scorching issues can often compromise the quality of the final product.
Choosing PVC materials with good thermal stability and incorporating heat stabilizers are crucial in preventing scorching during injection molding.
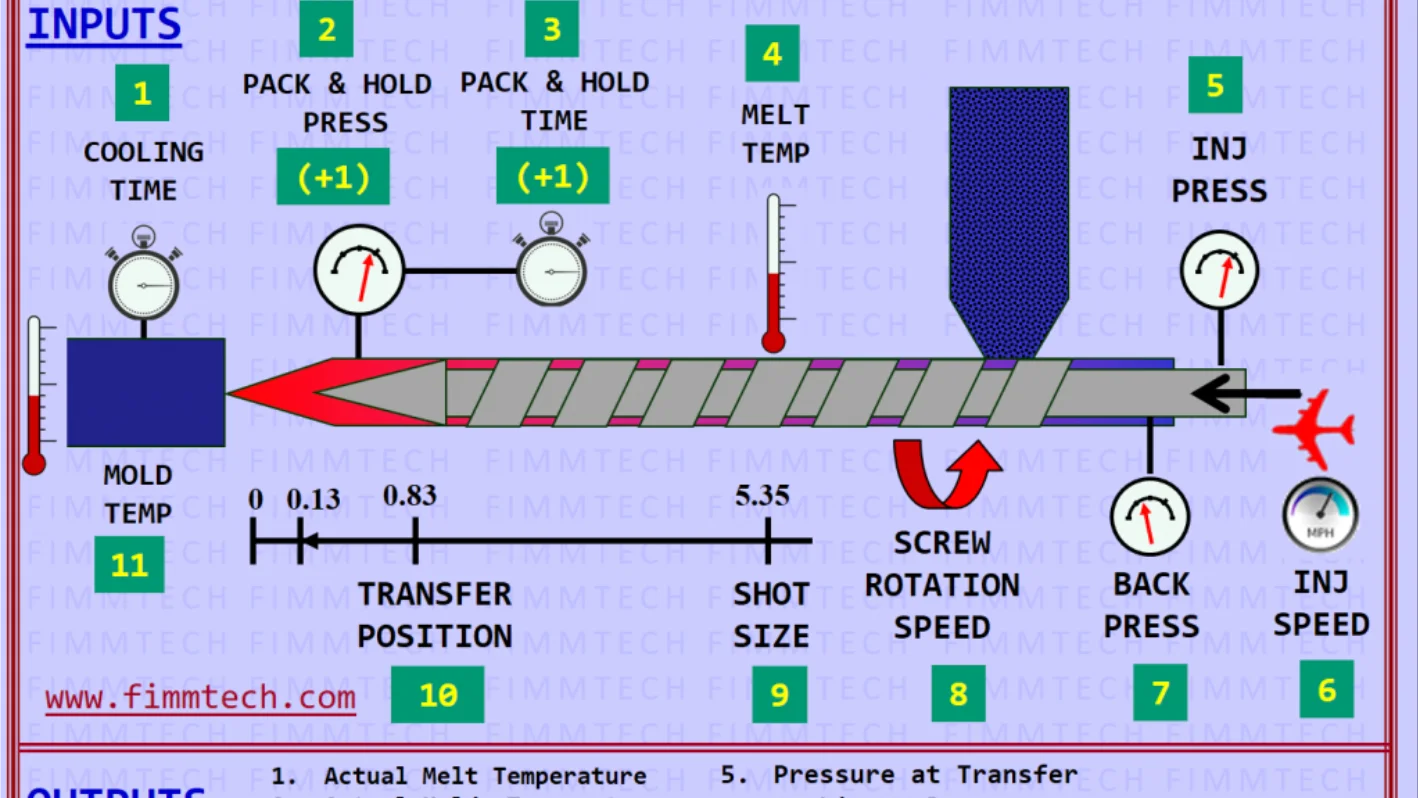
Choosing the Right PVC Materials
The first step in preventing scorching during PVC injection molding is selecting materials with superior thermal stability. Manufacturers often provide thermal stability indicators such as thermal decomposition temperature and thermal weight loss. By choosing materials with higher thresholds, you can reduce the likelihood of premature burning. It’s advisable to consult your supplier7 for these specific indicators and conduct small-scale tests to ensure compatibility with your product requirements.
Incorporating Heat Stabilizers
Heat stabilizers play a significant role in enhancing the thermal stability of PVC materials. By adding these additives, the material’s resistance to decomposition and burning during processing is improved. Popular choices include lead salts, organic tin, and calcium zinc stabilizers. When selecting a stabilizer, consider factors such as compatibility with the PVC material and environmental impact. Opting for environmentally friendly stabilizers can not only mitigate scorching but also align with sustainability goals.
Type of Stabilizer | Advantages | Considerations |
---|---|---|
Lead Salts | Cost-effective, high efficiency | Environmental concerns, toxicity |
Organic Tin | Excellent thermal stability | Higher cost, requires precise dosing |
Calcium Zinc | Non-toxic, eco-friendly | May require higher concentrations |
The Balance Between Material Choice and Additives
Balancing the choice of material with the right additives is essential for achieving optimal results. While selecting a material with excellent inherent thermal stability is beneficial, combining it with the right heat stabilizer can further reduce the risk of scorching. This combination allows for a more controlled molding process where material integrity is maintained even under stress.
To ensure effective results, it’s crucial to monitor how these materials and additives interact during the injection process. Regular testing and adjustments based on real-time feedback can significantly enhance the quality and durability of the final product. Experimenting with different stabilizer types and concentrations may also yield surprising improvements in performance.
Ultimately, understanding the unique properties of your chosen materials and how they interact with selected additives allows for more nuanced control over the injection molding process. This detailed approach not only minimizes scorching risks but also enhances overall product quality and consistency.
PVC materials with high thermal stability prevent scorching.True
Selecting PVC materials with superior thermal stability reduces burning risk.
Lead salts are the most eco-friendly stabilizers for PVC.False
Lead salts are effective but have environmental and toxicity concerns.
Conclusion
By systematically addressing process parameters, mold design, material selection, and equipment upkeep, you can significantly reduce PVC scorching. Implement these expert-recommended strategies to optimize your injection molding operations and enhance product quality.
-
Discover expert strategies to fine-tune molding parameters effectively.: The 8 Key Parameters in Injection Molding Process Optimization to Avoid Defects · 1. Temperature Control: · 2. Injection Speed: · 3. Cooling Time:. ↩
-
Learn precise techniques for managing barrel temperature effectively.: Shown here are the four basic barrel zones on an injection molding machine that must be set up properly, along with the nozzle body and tip. ↩
-
Discover how slowing down injection speed benefits molding outcomes.: If multiple injection speeds may be of value, best practice is using the injection profiling procedure. Utilize injection positions and the … ↩
-
Explore methods for controlling pressure to prevent scorching.: 1. Screw rotation in the plasticizing stage. 2. Slider feeder (the nozzle is close to the nozzle bushing). 3. Axial movement of the injection screw during … ↩
-
Discover how improved exhaust systems can prevent PVC scorching.: Why do injection molds have exhaust systems · 1) Air in the gating system and mold cavity. · 2) Some raw materials contain water that has not … ↩
-
Learn about optimizing gate design for even material flow.: In this paper, we develop a general methodology for gate location optimization. We first quantify quality in terms of flow simulation outputs. We can thus … ↩
-
Learn about key stability indicators crucial for material selection.: This overview will help to gain a profound understanding of the current state of PVC-based composites and nanocomposites in the context of thermal properties … ↩