Imagine transforming your manufacturing process with the magic of insert molding. It’s like bringing your design dreams to life, blending multiple materials into one seamless creation.
Insert molding improves injection processes by embedding components in one mold for complex designs and enhanced durability, reducing assembly costs and production time, thus streamlining modern manufacturing.
While the basics of insert molding offer clear advantages, I’ve found that its real magic shines through when you see it in action. The first time I used insert molding, it felt like fitting together pieces of a puzzle with no missing parts. Imagine shaving off precious minutes from production times while boosting the quality of your products – it’s like hitting the jackpot in efficiency!
I remember working on a project where the design needed both aesthetic appeal and structural integrity. By embedding different materials into a single mold, we achieved a level of durability and complexity that was previously unimaginable. This not only streamlined the production process but also resulted in a product that stood out in the market for its innovative design.
Insert molding reduces assembly costs.True
Insert molding combines components in one mold, reducing separate assembly.
Insert molding decreases product durability.False
Insert molding actually enhances product durability by integrating materials.
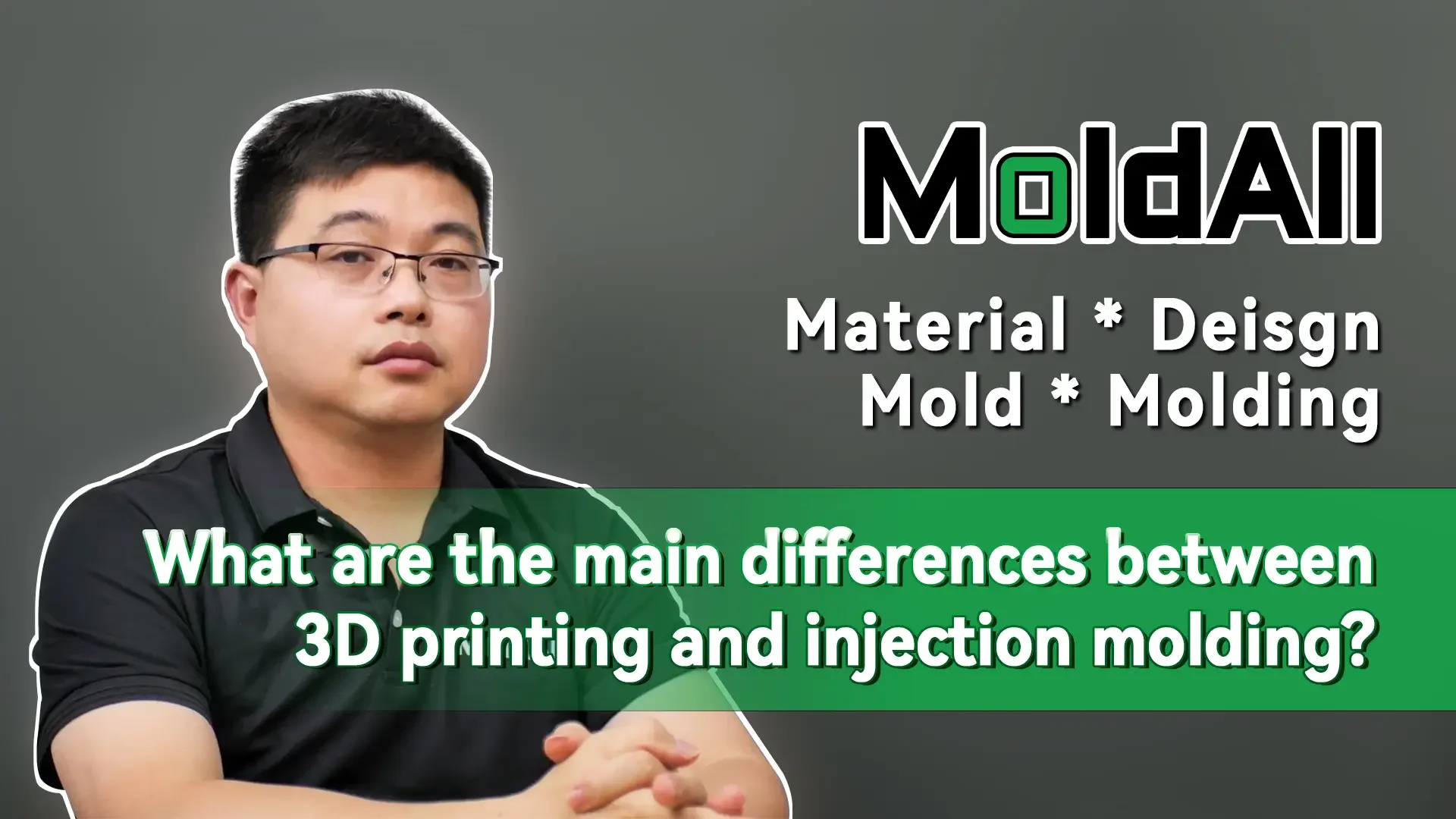
- 1. What is Insert Molding and How Does It Work?
