Overflow in injection molding isn’t just a technical hiccup; it can impact the quality of the products we create. Let me share how I learned to navigate these challenges.
To prevent overflow in injection molding, ensure precision in mold design, maintain optimal injection pressures and speeds, select appropriate materials, and regularly service equipment. These practices reduce the risk of flashing, enhancing product quality and production efficiency.
While these foundational steps are essential, there’s so much more to uncover. Let’s dive deeper into each aspect and explore nuanced strategies that not only enhance product quality but also prolong the life of your molds and equipment.
Precise mold design prevents overflow in injection molding.True
Precision in mold design ensures tight closures, reducing gaps that cause overflow.
What Role Does Mold Design Play in Preventing Overflow?
Understanding the intricacies of mold design can significantly mitigate overflow in injection molding processes.
Mold design plays a crucial role in preventing overflow by ensuring precise parting surfaces, appropriate cavity sizes, and regular maintenance. These factors help maintain tight closures and prevent gaps that lead to flashing.
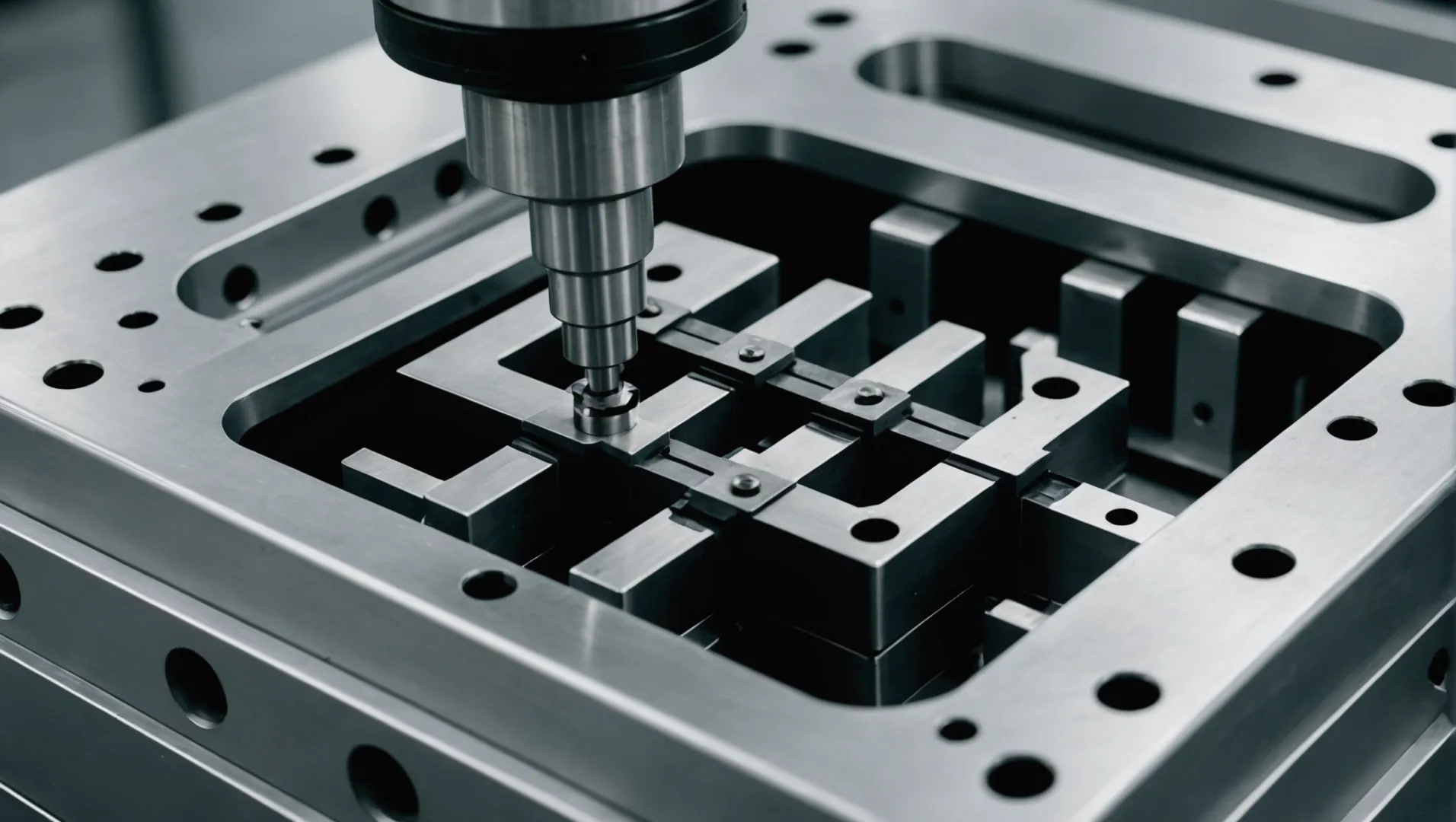
Precision in Mold Parting Surfaces
One of the primary considerations in mold design is ensuring the precision of the parting surfaces1. The parting surface must fit tightly with high flatness and finish to avoid any gaps that could lead to overflow. Uneven or imprecise surfaces are notorious for causing flashing, where molten plastic escapes the intended cavity space. Regular checks and fine-tuning can keep these surfaces in optimal condition.
Appropriate Mold Cavity Design
A well-designed mold cavity is essential for avoiding overflow. The cavity size should be calculated meticulously according to the size requirements of the product. Strict tolerance control is necessary to ensure that the cavity does not deviate from specified dimensions, which could lead to overflow. For instance, designing a mold with exact tolerances for thin-walled products can prevent excess material from filling areas it shouldn’t.
