A small detail impacts your product design greatly. The main channel length in injection molding plays a big role.
The length of the main channel in injection molding has a direct impact on how the product looks. It also matters for how exact the size is and the quality inside the product. Changing this length for better results helps spread pressure evenly. Also, the melt flows well. This change reduces inner stress. Better products come from this.
I remember working on a project where small design choices were very important. We crafted complex parts for consumer electronics. A poorly chosen main channel length might cause issues like flash and surface gloss changes. These problems affect the product’s sleek look. Dimensional accuracy and keeping parts from warping were critical to holding structural strength.
This realization really struck me when a colleague highlighted how uneven pressure from a too-long main channel led to big dimensional changes. We designed a component needing very tight tolerances. I understood how essential it was to balance these elements. It wasn’t just about fitting things. Every piece needed perfection to avoid problems like internal stress and uneven density that could weaken the product’s durability.
Main channel length affects product appearance quality.True
The length impacts melt flow and pressure, influencing appearance.
Shorter main channels always improve product quality.False
Short channels can cause uneven pressure, affecting quality negatively.
What are the key factors in designing main channel length?
Curious about how the length of a main channel in mold design affects your product’s quality?
Important parts in designing the main channel length are how it looks, the exactness of its size and its inside quality. Each piece impacts the final product’s beauty, accuracy and strength.
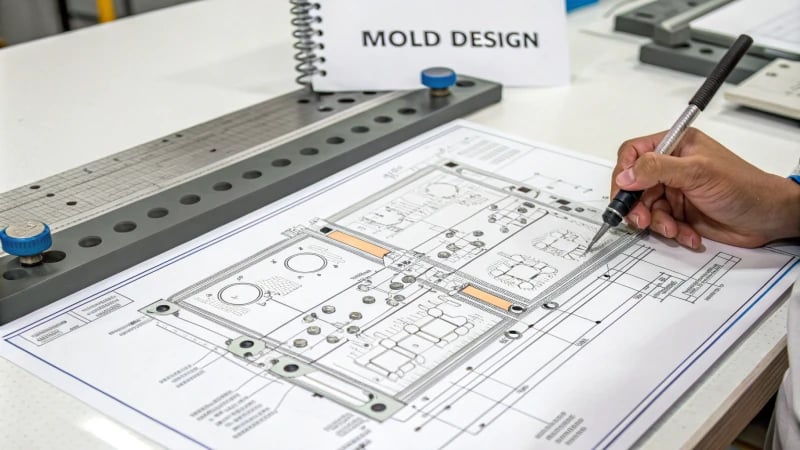
Appearance Quality
Looks really matter. I once helped design a sleek gadget case. The main runner was too long, which almost ruined the surface shine. The extra length caused overflow, leading to plastic going beyond its limit and making the case uneven and messy. This showed how the runner’s length matters a lot.
Surface Gloss: Keeping the right melt temperature is key for a shiny finish. A good runner length is important as it helps products look very polished and sleek.
Problem | Impact | Solution |
---|---|---|
Surface Shine | Uneven appearance | Optimize runner length |
Overflow Issues | Messy finish | Control melt temperature |
Dimensional Accuracy
Precision matters greatly, especially when tiny details are important. On another project, long channels caused wrong shape sizes, making assembly a headache due to uneven pressure distribution. Parts cooled unevenly and shrunk differently.
- Warping Deformation: Parts don’t fit well due to warping from unequal pressure during cooling.
- Dimensional Deviation: Long runners create uneven pressure, leading to shrinkage and inconsistent dimensions.
Explore more on dimensional accuracy1.
Internal Quality
Good internal quality helps products last long. I saw parts crack due to unequal filling; long channels are troublemakers here.
Density Uniformity: Even melt flow is essential, especially with complex shapes. Wrong density harms strength and durability.
- Internal Stress: Balanced pressure keeps cracks away by finding the perfect point where everything stays firm.
- Density Uniformity: Ensures even melt distribution; crucial for complex shapes.
Balancing these factors goes beyond meeting specs; it ensures products impress customers and work well. Every design choice influences both looks and function.
Long main runners cause flash problems.True
Excessive runner length increases injection pressure, leading to flash.
