As I delve into the world of injection molding, one thing becomes clear: uniform filling is paramount for quality.
To effectively reduce uneven filling in injection molding, consider optimizing plastic material selection, refining mold design, adjusting process parameters, and maintaining equipment. Each step plays a pivotal role in enhancing fill uniformity and overall product quality.
While these initial steps lay a solid foundation, the deeper insights we’ll explore can transform your injection molding process. Let’s dive into practical solutions and expert recommendations to tackle uneven filling head-on.
Material selection impacts injection molding quality.True
Choosing appropriate materials ensures optimal flow and reduces defects.
What Role Does Material Selection Play in Injection Molding?
Material selection in injection molding is critical, impacting the efficiency, quality, and cost-effectiveness of the production process.
Choosing the right material for injection molding ensures optimal flow characteristics, strength, and final product quality. Properly selected materials reduce defects like uneven filling and enhance production efficiency.
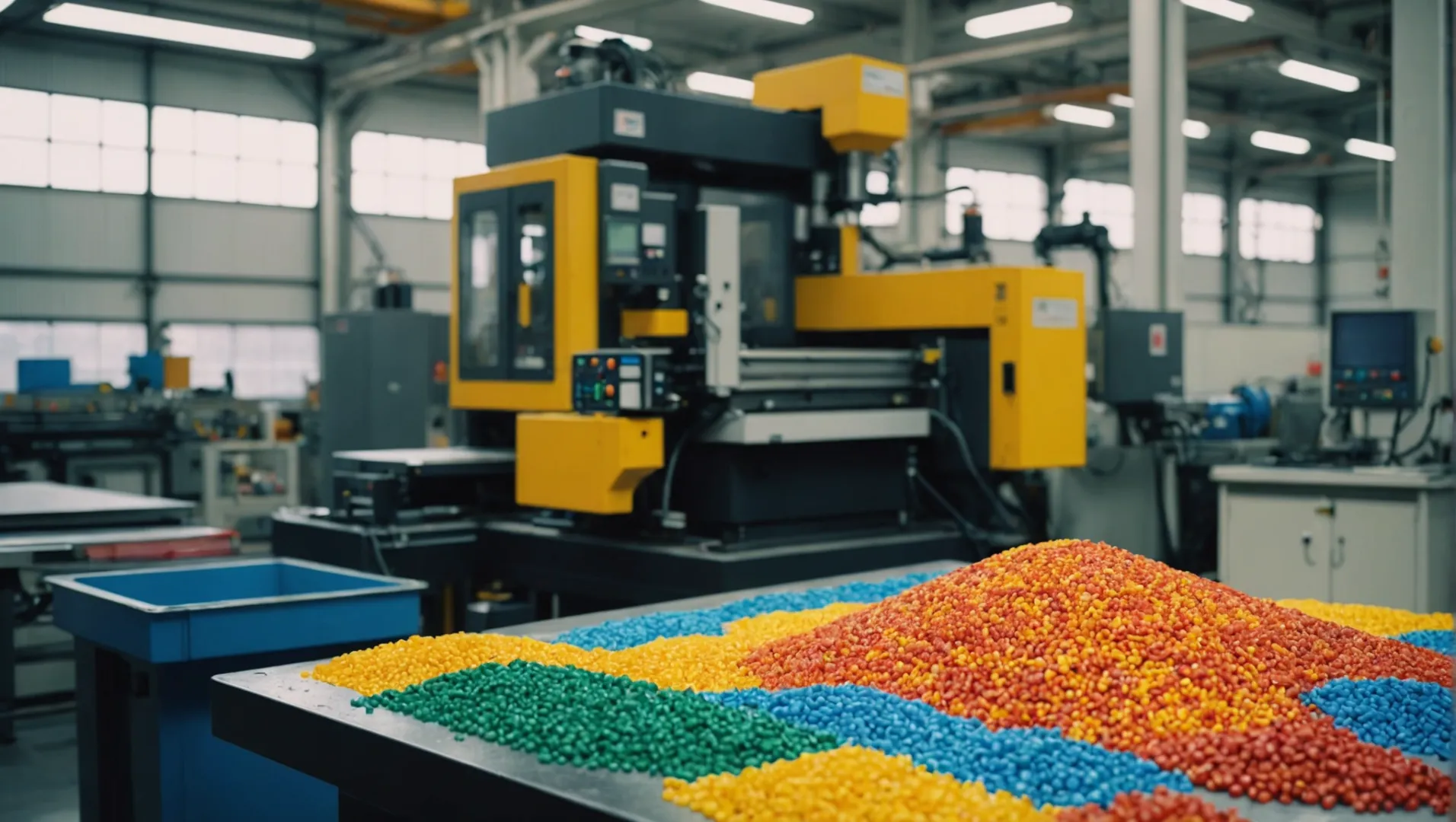
Understanding Material Characteristics
In injection molding, selecting the correct material begins with understanding its flow characteristics. Fluidity is a key factor influencing how well a material fills a mold. For complex structures or thin-walled parts, high-fluidity plastics are essential to ensure complete mold filling.
