Injection molding is a fascinating dance of precision and creativity, where the right nozzle design can make or break the entire production process.
To optimize nozzle design in injection molding, focus on selecting appropriate nozzle types, adjusting sizes for specific materials, and employing effective heating methods. Proper alignment and sealing between nozzle and mold are also critical for superior outcomes.
While the basic strategies for optimizing nozzle design are straightforward, the nuances of implementation can vary significantly depending on specific materials and production environments. Delve deeper into these techniques to uncover advanced methods that could transform your operations.
Straight-through nozzles are ideal for heat-sensitive plastics.False
Straight-through nozzles are best for high-viscosity plastics, not heat-sensitive ones.
How Does Nozzle Type Affect Injection Molding Efficiency?
In injection molding, nozzle type significantly influences efficiency, affecting material flow and product quality.
The nozzle type in injection molding determines the flow characteristics, temperature control, and material compatibility, directly impacting production efficiency. By selecting the right nozzle type, manufacturers can optimize material flow, reduce defects, and enhance product quality.
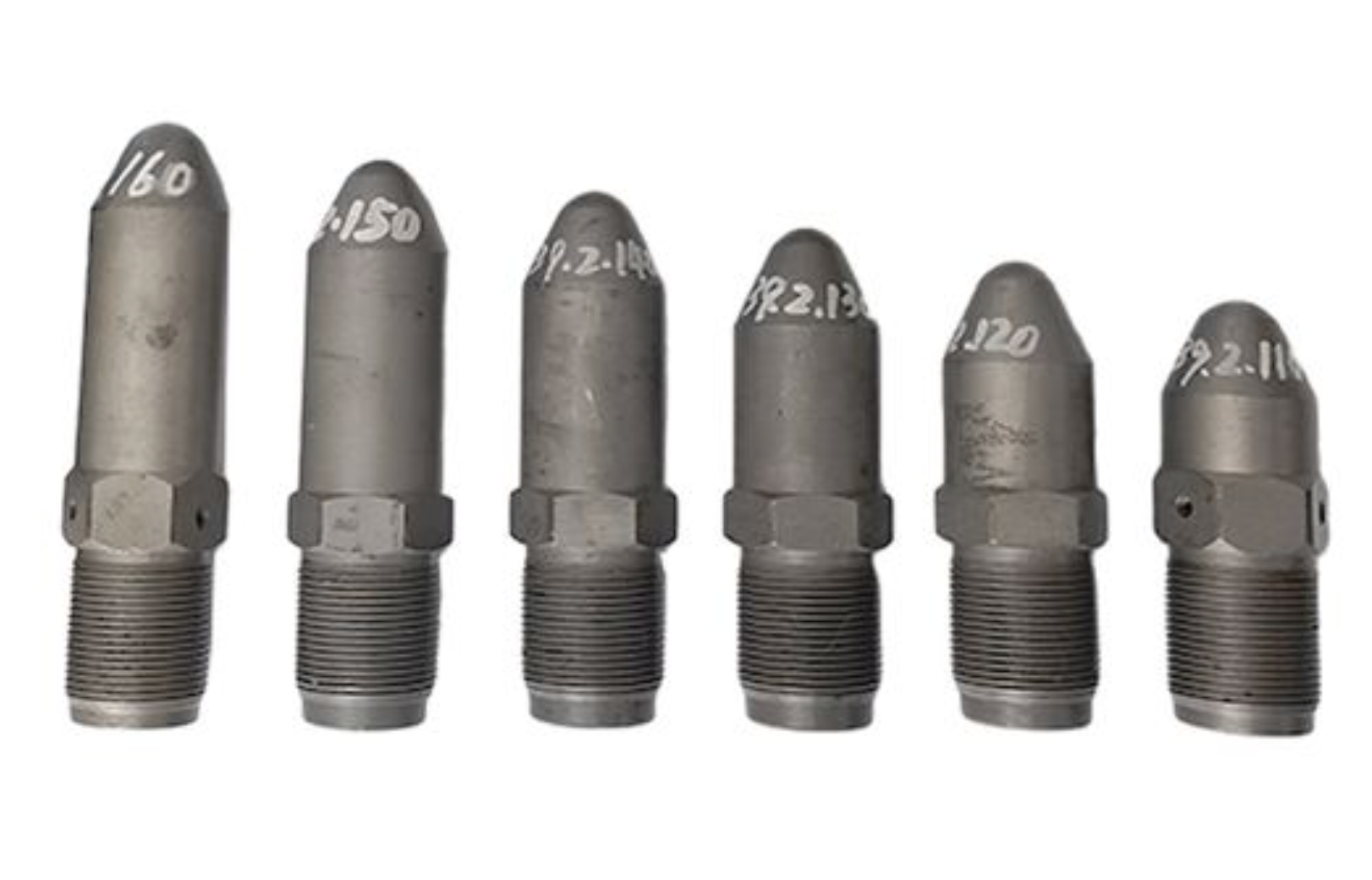
Understanding Nozzle Types in Injection Molding
In the injection molding process, selecting the right nozzle type is crucial for achieving efficient production. There are several types of nozzles, each designed for specific materials and molding conditions. Let’s examine some of these types and their impact on efficiency.
Straight-through Nozzle
Features and Applications:
- This nozzle has a simple structure, making it easy to manufacture.
- It is particularly effective for high-viscosity plastics like polyethylene and polypropylene.
- The design ensures low pressure loss but is prone to cold material formation due to its short flow channel.
Optimization Insights:
- Consider increasing the nozzle length to enhance heating effects and reduce cold material generation.
- Modify the inner hole shape to smoothen the flow, decreasing resistance.
Self-locking Nozzle
Features and Applications:
- Equipped with a mechanism to prevent plastic backflow, essential for heat-sensitive plastics such as polycarbonate.
