Choosing the right injection molding machine is like finding the perfect partner in manufacturing. It saves time. It saves money. It avoids problems.
I focus on the projected area to find the right injection molding machine. The mold size must match for compatibility. Product weight helps decide the needed injection volume. These things need to fit with clamping force and template size. Injection pressure also matters. They are really important for successful production.
When I began learning about injection molding, there were so many details to consider. It felt very overwhelming. Understanding how my product’s needs – such as size and weight – matched the machine’s capabilities helped me a lot. It is like fitting pieces into a puzzle. Each factor, like clamping force and injection volume, matters greatly.
For example, the projected area showed me the needed clamping force. A simple formula helped꞉ multiply the injection pressure by the projected area and a safety factor. Imagine a product with a 10,000 mm² area. You would need about 65 tons of clamping force if the injection pressure is 50 MPa. These numbers gave me confidence. It was really reassuring.
Mold size is also important. Your mold must fit well within the machine’s template size and tie rod spacing. This became very clear during a big project like a car bumper. I saw how important perfect alignment was to avoid expensive errors. Everything needed to match perfectly.
Product weight plays a major part too. I learned to find the product’s volume using its weight and material density. The machine’s injection volume must handle this. Imagine needing more than 83.3 cm³ for a 100g product. Details like these are critical. They truly decide the success of a project.
Injection pressure and product weight are linked. Heavier items probably need higher pressures to fill the mold correctly. This helped me avoid issues like short shots or uneven spreads.
The main lesson? Really understand your product’s details and how they fit with the machine’s abilities. With this method, manufacturing improves a lot. It leads to better efficiency and quality in production.
Clamping force depends on product's projected area.True
The clamping force is calculated using the product's projected area on the mold.
Heavier products require lower injection pressure.False
Heavier products often need higher injection pressure for complete mold filling.
Why is Tonnage Crucial in Injection Molding?
Have you ever been confused about how tonnage works in injection molding? Tonnage is really important. It changes everything in producing good products. It also improves efficiency.
