I’ve often found myself navigating the complex world of injection molding, where supplier quality can make or break a project.
Ensure consistent quality in injection molding by conducting thorough supplier evaluations, establishing clear contracts, maintaining vigilant production oversight, and implementing continuous quality improvement measures. These steps are essential for maintaining manufacturing integrity.
When I first started managing supplier relationships, it felt like juggling flaming torches—there was so much at stake! But over time, I learned the importance of diving deeper into each phase of the process. From evaluating suppliers’ qualifications and equipment to conducting sample tests, I discovered that every detail matters. Setting clear quality standards in contracts and maintaining a watchful eye during production also became second nature to me.
I remember one instance where our supplier’s advanced equipment made all the difference. Their ability to precisely control injection parameters ensured we met our stringent quality standards without a hitch. Regular audits and data analysis became my allies, revealing patterns and preventing potential pitfalls. By fostering open communication and feedback loops with suppliers, I found that continuous improvement wasn’t just a goal; it was an evolving journey that elevated our production quality. With these strategies, not only did we enhance our products, but we also built stronger, more trustworthy supplier relationships.
Thorough supplier evaluation ensures consistent quality in injection molding.True
Evaluating suppliers thoroughly helps maintain high quality standards.
Contract agreements are optional for ensuring supplier quality consistency.False
Contracts define expectations and responsibilities, ensuring quality consistency.

What Are the Key Stages in Supplier Evaluation?
Ever felt overwhelmed by the intricacies of choosing the right supplier? Let me walk you through the process, sharing some personal insights from my own experiences along the way.
Supplier evaluation involves qualification review, equipment inspection, sample testing, contract signing, production supervision, and continuous improvement. These steps ensure suppliers meet high standards, enhancing product quality and reliability.
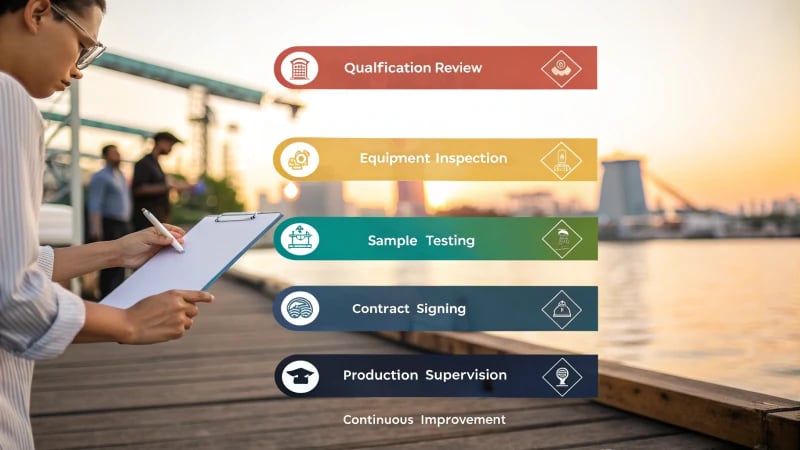
Stage 1: Qualification Review
Let me tell you, the first time I had to conduct a supplier qualification review1, it felt like I was back in college cramming for finals. It’s all about diving deep into their credentials. You look at things like business and production licenses—kind of like checking their report card to make sure they’re legit. And trust me, spotting an ISO 9001 certification is like finding gold; it’s a clear sign that they take quality management seriously.
But that’s not all. Ever had that moment where you read online reviews before trying a new restaurant? Evaluating a supplier’s reputation is just like that. You get to dig into customer reviews and see what the industry thinks about them. It’s fascinating to see how their past performance in injection molding quality stacks up.
Stage 2: Equipment and Process Inspection
I remember stepping into a supplier’s facility for the first time; it was like being in a sci-fi movie with all those machines humming around me. The next step is to check out their equipment up close. You want to see if their machines are up-to-date and well-maintained because that’s a big factor in ensuring quality.