Aspect | Importance |
---|---|
Parting Surface Fit | Ensures tight closures |
Cavity Size | Prevents material excess |
Tolerance Control | Reduces deviation |
Importance of Mold Maintenance
Regular maintenance is as crucial as design itself. Checking for wear, especially in active parts like sliders and guide pillars, is vital. Worn parts can affect the closure precision, leading to gaps where overflow may occur. Additionally, cleaning any residue from the mold’s parting surface after each production cycle helps maintain a perfect seal during future operations.
Case Study: Reducing Flashing through Design
Consider a company facing frequent flashing issues. By recalibrating their mold design to incorporate tighter parting surfaces and maintaining a rigorous cleaning schedule, they managed to cut down on overflow incidents by 40%. This example highlights how strategic design adjustments can have a tangible impact on production quality and efficiency.
In summary, mold design is foundational in preventing overflow during injection molding. Regular inspection and maintenance2, along with precise design specifications, ensure that molds function efficiently and produce high-quality products without defects like flashing.
Precise parting surfaces prevent mold overflow.True
Precision in parting surfaces ensures tight closures, preventing gaps.
Regular mold maintenance is unnecessary for preventing overflow.False
Maintenance prevents wear that could cause gaps and overflow.
How Can Injection Pressure and Speed Be Optimized?
Optimizing injection pressure and speed is vital in minimizing defects and enhancing the efficiency of the injection molding process.
To optimize injection pressure and speed, adjust settings based on material properties, product design, and process stages. Employing multi-stage pressure and segmented speed control can significantly improve product quality and reduce defects.
