Injection molding can feel like a labyrinth of costs that many manufacturers must navigate. But what if I told you there are pathways to significant savings?
The best strategies to reduce injection molding costs include optimizing raw material selection, enhancing production processes, improving mold quality, and streamlining logistics and inventory management. Implementing these practices can lead to substantial cost savings.
While this initial answer provides a roadmap, let’s dive deeper into each strategy. You’ll discover nuanced approaches that can significantly impact your bottom line.
Optimizing raw material selection reduces injection molding costs.True
Choosing cost-effective materials and strategic procurement lowers expenses.
How Can Optimizing Raw Material Selection Cut Costs?
Choosing the right raw materials is a critical step in reducing injection molding costs, offering immediate and long-term savings.
Optimizing raw material selection reduces costs by leveraging strategic procurement, selecting cost-effective materials, and conducting performance evaluations to ensure quality without unnecessary expenditure.
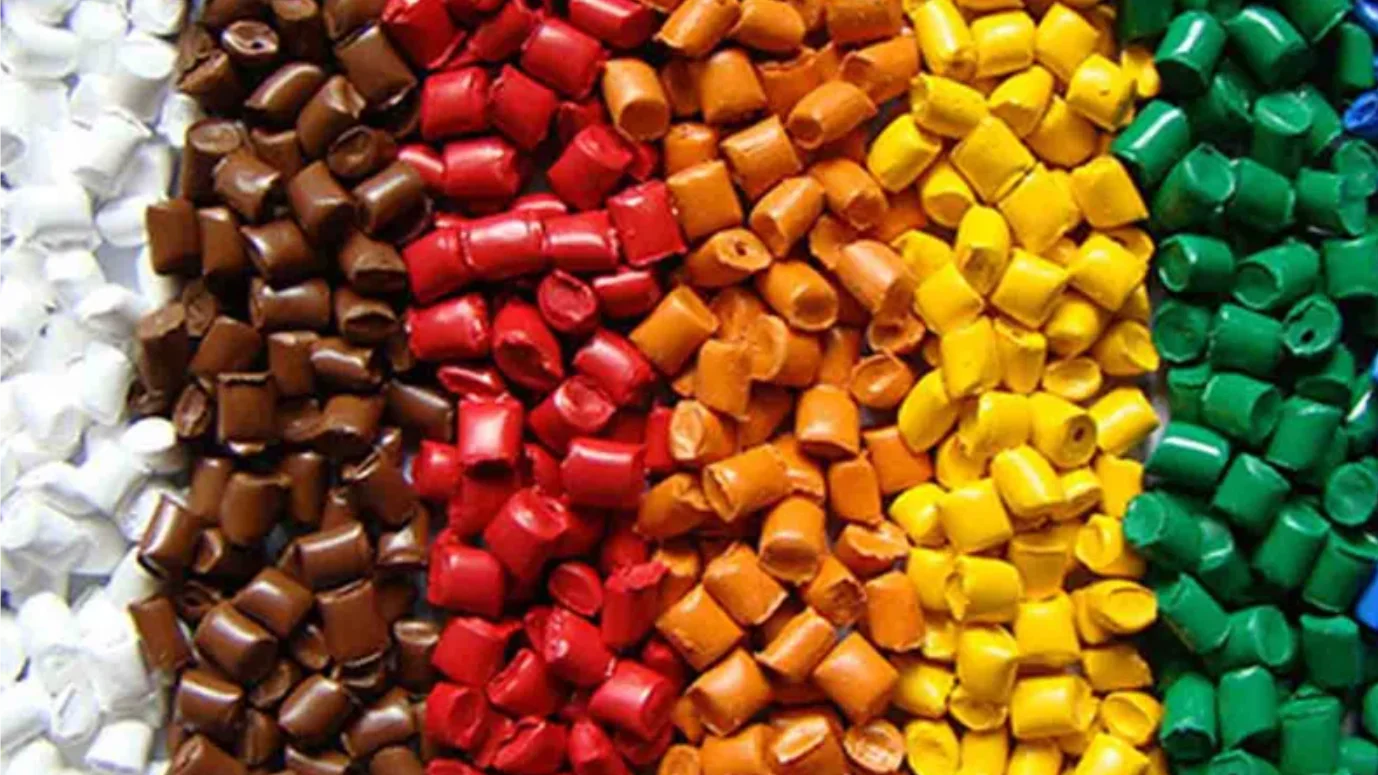
Strategic Procurement Channels
Establishing long-term relationships with reliable suppliers is fundamental for securing favorable prices. By engaging in bulk procurement1 and signing long-term contracts, companies can achieve significant cost reductions. Regular market research helps businesses anticipate price trends, allowing them to purchase and reserve materials at lower costs. This proactive approach ensures a steady supply of materials at optimal prices.