Tonnage, also known as clamping force, plays a key role in injection molding. This force keeps the mold halves tightly closed when injecting materials. It stops defects. Closing the mold properly allows for full filling and keeps the product strong. Key factors like projected area and injection pressure help decide the right tonnage.
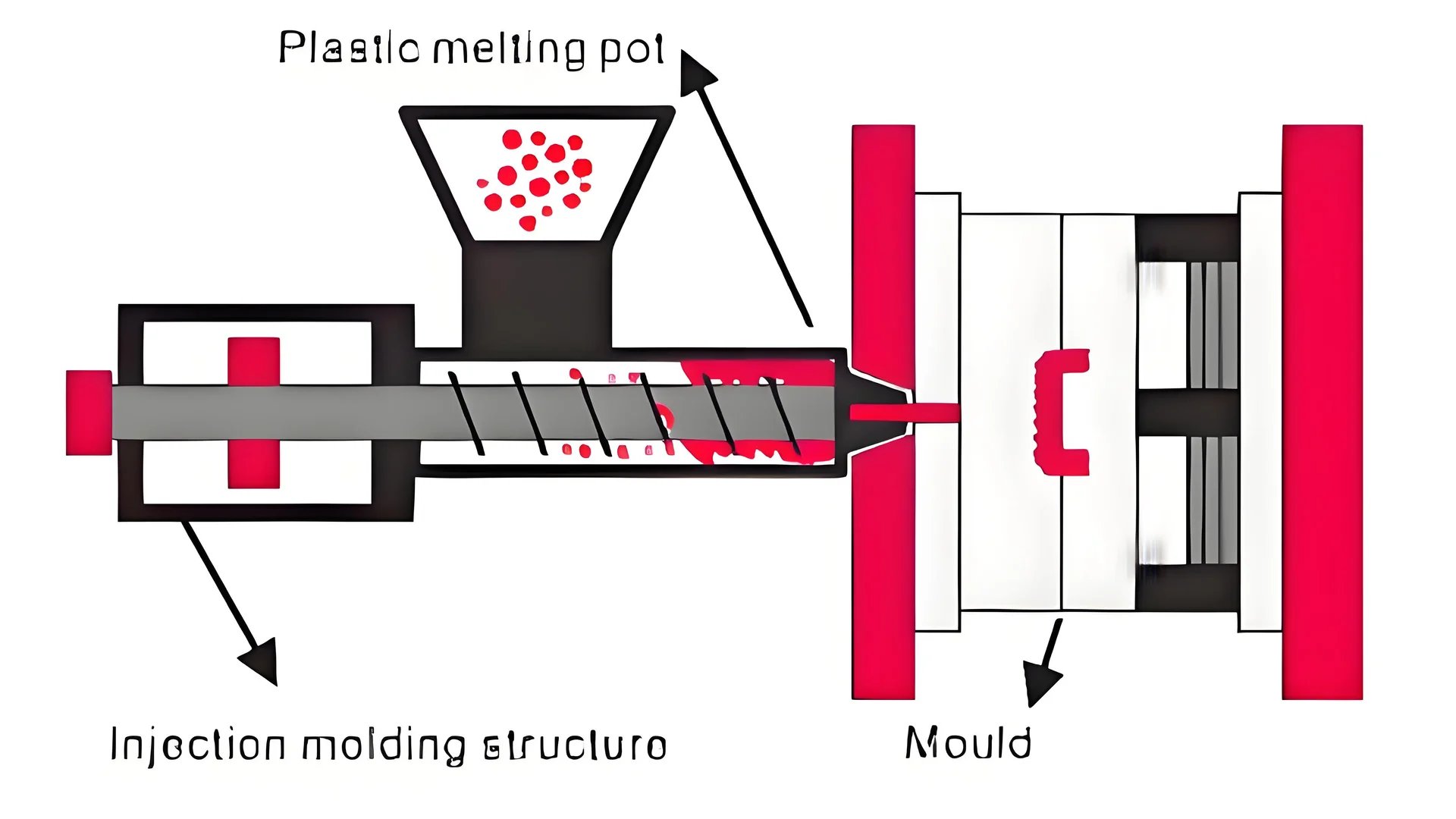
Understanding Tonnage in Injection Molding
Think of struggling to open a stubborn jar. Tonnage in injection molding works similarly. It uses strong force to keep the mold halves tightly together. Molten plastic fills the mold, and if the force is too low, problems arise. You might end up with defects like flash or incomplete parts.
Calculating Tonnage Requirements
At first, calculating the right tonnage seemed like a secret code to me. But soon, it became easy. Product size is very important. Imagine planning a new room; here, calculate the projected area where the mold parts meet. For example, if your product’s area is (10000mm^{2}) and needs (50MPa) injection pressure, about 65 tons of clamping force is necessary. Precision prevents mistakes—always double-check.
Matching Machine and Mold Sizes
Have you ever tried moving a large sofa through a small door? Matching the machine and mold size is just like that. Bigger products require bigger molds. The machine must have enough space for templates and rods. I faced this when handling a car bumper mold; it felt like solving a massive 3D puzzle. Explore more about mold sizing1.
Product Weight and Injection Volume
Product weight determines how much material to inject—it’s like cooking a big meal; use just the right amount. Determine the weight, use material density, and check the machine’s injection volume to avoid problems like under-filling or machine overloading.
Injection Pressure Considerations
Bulky items need higher injection pressure, similar to using extra force for kneading dough. Some items require machines that handle more pressure to prevent short shots or voids. When I worked on a thick piece, tweaking pressure settings changed everything.
Understanding these factors helps pick the right injection molding machine2. It smooths production and reduces defects—everything should work in harmony to find that perfect balance.
Clamping force depends on injection pressure.True
Clamping force is calculated using injection pressure, projected area, and safety coefficient.
Injection volume is always equal to theoretical volume.False
Actual injection volume is typically 80% - 90% of the theoretical volume.
How does mold size influence machine selection?
Have you ever tried fitting a big puzzle piece into a small space? That is similar to picking the right injection molding machine depending on the mold size.
