Picture cutting valuable seconds from your production process. This change is important. In injection molding, less cooling time matters a lot.
I reduce injection mold cooling time by changing cooling channel designs. Increasing the number of channels helps a lot. Larger channels also really help. Multi-layer channels can make a difference too. I pick materials that move heat fast. Exactly controlling the temperature and flow of the cooling medium is important. The changes help make cooling faster. Cooling gets much better this way.
I remember my first time facing this challenge. It was like solving a giant puzzle. Each piece brought more clarity. Choosing the right materials helped. Optimizing cooling channels was important. These techniques probably really change your molding work.
Symmetrical channels improve cooling efficiency.True
Symmetrical channels ensure even heat distribution, enhancing cooling.
Liquid nitrogen is a cost-effective cooling medium.False
Liquid nitrogen is expensive and complex to operate, not cost-effective.
- 1. Why Does Cooling Channel Layout Matter in Mold Design?
- 2. How does increasing cooling channel size affect cooling efficiency?
- 3. Why Should You Consider Multi-Layer Cooling Channels for Thick-Walled Products?
- 4. Which Mold Materials Offer the Best Thermal Conductivity for Faster Cooling?
- 5. Conclusion
Why Does Cooling Channel Layout Matter in Mold Design?
Mold design is not only about forming shapes. It involves the skillful control of cooling.
The cooling channel layout in mold design is very important. It helps cooling work better. This reduces cycle times. Product quality also gets better. A good cooling design gives even temperature. This reduces flaws. The cooling channels really matter.
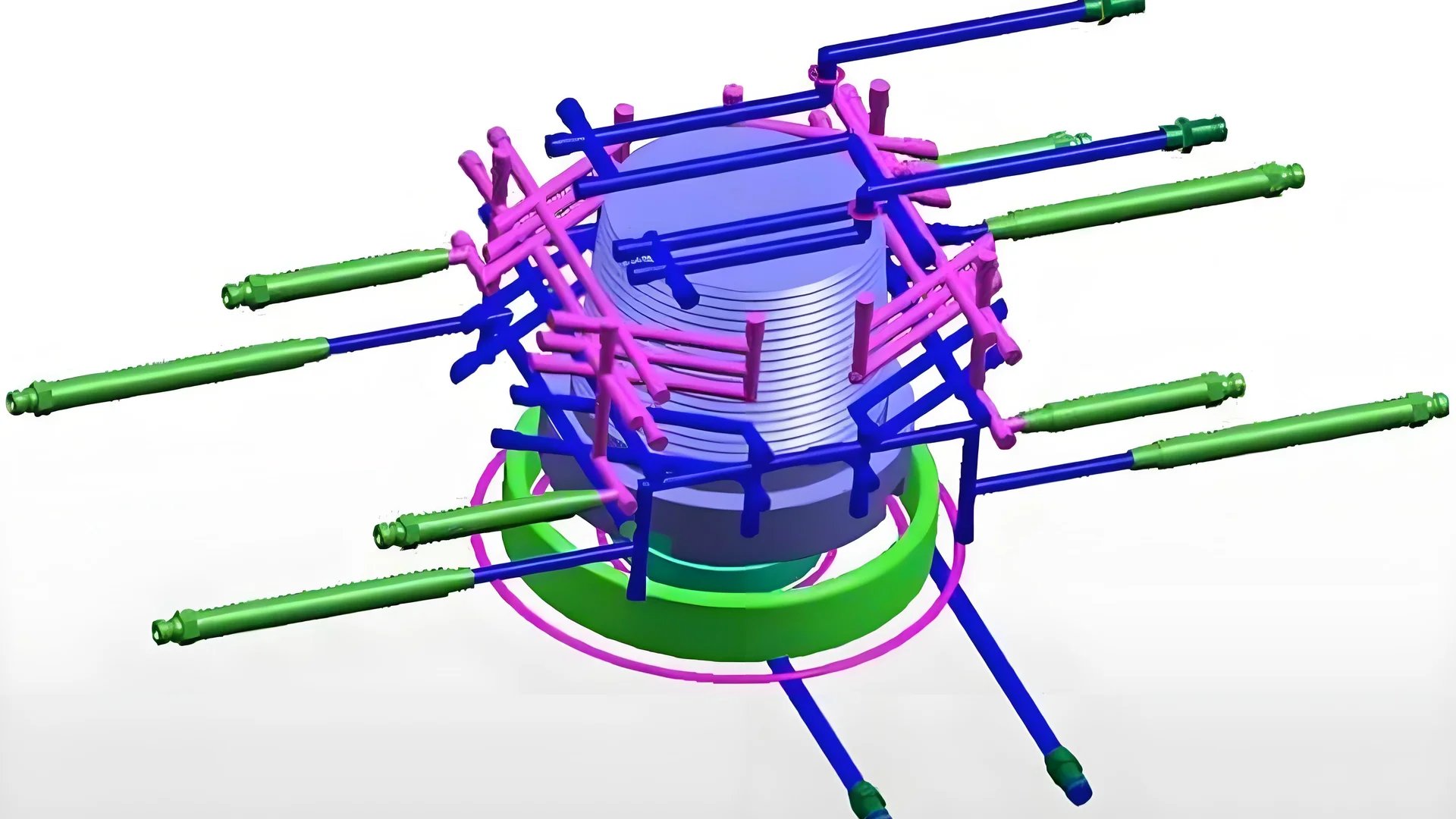
Optimizing Cooling Channel Design
I remember when I first understood the importance of cooling channel design. It happened during a project to produce cylindrical parts. At first, the cooling was uneven and parts became warped. Then I realized I must think symmetrically. We placed cooling channels all around1 the cylinder. Heat was whisked away evenly. It was like night turning into day; efficiency increased and defects decreased.
