Picture reducing your design work from long weeks to just a few days, all the while increasing both productivity and craftsmanship. This is the wonder of mold design standardization.
Mold design standardization uses the same parts and methods. It organizes the manufacturing process better. Efficiency goes up. Costs drop. Product quality increases. Design cycles become faster. Production expenses go down because bulk buying is possible. Maintenance tasks become simpler.
I remember my early days in design. Each project felt like starting from scratch. Every part needed careful customization. Weeks passed before finalizing a mold. Then, I found out about mold design standardization. Suddenly, details no longer overwhelmed me. Standard parts and steps quickened the process more than I thought possible.
Design cycles became really short. They went from weeks to just days. Working with my team became much easier. We understood each other because we used the same design rules. Costs dropped a lot too. Buying standard parts in large amounts cut production expenses by 20% or more.
Quality also got better. Standard components brought reliability. Nobody worried about them failing anymore. Maintenance was easy with parts that you could replace quickly. Imagine no stress about downtime when something broke – just replace it smoothly. Standardization brought efficiency to mold management. Now, I focus on creativity instead of dealing with logistics.
Standardized molds reduce design cycles significantly.True
Using standard parts and processes shortens design cycles from weeks to days.
Non-standard molds are cheaper to produce than standardized ones.False
Standardized parts allow for bulk purchasing, reducing production costs.
- 1. How Does Standardization Shorten the Design Cycle?
- 2. What Cost Savings Can Be Achieved Through Batch Procurement?
- 3. How Do Standardized Designs Enhance Mold Quality?
- 4. Why Is Standardization Beneficial for Mold Maintenance?
- 5. How Does Efficient Management Stem from Standardized Mold Designs?
- 6. Conclusion
How Does Standardization Shorten the Design Cycle?
Have you ever thought about how standardization changes your design work? I will tell you about my journey into this changing practice and how it really improves your productivity.
Standardization shortens the design process with ready-made parts and consistent specifications. Designers quickly assemble molds without starting from zero. This process eases communication and collaboration. Design time decreases a lot.
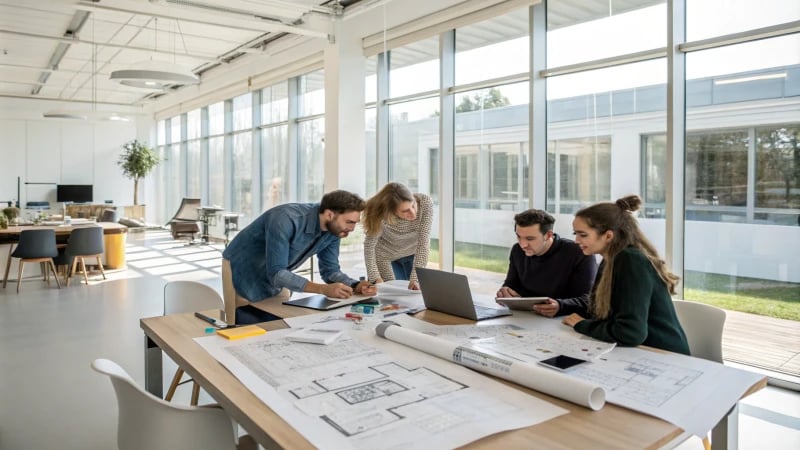
Simplifying Design with Ready-Made Parts
One of the key ways that standardization shortens the design cycle is through the use of ready-made components. I once doubted standardization; it sounded strange. But my view changed during a tough design job with a tight deadline. I found standard mold bases and demoulding parts, which are pre-defined in size and structure. These ready-made pieces saved me valuable time, shrinking my design time from weeks to days.
Component Type | Standardized Option | Time Savings |
---|---|---|
Mold Base | Standard Mold Base | From weeks to days |
Cooling System | Standard Channel Size | Quick integration |
Better Teamwork with Common Standards
Unified design standards improve teamwork by creating a common language among designers. Teamwork sometimes feels chaotic because designers speak different "languages." However, standardization changed this for us. We started using the same system, reducing communication costs1 significantly. A teammate made a cooling system with standard rules, allowing others to quickly evaluate or integrate this into their designs.
This approach ensures that when reviewing or assembling designs, team members can focus on creativity rather than logistics, enhancing overall design efficiency2. No more dealing with confusion made us really efficient.
