Injection molding is more than just a manufacturing technique; it’s a science that requires precision and understanding. Warping deformation, however, is a challenge many of us face.
To effectively reduce warping deformation in injection molding, focus on optimizing material selection, mold design, molding process parameters, and product design. Each factor plays a critical role in minimizing defects and ensuring high-quality production.
While these initial solutions might sound straightforward, truly mastering them requires diving deeper into each aspect. Trust me, the insights ahead will be invaluable!
Material selection affects warping in injection molding.True
Material properties like shrinkage and thermal expansion influence warping.
What Role Does Material Selection Play in Reducing Warping?
Choosing the right material is crucial to minimizing warping in injection molding.
Material selection significantly affects warping by influencing shrinkage rates and thermal expansion. Choosing materials with consistent shrinkage and low thermal expansion can reduce warping, ensuring more precise and durable final products.
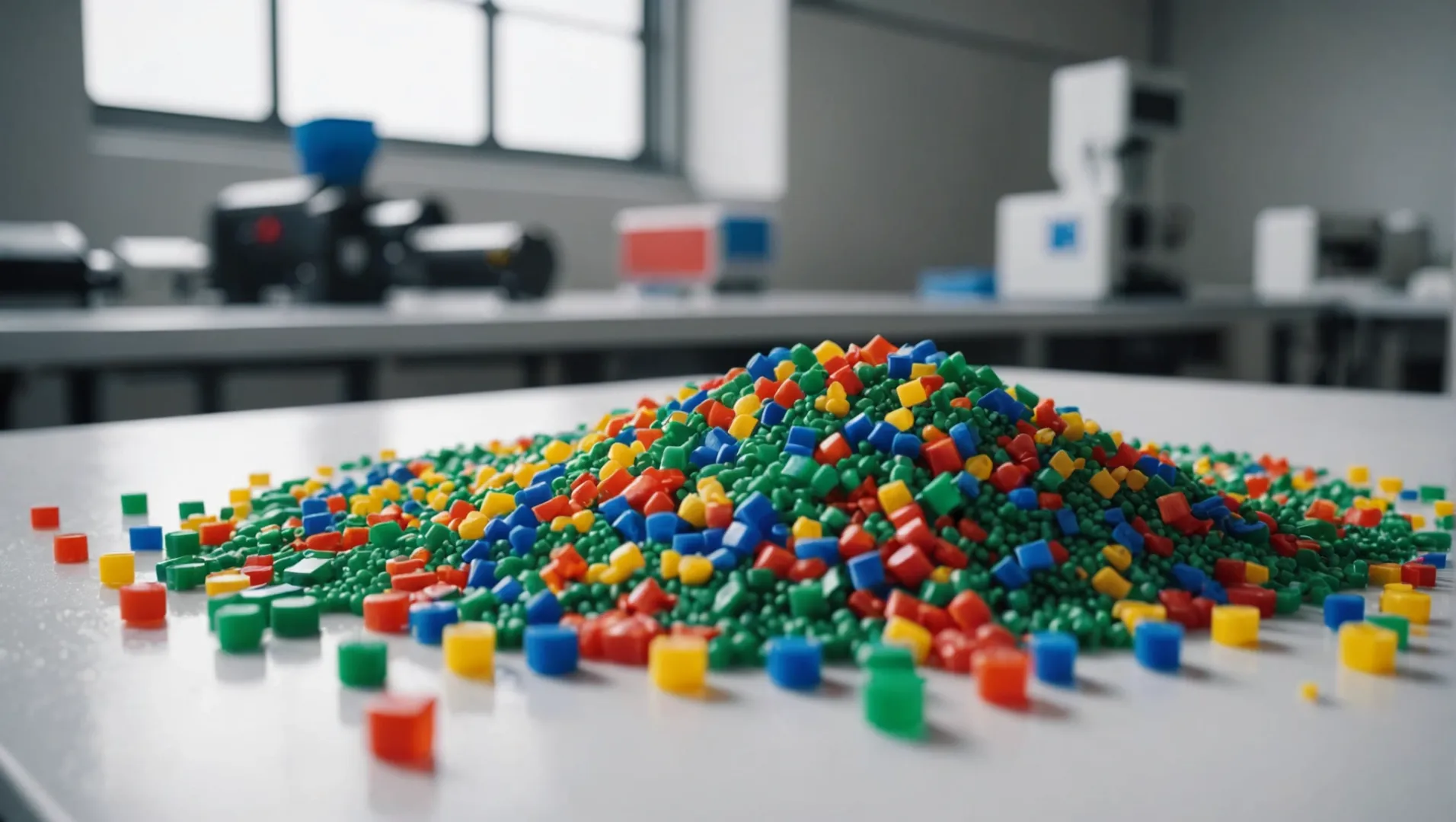
Understanding Material Properties
Warping is often a result of uneven shrinkage during the cooling phase of injection molding. Different materials have varied shrinkage rates1 and thermal expansion coefficients, which directly impact how much a molded part will warp. For instance, semi-crystalline plastics like polypropylene tend to have higher shrinkage rates compared to amorphous plastics such as polystyrene. Selecting materials with minimal differential shrinkage can significantly decrease warpage.
