In the competitive world of manufacturing, efficiency is paramount. Rapid cooling technology is revolutionizing injection molding processes, offering remarkable benefits for industries aiming to streamline production and enhance product quality.
Rapid cooling technology enhances injection molding efficiency by optimizing the cooling process, reducing cycle times, and improving part quality. Techniques like advanced cooling channels and intelligent systems enable faster heat dissipation, leading to increased productivity and reduced costs.
While the concept of rapid cooling might seem straightforward, its implementation involves a variety of sophisticated techniques and technologies. The following sections delve deeper into these methods, providing insights into how they transform manufacturing processes.
Rapid cooling reduces injection molding cycle times.True
Rapid cooling shortens the time needed for parts to solidify, boosting efficiency.
- 1. What Are the Key Benefits of Rapid Cooling Technology in Injection Molding?
- 2. How Do Built-In Cooling Channels Improve Cooling Efficiency?
- 3. What Role Does Intelligent Cooling Control Play in Injection Molding?
- 4. Can Advanced Cooling Media Revolutionize Injection Molding Processes?
- 5. Conclusion
What Are the Key Benefits of Rapid Cooling Technology in Injection Molding?
Rapid cooling technology is revolutionizing injection molding by dramatically shortening cycle times and enhancing product quality, essential for competitive manufacturing.
Rapid cooling technology enhances injection molding by reducing cycle times, improving dimensional accuracy, and boosting overall product quality. It achieves this through advanced cooling techniques that ensure efficient heat dissipation, making manufacturing processes faster and more cost-effective.
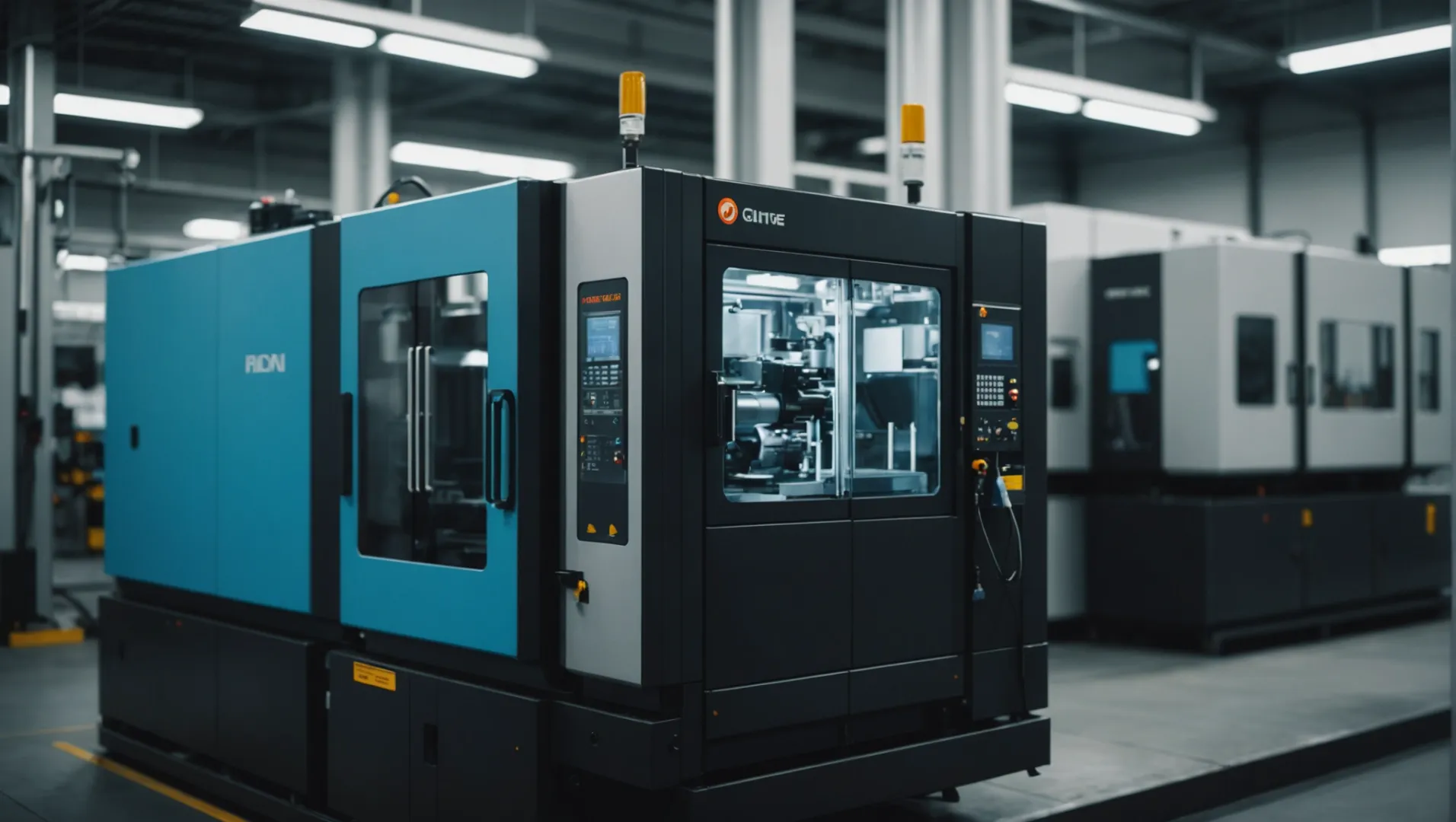
Reduced Cycle Times
One of the most significant advantages of rapid cooling technology is its ability to significantly reduce cycle times. By optimizing cooling channel designs1 and utilizing efficient cooling media, manufacturers can decrease the time it takes for an injection molded part to cool down, allowing for faster production cycles.
For instance, built-in cooling channels with intricate designs enable more effective heat removal, thus shortening the cooling phase. This not only accelerates production but also enhances throughput, making it a pivotal factor in high-volume manufacturing environments.
Enhanced Product Quality
Rapid cooling technology contributes to improved dimensional accuracy2 and surface finish of injection molded parts. Uniform cooling across the mold reduces internal stresses and warpage, resulting in parts that meet precise specifications with minimal defects.
