Weld lines trouble every mold designer. They ruin the appearance and strength of creations. The real trick to stopping them is the spot where the gate is placed.
Optimize gate position to prevent weld lines by ensuring balanced material flow and placing gates near thick sections or weld-prone areas. Proper positioning minimizes flow disruptions, enhances part strength, and improves cosmetic appearance.
I remember seeing weld lines for the first time. They appeared on a model that needed to be flawless. My hard work spoiled by those stubborn lines was really annoying. But as a determined designer, I started learning about gate positions.
Placing the gate wisely truly changes everything. For example, putting it on a symmetry line of a round object helped the melt spread evenly and nicely. No more annoying lines! Avoiding important areas was key. This trick saved me when I worked on a see-through cover for a project. The gate at the edge kept the view clear without ugly lines.
When designs were more complex, using several gates in sequence helped so much. It feels like guiding music. Changing gate angles and spacing matters, too. It keeps the hot material from cooling or flowing wildly.
Here’s a tip꞉ keep wall thickness even whenever possible. It smooths out cooling and blending, hiding weld lines. Sharp turns in design mean dealing with annoying weld lines again.
These methods changed how I work on every project. Hopefully, they will really help improve your designs too.
Symmetrical gate placement reduces weld lines.True
Placing the gate on the symmetry axis ensures even melt flow, minimizing weld lines.
Sequential gates increase weld line formation.False
