Dark spots ruining your beautifully molded products can feel like an uphill battle, can’t they? Let’s dive into some practical solutions together!
To effectively eliminate dark spots on injection molded products, ensure the purity of raw materials, maintain and clean machinery regularly, optimize process parameters, and uphold stringent environmental controls.
These initial tips are just the beginning. Dive deeper with me into each solution to refine your production process!
Contaminated raw materials cause dark spots.True
Impurities in raw materials lead to color defects in products.
How Do Raw Material Contaminants Cause Dark Spots?
Ever wonder how tiny contaminants in raw materials can lead to unsightly dark spots on your products?
Raw material contaminants cause dark spots by introducing impurities that affect the color and quality of injection molded products. Ensuring purity through rigorous inspection and proper storage is key to preventing these blemishes.
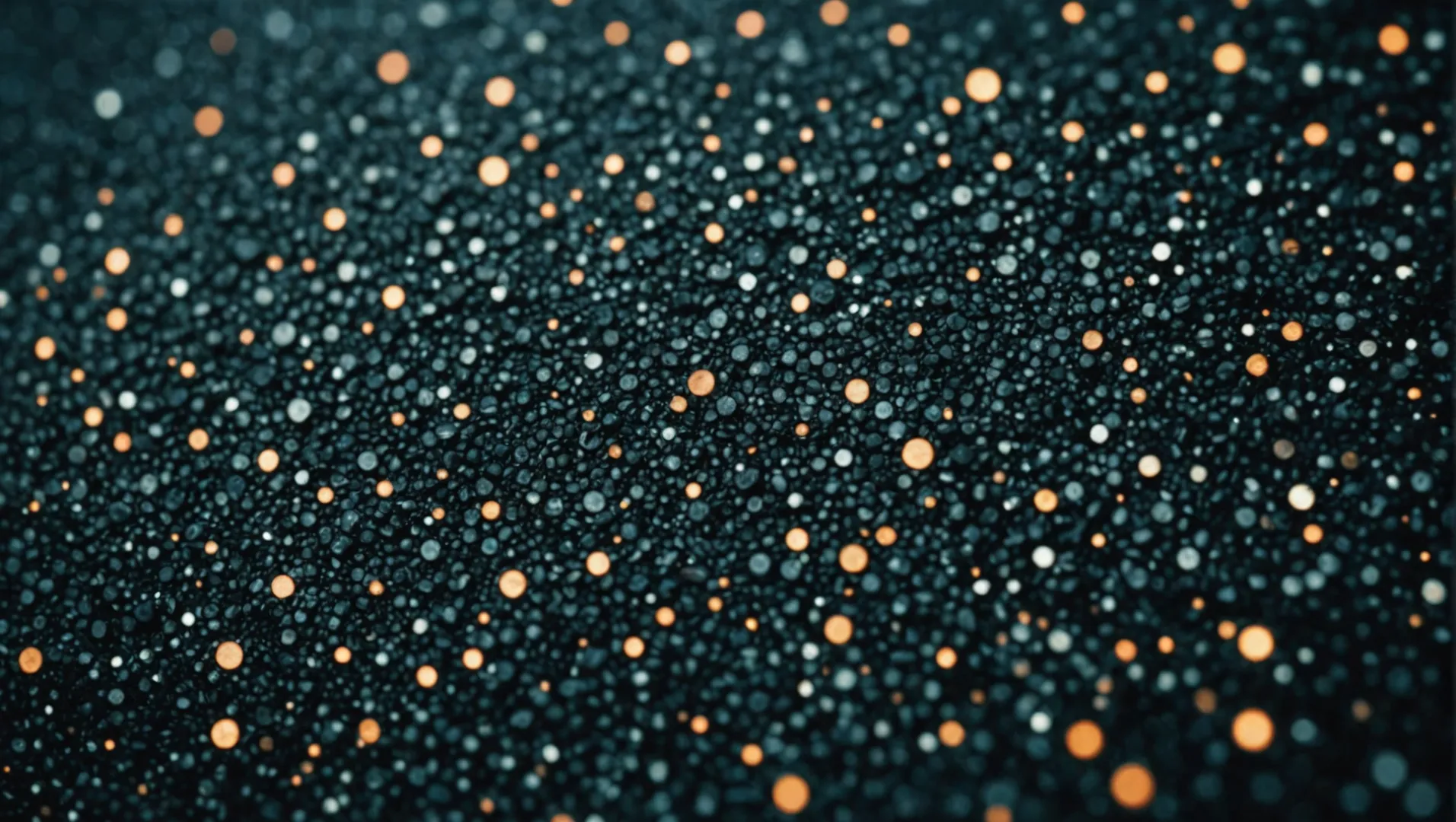
The Role of Raw Material Purity
The importance of raw material purity cannot be overstated when it comes to injection molding. Contaminants such as dirt, dust, or degraded particles can integrate into the plastic during processing, leading to visible dark spots. To combat this, companies should source their materials from reputable suppliers and conduct thorough inspections on each batch.
