Undercuts in injection molding can feel like a designer’s worst nightmare. But don’t worry—there are practical strategies to conquer these challenges!
Addressing undercuts in injection molding involves strategic mold designs like slider and lifter mechanisms, as well as optimizing product designs by simplifying or decomposing complex features. These approaches ensure efficient production and high-quality outcomes.
While this gives you a quick overview, delving deeper into specific strategies will provide you with the insights necessary for optimizing your injection molding projects. Let’s explore each method in detail to understand their applications and benefits.
Slider mechanisms reduce mold release damage.True
Slider mechanisms move laterally, easing complex feature removal.
How Do Slider Mechanisms Aid in Undercut Management?
Slider mechanisms are pivotal in managing undercuts during injection molding, ensuring smooth product release and maintaining quality.
Slider mechanisms address undercuts by moving laterally during mold opening, allowing for the removal of complex features without damaging the product.
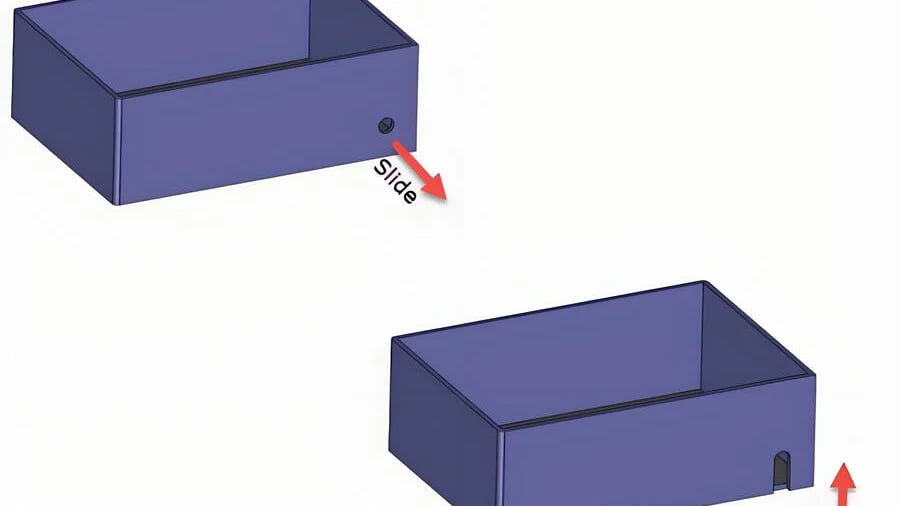
Understanding Slider Mechanisms in Injection Molding
Slider mechanisms play an integral role in the injection molding process, particularly when dealing with side inversions or undercuts. These are structural features that can prevent a mold from opening smoothly unless special measures are taken. Sliders are typically mounted on the moving part of the mold and are driven by slanting guide columns or hydraulic devices. This movement facilitates the retraction of the slider from the inverted side during mold opening, allowing for the smooth release of the molded part.
Application Scenario:
Sliders are particularly useful in scenarios involving side buckling, especially when the depth of the undercut is significant and the shape is regular. Common applications include products with side grooves or holes, such as electric appliance housings with button holes or automotive interior parts featuring side hanging structures.
The Working Principle of Slider Mechanisms
To delve deeper, let’s consider a plastic box injection mold with a side hole—an example of an inverted feature. During the mold opening, the slider is guided by an inclined column to move laterally. This lateral movement retracts the slider from the side hole, allowing the plastic box to be released from the mold seamlessly.
Example:
Product Type | Feature | Slider Application |
---|---|---|
Electric Appliance Housing | Side Button Holes | Smooth Mold Release |
Automotive Interior Parts | Side Hanging Structures | Efficient Ejection |
Advantages of Using Slider Mechanisms
- Complex Shape Management: Sliders allow for the molding of complex shapes with minimal risk of product damage.
- Enhanced Design Flexibility: Designers can create intricate designs that would otherwise be impossible with standard molds.
- Improved Production Efficiency: The use of sliders reduces cycle time and minimizes production downtime caused by stuck products.
By incorporating slider mechanisms into mold designs, manufacturers can effectively manage challenging undercut features, leading to high-quality, defect-free products. For further insights on optimizing these mechanisms, explore more about injection molding techniques1.
Slider mechanisms prevent product damage in undercut molds.True
Sliders allow lateral movement, avoiding damage during mold release.
Sliders are ineffective for managing complex shapes in molds.False
Sliders facilitate molding of complex shapes by retracting smoothly.
