Are you ready to level up your skills in automotive plastic part design? Let’s explore some essential best practices that can transform your approach!
The best practices for designing automotive plastic parts include careful material selection, maintaining uniform wall thickness, strategic rib and connection design, and ensuring effective mold and cooling system configurations. These practices ensure parts meet performance and cost criteria.
While this concise answer provides a solid foundation, there’s so much more to uncover. Dive deeper into materials, techniques, and the art of mold design—your journey to becoming a design expert starts here!
Uniform wall thickness prevents warping in plastic parts.True
Maintaining consistent wall thickness ensures even cooling, reducing deformation.
How Does Material Selection Impact Plastic Part Design?
Material selection is pivotal in plastic part design, influencing performance, cost, and durability.
Material selection impacts plastic part design by dictating performance characteristics such as strength, heat resistance, and cost. Choosing the right material ensures parts function optimally under varying conditions, meet industry standards, and remain economically viable.
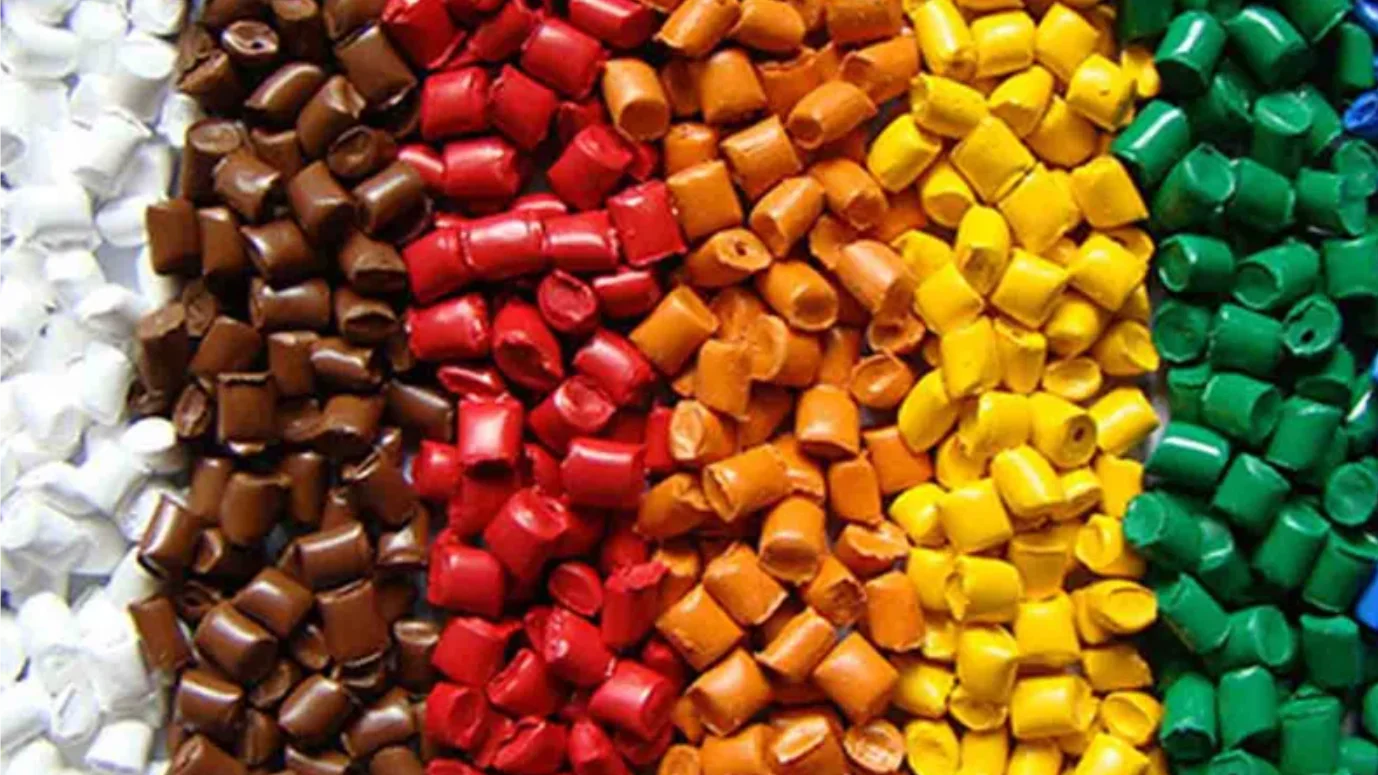
Understanding Performance Requirements
When designing plastic parts, particularly in the automotive industry, understanding the performance requirements1 is essential. For instance, a bumper requires high impact strength to absorb shocks during collisions, whereas interior components might prioritize surface hardness and wear resistance.