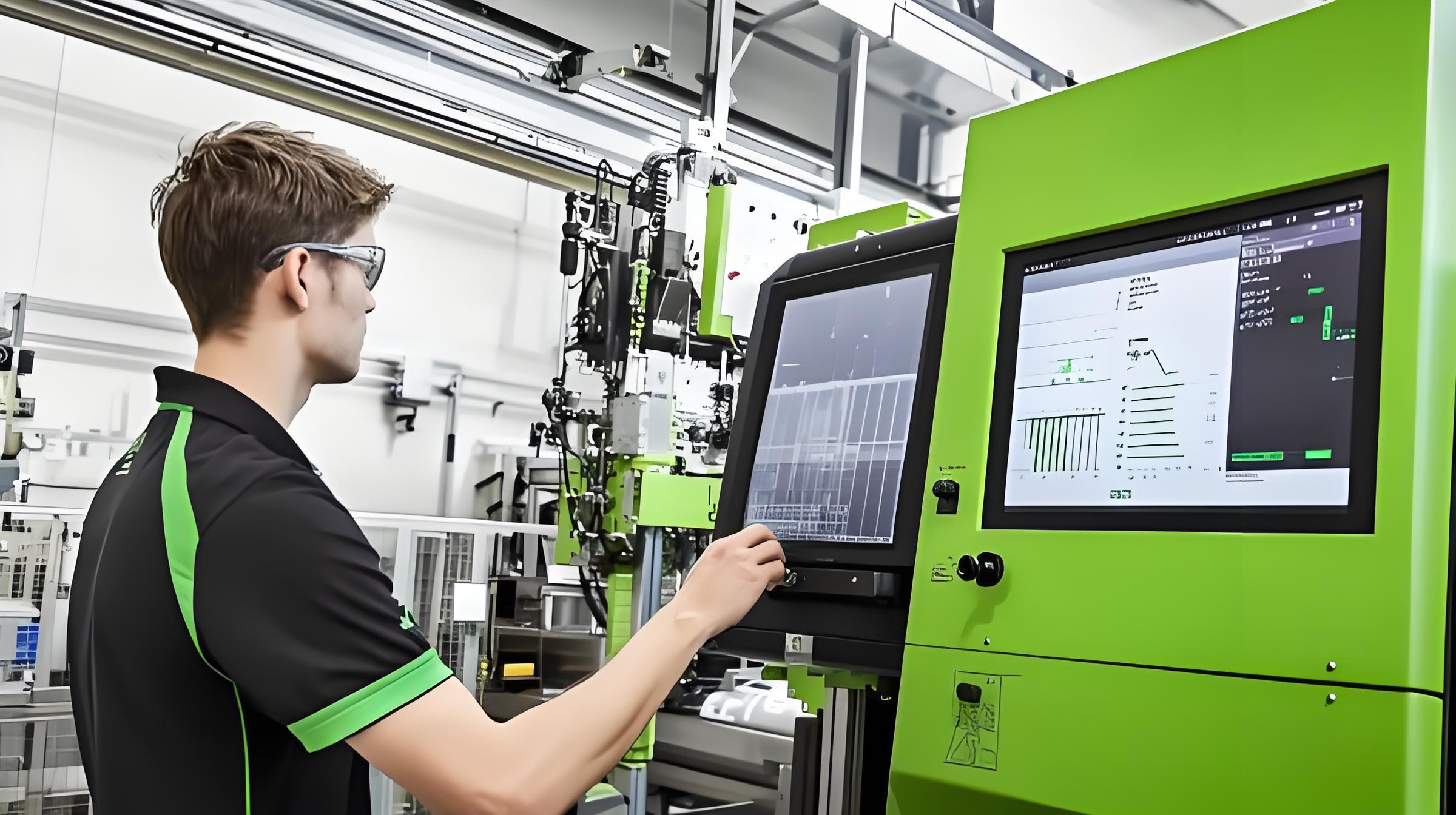
Understanding Injection Pressure
Injection pressure plays a pivotal role in filling the mold cavity efficiently. The key is to balance the pressure based on the product specifications3, material properties, and the complexity of the mold.
-
Low vs. High Pressure: Low pressure may result in incomplete filling, leading to weak parts, while high pressure increases risks of defects like flashing. For thin-walled products, adjust the pressure lower to prevent overflow.
-
Multi-stage Pressure: Using a multi-stage injection pressure approach allows the mold cavity to be filled with a lower initial pressure before gradually increasing it. This method minimizes the risk of overflow while ensuring even distribution of material.
Adjusting Injection Speed
Injection speed impacts the flow of material into the mold. Just like with pressure, it’s about finding the right speed that complements the material’s properties and mold design.