Implementing a robust quality control process can help identify contaminants before they enter the production cycle. This includes both visual inspections and advanced testing methods such as spectroscopy to detect even the smallest impurities.
Storage Conditions and Their Impact
Improper storage can also lead to contamination. Raw materials should be kept in a dry, cool, and ventilated area to prevent exposure to moisture and heat, which can degrade the material’s integrity and introduce contaminants. Using airtight containers and regularly monitoring storage conditions can help maintain material quality.
Maintaining a clean storage environment minimizes the risk of external contaminants entering the raw materials. For facilities dealing with bulk storage, implementing automated monitoring systems can ensure conditions remain optimal without continuous manual oversight.
Cleaning and Filtering Procedures
Even with the best precautions, some contamination may still occur. Implementing sieving or filtering processes can remove unwanted particles from the raw materials before they are used in production. For companies using recycled materials, rigorous screening and processing are essential to ensure that these materials meet the required standards.
A practical approach is to use a layered filtration system, which progressively removes particles of different sizes, ensuring only the purest material enters the production process.
Case Study: Tackling Contaminants in Real-Time
Consider a manufacturer facing persistent issues with dark spots in their products. By introducing a comprehensive raw material inspection protocol, coupled with state-of-the-art filtering technology, they significantly reduced the incidence of defects.
Additionally, by training staff to recognize signs of contamination early and adopting new storage solutions1, they improved overall product quality.
While contaminants pose a challenge, understanding their impact and implementing these strategies can vastly improve injection molding outcomes.
Contaminants cause dark spots in injection molded products.True
Contaminants introduce impurities affecting color and quality.
Proper storage prevents contaminants in raw materials.True
Storing materials in cool, dry places avoids contamination.
What Are the Best Practices for Machine Maintenance?
Ensuring optimal machine maintenance is crucial in preventing defects in injection molded products, such as unsightly black spots.
Best practices for machine maintenance include regular cleaning, monitoring process parameters, and ensuring uniform heating to prevent defects.

Regular Cleaning and Inspection
One of the cornerstones of effective machine maintenance is a rigorous cleaning routine2. This involves:
- Thorough cleaning of machine components: Regularly clean the barrel, screw, and nozzle using specialized cleaning agents. This prevents the buildup of carbides and oil stains that can lead to defects.
- Inspection of heating elements: Consistently check the heating system to ensure even heat distribution and avoid local overheating, which can result in dark spots.
Monitoring Process Parameters
Adjusting and monitoring process parameters is another essential practice:
- Temperature Control: Lower the barrel and nozzle temperatures slightly to prevent plastic decomposition.
- Screw Speed and Back Pressure: Reduce these to minimize shear stress and friction, which can cause excessive heat and dark spots.
- Injection and Holding Time: Optimize these times to prevent the material from lingering too long in the barrel or mold, reducing the risk of overheating.
Parameter | Recommended Adjustment |
---|---|
Barrel Temperature | Lower based on material needs |
Screw Speed | Reduce for less shear stress |
Injection Time | Adjust for quicker cycles |
Ensuring Uniform Heating
Uniform heating is critical for maintaining product quality:
- Regular Calibration: Ensure that all temperature sensors are accurately calibrated.
- Heat Distribution Checks: Perform regular checks to confirm uniform heat distribution across the machine’s heating zones.
By implementing these best practices, operators can significantly reduce the occurrence of defects like black spots in their injection molded products. These maintenance strategies not only enhance product quality but also extend the lifespan of machinery, promoting cost-efficiency and sustainability in manufacturing.
Regular cleaning prevents black spots in products.True
Cleaning removes buildup that causes defects like black spots.
Lowering screw speed increases shear stress.False
Reducing screw speed actually minimizes shear stress and friction.
How Can Mold Design Affect Product Quality?
