Have you ever wondered how something as invisible as pressure can shape the quality of plastic parts?
In plastic injection molding, pressure is a crucial player that impacts everything from filling to the final appearance of molded parts. Understanding its effects can significantly improve your manufacturing outcomes.
But there’s more to it than just the basics! Let’s dive deeper into the various pressures at play and uncover how they influence your molded parts.
High injection pressure prevents short shots.True
High pressure ensures complete mold filling, preventing unfilled sections.
What Are the Key Types of Pressure in Injection Molding?
Pressure in injection molding is crucial for ensuring high-quality plastic parts. But what types of pressure are involved?
Injection molding involves various pressures, primarily injection pressure and holding pressure. Injection pressure ensures the mold cavity is filled accurately, while holding pressure compensates for material shrinkage during cooling. These pressures are critical for achieving desired part dimensions and quality.
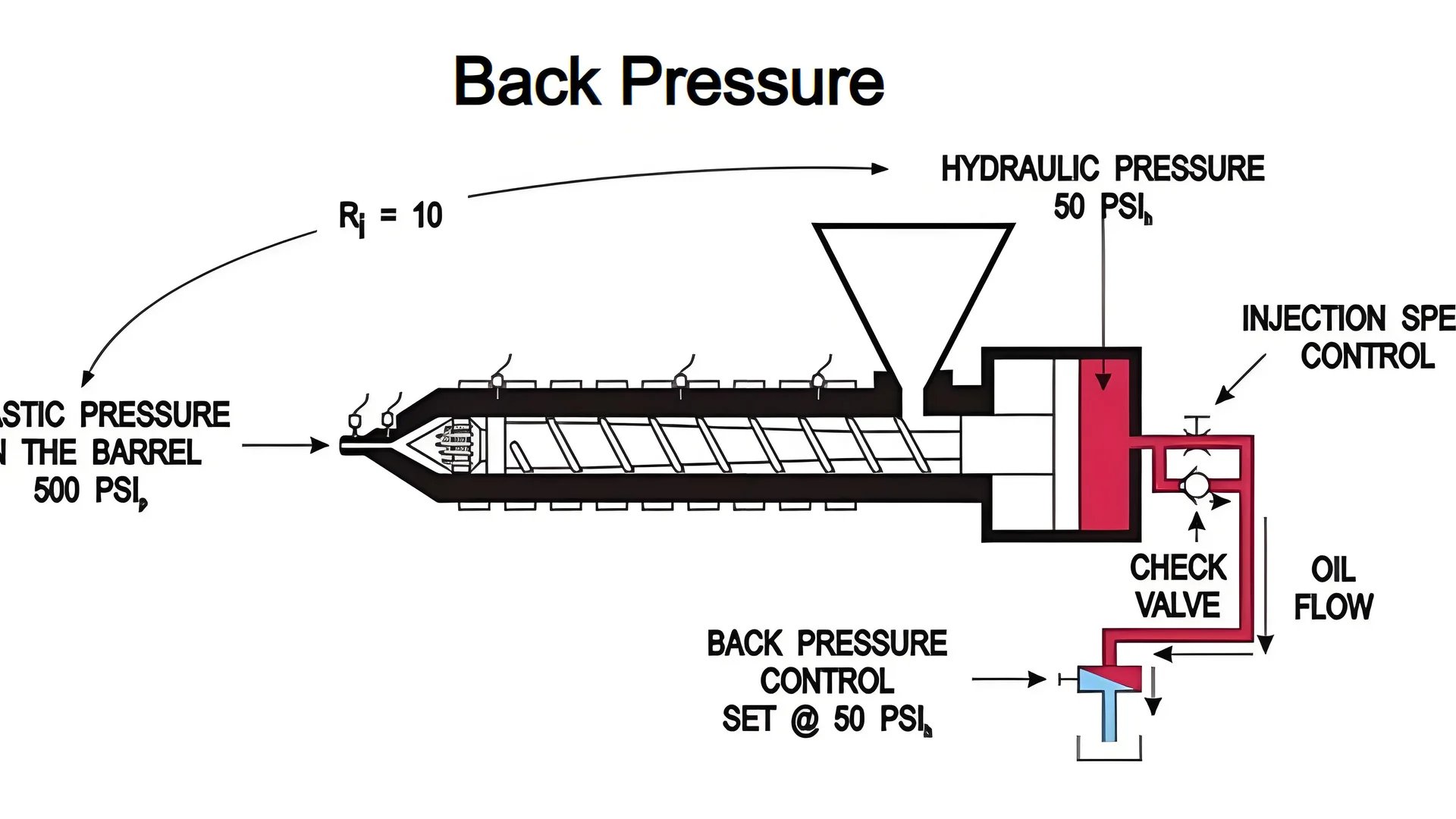
Injection Pressure
Injection pressure is the initial force that pushes molten plastic into the mold cavity. It plays a pivotal role in ensuring the material fills every intricate detail of the mold. High injection pressure helps prevent defects like short shots, where parts of the mold are not fully filled. However, excessive pressure can lead to flash, where excess material leaks out of the mold.
For instance, if you’re molding a complex part with thin walls, high injection pressure can ensure that the plastic reaches all corners before it begins to cool and solidify. This process maintains the part’s dimensional accuracy and structural integrity.
Holding Pressure
Once the mold cavity is filled, holding pressure takes over to maintain the material in place as it cools and solidifies. This phase is crucial for compensating for the volumetric shrinkage of the plastic as it transitions from liquid to solid state.