Increasing the Number and Diameter of Channels
Once, a colleague proposed adding more and larger cooling channels. Initially, I hesitated, fearing for the mold’s strength. We balanced it carefully and voilà! More contact area allowed better heat transfer without weakening the mold. A small change sometimes really impacts a lot.
Multi-layer Cooling Channel Strategies
For a thick-walled product, I was confused until I discovered multi-layer cooling channels. Adding layers in the mold core was like giving the design extra strength. Heat left both internal and external surfaces faster, reducing cooling time significantly2 and increasing productivity.
Selecting Appropriate Cooling Mediums
Water is my usual choice due to its low cost and high heat capacity. Yet, one project needed precise temperature control to stop rust, so we switched to a special coolant for thermal stability—it changed everything! Although I’ve not tried liquid nitrogen yet, it might be useful for very fast cooling in extreme situations.
Controlling Temperature and Flow
I learned the hard way that cooler isn’t always better. In one project, the cooling medium was too cold and caused marks on the surface of products. Now, precise control with regulators is vital to keep perfect conditions without causing defects like cold marks. Adjusting flow rates with strong pumps really improves efficiency without causing extra vibrations or leaks.
Planning the right cooling channel layout is now second nature to me; it’s crucial for quality and efficiency in production.
Symmetrical cooling improves heat distribution in molds.True
Symmetrical cooling channels ensure even heat removal, enhancing efficiency.
Larger cooling channels always increase mold strength.False
Increasing channel size can weaken mold strength if not carefully designed.
How does increasing cooling channel size affect cooling efficiency?
Have you ever thought about how changing the size of cooling channels might improve your cooling efficiency? Let me share some ideas.
Improving cooling efficiency often means using larger cooling channels. Bigger channels let more coolant flow. This helps transfer heat faster. However, one must balance these changes with possible problems. Structural weaknesses can occur. Mold may become more complex.