What Role Does Lifter Mechanism Play in Ejecting Molded Parts?
The lifter mechanism is a game-changer in injection molding, simplifying the ejection of complex parts with undercuts. Let’s uncover its pivotal role.
A lifter mechanism aids in ejecting molded parts with internal undercuts by moving diagonally during ejection, ensuring smooth release from the mold. It is particularly effective for products with shallow undercuts and small areas, optimizing the molding process.
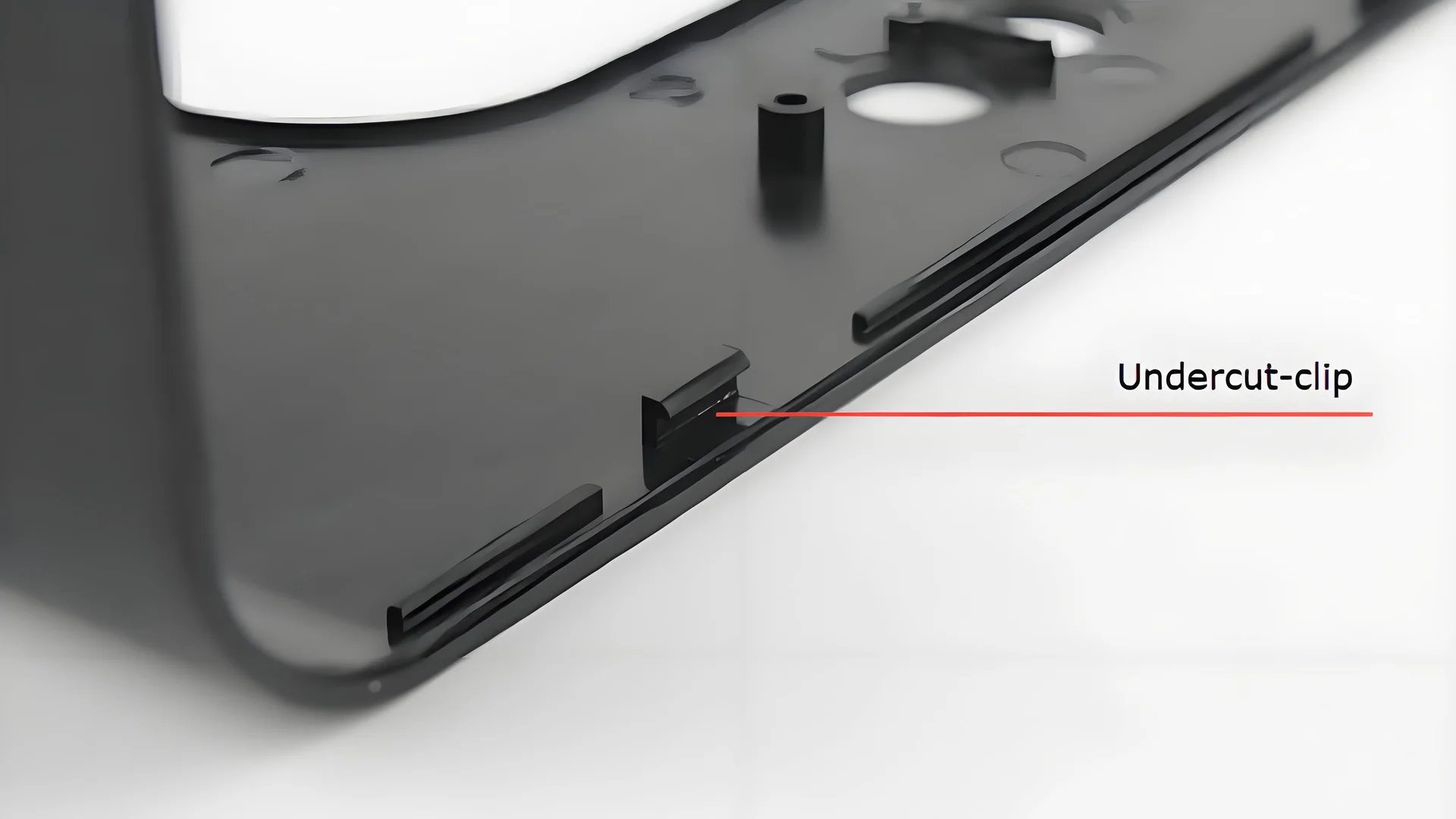
Understanding the Lifter Mechanism
In the realm of injection molding, the lifter mechanism emerges as a specialized tool for addressing internal undercuts2. Installed on the moving part of the mold, the lifter’s operation is both intricate and crucial. Unlike other mechanisms that may rely solely on vertical motion, the lifter moves diagonally, a feature that enables it to handle complex geometries and undercuts efficiently.