Proper holding pressure can prevent common issues such as shrinkage marks and sink holes, which occur when there’s insufficient material to compensate for shrinkage. For example, a part with varying wall thickness might require different holding pressures to ensure uniform shrinkage and stability.
Back Pressure
Back pressure is applied during the plasticizing stage, where raw material is melted and prepared for injection. It ensures consistent melting and mixing by providing resistance to the screw’s rotation. Proper back pressure can lead to uniform melting and color dispersion, enhancing the overall quality of the molded part.
In practical terms, adjusting back pressure can help eliminate air pockets in the melt, leading to better weld line strength and surface finish.
Clamp Pressure
Although not directly involved with the melt flow, clamp pressure is essential to keep the mold halves tightly closed during injection. It prevents flash by counteracting the force exerted by injection pressure.
The required clamp pressure depends on factors like part size and geometry. An inadequate clamp force can result in flash or even mold damage.
Comparison Table of Pressure Types
Pressure Type | Purpose | Potential Issues |
---|---|---|
Injection | Fills mold cavity | Flash, burn marks |
Holding | Compensates shrinkage | Sink marks |
Back | Ensures uniform melt | Air pockets |
Clamp | Keeps mold closed | Mold damage |
Understanding these different types of pressure and their functions is key to optimizing the injection molding process1. By managing each type effectively, manufacturers can enhance part quality and production efficiency.
Injection pressure prevents short shots in molding.True
High injection pressure ensures complete filling of the mold cavity.
Clamp pressure is unnecessary in injection molding.False
Clamp pressure prevents mold halves from opening during injection.
How Does Injection Pressure Affect Filling and Defects?
Injection pressure plays a vital role in ensuring the integrity and quality of plastic molded parts.
Injection pressure affects the filling of mold cavities and can prevent defects such as short shots and weld marks. Proper pressure ensures complete part formation and optimal fusion of materials, enhancing product quality.