- 2. Why Choose Insert Molding for Your Product Designs?
- 3. How Does Insert Molding Compare to Overmolding?
- 4. What Applications Are Best Suited for Insert Molding?
- 5. What Materials Can Be Used in Insert Molding?
- 6. How Can Insert Molding Improve Product Design Efficiency?
- 7. Conclusion
What is Insert Molding and How Does It Work?
Ever wondered how your sleek gadgets seamlessly blend metal and plastic? Enter the fascinating world of insert molding, where these two worlds collide to create magic!
Insert molding involves encasing metal inserts in plastic within a mold, enhancing part strength and reducing assembly time by creating a single, cohesive component.
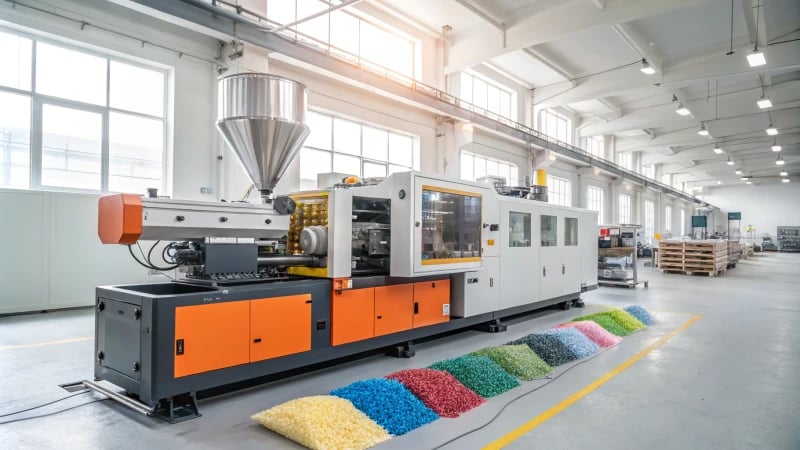
Understanding Insert Molding
Have you ever held a gadget in your hand and marveled at how the metal and plastic parts just seem to fit together perfectly? That’s the magic of insert molding—a technique I’ve come to appreciate deeply in my journey through product design. Imagine you’re building a jigsaw puzzle, but instead of pieces, you’re embedding inserts like metal into an injection mold. Then, like pouring syrup over pancakes, molten plastic envelops these inserts, creating a seamless, integrated part. This process isn’t just about making something that looks good; it’s about crafting components that stand up to wear and tear while reducing the hassle of assembly later on.
How Insert Molding Works
I remember the first time I watched the insert molding process in action—it was like witnessing alchemy! The operation begins with positioning the inserts1 securely in a mold cavity. Once everything’s in place, molten plastic floods in, wrapping around each insert like a warm embrace. After it cools, out pops a single, unified piece ready for use. This approach doesn’t just cut down on labor costs; it boosts the durability and integrity of each part.
Advantages of Insert Molding
- Reduced Assembly: It’s a bit like having a self-cleaning kitchen—less work and more efficiency!
- Enhanced Strength: With everything fused together, the final product can withstand much more stress.
- Design Flexibility: The ability to combine various materials opens up endless possibilities for creativity.