-
Appropriate Speed Selection: Choose an injection speed that matches the shape, size, and material attributes of the product. For intricate designs, slower speeds prevent uneven filling.
-
Segmented Injection Speed: Implementing segmented speed control divides the injection into phases, allowing for tailored speed adjustments at each stage. This approach helps manage flow dynamics better, reducing potential defects.
Practical Example: Multi-stage Pressure and Segmented Speed
Consider a scenario where you have a complex mold with varying thickness. By employing a multi-stage pressure system:
- Initial Filling: Start with a lower pressure to fill the thicker sections without causing stress marks or warping.
- Secondary Filling: Increase pressure to ensure thinner areas are fully packed.
For segmented speed control:
- Begin with a slower speed to fill intricate sections smoothly.
- Gradually increase speed for areas requiring rapid fill to maintain pace without compromising quality.
The synergy between multi-stage pressure and segmented speed control not only enhances product quality but also extends mold life by reducing wear.
The Importance of Monitoring and Adjustment
Constant monitoring and adjustment are crucial. Employ real-time monitoring systems to track parameters like temperature fluctuations4 and equipment wear.
Regularly reviewing these aspects ensures that the process remains within optimal conditions, adapting to any changes in material properties or environmental conditions.
Optimizing injection pressure and speed not only boosts production efficiency but also reduces wastage and enhances product quality.
Multi-stage pressure reduces defects in molding.True
Using multi-stage pressure balances initial and secondary filling, reducing defects.
High injection speed is ideal for intricate designs.False
Slower speeds are better for intricate designs to prevent uneven filling.
Why Is Material Selection Crucial in Injection Molding?
Choosing the right material for injection molding is vital for ensuring product quality and production efficiency.
Material selection in injection molding is crucial because it directly influences the product’s structural integrity, aesthetic quality, and manufacturing efficiency. Selecting the right material ensures optimal flow characteristics, minimizes defects like flashing, and aligns with the product’s functional requirements.

Understanding Material Properties
When selecting materials for injection molding5, understanding their properties is fundamental. Plastics vary widely in terms of thermal stability, mechanical strength, and flow characteristics. For instance, materials like Polypropylene (PP) are favored for their chemical resistance and flexibility, while Polycarbonate (PC) is chosen for its high impact resistance and optical clarity.
-
Thermal Properties: Materials must withstand the heat generated during molding without degrading. For example, materials like PEEK can endure high temperatures, making them suitable for industrial applications.
-
Mechanical Strength: The material must possess sufficient strength to meet the product’s functional demands. ABS is commonly used where strength and toughness are critical.
The Impact of Material Fluidity
Fluidity determines how well the material fills the mold cavity. Choosing a plastic with the right fluidity ensures uniformity and reduces defects. Materials with high fluidity, such as Nylon, are ideal for complex shapes but may require careful control to avoid issues like flashing6.
Material | Fluidity | Common Applications |
---|---|---|
Polypropylene (PP) | High | Packaging, automotive components |
ABS | Medium | Electronics, appliance housings |
Polycarbonate (PC) | Low | Lenses, safety helmets |
Influence on Product Aesthetics and Performance
The choice of material not only affects the structural aspects but also the product’s appearance and performance. Plastics come in different finishes and colors, impacting the final look of the product. For products requiring high aesthetic value, such as consumer electronics, choosing a material like Acrylic can enhance clarity and gloss.
Additionally, some applications demand specific performance characteristics, such as UV resistance or electrical conductivity. Materials like PVDF are used for applications requiring chemical resistance and electrical insulation.
- Aesthetic Quality: Materials must align with design specifications, ensuring that the end product meets visual expectations.
- Performance Requirements: Specialized plastics are chosen to meet specific environmental or functional conditions.
By considering these factors, manufacturers can significantly enhance their production efficiency and product quality while minimizing defects and extending the lifespan of both the product and the manufacturing equipment.
