In the fast-paced world of manufacturing, every little detail counts—especially when it comes to reducing scrap rates in injection molding.
To effectively reduce scrap rates in injection molding, focus on comprehensive equipment maintenance, precise raw material management, process optimization, and staff training. These practices lead to higher efficiency, less waste, and better product quality.
While these initial strategies lay a solid foundation for reducing scrap, let’s explore specific techniques that can unlock even greater efficiencies. Dive into actionable insights and advanced methods to fine-tune your injection molding process.
Regular equipment maintenance reduces scrap rates.True
Maintaining equipment prevents defects and ensures operational stability.
How Can Equipment Maintenance Reduce Scrap in Injection Molding?
In the fast-paced field of injection molding, effective equipment maintenance can significantly reduce scrap rates and boost overall productivity.
Regular maintenance of injection molding equipment ensures operational stability, reducing defects and scrap. Comprehensive inspections, precise calibrations, and timely replacements of parts maintain machine accuracy and efficiency.
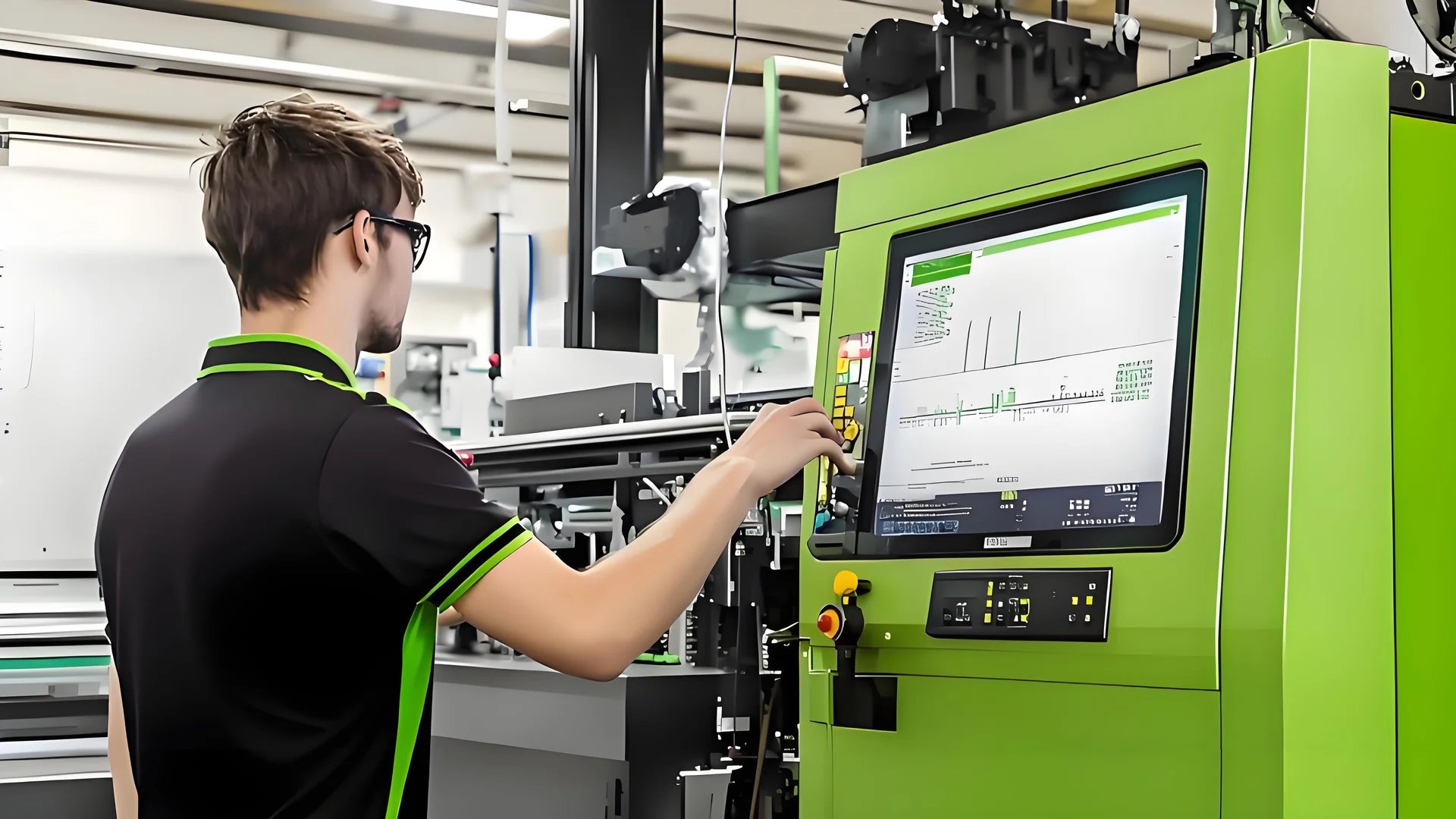
Regular Equipment Inspections and Maintenance
Frequent inspections and maintenance are paramount in the injection molding industry. By systematically checking the injection molding machine1, you can identify potential issues before they escalate into major problems. This includes cleaning, lubricating, and tightening various components to keep the machine running smoothly.