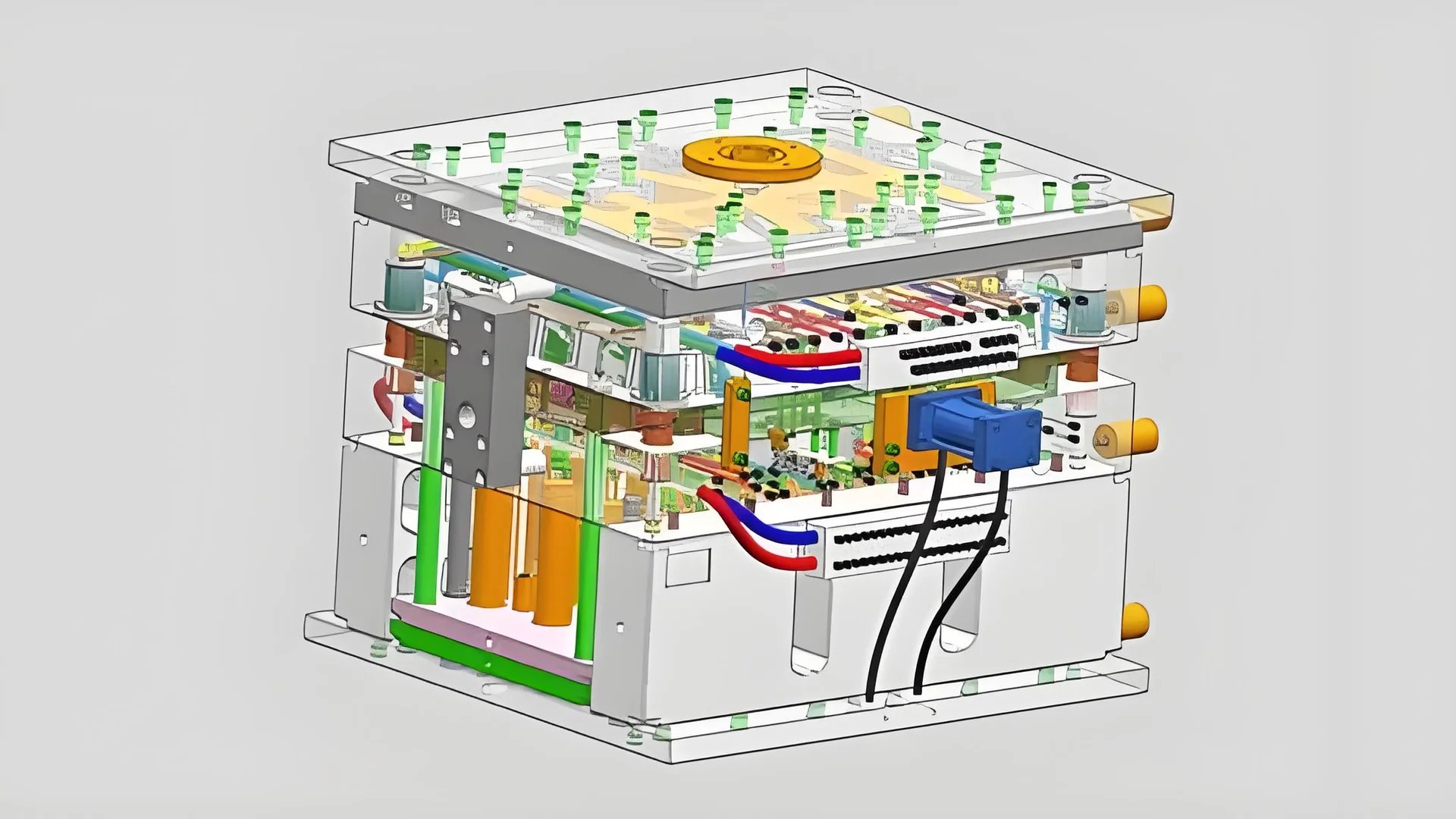
The Role of Cooling Channel Design
I remember the first time I had to improve a mold’s cooling channel design. It felt like solving a puzzle where everything needed to fit just right. By changing the number and size3 of the channels, I discovered more coolant contact led to faster heat loss. Simple shapes worked best with a symmetrical design. However, with complex parts like tabs and ribs, placing channels near hot areas was crucial.
The Impact of Increased Channel Size
Larger channels changed everything for me. They let more coolant move through, which removed heat faster. Bigger isn’t always better, though. I had to watch out for the mold’s strength. Too large and the mold could become weak, especially when under high pressure. Balancing size and strength was crucial in my projects.
Multi-Layer Cooling Strategies
For thick molds, I used multi-layer cooling strategies that cooled from both inside and outside surfaces simultaneously. This method shortened the heat’s journey significantly. A multi-layer design4 proved useful for uneven wall thicknesses, effectively giving each section its own cooling system.
Selecting Appropriate Cooling Mediums
Choosing the right cooling medium was crucial in my work. Water was my usual choice due to its low cost and efficiency; however, sometimes precision required special coolants offering better stability. For very fast cooling needs, liquid nitrogen was ideal despite being expensive and tricky.
Temperature and Flow Control
Controlling temperature and flow of the cooling medium proved essential in achieving optimal results. Lower temperatures increased the heat transfer rate but if too cold could cause defects like cold marks to appear. High-performance pumps increased circulation speed; yet it was important to avoid vibrations or leaks during operation5. Finding this perfect balance was indeed a real challenge.
Symmetrical cooling channels improve heat distribution.True
Symmetrical channels ensure even heat removal, enhancing cooling efficiency.
Increasing cooling channel diameter always strengthens the mold.False
Larger diameters can weaken mold structure, risking stability.
Why Should You Consider Multi-Layer Cooling Channels for Thick-Walled Products?