Polypropylene is ideal for high-impact applications.False
Polycarbonate, not Polypropylene, is preferred for high impact resistance.
ABS is used for products requiring high toughness.True
ABS is known for its strength and toughness, suitable for durable products.
How Does Equipment Maintenance Influence Injection Molding Quality?
Regular equipment maintenance is pivotal in ensuring the quality of injection molded products by preventing defects like flashing and improving consistency.
Equipment maintenance in injection molding ensures machine precision, stability, and proper functioning, directly influencing product quality. Regular checks on components such as screws, barrels, and nozzles, along with parameter adjustments, are vital to avoid defects and maintain optimal production efficiency.

Importance of Regular Equipment Checks
Injection molding machines are complex systems with numerous moving parts, each contributing to the overall quality of the final product. Regular maintenance checks7 ensure that components such as screws, barrels, and nozzles are functioning optimally. A worn screw or barrel can lead to inconsistent material flow, which might result in defective products.
Moreover, precise alignment of these components is crucial to maintain the stability and accuracy of the machine. Misalignment can cause uneven pressure distribution during molding, leading to defects such as flashing or incomplete filling.
Parameter Adjustments
Accurate adjustment of machine parameters is another critical aspect of equipment maintenance. These parameters include injection pressure, speed, and temperature. If not precisely set, they can cause defects or inefficient production cycles. For instance, incorrect pressure settings might result in excessive flash, while inappropriate temperature control can alter the material’s properties, affecting the end product’s strength and appearance.
Parameter | Impact on Product Quality |
---|---|
Pressure | Controls material flow; prevents excessive flash |
Speed | Affects fill time; crucial for thin-walled items |
Temperature | Influences material viscosity and product finish |
Lubrication and Cleaning Practices
Regular lubrication of moving parts reduces friction and wear, extending the lifespan of machinery. Meanwhile, thorough cleaning ensures there are no material residues that could interfere with the next production run. Cleaning practices should focus on critical areas such as the mold parting surface and vents to avoid unwanted contamination.
Conclusion
In summary, diligent equipment maintenance in injection molding is essential for sustaining high-quality output. By ensuring that machines are accurately adjusted and regularly maintained, manufacturers can prevent defects and achieve greater consistency in their products.
Understanding the nuances of equipment maintenance not only aids in quality control but also enhances overall production efficiency and cost-effectiveness.
Regular maintenance prevents defects in injection molding.True
Regular maintenance ensures machine precision, reducing defects like flashing.
Misaligned components do not affect injection molding quality.False
Misalignment causes uneven pressure, leading to defects such as flashing.
Conclusion
Implementing these strategies can significantly reduce overflow issues in injection molding. By refining processes and maintaining equipment, manufacturers can enhance product quality and operational efficiency, leading to better outcomes.
-
Explore how precision prevents gaps and ensures product quality.: With a reasonable parting surface selection, the mold structure can be simpler, making it easier to mold and release the plastic product, with … ↩
-
Learn why consistent maintenance extends mold life and prevents defects.: Regular, careful injection mold maintenance can prevent part failures and lower the overall cost of your injection molding program. ↩
-
Learn how product specs influence optimal injection pressure settings.: Too low pressure will cause incomplete mold filling, leading to voids and air pockets. These effects weaken the product’s structural integrity … ↩
-
Discover benefits of monitoring systems in maintaining optimal conditions.: Mold-Masters SmartMOLD is a cloud-based software platform dedicated to the plastics industry providing real-time data to drive injection molding … ↩
-
Explore how different material properties affect injection molding outcomes.: Other Material Properties. Properties other than thermal and mechanical can be important in specific applications. These include electrical properties such … ↩
-
Learn about fluidity’s role in preventing defects like flashing.: Higher temperature makes the fluid more prone to leak due to lower viscosity and resultingly increases the chances of injection molding flash. ↩
-
Explore the benefits of regular maintenance for consistent product quality.: Regular, careful injection mold maintenance can prevent part failures and lower the overall cost of your injection molding program. ↩