For instance, regular cleaning of the barrel and screw prevents the accumulation of raw material residue, which can lead to defective products. Similarly, replacing worn-out seals and heating rings according to manufacturer recommendations ensures that the equipment continues to perform optimally.
Importance of Equipment Calibration
Calibration is another critical aspect of equipment maintenance that directly affects scrap rates. Regularly calibrating parameters such as temperature, pressure, and injection speed is essential for maintaining accuracy and consistency in the molding process.
Using precise temperature sensors to calibrate the heating system ensures that product dimensions remain stable. Additionally, calibration of molds to match with the machine accurately reduces defects caused by misalignment or inaccuracies.
Benefits of a Proactive Maintenance Schedule
Adopting a proactive maintenance schedule can lead to significant reductions in scrap rates. This involves setting up a structured plan for regular check-ups and replacements, thus avoiding unexpected breakdowns that cause production delays and quality issues.
Consider implementing a digital maintenance log to track all maintenance activities. This enables quick adjustments to be made based on past performance data, ensuring continuous improvement in machine efficiency.
By integrating comprehensive maintenance routines into your production strategy, you can minimize waste, enhance product quality, and improve overall operational efficiency in injection molding.
Regular maintenance reduces scrap rates in injection molding.True
Maintenance ensures machines operate correctly, minimizing defects.
Ignoring calibration has no effect on scrap rates.False
Calibration maintains accuracy, reducing defects and scrap.
What Role Does Raw Material Selection Play in Scrap Rate Reduction?
Raw material selection is a critical factor in minimizing scrap rates in injection molding, directly influencing product quality and consistency.
Choosing the right raw materials reduces scrap by ensuring consistent product quality and processing performance. Key considerations include material properties, supplier reliability, and storage conditions.
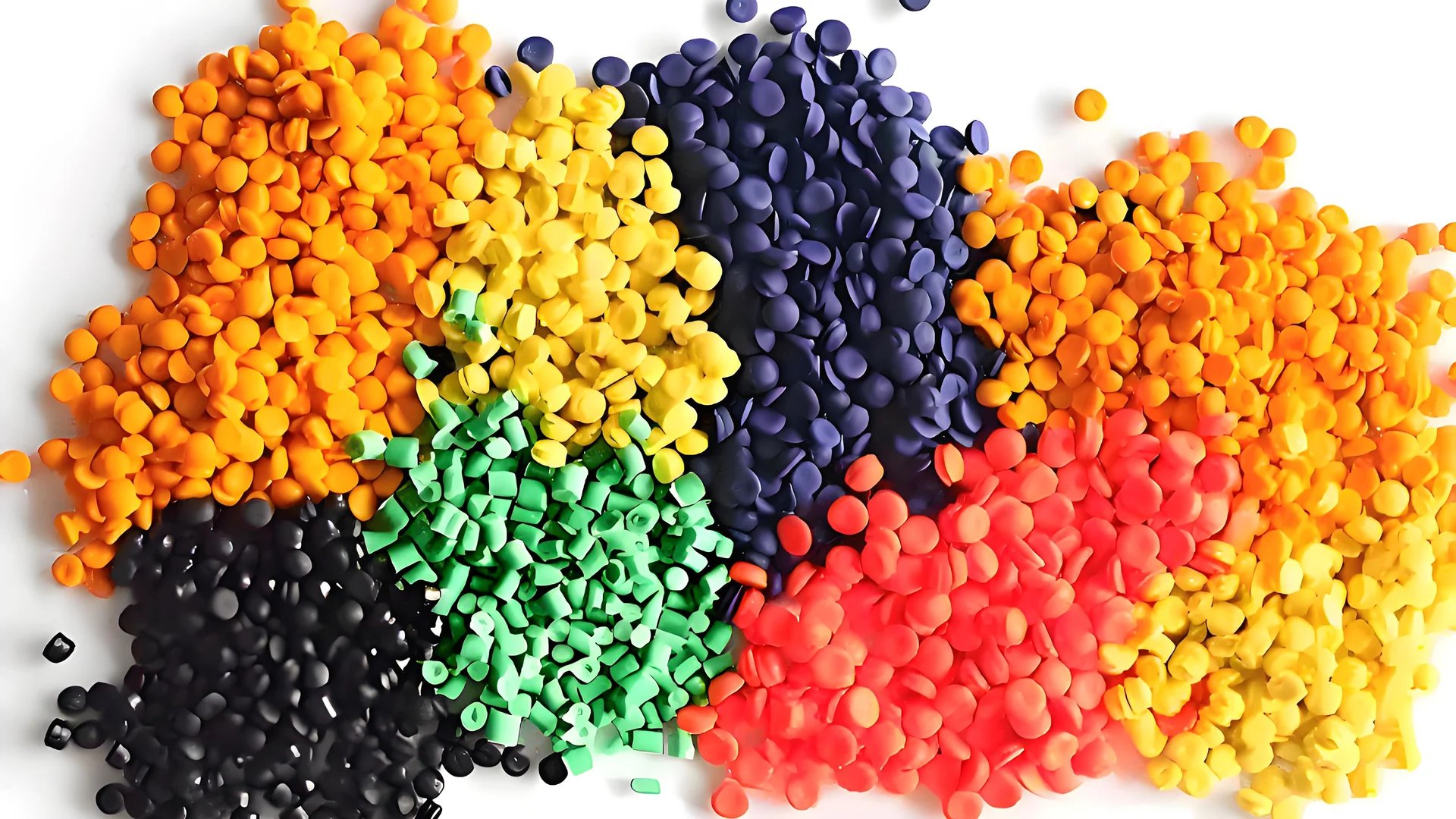
Understanding the Importance of Raw Material Properties
