Let’s talk about something that’s on every manufacturer’s mind—reducing part weight in injection molding.
The most effective ways to reduce part weight in injection molding involve selecting low-density materials, optimizing mold design, and adjusting the injection molding process. These techniques help achieve lighter components without compromising quality or functionality.
While these initial changes may seem straightforward, there’s a wealth of insights waiting to be uncovered. Join me as we explore these strategies in detail!
Low-density materials reduce part weight in injection molding.True
Using low-density plastics like polycarbonate decreases part density.
How Can Material Selection Impact Part Weight?
Material selection plays a pivotal role in reducing part weight, optimizing performance, and minimizing costs in injection molding.
Choosing low-density materials and incorporating lightweight fillers significantly impacts part weight in injection molding. Low-density plastics and high-performance fiber fillers can reduce weight while maintaining or enhancing strength, offering a strategic advantage in manufacturing lightweight components.
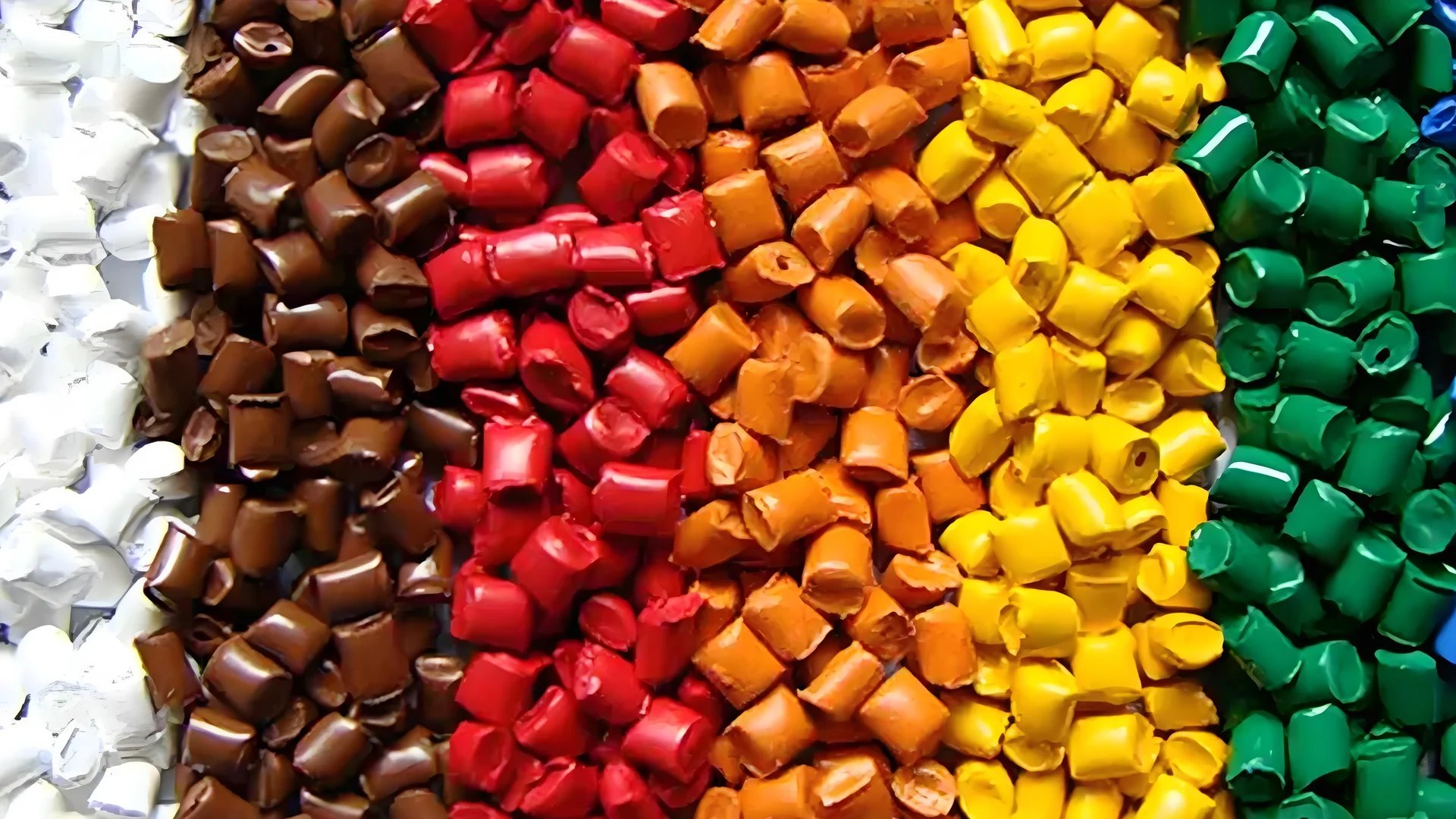
The Role of Low-Density Materials
Selecting low-density materials can dramatically decrease part weight without sacrificing strength or durability. For instance, using engineering plastics like modified polyphenylene ether (MPPO) or certain polycarbonates can effectively reduce density compared to traditional ABS materials. These materials maintain necessary strength levels, ensuring that the final product is both lightweight and robust.
In cases where high strength isn’t paramount, thermoplastic elastomers (TPE) or polyolefins provide an alternative with lower density options. These materials are particularly useful in applications where flexibility and reduced weight are prioritized.
Integrating Lightweight Fillers