Short main channels lead to uneven density.False
Long channels, not short ones, cause uneven density due to imbalanced filling.
How Does Main Channel Length Affect Surface Gloss?
Have you ever thought about why some surfaces shine so brightly while others look dull? The length of the main channel in injection molding is very important in solving this glossy puzzle.
The main channel’s length changes the surface shine by shifting the melt’s temperature and flow patterns. A longer channel probably reduces gloss because of heat loss. This change often creates rough surfaces or signs of cooler material.
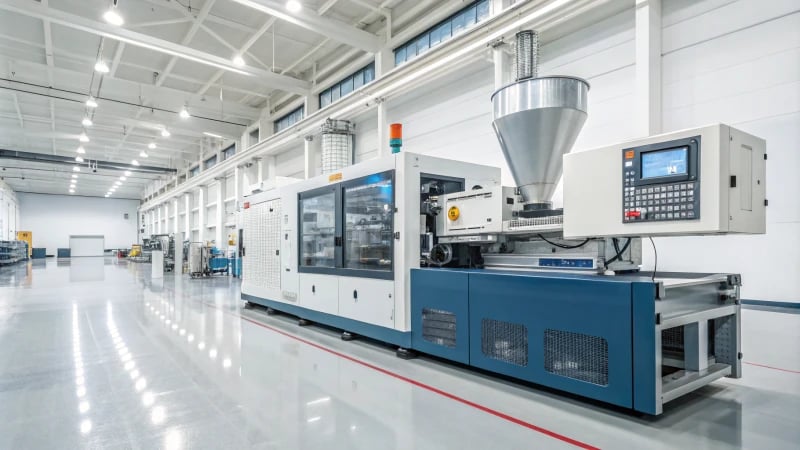
Impact on Appearance Quality
The shiny, glossy surfaces on your favorite devices owe their appeal partly to the length of the main channel in the injection-molding process. I remember a time when we worked on sleek cases for smartphones and made the main channel slightly too long. As the molten plastic traveled, it lost a lot of heat, causing a dull finish instead of a shiny one. Balancing the channel length is crucial. A channel that’s too long can not only reduce gloss but also lead to flash problems, where excess pressure makes the plastic spill over, ruining the smooth surface everyone loves. Explore suitable runner lengths2 to ensure optimal appearance quality.
Influence on Dimensional Accuracy
When I worked on a project featuring complex mechanical pieces, I saw how important precise dimensions are. An extended main channel might cause pressure drops during filling. This results in uneven shrinking as the part cools down, creating big headaches for precision items. An uneven spread of pressure can even twist large, flat pieces, making them far from ideal for putting together. Such issues are prevalent in large flat items where precise dimensions are critical for proper function and appearance.
Internal Quality Considerations
The inside quality of molded items might not get much spotlight as gloss does, but it holds equal importance. I had a batch of parts once with low-density areas because the channel was too long. This uneven filling produced weak, even unusable products. Also, high internal stress can quietly creep in, leading to cracks over time. It is about finding the right balance in channel length to get even density and lower stress, keeping items strong and dependable.
In injection molding, each small detail matters—from looking good to holding up inside. Tuning factors like the main channel length helps in creating excellent products that not only appeal visually but also last long. If you’re stepping into this design and manufacturing world as I did, probably explore plans for injection molding3 to strike the perfect balance for your projects.
Longer main channels reduce surface gloss.True
Extended channels cause heat loss, decreasing melt fluidity and gloss.
Shorter main channels cause more dimensional deviation.False
Longer channels lead to pressure loss, causing dimensional issues.
How Does Main Channel Length Affect Dimensional Accuracy?
Have you ever thought about how the length of a mold’s main channel affects your design’s precision?
The main channel in mold design is very important for accurate sizes. It influences how pressure spreads and how the melt flows. Long channels may lead to uneven pressure. This often causes shrinkage and warping. Shrinkage and warping affect the precision of the final product. Precision is very important.