- Automatically seals after injection to prevent plastic solidification.
Optimization Insights:
- Ensure reliability in the self-locking mechanism to improve opening and closing timing.
- Enhance nozzle heating systems to maintain plastic in a molten state.
The Impact of Nozzle Type on Material Flow
Nozzle type not only affects the physical properties of the injected material but also plays a pivotal role in controlling the flow rate and injection pressure. For instance, a straight-through nozzle might offer a simple design with minimal pressure loss; however, it can struggle with heat-sensitive materials due to potential cold material formation. In contrast, a self-locking nozzle provides better control over material flow and prevents backflow issues, which is critical for maintaining product integrity.
Influence on Product Quality
The choice of nozzle impacts not just efficiency but also the final product quality. Misalignment or inappropriate nozzle selection can lead to defects such as burning or bubbles in the molded parts. By carefully selecting a nozzle that complements the material properties, manufacturers can reduce defect rates significantly.
Evaluating Scenarios for Optimal Nozzle Selection
Material Type | Recommended Nozzle | Key Considerations |
---|---|---|
High-viscosity plastics | Straight-through | Minimize cold material by optimizing design |
Heat-sensitive plastics | Self-locking | Ensure precise temperature control |
Poor fluidity plastics | Self-locking | Reliable backflow prevention mechanisms |
Each type presents unique challenges and advantages. Understanding these nuances allows manufacturers to tailor their approaches, ensuring that efficiency is maximized across various scenarios.
For further insights on specific applications of these nozzles in different manufacturing environments, explore nozzle selection techniques1 and material compatibility guidelines2.
Straight-through nozzles minimize pressure loss.True
The simple design of straight-through nozzles results in low pressure loss.
Self-locking nozzles are unsuitable for heat-sensitive plastics.False
Self-locking nozzles are ideal for heat-sensitive plastics, preventing backflow.
What Are the Key Factors in Determining Nozzle Size?
Choosing the right nozzle size is crucial for optimizing the injection molding process and ensuring high-quality products.