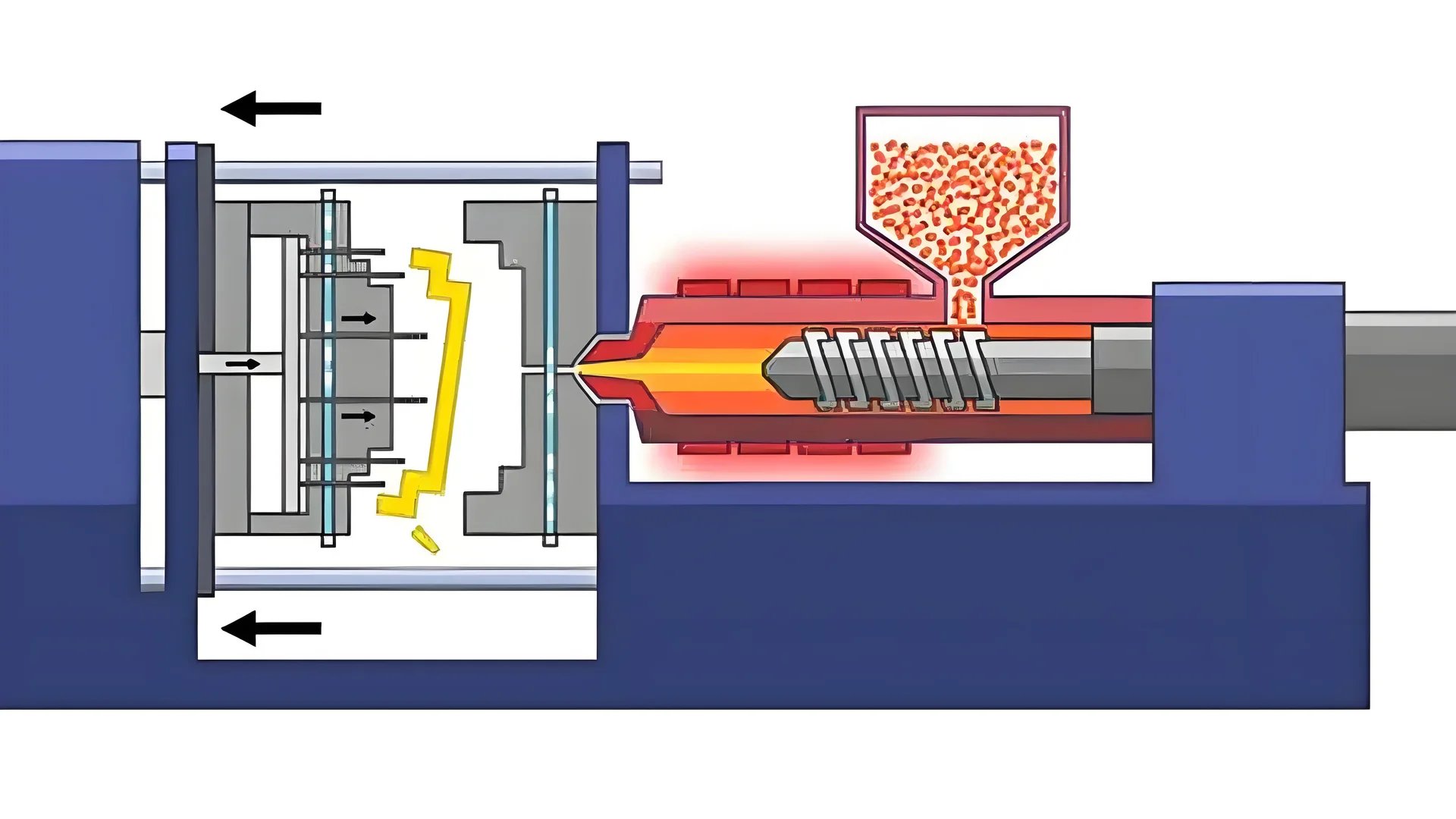
Mold size is key when picking an injection molding machine. It influences the clamping force, template size and tie rod spacing. Big molds require machines with more clamping power. Machines must have suitable dimensions. This is important for smooth production. Quality must be maintained.
