Exploring injection molding feels like discovering a secret formula. Every detail must be perfectly arranged. They work together to produce perfect plastic parts.
Injection pressure pushes the plastic melt through the mold. This pressure fills the cavity completely. Holding pressure keeps the material dense. It balances out shrinkage during cooling.
I remember when I first learned these terms. It felt like cracking a code. Injection pressure acts like the engine. It really pushes the plastic through every corner of the mold. Think of moments when a strong push is needed in tough times. This is that push for the plastic. However, if the pressure is too high, chaos happens inside the mold. This results in unwanted bubbles or even burnt spots.
Holding pressure offers steady support. It keeps everything stable as the plastic cools. Think of a friend who stays to ensure everything stays fine. This friend prevents dips or voids from forming. Balancing these pressures changed my design work. It brought consistency and quality. It’s a delicate dance that shapes our products.
Injection pressure fills the mold cavity.True
Injection pressure ensures the plastic melt completely fills the mold.
Holding pressure is not used during cooling.False
Holding pressure maintains material density and compensates for shrinkage.
- 1. What Is Injection Pressure and Why Does It Matter?
- 2. How Does Holding Pressure Affect Product Quality?
- 3. What are common mistakes when setting injection pressure?
- 4. How Can You Optimize Holding Pressure in Injection Molding?
- 5. When Should You Adjust Injection and Holding Pressures?
- 6. Conclusion
What Is Injection Pressure and Why Does It Matter?
Have you ever thought about how small details like pressure affect the final product in injection molding?
Injection pressure is the force used in injection molding to fill mold spaces. This pressure helps the material move and fill smoothly. It is very important for keeping the product’s quality high. It also probably affects the product’s size and stops defects.
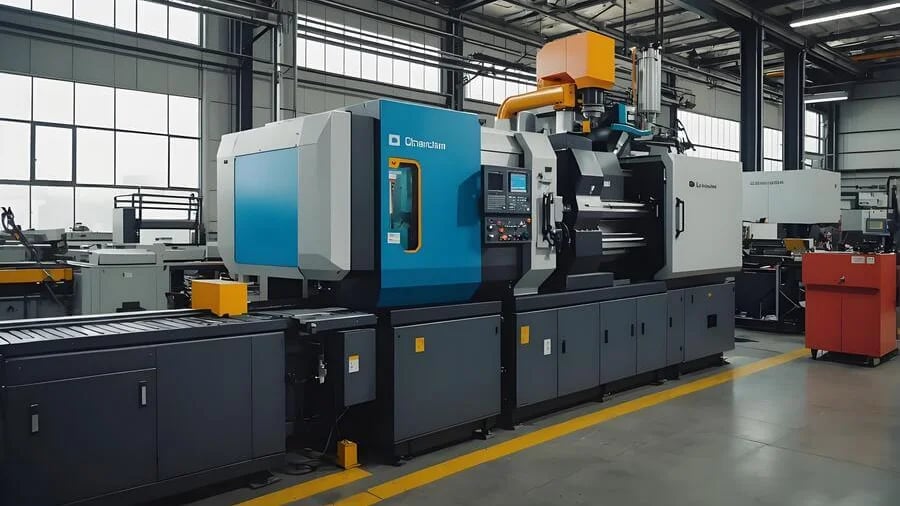
Understanding Injection Pressure
I remember my first experience with mold design. The simple idea of injection pressure really changes the success of a product. Injection pressure is the key force that pushes the molten plastic through the nozzle. It moves through the complex paths of runners before finally reaching the mold cavity. Imagine trying to push toothpaste back into its tube. It requires the right amount of force to do it smoothly without causing a mess.
Functionality:
- High injection pressure is essential for thin-walled or complex shapes. My experience shows that this fills every corner, stopping problems like underfill.
Impact on Molding Process
Injection pressure’s role in molding resembles an artist with a brush. Too much paint or pressure ruins the canvas. Excessive pressure causes turbulence, resulting in defects like air pockets or uneven surfaces. Too little pressure leaves you with an incomplete piece.