Sequential gating controls melt flow, reducing disorder and minimizing weld lines.
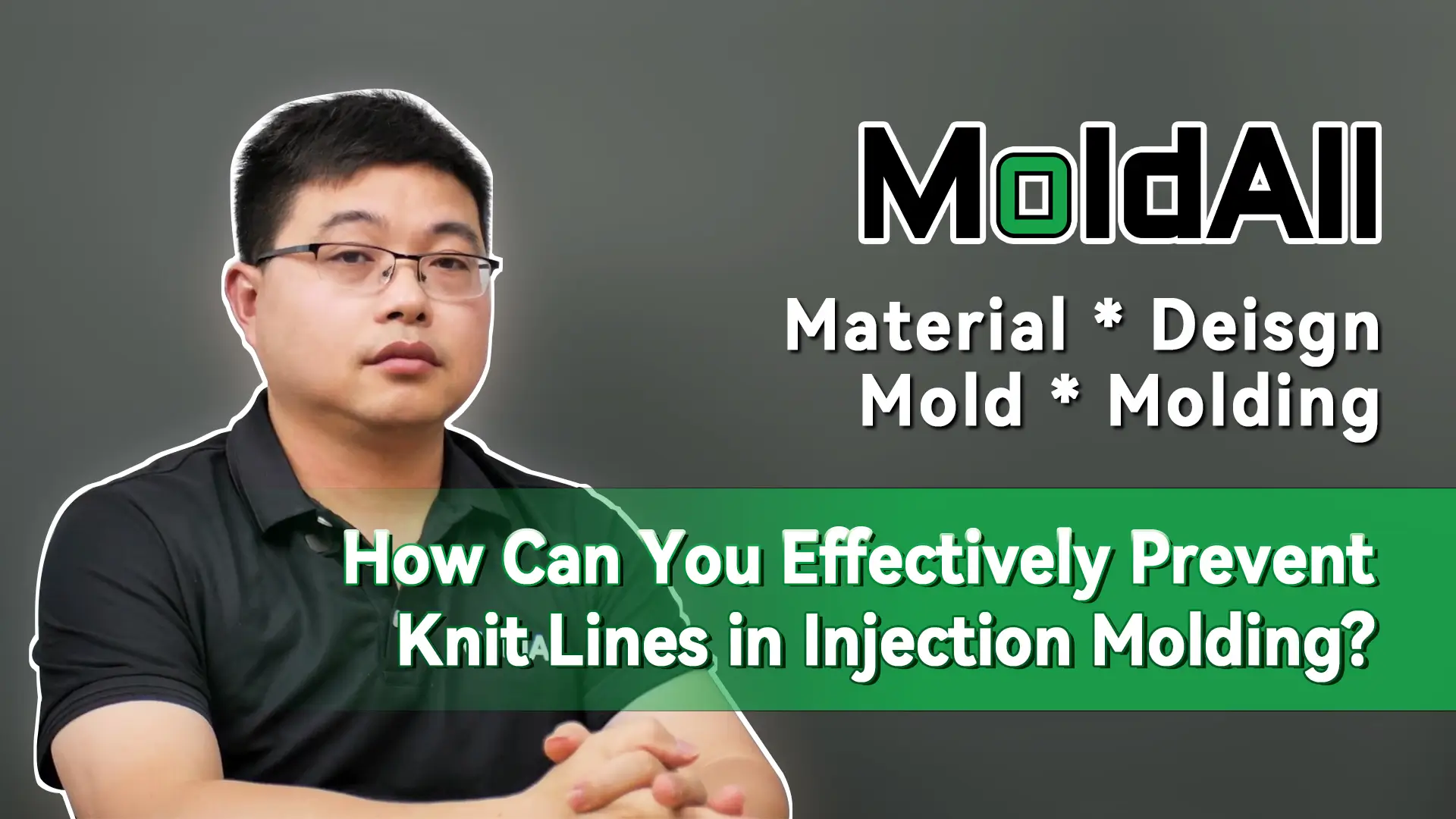
Why is Symmetrical Gate Placement Important in Mold Design?
Do you ever think about how placing gates in molds transforms your manufacturing process? Let’s explore!
Symmetrical gate positions in mold design play a key role in spreading molten material evenly. This even spread reduces defects such as weld lines. The result is more consistent products. Proper flow dynamics matter a lot for top-notch injection molding. Quality stays high.
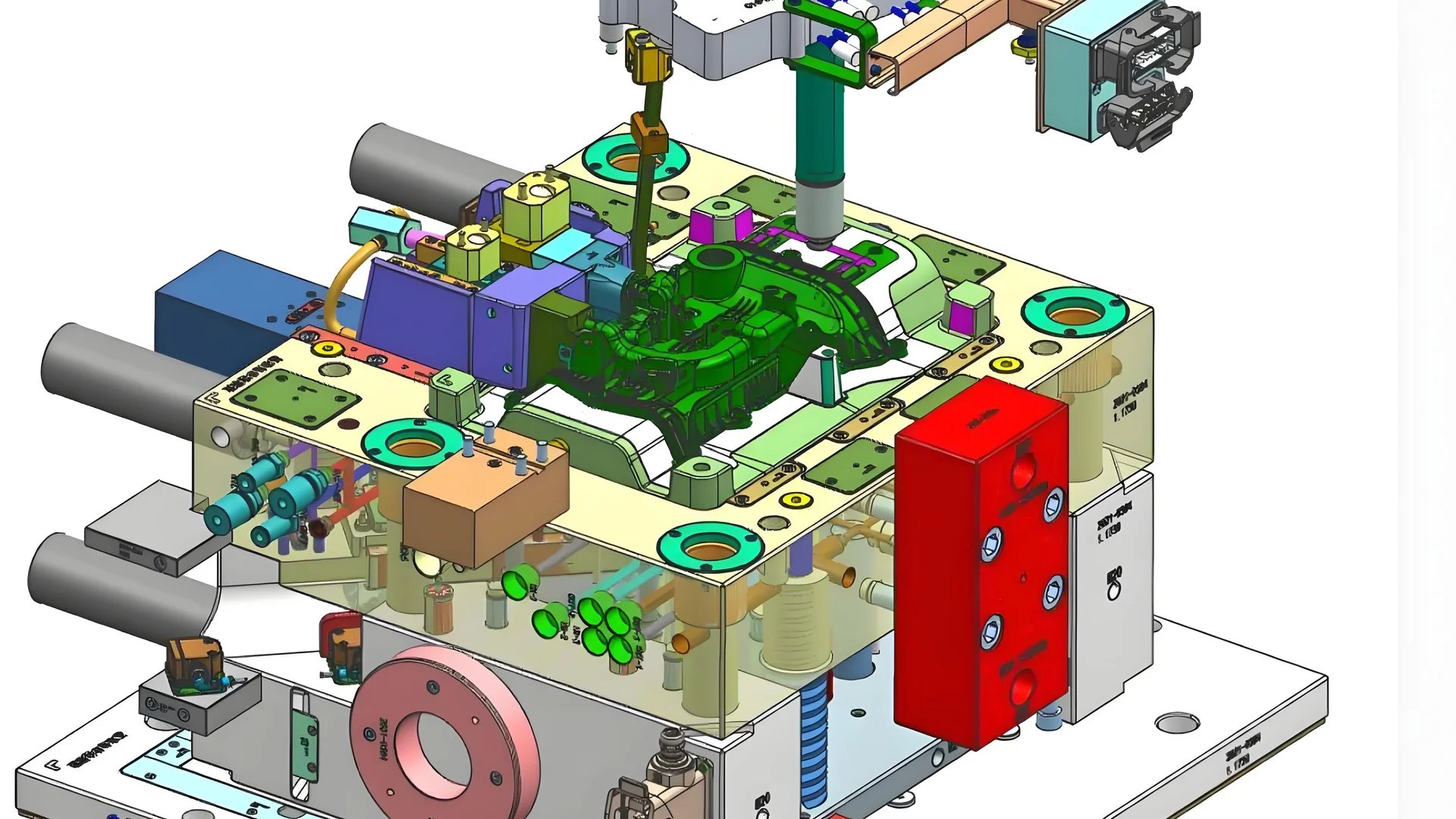
Improving Flow with Balanced Gate Placement
In my years of playing with mold designs, I saw that gate placement really affects how melted material moves in a mold. Imagine pouring water into a bathtub with taps placed randomly. It would be chaotic! But a symmetrical gate setup acts like a well-placed tap that spreads the melt evenly.
Gate Layout Strategies
- Single-Point Gate: For products with matching shapes, placing a single-point gate along the symmetry line helps the melt flow smoothly. It’s like putting a weight exactly in the middle of a seesaw.
- Important Area Avoidance: Do not place gates near areas that need to look nice, like clear parts of plastic objects. This is crucial because weld lines stand out like coffee stains on a white shirt.
Managing Multi-Point Gates
For complex molds, you might use several gates. Setting the right injection order is very important:
- Sequential Injection: Start flow from the farthest gate so the streams merge neatly.
- Gate Spacing and Angles: Correct spacing avoids cooling too quickly. Changing angles makes the flow smoother, similar to steering a boat carefully.
Parameter | Ideal Approach |
