In the fast-paced realm of manufacturing, where every detail counts, consistency becomes not just a goal, but a necessity. I’ve learned firsthand how dual-cavity molds can make or break the quality of products we produce.
To effectively reduce product differences in dual-cavity molds, focus on precise mold design, high-quality manufacturing, and stringent process controls. Implementing these strategies ensures consistency and enhances the quality of molded products.
While understanding these key strategies provides a foundation, diving deeper into each aspect—such as material selection and equipment maintenance—reveals additional insights critical for achieving optimal results. Continue reading to discover expert tips and techniques.
Precise mold design reduces product differences.True
Precision in mold design ensures consistent cavity dimensions, reducing variations.
What Role Does Mold Design Play in Reducing Product Differences?
Precision in mold design is pivotal in minimizing product differences, especially in dual-cavity molds.
Mold design significantly influences product uniformity by ensuring consistent cavity dimensions, strategic gate and runner placement, and optimal cooling systems. This precision reduces variations and enhances quality control.
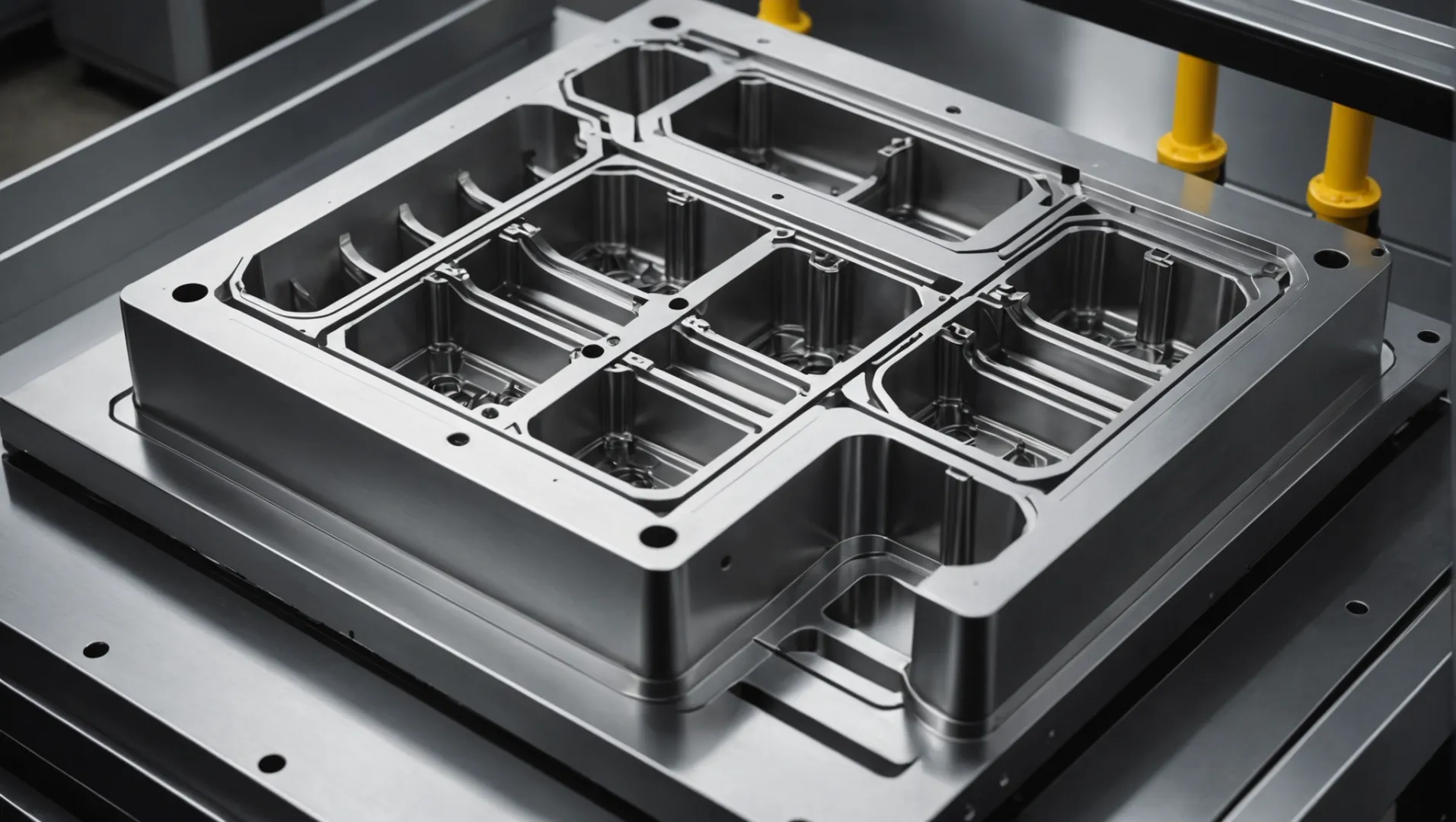
The Importance of Accurate Design
Achieving uniformity in dual-cavity molds begins with meticulous design. Utilizing advanced CAD/CAM technology, designers can ensure each cavity is identical in size, shape, and structure. This precision is critical to maintaining consistent product quality across all manufactured items.
