Injection molding is more than just a manufacturing process; it’s an intricate dance of science and art. Managing the stress within molds is crucial to avoid the dreaded defects that can ruin a perfectly crafted product.
Reducing molding stress in injection molding involves optimizing process parameters, improving mold design, selecting suitable materials, and employing post-processing techniques. These strategies help minimize defects such as stress marks and warpage, ensuring high-quality outcomes.
Understanding the basics is just the start. Let’s dive deeper into each strategy to uncover nuanced approaches that can truly transform your manufacturing process.
Reducing injection temperature decreases molding stress by 10%-20%.True
Lowering injection temperature reduces molecular orientation, minimizing stress.
How Can Injection Parameters Influence Molding Stress?
Injection parameters play a pivotal role in shaping the stress levels within molded products. By tweaking these settings, manufacturers can control the molecular orientation and shear forces, directly impacting the quality and performance of the end product.
Injection parameters influence molding stress by affecting molecular orientation and shear forces. Adjusting temperature, pressure, speed, and cooling times can significantly reduce stress levels, minimizing defects and improving product quality.

The Impact of Injection Temperature
The injection temperature is a critical parameter that influences the fluidity of the plastic melt. A higher temperature increases fluidity, which can enhance the filling of complex mold geometries. However, it also raises the orientation of molecular chains, thereby increasing stress within the molded part.
Optimizing Temperature: Selecting an optimal temperature range based on material properties and product specifications can significantly reduce stress. For instance, a reduction in injection temperature can decrease molecular orientation by up to 20%, leading to a more stable product structure.
Pressure and Speed Dynamics
Excessive injection pressure and speed are primary contributors to increased shear forces in the mold. These forces heighten the molecular chain orientation, escalating molding stress. By fine-tuning these parameters, manufacturers can achieve a delicate balance between adequate mold filling and minimized stress levels.
- Reducing Pressure and Speed: Adjustments to the injection molding machine settings can decrease stress by 15% to 30%. This approach ensures that the shear forces remain within tolerable limits, preserving the integrity of the product.
The Role of Holding and Cooling Time
The duration of holding and cooling times is crucial in stress management. Insufficient holding time results in greater shrinkage stress post-demolding, while inadequate cooling fails to allow full solidification of the product.
- Extending Times: By extending these periods appropriately—based on the size and complexity of the product—manufacturers can reduce shrinkage stress by 20% to 35%, ensuring better dimensional stability and fewer defects.
Combining Parameters for Optimal Results
A holistic approach that combines all these parameter adjustments can lead to significant improvements in product quality. By understanding how each parameter interplays with others, manufacturers can develop robust strategies to minimize stress effectively. For instance, coupling reduced injection pressure with optimized cooling time can yield compounded benefits beyond individual adjustments.
Such strategic combinations not only enhance product quality but also promote longer mold life and lower production costs. To explore how these factors interrelate, delve into resources like Injection Molding Parameter Optimization Techniques1 that provide comprehensive insights into advanced molding strategies.
Higher injection temperature increases molding stress.True
Higher temperature raises molecular orientation, increasing stress.
Reducing cooling time decreases molding stress.False
Insufficient cooling increases stress due to incomplete solidification.
What Role Does Mold Design Play in Stress Reduction?
Mold design is pivotal in the injection molding process, significantly affecting stress distribution and product quality. By optimizing mold features, manufacturers can reduce defects and enhance durability.
Effective mold design reduces stress by optimizing gate placement, cooling systems, and demolding slopes, ensuring balanced flow and uniform cooling. These adjustments mitigate stress concentrations, enhancing the overall quality of molded products.

Understanding Mold Design’s Impact on Stress
The design of a mold directly influences how stress is distributed throughout a molded product. An effectively designed mold ensures that the plastic melt flows evenly, cools uniformly, and releases without undue friction or force. Each of these elements plays a crucial role in minimizing stress and avoiding defects such as warping or cracking.