Special-shaped cooling channels, such as conformal cooling, are custom-designed to follow the contours of the mold cavity, providing even heat dissipation. This approach minimizes the risk of deformation and dimensional deviations, ensuring high-quality outputs.
Cost Efficiency
By reducing cycle times and enhancing part quality, rapid cooling technology helps lower operational costs. Faster cycles mean increased productivity with the same equipment setup, maximizing returns on investment.
Furthermore, advanced technologies like intelligent cooling control systems optimize energy usage by precisely managing temperature and flow parameters. Such systems ensure that cooling processes are efficient, further contributing to cost savings.
Innovation with New Cooling Media
The introduction of novel cooling media3 such as liquid metals and phase change materials marks a significant leap in injection molding efficiency. These materials exhibit superior thermal properties that accelerate heat transfer, thereby enhancing cooling rates.
For example, phase change materials can absorb significant amounts of heat during their transition phases, providing a rapid reduction in mold temperature. This innovative approach not only speeds up production but also opens doors for new applications in the industry.
Sustainability Considerations
Finally, rapid cooling technology supports sustainable manufacturing by reducing energy consumption and material waste. Shortened cycle times lead to lower energy usage per part produced, while improved product quality minimizes scrap rates and material wastage.
The adoption of eco-friendly cooling media further aligns with sustainability goals, reducing the environmental footprint of injection molding processes. By leveraging these technologies, manufacturers can achieve both economic and environmental benefits.
Rapid cooling reduces injection molding cycle times.True
Rapid cooling optimizes heat dissipation, shortening the cooling phase.
New cooling media increase energy consumption in molding.False
Innovative media enhance efficiency, reducing overall energy use.
How Do Built-In Cooling Channels Improve Cooling Efficiency?
Built-in cooling channels are game-changers in the injection molding industry, significantly boosting cooling efficiency and productivity.
Built-in cooling channels improve cooling efficiency by facilitating rapid heat transfer from the mold, reducing cycle times, and ensuring uniform cooling. This innovative design allows for precise temperature control, minimizing defects and enhancing the quality of injection molded parts.