Equipment Check | Details |
---|---|
Brand & Model | Current technology used |
Maintenance | Regular updates and calibrations |
I even jot down notes about the brand and model of their equipment, kind of like noting down the make and model of a car before buying it. Their production process needs to be as polished as a new car too, with standards covering every aspect from mold manufacturing to post-processing.
Stage 3: Sample Testing and Evaluation
Ah, sample testing—the moment of truth. It’s like trying out a new recipe; you need to ensure everything measures up. When I first tested samples, it was all about making sure dimensions were spot on and materials were strong enough for real-world use.
Stage 4: Contract and Agreement Signing
Signing the contract feels like sealing the deal on a new apartment. Every detail has to be clear—from quality standards to responsibilities if things go awry. Think of it as setting expectations so there are no surprises later on.
Stage 5: Production Process Supervision
For critical projects, I’ve found that having someone supervise the production process on-site is invaluable. It’s like having a coach on the sidelines, ready to catch and correct any missteps immediately.
Regular audits are like health check-ups for the supplier’s quality management system. They ensure everything is running smoothly and any issues are nipped in the bud.
Stage 6: Continuous Improvement Phase
This phase reminds me of those fitness trackers that constantly give feedback to help you improve. By collecting quality data and analyzing trends, we can work with suppliers to iron out issues—like mold wear—that might be affecting product quality.
Following these stages not only helps in building stronger partnerships with suppliers but also ensures our products maintain high standards. It’s a meticulous process, yet incredibly rewarding when done right. Learn more2 about optimizing supplier evaluations to enhance your business outcomes.
ISO 9001 certification is mandatory for supplier qualification.True
ISO 9001 ensures commitment to quality management, crucial for qualification.
Sample testing is optional in supplier evaluation stages.False
Sample testing is essential to verify product dimensions and material strength.
How Do You Define Quality Standards in Contracts?
Ever wondered how to ensure everyone’s on the same page in a contract?
Quality standards in contracts involve clear detailing of product specifications, performance indicators, acceptance methods, and supplier responsibilities, ensuring accountability and mutual understanding among all parties.
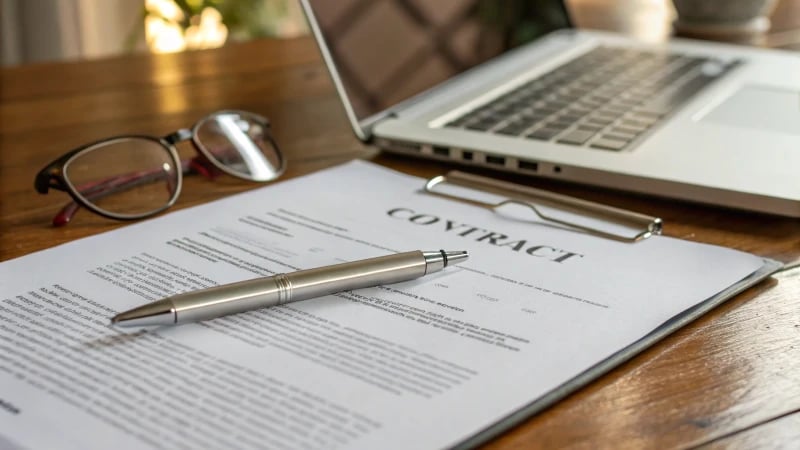
Supplier Evaluation and Selection Stage
Let me take you back to the time I was neck-deep in evaluating suppliers for a major project. It was like sifting through endless CVs in a job interview process, but instead of people, it was machines and processes. The starting point was always the qualification review. I’d meticulously check if the supplier had their legal ducks in a row—like a business license or ISO 9001 certification. These aren’t just paper qualifications; they’re the bedrock of quality control capabilities3.
Next up was the equipment and process inspection. This part was a bit like checking under the hood of a car I was considering buying. I’d dig into the brand, model, and even the age of their machinery. I once had a supplier with equipment so old, it was like they were using a flip phone in a smartphone world! Modern machines can really make or break the quality.