By implementing strict tolerance controls, engineers can minimize discrepancies between cavities. This involves not only the physical dimensions but also the arrangement of the gate, runner, and cooling systems. Symmetrical gate positioning and runner layouts are vital for consistent material flow and cooling conditions across both cavities, reducing the risk of defects.
High-Quality Manufacturing Practices
Beyond design, the manufacturing phase plays a crucial role. High-precision equipment like CNC machining centers is employed to fabricate molds with excellent dimensional accuracy and surface quality. These tools allow manufacturers to adhere closely to the design specifications, thus reducing the potential for variations.
Additionally, rigorous quality checks are essential. Inspections covering dimensional measurements, surface roughness, and hardness testing ensure that any deviations are promptly identified and corrected. Such quality assurance practices maintain the mold’s integrity and prolong its operational lifespan.
Strategic Gate and Runner Design
The gate and runner system in a mold significantly impacts how material fills the cavities. Symmetrical designs ensure uniform filling, which is crucial for maintaining consistency between products. By carefully planning these elements during the design stage, manufacturers can achieve better control over the molding process.
For instance, employing a balanced runner system1 can help distribute material evenly, thus reducing differential pressure and potential warpage in the final products. Such strategies are integral to effective mold design.
Cooling System Optimization
A well-designed cooling system is vital for maintaining consistent temperatures within the mold. By using uniform cooling channels, designers can ensure that both cavities are cooled evenly, preventing issues like differential shrinkage or warpage that could lead to product inconsistencies.
Advanced technologies like conformal cooling utilize 3D printing to create intricate cooling paths that enhance heat dissipation. This innovation allows for more precise temperature management within the mold.
In conclusion, while mold design is just one aspect of reducing product differences in dual-cavity molds, it lays the foundation for achieving high-quality, consistent outcomes in manufacturing.
Mold design affects product uniformity significantly.True
Precise mold design ensures consistent cavity dimensions, reducing variations.
Cooling systems in molds are irrelevant to product differences.False
Uniform cooling systems prevent shrinkage and warpage, ensuring consistency.
How Does Material Selection Impact Dual-Cavity Mold Consistency?
Choosing the right materials is vital for maintaining consistency in dual-cavity molds. It affects the uniformity and quality of the final product.
Material selection impacts dual-cavity mold consistency by ensuring uniform flow, reducing variability in performance, and enhancing product quality. Choosing stable, high-quality raw materials minimizes differences between cavities, leading to consistent output.

Importance of Material Quality Control
The first step in achieving consistency in dual-cavity molds is controlling the quality of raw materials. Selecting materials with stable properties ensures that both cavities receive identical inputs, reducing variability. For instance, raw materials should be scrutinized for particle size distribution and impurity content.
- Particle Size Distribution: Uniform particle size can significantly affect the flow characteristics of materials during molding, influencing how evenly each cavity fills.
- Impurity Content: High levels of impurities can alter material properties, leading to inconsistencies between the outputs of the two cavities.
Moreover, using raw materials from the same batch can further reduce fluctuations in performance across cavities. This approach minimizes differences that may arise from variations in material composition.