Evaluating Thermal Expansion
Materials with low thermal expansion coefficients are less likely to warp as they cool. This is particularly important for parts that will be exposed to fluctuating temperatures post-production. Engineers often consult material data sheets to ensure that the chosen plastic will perform consistently under expected operating conditions.
Material Type | Shrinkage Rate (%) | Thermal Expansion Coefficient (x10^-5/K) |
---|---|---|
Polypropylene | 1.5 – 2.5 | 11 – 15 |
Polystyrene | 0.4 – 0.8 | 7 – 9 |
ABS | 0.5 – 0.7 | 7 – 9 |
Considering Composite Materials
In some cases, composite materials or filled plastics can offer enhanced stability. Adding fillers like glass or carbon fibers can lower the material’s overall shrinkage rate and increase rigidity, which helps mitigate warping. However, these additions may alter other material properties, such as flexibility or weight, requiring a balanced approach.
Practical Application in Design
The choice of material should be integrated early in the design phase, not as an afterthought. Engineers should work closely with designers to understand the functional requirements and environmental conditions of the final product. By selecting a material tailored to these specific needs, the likelihood of warping can be substantially reduced.
Ultimately, the role of material selection in reducing warping cannot be overstated. It forms the foundation upon which other measures—such as mold design and process parameters—build to achieve optimal results.
Polypropylene has a higher shrinkage rate than polystyrene.True
Polypropylene's shrinkage rate ranges from 1.5% to 2.5%, higher than polystyrene's 0.4% to 0.8%.
Composite materials always increase warping in molded parts.False
Composite materials can reduce warping by lowering shrinkage rates and increasing rigidity.
How Does Mold Design Impact Warping Deformation?
Mold design is pivotal in determining the extent of warping deformation in injection molded products.
Mold design significantly impacts warping deformation by influencing cooling uniformity, gate placement, and structural reinforcement. Optimal design can mitigate defects, ensuring dimensional stability.
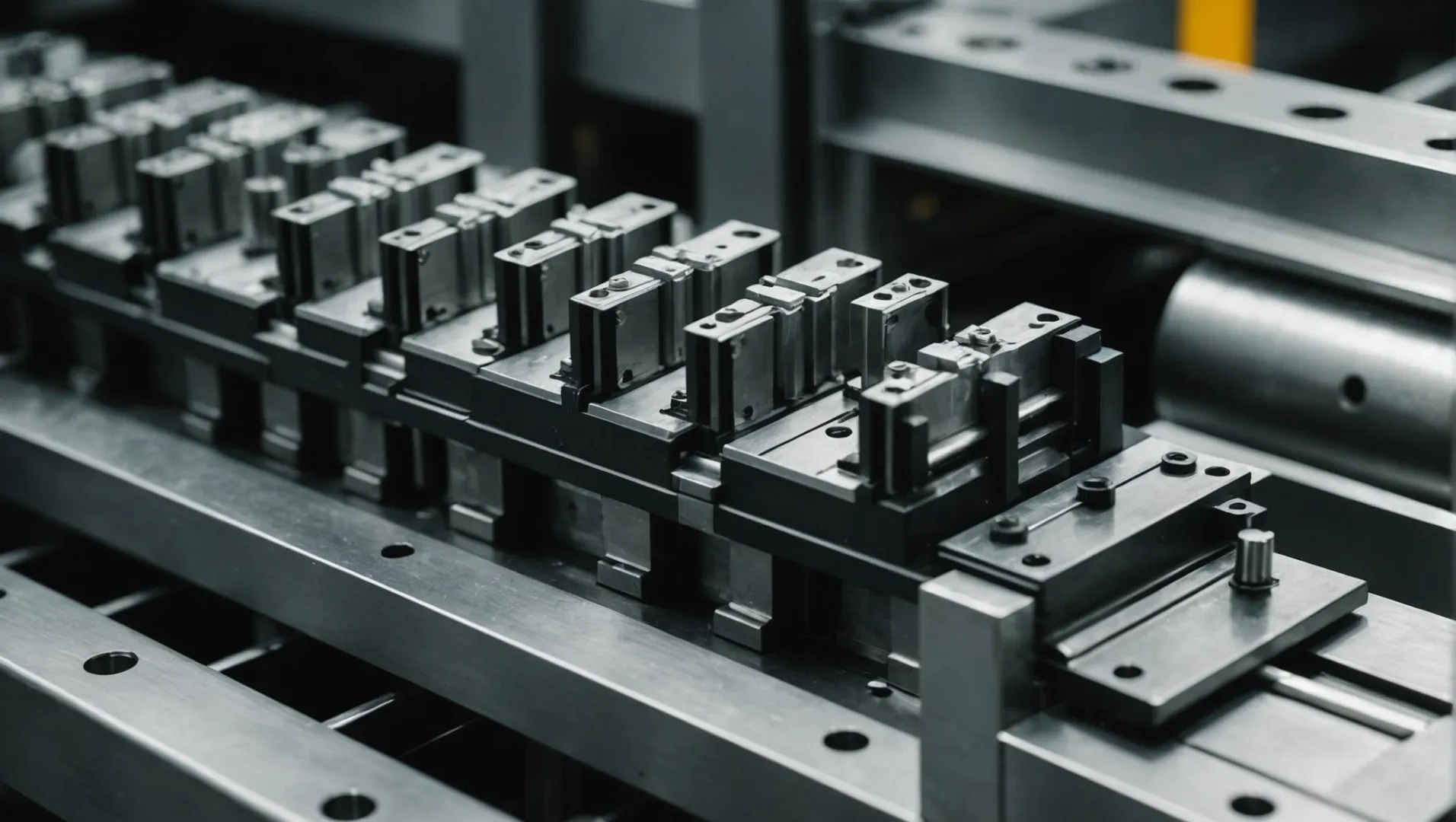
Understanding the Basics of Mold Design
The mold is the framework that shapes plastic into the desired form during injection molding. A well-designed mold considers factors like material properties, part geometry, and cooling systems. The primary aim is to achieve uniform cooling and shrinkage, which directly affects warping.
