Overmolding has transformed manufacturing. This process increases strength and adds elegance. Understanding quality control truly changes outcomes. Quality control is important. It really matters.
Successful overmolding depends on several important aspects. Material must be compatible. Surfaces need preparation. Dimensional stability is necessary. Bonding should be uniform. Overall performance should stay consistent. These elements are important for getting the best results. They really help maintain product quality during manufacturing.
I remember my first time with overmolding. It was exciting but also nerve-wracking. I learned that material compatibility is very important. If materials do not match, problems like discoloration or cracking may happen. I also value the importance of surface preparation. A clean surface is like a fresh canvas. It is ready for the masterpiece. Dimensional stability is also important. Nothing feels worse than seeing a product bend during production. Each factor is crucial for delivering consistent quality. We all strive for this in our designs.
Overmolding enhances product durability and aesthetics.True
Overmolding is known to improve both the strength and visual appeal of products, making it a valuable manufacturing technique.
Material compatibility is irrelevant in overmolding quality control.False
Material compatibility is crucial for successful overmolding, affecting bonding and performance. Ignoring it can lead to product failure.

- 1. What is Overmolding and Why is Quality Control Important?
- 2. How Can I Ensure Material Compatibility in Overmolding Processes?
- 3. How Can Surface Treatments Boost Bonding in Overmolding?
- 4. How Important is Dimensional Stability for Quality in Overmolding?
- 5. How Can You Maintain Functional Performance Consistency in Overmolded Products?
- 6. Conclusion
What is Overmolding and Why is Quality Control Important?
Have you ever held a product that felt perfect in your hand? That experience often comes from a process called overmolding. Overmolding involves carefully layering materials on a base object. This technique requires skill and precision. Quality is very important in this process. High-quality overmolding means the product feels just right and lasts longer. Getting it right truly matters.
Overmolding involves placing a second layer of material over a base layer. This new layer really helps to improve strength and appearance. Quality control checks are very important. These checks confirm that materials stick together well and work correctly together. They also examine the product’s overall performance.
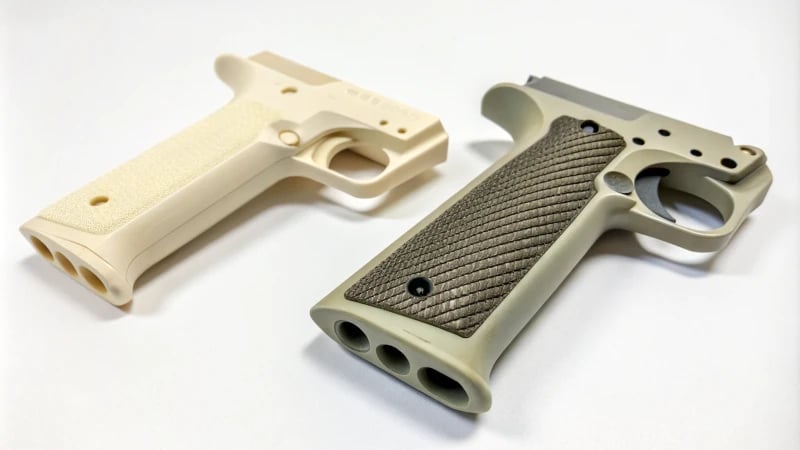
Understanding Overmolding
Overmolding is an interesting manufacturing method. It turns a basic plastic piece into a high-quality item. A second layer of material is placed over an existing one. This process creates a product that lasts longer and feels better to use.
Think of a smartphone case. The hard plastic shell protects the phone. However, the soft rubber overmold makes it comfortable to hold. It also stops it from slipping. Simple ideas like this improve user satisfaction.
Why Quality Control Matters
Quality control is very important in overmolding. Keeping high standards is crucial. This guarantees the final product looks good and works well. Poor quality control can lead to defects that include bubbles and wrinkles which ruin performance and appearance.
Key Quality Control Considerations for Overmolding
Here are some important points I focus on for smooth operations:
Quality Control Aspect | Description |
---|---|
Material Compatibility | Material compatibility is very important. On a project with special additives, I learned that some materials don’t mix well, causing cracks or bad discoloration. Testing helps avoid these problems. |
Surface Preparation | For overmolding, cleaning the substrate surface is crucial. We used chemical and mechanical methods for the best adhesion. |
Dimensional Stability | Shape and size must stay consistent during overmolding; pre-treatment methods like heat treatment are essential in my process. |
Material Compatibility
Material compatibility is vital for preventing adverse reactions that could diminish performance. For instance, if the chemical properties of the two materials are incompatible, issues such as cracking or discoloration may arise. Conducting thorough testing on material interactions1 can help avoid these problems.