Gate Design
The placement and number of gates in a mold are vital for maintaining balanced flow of the plastic melt. Incorrect gate positioning can lead to uneven flow, causing stress concentrations which result in defects. By employing multiple gates2 or balanced gate designs, manufacturers can ensure even distribution of material, thereby reducing stress by up to 25%.
Cooling System Optimization
A well-designed cooling system is essential for achieving uniform temperature distribution across the product. Uneven cooling leads to temperature gradients that can increase molding stress. Techniques such as rapid cooling and uniform cooling systems help to minimize these gradients, reducing stress by 20% to 30%. This not only prevents defects but also enhances the mechanical properties of the final product.
Demolding Slope Considerations
The slope of the mold’s surfaces affects how easily the product can be removed from the mold. Insufficient slope increases friction during demolding, leading to higher stress levels. By increasing the demolding slope, manufacturers can facilitate smoother release and lower stress accumulation. This adjustment can decrease molding stress by up to 20%.
Practical Insights for Implementing Effective Mold Design
Implementing these design improvements requires a thorough understanding of both material properties and product requirements. For example, different plastics have varying thermal expansion rates, which should be considered when designing cooling systems and gate placements.
Design Feature | Recommended Approach | Stress Reduction Potential |
---|---|---|
Gate Placement | Multiple/Balanced Gates | 15% – 25% |
Cooling Systems | Uniform/Rapid Cooling | 20% – 30% |
Demolding Slope | Increase Slope Angle | 10% – 20% |
By focusing on these key areas, manufacturers can significantly enhance product integrity and performance, leading to more consistent manufacturing outcomes and reduced waste from defective products. Learn more about these techniques3 to fully optimize your injection molding processes.
Balanced gate design reduces stress by 25%.True
Balanced gate designs ensure even material distribution, reducing stress.
Uneven cooling increases stress by 30%.True
Uneven cooling causes temperature gradients, increasing molding stress.
Why Is Material Selection Crucial in Minimizing Molding Stress?
Choosing the right material is fundamental in minimizing molding stress, which can prevent defects and ensure the longevity of molded products.
Material selection plays a pivotal role in minimizing molding stress by choosing low-stress plastics, adding stress-reducing additives, and considering environmental factors. These decisions help in achieving optimal product performance and longevity.

The Importance of Choosing Low-Stress Materials
Material selection is crucial because different plastics have inherently distinct stress characteristics. Crystalline plastics, for instance, tend to have higher molding stress compared to their non-crystalline counterparts. Opting for materials with lower intrinsic stress can significantly impact the final product’s durability.
For products with stringent performance requirements, materials like polycarbonate (PC) or polyphenylene ether (PPO) are preferred due to their lower stress levels. This choice is particularly essential when manufacturing components that will undergo mechanical stress during use, such as automotive parts or consumer electronics.
Role of Additives in Material Selection
Incorporating additives into the plastic resin can enhance material properties and reduce molding stress. Plasticizers, for example, make plastics more flexible, thus decreasing the brittleness and overall stress. Similarly, impact modifiers improve a material’s resistance to cracking under pressure.
Selecting the right additives depends on both the base plastic and the intended application of the product. This tailored approach can reduce molding stress by up to 25%, making it a cost-effective strategy for manufacturers aiming to optimize their production processes.
Environmental Considerations in Material Selection
Another aspect of material selection involves considering the environment where the product will be used. Factors such as exposure to UV light, temperature fluctuations, and humidity can influence the performance and longevity of plastic products. Materials chosen must withstand these conditions without compromising structural integrity.
For example, selecting a UV-resistant material for outdoor applications will prevent degradation over time, thereby maintaining the product’s functionality and aesthetic appeal.
Practical Applications and Examples
To illustrate, consider an automotive manufacturer selecting materials for interior components. By choosing a blend of low-stress plastics and appropriate additives, they can ensure components are durable, less prone to warping, and aesthetically pleasing over time.
Manufacturers should also conduct material stress tests4 to validate their material choices under real-world conditions. This step is vital for maintaining high standards of quality control and ensuring customer satisfaction.