The integration of lightweight fillers offers another strategy to diminish material density. Inorganic fillers such as glass beads or talcum powder can decrease overall density while enhancing rigidity and dimensional stability. However, it’s crucial to balance the filler quantity to maintain processing performance and mechanical properties.
Moreover, utilizing high-performance fiber fillers, like carbon fiber, significantly reduces weight while substantially boosting material strength and rigidity. Although costlier, these fillers present a premium choice for high-strength applications where weight reduction is critical.
Filler Type | Benefits | Considerations |
---|---|---|
Glass Beads/Talcum | Reduces density, enhances stability | Control filler amount carefully |
Carbon Fiber | Reduces weight, boosts strength | Higher cost |
Strategic Material Selection in Practice
Manufacturers can achieve optimal results by combining low-density materials with strategic filler choices. This hybrid approach not only lightens parts but also caters to specific application needs, allowing for customized solutions in diverse manufacturing scenarios.
For further optimization, the choice of materials should align with the component’s function and environmental conditions. Tailoring the material selection to these factors ensures longevity and efficiency in the final product.
Understanding how these material choices influence part weight is essential for developing lightweight products that meet modern engineering standards. It requires a nuanced approach to material science and practical manufacturing insights1 to fully leverage these benefits.
Low-density materials reduce part weight in injection molding.True
Low-density materials like MPPO decrease weight without losing strength.
Carbon fiber fillers increase part weight in injection molding.False
Carbon fiber fillers reduce weight while enhancing strength and rigidity.
What Mold Design Techniques Aid Weight Reduction?
Reducing part weight through mold design enhances efficiency and reduces costs in manufacturing.
Key mold design techniques for weight reduction include optimizing part structure, improving gate and runner systems, and leveraging advanced engineering tools.