Cheaper Production Using Standard Parts
Standardization didn’t just save time; it saved money too. By enabling batch procurement of standardized parts like pins and sleeves, manufacturers benefit from bulk discounts, lowering production expenses by 30%. This cost-efficiency translates into more competitive pricing and a streamlined production process.
For example, buying standard mold frames in bulk can reduce costs by 20% – 30% compared to custom frames. These savings are passed on to clients, making standardized designs an attractive option for mold manufacturers3 looking to maintain a competitive edge.
Better Quality and Trust
At first, I feared standardization might lower quality. It didn’t. The reliability of standardized components is another advantage as they have undergone extensive testing and are highly reliable across different designs. For example, using a standard demolding mechanism ensures effective removal of plastic parts, reducing defects like poor demolding.
Additionally, the interchangeability of standardized parts simplifies maintenance and repair. If a part failed, we could swap it fast with another of the same specification, cutting downtime and ensuring minimal downtime while sustaining mold quality4.
All these points help speed up design work. Standardization is not just a strategy; it’s essential for mold design success. Whether working on big projects or daily tasks, standardization probably leads to efficiency and probably success.
Standardization shortens mold design cycles significantly.True
Standard mold bases and parts reduce design time from weeks to days.
Bulk purchasing of non-standard parts reduces costs by 30%.False
Bulk purchasing reduces costs for standard, not non-standard, parts.
What Cost Savings Can Be Achieved Through Batch Procurement?
Have you ever thought about how buying in large quantities helps your business grow? Buying in bulk probably saves not just a few coins but a lot more.
Buying in large quantities lowers costs by using size advantages, getting big discounts and simplifying delivery. This method helps companies discuss better deals with suppliers, resulting in cheaper item prices and shipping. Savings on unit prices happen.
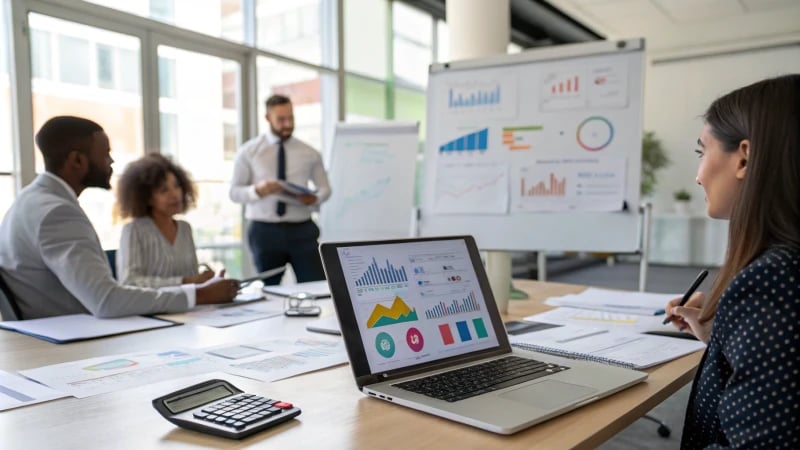
Economies of Scale in Batch Procurement
When companies engage in batch procurement5, they benefit from economies of scale. At the start of handling procurement, I was surprised by how much money we kept by buying large amounts. Combining orders meant we paid less for each item, improving our profits greatly. Negotiating for basic materials felt like buying groceries in bulk – you buy more, you pay less per piece. Very simple.
Quantity Purchased | Unit Price |
---|---|
100 Units | $5 |
500 Units | $4.50 |
1000 Units | $4 |
Bulk Discounts and Supplier Negotiation
Negotiating favorable terms is easier when orders are placed in bulk. Once, we got a big price cut on basic parts by ordering a lot at once. Our suppliers felt happy because they had secured a steady stream of business, leading to savings of about 10-20%.
- Example: A company ordering standard mold bases might save up to 30% over custom ones.
Streamlined Logistics and Reduced Transportation Costs
Batch procurement also means fewer deliveries, which can decrease logistics and transportation costs. With fewer deliveries, problems and costs go down! I once reduced our yearly transportation expenses by 15% by choosing bulk shipments.
- Case Study: By using batch procurement, a mid-sized company lowered transport costs by 15% yearly.
Standardization and Cost Efficiency
With standardized products, companies can further cut costs by aligning their procurement strategy with batch purchasing. Standardizing means simplifying – everything becomes cheaper and easier to handle.