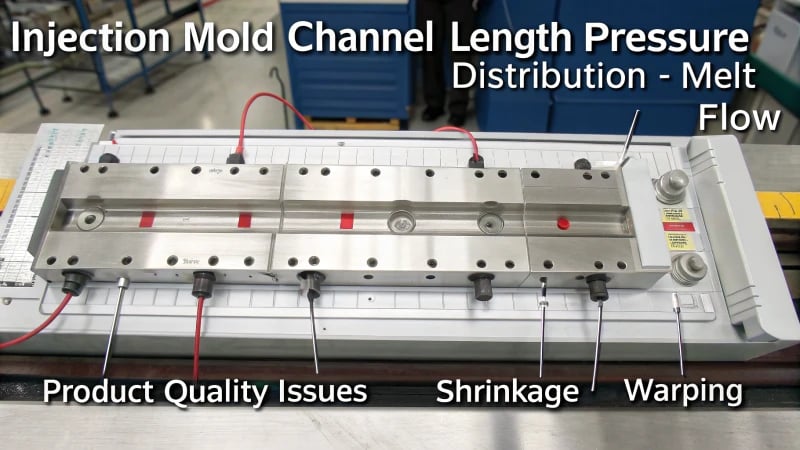
Understanding Pressure Distribution
The main channel length4 in injection molding is crucial for maintaining consistent pressure distribution. I spent many hours perfecting designs, only to see them ruined by the length of a main channel. Longer channels often cause higher pressure loss, leading to uneven pressure inside the cavity. This inconsistency can cause products to shrink variably, which affects their dimensional accuracy.
For example, when manufacturing detailed mechanical parts with stringent precision requirements, an improper main channel length could lead to dimensions that exceed tolerance levels, causing expensive changes and delays.
Effects on Appearance Quality
I recall my first mistake underestimating the effect of main channel length on how things look. An extended main channel may require increased injection pressure to fill the cavity effectively. This scenario often results in flash problems, where excess plastic overflows at the mold parting surface. Such overflow can compromise the product’s appearance, especially for high-gloss items5, by causing surface roughness or cold material marks.
These appearance issues highlight the importance of optimizing the main runner length to balance melt temperature and flow state.
Factor | Impact of Long Main Channel |
---|---|
Flash Problem | Increased injection pressure causes overflow |
Surface Gloss | Lower melt temperature leads to poor gloss |
For shiny items like fancy phone cases, adjusting the main runner length is really crucial. It helps the melt flow perfectly, stopping surface bumps or cold marks.
Internal Quality Concerns
Internal quality is another issue affected by long main channels as they can cause uneven melt filling, leading to variable density in the product. This issue is particularly problematic for complex designs where weak spots might break the structure.
Furthermore, inadequate runner design may cause internal stress, increasing the risk of cracks or ruptures during use—especially in products sensitive to stress like transparent plastics. I have seen transparent plastics crack due to inside stress from poor runner design. Solving these problems early is vital to stop cracks or breaks when in use.
Addressing Warping Deformation
Warping deformation taught me a tough lesson. The pressure difference between the front and rear ends of the melt increases with longer channels. This difference can lead to warping deformation6 as the product cools and solidifies. Warping not only affects flatness but also its assembly performance too.
When producing large flat products, it’s essential to manage channel length carefully to avoid these issues and ensure dimensional fidelity.
Overall, I learned that main channel length is not just a detail—it is a big part of mold design influencing size accuracy, looks, and internal quality. By understanding and optimizing this aspect, designers can significantly improve product performance and aesthetics.
Longer main channels increase pressure loss.True
Longer channels lead to higher pressure loss, affecting dimensional accuracy.
Short main channels cause more warping deformation.False
Longer channels, not shorter ones, increase pressure difference causing warping.
How Does Main Channel Length Affect Internal Stress in Products?
Have you ever thought about how the length of a product’s main passage might really impact its internal stress? This small detail might greatly affect a product’s quality and performance. It’s not a minor issue.
The main channel’s length in a product directly changes internal stress. This shift happens by altering how pressure spreads, how melt moves and how fast cooling happens. These aspects affect how the product looks. They also impact the precision of its size and shape. Overall product performance gets influenced as well. Performance really changes.