Cooling System Configuration
The cooling system within a mold plays a crucial role in determining the final shape and quality of the molded part. Inadequate or uneven cooling can lead to temperature gradients, causing differential shrinkage and subsequent warping. Increasing the number of cooling channels and optimizing their layout can significantly enhance cooling efficiency.
For instance, incorporating conformal cooling channels that follow the contour of the part can lead to more uniform temperature distribution and reduced warpage.
Gate Placement and Size
Gate placement and size are critical aspects of mold design that impact material flow and cooling. Proper gate location ensures even distribution of molten material, minimizing stress concentrations and potential deformation.
When gates are too small or incorrectly positioned, they can cause imbalanced flow, leading to differential shrinkage and warpage. Optimizing these parameters helps ensure that the material fills the cavity uniformly, reducing the risk of defects.
Structural Reinforcement with Ribs
Adding ribs to a design can bolster structural integrity and minimize warping. Ribs increase rigidity without significantly adding to weight or material cost. They also aid in controlling shrinkage rates by acting as support structures within the mold.
However, it is crucial to design ribs with care to avoid sink marks or stress concentrations. Balancing rib thickness and spacing is key to optimizing their effectiveness in preventing warpage.
Practical Strategies for Optimizing Mold Design
To achieve effective mold design:
- Use software simulations: These tools can predict potential warping issues by simulating the molding process, allowing designers to tweak parameters before production.
- Collaborate with material specialists: Different plastics behave uniquely under similar conditions. Engaging with material experts ensures the chosen material complements the mold design for minimal warping.
- Conduct iterative testing: Prototype molds should be tested under various conditions to assess their performance and refine designs before mass production.
By focusing on these aspects, manufacturers can significantly reduce warping deformation, leading to higher quality products and reduced wastage. For further insights on optimizing mold design, explore advanced molding techniques2.