Key factors in determining nozzle size include the type of material, desired flow rate, and product specifications. Adjusting nozzle aperture and length according to these factors enhances efficiency and product quality.
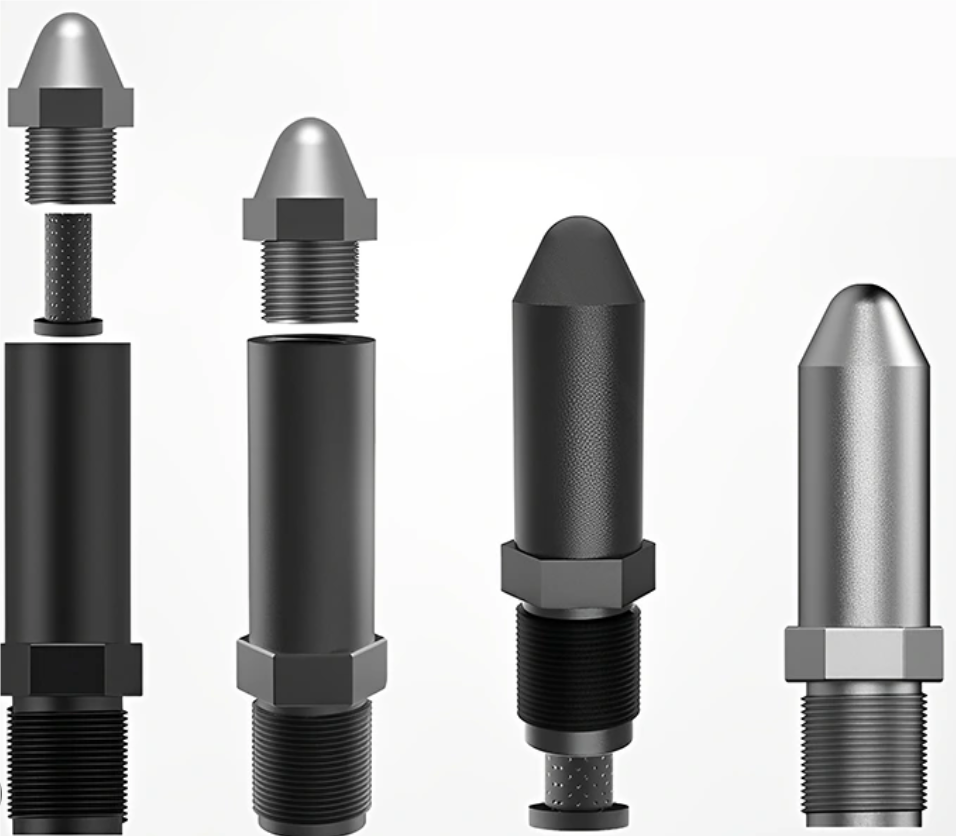
Understanding Nozzle Aperture and Flow Rate
The nozzle aperture’s size significantly impacts the plastic flow rate3 and injection pressure. A smaller aperture may increase resistance, leading to higher pressure and potential defects like burning or bubbles. Conversely, a larger aperture could cause rapid flow, complicating volume control and affecting product precision.
Determining Aperture Size
Factors such as plastic fluidity and product dimensions guide the selection of nozzle aperture:
- High Fluidity Plastics: Opt for smaller apertures to control flow and pressure.
- Low Fluidity Plastics: Larger apertures are preferable to facilitate smoother flow.
Experimentation in real-world settings often helps finalize the optimal aperture size. Employing a replaceable nozzle core design allows for quick adjustments based on varying production needs.
Balancing Nozzle Length
The nozzle length influences the plastic’s heating time4 and melting process. A longer nozzle might prolong plastic residence time, risking decomposition, while a shorter one might hinder proper melting.
Optimal Length Calculation
Typically, nozzle length ranges between 2 to 3 times its aperture. Considerations include:
- Heat-Sensitive Plastics: Shorter lengths reduce residence time, minimizing decomposition risk.