Applications in Various Industries
Insert molding is like the unsung hero in many industries:
Industry | Common Applications |
---|---|
Automotive | Engine components, electrical connectors |
Consumer Electronics | Circuit boards, housing for electronics |
Medical Devices | Surgical tools, device housings |
Aerospace | Complex assemblies needing durability |
I’ve seen firsthand how this manufacturing technique2 supports precision and integration across these demanding fields.
Key Considerations in Design
When designing for insert molding, there are a few things I’ve learned to keep in mind:
- Material Compatibility: It’s crucial to ensure that your insert materials will bond well with the plastic you’ve chosen.
- Insert Placement: Securing those inserts is key—they need to stay put when the plastic is injected.
- Thermal Expansion: Different materials expand at different rates, so it’s important to account for this.
These considerations can make all the difference in the success of your insert molding process3. Whether you’re crafting a complex component or a simple connector, paying attention to these details can help you achieve the best results.
Insert molding reduces post-production assembly costs.True
Parts are fully assembled in the mold, reducing labor costs.
Insert molding is unsuitable for complex parts.False
It is ideal for complex parts, integrating multiple materials.
Why Choose Insert Molding for Your Product Designs?
Imagine being able to create a product that not only looks sleek but is also built to withstand the test of time. That’s the magic of insert molding.
Choose insert molding for its enhanced durability, design flexibility, and cost reduction, integrating components seamlessly for innovative designs and efficient manufacturing.
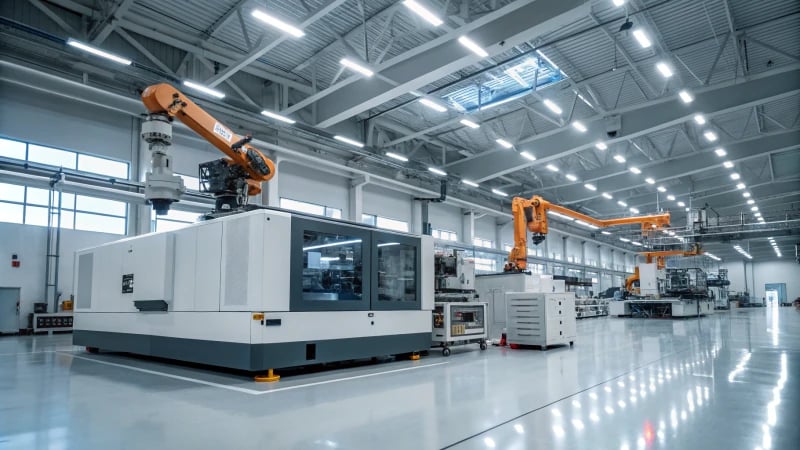
Enhanced Structural Integrity
I remember working on a project where our components were constantly failing under pressure. That’s when I discovered insert molding. By embedding metal inserts4 directly into plastic, we transformed our design’s durability. This technique allowed our products to endure higher mechanical loads, solving a problem that had been haunting us.
Design Flexibility
With insert molding, I felt like a kid in a candy store. The ability to integrate multiple functions into a single component is a game changer. Imagine not having to worry about adding extra parts. It was liberating to include threads and even electronics within the plastic mold, leading to innovative and simplified designs.
Cost Efficiency
Initially, I was skeptical about the tooling costs. But soon, the long-term savings became evident. By reducing parts and assembly steps, we cut labor costs and minimized assembly errors, which had been a hidden expense in our operations. This method proved to be a financially sound decision.
Benefit | Description |
---|---|
Structural Integrity | Embeds metal for increased strength under mechanical stress |
Design Flexibility | Integrates multiple functions, reducing part count and simplifying designs |
Cost Efficiency | Lowers assembly costs by minimizing labor and potential for errors |
Material Versatility
Insert molding is like having a palette of materials at my disposal. The ability to mix materials with different properties allows me to craft components that can meet specific needs. Whether it’s pairing heat-resistant metal with flexible plastic, the possibilities are endless.