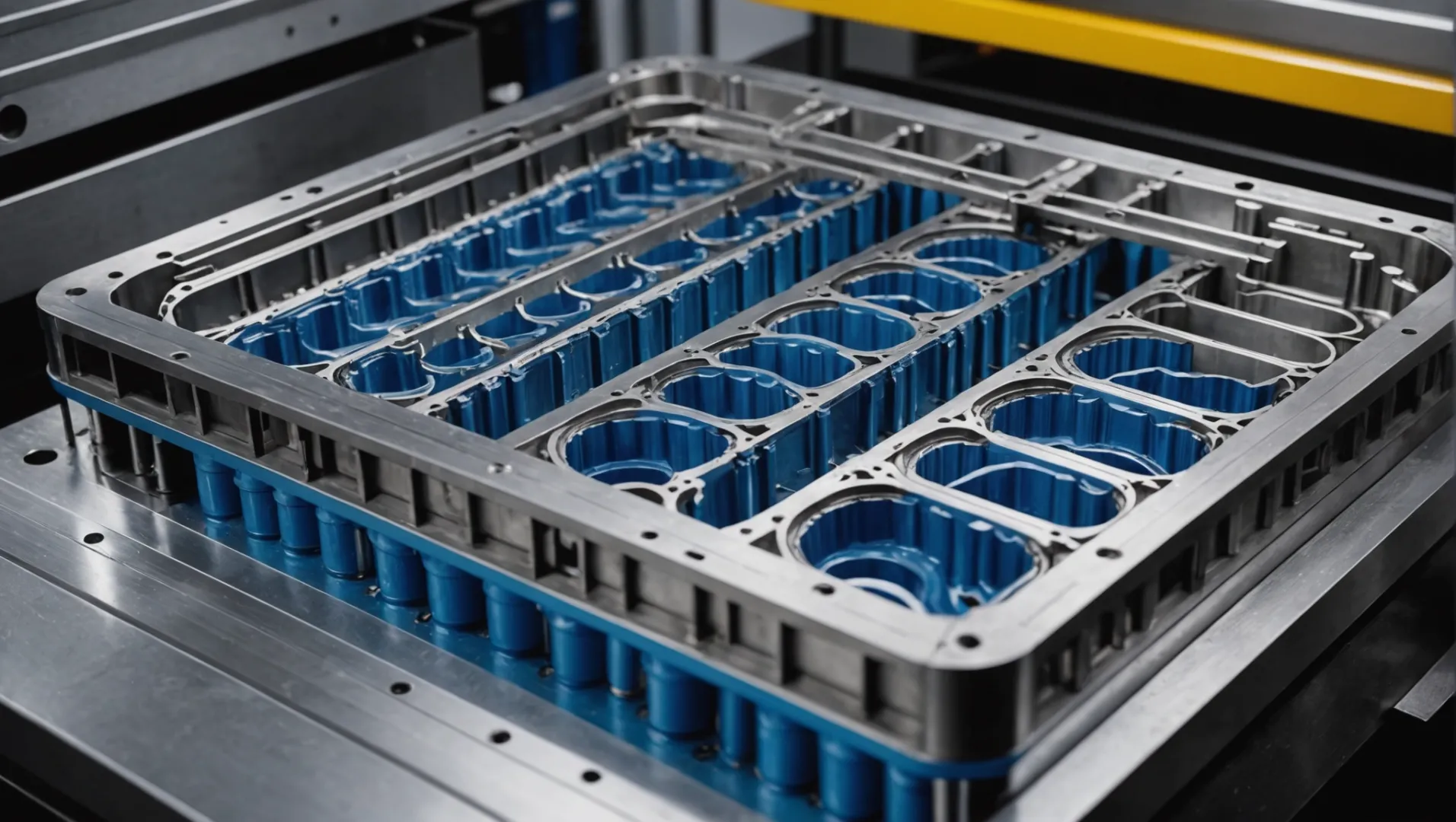
The Science Behind Built-In Cooling Channels
Built-in cooling channels are meticulously integrated into the design of injection molds to enhance the cooling process. These channels enable the flow of coolants—usually water or specialized cooling oils—close to the mold’s surface. This proximity ensures that heat is swiftly removed, allowing the molded part to solidify quickly and uniformly.