Mold design plays a pivotal role in determining the quality of injection molded products. A well-crafted mold ensures precision, efficiency, and defect-free outputs.
Effective mold design minimizes defects, ensures uniformity, and enhances product quality by optimizing material flow, cooling rates, and ventilation during the molding process.
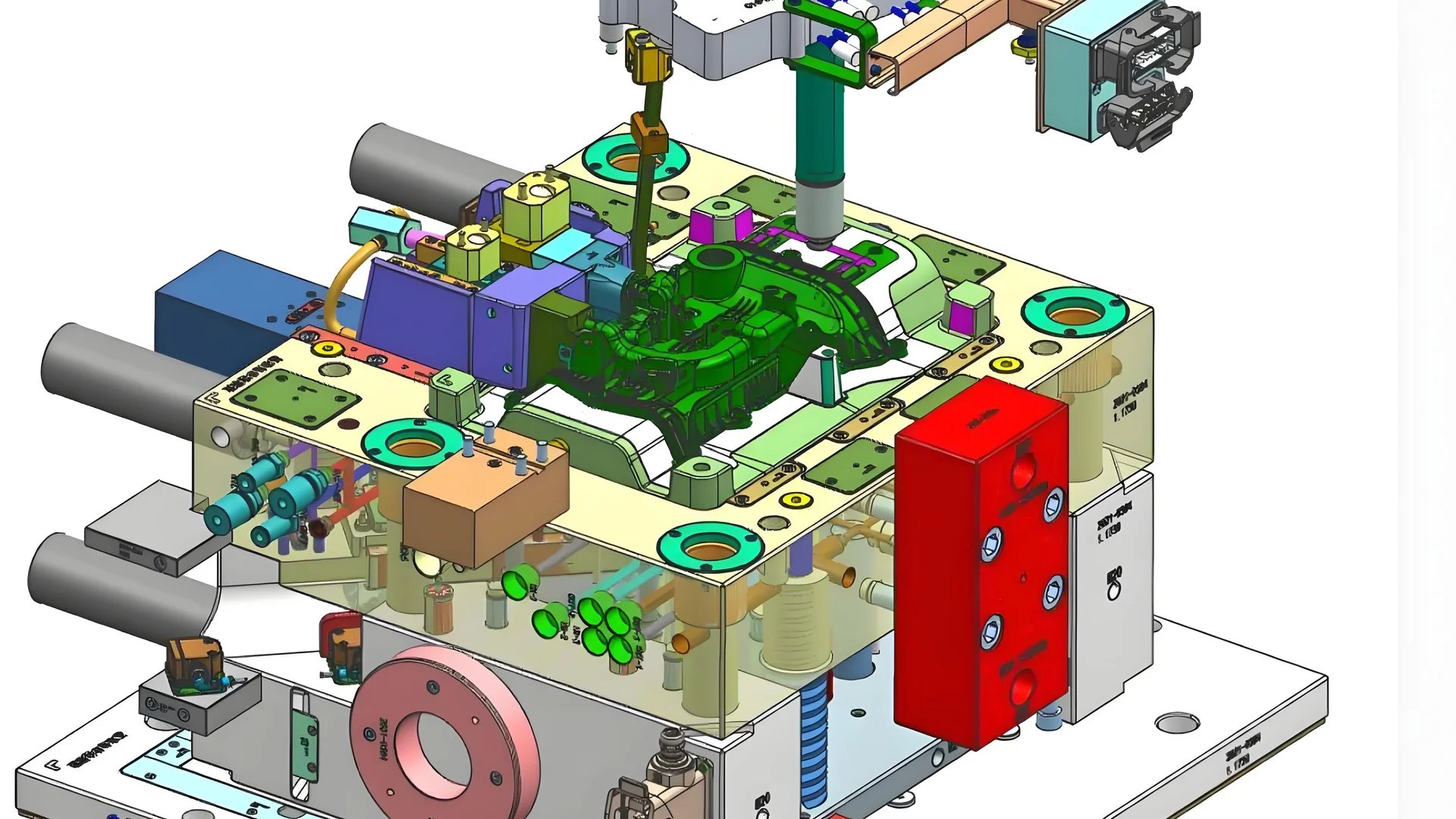
Understanding the Role of Mold Design
Mold design is critical in ensuring that the final product meets quality standards. A well-designed mold facilitates optimal material flow3, reducing the likelihood of defects such as warping, voids, or inconsistent textures. By controlling factors like the gate location, runner system, and cavity layout, designers can significantly impact how the molten plastic fills the mold.