Then came sample testing and evaluation. This was where I felt like a scientist in a lab coat, testing samples to ensure everything from dimensional accuracy to material strength was spot on. It wasn’t just about catching defects but ensuring the supplier could consistently deliver quality.
Contract and Agreement Signing Stage
Once I had my shortlist of suppliers, it was time to put pen to paper—or rather, fingers to keyboard. Defining quality standards in the contract was crucial. I’d specify every minute detail, like size tolerances or visual defect standards.
Quality Clause | Details |
---|---|
Specifications | ±0.1mm tolerance |
Acceptance Method | GB/T 2828.1-2012 |
I’d also make sure quality responsibility clauses were crystal clear. What happens if the quality doesn’t meet expectations? These clauses were my safety net, ensuring there were plans for compensation or replacement if things went south.
Production Process Supervision Stage
For those high-stakes projects, factory supervision became my go-to strategy. Imagine having a trusted pair of eyes right on the production floor, ensuring every raw material and process adhered to our agreed standards.
Regular audits became part of my routine, much like a health check-up. I’d schedule these inspections to keep the supplier on their toes, ensuring they consistently followed our quality management systems. Random product inspections were my surprise pop quizzes for them!
Continuous Improvement Phase
Finally, I couldn’t stress enough about establishing a system for data collection and analysis. Gathering data from inspection reports and customer feedback became my compass, guiding me through patterns and potential improvements.
Prompt feedback4 to suppliers was key. I’d encourage them to devise improvement measures—kind of like giving them constructive feedback after every project phase. This ongoing dialogue ensured continuous improvement and kept us all aiming for higher quality standards.
Example:
I remember a time when a supplier’s product started showing dimensional discrepancies—it was like they forgot to check their ruler! Analyzing the data revealed mold wear issues. This led to corrective actions that drastically improved our outcomes over time. It’s stories like these that underline why defining quality standards in contracts isn’t just paperwork; it’s peace of mind.
ISO 9001 certification is mandatory for all suppliers.False
ISO 9001 is a widely recognized standard but not mandatory for all suppliers.
Contracts should specify product size tolerance.True
Specifying size tolerance in contracts ensures clear quality expectations.
When Should You Implement Factory Supervision?
Ever wondered when to bring factory supervision into your production process?
Implement factory supervision during supplier evaluation, contract negotiation, production monitoring, and continuous improvement phases to ensure quality control, mitigate risks, and enhance operational efficiency.
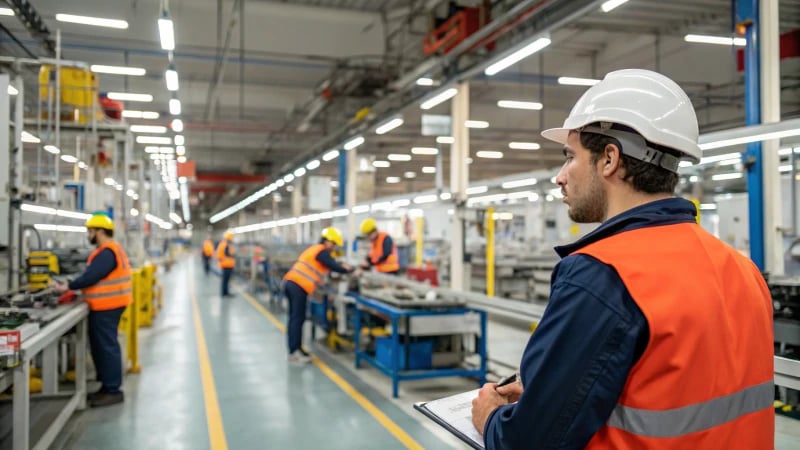
Supplier Evaluation and Selection
I remember when I first had to choose a supplier for a project with high quality demands. It felt like a monumental task, sifting through endless options. That’s when I learned the importance of factory supervision right from the supplier evaluation5 stage. Ensuring potential suppliers have the necessary qualifications, like a valid business license and production license, is non-negotiable. On one occasion, an on-site visit revealed outdated equipment that could have jeopardized our product quality.