Pressure Level | Effect |
---|---|
Too High | Air entrapment, surface defects |
Too Low | Incomplete filling |
Pressure Holding Pressure
One time, I had a batch of products that looked perfect until they cooled. I learned to value holding pressure. After filling, this pressure gently holds your product while it cools, ensuring it keeps its shape and density. This step stops shrinkage marks that can ruin the product’s surface.
Considerations:
-
Too much holding pressure leads to stress and possibly warping.
-
Too little causes shrinkage marks.
Finding the right balance between injection and holding pressures is crucial. This strategy helps in crafting high-quality products without defects. It’s not just about technical skills; it’s also about understanding the art behind engineering.
By mastering these techniques, many manufacturers achieve incredible precision in molded components, meeting both aesthetic and functional needs in products like consumer electronics. Such knowledge is valuable for professionals in design and manufacturing roles as it offers pathways to innovate and improve production processes.
Whether you are experienced or just beginning, understanding these pressures can change your approach to product design.
High injection pressure prevents underfill issues.True
High pressure ensures complete filling of the mold, preventing underfill.
Excessive injection pressure reduces surface defects.False
Excessive pressure can cause turbulence, leading to surface defects.
How Does Holding Pressure Affect Product Quality?
Explore the hidden details of injection molding. Holding pressure influences product quality. Precision and strength develop from this process. Holding pressure really shapes these qualities.
Pressure in injection molding is applied after the cavity fills. This keeps density even. It also stops shrinkage. Stability improves with pressure. Proper control prevents defects. Warping or voids might occur without careful management.
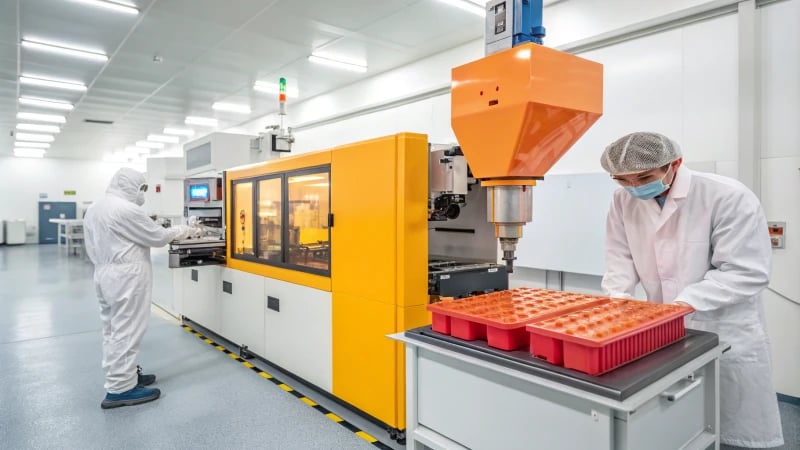
Understanding Holding Pressure
I started learning about injection molding and recognized the importance of holding pressure. It acts like a silent hero that keeps everything stable when the plastic fills the mold. Then it stays stable as the plastic cools. When baking, it’s similar to keeping the cake a bit longer in the oven to stay perfect. Holding pressure keeps the density even. It helps avoid dents or voids. This is crucial for designs with thick walls.
Holding Pressure Benefits | Description |
---|---|
Density Uniformity | Ensures consistent density throughout the product, crucial for structural integrity. |
Dimensional Stability | Maintains product dimensions by countering plastic shrinkage. |
Defect Reduction | Minimizes shrinkage marks and warping. |
Effects on Molding Process
Balancing holding pressure size and time was a challenge for me early on. I once used too much pressure on a test mold; it warped after cooling. It was costly but taught me a lot.
- High Holding Pressure: Causes overflow or flying edges at parting lines.
- Low Holding Pressure: Results in shrinkage marks and poor accuracy.
Finding the perfect balance is crucial for defect-free products that are both attractive and durable. The effect on the molding process4 involves managing these pressures to achieve precision without defects.
Practical Implications for Designers
Designers like me need to grasp holding pressure’s role, which helps create designs that look good and suit mass production. CAD tools are helpful in simulating pressure effects on designs.
- Injection Pressure: Fills molds, crucial for complex molds where more pressure stops short shots.
- Pressure Dynamics: Knowledge improves manufacturing by reducing bubbles or scorching.