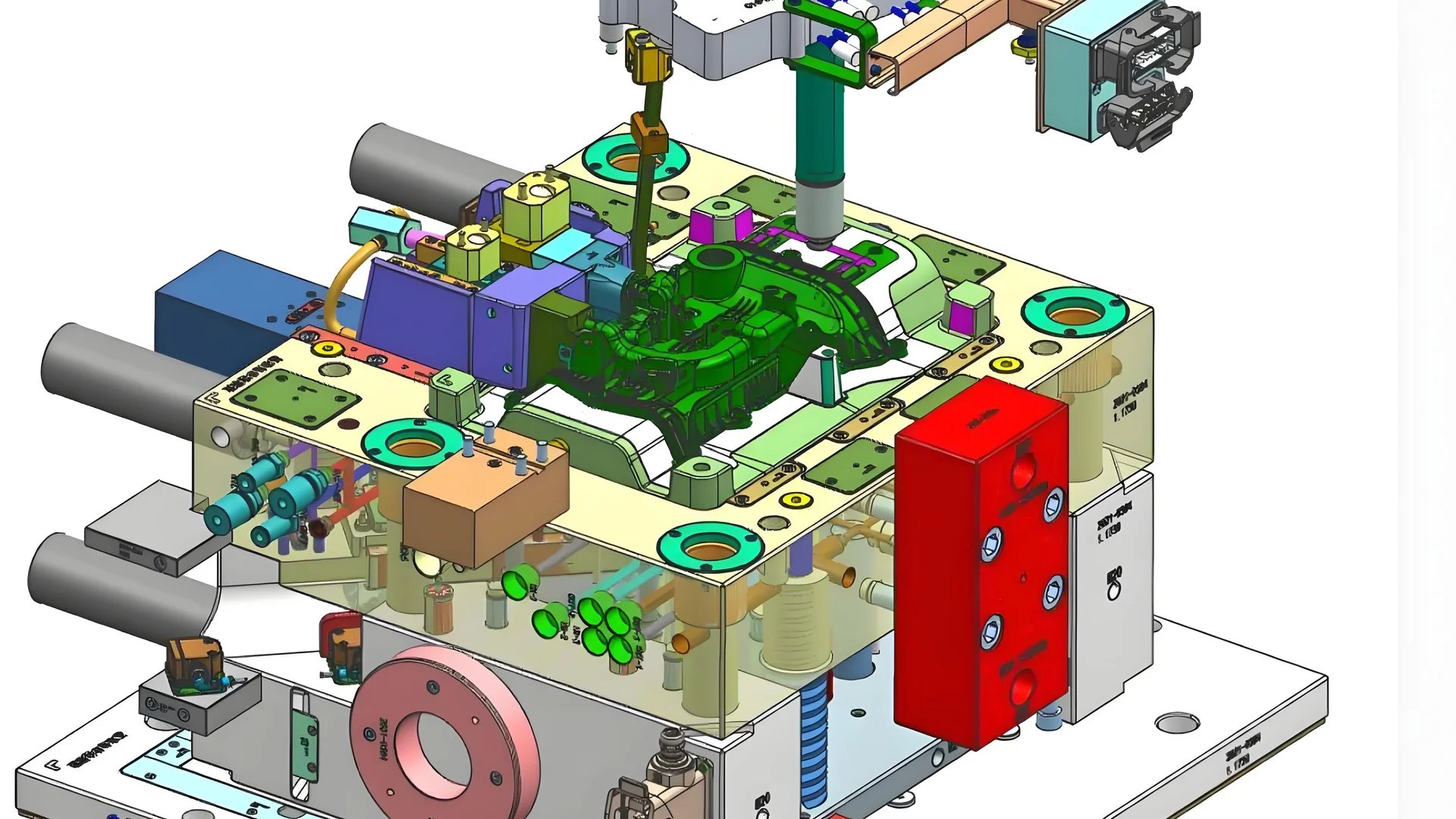
Optimizing Part Structure
One of the most impactful ways to reduce weight in mold design is by optimizing the structure of the parts themselves. This involves minimizing unnecessary wall thickness, which can be achieved through computer-aided engineering (CAE)2 analysis. By determining the minimum wall thickness requirements and reducing excess material, manufacturers can achieve lighter components without compromising structural integrity.
Designing parts with hollow structures, such as incorporating cavities or reinforcement ribs, further reduces weight. Strategic placement of these features not only decreases material usage but also enhances rigidity and strength.