Cooling channels reduce warping deformation.True
More cooling channels enhance uniformity, reducing differential shrinkage.
Ribs increase weight and cost significantly.False
Ribs add rigidity with minimal weight or cost increase, reducing warping.
Which Molding Process Parameters Are Crucial for Minimizing Warpage?
Understanding the crucial parameters in molding can significantly minimize warpage, a common defect in injection molding.
Key molding process parameters crucial for minimizing warpage include controlling injection temperature, pressure, and cooling time. Adjusting these parameters can lead to reduced stress within the molded part, thereby decreasing the likelihood of warpage and enhancing product quality.
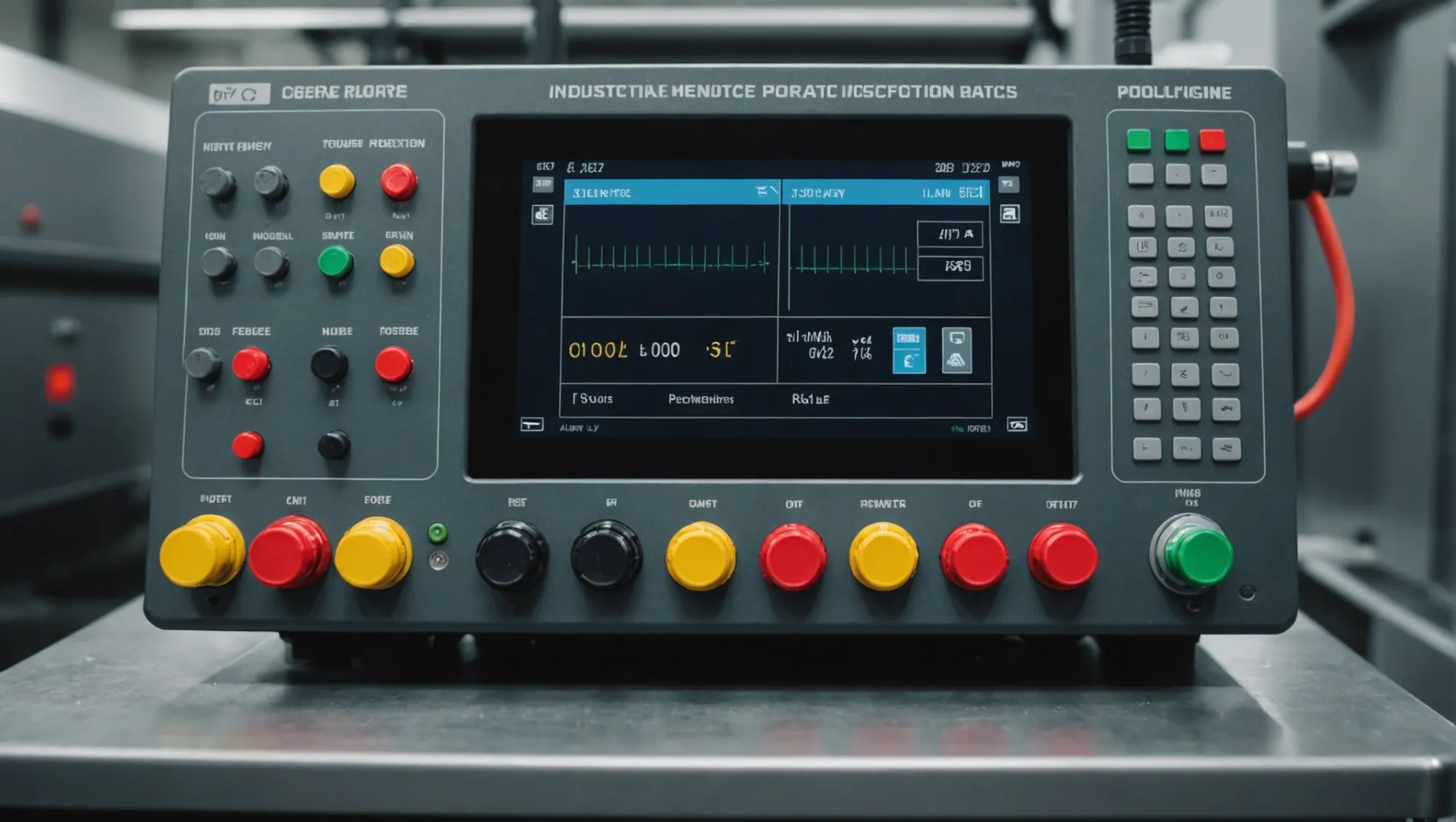
Understanding Injection Temperature
Injection temperature significantly influences the viscosity of the plastic melt. A higher temperature may lead to less resistance during flow but can also increase shrinkage and subsequently, warpage. By carefully controlling the injection temperature3, manufacturers can strike a balance that minimizes these risks.