Principle of Operation
During the ejection phase, the lifter pushes against the inverted section of the molded part. The diagonal movement is key here: it not only aids in ejecting the part from the mold cavity but also in smoothly detaching any undercut without causing damage or distortion to the part.
Applications of Lifter Mechanisms
Lifter mechanisms are particularly useful when dealing with:
- Internal Inverted Buckles: When producing items like plastic containers with internal reinforcements or toy parts that incorporate small internal buckles.
- Shallow Undercuts: For parts where the undercut is not too deep and spans a small area, making lifters ideal for achieving precision.
For example, consider a plastic bottle cap that features an internal buckle. Here, a lifter mechanism can efficiently push out the cap without damaging its structural integrity, ensuring a perfect fit every time.
Designing with Lifters in Mind
Advantages
- Enhanced Mold Efficiency: By incorporating lifter mechanisms, manufacturers can enhance the efficiency of their molds, reducing cycle times and increasing throughput.
- Versatility: Lifters can be adapted for various products and designs, making them a versatile choice in many manufacturing scenarios.
Challenges and Considerations
While lifters are incredibly useful, they require careful design considerations. The angle of movement and the contact points must be precisely engineered to prevent any potential damage to the product during ejection.
In summary, understanding and implementing lifter mechanisms can significantly optimize the injection molding process, ensuring high-quality outcomes while managing complex product designs efficiently. As you explore more about mold design strategies, consider how integrating lifters can transform your production line’s capabilities. For more insights into addressing undercuts effectively, explore further details on slider mechanisms3 and other innovative solutions.
Lifter mechanisms move only vertically during ejection.False
Lifter mechanisms move diagonally, not just vertically, to handle undercuts.
Lifter mechanisms enhance mold efficiency by reducing cycle times.True
Incorporating lifters can reduce cycle times, boosting mold efficiency.
When Is Forced Demolding a Viable Solution for Undercuts?
Forced demolding in injection molding can be a game-changer when dealing with undercuts, especially for parts made from flexible materials.
Forced demolding is suitable when the undercut area has good elasticity, allowing the product to deform without damage during removal. This approach is ideal for small, flexible plastic parts with shallow undercuts, like soft hooks or rubber seals.
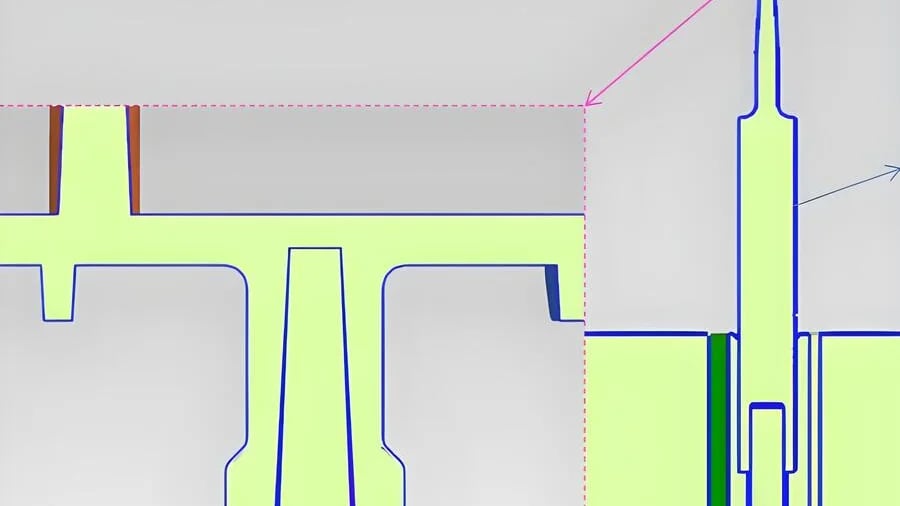
Understanding Forced Demolding
Forced demolding is a technique used in injection molding when the material properties of the molded part allow it to undergo elastic deformation without damage. This strategy leverages the elasticity of materials to manage undercuts effectively.
Material Considerations
Elasticity is Key: The primary criterion for using forced demolding is the elasticity of the material. Materials such as thermoplastic elastomers (TPE) or soft plastics can handle the strain during the demolding process. The material should have a high modulus of elasticity and elongation at break, ensuring it can stretch and return to its original shape without permanent deformation.
