Solving the complexities of injection mold processing often feels like an endless puzzle. However, a few clever methods probably reduce expenses without sacrificing quality. Costs go down. Quality remains high.
Implementing effective strategies like optimizing mold design, using efficient materials, improving cycle times, and regular maintenance can significantly reduce injection mold processing costs.
Continue reading to learn how these methods might completely change your manufacturing process. In the beginning, when I started in mold design, every penny really mattered. These techniques completely changed everything for me and my team. They improved not only our operations but also our profits. Let’s explore these useful solutions that could really help in your production workflow.
Optimizing mold design reduces processing costs.True
Efficient mold design minimizes material waste and cycle time.
Using expensive materials lowers production costs.False
Expensive materials increase initial costs, not reduce them.
How Can Mold Design Optimization Lower Costs?
Have you ever thought about how small changes in mold design save money?
Optimized mold design probably cuts costs. Designers simplify parting surfaces for easier processes. Efficient demoulding methods really help. Affordable materials reduce expenses. Advanced technologies lead to better results. These methods save time and decrease waste. Production expenses fall because of these changes.
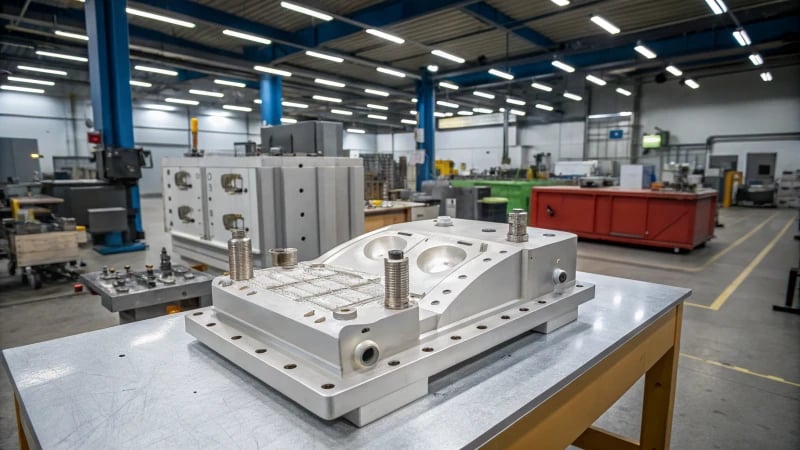
Optimizing Mold Structure
I remember my first encounter with a complex mold design. It felt like trying to solve a Rubik’s cube while blindfolded. Over time, I discovered the beauty of keeping things simple. Designing straightforward parting surfaces saves time and reduces costs significantly. Flat or gently curved surfaces allow for easier precision control and shorten processing time. Using standard demoulding parts, such as ejector pins and push plates, helps to avoid expensive custom designs.
Element | Strategy |
---|---|
Parting Surface | Use flat/simple curved surfaces to ease precision control |
Demoulding Mechanism | Employ standard ejector pins, sliders |
Demoulding Mechanism Integration
Dealing with products with undercut structures used to be daunting. Complex linkage mechanisms were difficult to design and manufacture. Then, I found that simplicity worked wonders. Inclined ejectors or slider structures provided a smart solution. This choice reduced my stress and greatly lowered both design and manufacturing expenses.
Material Selection for Cost Efficiency
Choosing Cost-Effective Materials
I once believed only expensive materials could perform well. However, I soon realized my mistake. For non-essential products like regular toys, choosing less costly steels like P20 was revolutionary. It delivers the needed durability without high expenses.
Consider innovative materials like surface-treated steels which offer high hardness at the surface but maintain toughness internally, balancing performance and cost effectively.
Material Type | Advantage |
---|---|
P20 Steel | Affordable, good for general use |
Surface-Treated Steel | High surface hardness, retains core toughness at a potentially lower cost |
Advanced Processing Techniques
Selecting Processing Technology
In my early career, I often used high-tech solutions for all problems. Then, I discovered that traditional methods, like turning and milling, work perfectly for simpler parts and are much more budget-friendly. Now, I choose CNC processing only when it’s absolutely necessary.
Advanced methods like high-speed cutting enhance efficiency despite initial equipment costs, benefiting mass production scenarios by reducing unit mold expenses in the long run.