Production Efficiency
The time saved in assembly is significant. Insert molding streamlines production, making it perfect for mass production scenarios where throughput rates are critical. I’ve seen firsthand how this efficiency boosts our output without compromising quality.
Improved Product Aesthetics
As a designer, aesthetics matter immensely. Insert molding provides control over the final appearance, allowing for smoother finishes and more appealing designs. This is particularly crucial when creating consumer-facing products.
By embracing these benefits, I’ve been able to make informed decisions that align with our project goals. It’s about more than just improving performance; it’s about optimizing cost-efficiency and pushing the boundaries of innovation. Insert molding has truly been a transformative tool in my design arsenal.
Insert molding enhances structural integrity.True
By embedding metal inserts into plastic, products withstand higher stress.
Insert molding increases assembly costs.False
It reduces part count and labor, lowering overall assembly expenses.
How Does Insert Molding Compare to Overmolding?
Ever found yourself torn between insert molding and overmolding for your next project?
Insert molding involves placing a component in a mold before plastic injection, while overmolding adds layers to an existing part. Each suits different manufacturing needs.
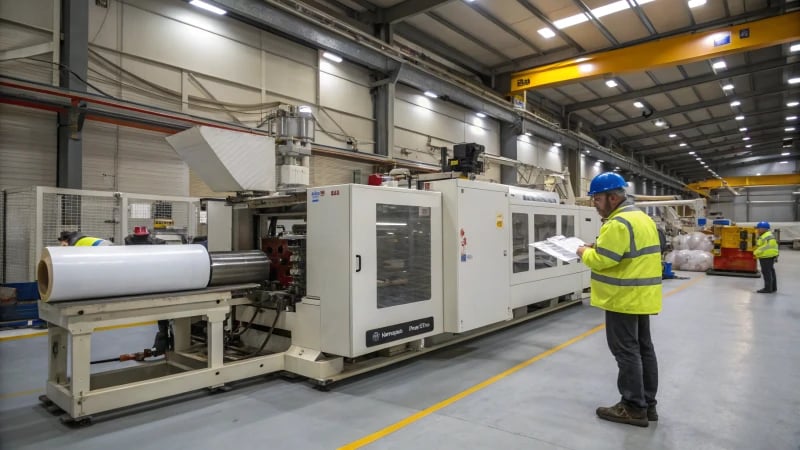
Let me tell you about the time I was tasked with deciding between insert molding and overmolding for a new gadget design. It felt like choosing between two beloved tools in my workshop. Each has its unique strengths, and understanding these can make a huge difference in achieving that perfect balance between function and form.
Understanding Insert Molding
In one of my past projects, we needed to integrate metal components seamlessly with plastic casings. That’s when insert molding came to the rescue. It’s all about placing a pre-formed piece, like a metal connector, into the mold before injecting the plastic. This technique not only saved us assembly time but also gave the final product a sturdy, reliable feel.
Advantages:
- Strong Bond: We achieved a secure fusion between materials, which was crucial for durability.
- Reduced Assembly Time: By merging parts during the molding, we cut down on production steps.
- Material Flexibility: We could use a variety of inserts—metal, ceramics, you name it!
Advantages | Description |
---|---|
Strong Bond | Ensures materials are securely fused together |
Reduced Assembly Time | Combines parts during the molding process |
Material Flexibility | Incorporates metal, ceramics, or other plastic inserts |
Exploring Overmolding
Now, overmolding is something I used for another project—a line of ergonomic grips for tools. This process involves adding layers over an existing piece, which allowed us to add soft-touch surfaces and vibrant color contrasts. It really enhanced the user experience, both in look and feel.
Advantages:
- Enhanced Ergonomics: Our tools were more comfortable to hold thanks to the added grip.
- Aesthetic Improvements: The contrasting colors added a visual flair that customers loved.
- Versatile Design: Overmolding opened up creative possibilities for unique shapes and material blends.
Advantages | Description |
---|---|
Enhanced Ergonomics | Provides better grip and comfort |
Aesthetic Improvements | Adds visual appeal with contrasting colors |
Versatile Design | Allows unique shapes and material combinations |
Comparing Both Methods
When it comes down to choosing between insert molding and overmolding, I always start by considering what the project truly demands. If strong bonds and minimized assembly are priorities, insert molding is my go-to. But if the design calls for ergonomic features or visual appeal, overmolding often wins out.