Application Scenarios
Small Parts with Elasticity
For products like soft rubber seals or small plastic hooks, forced demolding is advantageous. The elasticity allows these items to pass over mold features that would typically require more complex mold designs.
- Example: A small soft plastic hook designed for lightweight applications can benefit from forced demolding due to its ability to flex during ejection.
Shallow Undercuts
Forced demolding works well with shallow undercuts where the depth does not necessitate intricate mold adjustments.
- Example: In soft rubber seals with minimal buckling, the natural elasticity aids in smooth removal.
Evaluating Suitability for Forced Demolding
Before opting for forced demolding, it’s crucial to assess whether this method will suit your specific product needs. Here’s a simple assessment checklist:
Criteria | Description |
---|---|
Material Elasticity | Does the material exhibit sufficient elasticity? |
Undercut Depth | Are the undercuts shallow enough to avoid damage during demolding? |
Production Volume | Is this method economically viable for your production scale? |
Conclusion and Next Steps
While forced demolding can simplify mold designs and reduce costs, it’s vital to weigh the material properties and application requirements carefully. In scenarios where elasticity aligns with design needs, this approach not only ensures efficiency but also maintains product integrity.
For further insights on how forced demolding can be implemented in various injection molding processes4, explore detailed case studies and expert recommendations.
Forced demolding is ideal for shallow undercuts in soft plastics.True
Shallow undercuts allow for deformation without damage, ideal for forced demolding.
Forced demolding is unsuitable for parts with high rigidity.True
High rigidity prevents elastic deformation needed for safe forced demolding.
How Can Product Design Optimization Simplify Injection Molding?
Unlocking efficiencies in injection molding begins with astute product design, minimizing complexities from the start.
Simplifying injection molding through product design involves reducing complex undercut features, optimizing buckle structures, and decomposing components. By addressing these elements early in the design phase, manufacturers can achieve smoother production processes, reduced costs, and improved product quality.
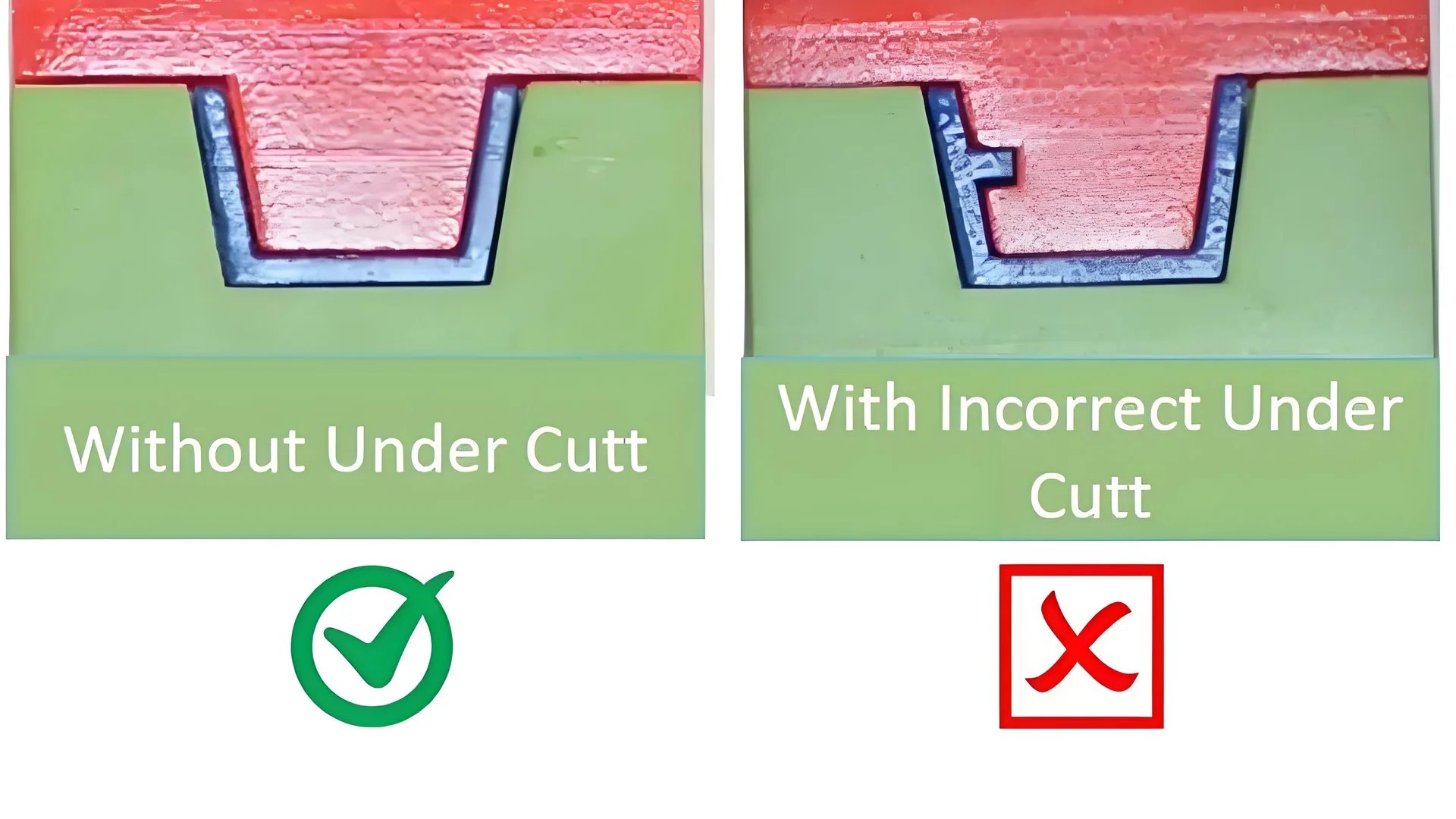
Streamlining Designs to Simplify Mold Production
One of the fundamental ways to simplify injection molding is by optimizing product design at the outset. By minimizing unnecessary complexity in features like undercuts and buckles, manufacturers can facilitate easier mold construction and more efficient production cycles. For instance, redesigning intricate buckle structures5 into simpler forms can significantly reduce molding challenges.
Designers can employ computer-aided design (CAD) software to visualize potential issues and optimize designs. Early simulations help in identifying problem areas, allowing designers to make informed adjustments before the physical mold creation begins.
Decomposition of Complex Features