Cost-Effective Material Selection
Selecting the most appropriate materials according to product performance requirements and environmental conditions is crucial. For instance, using modified plastics or recycled materials for products with lower strength requirements can drastically cut costs while maintaining quality. Conducting thorough performance tests ensures that these alternative materials meet necessary standards, preventing quality compromises.
Performance Evaluation and Testing
Implementing a comprehensive testing regime allows manufacturers to assess raw materials for both cost-effectiveness and performance suitability. By evaluating materials under realistic conditions, businesses can make informed decisions that balance cost with quality. This process involves examining factors such as tensile strength, durability, and compatibility with existing manufacturing processes. Companies benefit by avoiding costly material failures and ensuring consistent product quality.
Optimizing the selection of raw materials is not just about choosing the cheapest option but involves a strategic balance of cost, quality, and supplier reliability. By prioritizing these aspects, businesses can enhance their competitive edge while achieving significant cost savings. Consider exploring more about procurement strategies2 to understand how they can impact your manufacturing efficiency.
Strategic procurement channels secure lower raw material costs.True
Long-term supplier relationships and bulk buying reduce costs.
Using recycled materials always compromises product quality.False
Recycled materials can meet standards for products with lower strength needs.
What Production Process Enhancements Can Save Money?
Enhancing production processes in injection molding can significantly reduce costs and increase efficiency. Here’s how.
Optimizing production process parameters, improving mold quality, and strengthening production management are key enhancements that save money in injection molding. These improvements boost efficiency, reduce waste, and lower maintenance costs, leading to substantial savings.
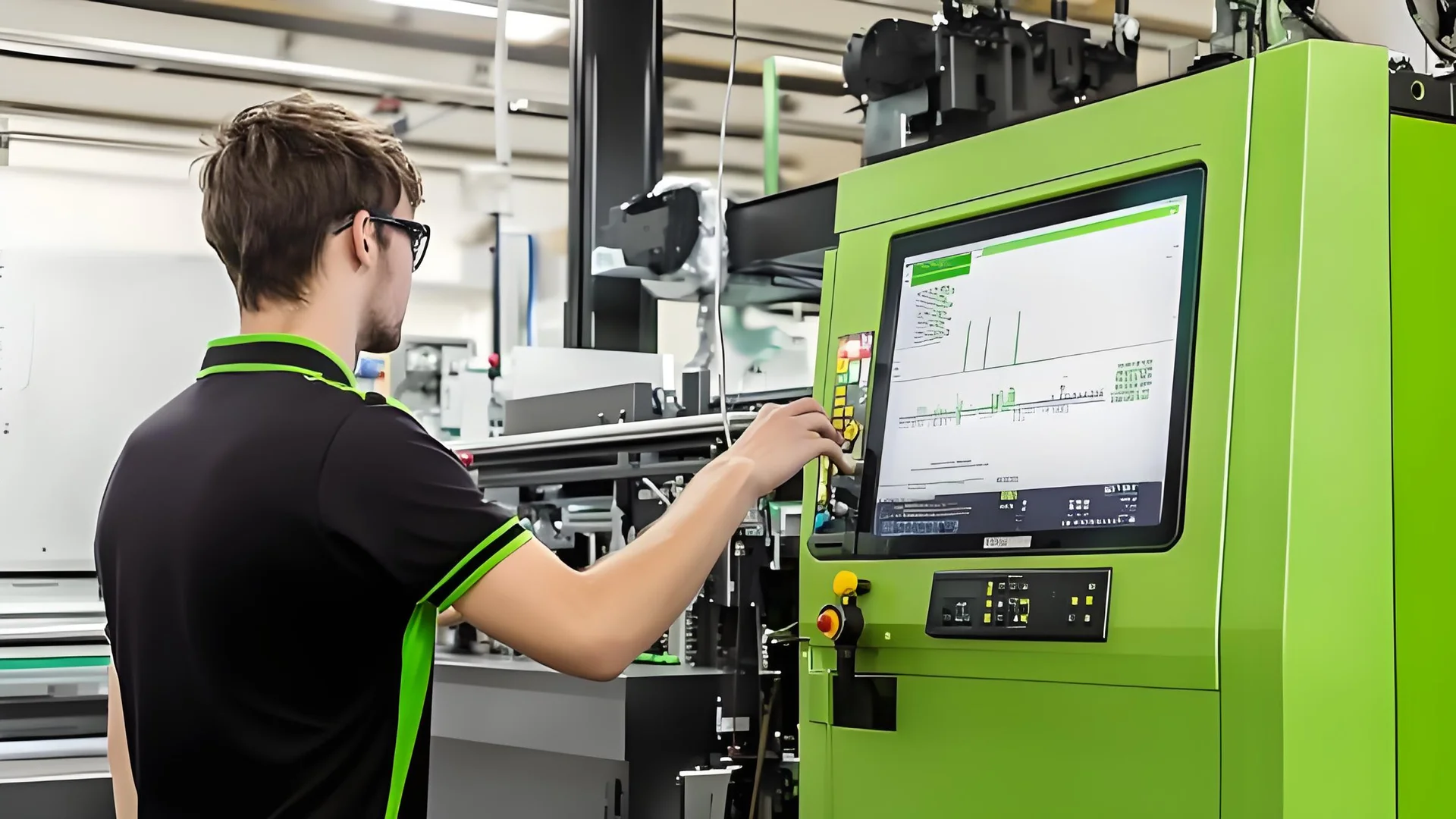
Optimizing Injection Molding Process Parameters
Fine-tuning the parameters of the injection molding process can lead to remarkable cost savings. By adjusting variables such as temperature, pressure, and speed, manufacturers can increase efficiency and minimize waste. For instance, raising the injection temperature can decrease melt viscosity and pressure, reducing both energy consumption and equipment wear. Employing advanced technologies like hot runner systems or multi-color injection molding can further enhance efficiency by minimizing material wastage and optimizing cycle times.