Selecting suitable raw materials for injection molding begins with understanding the specific properties required for the final product. Factors like fluidity, shrinkage, and heat resistance directly impact the quality and stability of molded parts. For instance, materials with appropriate fluidity ensure smooth filling of molds, reducing defects and waste.
A comprehensive guide on material selection2 can provide insights into choosing the best materials based on product requirements.
The Influence of Supplier Reliability
Reliable suppliers are essential for maintaining consistent raw material quality. It’s important to establish relationships with suppliers known for their high standards. Regular audits and evaluations can help ensure that the materials meet the necessary specifications, thus minimizing variations that could lead to increased scrap rates.
Industry experts often recommend a supplier evaluation checklist3 to assess potential partners effectively.
Proper Storage and Handling of Raw Materials
Improper storage can lead to material degradation, resulting in increased scrap rates. Raw materials should be stored in dry, ventilated areas away from contaminants. Moisture absorption is a common issue, leading to defects such as bubbles or voids in the final product.
Implementing a structured raw material storage protocol4 ensures optimal conditions are maintained, preserving material integrity.
Drying Techniques to Enhance Material Quality
Pre-processing drying techniques are crucial for materials that are prone to moisture absorption. Adjusting drying temperatures and times according to material properties can significantly reduce defects.
Adopting advanced drying systems can improve efficiency, as detailed in this expert analysis on drying systems5.
Proper material selection reduces scrap rates in molding.True
Selecting materials with suitable properties ensures quality, reducing waste.
Supplier reliability does not affect scrap rates.False
Reliable suppliers ensure consistent quality, minimizing variations and scrap.
Why Is Process Optimization Crucial for Minimizing Scrap?
In the world of injection molding, minimizing scrap is not just about cost savings—it’s a pathway to enhanced efficiency and superior product quality.
Process optimization in injection molding is vital to minimizing scrap because it allows for precise control over production variables, leading to consistent product quality and reduced waste. This involves fine-tuning parameters such as temperature, pressure, and speed to achieve optimal conditions.