Designers use this knowledge to optimize settings, leading to high-quality products and success in competitive markets by improving manufacturing processes5.
High holding pressure causes mold overflow.True
Excessive pressure can lead to material spilling over the mold edges.
Low holding pressure improves product accuracy.False
Insufficient pressure fails to compensate for shrinkage, reducing accuracy.
What are common mistakes when setting injection pressure?
I experienced how a small change in injection pressure controls the success or failure of a molding process. This adjustment truly plays a crucial role.
Common mistakes in setting injection pressure involve using very high or very low pressure. Ignoring material properties also causes errors. Not adjusting for mold complexities is another common error. Such mistakes probably lead to defects. They really affect product efficiency.
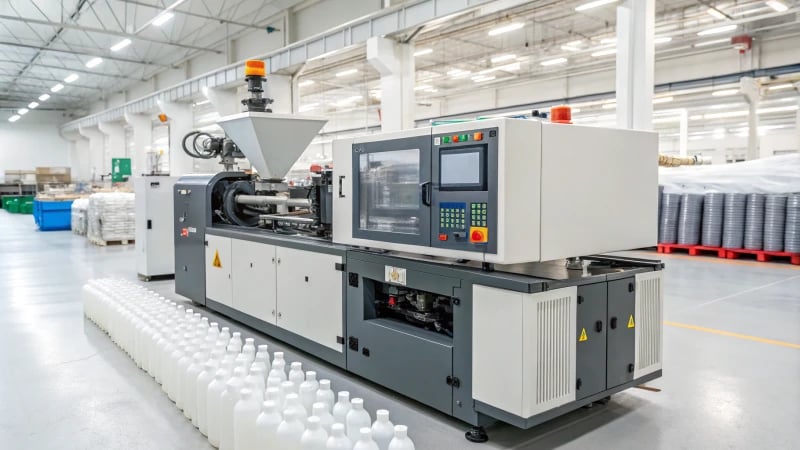
Misjudging Material Properties
A common error is not considering how each material is different. When I began designing molds, I did not realize how important it was to adjust pressure settings for the specific plastic. Materials with high viscosity6 need more force to move smoothly through the mold. If you get this wrong, it might lead to a perfect piece or one full of defects. This error can truly change everything.
Overlooking Mold Design
Mold design combines art with science, particularly with detailed features or thin walls. I once worked on a project with a complicated shape. It taught me the importance of precise pressure settings. Ignoring this leads to short shots7 or surface flaws, causing frustration after hard work. A simple table helped me during those times:
Mold Type | Recommended Pressure Range |
---|---|
Thin-walled | 900-1200 psi |
Thick-walled | 700-900 psi |
Complex shapes | 1000-1300 psi |
Ignoring Temperature Interactions
Temperature has a big role in molding, acting like a secret ingredient in a dish. It truly influences the outcome. The connection between injection pressure and temperature is vital; ignoring this causes issues like warping or incomplete fills. Balancing these aspects maintains dimensional accuracy8. I focus on this balance in every project. It is necessary.
Skipping Pressure Adjustment
Early in my career, I learned that keeping injection pressure the same is a recipe for disaster. Constantly checking and adjusting in real-time avoids defects like trapped air or unnecessary stress in the product. This teaches adaptability and has saved me many headaches.
Mistakes in setting injection pressure are not just technical errors; they are chances for growth and learning. By looking at industry standards9 and using simulations, I have improved my skills. This has led to increased efficiency and much better results.
High viscosity materials need lower injection pressure.False
High viscosity materials require higher pressure for smooth mold flow.
Ignoring temperature can cause incomplete fills in molding.True
Temperature affects melt flow; ignoring it can lead to fill issues.
How Can You Optimize Holding Pressure in Injection Molding?
Ever thought about how to adjust holding pressure in injection molding to get excellent plastic parts? I want to share some insights and personal tips. These tips could really improve your manufacturing skills.
Optimizing holding pressure in injection molding involves adjusting pressure settings. This helps to accommodate material shrinkage. Consistent density results. Fewer defects, such as shrink marks, occur. Correct holding pressure leads to higher product quality. Dimensional accuracy improves very much.