Parameter | Impact on Cost Savings |
---|---|
Temperature | Reduces energy consumption and wear |
Pressure | Minimizes scrap rate and boosts efficiency |
Speed | Enhances production throughput |
Implementing these strategies requires a deep understanding of machine capabilities and material behavior, highlighting the importance of regular training for operators.
Improving Mold Quality
Investing in high-quality molds is a critical step in cutting production costs. A well-designed mold ensures product precision and stability, leading to fewer defects and higher productivity. Using durable materials enhances the mold’s lifespan, thus decreasing replacement costs over time.
- Design Considerations: A properly structured mold reduces maintenance needs and enhances product quality.
- Material Selection: High-wear resistance materials extend mold life, reducing long-term expenses.
The selection of high-quality mold materials3 is crucial to withstand the rigors of continuous production.
Strengthening Production Management
Effective production management can prevent resource wastage and increase output quality. By optimizing production schedules, companies can minimize idle time and improve task allocation. Regular equipment maintenance is also vital to avoid unexpected downtimes.
- Production Planning: Align production with demand to maximize resource use.
- Employee Training: Enhance operator skills to reduce human errors and improve product consistency.
Investing in training programs for staff4 not only boosts efficiency but also fosters a culture of quality and accountability within the workforce.
By focusing on these enhancements, manufacturers can achieve significant cost reductions while maintaining high standards of quality and efficiency.
Optimizing temperature reduces energy use in injection molding.True
Higher temperatures lower melt viscosity, cutting energy costs.
High-quality molds increase defect rates in production.False
Quality molds ensure precision, reducing defects and waste.
How Does Logistics Management Impact Injection Molding Expenses?
Logistics management plays a pivotal role in controlling expenses in injection molding. Efficient logistics can drastically reduce costs associated with transportation and inventory.
Effective logistics management can significantly lower injection molding expenses by optimizing distribution methods, planning efficient routes, and controlling inventory levels. These strategies help minimize transportation costs, reduce storage expenses, and prevent production delays due to insufficient materials.