Consider a scenario where a spiral or circuitous network is employed within the mold. This design maximizes the contact area between the coolant and the mold, significantly increasing the efficiency of heat transfer. For instance, precision injection molds often leverage such designs to boost the overall cooling rate.
Advantages of Special-Shaped Cooling Channels
While traditional circular or rectangular channels are common, special-shaped channels, like conformal cooling channels, are gaining traction. These are tailored to fit the mold cavity’s shape and the part’s structure. As a result, they offer more consistent cooling and minimize issues like deformation or dimensional inaccuracies.
Special-shaped channels are particularly beneficial in complex injection molding tasks where uniformity is crucial. By matching the coolant path to the geometry of the part, these channels ensure even distribution of temperature and prevent hotspots that could compromise part quality.
Impact on Cycle Times and Production Quality
The implementation of built-in cooling channels has a direct impact on reducing cycle times in injection molding. Faster cooling means quicker cycle completion, allowing for increased throughput without sacrificing quality. This efficiency translates into cost savings and improved production schedules.
Moreover, by maintaining consistent temperatures throughout the mold, built-in cooling channels help reduce common defects such as warping or internal stresses. This results in higher-quality finished products with fewer rejections or need for post-processing.
Optimizing Cooling Media for Maximum Efficiency
To fully leverage built-in cooling channels, optimizing the cooling media is essential. Adjustments in parameters like coolant temperature, flow rate, and pressure can dramatically affect performance. Using low-temperature water or advanced coolants can enhance heat transfer even further.
Emerging cooling media, such as phase change materials or liquid metals, are also making waves in this domain. These materials offer superior thermal properties that enhance cooling efficiency beyond traditional methods.
By integrating innovative cooling techniques4 with precision-engineered built-in channels, manufacturers can achieve unprecedented levels of efficiency in their production processes.
Built-in cooling channels reduce cycle times.True
They facilitate rapid heat transfer, speeding up the molding process.
Traditional channels outperform special-shaped ones in efficiency.False
Special-shaped channels match the mold's geometry, enhancing cooling.
What Role Does Intelligent Cooling Control Play in Injection Molding?
In the intricate process of injection molding, maintaining optimal cooling is crucial for achieving high-quality products efficiently. But how does intelligent cooling control fit into this equation?