Addressing Cooling and Ventilation
One crucial aspect of mold design is the cooling system4. Efficient cooling systems reduce cycle times and improve surface finish by preventing issues such as sink marks or internal stresses. Moreover, proper ventilation prevents air traps, which can lead to burn marks or incomplete fillings.
Precision and Material Considerations
Precision in mold design is paramount, especially for products requiring tight tolerances. For instance, precision molds ensure that all parts fit together perfectly without excessive machining post-production. Additionally, selecting the right materials for the mold itself can enhance longevity and resistance to wear.
High-quality steel or alloys are often chosen for their durability and ability to withstand high pressures and temperatures.
Maintaining Mold Integrity
Regular maintenance of molds can prevent wear that leads to defects like flashing or black spots. Over time, wear can alter the flow paths within the mold, resulting in uneven material distribution. Employing techniques like surface treatments5 can extend a mold’s life and maintain product consistency.
Balancing Costs with Quality
While intricate designs can drive up initial costs, they often lead to lower long-term production costs by reducing defect rates and material waste. Thus, investing in advanced mold designs not only improves quality but also enhances overall production efficiency.
Mold design affects material flow efficiency.True
Strategic mold design enhances how molten plastic fills the mold.
Poor cooling systems reduce surface quality.True
Inefficient cooling leads to defects like sink marks and stresses.
Why Is Environmental Control Crucial in Injection Molding?
In the realm of injection molding, maintaining an optimal environment is key to producing flawless products. But why is this control so essential?
Environmental control in injection molding is vital to prevent contamination, ensure consistent production quality, and reduce defects such as black spots. By maintaining clean and regulated conditions, manufacturers can enhance product integrity and minimize waste.
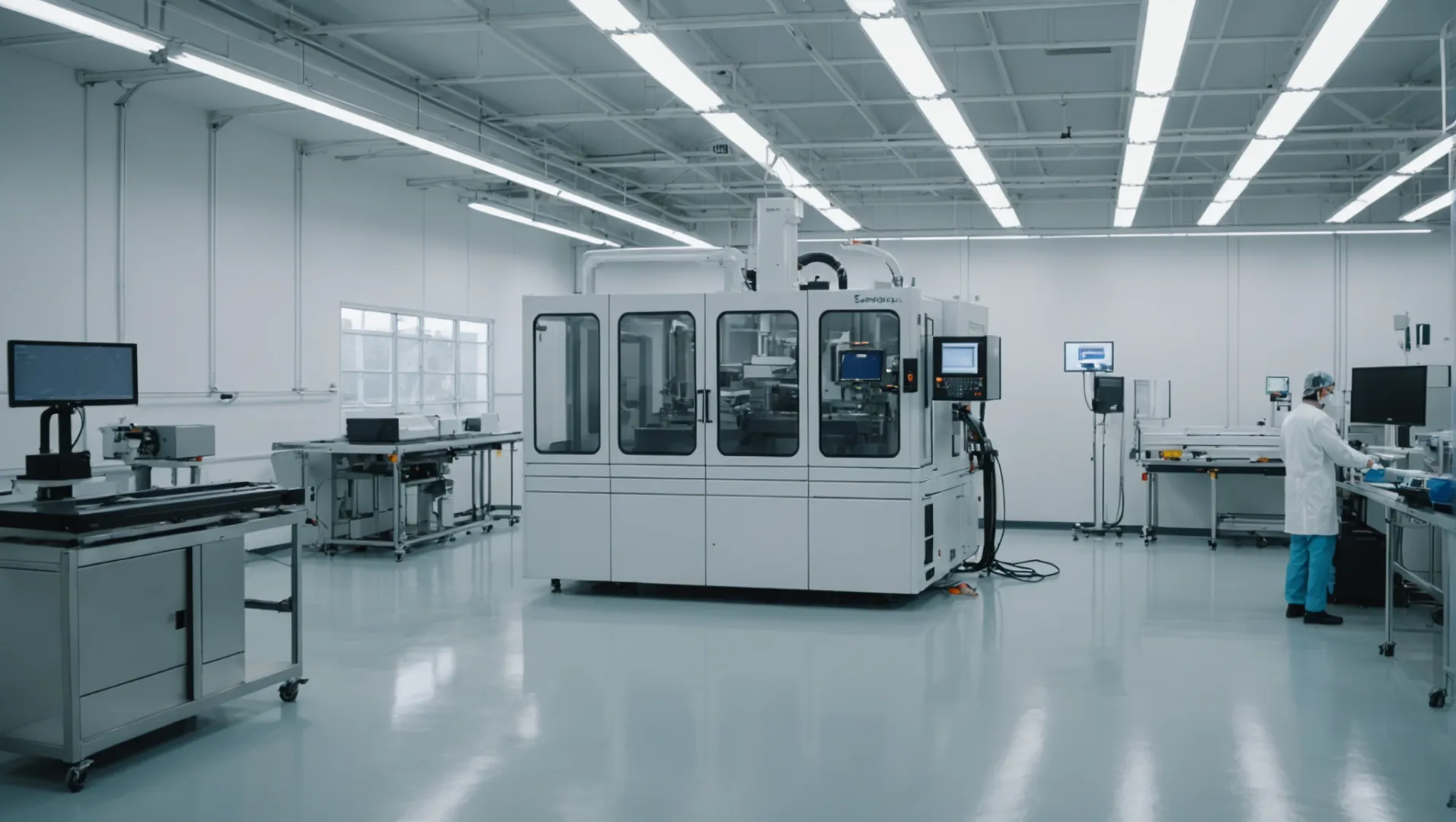
Ensuring Cleanliness and Reducing Contamination
One of the most significant challenges in injection molding is preventing contamination, which can lead to defects like black spots. By maintaining a clean production environment, you can significantly reduce the introduction of dust, oil, and other impurities that may affect the final product. For instance, using air purification systems and routinely cleaning floors and equipment are effective strategies.
Temperature and Humidity Control
Controlling temperature and humidity is crucial as it affects both the material properties and the molding process. Fluctuations can lead to inconsistencies in product quality. Therefore, keeping these environmental factors stable helps maintain the material’s integrity and reduces the risk of defects.
Impact on Process Stability