I’ve seen both methods work wonders in diverse applications like medical devices5 that need both structural integrity and user comfort. By understanding these techniques’ strengths, I can tailor my approach to align with the product’s goals and create solutions that truly shine.
Insert molding reduces assembly time and cost.True
Insert molding combines parts during the molding process, saving time.
Overmolding is unsuitable for ergonomic improvements.False
Overmolding enhances grip and ergonomics, ideal for tool handles.
What Applications Are Best Suited for Insert Molding?
Ever wondered how those sleek gadgets or robust car parts come to life? Let me take you on a journey through insert molding, a technique that fuses metal and plastic seamlessly for top-notch durability and design.
Insert molding is ideal for applications requiring robustness, such as automotive parts, medical devices, and consumer electronics, combining metal inserts with plastic for enhanced durability.
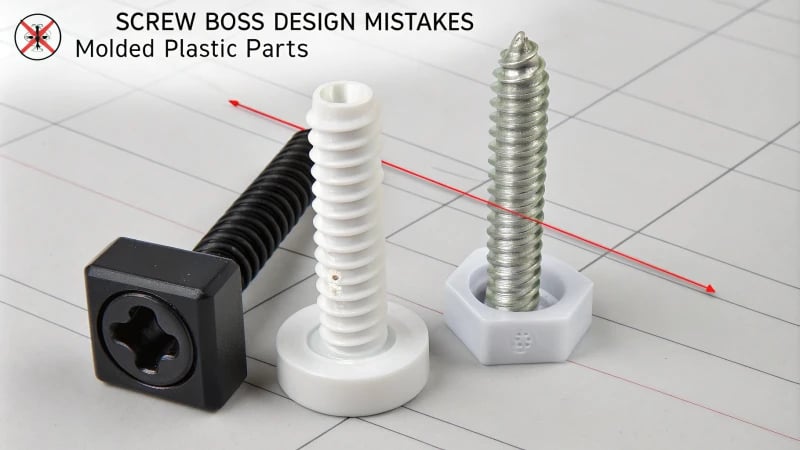
Automotive Applications
As I delved into the world of automotive design, I realized how crucial durability is for parts like gears and bushings. In the automotive industry6, insert molding ensures these components withstand the rigors of daily use. The technique precisely integrates metal within plastic, offering both longevity and resilience—something I’ve seen transform the reliability of vehicles over time.
Medical Devices
A friend of mine who designs medical tools once shared how insert molding revolutionized their work on surgical instruments. This process allows for complex designs that integrate metal parts, ensuring safety and precision. In medical settings, every detail matters; insert molding supports this need by enhancing device functionality and biocompatibility.
Consumer Electronics
Remember that moment when you unboxed your new smartphone, admiring its sleek, compact design? Insert molding is the unsung hero here. It helps create sturdy housings for connectors and sensors in electronics. For folks like me who are all about optimizing space without compromising integrity, this method is a game-changer—especially in gadgets where every millimeter counts.
Comparison with Overmolding
I’ve often compared insert molding with overmolding7 in my projects. While both are brilliant for material integration, insert molding involves placing metal inserts into the mold before injecting plastic. In contrast, overmolding starts with a molded substrate followed by another layer. This distinction helps me pick the best method based on specific project needs.
Benefits in Manufacturing
From my experience, insert molding streamlines production by combining multiple processes into one seamless operation. This not only slashes assembly time and costs but also enhances product performance. The efficiency gains—like reduced labor costs and increased output—are reasons why I vouch for this technology.
Application | Benefits of Insert Molding |
---|---|
Automotive | Enhanced durability, resistance to wear, precise integration |
Medical Devices | High precision, biocompatibility, intricate design capabilities |
Consumer Electronics | Compact design, improved product integrity, optimized space utilization |
Exploring these applications has deepened my appreciation for how insert molding can elevate product designs to new heights. For anyone in manufacturing or product design, understanding its strengths is not just helpful—it’s essential for achieving superior results.