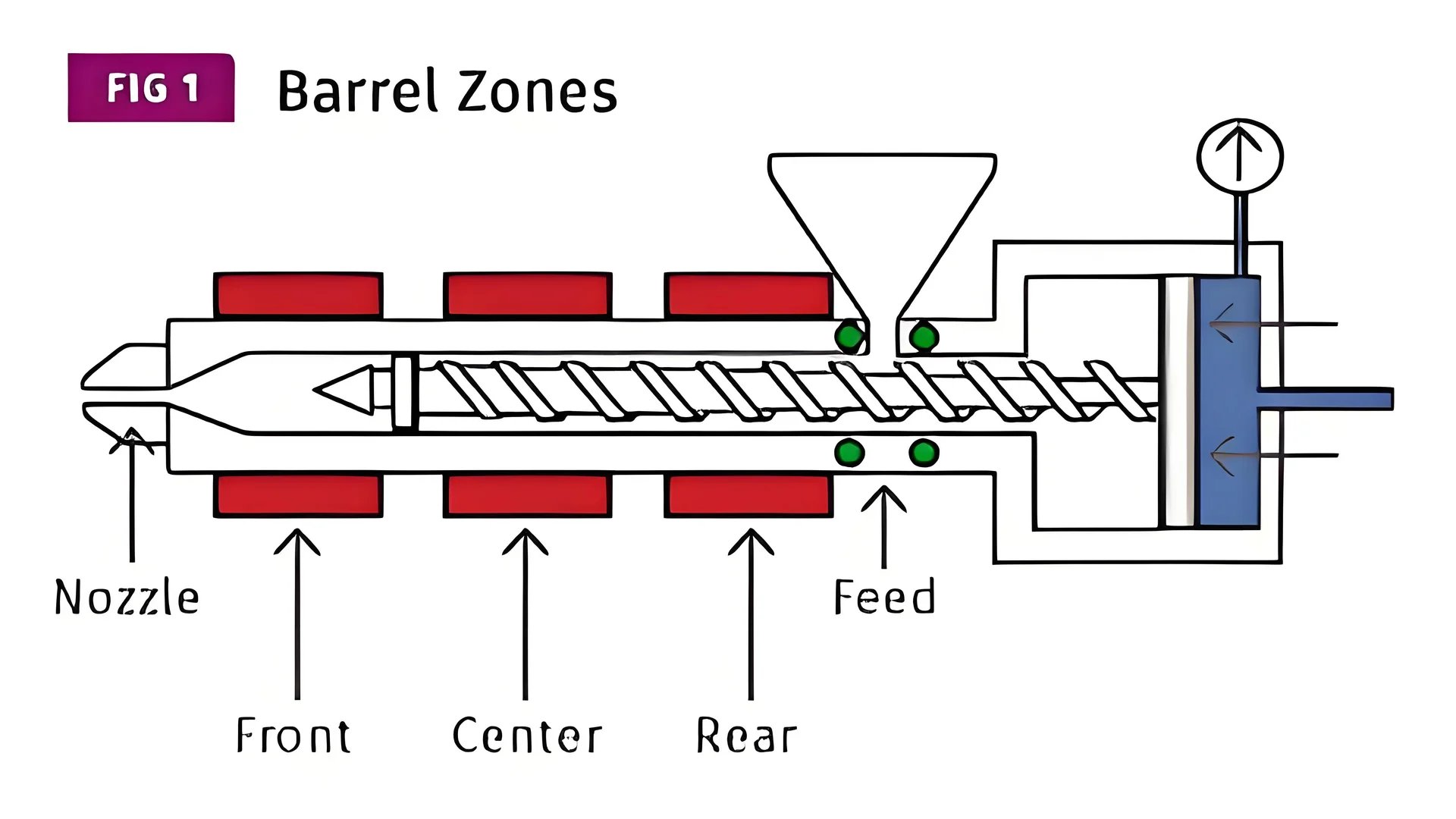
Understanding the Role of Injection Pressure
Injection pressure is a critical parameter in the plastic injection molding process. It directly impacts how well the molten plastic fills the mold cavity, thereby influencing the final product’s quality. A higher injection pressure can accelerate the filling process, ensuring that the plastic reaches all corners of the mold quickly and effectively. This reduces the risk of short shots, where some sections of the part remain unfilled due to insufficient material flow.