Surface Preparation
The surface of the substrate material must be meticulously cleaned and potentially treated to enhance adhesion. Techniques such as chemical activation or mechanical grinding can be employed. Consider this example: when overmolding a rubber grip onto a hard plastic tool handle, the handle’s surface must be free of oils and dirt to ensure a firm bond. A guide on surface treatments2 can provide further insights.
Dimensional Stability
Maintaining the shape and size of the substrate during the overmolding process is critical. Any deformation could lead to misalignment and affect the quality of the final product.
The Impact of Quality Control on Functionality
Quality control ensures the product functions properly; it’s not just about looks.
I recall needing to improve a product’s waterproof features after production testing confirmed improvements worked, ensuring customer satisfaction without unexpected issues.
Overmolding improves the durability of plastic components.True
The overmolding process enhances product durability by applying a second material layer, creating a stronger bond and better resistance to wear and tear.
Quality control is unnecessary in the overmolding process.False
Quality control is essential in overmolding to ensure product integrity and prevent defects that could compromise functionality and aesthetics.
How Can I Ensure Material Compatibility in Overmolding Processes?
Perfecting materials is crucial for overmolding to create high-quality products. I often share methods to handle this complex process. These approaches lead to seamless results.
Focus on both chemical and physical compatibility in overmolding processes. Implement strict quality control measures. Use effective bonding methods during production.
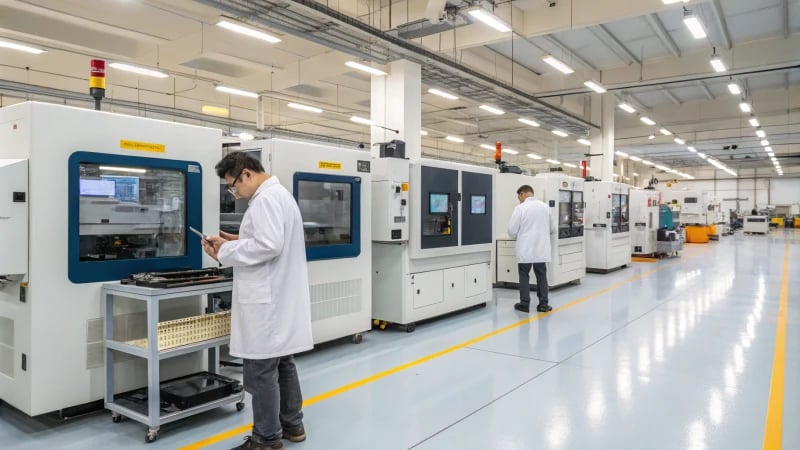
Understanding Material Compatibility
Material compatibility in overmolding is not just a technical issue – it forms the base of creating products that perform very well and last long. I remember my first overmolding project clearly. I felt nervous about whether my material choices would hold up. It was important to understand both chemical and physical compatibility to prevent problems like delamination or cracking. Trust me, nothing is more disappointing than watching a product fail because of a simple mistake in picking materials.
When selecting materials for overmolding, consider the following:
-
Chemical Compatibility: This aspect is crucial! I always double-check that the materials in both the first and second injection molding don’t react badly. For instance, I once worked with a plastic with special additives. It turned out that they didn’t mix well with another material I picked. The outcome? A poor product that didn’t meet expectations.
-
Physical Compatibility: Matching physical properties such as thermal expansion is key. If they shrink differently during cooling, serious issues may arise. I remember combining a hard and soft material for a project. I carefully analyzed their thermal properties. This taught me how critical these details can be!
Quality Control Considerations
Implementing strict quality control measures during the overmolding process is a must:
- Surface Treatment: Treating the surface of the first molded part is crucial for strong adhesion. Techniques like chemical etching or mechanical grinding really improve bonding strength.
- Injection Parameters: Careful control of temperature and pressure during the second injection molding is important for good bonding. High temperatures cause bubbling, while low temperatures weaken bonds. Finding that balance is like an art!