Intelligent cooling control in injection molding optimizes temperature management, ensuring consistent part quality and reducing cycle times through real-time adjustments.
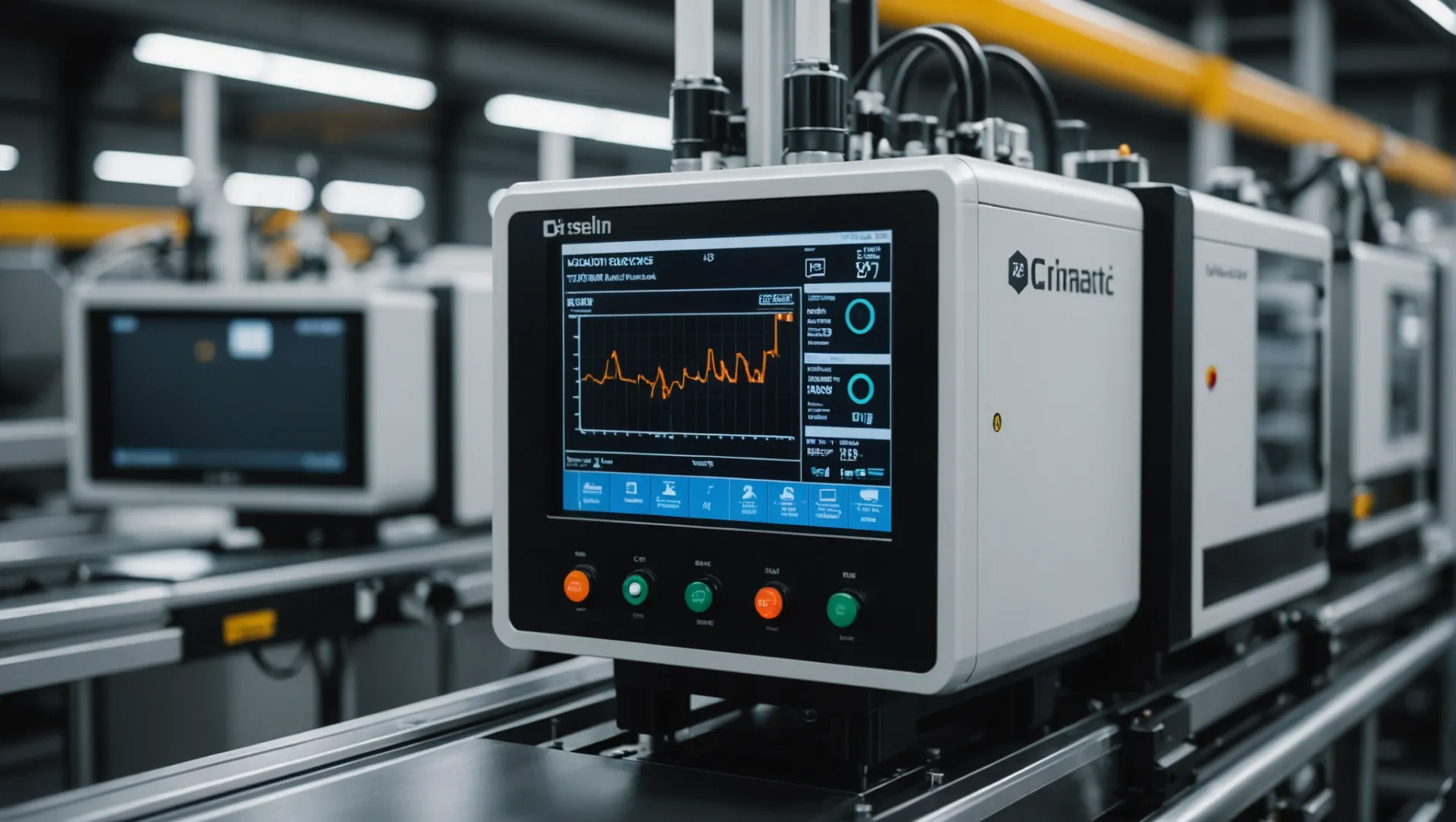
The Importance of Temperature Monitoring
Intelligent cooling control systems are equipped with advanced temperature sensors placed at strategic points in both molds and injection molded parts. These sensors provide real-time data on temperature variations, allowing for precise adjustments to be made during the cooling process.
For instance, when the sensors detect a hotspot within a mold, the system can automatically alter the flow or temperature of the coolant to address this issue promptly. This proactive approach helps maintain uniform cooling, minimizing defects like warping or residual stress in the final product.
Precision in Cooling Time Management
Another critical aspect of intelligent cooling systems is their ability to manage cooling times with precision. By pre-setting the cooling duration based on factors like material type and part geometry, these systems ensure that each part undergoes adequate cooling before demolding.
For example, a polymer part with intricate details may require longer cooling to maintain structural integrity. By controlling the cooling time accurately, intelligent systems prevent premature ejection, which can lead to defects.
Optimizing Cooling Medium Parameters
Intelligent systems also allow for the optimization of cooling medium parameters such as flow rate, temperature, and pressure. These adjustments are made based on real-time feedback from temperature sensors, ensuring that each parameter is set to achieve optimal cooling conditions.
Table: Comparison of Cooling Medium Parameters
Parameter | Traditional Control | Intelligent Control |
---|---|---|
Flow Rate | Manually set | Automatically adjusted |
Temperature | Fixed | Dynamic changes |
Pressure | Constant | Variable based on need |
Benefits of Intelligent Cooling in Injection Molding
By implementing intelligent cooling control, manufacturers can achieve several key benefits:
- Improved Product Quality: Consistent and uniform cooling results in fewer defects and higher quality parts.
- Reduced Cycle Times: By optimizing each aspect of the cooling process, cycle times are significantly shortened.
- Cost Efficiency: Reduced waste and faster production lead to lower operational costs.
Incorporating intelligent control systems5 in injection molding not only enhances efficiency but also ensures that products meet stringent quality standards consistently. For industries aiming to remain competitive, understanding and leveraging these systems is crucial.
Intelligent cooling control reduces cycle times.True
By optimizing cooling parameters, cycle times are shortened significantly.