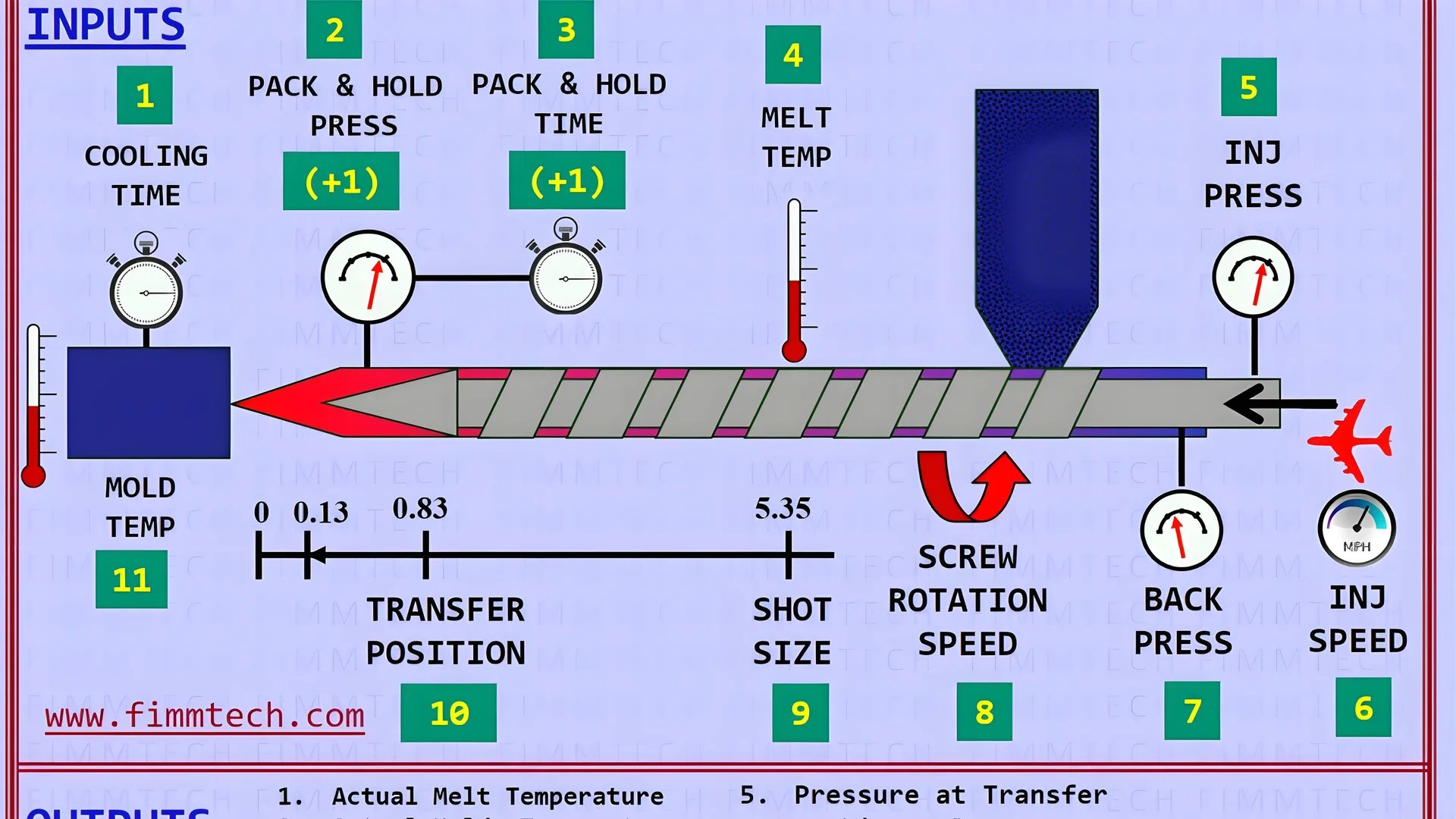
Understanding Process Optimization in Injection Molding
Process optimization is the deliberate adjustment and refinement of production parameters to enhance efficiency, quality, and cost-effectiveness. In injection molding, this process is critical due to the numerous variables that influence the final product quality.
Key Parameters in Process Optimization
-
Temperature Management
- Barrel Temperature: Proper control ensures the polymer is adequately melted and homogenized, reducing defects like burn marks or incomplete filling.
- Mold Temperature: As highlighted in the importance of mold temperature control6, maintaining uniformity prevents issues such as warping and shrinkage.
-
Pressure Regulation
- Injection Pressure: Adjusting pressure helps in achieving the desired flow and fill of the mold, essential for avoiding short shots or flash.
- Holding Pressure: This stabilizes the part dimensions as the material cools and solidifies, which is crucial in preventing sink marks and voids.
-
Speed and Time Control
- Injection Speed: Fine-tuning the speed can prevent problems such as jetting or flow marks, often caused by excessive velocity.