Parameter | Importance | Example |
---|---|---|
Temperature | Affects material flow and bonding quality | High temperatures may cause softening and bubble formation; low temperatures might lead to weak bonds. |
Pressure | Ensures uniform distribution of the overmolding material around the substrate | Insufficient pressure can leave voids and lead to poor adhesion. |
Holding Time | Determines the duration for which pressure is maintained during cooling to allow proper bonding | An optimal holding time helps mitigate shrinkage issues and ensures dimensional stability. |
Bonding Techniques
Effective material bonding is very important:
- Edge Treatment: Proper edge treatment can make or break a project. Covering the substrate edges completely with the laminating material prevents peeling or warping. Techniques like heat sealing work well here.
- Fitting Uniformity: Consistency across surfaces is key to avoiding defects like wrinkles or bubbles. Through experience, I have learned that controlling temperature and pressure during overmolding is vital for this.
To gain deeper insights into enhancing bond strength, you can explore advanced bonding techniques3 that offer innovative solutions.
Testing and Validation
After overmolding, I always do thorough testing to ensure our product performs its best:
- Functional Testing: This step checks if metrics like waterproofing or impact resistance meet expectations after overmolding.
- Visual Inspection: I ensure that appearance, including color and texture, is uniform to meet aesthetic standards.
For more guidance on testing methodologies, check out testing standards for overmolding .
My journey through product design taught me valuable lessons about material compatibility and quality control in overmolding. By sharing these insights, I hope to help others avoid the same pitfalls and achieve great results in their designs.
Chemical compatibility is vital in overmolding processes.True
Chemical compatibility prevents adverse reactions between materials, ensuring product performance and durability.
Surface treatment enhances adhesion in overmolding.True
Improving surface profiles through treatment techniques increases bonding strength between materials during the overmolding process.
How Can Surface Treatments Boost Bonding in Overmolding?
Ever wondered how simple plastic products become so strong? The secret lies in surface treatments. These treatments are crucial in the bonding process of overmolding. They help products last longer and become stronger. This really is the key to durability!
For better bonding in overmolding, surface treatment methods like chemical etching, mechanical grinding and thorough cleaning are useful. These techniques prepare materials for excellent adhesion with overmolding substances. This results in stronger and more lasting products. Products become stronger and more durable.
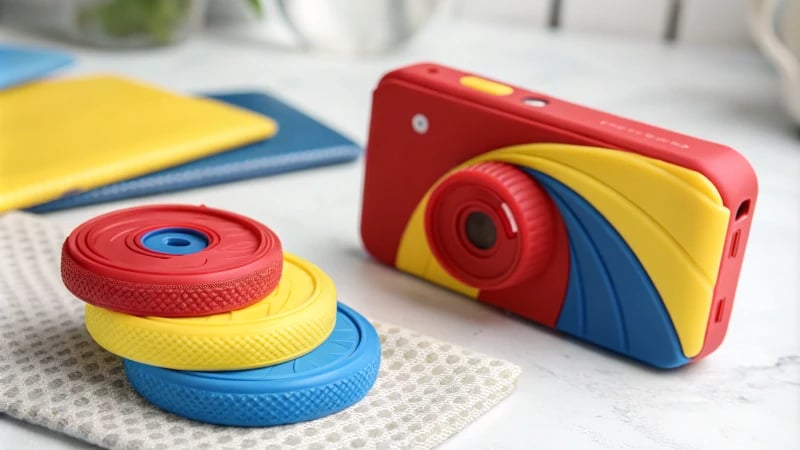
Understanding Surface Treatments for Overmolding
Surface treatments play a crucial role in enhancing the bonding between materials in the overmolding process. These treatments prepare the surface of the substrate to ensure a stronger adhesion with the overmolding material, ultimately improving the product’s durability and performance.
Key Surface Treatment Techniques
-
Chemical Etching: This method transformed my work. Chemical solutions roughen surfaces, creating more area for a solid mechanical grip. Think of it as a great handshake ensuring a strong link! Curious minds can explore benefits of chemical etching4 for more details.
-
Mechanical Grinding: My first grinding session felt like real exercise! This physical process greatly improves stickiness, especially for hard surfaces where chemicals fail. However, too much strength can harm the material. It truly felt like mastering an art! Learn more about mechanical grinding techniques5.
-
Surface Cleaning and Pretreatment: Clean surfaces are crucial before applying any overmolding material. They need to be spotless and free of dust and oils. I often use:
- Solvent cleaning
- Plasma treatment
- Sandblasting
These methods ensure that the adhesive properties of the surfaces are maximized. Explore detailed cleaning methods here6.