---|---|
Symmetrical Shape | Centered gate placement |
Multi-Gate Layout | Sequential opening based on distance |
Critical Areas | Avoid gate proximity to high-performance sections |
Wall Thickness Importance
Keeping wall thickness even hides weld lines. I always choose places where walls are even for the melt to come together. Uniform cooling prevents appearance issues. This approach has really helped me avoid trouble from clients noticing marks after production.
Avoiding Sharp Flow Turns
Sudden turns in the melt flow are like quick turns in traffic. They increase risks, creating weld lines. Placing gates for gentle turns keeps the flow smooth. This is vital for detailed structures.
Learn more about sequential gate setting1 for complex items. The idea of the geometric center2 also helps in improving flow paths.
In conclusion, symmetrical gate placement really improves melt flow and reduces flaws, leading to excellent product quality. By avoiding key areas and considering wall thickness, this method’s success is further increased.
Symmetrical gate placement reduces weld lines.True
Placing gates symmetrically helps melt flow evenly, reducing weld lines.
Sequential gates increase weld line occurrence.False
Sequential gates control melt flow order, reducing weld line formation.
How Does Sequential Gating Reduce Weld Lines in Multi-Gate Designs?
Have you ever thought about how sequential gating changes your injection molding process?
Sequential gating decreases weld lines in multi-gate injection molding by controlling when and how gates open. This technique guides the molten plastic flow more neatly. It stops the melt fronts from meeting too early. The result is stronger and more attractive products.