Role of Material Pretreatment
Material pretreatment is essential for enhancing the flow and molding performance of raw materials. This process involves drying and preheating materials to remove moisture and volatiles, which can otherwise lead to inconsistent molding outcomes.
Additionally, incorporating appropriate additives like lubricants and stabilizers can improve processing performance. These additives help in achieving uniformity by reducing friction and enhancing the material’s stability during the molding process.
Choosing Additives for Uniformity
Selecting the right additives is crucial for maintaining consistency across dual-cavity molds. Additives such as stabilizers and lubricants are introduced to enhance material properties and ease of processing:
- Stabilizers: Help maintain material integrity under processing conditions, thereby ensuring that both cavities produce outputs with similar characteristics.
- Lubricants: Reduce friction during the molding process, enabling smoother flow and reducing wear on the mold itself.
Impact of Batch Consistency
Ensuring that raw materials come from the same batch is another strategy to maintain consistency in dual-cavity molds. Batch consistency reduces variability in chemical composition and physical properties, leading to more predictable outcomes across both cavities.
This practice can be particularly beneficial when producing high-volume runs where even minor differences in material composition could lead to noticeable variations in final products.
Implementing a Comprehensive Quality Inspection
A robust quality inspection process is vital for identifying any discrepancies before materials enter the production line. Inspections might include:
- Dimensional Measurement: Ensures that materials meet specified tolerances.
- Surface Roughness Inspection: Assesses the quality and texture of material surfaces, which can affect how well they fill the mold.
- Hardness Testing: Determines material resilience under stress, impacting how it behaves during molding.
By employing these inspection techniques, manufacturers can catch potential issues early, thus maintaining a high level of consistency in dual-cavity mold outputs.
Material pretreatment removes moisture for better mold flow.True
Pretreatment like drying removes moisture, enhancing flow and consistency.
Using different batches improves dual-cavity mold consistency.False
Using the same batch reduces variability, improving mold consistency.
Which Molding Process Controls Are Most Effective?
Achieving uniformity in dual-cavity molds requires mastering precise process controls. Learn the most effective strategies to ensure consistent quality.