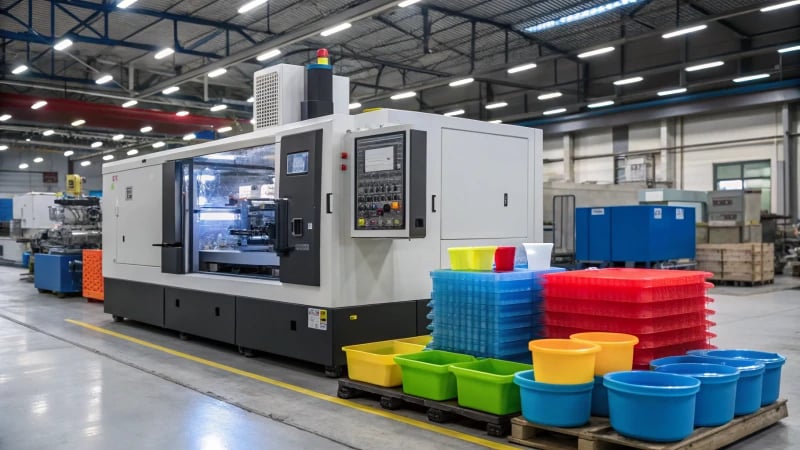
Understanding Holding Pressure
When I first tried injection molding, the importance of holding pressure became clear to me. Holding pressure is applied after the mold cavity is filled to compensate for material shrinkage during cooling. It ensures that the plastic10 remains dense and stable, preventing defects like voids or shrink marks.
Key Factors in Optimization
Factor | Impact on Process |
---|---|
Material Type | Different plastics require unique pressure settings for uniformity. |
Part Geometry | Complex shapes may need adjusted pressures to ensure full filling. |
Cooling Time | Longer cooling times can affect pressure distribution and final form. |
Adjusting Holding Pressure
-
Assess Material Needs
- At first, different materials’ shrinkage rates confused me. But understanding them becomes easy with practice. For example, nylon requires higher holding pressures due to its high shrinkage rate.
-
Monitor Injection Pressure
- My mentor said that adjustments in injection pressure11 directly affect holding pressure requirements. High initial injection pressures may necessitate lower holding pressures to prevent defects.
-
Implement a Stepwise Approach
- I tried varying pressure settings slowly to see quality changes. Gradually increase or decrease holding pressure while monitoring product quality. This trial-and-error method helped find the best settings without losing efficiency.
Analyzing Effects on Product Quality
-
Residual Stress
- Too much holding pressure adds stress to the material, leading to residual stress and warping risks, which I learned by experience. Precise adjustments help maintain structural integrity.
-
Dimensional Accuracy
- Correctly set holding pressures ensure that the product maintains its intended dimensions, crucial for components with precise specifications.
Practical Application
Simulation software really changed things for me by allowing modeling of different scenarios and assessing the effects of various holding pressures on mold design before production started. This proactive approach saved time and reduced material waste by optimizing settings beforehand.
By following these strategies, you can optimize the holding pressure settings in your injection molding process, leading to better product quality and reduced manufacturing costs—especially vital for complex or high-demand items where quality cannot be compromised. Implementing these practices has given me reliable results during production, enhancing both efficiency and product reliability.
Nylon requires lower holding pressure in molding.False
Nylon actually requires higher holding pressures due to high shrinkage.
Simulation software aids in optimizing molding pressure.True
Simulations model scenarios to refine pressure settings pre-production.
When Should You Adjust Injection and Holding Pressures?
Have you ever stood in the middle of a molding process, looking at defects and wondered if you should adjust the pressure settings?
Adjusting injection pressures is vital for thin-walled or complex molds. This prevents underfills. Likewise, adjusting holding pressures gives products uniform density. It reduces shrinkage marks in thick-walled items. These changes greatly improve product quality. Efficiency really benefits from these adjustments.