Understanding Clamping Force Requirements
Picture trying to close a door against a strong wind. Clamping force in injection molding works similarly; it holds the mold together tightly. Finding the right clamping force once felt like solving a big math puzzle. To calculate this, consider the projected area of the product on the mold’s parting surface. For instance, a 10,000 mm² product area at an injection pressure of 50 MPa requires about 65 tons of clamping force, with a safety factor included. Imagine an elephant sitting on the mold to ensure that it can handle the process without defects like flash.
Importance of Template Size and Tie Rod Spacing
It’s more than just clamping; the mold should fit snugly in the machine. This involves considering template size and tie rod spacing3. I learned this with a giant car bumper mold that needed a machine with big template sizes and wide tie rod spacing. Big molds resemble large vehicles; they require more room. Additionally, these machines must support sufficient open stroke and mold thickness for easy product removal.
Balancing Product Weight and Injection Volume
Product weight is like balancing scales when choosing a machine. Consider converting weight into volume using material density to meet injection volume requirements4. It felt like changing ounces to grams in cooking. A 100g product with a density of 1.2g/cm³ results in approximately 83.3cm³, necessitating a machine capable of injecting over this volume.
Injection Pressure Considerations
Think of thick products as dough needing thorough kneading; higher pressure helps spread material evenly, avoiding air pockets or defects like short shots or voids. Different machines offer diverse pressures, so understanding this aspect is crucial for selecting machines that can handle such requirements effectively.
By evaluating these factors, manufacturers can choose machines that align perfectly with their production needs, optimizing both efficiency and product quality.
Projected area determines clamping force needed.True
The clamping force is calculated using the projected area of the product.
Heavier products need lower injection pressure.False
Heavier products often require higher injection pressure for proper molding.
Why is Injection Volume Crucial for Product Weight?
Have you ever thought about how tiny details change everything in manufacturing? Discover the world of injection volume. This plays a crucial role in creating products with precision and perfection.
Injection volume is vital for product weight. It decides how much material goes into the mold. This affects the weight of the finished product. To figure out injection volume, consider product size, density and machine capacity. Controlling volume precisely leads to stable product weight. Consistent weight is important. It keeps quality steady and meets standards.
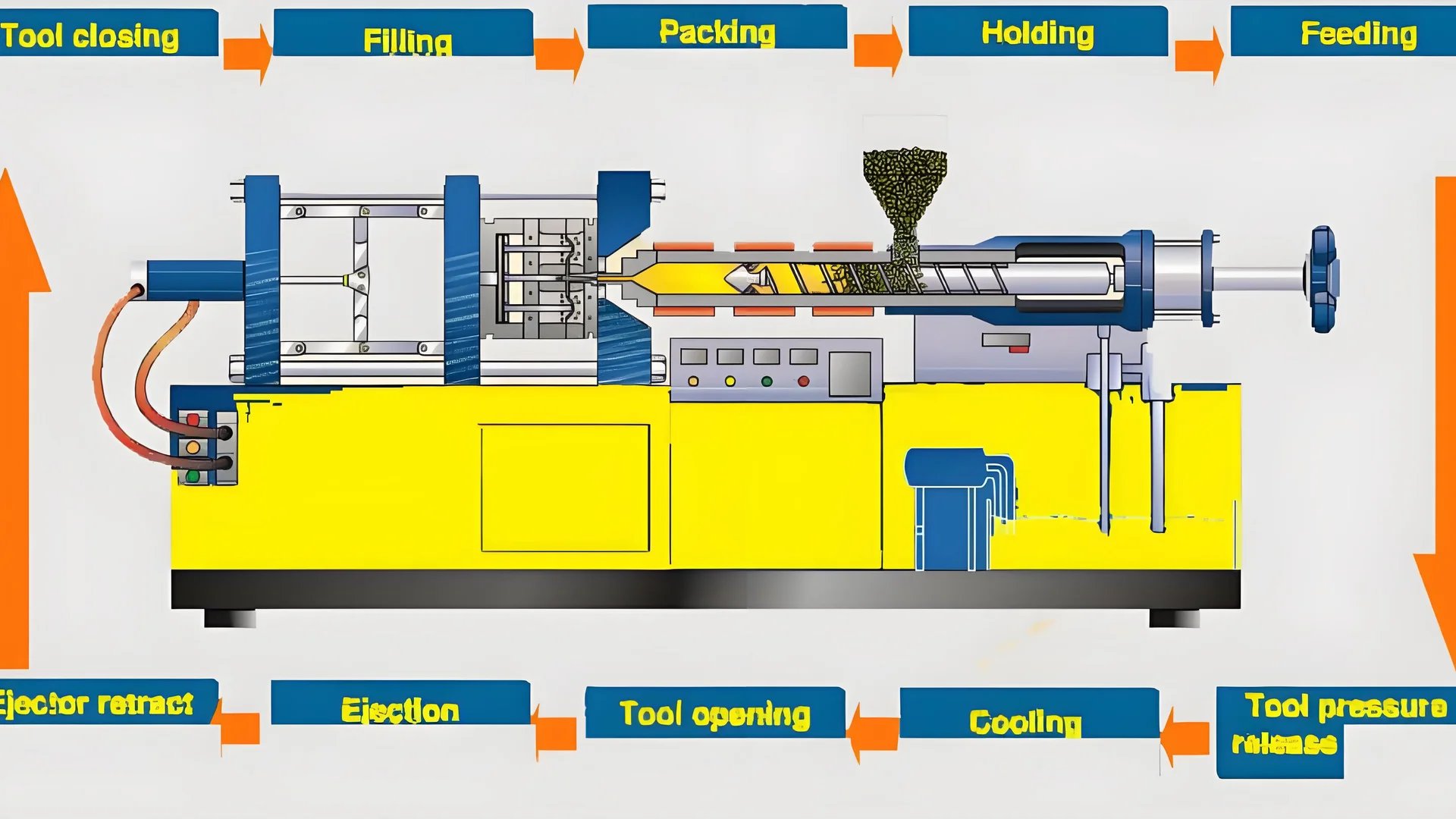
Determining Injection Volume