Insert molding is ideal for medical devices.True
It allows high precision and biocompatibility, crucial for medical tools.
Overmolding is identical to insert molding.False
Insert molding integrates pre-fabricated inserts; overmolding adds layers.
What Materials Can Be Used in Insert Molding?
Ever wondered what goes into making those robust, intricate parts in your favorite gadgets?
Insert molding uses materials like thermoplastics, thermosets, metals, and ceramics. Thermoplastics offer design flexibility; metals provide strength. Material choice depends on application requirements.
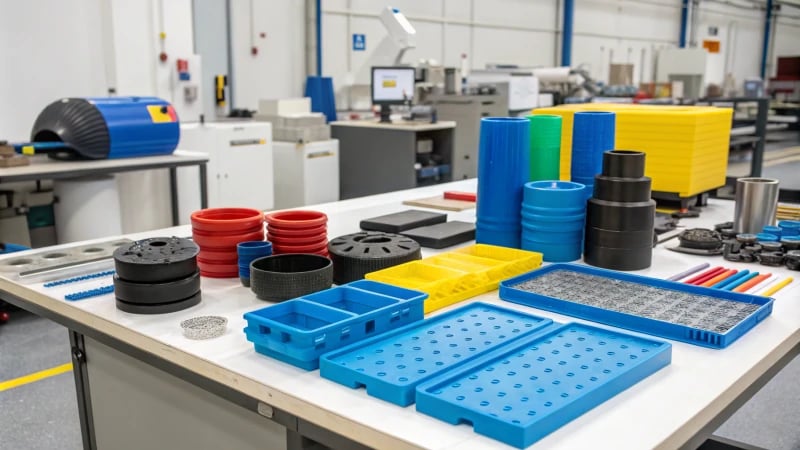
Thermoplastics in Insert Molding
Thermoplastics are often my go-to in insert molding because of their versatility and ease of use. I remember working on a project for a new line of consumer electronics8 where we needed a material that could take a beating but still look sleek. Acrylonitrile Butadiene Styrene (ABS) was perfect for this due to its toughness and ability to resist impact. It’s like finding that perfect pair of shoes that are both stylish and sturdy!
Then there was this time we had to design a mechanical component that needed to withstand a lot of wear and tear. Nylon (Polyamide) came to the rescue. Its abrasion resistance and strength were exactly what we needed. Think of it like choosing a reliable vehicle that can handle rough terrains.
And don’t get me started on Polycarbonate (PC)! Its high impact resistance and clarity make it a favorite for optical lenses and protective gear. It’s like having a transparent shield that’s tough as nails!
Thermoplastics generally allow flexibility in design and cost-effective production, but they may not be suitable for high-temperature applications.
Thermosets in Insert Molding
Thermosets are another category I frequently explore, especially when high heat resistance is non-negotiable. Picture this: working on automotive parts9 that had to endure extreme conditions. Phenolic Resins offered the heat resistance we needed.
On another project involving electrical components, Epoxy Resins proved invaluable due to their adhesive properties and strength. They remind me of those strong glues that hold everything together, no matter what.
Thermosets tend to be more rigid but offer superior heat and chemical resistance compared to thermoplastics.
Metals and Ceramics in Insert Molding
When projects call for serious strength and durability, metals or ceramics are my top picks. I recall integrating brass into a component to enhance its structural integrity — it was like adding a backbone to the design.
In the realm of medical devices10, ceramics stand out for their hardness and thermal resistance. They’re akin to an impenetrable fortress that safeguards precious life-saving technologies.
Material Selection Table
Material | Key Properties | Applications |
---|---|---|
ABS | Impact resistance | Consumer electronics |
Nylon | Abrasion resistance | Mechanical components |
Polycarbonate | Impact resistance | Optical lenses |
Epoxy Resin | Adhesive strength | Electrical components |
Phenolic Resin | Heat resistance | Automotive parts |
Metals | Structural integrity | Wear-resistant components |
Ceramics | Thermal resistance | Medical devices |
Selecting the right material feels much like curating the perfect playlist. It’s about balancing durability, cost, and application-specific needs to create a harmonious design outcome that hits all the right notes.