Advanced Processing Techniques1 offer benefits in terms of speed and quality improvements that justify their upfront investment for large-scale operations.
Improving Material Utilization
I have learned to carefully plan the size and shape of mold parts. Using standard material sizes for inserts reduces waste and significantly streamlines production. Aligning part dimensions with standard specifications lets me use leftover materials effectively.
Efficient material utilization has become a vital part of my strategy. It ensures that we very effectively use every resource at our disposal.
Material Utilization Strategies2 can optimize resource usage, cutting down unnecessary expenditure on excess materials.
Flat parting surfaces reduce mold processing costs.True
Flat surfaces are easier to control and process, reducing complexity.
Using custom demoulding components lowers costs.False
Custom components increase design and manufacturing expenses.
How Can Material Selection Lead to Cost Savings?
Have you ever thought about how choosing the right materials really saves a lot of money in manufacturing?
Picking the correct materials lowers expenses. Production becomes easier and waste goes down. These choices help create long-lasting, high-quality products. This is all possible while staying within budget.
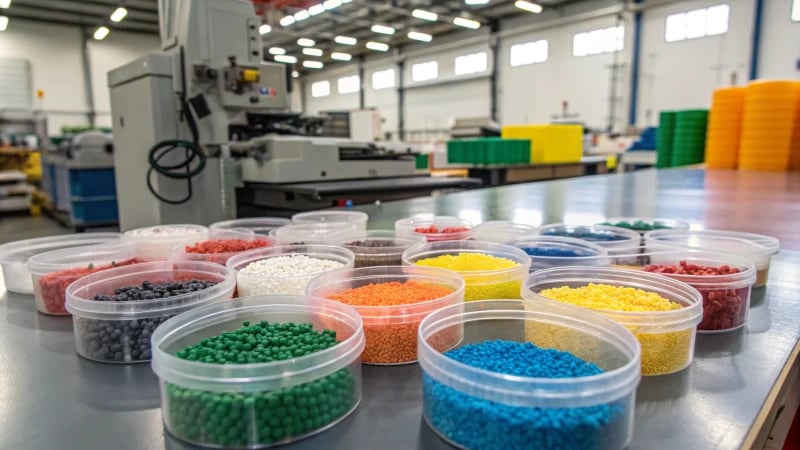
Importance of Choosing Cost-Effective Materials
I remember my first big project as a designer. Every penny mattered. The materials we picked could either help or hurt our budget. We chose cost-effective options, like the new mold materials3, to save money. These materials kept costs low while staying strong and durable. This choice kept us under budget and taught me the value of careful material selection—a very important lesson.
Improving Material Utilization Rate
When I began in the industry, wasting material was common. Strategic planning helped fix this problem. Using standard size materials4 reduced waste significantly. For example, matching mold inserts with standard steel specifications saved money—it was like solving a puzzle. Finding the perfect fit minimized waste, which really worked well.
Material | Cost-Effectiveness | Durability |
---|---|---|
P20 Steel | High | Moderate |
Composite | Moderate | High |
Utilizing New Materials and Technologies
Embracing new technologies changed the game. Surface-treated steels5 are a great example; they resist wear without costing too much. This discovery balanced performance and cost in our projects, transforming how we worked.
Aligning Material Choice with Production Needs
Over-specification caused us to spend more than needed. Aligning materials with production needs saves money—lower-cost steels are used when mold longevity isn’t vital, saving money while keeping quality intact without extra expenses.
Integrating Material Selection in Mold Design
I remember a project where material choice during design led to big savings. We simplified the mold structure, reducing complexity and enhancing cost-effectiveness by streamlining mold processing technology6. A well-chosen material boosts production without losing quality—a lesson in efficiency that underscores how crucial material selection is to success.
Strategic material selection is not only about cost-cutting; it’s about informed decisions supporting sustainability and efficiency. Balancing quality and economy is an art, making designing a rewarding challenge when done right.
Material choice affects manufacturing costs.True
Choosing cost-effective materials reduces initial and maintenance costs.
Standard size materials increase waste.False
Using standard sizes minimizes waste and cuts excess processing costs.
How Can Advanced Processing Technology Enhance Cost Efficiency?
Have you ever thought about how advanced technology saves money in factories? It’s not only about fancy devices. It’s about smarter methods. These methods reduce waste and improve efficiency. Factories run better with less.