Traditional control systems automatically adjust flow rates.False
Traditional systems require manual setting of flow rates, unlike intelligent ones.
Can Advanced Cooling Media Revolutionize Injection Molding Processes?
In the fast-paced realm of injection molding, advanced cooling media are emerging as game-changers, promising to revolutionize production efficiency and product quality.
Advanced cooling media revolutionize injection molding by enhancing thermal management, reducing cycle times, and improving part precision. By integrating innovative materials like phase change substances and liquid metals, these media provide superior cooling performance, transforming traditional processes.
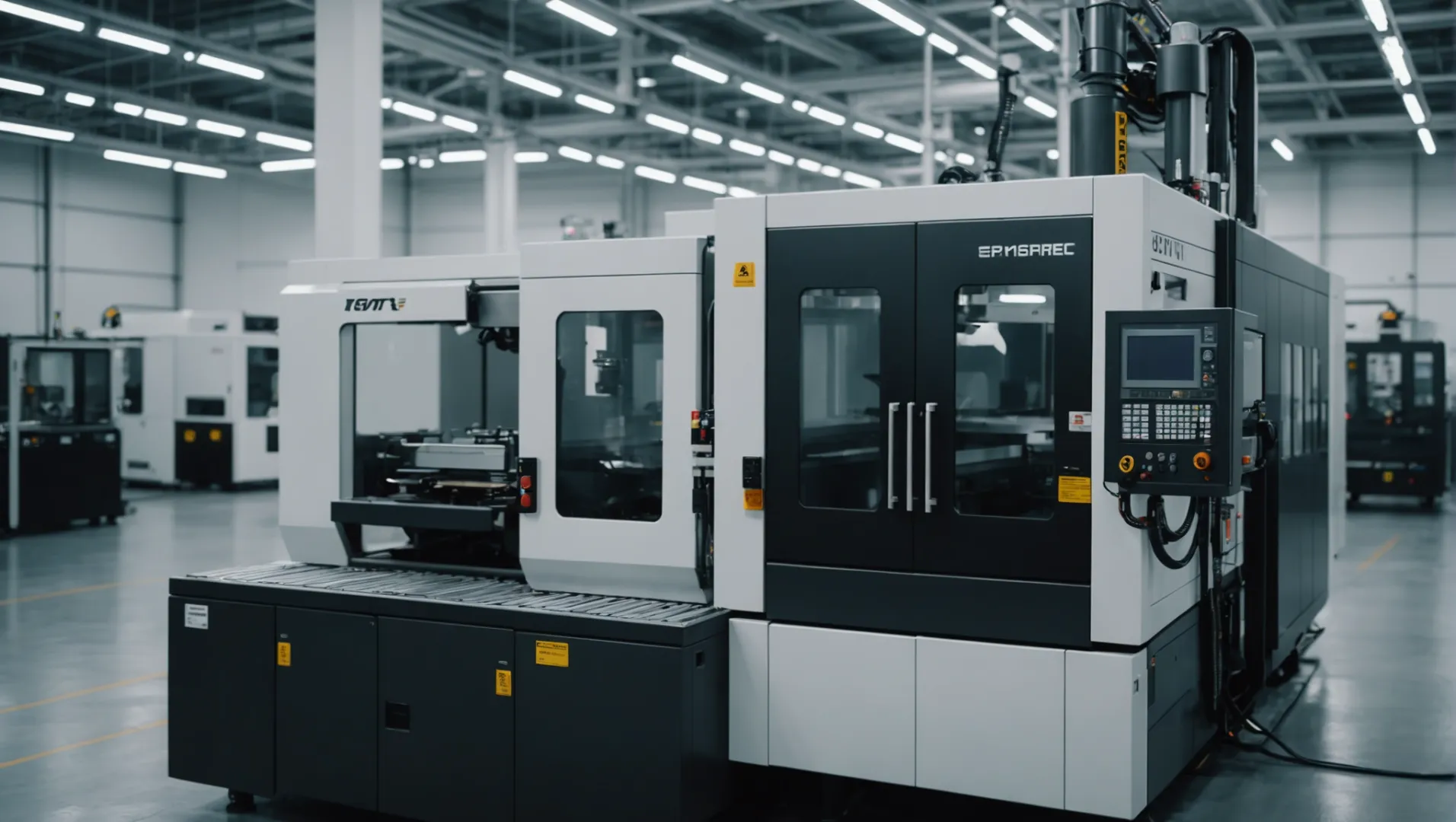
The Role of Advanced Cooling Media
The introduction of advanced cooling media in injection molding marks a significant leap in manufacturing technology. Traditional cooling methods predominantly relied on water and basic coolants, but recent innovations have brought in materials with superior thermal properties. Phase change materials6 and liquid metals are at the forefront of this transformation.