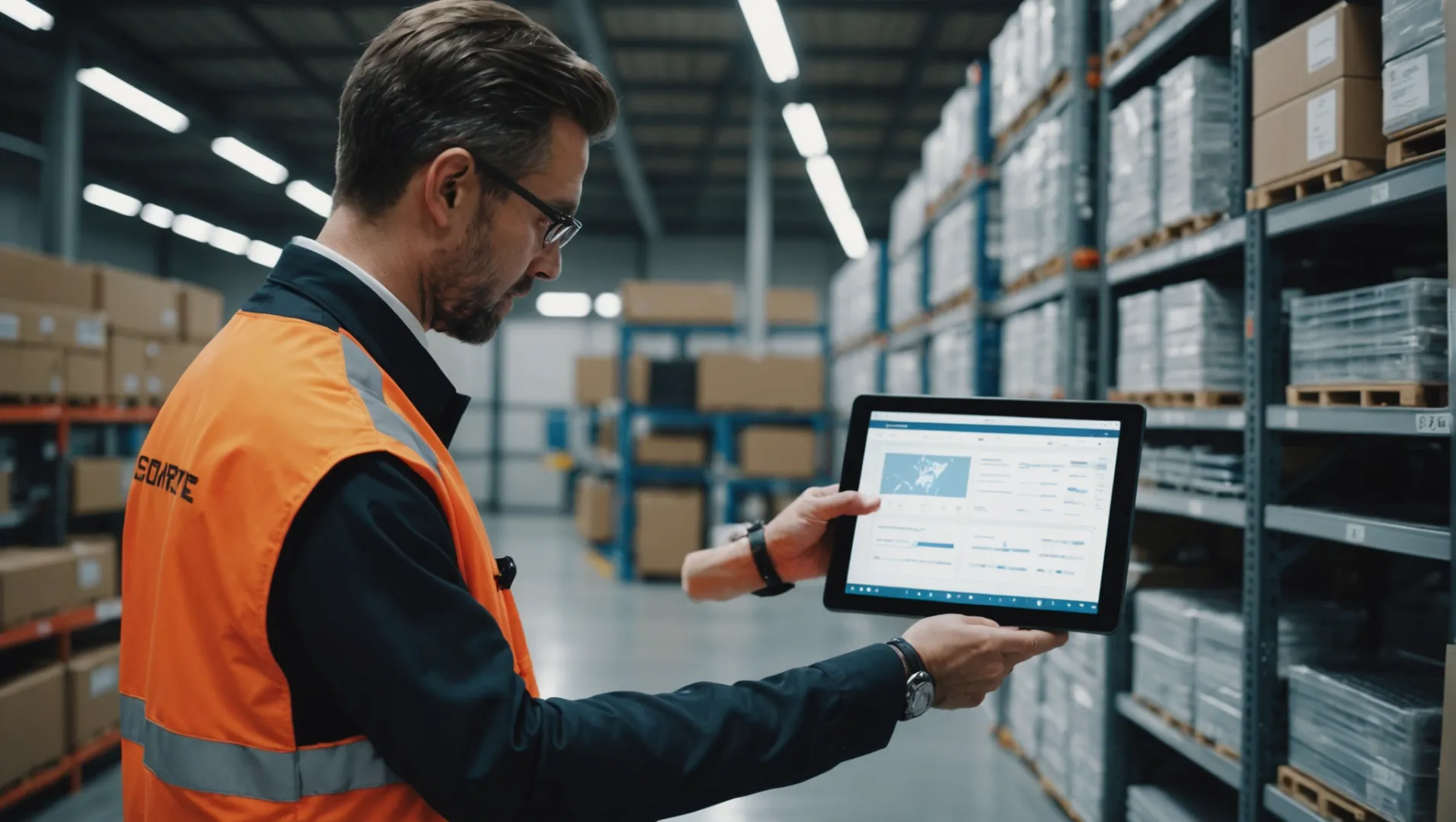
Optimizing Logistics Distribution
Selecting the right logistics method and transportation suppliers is critical. For large batch products, opting for sea or rail transportation can be cost-effective, whereas air or express delivery might be suitable for urgent orders. Implementing these strategies ensures timely delivery without incurring unnecessary costs.
Moreover, rationally planning logistics routes5 not only reduces transportation distance and time but also enhances overall logistics efficiency. This meticulous planning contributes to lower fuel consumption and less wear and tear on vehicles, further driving down costs.
Controlling Inventory Levels
A balanced inventory level is crucial to avoid excess storage costs or production halts. By aligning inventory levels with market demand and production plans, companies can prevent capital from being tied up in overstocked materials. This alignment also reduces storage costs and the risk of material obsolescence.
Advanced inventory management techniques such as ABC classification and JIT (Just-In-Time) inventory management are instrumental in maintaining optimal inventory levels. These approaches ensure that materials are available when needed without excessive stockpiling. Implementing effective inventory control measures6 can mitigate the risk of production delays and enhance cash flow.