Improving Gate and Runner Systems
Another crucial technique involves optimizing the gate and runner systems within the mold. By carefully selecting gate positions and numbers, manufacturers ensure even plastic flow, preventing areas of over-thickness that can increase weight. Efficient runner system designs, including reduced size and length, help minimize residual material waste.
The use of hot runner technology is particularly effective in reducing waste and maximizing material utilization, leading to lighter finished parts.
Utilizing Advanced Engineering Tools
Leveraging advanced engineering tools like CAE software aids in simulating different design scenarios. These tools allow engineers to test various configurations, ensuring optimal material usage and weight reduction while maintaining part quality.
Through these simulations, adjustments to parameters such as injection pressure, speed, and mold temperature can be fine-tuned to support weight reduction efforts without sacrificing performance.
By focusing on these mold design techniques, manufacturers can significantly reduce part weight, contributing to more sustainable and cost-effective production processes.
Optimizing part structure reduces mold weight effectively.True
Optimizing part structure, like reducing wall thickness, cuts weight.
Hot runner systems increase material waste in molds.False
Hot runner systems reduce material waste by minimizing residuals.
Which Injection Molding Process Adjustments Are Most Effective?
Achieving the right balance in injection molding adjustments can significantly impact part quality and weight, promoting efficiency and cost savings.
Adjustments such as reducing injection pressure, optimizing holding time, and controlling mold temperature are critical for minimizing part weight without sacrificing structural integrity.
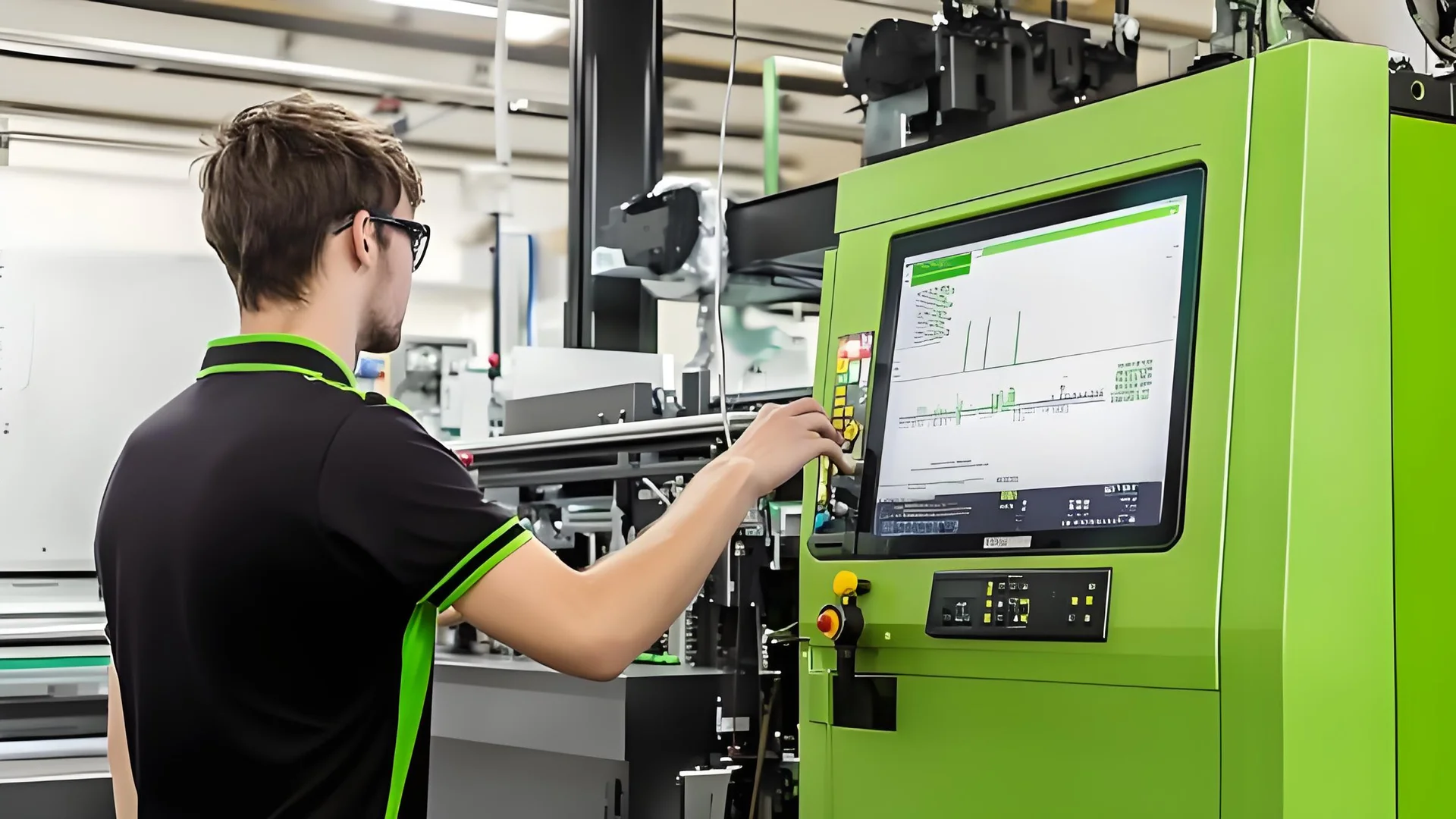
Optimizing Injection Pressure and Speed