- Standardized Parts6 usage ensures that components are interchangeable, simplifying maintenance and minimizing downtime, thereby indirectly saving costs.
Impact on Inventory Management
Buying in bulk means more goods to keep track of. However, with smart planning, the positives are much bigger than the negatives. Careful planning helped us maintain the right balance between how much we stored and how often we bought, avoiding extra storage costs.
- Inventory Strategy: Smart planning balances stock with how often you buy.
These strategies really show how batch procurement can change a business – not just by reducing costs but by improving efficiency everywhere. Whether you’re new in procurement or experienced like me, these ideas could probably change how you work.
Standard mold bases shorten design cycles significantly.True
Using standard mold bases allows designers to skip custom sizing, saving time.
Batch procurement increases mold production costs by 20%.False
Batch procurement actually reduces costs by 20% - 30% due to bulk discounts.
How Do Standardized Designs Enhance Mold Quality?
Ever thought about how a small change in design could transform mold quality? I really want to tell you about my experience with standardized designs. These designs completely changed everything for me.
Standardized designs improve mold quality through greater efficiency, lower costs and solid reliability. These designs simplify maintenance and management. Molds last longer and save money.
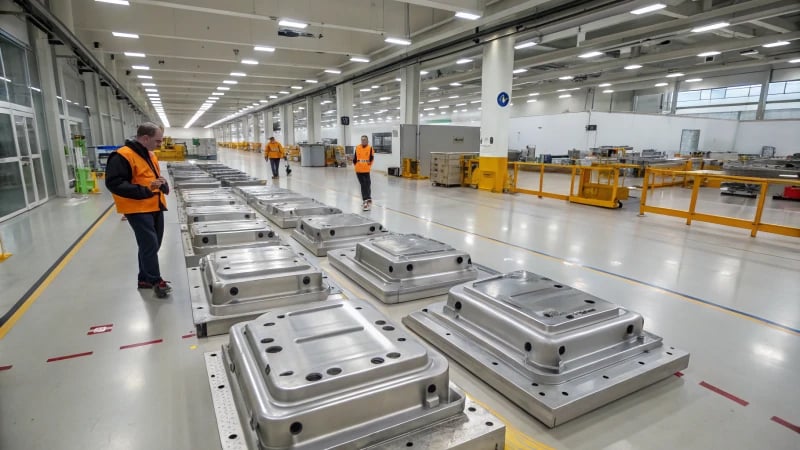
Improving Design Efficiency
Using standardized designs felt refreshing in my work. No more hours spent designing every single part from the start. With ready-made components like standard mold bases7, design cycles were reduced from weeks to just a few days. It was as if my team found a unified language, which made working together effortless.
Reducing Production Costs
Standardized parts changed how we looked at costs. I recall buying standard guide pins8 and sleeves in bulk, which cut our expenses by nearly 30%. Consistent quality and less need for special equipment kept us precise without large spending.
Standard Part | Cost Reduction (%) |
---|---|
Mold Frames | 20 – 30 |
Guide Pins | 15 – 25 |
High Reliability
Reliability became less of a concern as standardized parts showed their quality through tough tests. I witnessed a standard demolding mechanism consistently perform better than expected, leading to fewer defects and better-quality molds.
Easy Maintenance and Management
Standardized designs made maintenance simple. Troubleshooting became easier with familiar mold structures9. Inventory management improved too. Everything became more organized, which let us think more about new ideas than about managing logistics.
Standardized mold design shortens the design cycle by 50%.True
Standardized parts reduce design time from weeks to days, enhancing efficiency.
Using non-standard parts always reduces production costs.False
Non-standard parts often increase costs due to custom processing needs.
Why Is Standardization Beneficial for Mold Maintenance?
Curiosity about how order changes chaos into smooth operation? Standardization achieves this in mold maintenance.
Standardization in mold maintenance increases design efficiency. It reduces production costs and improves mold quality. Management becomes simpler. Parts remain consistent and interchangeable. Teamwork thrives. The whole process becomes optimized.