- Cooling Time: Adequate cooling time allows proper crystallization of polymers, reducing internal stresses and enhancing part durability.
Establishing a Process Parameter Database
Creating a comprehensive database that records successful parameters for various products can drastically reduce setup times for future runs. This approach also enables quick adjustments and helps maintain consistency across production batches. Learn more about maintaining consistency in production7.
Impact of Process Optimization on Scrap Rates
Process optimization not only stabilizes product quality but also reduces material waste by minimizing trial-and-error adjustments. This approach ensures that each cycle is productive, with fewer defective parts reaching the inspection stage.
By focusing on these elements, manufacturers can significantly decrease their scrap rates while simultaneously improving operational efficiency and product reliability. For those aiming to stay competitive, mastering process optimization in injection molding is an invaluable skill.
Process optimization reduces scrap in injection molding.True
By controlling production variables, process optimization minimizes defects.
High injection speed increases scrap rates in molding.True
Excessive velocity can cause defects like jetting or flow marks.
How Can Effective Mold Design Contribute to Lower Scrap Rates?
Effective mold design is pivotal in minimizing scrap rates in injection molding, ensuring superior product quality and operational efficiency. Dive into how strategic mold design choices can significantly impact production outcomes.
Effective mold design reduces scrap rates by optimizing the mold structure, ensuring precise dimensions, and facilitating smooth material flow. This leads to consistent product quality and minimizes defects during production.
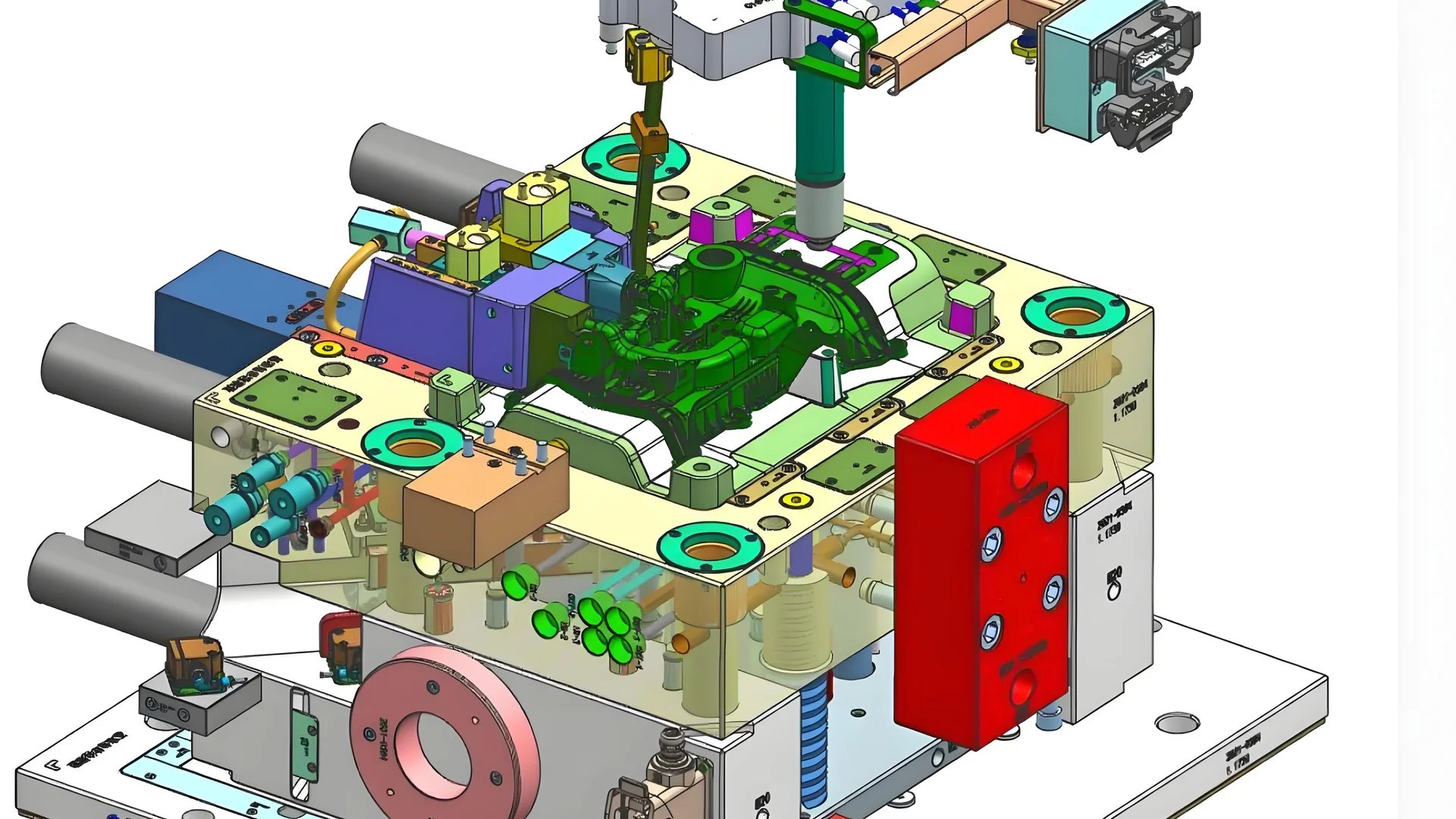
Importance of Precision in Mold Design
The foundation of effective mold design lies in precision. A well-designed mold ensures that each product maintains the intended shape and structural integrity. By utilizing advanced CAD software, designers can create molds with exact dimensions, thereby reducing the likelihood of defects.