Materials like polycarbonate or ABS (Acrylonitrile Butadiene Styrene) are popular for their superior impact resistance and thermal stability.
- Strength: Polycarbonate provides excellent impact resistance, ideal for exterior parts.
- Heat Resistance: Nylon-based composites are suitable for high-temperature areas, like engine components.
- Chemical Corrosion Resistance: Selecting materials that resist degradation from automotive fluids is crucial for longevity.
- Dimensional Stability: Materials like PEEK (Polyether ether ketone) ensure dimensional stability under fluctuating temperatures.
Balancing Cost Factors
The cost factors2 involved in material selection cannot be overlooked. High-performance materials often come with a higher price tag. Balancing cost without compromising on quality is key.
Material | Cost Range | Application Example |
---|---|---|
Polypropylene | Low | Interior trim |
ABS | Medium | Instrument panels |
Polycarbonate | High | Headlamp lenses |
- Material Price: Opt for materials that meet requirements but are economically feasible.
- Processing Cost: Consider materials that are easy to mold and require less energy to process.
The Role of Simulation in Material Selection
Simulation tools play a critical role in optimizing material selection. Using CAE software3, designers can predict how different materials will perform under stress, temperature changes, and exposure to chemicals.
Simulation allows for:
- Predicting Material Behavior: Understanding how materials react under specific conditions.
- Optimizing Material Usage: Reducing waste by selecting the right material thickness and composition.
- Reducing Development Time: Identifying potential issues before physical prototyping.
By utilizing these strategies in material selection, designers can ensure that plastic parts not only meet the technical specifications but also remain within budgetary constraints while maximizing performance.
Polycarbonate is ideal for interior automotive parts.False
Polycarbonate is used for exterior parts due to impact resistance.
Simulation tools reduce development time in plastic part design.True
Simulation identifies potential issues early, speeding up development.
What Structural Design Principles Should You Follow?
Understanding structural design principles is key to creating robust, efficient automotive plastic parts.
Follow principles like uniform wall thickness, strategic rib placement, and effective connection designs to enhance strength and functionality. These principles minimize defects such as warping and ensure reliability in diverse conditions.
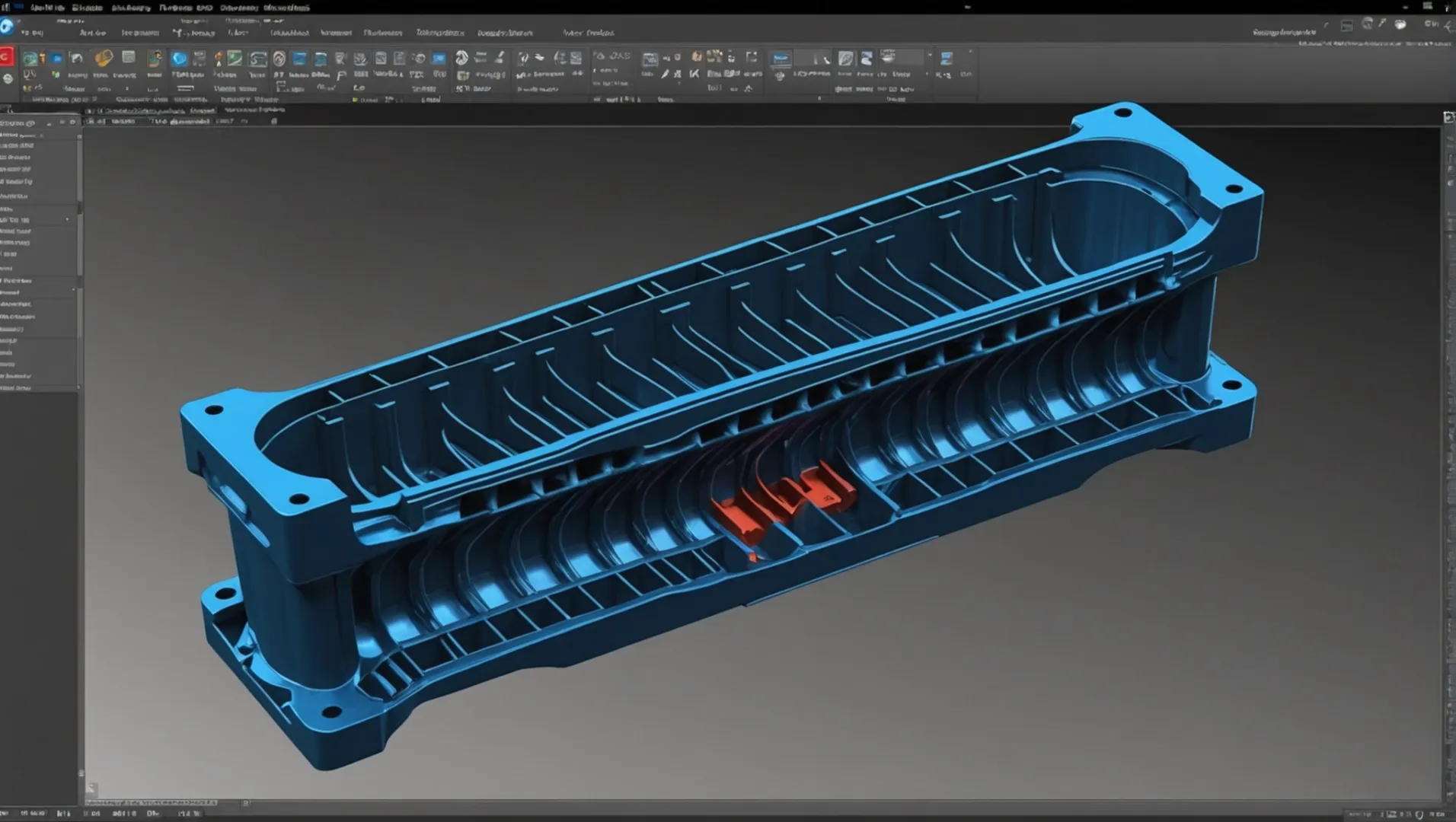
Uniform Wall Thickness
One of the fundamental principles in structural design is ensuring uniform wall thickness across plastic parts. Non-uniform thickness can lead to problems such as uneven cooling and inconsistent shrinkage, which manifest as warping and deformation. To combat this, designers should aim for a consistent wall thickness, adjusting slightly only where load requirements demand.