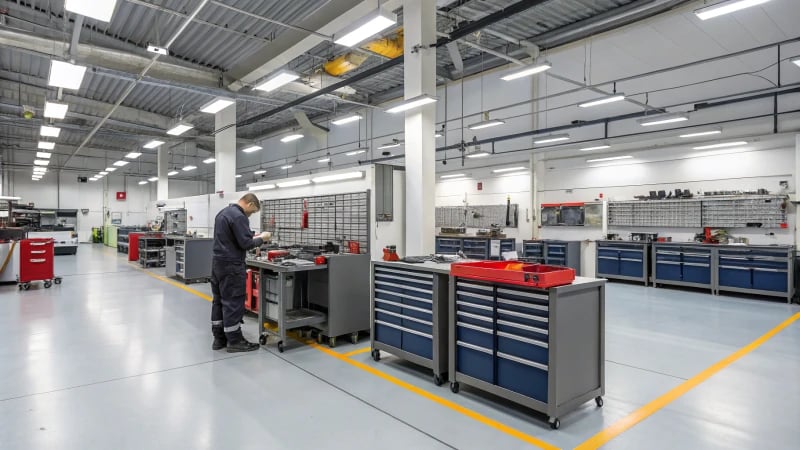
Improving Design Efficiency
Projects without a clear plan can tire you out quickly. Standardization10 acts like a helpful tool, saving hours and reducing stress. For molds, pre-made standard bases and demoulding parts simplify the process. Designers can skip starting fresh, easing their workload greatly. This quickens progress and helps teams work in sync, creating smooth collaboration.
Benefit | Explanation |
---|---|
Shortened Design Cycle | Ready-made parts enable quicker assembly and design processes. |
Easy Teamwork | Unified standards improve communication and collaboration among team members. |
Cutting Production Costs
Ordering custom parts is costly. Buying in bulk is better. Bulk purchases reduce expenses, especially for standard components. Using proven techniques becomes easier with these parts. Imagine reducing expenses without losing quality. Standardization11 offers this advantage.
- Bulk Buying: Bulk purchasing of standard items like guide pins cuts costs.
- Lower Processing Expenses: Efficient methods with standard parts save both time and money.
Enhancing Mold Quality
High-quality molds matter a lot. Standard parts are reliable because they have been tested many times. If something fails, replacing it is straightforward. Mold performance remains steady as each piece fits perfectly.
Quality Improvement | Description |
---|---|
Enhanced Reliability | Standard designs ensure stable and dependable mold performance. |
Good Interchangeability | Damaged parts are easily replaced with identical standard components, maintaining the mold’s effectiveness. |
Simplifying Maintenance and Organization
Diagnosing mold issues can be tricky. Standardized molds minimize confusion. Predictive maintenance reveals issues quickly, easing tasks for teams. Mold management also becomes simpler, with clear organization.
- Quick Maintenance: Staff swiftly find and solve problems with standard designs.
- Organized Handling: Standard molds help classify and manage inventory, making company operations efficient.
Overall, standardization12 plays a vital role in improving mold maintenance by ensuring consistency, reducing mistakes, and wisely using resources during production and upkeep.
Standard mold bases reduce design cycle by 50%.True
Using standard mold bases streamlines design processes, significantly cutting time.
Non-standard parts increase processing costs by 30%.True
Complex shapes in non-standard parts require special tech, raising costs.
How Does Efficient Management Stem from Standardized Mold Designs?
Have you ever thought about how a small shift in your mold design might transform your production methods?
Efficient management in manufacturing often starts with standardized mold designs. These designs simplify design processes, really cut costs and improve product quality. They help teamwork become more straightforward. Procurement improves with standardization. Maintenance becomes easier too. All these factors lead to smoother operations.
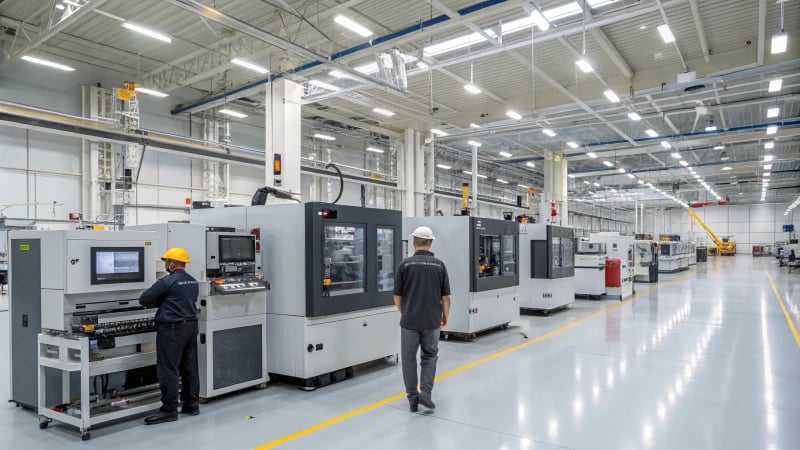
Streamlining the Design Process
Standardized mold designs provide a framework that enhances design efficiency13. I recall my first encounter with these designs. Initially, doubt filled my mind—could such structured designs truly offer the flexibility we needed? But then I started using the set sizes and forms, and it was like discovering something new. No longer did I need to spend endless days or weeks crafting each design from the ground up. Instead, I dove straight into the creative parts, feeling confident that the basics were already handled. This approach shortened our design time significantly.