Moisture Content is another critical attribute. High moisture levels in plastic materials can lead to bubbles during injection, disrupting filling uniformity. Pre-drying materials like hygroscopic plastics ensures reduced moisture-related defects.
The Role of Additives
Adding Lubricants such as silicone oil can significantly improve the flow of plastics by reducing friction between the material and the mold walls. This aids in achieving uniform fill and reduces wear on the mold.
Modifiers can enhance the plastic’s properties, including fluidity and mechanical strength. These additives are selected based on specific product requirements, ensuring that the material performs optimally during the molding process.
Impact on Product Quality
The choice of material directly influences product quality. Material Compatibility with the intended application is vital. For instance, a product requiring high durability should be molded using a material with the requisite strength and temperature resistance.
Additionally, the wrong material choice can lead to warping or shrinkage, affecting the product’s dimensions and aesthetic appeal. Careful consideration of the material’s thermal expansion properties can mitigate these issues.
Cost Implications
Material selection also affects cost-efficiency. Opting for more expensive but better-suited materials can save costs in the long run by reducing wastage, minimizing defect rates, and enhancing production speed.
By investing in quality materials, manufacturers can avoid costly rework and returns due to poor-quality products, thereby safeguarding their reputation and customer satisfaction.
Table: Material Selection Factors
Factor | Impact on Injection Molding |
---|---|
Fluidity | Determines ease of mold filling |
Moisture Content | Affects bubble formation and fill uniformity |
Lubricants | Enhances flow, reduces mold friction |
Modifiers | Improves strength and flow characteristics |
Cost | Influences overall production efficiency and quality |
By thoroughly understanding these material properties, manufacturers can optimize their injection molding processes to produce high-quality, defect-free products consistently. For further insights into how specific materials behave under various conditions, explore our detailed material selection guide1.
High moisture in plastics causes bubbles in injection molding.True
Moisture leads to bubbles, disrupting uniform filling during molding.
Lubricants increase mold friction in injection molding.False
Lubricants reduce friction, aiding material flow and uniform filling.
How Can Mold Design Affect Filling Uniformity?
Mold design is a critical factor that influences the uniformity of filling in injection molding, impacting the quality and consistency of the final product.
Mold design significantly affects filling uniformity in injection molding by optimizing gate placement, runner systems, and mold temperature control. A well-designed mold ensures even distribution of plastic material, reducing defects and enhancing product integrity.

The Importance of Gate Location and Number
The positioning and number of gates in a mold are paramount to achieving uniform filling. Gates should ideally be placed in thicker sections of the product or away from areas with thin walls. This strategic positioning aids in distributing the plastic material evenly throughout the mold cavity. Implementing multiple gates or a hot runner system can further promote consistent flow and mitigate filling irregularities.
Design Feature | Impact on Filling Uniformity |
---|---|
Gate Location | Ensures even distribution of material |
Number of Gates | Multiple gates can balance flow distribution |
Hot Runner System | Promotes consistent material flow |
Designing an Efficient Runner System
The runner system serves as the conduit through which molten plastic travels to fill the mold cavity. The cross-sectional shape and size of the runner must be tailored to the plastic’s fluidity and product specifications. Typically, circular or trapezoidal runners offer superior fluidity, reducing resistance during flow. Additionally, shorter runners minimize pressure loss and temperature drop, enhancing flow consistency.
Avoiding sharp turns and dead ends in runner design is crucial to maintaining smooth flow and preventing disruptions that could lead to uneven filling.
Adjusting Mold Temperature for Optimal Filling
Temperature control within the mold has a profound impact on the viscosity and flow characteristics of the plastic. Raising the mold temperature can lower viscosity, thereby improving fluidity and ensuring more uniform filling. However, care must be taken to avoid excessively high temperatures that could degrade the plastic or deform the product.
To maintain a stable and uniform mold temperature, utilize equipment such as heating rods and oil temperature machines. Consistent temperature management facilitates better material flow and enhances overall filling uniformity.
By integrating these considerations into mold design, manufacturers can significantly improve the uniformity of filling, leading to higher quality and more reliable injection-molded products. For further insights, explore expert discussions on mold design optimization2.
Gate location affects material distribution.True
Strategic gate placement ensures even material flow, enhancing uniformity.
Hot runner systems increase filling irregularities.False
Hot runner systems promote consistent flow, reducing filling irregularities.
Which Process Adjustments Can Improve Filling Consistency?
In the world of injection molding, achieving consistent filling is key to producing defect-free products. Adjusting specific process parameters can make a significant difference.
To improve filling consistency in injection molding, adjust parameters such as injection pressure, speed, and barrel temperature. Fine-tuning these settings enhances the plastic’s fluidity, reduces defects, and ensures a uniform fill.

Adjusting Injection Molding Parameters
One of the foremost methods to enhance filling consistency is to meticulously fine-tune the injection molding parameters3. Increasing the injection pressure and speed can substantially improve the plastic’s ability to flow and fill the mold cavity uniformly. However, it’s crucial to balance these adjustments as excessive pressure and speed might lead to defects like plastic burning or flashing.
Moreover, extending the injection time can provide the plastic with ample opportunity to settle evenly within the mold. Yet, be cautious — too long of an injection time may reduce production efficiency and degrade product quality. Achieving the right balance between speed and time is pivotal for optimal results.