Utilizing Technology for Logistics Efficiency
Incorporating technology into logistics processes, such as using GPS tracking and real-time data analytics, provides insights into the supply chain’s functioning. These technologies facilitate better decision-making by offering detailed visibility into the movement of goods, enabling adjustments in real-time to improve efficiency.
Additionally, leveraging automated systems for warehousing and distribution can streamline operations. Automated systems reduce human error, enhance accuracy in stock management, and optimize space utilization in storage facilities. Exploring technology solutions in logistics7 can unlock new efficiencies and cost-saving opportunities.
Efficient logistics reduces injection molding costs.True
Optimizing routes and inventory management lowers transportation and storage expenses.
Air delivery is always cheaper for large batch products.False
Sea or rail transport is generally more cost-effective for large batches.
Why Is Product Design Crucial for Cost Reduction?
In the competitive world of manufacturing, product design plays a pivotal role in controlling and reducing costs.
Product design is crucial for cost reduction as it simplifies structures, uses standardized parts, and optimizes material use, leading to lower production and maintenance costs.
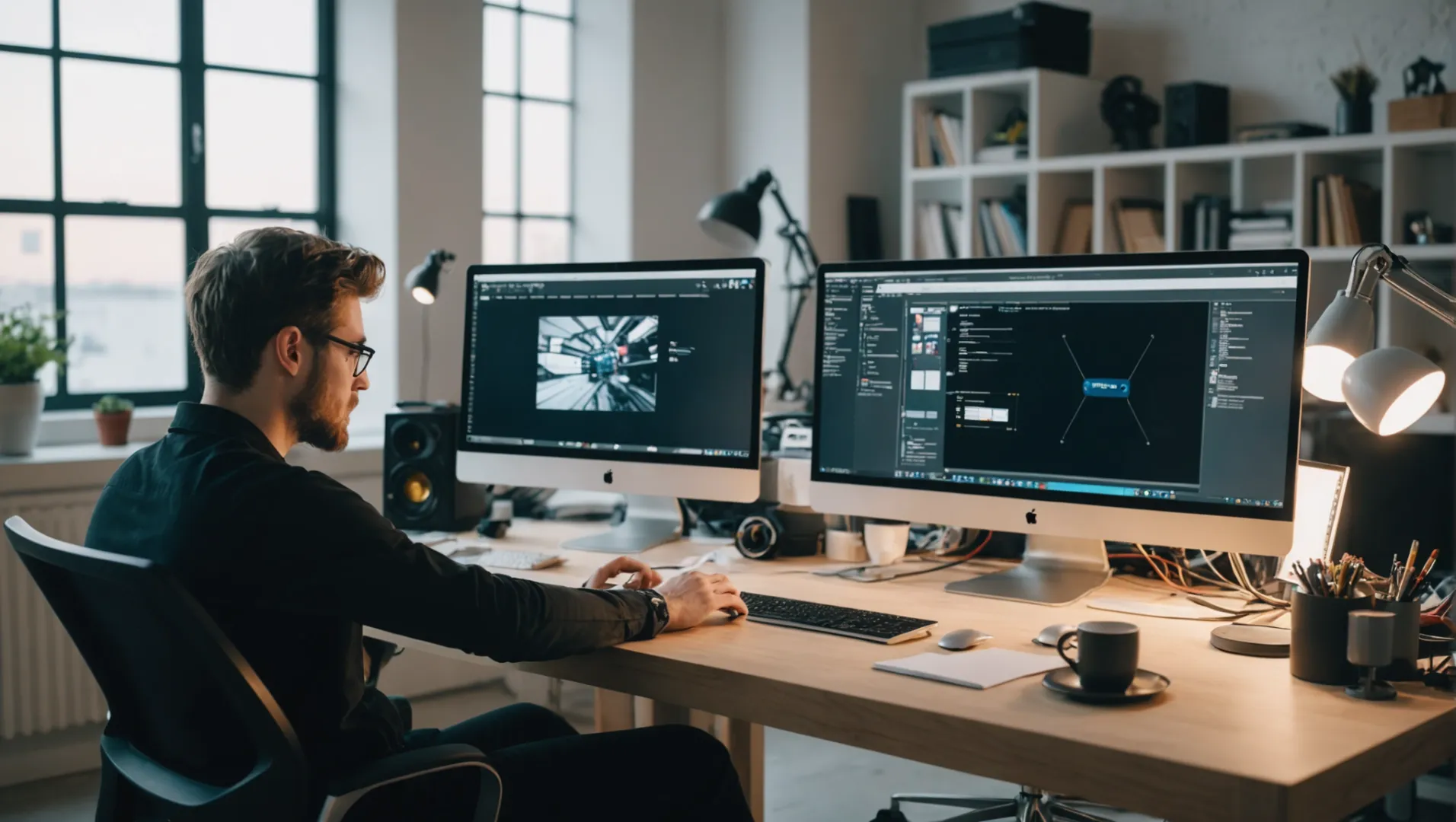
Simplifying Product Design
Simplifying a product’s design can significantly reduce manufacturing costs8. By minimizing the number of components and processing steps, manufacturers can cut down on the time and resources required for production. For instance, reducing the number of parts in an assembly can lower labor costs and reduce potential failure points in a product.