Effective molding process controls focus on optimizing parameters like temperature, pressure, and injection speed. Utilizing advanced technologies such as hot runner systems and real-time monitoring further enhances product consistency in dual-cavity molds.
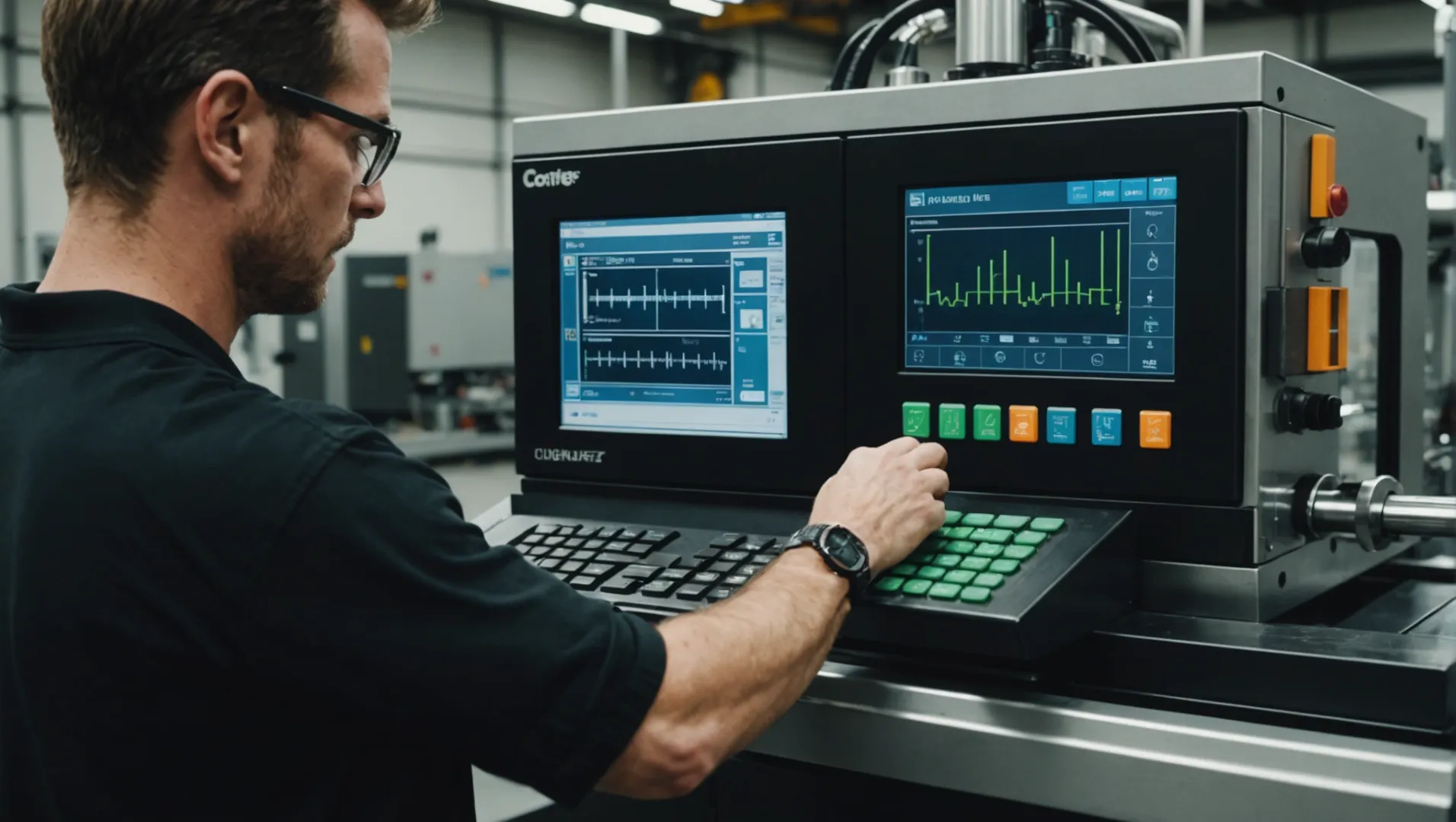
Temperature Control: The Bedrock of Consistency
Temperature regulation is crucial for maintaining uniformity in dual-cavity molds. By ensuring each cavity maintains the same temperature, manufacturers can significantly reduce variations. Implementing temperature sensors and controllers enables real-time monitoring and adjustments, thus minimizing discrepancies between products.
Key Techniques
- Uniform Mold Temperature: Use advanced controllers to maintain consistent mold temperatures across both cavities.
- Barrel and Nozzle Temperature: Precise control here ensures the material’s melting state is stable, which is vital for consistent flow and filling.
For further insights, explore injection molding temperature control strategies2.
Pressure Optimization: Achieving Balance
Controlling injection and holding pressures is pivotal for ensuring equal material distribution across cavities. By carefully adjusting the pressure curve, manufacturers can achieve uniform density and reduce defects such as warping or flashing.
Techniques to Consider
- Adjustable Pressure Curves: Tailor the pressure curve to match specific material and product needs.
- Consistent Clamping Force: Proper clamping prevents size changes and excess flash, enhancing uniformity.
Discover more about pressure control techniques3 that optimize molding processes.
Advanced Injection Technologies: Enhancing Precision
Leveraging cutting-edge technologies such as hot runner systems and sequential injection molding can dramatically improve the precision of molding processes.
- Hot Runner Systems: Enable precise control over material flow, reducing wastage and ensuring uniform filling.
- Sequential Injection Molding: This technique allows for controlled flow into different sections, crucial for maintaining consistency in complex designs.
Learn how advanced technologies4 are transforming injection molding consistency.
Real-Time Monitoring: Instant Feedback for Optimal Control
Real-time monitoring systems provide immediate feedback on process conditions, allowing for quick adjustments to maintain uniformity. These systems use sensors and automated feedback loops to ensure all parameters are within specified ranges, preventing deviations that could lead to product inconsistencies.
Explore more on real-time monitoring in injection molding5 to enhance process control.