Crystalline plastics have lower molding stress.False
Crystalline plastics generally exhibit higher molding stress than non-crystalline ones.
Additives can reduce molding stress by up to 25%.True
Incorporating specific additives into plastics can decrease molding stress significantly.
How Do Post-Processing Techniques Affect Product Quality?
Post-processing techniques are pivotal in refining product quality by reducing molding stress, enhancing durability, and improving performance.
Post-processing techniques, such as annealing and humidity conditioning, significantly affect product quality by reducing molding stress, enhancing material properties, and improving dimensional stability. These methods ensure that products meet stringent performance and durability standards.
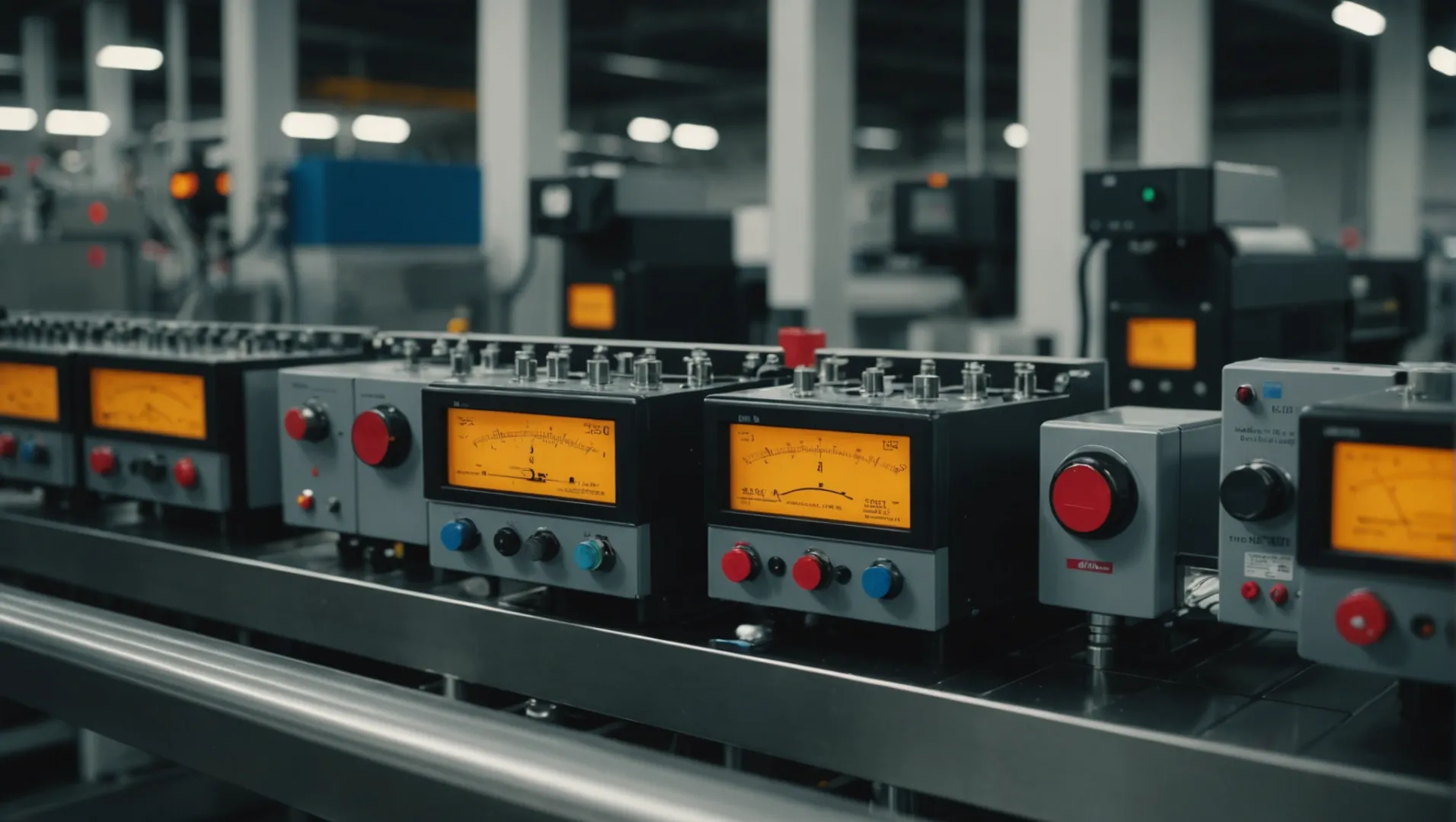
The Impact of Annealing on Product Quality
Annealing is a critical post-processing technique that involves heating the molded product to a specific temperature, maintaining it for a set duration, and then gradually cooling it. This process allows molecular chains within the plastic to relax, significantly reducing residual stress and potential defects like warping or cracking.