The Role of Injection Pressure
The injection pressure directly affects the filling of the mold cavity. While high pressure ensures complete filling, it can also induce residual stress, leading to warpage. Lowering injection pressure where feasible, while maintaining part integrity, is advisable. Techniques such as pressure profiling can be employed to optimize this parameter effectively.
Optimizing Cooling Time
Cooling time is another critical parameter. Insufficient cooling can result in uneven shrinkage and increased warpage. Extending the cooling time allows for more uniform solidification of the part, reducing internal stresses. Implementing an efficient cooling system within the mold design can further aid in achieving optimal results.
Importance of Holding Time
Holding time affects how long the pressure is maintained after the cavity has filled. This parameter helps in compensating for material shrinkage and ensures even density throughout the part. Increasing holding time can help in reducing voids and sink marks, thus minimizing warpage.
Balancing All Parameters
Achieving minimal warpage requires a delicate balance of all these parameters. For instance, adjusting cooling time might necessitate changes in injection pressure or temperature. Understanding the interplay of these variables is crucial for developing a robust molding process that consistently delivers high-quality products.
By focusing on these key parameters, manufacturers can significantly minimize warpage, ensuring product reliability and customer satisfaction.
Higher injection temperature increases warpage risk.True
Higher temperatures can increase shrinkage, leading to warpage.
Longer cooling time reduces warpage in molded parts.True
Extended cooling allows uniform solidification, reducing stress.
Why Is Product Design Essential in Preventing Warping Deformation?
Product design is pivotal in minimizing warping deformation during injection molding, impacting the final product’s quality.
Product design is essential in preventing warping deformation as it directly influences the uniformity of wall thickness and the structural complexity of the product. By optimizing these design aspects, manufacturers can significantly reduce warpage, ensuring higher precision and performance in injection-molded parts.
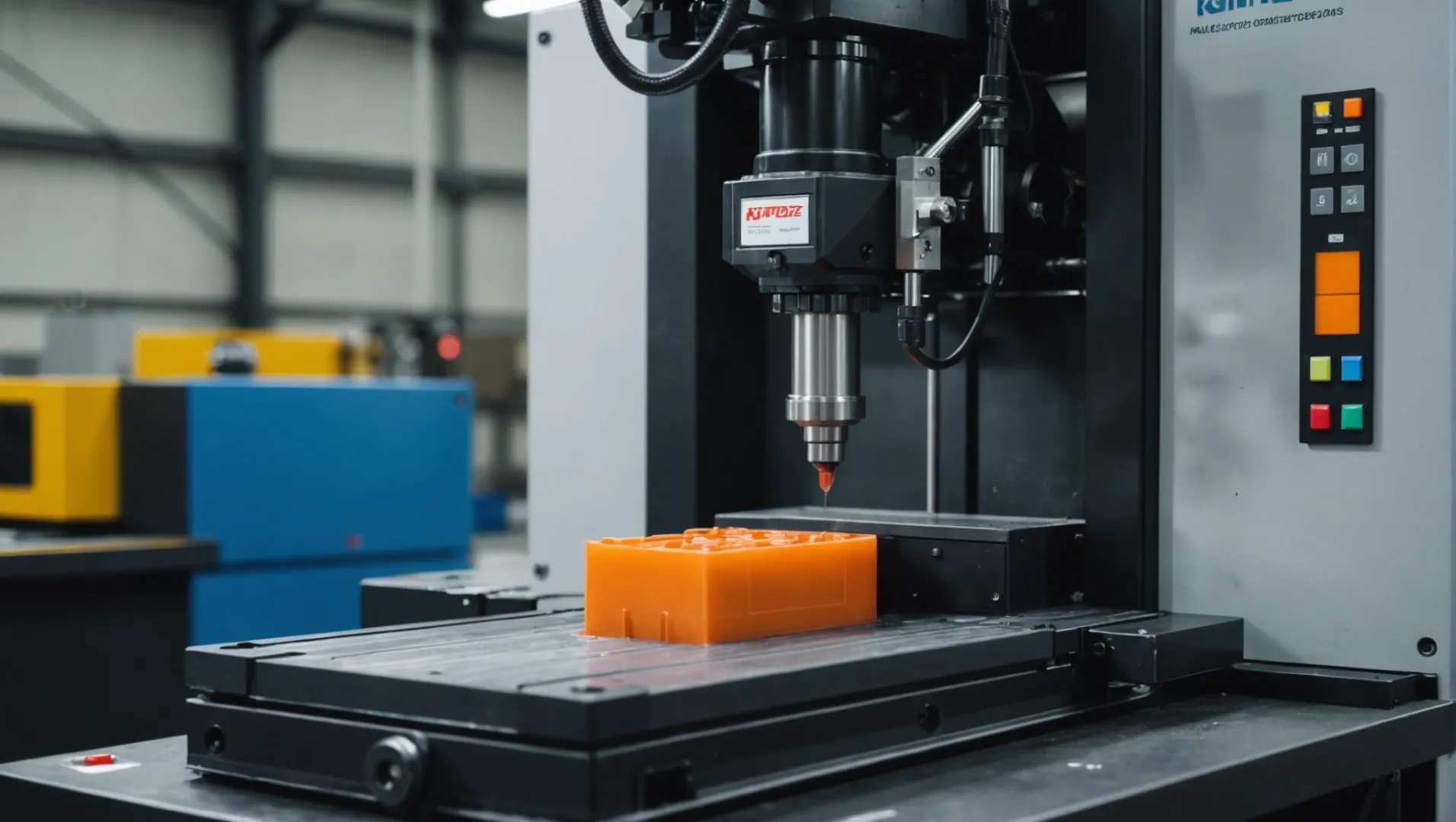
The Importance of Uniform Wall Thickness
Uniform wall thickness is crucial in mitigating warping deformation. Inconsistent thickness can lead to uneven cooling and shrinkage, resulting in distortions. Designers should aim for consistent wall thickness throughout the product to promote uniform thermal expansion and contraction. This practice minimizes internal stresses that cause warping.
Reducing Structural Complexity