- High Viscosity Plastics: Longer lengths enhance heating, promoting better melting.
Segmented nozzle structures allow length adjustments to meet specific production needs, potentially integrating internal heating elements for improved efficiency.
Strategic Nozzle Size Adjustments
Adapting nozzle size based on material properties and production requirements can significantly boost process efficiency. Consider employing:
- Experimental Techniques: Test various configurations to identify ideal conditions.
- Modular Designs: Facilitate easy swaps or modifications to adapt to different scenarios.
By fine-tuning these elements, manufacturers can achieve optimal injection performance, enhancing product quality and reducing defects. Such adaptability is essential in navigating the complexities of diverse materials and intricate designs.
Smaller nozzle apertures increase injection pressure.True
Smaller apertures restrict flow, raising pressure and risk of defects.
Longer nozzles reduce plastic decomposition risk.False
Longer nozzles increase residence time, heightening decomposition risk.
Which Heating Methods Improve Nozzle Performance?
Achieving optimal nozzle performance in injection molding hinges on selecting the right heating methods.
The best heating methods for improving nozzle performance include resistance heating for uniformity, induction heating for precision, and hot runner systems for efficiency. Each method has unique benefits, and choosing the right one depends on specific material and production requirements.
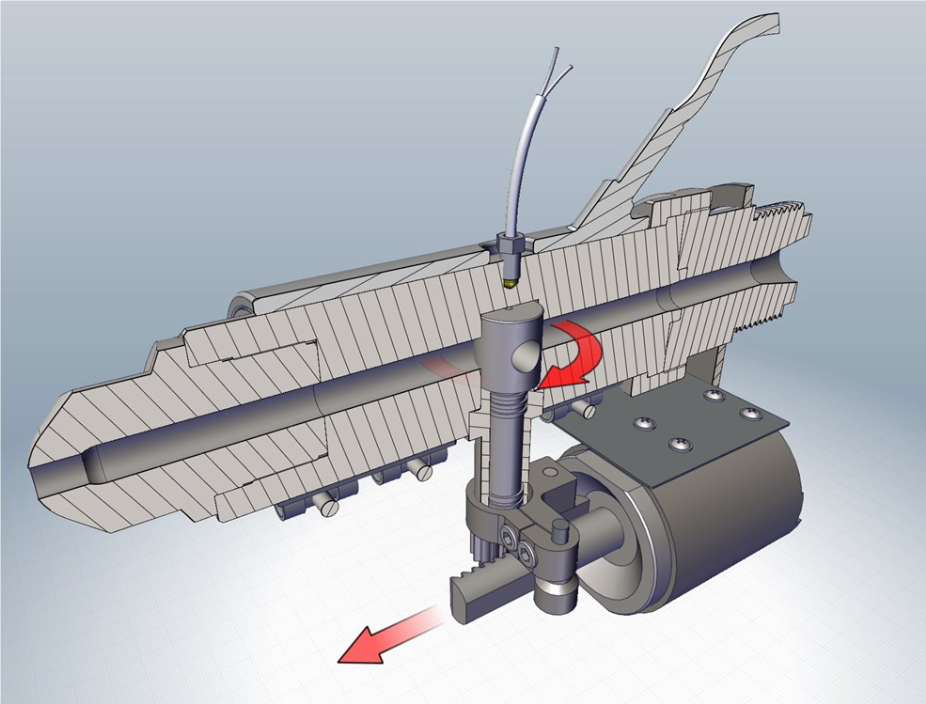
Resistance Heating
Resistance heating remains a popular choice due to its straightforward setup and cost-effectiveness. By wrapping resistance wires or integrating heating rods around the nozzle, this method ensures consistent heat distribution. Despite its simplicity, it may suffer from slower heating speeds and less accurate temperature control.
- Advantages: Low-cost setup, easy maintenance, uniformly distributed heat.