Contract and Agreement Signing
Getting into contract signing without clear quality clauses is like jumping into a pool without checking the water’s depth. I’ve been there, and let me tell you, it’s not pleasant. Factory supervision at this stage helps establish explicit product specifications and performance indicators. It’s about nailing down every detail—like size tolerances—so there are no surprises later on.
Contract Element | Details |
---|---|
Quality Standards | Product specs, performance, appearance requirements |
Acceptance Methods | Inspection items, sampling methods, inspection standards |
Quality Responsibilities | Free replacement, repair, compensation measures |
Production Process Supervision
For high-stakes projects, having someone on the ground to oversee production is invaluable. I once had a factory rep who was an absolute lifesaver during a critical injection molding project. Their keen eye caught potential discrepancies in process parameters before they became issues. Regular audits and inspections are essential to keep everyone accountable.
Continuous Improvement Phase
Data collection and analysis might sound tedious, but it’s the secret sauce to continuous improvement. Implementing a system to track quality data helped me pinpoint where things were slipping through the cracks. This kind of insight allowed us to provide constructive feedback to suppliers, ultimately lifting our product standards.
For those seeking more in-depth advice on refining their factory supervision strategies, resources on production audits6 and quality management systems7 are excellent places to start. They offer robust methodologies for ensuring ongoing quality assurance and improvements.
Factory supervision is crucial during supplier evaluation.True
Supervision ensures suppliers meet qualifications and quality standards.
Contract signing doesn't require factory supervision.False
Supervision helps establish clear quality clauses and responsibilities.
How Do Regular Audits Enhance Quality Assurance?
Ever wonder how some companies always seem to nail product quality? Regular audits might be their secret weapon.
Regular audits enhance quality assurance by identifying inconsistencies and ensuring standards are met, thereby driving continuous improvements and maintaining high-quality products and processes.
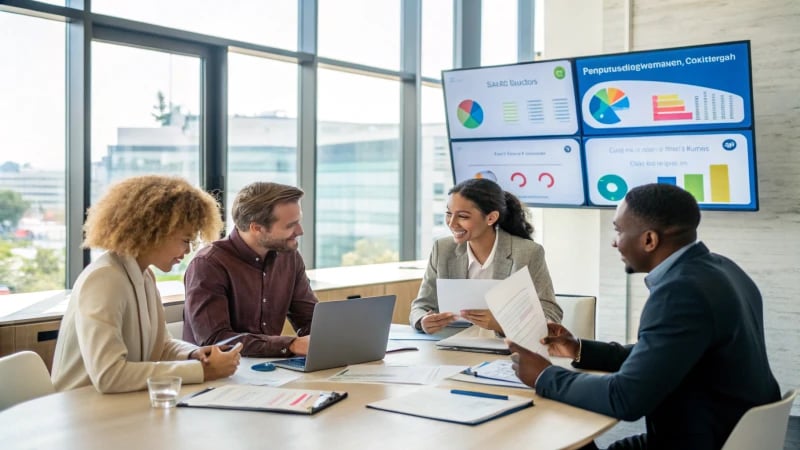
Supplier Evaluation and Selection
When I first started working with new suppliers, it felt a bit like dating. You want to know who you’re dealing with and ensure they tick all the right boxes before committing. Regular audits play a crucial role here. They’re like that wise friend who helps you vet potential matches by checking qualifications—like a supplier’s business and production licenses. But it doesn’t stop there. I also look into whether they have ISO 9001 certification, which is like a badge of honor in quality management.