For instance, consider a car’s bumper which needs to withstand impacts. The bumper’s wall might be thicker in areas subject to more stress but should taper gradually to avoid defects. Learn more about wall thickness strategies4.
Strategic Rib Placement
Ribs are essential for reinforcing plastic parts without adding substantial weight. Properly placed ribs can significantly improve strength and rigidity while reducing deformation risks. When designing ribs, consider their height, width, and spacing to prevent surface defects like shrinkage marks.
A practical example is in dashboard components where ribs provide structural support without compromising aesthetics. Designers must balance rib dimensions to maintain visual appeal while enhancing strength.
Effective Connection Designs
Connections are crucial for assembly and disassembly processes. Clip connections are ideal for infrequently removed parts like interior panels, offering ease of assembly with minimal tooling. Threaded connections suit parts requiring regular removal, such as filter covers, providing strength and sealing.
In complex assemblies, welding connections are used. Methods such as ultrasonic or hot plate welding provide robust joints, but design must consider the specific requirements of each method to ensure joint integrity.
Considerations in Rib Design
When designing ribs, it’s vital to align them with the part’s stress patterns. This alignment ensures that ribs provide maximum reinforcement where needed most. Additionally, transition zones between ribs and the main part should be smooth to prevent stress concentrations that could lead to cracking or failure.
Proper rib design not only improves performance but also facilitates efficient manufacturing by reducing cycle times and minimizing material use.
By adhering to these structural design principles, engineers can enhance the durability and functionality of automotive plastic parts, ultimately contributing to better vehicle performance and customer satisfaction.
Uniform wall thickness prevents warping in plastic parts.True
Consistent wall thickness ensures even cooling and shrinkage, reducing warping.
Clip connections are ideal for frequently removed parts.False
Clip connections suit infrequently removed parts, like interior panels.
How Important Is Mold Design in Automotive Parts Manufacturing?
Mold design is a cornerstone in automotive parts manufacturing, influencing quality and efficiency.
In automotive manufacturing, mold design is crucial as it directly impacts the quality, production efficiency, and overall cost of plastic parts. Effective mold design ensures precise part dimensions, minimizes defects like warping or flash, and optimizes cooling time to boost production rates.