Controlling Barrel Temperature
The temperature of the barrel directly affects the viscosity of the plastic. By setting it according to the plastic’s properties, one can significantly influence the flow characteristics. A higher barrel temperature often lowers viscosity, thus enhancing flow and filling consistency. Yet, it is vital to avoid overheating, which can cause degradation or discoloration of the plastic.
Employing multi-stage heating and precise temperature control systems can help maintain a stable and uniform barrel temperature, thereby preventing localized hot spots or cold regions which could disrupt uniformity.
Pre-drying Treatment for Plastics
For plastics prone to absorbing moisture, a pre-drying treatment can be indispensable. This process removes excess moisture, improving both fluidity and filling consistency. The pre-drying time and temperature should be tailored to the specific type of plastic being used, ensuring that it’s adequately prepared for molding.
Benefits of Process Adjustments
Below is a summary table illustrating how each process adjustment impacts filling consistency:
Adjustment | Benefit |
---|---|
Increase Injection Pressure | Improves flow into cavities |
Optimize Injection Speed | Balances fill time and quality |
Control Barrel Temperature | Reduces viscosity for better flow |
Pre-drying Treatment | Eliminates moisture-related defects |
Each adjustment plays a vital role in ensuring uniform filling, ultimately leading to higher quality products and more efficient production processes.
Increasing injection pressure improves flow.True
Higher pressure enhances the plastic's ability to fill the mold.
Pre-drying treatment is unnecessary for all plastics.False
Some plastics absorb moisture, needing pre-drying to improve consistency.
Why Is Equipment Maintenance Critical in Injection Molding?
Equipment maintenance is the backbone of a successful injection molding operation, ensuring consistent product quality and operational efficiency.
Regular equipment maintenance prevents failures, maintains production quality, and prolongs machinery life, crucial for successful injection molding.

Importance of Regular Inspections
In the injection molding4 industry, equipment failures can lead to production delays and compromised product quality. Regular inspections of hydraulic, electrical, and mechanical systems help prevent unexpected breakdowns. By routinely checking critical components like the screw, barrel, and nozzle for wear and damage, operators can ensure smooth operations.
Benefits of Routine Maintenance
- Prevention of Downtime: Regular maintenance minimizes unscheduled downtimes, which can significantly affect productivity.
- Cost Efficiency: Early detection of potential issues can reduce costly repairs or replacements.
- Consistent Quality: Well-maintained equipment ensures stable process conditions, leading to high-quality products.
Cleaning and Calibration
Mold Cleaning: Residue and dirt accumulation in molds can obstruct plastic flow and filling uniformity. Utilizing special cleaning agents ensures molds remain smooth and operationally efficient.
Calibration: Regular calibration of machine parameters such as pressure, speed, and temperature is critical. Accurate parameter settings stabilize the injection process, reducing variability in product dimensions and properties.
Maintenance Task | Frequency | Tools Needed |
---|---|---|
Inspect Machine Parts | Monthly | Visual inspection tools |
Mold Cleaning | After every production run | Mold cleaning agents |
Parameter Calibration | Quarterly | Calibration tools |
Ensuring Longevity and Efficiency
Proper equipment maintenance5 extends the lifespan of machinery, safeguarding against unexpected expenses associated with equipment failure. Moreover, it fosters a safer work environment by reducing the likelihood of mechanical mishaps.
Key Takeaways:
- Prioritize regular inspections and cleaning.
- Implement a schedule for calibration and parameter checks.
- Utilize professional services for comprehensive evaluations when needed.
Adopting these practices not only enhances the operational reliability but also optimizes the entire injection molding process.
Regular maintenance prevents injection molding failures.True
Routine checks prevent unexpected breakdowns, ensuring smooth operations.
Skipping mold cleaning improves injection molding efficiency.False
Neglecting cleaning leads to residue build-up, obstructing plastic flow.
Conclusion
By implementing thoughtful material choices, refining mold design, and ensuring diligent maintenance, you can drastically reduce uneven filling issues, leading to exceptional product quality.
-
Gain expert insights on selecting materials for better molding outcomes.: Learn how to select the right material for your injection molding design with this technical overview of thermoplastic resins. ↩
-
Learn advanced techniques for optimizing mold design to enhance product quality.: Steps to INJECTION MOLDING Process Optimization · 1. Tool functionality examination · 2. Short shot testing · 3. Gate seal studies · 4. Sample parts evaluation/data … ↩
-
Discover techniques for fine-tuning molding parameters effectively.: 1. Temperature Control: · 2. Injection Speed: · 3. Cooling Time: · 4. Plastic Material Selection: · 5. Screw Speed and Back Pressure: · 6. Injection … ↩
-
Learn how maintenance prevents costly downtime in injection molding.: Regular, careful injection mold maintenance can prevent part failures and lower the overall cost of your injection molding program. ↩
-
Explore why maintenance extends machinery lifespan and efficiency.: Extend equipment lifespan and reduce the need for having to purchase new equipment. Prevent unplanned downtime which can be costly and interrupt the … ↩