Have you ever thought about why multi-layer cooling channels transform injection molding? These channels improve efficiency. Cooling is quicker. This results in faster production. Faster production is important. It saves time. With quicker cooling, products become stronger. Stronger products last longer. They are also more reliable. These channels minimize defects. Fewer defects ensure high quality. High-quality products are in demand. Demand really means success.
Multi-layer cooling channels in injection molding help control temperature better. They cut down cooling time for thick-walled items. Cooling time becomes shorter. These channels spread heat evenly, which really improves the quality of the product. Complex shapes cool evenly.
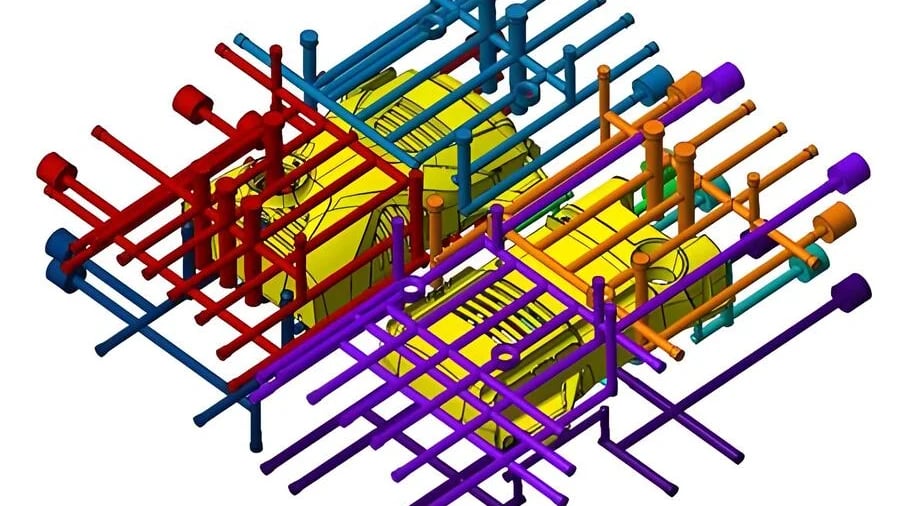
Improve Cooling Efficiency
I remember my first time with injection molding. The complexity of designing cooling systems for thick-walled products6 fascinated me. The challenge involved handling heat during cooling. At first, I used single-layer cooling channels. They failed to meet the demands of complex designs. Moving to multi-layer channels felt like leveling up in a game. This change really improved thermal conductivity, making cooling more uniform.
Flexibility and Precision in Design
Creating a reasonable layout7 that fits each product’s shape feels very satisfying, like placing the final piece in a puzzle. This adaptability provides tricky areas—like tabs and ribs—with the cooling they need. I remember working on cylindrical parts; arranging the channels around them drastically reduced cooling time, solving a complex problem.
Expand Cooling Channel Capacity
Increasing the number and size of these channels was a real eye-opener for me, akin to adding more lanes to a highway, allowing more cooling medium, such as water, to pass through and increase the heat transfer rate8. But balancing that with the mold’s strength? It felt like juggling on a unicycle.
Choose the Right Cooling Medium
Picking the right cooling medium is as important as choosing the right tool. Water is often my favorite due to its cost-effectiveness and high specific heat capacity. However, sometimes I use other coolants for precise temperature control or anti-corrosion purposes. It’s interesting how ultra-cold substances like liquid nitrogen can be used—powerful yet complicated.
Consider Materials and Process Parameters
Using high thermal conductivity materials in molds is important; imagine using copper alloys in key areas—it’s like boosting your cooling process with rockets, really speeding up heat dissipation9. Adjusting injection molding parameters, such as melt temperature and injection speed, feels like tuning a machine to keep the thermal profile balanced and prevent issues like cold marks or uneven solidification. It’s about finding that perfect balance where everything harmonizes.
Multi-layer cooling channels reduce cooling time.True
Multi-layer cooling channels efficiently remove heat from all surfaces, reducing time.
Liquid nitrogen is a cost-effective cooling medium.False
Liquid nitrogen is costly and complex, not typically cost-effective for cooling.
Which Mold Materials Offer the Best Thermal Conductivity for Faster Cooling?
Do you ever think about how choosing the correct mold materials might change your manufacturing process?
Copper alloys and high-thermal conductivity steels are my favorite mold materials. They transfer heat very well. This reduces cooling times a lot. Production speeds up as a result.