Filling Effects
During the filling phase, maintaining an adequate injection pressure is essential for achieving complete part formation. If the pressure is too low, it can lead to defects like short shots, where parts are partially formed. These issues not only affect the dimensional accuracy but also compromise the visual appeal of the product. On the other hand, excessive pressure might cause flash, where material leaks out of the mold cavity, creating unwanted thin layers.
Managing Weld Marks
Injection pressure also influences weld mark strength, which occurs when two flow fronts meet and fail to fuse properly. Insufficient pressure can result in weak weld marks, creating potential points of failure in the part. To counteract this, higher pressures improve material fusion at these critical junctures, enhancing weld mark strength and overall part robustness.
Injection Pressure | Potential Defects | Solutions |
---|---|---|
Low | Short shots, weak welds | Increase pressure |
High | Flash, internal stress | Optimize pressure levels |
Practical Applications
Consider a scenario involving complex mold geometries or intricate design features. In such cases, maintaining consistent injection pressure across different sections of the mold is vital. Pressure imbalances can lead to localized defects such as air traps or incomplete filling.
Case Study: Automotive Parts
In the automotive industry, precise injection pressure management is crucial for producing components that meet strict safety and durability standards. For instance, ensuring uniform pressure during molding can prevent potential weak points in structural components like bumpers or dashboards, where weld marks must be minimized.
In conclusion, effective injection pressure control is indispensable for preventing defects in injection molded parts. By understanding and optimizing this parameter, manufacturers can achieve superior product quality and reliability. Learn about injection molding defects2.
Higher injection pressure reduces short shots.True
Higher pressure ensures complete filling of mold cavities, reducing short shots.
Low injection pressure strengthens weld marks.False
Low pressure results in weak weld marks due to poor material fusion.
Why Is Holding Pressure Crucial for Dimensional Stability?
In the precise world of injection molding, holding pressure is essential for achieving dimensional accuracy and product quality.
Holding pressure maintains dimensional stability in injection molded parts by compensating for material shrinkage during cooling. It ensures the integrity of the part, preventing defects such as shrinkage marks and pits, which can compromise performance and appearance.

The Role of Holding Pressure in Injection Molding
Holding pressure is applied after the initial filling of the mold to maintain pressure on the material as it cools and solidifies. This step is crucial for mitigating shrinkage, which can lead to dimensional inaccuracies and surface defects.
-
Compensation for Material Shrinkage
Plastic materials tend to shrink as they cool, which can cause parts to become smaller than the desired dimensions if not properly managed. By maintaining appropriate holding pressure, manufacturers can ensure that the molten material fills out the mold completely, compensating for this natural shrinkage tendency. -
Prevention of Surface Defects
Without adequate holding pressure, parts can develop shrinkage marks and pits, especially in areas where the material thickness varies. This results in surface blemishes that detract from both the aesthetic quality and the structural integrity of the product. Maintaining holding pressure helps avoid these issues by ensuring even material distribution. -
Influence on Mold Cavity Filling
During the cooling phase, holding pressure ensures that any additional material required to compensate for shrinkage is forced into the mold cavity. This is especially important in complex mold designs with intricate features or varying wall thicknesses.
Effects on Physical Properties
The influence of holding pressure extends beyond dimensional stability; it also affects physical properties:
-
Density and Mechanical Strength
By improving how densely plastic molecules are packed, holding pressure enhances mechanical properties such as tensile strength and hardness. However, excessive pressure might result in anisotropic properties, where strength is enhanced in one direction but reduced in others. -
Crystallinity
For certain crystalline plastics, holding pressure can improve crystallinity, leading to better heat and chemical resistance. However, this can also result in decreased transparency and toughness.
Practical Implications
-
Impact on Production Efficiency
Maintaining correct holding pressure reduces waste by minimizing defects, leading to more efficient production runs. -
Balancing Act
Finding the right balance is key; too much pressure can cause internal stresses, whereas too little may not adequately fill out the mold. This delicate balance requires precise control and expertise.