Stable environmental conditions contribute to process stability, ensuring that every cycle produces consistent results. This stability is essential for high-volume manufacturing where even minor variations can lead to significant waste. By regulating environmental conditions, manufacturers can achieve a more predictable and efficient process.
Reducing Chemical Interference
The use of chemicals such as release agents or rust inhibitors should be minimized as they can contaminate the plastics. However, if necessary, choosing high-quality products and controlling their application can mitigate adverse effects. For more detailed strategies on minimizing chemical use, check proper chemical management in injection molding6.
Enhancing Quality Control Measures
Establishing a rigorous quality control system is imperative in identifying issues early in the production process. Employing advanced equipment like optical and electron microscopes for inspections allows for precise analysis of any defects, leading to targeted solutions. Explore more about quality control techniques in quality control in injection molding7.
Temperature control prevents defects in injection molding.True
Stable temperatures ensure material consistency, reducing defects.
Humidity fluctuations do not affect injection molding quality.False
Humidity changes can alter material properties, affecting quality.
Conclusion
By addressing dark spots through rigorous quality control and proper maintenance, you can significantly enhance your product quality and reduce waste.
-
Learn effective methods for storing raw materials to prevent contamination.: It’s recommended that manufacturers store raw materials at around 70°F in a moisture-free place away from direct sunlight. ↩
-
Discover effective cleaning techniques to prevent black spot formation.: Regularly clean the surfaces, molds, and components of your injection molding equipment using suitable cleaning agents and techniques. Pay … ↩
-
Learn how strategic mold design enhances material flow efficiency.: Mold flow analysis (MFA) software simulates the flow of plastic, which allows you to elevate part and mold design to create products of impeccable quality. ↩
-
Discover why efficient cooling is essential for defect-free products.: An improper injection mold cooling process, then, will almost always result in part defects that require rework or discard. The cooling process … ↩
-
Explore techniques to extend mold life and maintain quality.: 8 Ways to Increase Mold Life · 1 Tonnage · 2 Low-pressure close · 3 Core set up · 4 Mold open and close · 5 Ejection set up · 6 Hot runners and valve … ↩
-
Learn strategies to minimize chemical interference in production.: Ensuring that all materials used are compatible with one another. · Increasing the mold temperature or pre-drying the material if moisture is the … ↩
-
Discover advanced techniques for enhancing quality control measures.: The first stage is the design stage, followed by Mold and Pre-Production Inspection and In Process Quality Control and Final Inspection. ↩