Optimizing Flow Channels
In the injection molding process, flow channels8 play a crucial role in directing molten material. By designing channels that facilitate even material distribution, you prevent common issues such as air entrapment and inconsistent wall thickness. This optimization not only minimizes scrap but also enhances product strength.
Material Selection and Mold Design
Choosing the right materials for both the mold and the products is essential. The mold material must withstand repeated cycles without degrading. Simultaneously, the mold design should account for the characteristics of the production material to ensure compatibility and reduce wear and tear.
Implementing Cooling Systems
Cooling is integral to the mold design process. Efficient cooling systems reduce cycle times and prevent warping or shrinkage of products. By integrating advanced cooling technologies like conformal cooling, manufacturers can achieve uniform temperature distribution, further decreasing scrap rates.
Maintenance and Calibration
Regular maintenance and calibration of molds ensure longevity and consistent performance. Implementing a schedule for cleaning and repairing molds can prevent defects related to wear and tear. Additionally, regular calibration helps maintain alignment and accuracy, which are critical for reducing scrap.
Case Study: Application of Advanced Mold Design Techniques
Consider a manufacturer who faced high scrap rates due to uneven product dimensions. By redesigning their molds with improved flow channels and incorporating conformal cooling, they managed to reduce scrap by 30%. This case highlights how targeted design changes can lead to substantial improvements in quality and efficiency.
Through strategic choices in mold design, manufacturers can significantly reduce scrap rates, resulting in cost savings and improved product quality. By focusing on precision, material compatibility, and regular maintenance, effective mold design serves as a cornerstone for successful injection molding operations.
Precision in mold design reduces scrap rates.True
Precise molds ensure consistent product quality, minimizing defects.
Cooling systems have no impact on scrap rates.False
Efficient cooling prevents warping, reducing scrap during production.
Conclusion
By adopting these strategies, you not only lower scrap rates but also contribute to sustainable manufacturing. Reflect on these methods to optimize your processes and boost profitability.
-
Gain deeper insights into how inspections prevent costly equipment failures.: Your inspections should regularly check the mold for any condensation, as well as the nearby parts for any signs of deformity caused due to … ↩
-
Discover criteria for selecting high-performance materials to reduce defects.: Learn how to select the right material for your injection molding design with this technical overview of thermoplastic resins. ↩
-
Learn how to choose reliable suppliers for consistent material quality.: Use this Supplier Factory Audit Form template to assess manufacturing facilities and quality processes of your existing or potential vendors or suppliers. ↩
-
Explore strategies to maintain raw material quality through proper storage.: For starters, ensure any storage area is clean. Try to keep relative humidity as low as possible. Keep similar metals together, and keep all … ↩
-
Understand how improved drying techniques enhance material performance.: Plastics Northwest benefits from an industrial desiccant dryer with a more flexible, energy-efficient, and smart design. ↩
-
Mold temperature control impacts product quality and reduces waste.: Filling molds requires an incredible amount of pressure, the lack of which results in improper filling of molds. However, applying too much … ↩
-
Maintaining consistency ensures quality and minimizes scrap rates.: 1 Define your quality objectives · 2 Implement quality management systems · 3 Train and empower your staff · 4 Use quality tools and techniques · 5 … ↩
-
Understanding flow channels prevents defects like air entrapment and thickness variation.: The phenomenon of fountain flow affects almost every aspect of the molded product, starting with filling, extending to pack and hold, … ↩