ABS is suitable for high-temperature applications.False
ABS is not suitable for high-temperature applications due to its thermoplastic nature.
Phenolic resins provide excellent heat resistance.True
Phenolic resins offer superior heat resistance, making them ideal for automotive parts.
How Can Insert Molding Improve Product Design Efficiency?
Imagine a world where product design is not just efficient but also feels like an art form. Enter insert molding, a game-changer for designers like me.
Insert molding improves product design efficiency by integrating components in a single process, reducing assembly time and costs, while enhancing durability and flexibility.

What is Insert Molding?
Let me take you back to the first time I discovered insert molding. Picture this: a cluttered desk with sketches scattered around, and a looming deadline. I needed a way to streamline my design process without compromising on quality. That’s when I stumbled upon insert molding. Essentially, it’s a process where you place preformed parts, or inserts, into a mold before injecting plastic to encapsulate them. This technique seamlessly integrates metal and plastic, enhancing the overall functionality of a product.
Benefits to Design Efficiency
- Reduced Assembly Time:
Combining parts into a single operation is like solving a complex puzzle with fewer pieces. Insert molding cuts down assembly steps, which means faster production cycles. This was a lifesaver during project crunch time. - Cost Efficiency:
Imagine having fewer components to worry about—less labor, fewer materials, and ultimately, cost savings. This process is ideal for mass production11 scenarios. - Enhanced Durability:
The first time I held a product made with insert molding, I was impressed by its robustness. The encapsulation process ensures inserts are securely held, increasing the product’s lifespan and reliability.
Applications in Various Industries
Insert molding’s versatility has allowed me to explore new territories across different sectors:
Industry | Application Example |
---|---|
Consumer Electronics | Connectors and housings |
Automotive | Engine components |
Medical Devices | Surgical tools |
The capability to incorporate complex geometries12 lets designers like me push the boundaries of innovation.
Technological Advancements
Thanks to advancements in CAD and simulation tools, predicting and optimizing insert molding outcomes has become more accessible. This means fewer design iterations and greater precision. Meeting functional requirements13 has never been easier.
Design Flexibility and Aesthetics
Insert molding allows for the blending of different materials. This gives designers the freedom to boost product aesthetics without sacrificing functionality. Sleek designs with minimal visible joints are now within reach.
Exploring these benefits has empowered designers like me to innovate efficiently, ensuring our products not only meet but exceed industry standards.
Insert molding reduces assembly time by 50%.False
While insert molding reduces assembly time, the exact percentage varies.
Insert molding improves product durability.True
Encapsulation secures inserts, enhancing product lifespan and reliability.
Conclusion
Insert molding enhances injection processes by integrating multiple materials into a single part, improving durability, reducing assembly costs, and enabling complex designs for various industries.
-
Discover different types of inserts used in insert molding to better understand material selection. ↩
-
Learn about how insert molding can improve manufacturing efficiency and part quality. ↩
-
Explore critical design considerations that ensure successful insert molding projects. ↩
-
Explore how metal inserts enhance durability and functionality in molded parts. ↩
-
Understand why these techniques are vital for medical device innovation. ↩
-
Explore how insert molding is revolutionizing automotive component manufacturing with its durability and precision integration advantages. ↩
-
Understand the key differences between insert molding and overmolding to select the best method for your production needs. ↩
-
Explore how ABS’s toughness benefits consumer electronics by providing durable casings that withstand impact. ↩
-
Learn why phenolic resins are essential in automotive parts for their superior heat resistance. ↩
-
Discover how ceramics enhance medical devices with their hardness and thermal properties. ↩
-
Understanding how insert molding benefits mass production can help optimize manufacturing processes, reducing costs and time. ↩
-
Exploring examples of complex geometries can inspire innovative design solutions and improve product functionality. ↩
-
Learning how insert molding satisfies functional requirements ensures that products are both durable and efficient. ↩