Compatibility Considerations
When considering surface treatments, it’s important to ensure material compatibility:
Property | Description |
---|---|
Chemical Compatibility | Ensure no adverse chemical reactions occur between materials. |
Physical Compatibility | Match thermal expansion coefficients to avoid shrinkage issues during cooling. |
Bond Strength Enhancements
To enhance bond strength further, specific treatments can be applied directly to the interface:
- Adhesive Application: Adding adhesive between surfaces dramatically strengthens bonds.
- Coating Treatments: Trying various coatings helped enhance adhesion and stop layers from peeling under pressure.
Injection Molding Process Parameters
Don’t overlook how injection molding settings affect bonding:
- Injection Temperature: High temperatures lead to better material mixing. Think of them melting together!
- Injection Pressure: Correct pressure enables the second material to fill gaps, resulting in a sturdy bond.
- Injection Speed: Altering speed reduces air pockets, preventing weak spots.
Understanding these treatments and their implementation can significantly impact the quality and performance of overmolded products. Find a full guide on best practices for overmolding7.
Every project brings a chance for creativity and precision. I hope sharing these insights really inspires you on your own path!
Chemical etching improves bond strength in overmolding.True
Chemical etching creates a rough surface, enhancing mechanical interlocking and bond strength between the substrate and overmolding material.
Surface cleaning is unnecessary for effective overmolding.False
Surface cleaning is crucial to remove contaminants, ensuring optimal adhesion and improving the overall quality of the overmolded product.
How Important is Dimensional Stability for Quality in Overmolding?
Some overmolded products look perfect, while others do not. Dimensional stability is the hidden champion in this process. It plays a key role in both the appearance and function of the final product. Let’s explore why this is so important!
Dimensional stability is very important for creating high-quality overmolded products. It helps substrate materials keep their shape during processing. This stability stops issues like misalignment and delamination. Designers probably improve product quality by choosing compatible materials. Precise processing conditions are really significant too.
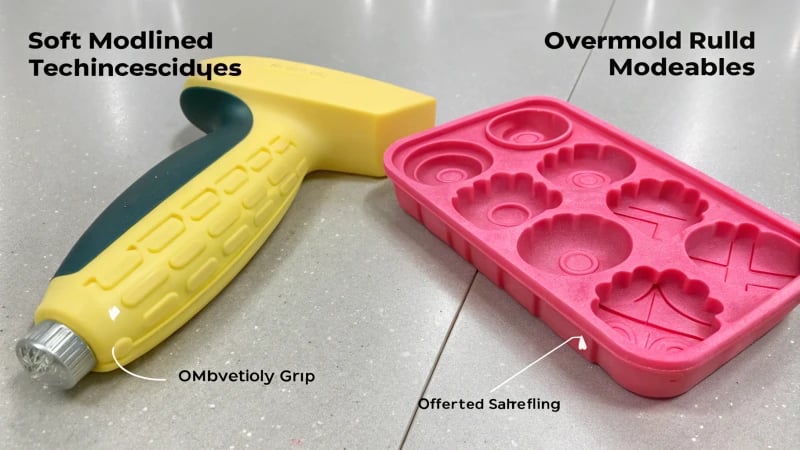
Understanding Dimensional Stability in Overmolding
Dimensional stability refers to the ability of a material to maintain its original shape and size under varying conditions, which is crucial during the overmolding process. When a substrate is molded, any deformation can lead to defects in the final product.
For example, if a substrate expands or contracts significantly during the heating phase of overmolding, it may not align properly with the overmolding material. This misalignment can lead to bonding issues or aesthetic defects, such as wrinkles or bubbles. Ensuring dimensional stability involves careful material selection and design considerations.
Key Factors Influencing Dimensional Stability
-
Material Selection
Choosing materials with similar thermal expansion coefficients is vital. Mismatched materials can behave differently when heated or cooled, leading to stresses that compromise stability. For instance, if a soft elastomer is overmolded onto a rigid plastic, the cooling rates may differ significantly, affecting the bond integrity. -
Processing Conditions
The temperature and pressure during the injection process can significantly affect dimensional stability. High temperatures may cause unwanted expansion, while low temperatures might not allow proper flow into the mold cavities. Adjusting these parameters helps maintain stability throughout the process. -
Mold Design and Accuracy
Accurate mold design is essential for achieving dimensional stability. Molds should be engineered to accommodate the expected shrinkage of both the substrate and overmolding materials. For example, if the mold does not account for the shrinkage of the overmolded material, it could result in a final product that does not meet size specifications.
