Do you often think about why some molded products do not last as long as you want? High mold temperatures might be the hidden reason.
I work on fixing high mold temperatures that affect product strength. This means improving the cooling system. Changes in channel layouts help a lot. Adjusting injection settings like cycle time and barrel temperature also helps. Finally, materials with good thermal conductivity are useful. This is very important.
When I started in the mold industry, I was confused by products breaking differently. Then, I studied the cooling system details. Changing the cooling channel layout, especially in big molds, helped control the temperature. This was like moving channels in car parts with computer programs.
Changing the size or number of cooling channels was also important. I remember making a channel wider from 8mm to 12mm, which really sped up cooling. Using good cooling liquids like water or special oils lowered the mold temperature even more, helping my designs stay strong.
Adjusting injection settings was important too. I tried shorter injection cycles and colder barrel temperatures. These changes saved time and reduced extra heat. Choosing mold materials, like copper or aluminum, that carry heat well also helped a lot. They moved heat away from important spots.
Every change taught me to build stronger products. I turned early confusion into valuable knowledge.
High mold temperatures always reduce product strength.False
High temperatures can reduce strength, but adjustments can mitigate effects.
Optimizing cooling channels can enhance product durability.True
Efficient cooling prevents overheating, maintaining product integrity.
Why Do Injection Mold Temperatures Rise?
Sometimes, your injection mold seems too hot. This happens to many people. High mold temperatures really cause problems. They affect both quality and efficiency.
High mold temperatures often arise from cooling systems not working properly, unsuitable injection molding settings and bad material choices. Fine-tuning these areas really lowers temperatures and improves overall production quality.
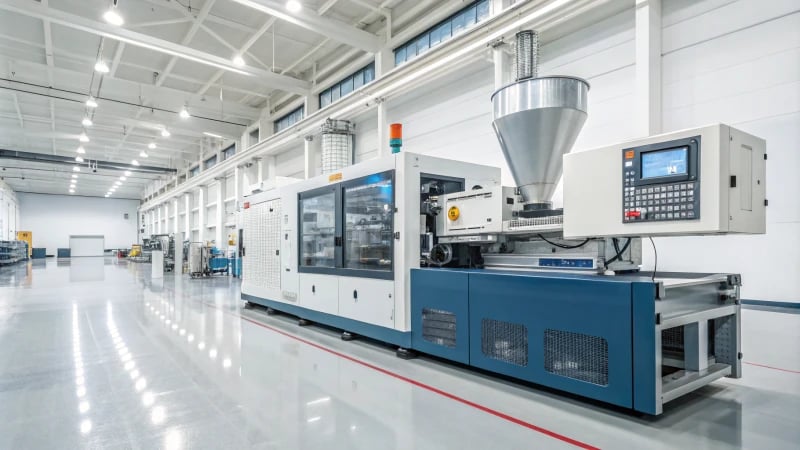
Inadequate Cooling Systems
I remember when I first faced an overheating mold. It was stressful. The problem came from an old cooling system. Good cooling channels are very important. For example, a 3D cooling channel design1 helps complex molds by stopping hot spots.
Upgrading cooling channel sizes is really important. Going from 8mm to 10-12mm changes how heat moves out a lot. Also, using a good cooling liquid makes a huge difference. Specialized water coolants or heat transfer oils were really helpful in my work.
Cooling System Enhancements | Benefits |
---|---|
3D Cooling Design | Uniform temperature distribution |
Increased Channel Size | Improved heat dissipation |
Efficient Cooling Medium | Faster temperature reduction |
Improper Injection Molding Parameters
Once, I spent many hours adjusting parameters to control temperatures. Reducing the injection cycle from 60 seconds to about 40-50 seconds reduced heat buildup. Lowering the barrel temperature helped too while keeping quality high.
By shortening the injection cycle, the mold’s exposure to high-temperature melt reduces significantly. Moreover, adjusting the barrel temperature can decrease heat transfer2 to the mold without compromising product quality.
Inappropriate Mold Materials and Surface Treatment
Choosing the right materials is crucial. Materials like copper or aluminum alloys in key parts move heat to the cooling medium fast. Surface treatments like ceramic coatings3 act as insulators, protecting the product from too much heat.
Improving these parts increases performance and also extends the mold’s life, which is very beneficial for manufacturing.