Reducing the injection pressure and speed is crucial to minimizing the internal stresses of materials. This adjustment helps prevent excessive shrinkage and warping of parts, contributing to weight reduction. By conducting multiple mold trials, manufacturers can determine the optimal combination of pressure and speed, ensuring quality without unnecessary material use.
Fine-tuning Holding Time and Pressure
Adjusting the holding time and pressure plays a pivotal role in controlling the shrinkage rate of parts. Shortening the holding time while maintaining necessary pressure can result in significant weight savings. Utilizing CAE analysis software3 can help simulate this stage and optimize parameters effectively.
Managing Mold Temperature
Maintaining an appropriate mold temperature ensures smooth plastic flow and reduces material build-up due to flow resistance. A higher mold temperature can decrease material crystallinity, further reducing part density and weight. However, balancing temperature is key, as excessive heat may compromise production efficiency and surface quality. It’s important to experiment with specific materials to find the optimal temperature range.
Incorporating these adjustments requires an understanding of material behavior and a strategic approach to engineering solutions, as they can significantly impact both the economic and environmental aspects of manufacturing.
Reducing injection pressure minimizes part weight.True
Lowering injection pressure reduces internal stresses, decreasing shrinkage.
Higher mold temperatures increase part density.False
Higher mold temperatures reduce crystallinity, lowering part density.
How Does Reducing Part Weight Benefit Sustainability?
Reducing the weight of parts not only cuts costs but also significantly enhances sustainability, offering environmental and operational benefits.
By reducing part weight, manufacturers lower material usage, decrease energy consumption during production, and minimize emissions during transportation, thus advancing sustainability goals.