-
Qualification Review
Criteria Importance Business License Legal authorization for operation Production License Specific to injection molding practices -
Equipment and Process Inspection
On-site inspections are a game-changer. I remember visiting a supplier once, armed with a checklist. It wasn’t just about ticking boxes but understanding their equipment and processes. Regular audits involve checking for advancements and maintenance status of production equipment, revealing if equipment calibration is up-to-date—crucial for consistent product quality8.
-
Sample Testing and Evaluation
Testing samples against quality standards is non-negotiable. It’s like taking a car for a test drive before buying it—crucial to ensure everything’s up to scratch.
Contract and Agreement Signing
Signing contracts can feel daunting, but audits help ensure all quality clauses are crystal clear. They remind me of those moments when you read the fine print on an agreement, ensuring everything from product specs to acceptance methods is detailed to avoid future hiccups.
-
Quality Clauses
Regular audits verify compliance with contract stipulations like product size tolerances and appearance requirements, keeping everything in line with what we agreed on paper.
Production Process Supervision
Once production kicks off, regular audits become my eyes and ears on the ground. It’s like having a trusty co-pilot who keeps everything on course.
-
Factory Supervision
For key products, audits allow real-time monitoring9 of production processes. This oversight is essential for maintaining top-notch quality.
-
Regular Audits and Inspections
Random inspections are the wildcards in my quality assurance toolkit. They keep suppliers on their toes, ensuring standards are upheld consistently.
Continuous Improvement Phase
In my journey towards continuous improvement, audits are invaluable. They’re not just about pointing out what’s wrong but about fostering a culture of ongoing enhancement.
-
Data Collection and Analysis
By collecting quality data and analyzing it, I can pinpoint major issues over time through statistical analysis and address them head-on.
-
Feedback and Improvement Measures
It’s all about collaboration. By sharing audit findings with suppliers within the quality management10 framework, we can work together to boost product quality, ensuring that improvement is a constant goal.
Regular audits aren’t just about ticking boxes—they’re about creating a reliable feedback loop that propels quality assurance forward. By embedding them into each stage of production—from supplier evaluation to continuous improvement—I can safeguard our reputation for excellence and drive innovation, ensuring we stay at the forefront of our industry.
Regular audits ensure ISO 9001 compliance in suppliers.True
Audits verify that suppliers meet ISO 9001 standards, ensuring quality control.
Audits are not essential for continuous improvement.False
Audits collect data crucial for identifying quality issues, aiding improvement.
How Can Continuous Improvement Drive Supplier Quality?
Ever wondered how continuous improvement can turn supplier headaches into smooth sailing partnerships? Let’s dive into the magic behind this strategic approach.
Continuous improvement in supplier quality involves regular performance assessments, corrective actions, and open communication, resulting in enhanced product quality, cost reduction, and stronger supplier relationships.
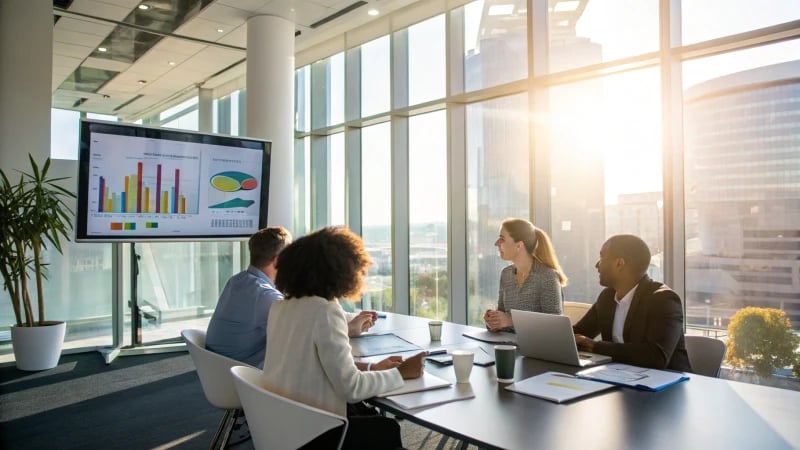
Supplier Evaluation and Selection
Reflecting on my early days in mold design, I remember how crucial a rigorous supplier evaluation11 was. Back then, we’d start with a deep dive into a supplier’s qualifications, much like checking if they had the right credentials, including their business license and ISO 9001 certification. I once spent a day at a factory, walking through aisles of advanced machinery, each hum telling a story of precision and maintenance. It was like being in a technological library where each piece of equipment had its own tale.