Quality Control Measures for Dimensional Stability
Quality Control Aspect | Description |
---|---|
Material Compatibility | Ensuring that the selected materials are compatible in terms of physical and chemical properties. |
Shrinkage Compensation | Adjusting the design to consider different shrinkage rates of materials after molding. |
Mold Accuracy | Maintaining tight tolerances in mold design to ensure proper alignment and fit during the molding process. |
Interface Treatment | Proper treatment of surfaces to enhance bonding strength between materials can improve overall stability. |
By focusing on these quality control measures, designers can enhance the dimensional stability of their products during the overmolding process. This stability is not just about maintaining size; it plays a significant role in ensuring that the final product meets performance and aesthetic standards, ultimately leading to higher customer satisfaction.
Conclusion
Although we will refrain from concluding this section, it’s essential to recognize that maintaining dimensional stability throughout overmolding is critical for achieving quality outcomes. By considering these factors, designers can effectively mitigate risks associated with dimensional changes.
For further insights into optimizing overmolding processes and material selections, check out material compatibility considerations8 and quality control measures .
Dimensional stability prevents defects in overmolded products.True
Maintaining dimensional stability during overmolding is crucial to avoid misalignment and defects like bubbles or wrinkles, ensuring product quality.
Material selection does not affect overmolding quality.False
Choosing compatible materials is essential; mismatched thermal properties can lead to instability and defects in the final product during overmolding.
How Can You Maintain Functional Performance Consistency in Overmolded Products?
Ever thought about how to keep your overmolded products working well every time? As someone who understands manufacturing challenges, I know consistency is really important. Let’s explore some important strategies together!
To keep overmolded products working well, use materials that get along, adjust molding settings, check quality closely and test performance carefully. These actions are very important for keeping products reliable. Meeting customers’ needs is also crucial in manufacturing.
Understanding Material Compatibility
Material compatibility matters a lot. I once picked wrong materials and they failed. They need to blend both chemically and physically. Chemical harmony is key. For instance, a wrong additive in plastic may weaken the product or change its color. I learned this when a batch had an unexpected shade.
Physical compatibility is equally essential. Matching thermal expansion and shrinkage rates is necessary. If they don’t fit, products may warp or peel apart. Mixing hard and soft materials needs careful thought, especially with temperature changes.
Quality Control Measures
Quality control is a must in overmolding. I follow these key points to keep performance consistent:
Optimizing Injection Molding Parameters
Injection molding settings greatly affect how products turn out. I often tweak temperature, pressure and speed for perfect results. Here’s what I’ve learned:
Injection Temperature: Too high damages material; too low fails to bond.
Injection Pressure: Enough pressure ensures even spreading.
Injection Speed: Adjust to avoid defects.
Right parameters improve strength and quality significantly.
Functional Performance Testing
After overmolding, thorough testing is next. The product must meet performance goals. For example, waterproof designs need tough testing. Without it, failures occur.
Interface Treatment Techniques
Interface treatment is crucial for a solid bond. Techniques include꞉
- Roughening surfaces (like etching or grinding)
- Using adhesives if required
These methods lower the risk of peeling and increase durability.
Following these steps, I achieve consistent quality in overmolded items, pleasing customers. Attention to detail in every stage leads to excellent results. Let’s aim for greatness!
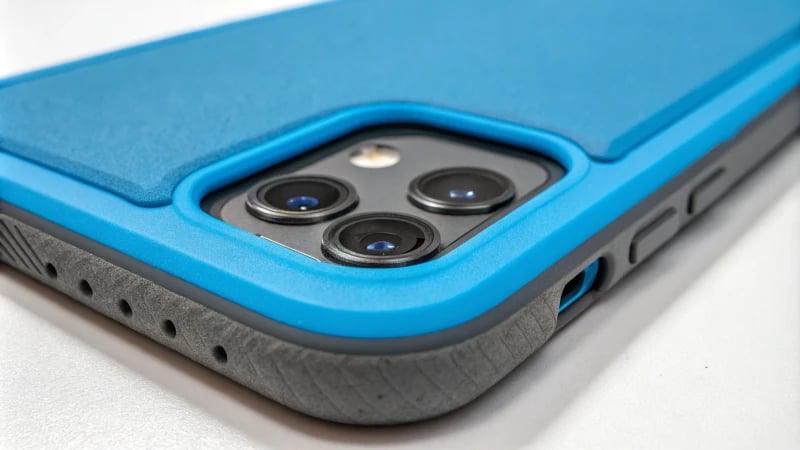
Maintaining Overmolded Product Performance
To keep overmolded products working well, focus on matching materials correctly. This begins with a deep understanding of material compatibility. When selecting materials for both the substrate and the overmolding layer, it’s crucial to ensure they are chemically and physically compatible. Chemical compatibility is vital to prevent adverse reactions that could lead to product failure, such as reduced strength or discoloration. For instance, specific plastic additives may react unfavorably with certain materials, impacting performance.