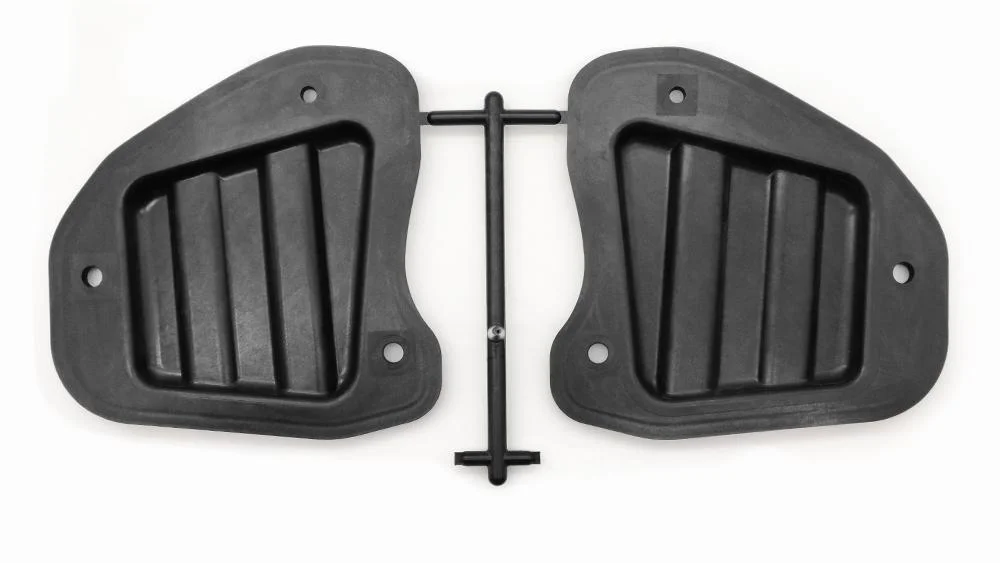
Material Efficiency and Resource Conservation
Reducing the weight of parts directly contributes to material efficiency. By using less raw material, manufacturers can significantly conserve resources. This conservation is critical in industries where raw materials are scarce or expensive. For instance, opting for low-density materials4 not only reduces part weight but also enhances product lifespan by improving performance characteristics such as thermal resistance.
Energy Savings During Production
Lightweight parts require less energy to produce. This is because smaller amounts of material mean reduced processing times and lower energy consumption in molding machines. Moreover, adjustments in the injection molding process5, like reducing injection pressure, can further diminish energy requirements.
Emission Reductions in Transportation
Lighter parts are easier and cheaper to transport. This reduction in weight translates into less fuel consumption and consequently lower carbon emissions during transportation. For companies committed to reducing their carbon footprint, optimizing part weight is an essential strategy.
Enhanced Recycling and End-of-Life Management
Parts with reduced weight often use less complex material compositions, which can simplify recycling processes. By focusing on sustainable design principles, manufacturers can ensure that lightweight parts are easier to dismantle and recycle at the end of their lifecycle, contributing to a circular economy. Utilizing materials that are recyclable or biodegradable further aids in reducing waste generation and landfill usage.
Competitive Advantage and Compliance
Sustainability has become a key differentiator in today’s market. Companies that prioritize reducing part weight can achieve a competitive advantage by offering eco-friendly products. Furthermore, as regulations around environmental impact tighten, reducing part weight can help organizations meet compliance standards more easily.
To explore more about how these techniques and strategies are implemented in real-world scenarios, check out this detailed case study6.
Reducing part weight lowers production energy consumption.True
Lighter parts require less energy due to reduced processing times.
Heavier parts are easier to recycle than lighter ones.False
Lighter parts often use simpler materials, easing recycling.
Conclusion
By implementing these techniques, manufacturers can achieve lighter, cost-efficient components while boosting sustainability and performance.
-
Gain insights into material selection impact on part weight.: Material selection significantly influences your product’s performance, durability, and cost. In this guide, we explore the most common … ↩
-
Learn how CAE helps optimize mold designs for better weight management.: CAE simulation of compression molding allows engineers to predict and optimize processing to help yield a good part design. ↩
-
Discover tools to optimize injection molding processes efficiently.: CAE Services provides consulting software and training for Moldflow Autodesk Analysis. We are the experts in Moldflow Consulting Analysis. ↩
-
Discover how low-density materials enhance performance and sustainability.: It’s Lighter and More Affordable Than Steel … Many manufacturing businesses have pivoted away from steel and moved to aluminum because it’s much … ↩
-
Learn about energy-efficient practices in injection molding.: Although it may sound obvious, programming the optimum settings on the machine controller can reduce energy costs, sometimes very significantly. ↩
-
Explore real-world applications of sustainable manufacturing techniques.: The following case studies are examples of manufacturers and other organizations that have successfully implemented sustainable manufacturing practices. ↩