Additionally, by optimizing the size and weight of a product, companies can save on material costs. For example, designing a product with thinner walls can reduce the amount of raw material needed without compromising on strength and durability. These reductions not only decrease the cost of materials but also result in less energy consumption during production.
Implementing Standardized Designs
Using standardized components and design specifications is another effective strategy9 for cost reduction. Standard parts are typically more readily available, less expensive, and easier to integrate into the manufacturing process. This standardization reduces the need for custom manufacturing processes and allows companies to benefit from economies of scale.
By adhering to industry standards, companies can ensure consistent product quality while also reducing certification and testing expenses. For instance, in the automotive industry, using standard fasteners across different models reduces inventory complexity and simplifies assembly processes.
Advantages of Standardized Design | Description |
---|---|
Cost Savings | Reduces manufacturing and procurement costs |
Improved Efficiency | Streamlines production processes |
Quality Assurance | Ensures products meet regulatory standards |
Material Optimization
Selecting the right materials is a critical aspect of product design that directly impacts cost. By choosing cost-effective materials that meet performance requirements, companies can save significantly on raw material expenses. For example, opting for recycled or modified plastics for non-load-bearing components can maintain quality while reducing costs.
Performance testing is vital to ensure that alternative materials meet necessary standards without compromising on durability or functionality. This approach not only reduces initial material costs but also minimizes waste and environmental impact.
In conclusion, product design is not just about aesthetics or functionality; it’s a strategic component of cost management in manufacturing. By simplifying designs, standardizing components, and optimizing material selection, companies can achieve substantial cost savings while maintaining high-quality production standards.
Simplifying design reduces manufacturing costs.True
Fewer components and steps cut labor and resource expenses.
Standardized parts increase manufacturing costs.False
Standardization reduces costs by simplifying processes and inventory.
Conclusion
By focusing on strategic areas like raw materials and logistics, I can effectively reduce injection molding costs while enhancing quality.
-
Learn how bulk procurement reduces costs in manufacturing processes.: Techniques such as bulk purchasing, vendor consolidation, value analysis, and supplier negotiation can help streamline costs without compromising quality. ↩
-
Explore advanced procurement strategies to boost efficiency and reduce costs.: Techniques such as bulk purchasing, vendor consolidation, value analysis, and supplier negotiation can help streamline costs without compromising quality. ↩
-
Learn how superior materials extend mold life and reduce costs.: Injection molding can help manufacturers produce highly complex, detailed plastic parts in large volumes with virtually no deviation. ↩
-
Understand how skilled employees minimize errors and enhance productivity.: Well-trained employees are better equipped to maintain high standards of quality and efficiency. Training in quality control techniques, such as … ↩
-
Discover strategies to plan routes that save time and reduce costs.: Utilize Route Optimization Software: Implement route optimization software to streamline the planning process by considering various factors … ↩
-
Learn effective JIT techniques to balance inventory levels efficiently.: With a JIT model, the goal is to physically stock zero inventory until a customer places an order. Learn how to reduce inventory in retail … ↩
-
Explore how technology can optimize logistics operations.: From advanced data analytics to digital twins to automation we have identified the 10 important logistics technologies and trends that will redraw the sector. ↩
-
Learn how simplified designs cut costs by reducing components and processing steps.: Simplifying product design and cutting costs involves streamlining the design process, focusing on core functionalities, and leveraging efficient manufacturing … ↩
-
Discover how standardization cuts costs and boosts manufacturing efficiency.: Standardization helps you identify and resolve bottlenecks or other inefficiencies in your production processes. This can result in your … ↩