For those looking to optimize their injection molding processes3, understanding the nuances of holding pressure is vital. Proper management ensures not only dimensional accuracy but also enhances overall product quality and performance.
Holding pressure reduces shrinkage marks in molded parts.True
Holding pressure compensates for material shrinkage, preventing surface defects.
Excessive holding pressure improves transparency of crystalline plastics.False
Excessive holding pressure decreases transparency due to increased crystallinity.
How Can Pressure Influence the Mechanical Properties of Parts?
Pressure plays a crucial role in determining the mechanical properties of injection molded parts, impacting everything from strength to toughness.
Pressure affects the density and crystallinity of injection molded parts. Higher pressure increases density, enhancing tensile and bending strength but may also induce internal stress, affecting toughness. Proper pressure control optimizes these mechanical properties.
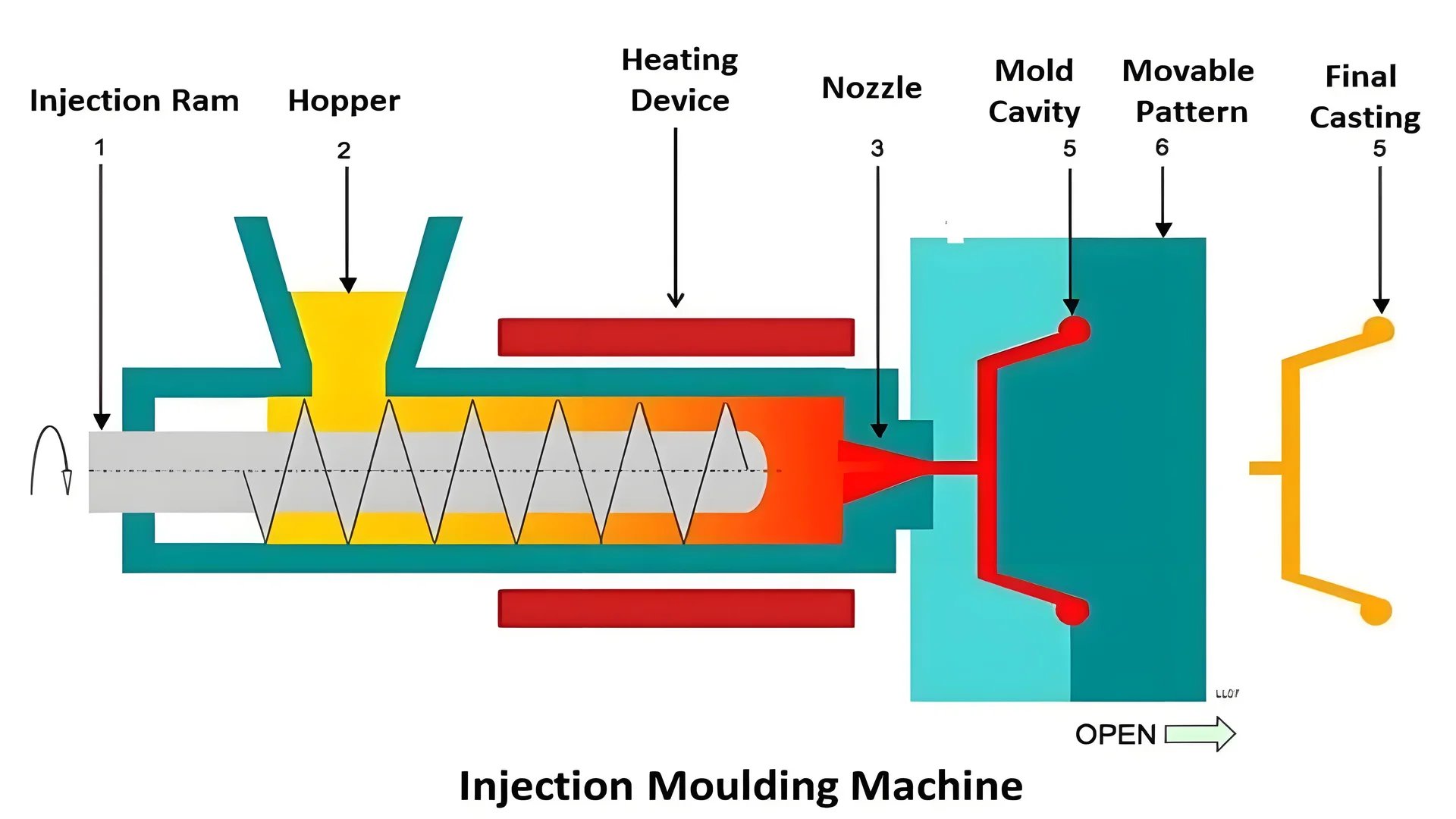
The Role of Pressure in Molecular Arrangement
Pressure significantly influences the arrangement and packing of plastic molecules during the injection molding process. When pressure is increased, molecules are forced closer together, enhancing the density of the material. This densification can lead to improved mechanical properties, such as higher tensile and bending strength.