Complex structures often contribute to warping due to varied stress distributions. Simplifying the design, without compromising on functionality, can be beneficial. Avoid sharp corners and sudden changes in thickness, which can create stress concentration points. Instead, use gradual transitions to maintain an even stress distribution.
Reinforcement Features
Incorporating reinforcement ribs is another strategy to enhance rigidity and reduce warping. These features provide structural support without adding excessive material, which can exacerbate warpage. It’s crucial to place ribs strategically to reinforce weak sections while maintaining uniformity across the product.
Case Studies: Successful Product Design Strategies
Example 1: Automotive Parts
For automotive components, achieving a balance between lightweight and strength is vital. By implementing consistent wall thickness and strategic rib placement, manufacturers have successfully reduced warping in large panels like dashboards.
Example 2: Consumer Electronics
In the realm of consumer electronics, devices like smartphones demand high precision. Designers focus on simplifying internal structures and enhancing uniformity to prevent deformation under thermal stress.
Innovative Approaches in Product Design
Innovative techniques such as deformation pre-compensation4 can further mitigate warpage. This involves predicting potential deformations and adjusting the design accordingly, ensuring the final product meets specifications despite inherent material and process challenges.
Uniform wall thickness reduces warping in molding.True
Consistent thickness ensures even cooling, minimizing deformation.
Sharp corners improve structural integrity in design.False
Sharp corners cause stress concentration, increasing warping risk.
Conclusion
By strategically addressing material choice, mold design, and process parameters, we can significantly minimize warping and enhance product quality.
-
Learn how shrinkage rates influence warping and improve material choices.: The difference in shrinkage between the in-plane and thickness directions can cause warpage, particularly in the corners of the part due to … ↩
-
Discover innovative techniques that enhance mold design and reduce defects.: Techniques for Reducing Warp and Sink in Injection Molded Parts · 1. Optimize Mold Design · 2. Material Selection and Handling · 3. Optimize … ↩
-
Learn how temperature adjustments can impact warpage in molded parts.: Uneven mold temperatures cause molecules to cool and shrink at an uneven rate, resulting in mold warpage. Solution: Check mold surfaces that are … ↩
-
Learn how pre-adjusting designs can counteract material warping.: Under optimized injection process conditions of automobile water chamber, pre-deformation compensation technology is adopted to control … ↩