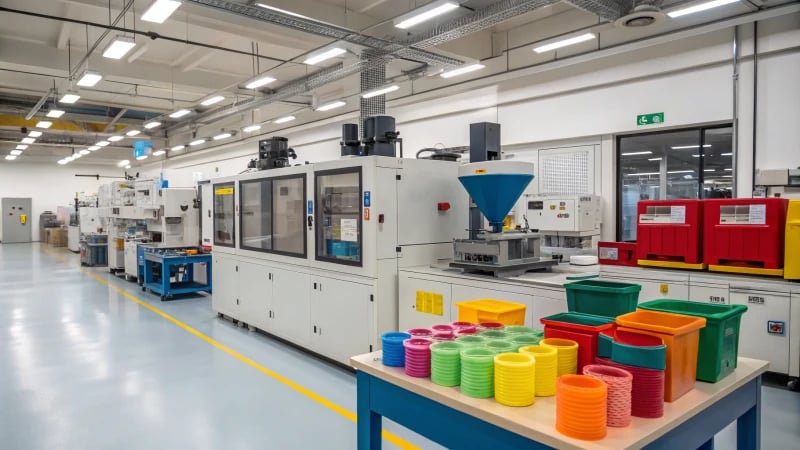
Understanding Injection Pressure Adjustments
Injection pressure plays a vital role in pushing the plastic melt through the mold cavity. It’s like trying to squeeze the last bit of toothpaste out of a tube. The goal is to fill every nook and cranny. For thin-walled or intricately designed products, like thin-walled reinforcement products12, this pressure must be high enough to prevent underfills. But too much pressure can cause air bubbles, burn marks, or even deform the mold cavity.
Finding the right pressure that fills effectively without causing problems is essential.
When to Tweak Holding Pressure
Holding pressure matters after the initial fill. It acts as a helper during the cooling phase. This pressure compensates for any shrinkage. Thick-walled products, like those in consumer electronics13, rely on this pressure to stay strong. Imagine inflating a balloon just right – not too much, not too little. With too much pressure, the product may warp; too little leads to shrinkage issues.
Practical Examples with Tables
Scenario | Injection Pressure | Holding Pressure |
---|---|---|
Thin-walled products | High | Moderate |
Complex designs | High | Low |
Thick-walled products | Moderate | High |
This table has guided me many times. Jacky from Canada, an expert, also finds balance in pressure settings essential for avoiding costly mistakes. By understanding how these pressures affect the molding process, we probably troubleshoot like experts and refine techniques effectively.
Balancing these pressures resembles perfecting a recipe. Every change improves the final product without lowering its quality. Whether you’re a newbie or seasoned designer like Jacky14, these insights might help you optimize your molding processes.
High injection pressure prevents short shots.True
High pressure ensures the melt fills the cavity, preventing underfills.
Excessive holding pressure reduces shrinkage marks.False
Excessive pressure causes stress and warping, not shrinkage reduction.
Conclusion
Injection pressure fills the mold, while holding pressure maintains density during cooling. Balancing both is crucial for producing high-quality plastic parts without defects.
-
This link explores how injection pressure influences mold cavity filling, ensuring complete and defect-free products. ↩
-
Discover how varying injection pressures impact the dimensional accuracy of molded products. ↩
-
Learn about optimal injection pressure levels for various materials to avoid defects. ↩
-
Explore how proper management of holding pressure impacts the molding process to enhance product quality. ↩
-
Understand how injection pressure dynamics influence mold design to prevent common defects like short shots and air entrapment. ↩
-
Understanding how high-viscosity plastics behave under different pressures helps avoid common molding issues. ↩
-
Discovering solutions for short shots can guide you in adjusting pressure settings effectively. ↩
-
Maintaining dimensional accuracy prevents defects and ensures consistent quality across products. ↩
-
Industry standards offer guidelines for optimal pressure settings, enhancing process efficiency. ↩
-
Understanding plastic density helps optimize holding pressure, ensuring uniformity and reducing defects. ↩
-
Learn how injection pressure adjustments impact product quality and help optimize the molding process. ↩
-
Understanding thin-walled reinforcement products helps optimize injection pressure settings to prevent underfills and ensure product quality. ↩
-
Exploring the injection molding process in consumer electronics reveals how holding pressure adjustments impact product quality. ↩
-
Learning about effective techniques aids designers like Jacky in refining injection and holding pressure adjustments for optimal results. ↩