Advanced processing technology is very important for saving money. It organizes production, reduces waste and improves accuracy. Methods like CNC machining and high-speed cutting make operations better. These methods lower costs for materials and labor.
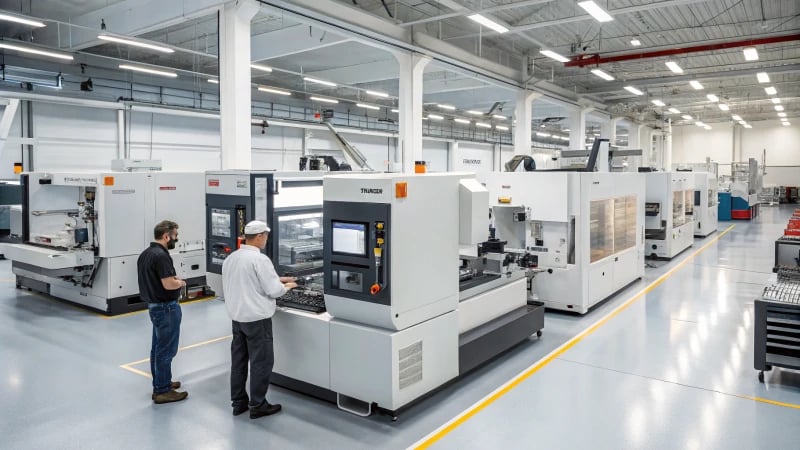
Optimization of Mold Design
When I began learning about mold design, I didn’t know that advanced processing technology could really change cost efficiency. But it’s a big improvement! Here’s how it works.
At the mold design stage, leveraging advanced processing technology is pivotal. Techniques such as CNC machining enable the optimization of mold structure7. By simplifying the parting surface design, you reduce complexity and cost. Mold flow analysis further aids in refining parameters, decreasing the need for costly modifications.
Material Selection and Utilization
I used to spend a lot of time thinking about which materials to use. Advanced technology has made choosing cost-effective materials really easy. For example, using mold flow analysis helps optimize gate placement, reducing trials and waste. Furthermore, new composite materials can be considered, ensuring durability while being cost-efficient.
Material | Characteristics | Benefits |
---|---|---|
Cost-effective | Good processing performance | Suitable for toy plastic molds |
Composite Materials | Surface strengthened, durable | Cost-effective alternative |
Processing Technology Optimization
At first, I doubted high-speed cutting because it costs more initially. In mass production, though, it’s like finding a hidden treasure. Over time, unit costs drop a lot. Advanced processing techniques like high-speed cutting are essential for efficiency. Although initially costly, they decrease unit costs over time in mass production settings. The standardization and modular processing8 of molds also contribute to reduced costs by promoting mass production of parts.
- Example: High-speed cutting improves surface quality and speed; it’s great for complex parts.
- Control Accuracy: Tailor precision to product needs by avoiding unnecessary costs from over-pursuing high precision for non-critical parts.
Using these technologies has really made me work more efficiently and also improved product quality while reducing waste. I’ve learned that advanced processing technology is not just about keeping up; it’s about doing really well in today’s manufacturing world.
CNC machining reduces mold design complexity.True
CNC machining simplifies parting surface design, reducing complexity and cost.
High-speed cutting increases unit costs over time.False
High-speed cutting decreases unit costs in mass production settings.
How Can Standardization and Modular Processing Drive Savings?
Have you ever thought about how simplifying processes leads to big savings? Standardization and modular processing transform manufacturing efficiency. This is really a remarkable change.
Standardization and modular processing lower costs by simplifying manufacturing. These methods reduce complexity and waste. Companies often need fewer custom parts. Efficiency greatly increases. Production becomes more scalable. Manufacturing expenses probably decrease.