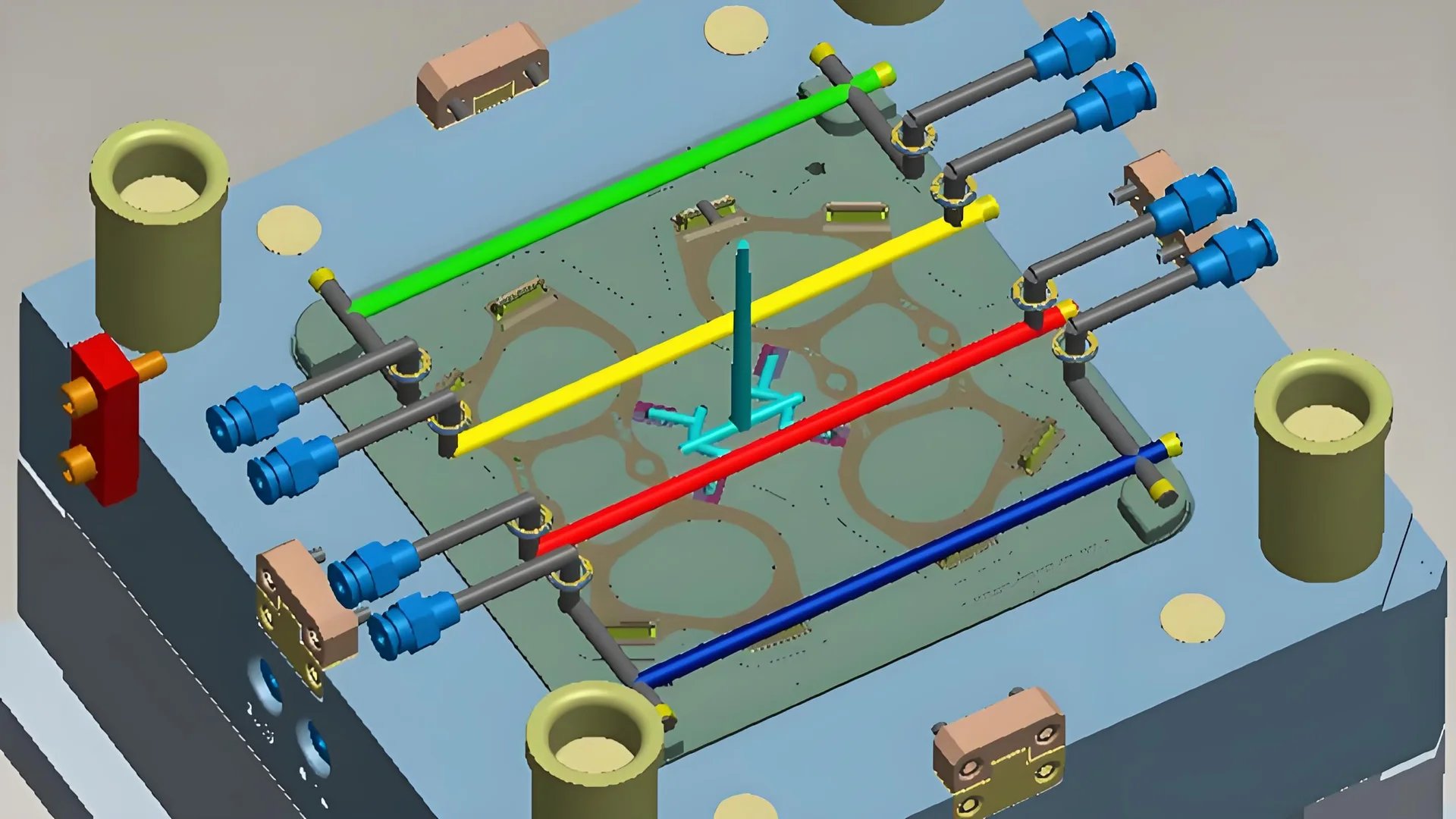
The Principle of Sequential Gating
Picture yourself directing a ballet of hot, flowing plastic as it fills a mold, each movement thoughtful and careful. Sequential gating allows this control. By managing when each gate opens, one guides the material smoothly into the mold. This orderly process lowers the chance of the material clashing early, which often leads to those unwanted weld lines3.