Inspecting processes was another layer of assurance. One visit involved poring over process documents with the supplier’s team. We checked for standard adherence and often ended up learning more about how they approached mold manufacturing—a process that felt as complex as crafting a fine watch.
Sample testing provided the hands-on experience I loved. Holding a product, measuring its dimensions, scrutinizing its surface for flaws—it was a tangible way to ensure quality. These early checks could spot potential issues long before they hit production.
Clarity in Contracts
When it comes to contracts, I’ve learned that clarity is king. Detailed quality clauses set the stage for accountability. It’s like planning a trip; every detail needs to be spelled out—product specifications, acceptance criteria, even compensation clauses.
Quality Aspect | Specification | Inspection Method |
---|---|---|
Size Tolerance | ±0.1mm | GB/T 2828.1-2012 |
Appearance | No scratches or bubbles | Visual Check |
I recall a contract where we outlined every expectation down to the size tolerance and appearance checks. It was satisfying knowing both parties were on the same page.
Production Process Supervision
Supervising production is where continuous improvement really shines. It’s about vigilance and collaboration. I remember overseeing a critical project and the importance of having real-time monitoring by factory supervision12. It was like having a front-row seat to the entire process, ensuring raw materials were top-notch and operations were smooth.
Regular audits became routine—checking document updates and product samples for conformity with agreed standards. Each audit was an opportunity to solidify our commitment to quality standards.
Emphasizing Continuous Improvement
In my journey, data collection13 became an invaluable tool. By tracking patterns in defects, we could pinpoint root causes—like mold wear—which led to significant quality enhancements. Feedback loops with suppliers created a culture of continuous improvement. We’d require detailed corrective actions, follow-ups ensuring these measures were more than just promises—they were realities.
With these strategies, I’ve seen firsthand how continuous improvement doesn’t just elevate supplier quality; it transforms business partnerships into engines of mutual growth and success.
ISO 9001 certification ensures supplier quality commitment.True
ISO 9001 is a recognized standard for quality management systems.
Real-time monitoring is unnecessary for critical projects.False
Real-time monitoring helps prevent quality issues in critical projects.
Conclusion
Ensure quality consistency in injection molding by evaluating suppliers, establishing clear contracts, supervising production, and fostering continuous improvement through audits and data analysis.
-
Discover why evaluating suppliers is crucial for maintaining high-quality standards in manufacturing. ↩
-
Explore strategies for enhancing your supplier evaluation processes to boost efficiency and quality. ↩
-
Understand how ISO 9001 certification reflects a supplier’s commitment to quality management systems. ↩
-
Learn effective techniques for giving feedback that leads to supplier improvements. ↩
-
Understanding supplier evaluation processes ensures you select partners who meet quality standards and compliance requirements. ↩
-
Learn how production audits improve manufacturing quality by ensuring adherence to set standards and identifying areas for improvement. ↩
-
Explore how implementing a quality management system enhances product consistency and compliance with industry standards. ↩
-
Learn how equipment calibration impacts product consistency and quality control, critical for manufacturing success. ↩
-
Understand how real-time monitoring enhances production efficiency and identifies quality issues early on. ↩
-
Discover how implementing robust QMS fosters continuous enhancement of product and process quality. ↩
-
Understand the essentials of conducting a thorough supplier evaluation to ensure quality and reliability. ↩
-
Learn how real-time supervision can prevent defects and enhance product standards. ↩
-
Discover effective methods for gathering and analyzing supplier performance data to drive improvements. ↩