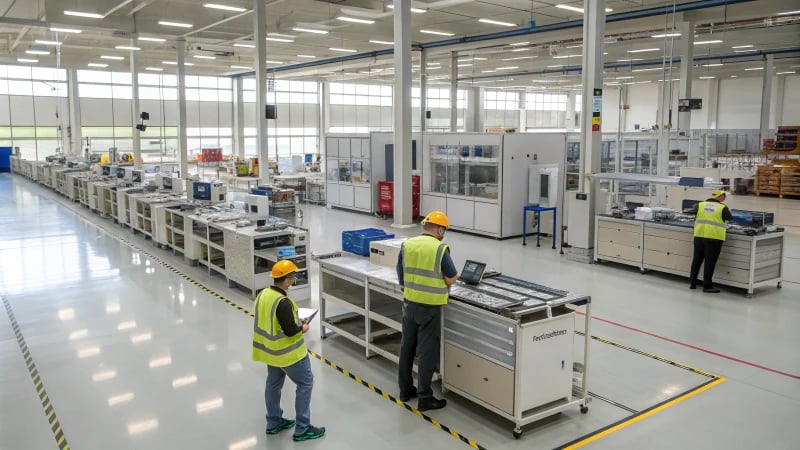
The Role of Standardization in Cost Reduction
Standardization in manufacturing involves using uniform specifications for parts and processes, significantly reducing variability. When I started designing molds, I noticed I wasted a lot of time creating custom parts. This experience taught me the importance of standardization. Using the same specifications everywhere simplified my work. In the mold design phase9, choosing simple mold structures with easy-to-work parts saved both time and money. It felt like organizing a messy closet; having fewer options reduced stress and increased efficiency.
-
Mold Material Selection: Not all projects need the best materials. Prioritizing cost-effective materials that meet the required life expectancy without overshooting on quality can lead to substantial savings. I found that choosing cheaper options, like P20 steel for easier jobs, lowered costs and still kept good quality. It’s about finding the right balance between strength and cost.
-
Material Utilization: Careful planning of mold parts can turn what looks like waste into savings. Planning the size and shape of mold components to maximize material usage is essential. Sticking to standard sizes helped me cut scrap and use materials better, similar to finding new uses for fabric leftovers in sewing.
Advantages of Modular Processing
Modular processing involves breaking down products into smaller, interchangeable modules. Dividing products into smaller parts changed everything for the better. This approach not only accelerates assembly but also facilitates easier maintenance and upgrades.
-
Efficient Assembly and Maintenance: With components designed to fit together seamlessly, modular systems minimize downtime during assembly or repairs. Modular systems reduced repair time; quick fixes led to faster production resumes, saving money.
-
Scalability and Flexibility: The use of standard modules allows manufacturers to easily scale production up or down based on demand. Standard modules allowed for easy expansion of operations, similar to increasing a recipe’s servings without losing flavor.
Case Studies on Cost Savings
Seeing these ideas working in different industries was very motivating:
Industry | Application | Outcome |
---|---|---|
Electronics | Modular smartphone designs | Reduced production costs |
Automotive | Standardized engine components | Lowered manufacturing expenses |
Construction | Prefabricated building modules | Minimized on-site labor costs |
In every example, using modular strategies lowered direct costs like materials and labor and also indirect costs such as time-to-market.
Learning these methods showed me how businesses probably improve efficiency while reducing expenses. Exploring more about modular technology applications10 highlighted the chance for industry-specific improvements—something I wish I had discovered earlier in my career.
Standardization reduces mold design costs.True
Using uniform specifications simplifies processes, cutting design costs.
Modular processing increases assembly downtime.False
Modular processing minimizes downtime by facilitating quick assembly.
Conclusion
Effective strategies to reduce injection mold processing costs include optimizing mold design, selecting cost-effective materials, and utilizing advanced processing technologies for improved efficiency and reduced waste.
-
Explores how advanced methods boost speed and quality, justifying their cost in mass production. ↩
-
Offers insights on planning mold parts to minimize waste and reduce material costs. ↩
-
Discover new materials that reduce costs without compromising on performance, offering innovative solutions for modern manufacturing challenges. ↩
-
Learn how using standard size materials minimizes waste and lowers costs, enhancing efficiency in production processes. ↩
-
Explore how surface-treated steels provide durability and cost savings, optimizing material performance for industrial applications. ↩
-
Understand how advancements in mold processing technology can streamline production and reduce costs effectively. ↩
-
This link provides insights into CNC machining benefits, explaining how it optimizes mold structures for cost reduction. ↩
-
Learn about the cost benefits and efficiency improvements from standardizing mold components. ↩
-
Learn how standardized practices can simplify mold design, reducing complexity and cost. ↩
-
Explore various industries where modular technology has been successfully implemented. ↩