Additionally, it facilitates easier collaboration as team members share a common understanding of design specifications. Our teamwork improved as well; everyone communicated in the same ‘design language.’
Design Efficiency Impact Table
Factor | Impact |
---|---|
Predefined Structures | Shorter design cycles |
Unified Specifications | Improved teamwork |
Cost Reduction Strategies
Picture entering a workshop where everything functions smoothly and clearly. The economic benefits of standardized mold designs are substantial. Batch procurement with standardized mold designs mirrors this efficiency by enabling companies to leverage economies of scale.
When my company began buying standard parts like guide pins and sleeves in large quantities, we noticed significant discounts—up to 30%. It was like uncovering a hidden treasure. These savings had a major impact on our profits.
Moreover, established processing techniques meant less reliance on expensive custom parts, giving us more room for new ideas and projects.
Product Quality Improvement
Quality stands at the core of manufacturing, and standardized molds have transformed how I ensure it through enhanced reliability14. These designs serve as reliable recipes that produce consistent results every time.
Knowing that a standard demolding mechanism will safely remove parts without causing damage provides tremendous peace of mind. And if a part breaks, interchangeable parts allow quick fixes, preventing disruption and keeping quality consistent everywhere.
Simplified Maintenance and Management
I often dreaded maintenance days—until standardized mold structures arrived. With familiar setups, solving problems became much easier; I almost predicted issues before even opening a mold.
This simplicity extended to managing our entire stock. By organizing molds based on standard specifications, we improved everything from storage to maintenance scheduling—very efficient.
Maintenance & Management Benefits Table
Benefit | Example |
---|---|
Easier Maintenance | Quick troubleshooting |
Efficient Management | Simplified inventory control |
Through embracing standardization15, I have directly witnessed how businesses can operate with greater efficiency, achieve large cost savings, and maintain high quality. It goes beyond just making things simpler; it changes how we tackle challenges in the world of manufacturing.
Standard molds reduce design time by 50%.True
Using standardized parts, designers can cut design cycles from weeks to days.
Non-standard molds are cheaper than standard ones.False
Standard molds allow for bulk purchasing and lower costs by 20%-30%.
Conclusion
Mold design standardization enhances efficiency, reduces costs, improves quality, and simplifies maintenance by utilizing ready-made components and unified specifications, transforming the manufacturing process significantly.
-
Learn about the benefits of standardized communication within design teams, including reduced costs and improved efficiency. ↩
-
Explore how standardization enhances design efficiency by simplifying processes and reducing time wastage. ↩
-
Discover cost-saving strategies for mold manufacturers through bulk purchasing of standardized components. ↩
-
Find out how using standardized parts ensures consistent quality and reliability in mold production. ↩
-
Learn how leveraging economies of scale through batch procurement can reduce unit costs and enhance purchasing efficiency. ↩
-
Explore the advantages of using standardized parts in manufacturing, including cost efficiency and ease of maintenance. ↩
-
Understand how standardized bases expedite the mold design process and enhance efficiency. ↩
-
Learn why buying guide pins in bulk reduces costs and improves manufacturing efficiency. ↩
-
Discover how familiar structures simplify maintenance tasks and troubleshooting. ↩
-
Learn how standardized practices lead to faster, more efficient design processes. ↩
-
Explore why standardization is crucial for improving manufacturing processes. ↩
-
Explore why standardization is crucial for improving manufacturing processes. ↩
-
This link offers insights into how standardized mold designs improve design efficiency and teamwork in manufacturing. ↩
-
Explore how standardized molds contribute to product reliability and quality through enhanced design features. ↩
-
Understand the broader impact of standardization on improving manufacturing efficiency and operational effectiveness. ↩