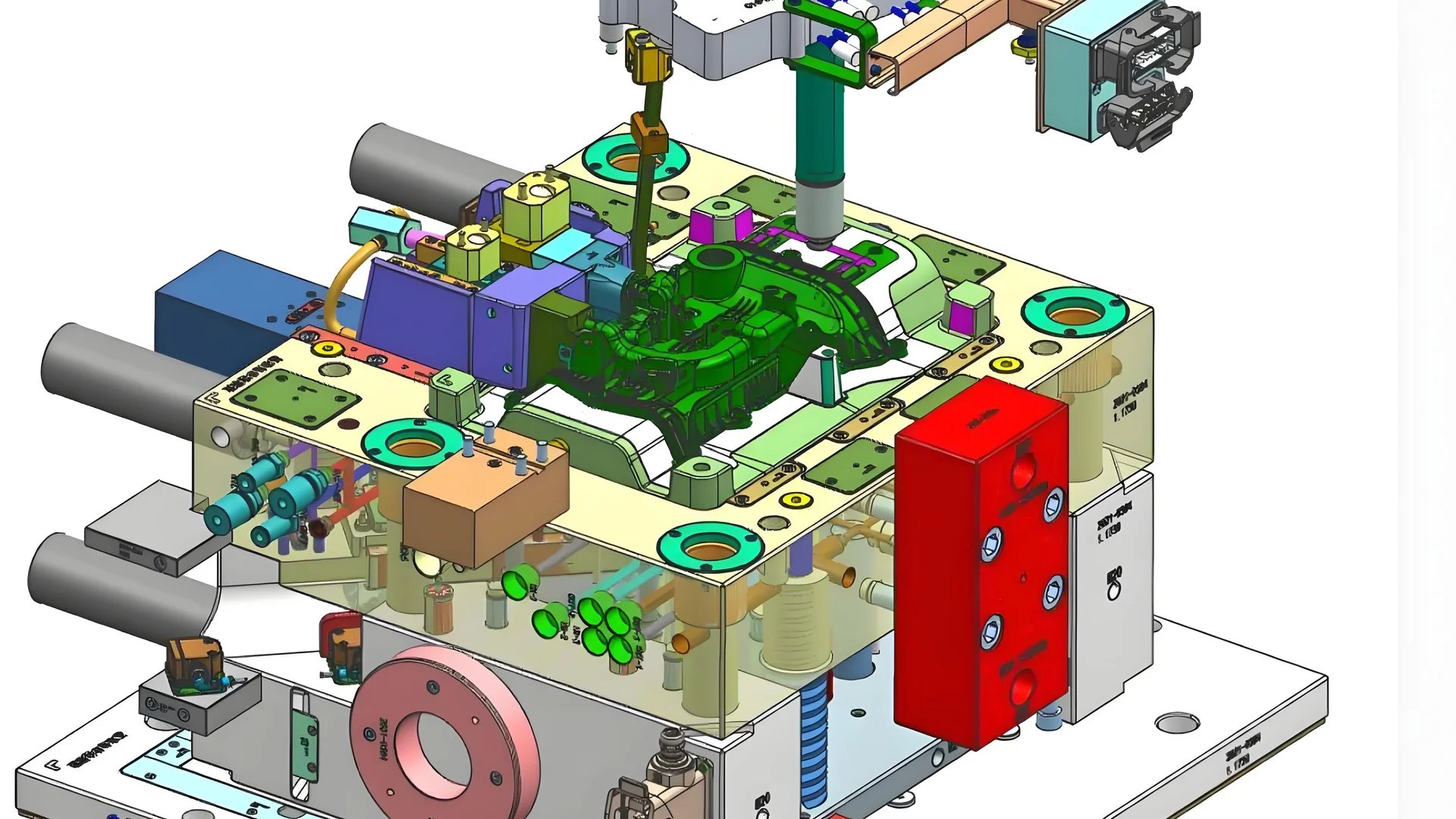
Parting Surface Design
The parting surface of a mold is essential for the final quality of the automotive part. Choosing the correct position for the parting surface can prevent defects and ensure ease of demolding. Ideally, this surface should not intersect with significant functional or aesthetic areas of the part. This parting surface strategy5 helps avoid issues such as flash formation during molding.
Gate Design and Placement
Gate design involves selecting the right type and location for the gate to facilitate optimal plastic flow. Different types of gates, like direct or side gates, can be chosen based on the part’s geometry and material properties. An effective gate design prevents issues like short shots or cavitation and enhances molding efficiency6.
