Ever thought about how much impact a small weight change can have on injection-molded parts?
To reduce part weight in injection molding, employ design modifications, choose lightweight materials, and optimize processes like reducing wall thickness and adjusting injection settings, ensuring weight reduction without compromising strength and functionality.
When I first started exploring ways to make parts lighter, I was amazed at the potential for innovation. It’s like piecing together a puzzle where each move can lead to cost savings and better performance. Let’s dive deeper into how each of these strategies can be tailored to fit your projects, offering not just financial benefits but also a boost in product efficiency and sustainability. By rethinking designs with hollow structures or reinforced ribs, you can use less material without compromising on strength. Similarly, experimenting with different materials can open up a world of possibilities for lightweight yet durable parts.
Reducing wall thickness decreases injection-molded part weight.True
Thinner walls require less material, thus reducing the overall weight.
Using heavier materials helps reduce injection-molded part weight.False
Heavier materials increase the part's weight, not reduce it.
How Can Design Optimization Lead to Weight Reduction?
Ever wondered how tweaking your design can trim down weight without losing any oomph?
Design optimization reduces weight by adjusting wall thickness, using hollow structures, and refining rib and boss designs, minimizing material use while maintaining functionality.
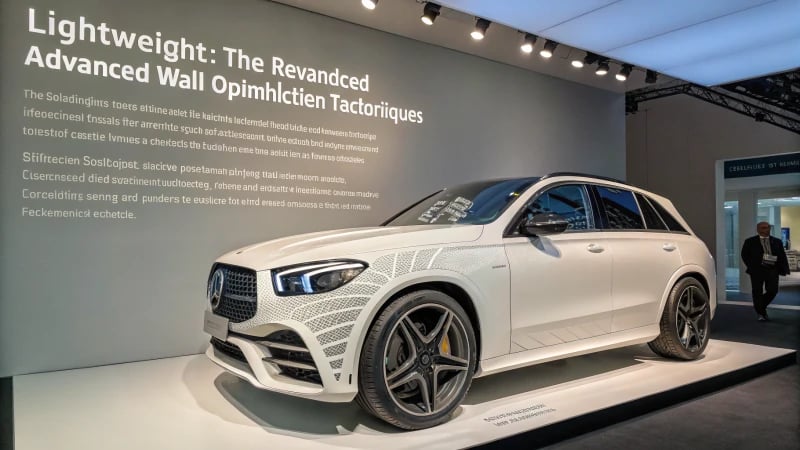
When I first ventured into the world of design, I quickly learned that every gram counts. Whether crafting a lightweight laptop or a sleek smartphone, design optimization is a game-changer.
Wall Thickness Reduction
Reducing wall thickness is an effective way to decrease weight. By analyzing part designs, areas for thinning can be identified. Imagine holding a box in your hand; you wouldn’t want it to feel like a brick, right? By strategically thinning out the walls, we maintain durability without the heft. Use tools like finite element analysis1 to predict performance changes due to wall thinning—kind of like having a crystal ball for structural integrity. This ensures mechanical integrity isn’t compromised while reducing material usage.
Incorporating Hollow Structures
Switching to hollow structures instead of solid parts offers substantial weight savings. It’s like cutting out the heavy core and leaving behind a strong, beautiful shell. Gas-assisted injection molding techniques can be used where nitrogen is injected to form a hollow core—injecting nitrogen felt like magic! Learn more about gas-assisted injection molding2 for effective weight reduction.
Optimizing Rib and Boss Design
The devil’s in the details, they say. Designing ribs and bosses efficiently helps in weight reduction by giving the part strength without extra bulk. Properly designed ribs support structures efficiently, allowing for thinner walls.
Design Element | Optimal Thickness |
---|---|
Ribs | 40-60% of wall thickness |
Bosses | Minimal but functional |
Ensure ribs have a thickness of 40-60% of the base wall thickness.
Selecting Lightweight Materials
Material choice greatly impacts weight. The right material can make all the difference; opt for materials with lower densities like polyethylene or polypropylene when possible—it’s like night and day! Exploring advanced polymer blends is akin to finding the perfect pair of running shoes—light yet durable.