Designing Multi-Gate Systems
Designing a system with several gates feels like piecing together a puzzle. Every gate must sit in the right spot for the plastic to flow evenly. For example, putting a gate in the middle of a round object helps the material spread out evenly, cutting down on possible flaws. It’s really important to keep gates away from spots where looks or strength matter most.
Design Factor | Consideration |
---|---|
Symmetry | Align gates with symmetry axes for even melt flow. |
Critical Areas | Avoid gate placement near visible or load-bearing parts. |
Optimizing Flow Dynamics
Consider adjusting the speed in a musical performance – every gate opens in sync with the others to manage flow. By changing the order and timing, exact points of meeting can be planned where weld lines are less obvious or damaging. This tactic works very well for items with tricky shapes or different wall thicknesses.
Real-World Applications and Benefits
In fields like car manufacturing and electronics, where looks and strength matter a lot, sequential gating becomes incredibly helpful. By opening secondary gates only when needed, weld lines are greatly reduced, leading to items that not only seem better but also last a very long time.
Exploring these techniques provides insights into minimizing defects in plastic components4, enhancing both manufacturing efficiency and product quality. Smartly arranged gate sequences help products reach high-quality levels while cutting down waste and saving costs.
Symmetrical gate layout reduces weld lines.True
Placing gates symmetrically helps melt flow evenly, minimizing weld lines.
Sequential gating increases weld lines in injection molding.False
Sequential gating controls melt flow, reducing weld line formation.
How Does Wall Thickness Affect Gate Positioning?
Have you ever thought about how the thickness of a product’s walls could decide the success or failure of the injection molding process?
Product wall thickness plays an important role in gate positioning during injection molding. Thickness that is the same throughout helps with even cooling. This optimizes material flow. It also reduces defects such as weld lines. When thickness varies, filling might be inefficient. Uneven filling can lead to possible flaws.
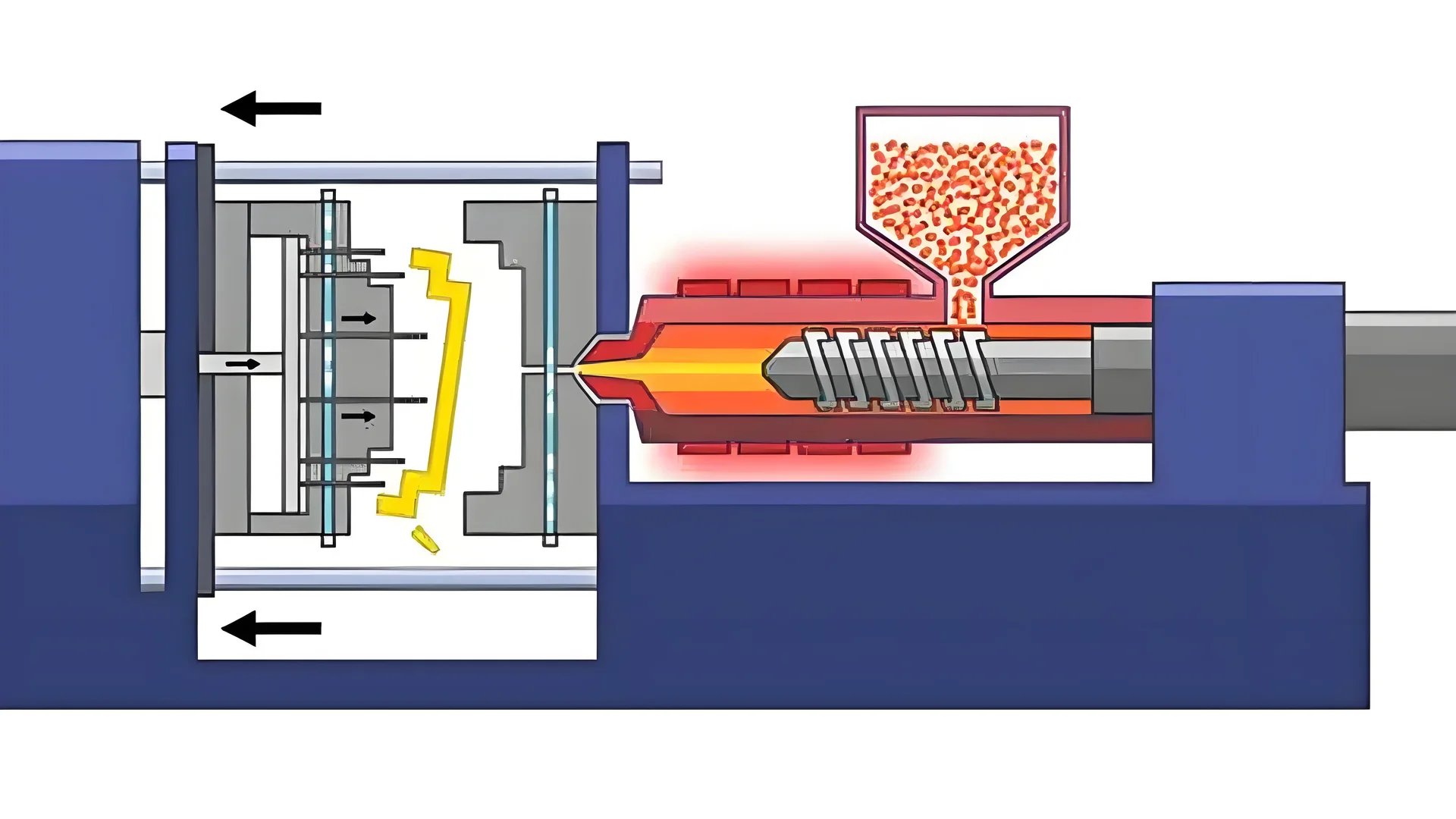
The Influence of Wall Thickness on Material Flow