By focusing on these core areas—temperature, pressure, advanced technologies, and real-time monitoring—manufacturers can significantly enhance the effectiveness of their molding process controls, leading to higher quality and consistency in dual-cavity molds.
Temperature control is crucial for mold uniformity.True
Temperature regulation reduces variations, ensuring consistent product quality.
Hot runner systems increase material wastage in molds.False
Hot runner systems actually reduce wastage by controlling material flow.
Why Is Equipment Maintenance Crucial for Consistency?
In the fast-paced world of manufacturing, equipment maintenance stands as a pillar of consistency, ensuring seamless production and product uniformity.
Equipment maintenance is crucial for maintaining consistency in manufacturing processes, particularly in dual-cavity mold operations. Regular maintenance prevents machine wear, ensures precise mold alignment, and supports consistent product quality by minimizing variations and downtimes.
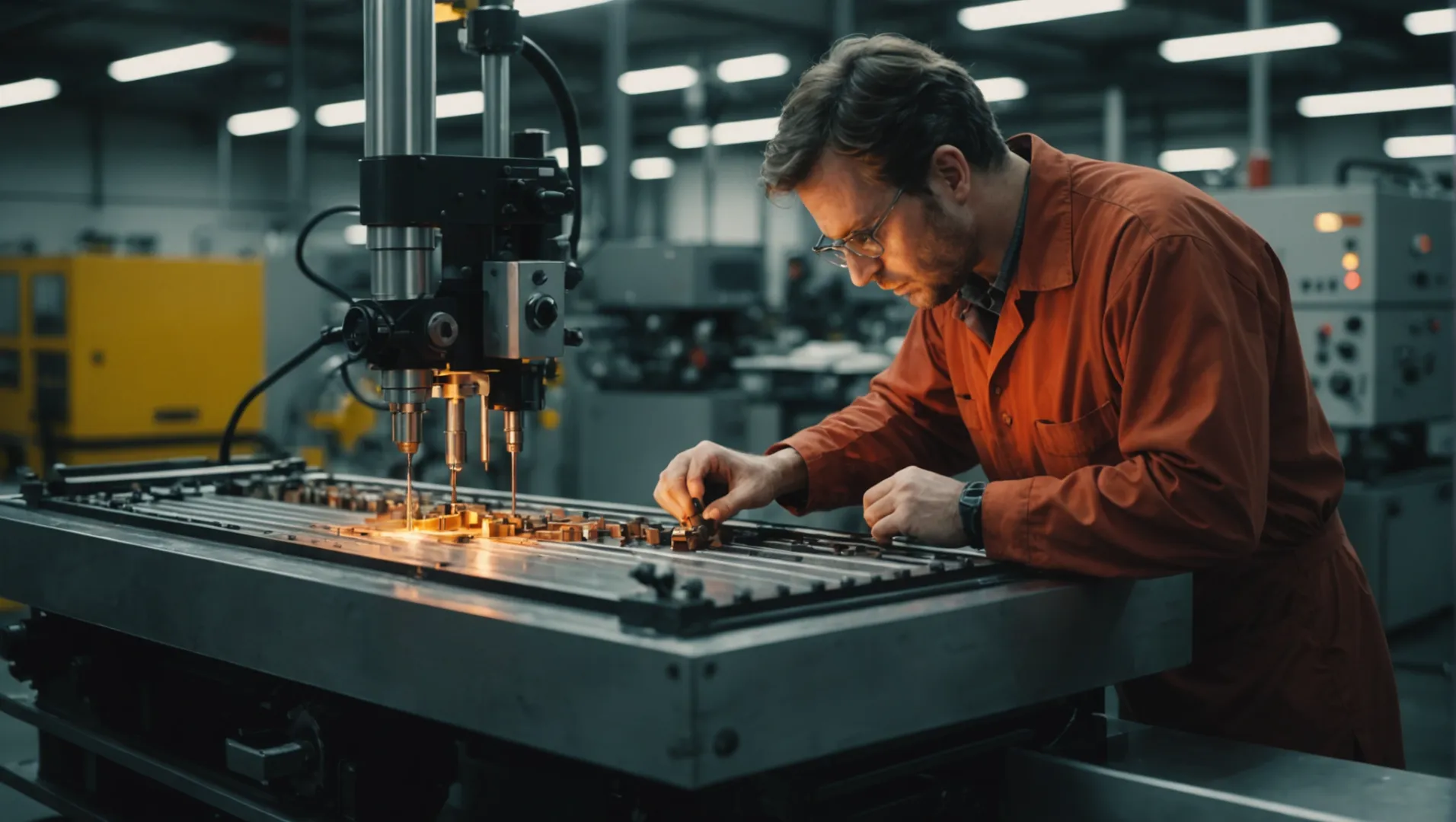
Importance of Regular Maintenance
Maintaining equipment regularly is not just about prolonging the life of machinery, but it directly impacts the consistency of the products being manufactured. For dual-cavity molds, inconsistencies often arise from machinery faults that can be mitigated through a systematic maintenance schedule.