Cooling System Configuration
A well-designed cooling system is vital for rapid and uniform cooling, which directly affects cycle times and part quality. The layout should be optimized according to the part’s shape and wall thickness. Proper cooling channel design can significantly reduce warping and improve production speed.
Simulation Analysis for Mold Design
Utilizing CAE software for simulation can preemptively identify potential issues in mold design. By simulating factors like structural strength and flow filling, designers can optimize solutions before physical mold trials, reducing costs and improving design accuracy. This approach also allows for adjustments in cooling strategies7 and gate placements based on simulated outcomes.
Through strategic planning in parting surface selection, gate design, cooling configuration, and simulation analysis, mold design becomes a pivotal element in manufacturing high-quality automotive parts.
Mold design does not affect automotive part quality.False
Mold design directly impacts part quality, influencing precision and defect rates.
Simulation analysis reduces costs in mold design.True
Simulating mold designs identifies issues early, reducing trial costs.
Why Is Verification and Optimization Crucial in Design?
In the intricate world of design, ensuring that every component functions flawlessly isn’t just important—it’s essential.
Verification and optimization are critical in design to identify potential issues early, enhance functionality, and reduce costs. By leveraging simulation analysis and sample testing, designers can refine products, ensuring they meet performance and durability standards efficiently.
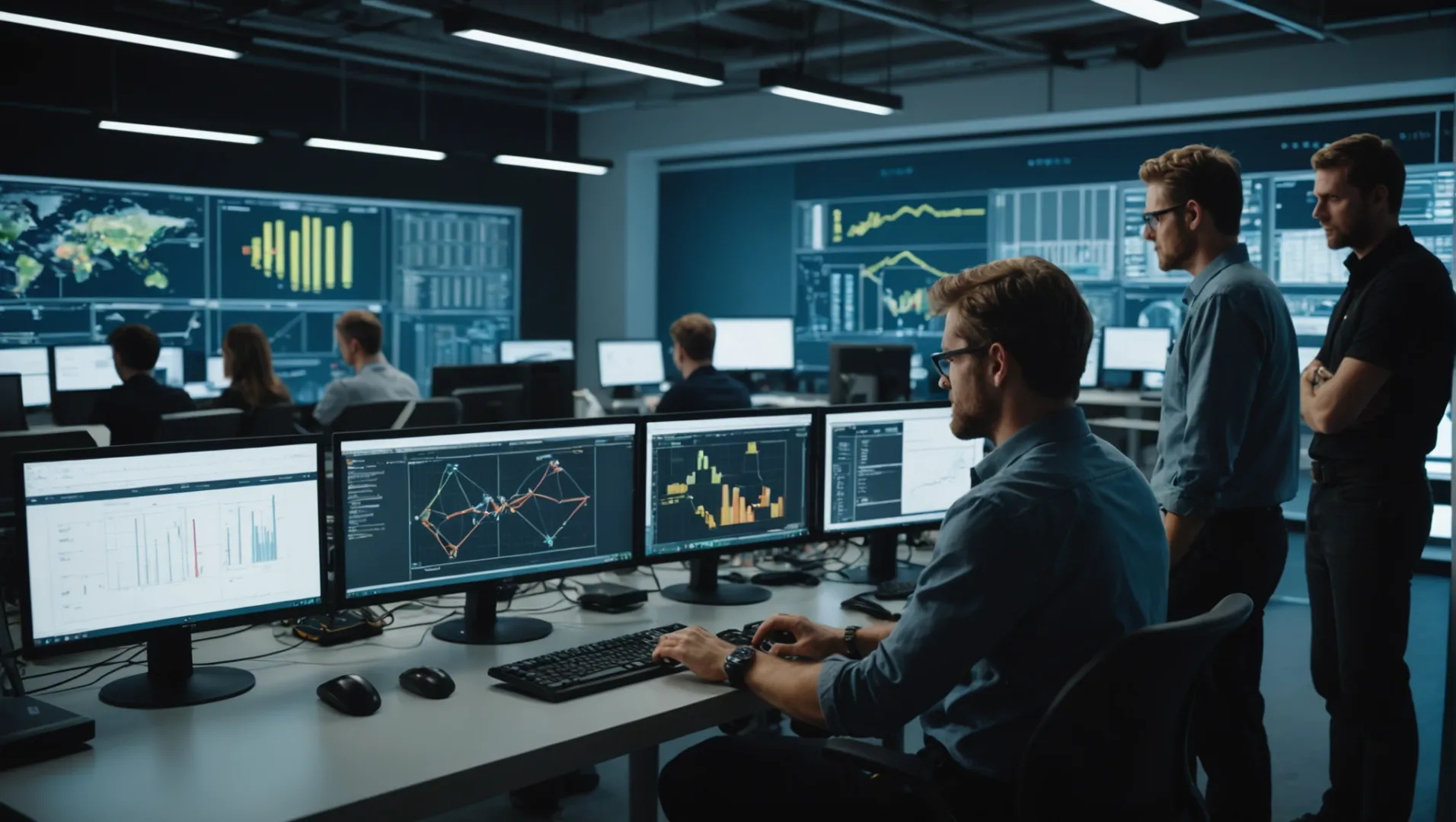
The Role of Simulation Analysis in Design
Simulation analysis serves as a proactive approach in the design phase, allowing engineers to predict how a part will behave under various conditions without physical prototypes. Using computer-aided engineering software8, designers can simulate structural strength, thermal behavior, and material flow.