- Drawbacks: Slower heating rate, lower precision in temperature control.
To maximize effectiveness, consider combining resistance heating with advanced temperature control systems like PID (Proportional-Integral-Derivative) controllers. These controllers enhance precision by continuously adjusting the power based on real-time temperature feedback.
Induction Heating
Induction heating offers rapid and precise temperature adjustments using electromagnetic fields to induce heat directly within the nozzle. This method is especially beneficial for high-precision applications where quick response times are essential.
- Advantages: Fast heating speed, high precision in temperature control, energy efficiency.
- Drawbacks: Higher initial cost, specific material requirements for nozzles.
Implementing induction heating can significantly improve nozzle performance, particularly when dealing with heat-sensitive plastics that require strict temperature management. However, it’s crucial to ensure that the nozzle materials are compatible with induction systems.
Hot Runner Systems
The integration of hot runner systems provides superior heating efficiency by maintaining consistent temperatures across the entire nozzle. This system is ideal for high-volume production runs where maintaining quality and reducing waste are paramount.
- Advantages: High heating efficiency, uniform temperature control, reduced material wastage.
- Drawbacks: Complex system setup, higher cost of implementation.
For operations prioritizing quality and efficiency, hot runner systems offer a compelling option. When implementing this system, it’s essential to balance the benefits against the complexity and cost, ensuring it aligns with the production scale and desired outcomes.
By understanding these heating methods5 and their respective advantages and limitations, manufacturers can enhance nozzle performance, leading to improved product quality and operational efficiency. Each method’s suitability will depend largely on specific production needs and material characteristics.
Resistance heating offers high precision temperature control.False
Resistance heating is less precise in temperature control than induction.
Induction heating is suitable for heat-sensitive plastics.True
Induction heating provides precise temperature control, ideal for sensitive materials.
How to Ensure Proper Alignment and Sealing of Nozzle and Mold?
The alignment and sealing of the nozzle and mold are crucial for maintaining product quality and minimizing defects in injection molding.
Proper alignment and sealing between the nozzle and mold ensure optimal injection pressure, prevent leakage, and enhance product quality. To achieve this, employ precise centering devices and robust sealing elements. Regular maintenance and adjustments are essential to sustain performance.
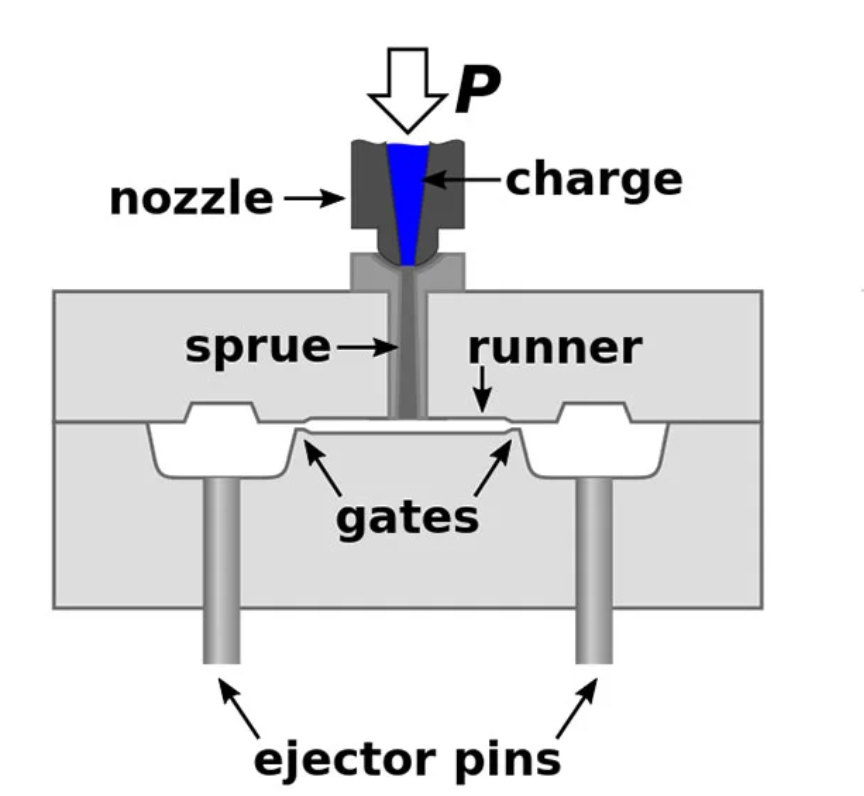
Importance of Alignment
The alignment between the nozzle and mold is pivotal in ensuring uniform plastic flow during injection molding. Misalignment can lead to uneven distribution of material, impacting the dimensional accuracy and appearance of the final product. Positioning devices, such as positioning pins6 and blocks, are commonly used to maintain this precision.