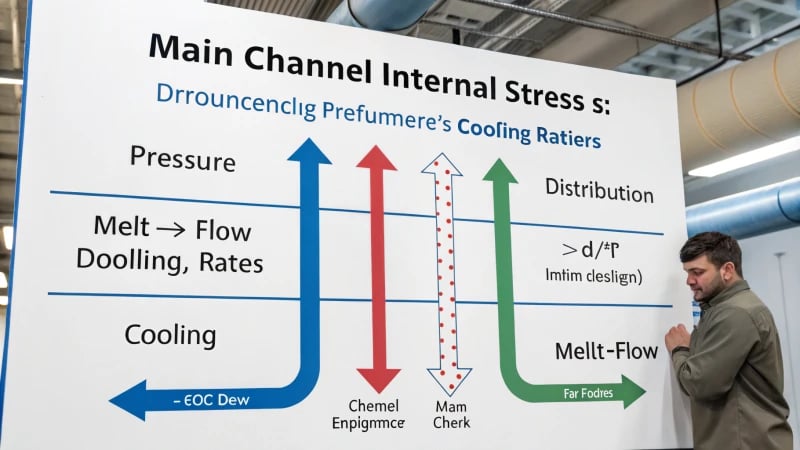
The Role of Main Channel Length in Injection Molding
I recall my first challenge designing an injection mold. It felt like solving a puzzle with ever-changing pieces. One project remains vivid – crafting a sleek electronic case. A longer main channel raised injection pressure, leading to flash problems7, the unattractive plastic excess at mold joints. Imagine investing effort into a perfect box, only for edges to appear chewed by a toddler’s sharp teeth! The long main channel caused this.
Impact on Surface Gloss
Gloss issues also surfaced. A client demanded a glossy finish for their premium products. Each prototype looked less glossy, as if splashed with cold water. Then realization hit – the main channel was overly long, cooling the material too much before mold filling. This created dull surfaces with cold material marks.
Channel Length | Impact on Gloss |
---|---|
Short | High gloss |
Long | Low gloss |
Dimensional Accuracy Concerns
Dimensional accuracy proved challenging. In one project, precision parts for a device had measurements completely off. Why? A too-long main channel led to uneven cavity pressure. Key dimensions were inconsistent, like measuring a rubber band – it just didn’t stay still.
Warping Deformation and Internal Stress
Warping was another issue. One project required large flat panels. Instead, panels warped like soggy cardboard due to warping deformation8. The main channel length caused this, creating uneven pressures and shrinkage in different areas.
Examining Density Uniformity
Density uniformity hadn’t been a focus until a mentor highlighted an oversight. Complex designs caused density variations due to poor channels. Imagine baking a cake with some sections undercooked and others overdone – our products faced similar inconsistencies inside.
Internal Stress and Product Integrity
Internal stress affected product integrity, too. Once, an entire batch of transparent items was returned due to cracks. This taught a tough lesson about balancing channel length to protect product quality and prevent expensive failures.
Recognizing these issues lets designers like me adjust mold design9 for optimal results. Getting the channel length balanced means our products not only look good but work better.
Longer main channels increase injection pressure.True
Long channels require more pressure to push the melt, affecting molding.
Short channels result in low surface gloss.False
Short channels maintain higher gloss by ensuring proper melt flow and cooling.
Conclusion
Main channel length in injection molding significantly affects product appearance, dimensional accuracy, and internal quality by influencing melt flow, pressure distribution, and cooling rates.
-
Understand how dimensional deviation impacts precision in injection molding. ↩
-
Discovering optimal runner lengths helps ensure high surface gloss in molded products, enhancing their aesthetic appeal. ↩
-
Learning effective strategies can help minimize internal stress, improving product quality and reducing defects. ↩
-
Explore how main channel length impacts pressure distribution in molds, crucial for maintaining dimensional accuracy. ↩
-
Discover why runner design is vital for achieving high-gloss surfaces in injection-molded products. ↩
-
Learn strategies to minimize warping deformation in injection-molded products by managing channel length effectively. ↩
-
Clicking this link provides insights into common flash issues in molding processes and their solutions. ↩
-
Explore causes of warping deformation in injection-molded products and strategies to prevent it. ↩
-
Discover strategies for optimizing mold design to enhance product quality and reduce stress. ↩