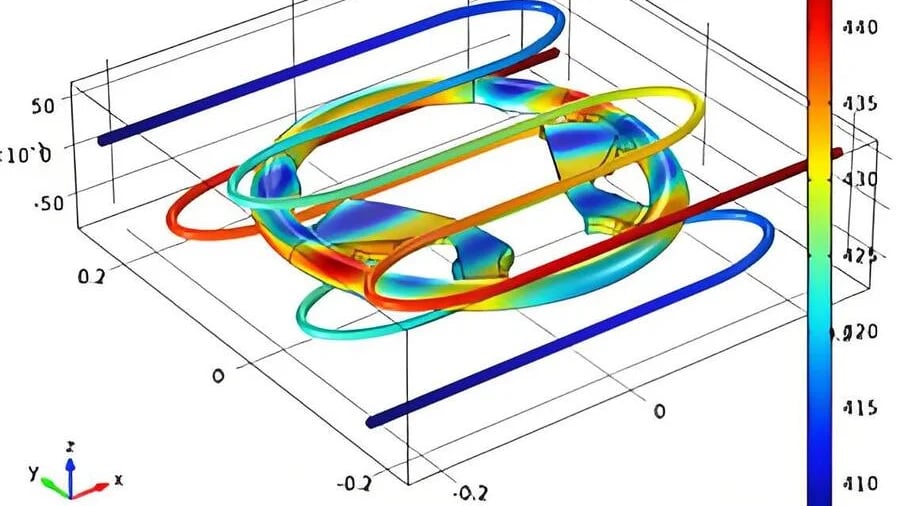
Understanding Thermal Conductivity in Mold Materials
When I first explored mold materials, it felt like deciphering a secret code. Thermal conductivity in a material acts like a superpower. It lets heat flow freely, like wind through an open window. This power is crucial because it affects how fast a product cools in the mold. High thermal conductivity means heat swiftly moves away to the cooling channels. This speeds up the process.
Copper Alloys: The Gold Standard
Copper alloys are like my magic tool for cooling. Beryllium copper stands out; it feels like a small engine speeding up heat transfer. They might cost more and are not as strong as steel, but their cooling ability is valuable. I use copper alloy parts in molds where they meet hot plastic. The difference is clear—it improves cooling channel efficiency10 and increases mold life by reducing heat stress.
High-Thermal Conductivity Steels
High-thermal conductivity steels are great partners for copper alloys. They balance strength and speed well, moving heat away fast while staying strong for tough jobs. Some stainless steels get modified to improve11 their thermal properties without sacrificing structural integrity. These steels are good for complex molds needing strength.
Innovative Coatings for Better Performance
Mold surfaces with special coatings look impressive. Coatings like ceramic or diamond-like carbon give molds a modern upgrade—they help heat dissipate and protect from damage. Applying these coatings reduces cooling times, especially for detailed designs where time matters.
These coatings excel when applied to molds12 needing quick heat changes, improving thermal performance and extending mold lifespan.
Integrating Material Choices with Design
Choosing the right material is just the start; designing the cooling channels matters too—it’s like arranging music where every note is important. Multi-layer cooling channels placed in the right spots keep things smooth. High-conductivity materials mixed with a thoughtful cooling channel layout13 speed up cooling.
By using these materials and methods, cycle times get shorter and production increases while keeping quality high—it’s like a perfect dance between materials and design.
Symmetrical cooling channels enhance cooling efficiency.True
Symmetrical channels ensure even heat distribution, improving cooling.
Copper alloy is less conductive than mold steel.False
Copper alloy has higher thermal conductivity than mold steel.
Conclusion
Optimizing injection mold cooling involves redesigning channels, increasing their size and number, using multi-layer strategies, selecting effective cooling mediums, and controlling temperature for improved efficiency and product quality.
-
Explore how symmetry aids even heat distribution. ↩
-
Learn how to efficiently cool complex shapes. ↩
-
Learn how channel diameter influences heat transfer rates. ↩
-
Discover why multi-layer designs enhance cooling efficiency. ↩
-
Explore how flow rate adjustments prevent mold defects. ↩
-
Learn how multi-layer channels optimize heat management in complex designs. ↩
-
Explore strategies for effective channel layout in various mold shapes. ↩
-
Discover methods to enhance thermal efficiency in molding processes. ↩
-
Understand how material choice affects cooling performance. ↩
-
Learn how copper alloys enhance cooling channel performance. ↩
-
Discover methods to enhance steel’s thermal efficiency. ↩
-
Explore how ceramic coatings boost mold cooling efficiency. ↩
-
Find strategies for effective cooling channel design. ↩