However, excessive pressure can orient molecular chains in a specific direction, potentially increasing performance anisotropically. While this enhances strength in one direction, it can compromise properties like toughness and impact resistance in other directions due to induced internal stresses.
Crystallinity and Its Effects
For crystalline plastics, pressure can affect the degree of crystallization. Appropriate pressure encourages crystallization, which in turn boosts heat resistance and chemical stability. An increase in crystallinity generally enhances dimensional stability but may reduce transparency and toughness. It’s a delicate balance that requires careful control to optimize the mechanical properties of the part.
Balancing Pressure for Optimal Performance
Achieving the right balance of pressure is essential for optimizing the mechanical properties of injection molded parts. If pressure is too low, it can lead to underfilled molds, resulting in defects that compromise structural integrity. Conversely, too much pressure may result in high internal stresses and unwanted anisotropic behavior.
Here’s a table summarizing the effects of varying pressure levels:
Pressure Level | Molecular Arrangement | Crystallinity | Mechanical Properties |
---|---|---|---|
Low | Loose | Low | Weak, more defects |
Optimal | Dense | Balanced | Strong, uniform |
High | Overly oriented | High | Strong in one direction; increased stress |
Understanding these influences allows manufacturers to fine-tune the injection molding process. Adjusting parameters such as injection speed4 and cooling time can also play a pivotal role in managing these pressures effectively.
In conclusion, mastering the nuances of pressure control in injection molding can significantly enhance the mechanical performance of parts. By understanding how pressure influences molecular arrangement and crystallinity, manufacturers can produce parts with desired mechanical characteristics while minimizing defects and maintaining consistency.
Higher pressure increases tensile strength.True
Increased pressure enhances material density, boosting tensile strength.
Excessive pressure reduces transparency.True
High pressure can increase crystallinity, which often reduces transparency.
Conclusion
By mastering pressure management, you can elevate your production quality and efficiency, ensuring that your molded parts meet the highest standards.
-
Explore deeper insights into managing various pressures for optimal molding.: What pressures are involved in injection molding? · 1. Injection pressure · 2. Clamping pressure · 3. Back pressure · 4. Holding pressure. ↩
-
Discover how to identify and prevent common molding defects.: Here are 11 common injection molding defects, what the causes are and how you can avoid them. Explore our injection molding troubleshooting guide! ↩
-
Discover ways to enhance efficiency and product quality in injection molding.: Steps to INJECTION MOLDING Process Optimization · 1. Tool functionality examination · 2. Short shot testing · 3. Gate seal studies · 4. Sample parts evaluation/ … ↩
-
Explore how injection speed influences molecular orientation and part performance.: If the polyethylene itself is injected into the mould at a lower temperature, orientation commonly becomes more pronounced as the plastic solidifies quickly … ↩