Filled materials such as microcellular foamed plastics offer another pathway by maintaining some mechanical properties while significantly reducing density through cellular structures.
Process Optimization Techniques
It’s not just about what you make but how you make it. Optimizing injection parameters—tweaking speed, pressure, temperature—has been crucial in my process to enhance mold filling efficiency with less material. Improved mold venting also ensures that every last bit of plastic fits perfectly into place without waste by allowing trapped air to escape.
Each of these strategies has become a tool in my belt, helping me craft designs that are not just lighter but smarter too.
Reducing wall thickness decreases weight.True
Thinner walls use less material, reducing overall weight.
Hollow structures increase part weight.False
Hollow structures decrease weight by using less material.
How Does Material Selection Impact Part Weight?
When it comes to designing lightweight parts, choosing the right material is like picking the perfect ingredient for a recipe—it’s all about balance.
Material selection impacts part weight by choosing low-density materials, utilizing filled plastics like microcellular foams, and optimizing design features, leading to significant weight reduction while maintaining structural integrity.
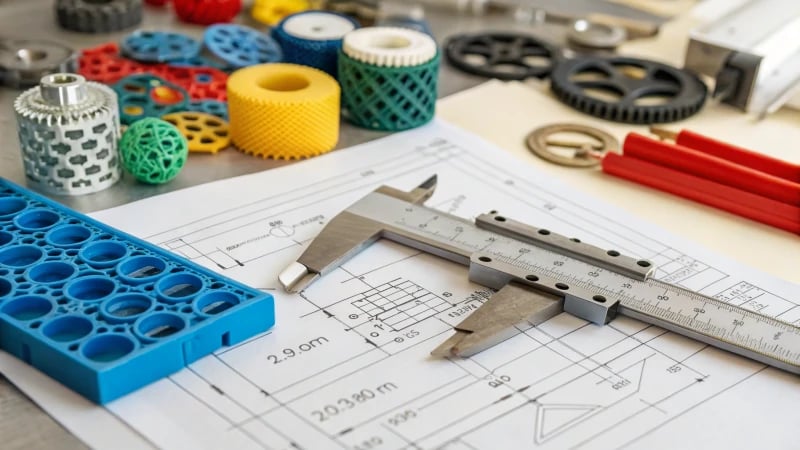
Design Optimization in Material Selection
Material selection feels a bit like a puzzle I used to solve as a kid. I’d try to make sure every piece fit perfectly without wasting any space. Similarly, when designing parts, I often analyze wall thickness3 possibilities to minimize material usage while maintaining strength. For instance, experimenting with hollow structures using techniques like gas-assisted injection molding can make a huge difference, cutting down material use without losing functionality.
Lightweight Materials
Choosing the right lightweight materials reminds me of picking the right hiking gear—light yet strong enough for the journey. I’ve often found polyethylene4 or polypropylene to be the perfect balance of weight and performance, especially when density is a major concern. These materials have become my go-to in applications where every gram matters.
Material Type | Density (g/cm³) | Application Example |
---|---|---|
Polyethylene (PE) | 0.91-0.97 | Packaging, Containers |
Polypropylene (PP) | 0.89-0.92 | Automotive Parts |
Filled Materials for Weight Reduction
Once, while tinkering with a childhood project, I discovered that adding air pockets made my structure lighter yet surprisingly sturdy. This memory comes to mind when using filled plastics like microcellular foams5 in manufacturing. They reduce weight while maintaining strength, thanks to an integrated foaming process.
Process Optimization
Finding the perfect injection parameters is a bit like tuning a guitar. You tweak it just right to get that perfect sound—or in this case, optimal filling with minimal material. By adjusting these parameters and enhancing mold venting6, we can prevent defects and ensure quality without overusing materials.
The strategies I’ve explored highlight how material selection is fundamental in achieving lighter parts without sacrificing functionality. It’s like crafting a masterpiece—each choice and adjustment contributes to the final product’s performance and sustainability.
Additional Strategies for Weight Reduction
Rib and boss design optimization feels like an art form that complements engineering. Proper rib design provides structural support, allowing for wall thickness reductions while maintaining integrity. This approach ensures parts remain robust while using less material.