I remember when I first entered the field of injection molding, wall thickness seemed unimportant. But as I learned more, I saw its huge impact on material flow. Uniform wall thickness acts like a well-coordinated performance, allowing material to flow smoothly and evenly in the mold. This balance reduces problems such as warping or incomplete fills. You really do not want these in your final product.
Importance of Uniform Wall Thickness
Designing gates in areas with uniform wall thickness truly changes everything. This smart placement helps the material flow evenly, cutting down on annoying weld lines. These lines can spoil both the look and strength of a product. Think of it this way: if you control the melt to meet in thin-wall spots first, success is more likely. It’s a good move.
Wall Thickness | Impact on Gate Position |
---|---|
Uniform | Consistent material flow, reduced weld lines |
Uneven | Variable cooling rates, potential defects |
Managing Multiple Gates in Complex Designs
Dealing with complex designs with multiple gates was once intimidating, but sequential gate settings work wonders. By adjusting spacing and angles to fit different wall thicknesses, material flow is handled well. It’s very much about controlling how the melt comes together, decreasing weld lines. Very effective.
Avoiding Sharp Turns in Melt Flow
Picture driving on a curvy road; sharp turns can really throw you off track. Melt flow in injection molding is similar. If gates are placed where sharp turns happen, flow can get disrupted. This raises the chance of weld lines. Instead, a smooth path lets the melt flow through these areas calmly without sudden changes in direction.
Understanding these details not only raises efficiency but also improves the quality of plastic products with fewer mistakes and better performance characteristics. Considering wall thickness and gate positioning together really optimizes manufacturing results.
For more insights on multi-gate designs and sequential gating strategies, see this resource on sequential gating5.
Symmetrical gate placement reduces weld lines.True
Placing gates on symmetry axes ensures even melt flow, reducing weld lines.
Gate spacing doesn't affect weld line formation.False
Improper gate spacing can cause overcooling or flow disorder, leading to weld lines.
How Can Adjusting Gate Angles Prevent Weld Lines?
Do you ever see a plastic piece and think it looks off? Those annoying weld lines are the reason.
Changing gate angles in injection molding probably lessens weld lines by directing how molten plastic moves. This allows the material to join more smoothly. The method not only strengthens the product but very often makes it look better.