For instance, in the design of an automotive bumper, simulation can predict how the material will respond to impact, enabling designers to tweak thickness or material choice to enhance safety. This not only reduces trial-and-error in physical testing but also slashes development time and cost.
Sample Testing: From Theory to Reality
Once a design has been optimized through simulations, physical samples are crafted to test real-world performance. This step bridges the gap between digital predictions and tangible results.
Consider an engine cover; it must withstand high temperatures and chemical exposure. Sample tests might involve prolonged heat exposure or immersion in corrosive substances, assessing whether the material retains its integrity. Results from these tests inform further optimizations, ensuring the final product is both reliable and durable.
Cost Implications of Verification and Optimization
Investing in comprehensive verification and optimization initially may seem costly, but it averts expensive modifications later. By identifying design flaws early through simulation analysis9, the need for extensive revisions is minimized, reducing the risk of costly recalls.
Moreover, optimized designs often lead to more efficient manufacturing processes. For instance, a well-optimized cooling system design within a mold can decrease cycle times and energy consumption, yielding significant cost savings over time.
Enhancing Product Longevity and Customer Satisfaction
Thorough verification and optimization also play a vital role in extending product lifespan. By ensuring that parts like door panels or dashboards meet stringent durability criteria through rigorous testing, manufacturers can prevent premature failures.
Ultimately, this not only enhances customer satisfaction but also fortifies brand reputation. Customers tend to favor brands that consistently deliver reliable products, making verification and optimization crucial components in maintaining competitive edge.
Simulation analysis reduces design errors.True
Simulation predicts part behavior, minimizing errors and costly revisions.
Sample testing is unnecessary after simulations.False
Sample testing verifies real-world performance, complementing simulations.
Conclusion
By mastering material selection and adhering to robust design principles, you can elevate the quality of automotive plastic parts while optimizing costs.
-
Discover how material choices affect part performance and durability.: Safety Enhancement. Many plastic materials used in automotive applications offer excellent impact resistance, contributing to enhanced safety for both vehicle … ↩
-
Learn about balancing performance and cost in material selection.: Material Costs: The choice of material significantly impacts the overall cost. While plastics offer versatility and cost-effectiveness, the … ↩
-
Explore how simulations optimize material choice and design.: There are several steps involved in CAE for plastics, from importing a solid model to reading different types of results. Eclipse Product Development Corp., … ↩
-
Explore techniques for maintaining optimal wall thickness in plastic parts.: Walls in any plastic-molded part should be no less than 40 to 60 percent that of adjacent walls, and all should fit within recommended thickness ranges for the … ↩
-
Learn how parting surfaces affect mold quality and minimize defects.: With a reasonable parting surface selection, the mold structure can be simpler, making it easier to mold and release the plastic product, with … ↩
-
Explore effective gate designs to enhance plastic flow and reduce defects.: The gate architecture and its location affects cycle times, tooling costs, lead times, the location of witness marks and many other potential defects. ↩
-
Understand how cooling designs impact cycle times and product quality.: There are two primary types of cooling in injection molding — traditional cooling and conformal cooling. Each one is built on the general … ↩
-
Explore how CAE software enhances design accuracy and efficiency.: Advantages And Disadvantages of Using Computer Aided Design (CAD) · 1. Saves time · 2. Easy to edit · 3. Decrease in error percentage · 4. Decrease design effort · 5 … ↩
-
Discover how early simulations reduce overall product development costs.: Design simulation means fewer prototypes and saves time, effort and, as a result, a great deal of the cost during product development. ↩