- Preventing Wear and Tear: Regular inspections and servicing can identify early signs of wear and tear, preventing unexpected breakdowns. For instance, cleaning the barrel and nozzle of injection molding machines keeps them in optimal condition.
- Calibration: Regular calibration of pressure sensors and temperature controls ensures that the equipment performs within specified tolerances, essential for producing identical products in both cavities.
Operator Training and Its Impact
A well-maintained machine is only as good as its operator. Training operators not only on the operational aspects but also on basic maintenance tasks can significantly improve overall consistency.
- Understanding Equipment: Operators trained to notice anomalies can address minor issues before they escalate, keeping production lines running smoothly.
- Quality Awareness: Trained operators who understand the importance of precision in settings such as injection speed or cooling time can better maintain the desired output consistency.
Establishing a Maintenance Schedule
Developing a detailed maintenance schedule6 helps in organizing the various maintenance activities efficiently.
Maintenance Task | Frequency | Responsible Party |
---|---|---|
Cleaning machine parts | Weekly | Operators |
Calibration checks | Monthly | Maintenance Team |
Full system inspection | Quarterly | Technical Experts |
Advantages of Regular Equipment Checks
- Minimized Downtime: Scheduled maintenance reduces the likelihood of unexpected equipment failures, minimizing downtime and keeping production schedules intact.
- Consistent Quality: By ensuring machinery operates at peak efficiency, product consistency is maintained across multiple runs, vital for dual-cavity mold operations.
In conclusion, while focusing on material selection7 and process controls are important, neglecting equipment maintenance can undo these efforts. Ensuring your equipment is regularly maintained not only enhances product quality but also boosts overall production efficiency.
Regular maintenance prevents machine wear.True
Regular maintenance identifies early wear signs, preventing breakdowns.
Operators don't impact equipment consistency.False
Trained operators notice anomalies, improving production consistency.
Conclusion
By implementing these strategies, you can significantly reduce product variations in dual-cavity molds, leading to improved product quality and manufacturing efficiency.
-
Learn how balanced runner systems improve material distribution and product consistency.: The design is to ensure each cavity has a balanced material flow and is filled out at the same time. for example, radiate runners, linear runners, Y-shape … ↩
-
Gain insights into maintaining uniform temperatures for quality consistency.: To control the temperature of the mold, you need to figure out the temperature difference between the male mold and the female mold, the mold … ↩
-
Explore methods to optimize pressure for better product uniformity.: These systems typically include an Electronic Pressure Regulator, which controls the flow of air or nitrogen gas into the system. The nitrogen … ↩
-
Learn about innovations improving precision in molding processes.: A great innovation for injection molding is structural foam molding. This process combines injection molding and gas-assisted injection molding … ↩
-
Understand how monitoring enhances process control efficiency.: Matics provides real-time production monitoring that enables injection molding operations to aggregate and analyze the KPIs they need to … ↩
-
Learn how a structured schedule enhances equipment reliability and product quality.: Effective maintenance scheduling plays a pivotal role in ensuring smooth operations, preventing costly breakdowns, and maximizing the lifespan of assets. ↩
-
Explore how choosing the right materials complements equipment maintenance.: Material selection is a vital part of the design phase. Choosing the right material to work with will ensure that your component is durable enough for its … ↩