Physical compatibility is just as important. The thermal expansion coefficients and shrinkage rates of the two materials must be closely matched. If they differ significantly, the result may be deformation or delamination during cooling. For example, hard and soft materials need careful consideration to prevent mismatched deformation under varying temperatures. More about material compatibility considerations9 can provide insights into making effective material choices.
Quality Control Measures
Implementing stringent quality control measures is essential in the overmolding process to ensure consistent functional performance. Here are key quality control considerations:
Quality Control Aspect | Description |
---|---|
Surface Cleaning | Ensure surfaces are free from contaminants like oil and dust to enhance adhesion. |
Dimensional Stability | Maintain the shape and size of substrate materials throughout the overmolding process. |
Edge Treatment | Properly treat edges of laminating material to prevent warping or peeling. |
Appearance Quality | Control color uniformity and gloss to meet design specifications. |
Optimizing Injection Molding Parameters
Injection molding process parameters greatly influence the final product’s performance. Parameters such as injection temperature, pressure, and speed should be optimized to create a strong bond between materials. For example:
- Injection Temperature: Too high may degrade material properties; too low can prevent adequate fusion.
- Injection Pressure: Proper levels are needed to ensure even filling around the substrate.
- Injection Speed: Should be adjusted to avoid turbulence that can introduce defects.
Controlling these parameters effectively can improve bond strength and overall quality. Explore more on optimizing injection parameters10.
Functional Performance Testing
After overmolding, it is critical to conduct thorough functional performance testing. The overmolded product should meet or exceed performance expectations based on its intended application. For example, if the goal is to enhance waterproofing, rigorous testing must confirm that the product adheres to required standards.
Interface Treatment Techniques
Good interface treatment techniques ensure strong adhesion between the substrate and overmolding material. Considerations include:
- Surface roughening techniques (e.g., chemical etching or mechanical grinding)
- Application of adhesives where necessary
These practices can significantly reduce the risk of delamination, enhancing durability and reliability in end-use applications.
By adhering to these guidelines, manufacturers can maintain the functional performance consistency of their overmolded products, ensuring they meet quality standards and customer expectations. For further reading on interface treatment methods11, check here.
Material compatibility is crucial for overmolded product performance.True
Ensuring chemical and physical compatibility prevents failures like deformation or discoloration in overmolded products.
Quality control measures can enhance overmolded product consistency.True
Stringent quality control, including surface cleaning and dimensional stability, ensures consistent performance in overmolded products.
Conclusion
This article discusses essential quality control considerations for overmolding, emphasizing material compatibility, surface preparation, and dimensional stability to achieve high-quality products.
-
Discover comprehensive insights into overmolding processes and quality control practices to enhance your manufacturing knowledge. ↩
-
Learn more about effective surface preparation techniques crucial for successful overmolding applications. ↩
-
Discover key strategies to enhance material compatibility during overmolding processes and avoid common pitfalls. ↩
-
Discover advanced techniques and methods to optimize surface treatments for better adhesion in overmolding processes. ↩
-
Learn how mechanical grinding can improve bonding in your overmolding applications. ↩
-
Find out about effective surface cleaning methods that improve bonding in overmolding. ↩
-
Get insights on how injection molding parameters affect bonding strength. ↩
-
Explore how maintaining shape during overmolding affects product performance and quality. ↩
-
Learn more about material compatibility considerations to enhance your design processes. ↩
-
Explore effective strategies for optimizing injection molding parameters in your production line. ↩
-
Discover advanced interface treatment techniques for improving adhesion in overmolded products. ↩