For more insights, exploring resources on rib design guidelines7 can be incredibly valuable, revealing how even small adjustments can lead to significant material savings.
Polyethylene has a lower density than polypropylene.False
Polyethylene's density range (0.91-0.97) overlaps with polypropylene's (0.89-0.92).
Gas-assisted injection molding reduces material usage.True
This process creates hollow structures, cutting down on material use.
How Can Process Optimization Lead to Lighter Parts?
Ever wonder how streamlining processes can make manufacturing lighter, literally? Let me walk you through how optimizing techniques not only boosts efficiency but also trims down the weight of the parts we create.
Process optimization results in lighter parts by improving design efficiency, selecting optimal materials, and adjusting injection parameters, reducing material use without compromising structural integrity.

Design Efficiency
When I first started in the world of mold design, I quickly learned that one of the most impactful ways to reduce weight is through design optimization. Picture this: you’re holding a smartphone case that’s feather-light but still as sturdy as a rock. How is that possible? It all starts with reducing wall thickness and using hollow structures, which can dramatically cut down on weight.
I remember a project where we used finite element analysis8 to tweak the wall thickness of a part. We managed to keep the part strong enough for everyday use while shaving off unnecessary material. This technique ensures that even as we alter the design, we don’t compromise on functionality.
Design Technique | Benefits |
---|---|
Wall Thickness Reduction | Less material, maintains strength |
Hollow Structures | Lighter weight, retains form |
Rib and Boss Optimization | Reduces material, adds strength |
Rib and boss designs offer another avenue for cutting down on material use. These features provide support, allowing for thinner walls without sacrificing strength.
Material Selection
Choosing the right materials is like picking the perfect ingredients for a recipe. Opt for lightweight materials such as polypropylene, which are less dense yet perform just as well as their heavier counterparts. I once switched to microcellular foamed plastics9 for a project, and it was a game-changer. These materials maintain mechanical properties while significantly cutting down on weight.
Material Type | Characteristic Benefit |
---|---|
Lightweight Polymers | Lower density, similar performance |
Filled Materials | Maintains properties, less material |
These choices help ensure that we’re not just making parts lighter but smarter.
Adjusting Injection Parameters
Tweaking injection parameters is another crucial step in the process. By adjusting speed, pressure, and temperature, we can ensure molds fill efficiently with minimal waste. I’ve found that managing these elements correctly can significantly reduce the need for over-injection, making our parts lighter without compromising on quality.
And don’t forget about mold venting—it’s essential for getting rid of trapped air during injection. Proper venting means we use just the right amount of material, cutting down on waste and weight.
By focusing on these strategies—design efficiency, selecting the right materials, and adjusting parameters—I’ve seen firsthand how manufacturers can produce lightweight components that are both strong and functional. For those curious about more injection molding techniques10 that contribute to process optimization, there’s plenty more to explore.
Reducing wall thickness always compromises part strength.False
Finite element analysis ensures wall reduction maintains part functionality.
Lightweight polymers have lower density than denser plastics.True
Lightweight polymers reduce weight without compromising performance, unlike denser plastics.
Are There Sustainability Benefits to Reducing Part Weight?
I remember the first time I realized that reducing part weight in manufacturing could be a game-changer for sustainability. It was like uncovering a secret superpower that could help save the planet.
Reducing part weight in manufacturing enhances sustainability by cutting material and energy usage, decreasing transportation emissions, and ultimately lowering the environmental footprint.