3D cooling designs prevent mold overheating.True
3D cooling channels distribute temperature evenly, reducing hotspots.
Ceramic coatings increase mold temperature impact.False
Ceramic coatings insulate, reducing temperature impact on molds.
How Does Mold Cooling System Design Affect Product Strength?
Ever think about how the mold cooling system affects your product’s strength? Learn the secrets behind this important design part! Variety of cooling techniques impact the final quality. Temperature control is really essential. Proper cooling probably leads to durable products.
The mold cooling system design greatly impacts product strength. Uniform cooling is crucial to prevent warping and shrinking. Cooling channel arrangement is important. Medium efficiency really matters too. Material conductivity affects heat dissipation. Stability relies on these factors.
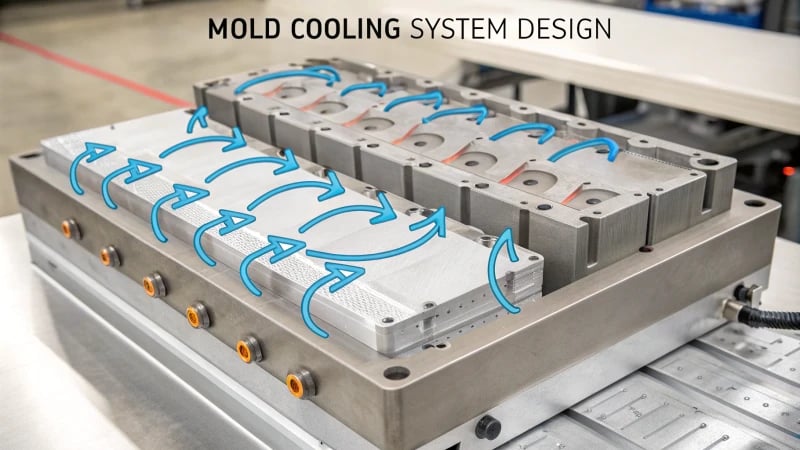
Importance of Uniform Cooling
Uniform cooling is vital in maintaining product integrity. In my early days working in molds, uneven cooling ruined many products. Imagine creating a design, only to see it come out bent or shrunk due to warpage or shrinkage, compromising strength. To achieve uniformity, check the cooling channel layout4. 3D designs help avoid local overheating, crucial for large or complex molds.
Optimizing Cooling Channel Design
An effective cooling channel design maximizes heat dissipation. During a project with car parts, we had an overheating problem. This taught me that increasing the number or diameter of cooling channels5 matters a lot. For example, expanding diameter from 8mm to 10-12mm enhances flow efficiency. A simple change makes a big impact. The table below illustrates potential improvements:
Diameter (mm) | Cooling Efficiency |
---|---|
8 | Standard |
10 | Improved |
12 | Optimal |
Choosing the Right Cooling Medium
Choosing the right coolant is like finding the right tool for a job. The choice of cooling medium significantly affects performance. When I tried water coolant first, its speed in reducing mold temperature surprised me due to its high efficiency. For detailed tasks and precise applications, special heat transfer oils offer better control and ensure the mold maintains an optimal temperature, reducing impact6 on product strength.
Adjusting Process Parameters
Changing molding parameters is like tuning an instrument. Adjusting injection molding parameters, such as shortening cycles or lowering barrel temperatures, can reduce heat absorption by the mold. Small tweaks bring big results and minimize excessive temperature issues without compromising product quality.
Material and Surface Treatment
Using materials with high thermal conductivity opened my eyes to new possibilities. Selecting materials such as copper or aluminum alloys ensures efficient heat transfer. Additionally, surface treatments like ceramic coatings act as insulators, reflecting heat and preserving mold temperature integrity while increasing product strength.
By studying these aspects of mold cooling system design—uniform cooling importance, optimizing channel design, choosing suitable mediums, adjusting process parameters, and selecting appropriate materials—manufacturers can enhance product strength and quality effectively. This comprehensive analysis ensures that molds operate at optimal temperatures directly influencing the final product’s robustness and reliability.
Uniform cooling prevents product warpage.True
Uneven cooling causes warpage, impacting product strength.
Increasing cooling channel diameter reduces heat dissipation.False
Larger diameters improve flow and enhance heat dissipation.
What Process Parameters Can Be Adjusted to Control Mold Temperature?
The day remains vivid when I saw how important mold temperature is in injection molding. That discovery transformed my production line. It saved us from many problems and flaws. Really important.