For instance, products made from materials like polycarbonate benefit immensely from annealing as it enhances their impact resistance and clarity. According to industry standards, annealing can reduce molding stress by up to 50%, thus improving the product’s durability5 and lifespan.
Humidity Conditioning’s Role in Stress Reduction
Humidity conditioning is particularly beneficial for hygroscopic materials such as nylon. By exposing the product to controlled humidity levels, it absorbs moisture which alleviates internal stresses. This method is effective in reducing shrinkage and distortion, which are common issues in injection-molded products.
For example, adjusting the humidity conditioning parameters can lead to a reduction in molding stress by 20% to 40%. This process also improves the dimensional stability of the product, ensuring that it maintains its intended shape and size under various environmental conditions.
Comparing Annealing and Humidity Conditioning
Method | Suitable Materials | Stress Reduction | Additional Benefits |
---|---|---|---|
Annealing | Polycarbonate, ABS | 30% – 50% | Increases clarity and impact resistance |
Humidity Conditioning | Nylon, PET | 20% – 40% | Enhances dimensional stability |
Strategic Selection of Post-Processing Techniques
Selecting the appropriate post-processing technique depends on the material used and the desired properties of the final product. For example, a manufacturer aiming for high impact resistance might favor annealing, while one focusing on dimensional accuracy may opt for humidity conditioning.
By understanding the nuances of each method, manufacturers can tailor their processes to improve overall product quality6. This strategic approach not only enhances performance but also reduces waste and rework, leading to more efficient production cycles.
Annealing reduces molding stress by 50%.True
Annealing can significantly reduce residual stress, improving product durability.
Humidity conditioning increases shrinkage in nylon products.False
Humidity conditioning reduces shrinkage by alleviating internal stresses in hygroscopic materials.
Conclusion
Applying these strategies can significantly improve product quality in injection molding. Reflect on which techniques best suit your operations to reduce defects and optimize production.
-
Explore techniques for strategic parameter adjustments in molding.: 1. Temperature Control: · 2. Injection Speed: · 3. Cooling Time: · 4. Plastic Material Selection: · 5. Screw Speed and Back Pressure: · 6. Injection … ↩
-
Discover how multiple gates improve material flow and reduce stress.: This helps to prevent the molten plastic from hardening untimely and unevenly. It also prevents plastic parts from deformations like stress … ↩
-
Explore advanced techniques for optimizing mold design and reducing stress.: Create more engaging and efficient parts, plus reduce production costs with these injection molding design tips, including living hinges, bosses, text, & more … ↩
-
Learn how to evaluate materials under real-world conditions effectively.: Mold Stress Testing, also known as Mold Stress-Relief Distortion Testing, is conducted on products that have a plastic enclosure. ↩
-
Learn how annealing enhances durability and reduces defects.: Annealing is a heat treatment method used to eliminate any unacceptable stress that may result from the manufacturing process, improve dimensional stability. ↩
-
Discover how these techniques elevate product standards.: Indeed, post-processing techniques can highly improve the microstructure, and consequently the mechanical behavior of the functional end-use … ↩