Impact on Product Quality
When the nozzle and mold are not properly aligned, plastic can deviate during the injection process, leading to defects such as warping or incomplete filling. This can significantly affect not only the visual appeal but also the functional integrity of the product.
Optimizing Alignment
To optimize alignment, regular checks and adjustments should be conducted. Utilizing advanced technologies like laser alignment systems7 can enhance accuracy by providing real-time feedback during setup.
Enhancing Sealing Effectiveness
The sealing between the nozzle and mold is another critical factor that influences injection pressure and material flow. Inadequate sealing may cause leakage, reducing the efficiency of the injection process.
Sealing Elements
Sealing rings and pads are often employed to enhance the sealing performance. Materials used for these elements should withstand high pressures and temperatures without degradation. Regular inspection and timely replacement of worn sealing components are necessary to maintain effectiveness.
Design Considerations
Incorporating a well-designed sealing structure in the nozzle and mold interface is crucial. This includes analyzing the compatibility of materials used in both the nozzle and the sealing elements to prevent wear and tear.
Maintenance and Adjustments
Routine maintenance is vital for sustaining both alignment and sealing effectiveness. This involves:
- Regular inspections for wear and tear on sealing components.
- Calibration of positioning devices to ensure they remain effective.
- Adoption of automated systems for consistent monitoring of alignment and sealing integrity.
By prioritizing these aspects, manufacturers can significantly reduce production defects, leading to higher quality products and increased operational efficiency.
Misalignment causes uneven material distribution.True
Misalignment impacts dimensional accuracy, leading to defects.
Sealing elements do not affect injection pressure.False
Proper sealing prevents leakage, ensuring optimal injection pressure.
Conclusion
By carefully considering nozzle type, size, heating, and mold coordination, engineers can significantly improve injection molding efficiency and product quality.
-
Discover tailored approaches for different nozzle types.: Machine nozzles today can provide a variety of functions, including filtering, mixing, and shut-off of melt flow. ↩
-
Learn about matching nozzles with materials for optimal results.: The two materials must be compatible with each other, which means they can be melted and injected into the mold at the same time. They must … ↩
-
Explains how nozzle size affects flow rate and product quality.: This parameter is critical for ensuring the material fills the mold cavity effectively, influencing the quality of the final product. ↩
-
Describes how nozzle length impacts heating and plastic decomposition.: The purpose of the nozzle body and tip is to provide a flow path for the molten plastic from the end of the barrel to the sprue bushing of the mold. ↩
-
Explore comprehensive insights on various nozzle heating methods.: The main types of hot runner nozzle heating methods include Embedded Heat Sources (Brazing) or External Heat Sources (Sleeves and Coil). So the … ↩
-
Learn how positioning pins ensure precise alignment.: Injection Mold Alignment Pins for desktop injection molding machines. These small, DIY … ↩
-
Discover how laser systems enhance alignment accuracy.: Continuously sweeping lasers and live data output create a powerful combination to align injection molding machines up to 70% faster than traditional methods. … ↩