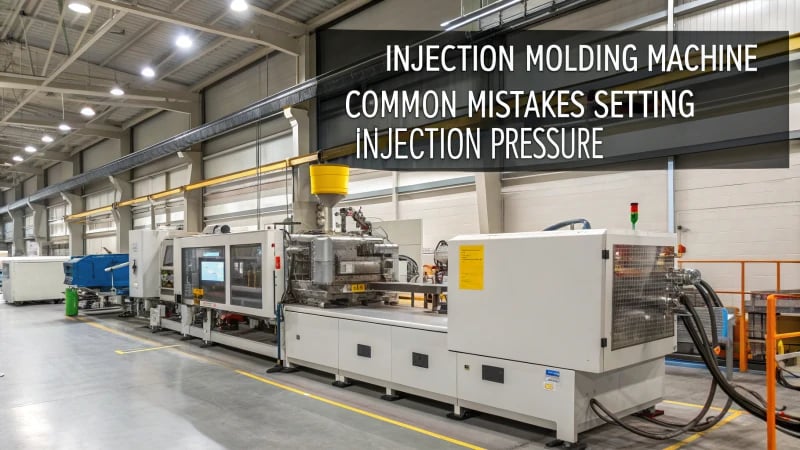
The Role of Gate Angles in Mold Design
I remember spotting weld lines on a project for the first time. It was a smooth, see-through piece for an expensive product and those lines were very noticeable. This experience taught me how important gate angles are for guiding molten plastic in injection molding. Adjusting these angles helps steer the material, reducing unpleasant intersections.
-
Symmetrical Layouts: Symmetrical products need gates on the symmetry line for even material spreading. This lessens weld line risks at meeting points. I worked on a round piece once where this tactic was crucial.
-
Avoiding Critical Areas: Products requiring visual appeal or strength need careful gate placement to hide weld lines. In car headlights, placing gates in unseen areas keeps them clear and strong.
Optimizing Multi-Point Gates
Handling multiple gates means sequencing and angling them correctly.
Consideration | Description |
---|---|
Sequential Gate Setting | Open gates in a designed order to control flow convergence. |
Gate Spacing & Angle | Adjust spacing and angles to ensure smooth melt merging. |
In one project, I learned that merging melts tangentially decreases weld lines6 a lot. Aligning gate angles7 with flow direction really improves quality.
Integrating Gate Position with Product Design
-
Uniform Wall Thickness: Guiding melts in uniform thickness areas allows even cooling and smoother merges. This greatly reduces weld lines.
-
Avoiding Sharp Turns: Prevent sharp melt flow turns by adjusting gate positions. A straight flow reduces weld line formation.
In complex designs with different wall thicknesses, directing melt into thinner sections first really helps. Matching melting rates across thicknesses allows neat merging and fewer defects.
Explore how adjusting gate angles8 can improve design by understanding their effect on melt movement and merging.
Symmetrical gate placement reduces weld lines.True
Placing gates symmetrically helps melt diffuse evenly, reducing weld line risk.
Uneven wall thickness increases weld line visibility.True
Different cooling rates in uneven walls make weld lines more noticeable.
Conclusion
Optimizing gate positions in injection molding minimizes weld lines, enhancing product quality. Techniques include symmetrical placements, sequential gating, and maintaining uniform wall thickness for efficient material flow.
-
Learn how sequential gate setting controls melt flow for complex products, enhancing product quality by reducing weld lines. ↩
-
Discover how utilizing the geometric center in gate placement improves melt distribution and reduces defects. ↩
-
Discover how sequential gating precisely controls melt flow to improve product quality by reducing weld lines. ↩
-
Learn how industries benefit from sequential gating by producing defect-free plastic components efficiently. ↩
-
Sequential gating helps manage material flow efficiently in complex designs, reducing defects. ↩
-
Understand how symmetrical gate layouts help prevent defects by ensuring even melt flow. ↩
-
Learn how adjusting gate angles impacts melt flow and minimizes weld lines. ↩
-
Discover how gate angle adjustments enhance product design by reducing defects. ↩