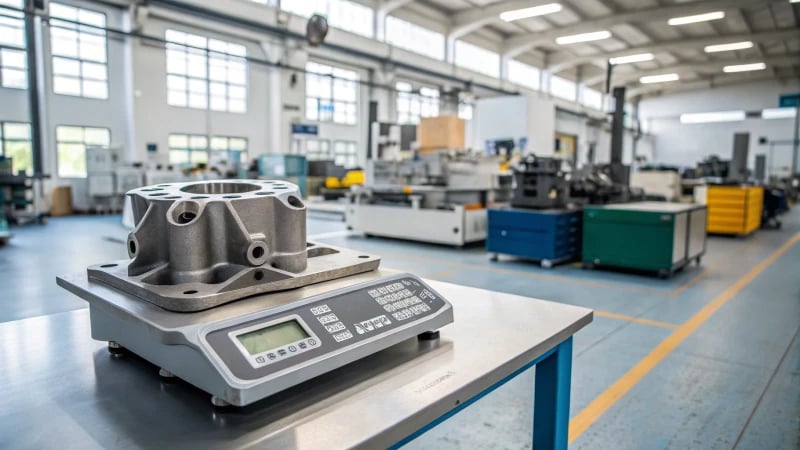
Material Efficiency and Conservation
When I first began exploring the impact of reducing part weight, I was amazed by how something so seemingly simple could lead to such significant material efficiency. Imagine designing a part where every gram counts. Through techniques like design optimization11 and wall thickness reduction12, I’ve learned that we can drastically lower material consumption. This not only helps cut costs but also conserves our planet’s precious natural resources. I remember working on a project where we managed to trim down the material usage significantly, which felt like winning a small victory for Mother Earth.
Energy Savings During Production
I’ve also found that lighter parts require less energy to produce. Using lightweight materials13 and optimizing injection parameters14 can dramatically reduce the energy needed for molding and shaping processes. In one of my projects, tweaking these parameters felt like tuning a musical instrument—it required precision, but once perfected, it resulted in harmonized energy savings and a notable decrease in greenhouse gas emissions.
Optimization Technique | Sustainability Benefit |
---|---|
Wall Thickness Reduction | Material conservation, lower energy use |
Hollow Structures | Less material use, reduced cooling requirements |
Rib and Boss Design | Material efficiency, structural integrity |
Reduced Transportation Emissions
One of the most eye-opening moments for me was realizing how lighter components can lead to reduced transportation costs and emissions. When I think about the global supply chains my projects are part of, it’s clear that less weight means lower fuel consumption and fewer carbon emissions. This realization hit home when I saw the positive impact on our company’s carbon footprint—proof that small changes can have big effects.
Enhancing Product Lifecycle and End-of-Life Impact
Lastly, reducing part weight isn’t just about the manufacturing process; it’s about enhancing the entire lifecycle of a product. I’ve noticed how lightweight components often result in more durable products with longer lifespans. Plus, they’re easier to handle and recycle, which aligns perfectly with circular economy practices. In one instance, a product redesign incorporating lighter parts led to improved user satisfaction and extended product life—an outcome that left both me and our customers smiling.
Considering these factors, it’s clear to me that adopting lightweighting strategies isn’t just about saving money—it’s about contributing to a sustainable future while achieving efficient production.
Reducing part weight conserves natural resources.True
Less material use leads to conservation of raw materials.
Lighter parts increase transportation emissions.False
Lighter parts reduce fuel consumption, lowering emissions.
Conclusion
Effective strategies for reducing part weight in injection molding include design optimization, lightweight material selection, and process refinement to enhance performance while minimizing material use.
-
Discover how finite element analysis predicts performance changes with reduced wall thickness. ↩
-
Understand the benefits of gas-assisted injection molding in creating hollow structures. ↩
-
Discover strategies to optimize wall thickness, aiding in reduced material usage while maintaining strength. ↩
-
Learn why these lightweight materials are preferred for reducing part weight across various industries. ↩
-
Explore how microcellular foams reduce density while maintaining mechanical properties. ↩
-
Find out how enhancing mold venting techniques can prevent injection defects and reduce material waste. ↩
-
Uncover how optimized rib designs contribute to structural support while minimizing material use. ↩
-
Discover how finite element analysis can predict changes in part performance when altering designs. ↩
-
Learn about microcellular foamed plastics and their role in reducing part weight while maintaining properties. ↩
-
Explore various injection molding techniques that enhance process optimization for lighter parts. ↩
-
Explore how design optimization can lead to material efficiency and sustainability improvements. ↩
-
Learn about the sustainability advantages of reducing wall thickness in product design. ↩
-
Discover how using lightweight materials can enhance sustainability in production. ↩
-
Understand how adjusting injection parameters can lead to significant energy savings. ↩