Phase Change Materials (PCMs): These materials are known for their ability to absorb or release substantial amounts of heat during phase transitions. This property is leveraged in injection molding to swiftly reduce mold temperatures, thereby decreasing cooling times without compromising on part quality. PCMs are particularly effective in applications where uniform temperature distribution is crucial, as they can prevent hot spots and ensure even cooling.
Liquid Metals: Known for their exceptional thermal conductivity, liquid metals facilitate rapid heat transfer from the mold surface. This capability significantly accelerates the cooling process, which is beneficial in high-speed or thin-wall injection molding scenarios. However, the use of liquid metals requires careful handling and specialized equipment to manage safety and compatibility concerns.
Innovative Applications in Mold Cooling
Advanced cooling media are not just about new materials but also about innovative applications that maximize their benefits.
-
Custom Cooling Channels: By designing channels that conform to the mold’s geometry, manufacturers can ensure that the cooling medium flows optimally through the mold. This tailored approach allows for more efficient heat removal compared to traditional straight channels.
-
Integration with Intelligent Systems: Incorporating temperature sensors and automated controls enhances the effectiveness of advanced cooling media. These systems can dynamically adjust flow rates and temperatures, ensuring optimal conditions throughout the cooling phase. For instance, a smart system might increase liquid metal flow in areas detected as overheating by embedded sensors.
Benefits Over Traditional Cooling Methods
The shift to advanced cooling media offers several advantages:
-
Reduced Cycle Times: Faster cooling directly translates into shorter cycle times, increasing throughput without additional machinery.
-
Improved Part Quality: Consistent and rapid cooling reduces defects such as warping or dimensional deviations, leading to higher-quality end products.
-
Energy Efficiency: More effective cooling can lower energy consumption as molds spend less time at elevated temperatures, reducing the need for prolonged heating or cooling phases.
The integration of advanced cooling media into injection molding is not without challenges, such as initial setup costs and the need for technical expertise. However, the potential benefits in terms of efficiency and product quality make it a promising direction for future innovations in manufacturing.
Phase change materials reduce mold cooling times.True
PCMs absorb or release heat during phase transitions, speeding up cooling.
Liquid metals are safe and easy to handle in molding.False
Liquid metals require careful handling due to safety and compatibility issues.
Conclusion
Embracing rapid cooling technology not only leads to faster production cycles but also ensures higher-quality products. By leveraging these advancements, manufacturers can position themselves at the forefront of innovation and efficiency.
-
Discover how built-in channels enhance efficiency and part quality.: The lattice structure not only enhances the overall structural integrity of the molds but also facilitates efficient heat dissipation during the … ↩
-
Learn how uniform cooling reduces defects and enhances precision.: A developed rapid cooling system for injection molds reduces cooling time by 29.2%. · The direct spraying of liquefied CO2 into the mold reduced the temperature … ↩
-
Explore innovative cooling media that boost efficiency and sustainability.: The new design increased the surface area of the cooling lines and helped maintain a cooler mold temperature which allowed the cycle time to be reduced. The … ↩
-
Explore cutting-edge methods to enhance mold cooling efficiency.: A developed rapid cooling system for injection molds reduces cooling time by 29.2%. •. The direct spraying of liquefied CO2 into the mold … ↩
-
Explore how intelligent systems optimize injection molding processes.: The closed-loop control system, composed of the ARM controller and sensors, realizes the prompt adjustment of the processing parameters, such as flow, injection … ↩
-
Explore how PCMs enhance thermal management in molding processes.: Phase change material products replace grease as the interface between power devices and heat sinks to provide effective thermal performance in components. ↩