To keep mold temperature steady, adjust how well the cooling system works. Change the times for the injection cycle. Control barrel temperatures carefully. Select mold materials wisely. These changes help heat management a lot during injection molding. Yes, they really do.
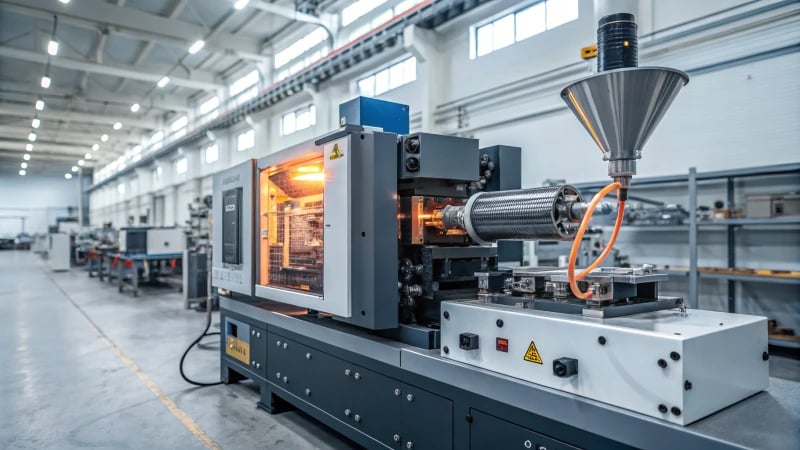
Optimize the Cooling System
An efficient cooling system is pivotal in controlling mold temperature. At first, when I worked with molds, I did not realize how important an effective cooling system was. Many nights were spent at the factory, changing the cooling channel design7 to get even cooling for every mold part. Complex designs stressed me, but using 3D cooling channels saved the day. These channels stopped local overheating, keeping the process very smooth.
Increasing the number or size of channels was extremely helpful – changing a channel from 8mm to 10-12mm made heat disappear faster. Additionally, choosing a high-efficiency cooling medium8, like water coolant or specialized oils, can effectively lower mold temperature and save a lot of stress.
Cooling Solution | Advantage |
---|---|
3D Cooling Channels | Uniform temperature control |
Larger Channel Diameter | Faster heat dissipation |
Efficient Cooling Mediums | Enhanced cooling performance |
Modify Injection Molding Parameters
Adjusting injection cycle times was like fine-tuning a watch. Shortening cycles helped molds absorb less heat from hot melts. For example, reducing the cycle from 60 to 40-50 seconds was perfect – less heat and fewer defects.
Furthermore, lowering the barrel temperature without compromising melt fluidity helps control heat input into the mold. Just a 10-20°C drop9 made a big difference in stopping too much heat buildup.
Choose the Right Mold Material and Treatments
Choosing mold materials with high thermal conductivity was a game-changer. Using copper or aluminum alloys near cooling areas greatly improved heat management. It felt like having a secret weapon!
Applying surface coatings like ceramic or thermal barriers10 can insulate against excess heat. These coatings reflect heat away, maintaining a more consistent mold temperature and improving product integrity.
Material/Coating | Benefit |
---|---|
High Thermal Conductivity | Quick heat transfer |
Surface Coatings | Reduces heat absorption |
By using these strategies, I found manufacturers like us could control mold temperatures well. Product quality went up without losing production efficiency. Each change was like solving a puzzle, leading to more reliable and consistent results.
Increasing cooling channel diameter improves heat dissipation.True
Larger channels allow more coolant flow, enhancing heat removal.
Lowering barrel temperature increases mold temperature.False
Reducing barrel temperature decreases heat input to the mold.
What Mold Materials Have the Best Thermal Conductivity?
I remember the first time I needed to select mold materials. So many choices filled me with confusion and doubt about what mattered most. Thermal conductivity became my guiding star.
Copper and aluminum alloys serve as my favorite materials for molds because they transfer heat really well. They do a great job at moving heat. This ability keeps mold temperatures even, probably helping cut down the time needed in manufacturing tasks like injection molding.