Another effective strategy involves decomposing complex product components into simpler, manageable sections. By doing so, each part can be individually molded and later assembled, thus bypassing the need for intricate mold mechanisms that handle complex undercuts.
Feature | Traditional Approach | Optimized Approach |
---|---|---|
Complex Buckle | Integral Design | Decomposed Sections |
Large Undercut | Single Part Mold | Modular Assembly |
This approach is particularly beneficial for large products where undercuts present significant challenges. For example, a large plastic housing with multiple internal undercuts can be broken into smaller parts that are easier to mold and then assembled using snaps or adhesive methods.
Material Selection and Structural Considerations
Choosing the right materials is crucial for optimizing product designs for injection molding. The elasticity and flexibility of materials can influence design decisions. For instance, selecting materials with higher elasticity can permit designs with minimal undercuts that rely on the material’s flexibility for release during demolding.
Additionally, incorporating structural considerations6 such as uniform wall thicknesses and reducing sharp transitions can prevent defects like warping and ensure a more consistent product output. Ensuring that every part of the product meets structural requirements also aids in maintaining product integrity post-molding.
By integrating these strategies during the design phase, manufacturers not only streamline production but also improve the overall quality and reliability of their products.
Reducing undercuts simplifies injection molding processes.True
Minimizing undercuts reduces mold complexity, easing production.
Complex buckles increase efficiency in mold production.False
Complex buckles complicate molds, hindering efficient production.
Conclusion
Embracing effective undercut strategies not only enhances moldability but also elevates product functionality. Implement these insights to streamline your injection molding projects.
-
Discover techniques to enhance mold efficiency and product quality.: Optimizing injection molding design with injection molding side action requires adequate understanding of the process. ↩
-
Learn how lifters simplify complex mold designs.: The lifter is mainly used to form the internal undercuts of an injection molded plastic part, and at the same time it also offers ejection function. ↩
-
Discover complementary methods to handle undercuts efficiently.: At its most basic level, the slider is used to turn the vertical movement of the mold opening or closing into horizontal motion. Slide … ↩
-
Explore expert insights and case studies on forced demolding techniques.: Explore effective demolding techniques in injection molding to enhance product quality, reduce cycle time, and minimize defects in the finished products. ↩
-
Discover methods to reduce complexity in buckle designs.: #1 Use the “shell & infill” method as the benchmark · #2 Vary the thickness of a shell using simulation data · #3 Create a graded lattice driven … ↩
-
Learn about key structural factors for molding success.: Wall thickness depends on the material · Adding draft makes the part easier to remove · Radii improve material flow · Coring out saves money · Undercuts or no … ↩