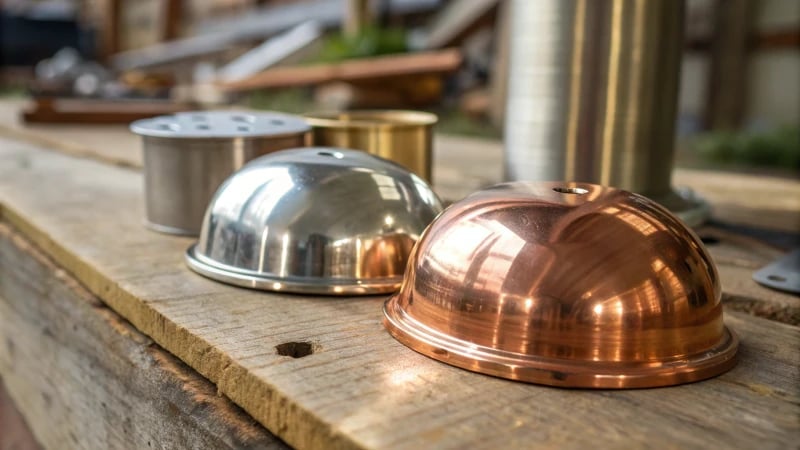
Exploring Thermal Conductivity in Mold Materials
When I first entered the world of mold materials11, I quickly found out that thermal conductivity is very important for successful manufacturing. If the material moves heat away quickly, the molds are less likely to get too hot. This means better and faster production.
Copper Alloys
Copper alloys have amazed me, especially beryllium copper. I found it during a tough project. Its ability to transfer heat surprised me a lot. It works much better than the steel molds I used before.
Property | Copper Alloys | Steel |
---|---|---|
Thermal Conductivity (W/m·K) | 300-400 | 20-60 |
Copper keeps mold temperatures stable. This stability has saved me from problems like warping, which gave me many issues in my early projects.
Aluminum Alloys
Aluminum alloys are another top choice for me. They help when I need something light but strong. They are very useful for big molds or molds that need frequent handling.
While not as conductive as copper, aluminum still offers a good mix of being light and working well. It finds that perfect middle spot—no need to choose between weight and performance.
Optimizing Mold Design with Thermal Conductivity
A key moment in my mold design was understanding the importance of improving the cooling system. By changing the cooling channel layout and increasing their size or amount, I improved cooling efficiency a lot. Using efficient cooling mediums like water coolant has changed the game for me, keeping things moving smoothly.
Simulation software12 is now a reliable tool for me. It helps design cooling channels to spread cooling mediums evenly, preventing local overheating spots.
Surface Treatments and Coatings
Apart from choosing the right materials, I’ve learned that surface treatments can really improve a mold’s thermal performance. Coating molds with ceramic or thermal barrier coatings acts as a shield, cutting back unwanted heat transfer and making the mold last longer.
Combining high-conductivity materials with advanced cooling techniques has let me take my manufacturing to new levels of efficiency and consistency—exactly what modern manufacturing needs.
Copper alloys have higher thermal conductivity than steel.True
Copper alloys' thermal conductivity is 300-400 W/m·K, while steel's is 20-60.
Aluminum alloys are heavier than copper alloys.False
Aluminum alloys are known for being lightweight compared to copper.
Conclusion
To enhance injection molded product strength, optimize cooling systems, adjust molding parameters, and select high thermal conductivity materials to manage mold temperatures effectively.
-
Discover how 3D cooling channels prevent local overheating, enhancing uniformity and efficiency. ↩
-
Understand techniques to fine-tune barrel temperature for optimal heat management without quality loss. ↩
-
Explore how ceramic coatings help insulate molds, reducing heat transfer and improving product durability. ↩
-
This link explains how optimizing the cooling channel layout prevents local overheating and ensures uniform cooling. ↩
-
Explore how increasing cooling channel diameter improves heat dissipation and enhances mold efficiency. ↩
-
Learn why water coolant is preferred for its rapid temperature reduction capabilities in mold systems. ↩
-
Exploring different cooling channel designs helps ensure uniform cooling, preventing defects and enhancing product quality. ↩
-
Understanding various cooling mediums aids in selecting options that efficiently manage mold temperatures. ↩
-
Learn how adjusting barrel temperatures influences mold heat levels and product outcomes. ↩
-
Discover how surface coatings help manage heat transfer, maintaining consistent mold temperatures. ↩
-
Explore various materials offering high thermal conductivity and their applications in manufacturing. ↩
-
Discover methods to enhance mold cooling efficiency through channel layout optimization and medium selection. ↩