I remember when I first stood before a huge injection molding machine. I felt amazed and a bit overwhelmed. It was like meeting a mechanical giant that could turn plastic pellets into something extraordinary. Understanding how injection volume5 affects the product’s final weight is very important in this process.
The injection volume sets the exact amount of molten material injected into the mold, which in turn determines the size and weight of the final product. It’s like filling a cup with the right amount of water. Too little leaves you with an incomplete product; too much causes overflow and waste. Calculating the projected area on the mold’s surface helps find the clamping force needed in a machine. This calculation often uses formulas like (F = p \times A \times S), where (p) is injection pressure, (A) is the projected area, and (S) is a safety coefficient to help achieve the perfect balance.
Role of Material Density
I was sipping coffee one afternoon, pondering these details. I realized how much injection molding resembles baking. Flour must be measured precisely so a cake rises perfectly. Similarly, material density must be considered for the ideal product weight6. A 100g product with 1.2g/cm³ density needs about 83.3cm³ volume. Manufacturers choose a machine that handles a bit more volume for consistency because consistency is key.
Injection Pressure Considerations
Injection pressure reminds me of fixing a leaky hose with my dad—too much pressure sends water spraying everywhere! Similarly, too little pressure in molding leads to incomplete products. Heavier products might require higher injection pressures to ensure that every corner of the mold cavity is filled completely, avoiding defects such as short shots.
Matching Mold and Machine
Choosing the right machine is like picking shoes—the perfect fit is everything! For bigger products, this means matching the mold size7 with the machine, just like Cinderella’s slipper fits her foot perfectly. Larger products necessitate bigger molds, impacting template size and tie rod spacing.
By exploring projected area calculations, material density considerations, injection pressure requirements, and mold-machine compatibility, manufacturers control product weight through precise injection volume management efficiently turning raw materials into quality products with each shot.
Injection volume affects product weight accuracy.True
The injection volume must match the product weight to ensure accuracy.
All products require the same injection pressure.False
Different products require varying injection pressures based on weight.
How Does Injection Pressure Affect Product Quality?
Do you ever think about why your products are perfect at times but other times they are a total mess?
Injection pressure is very important for product quality in molding. It affects how accurate the size is, the finish of the surface and how the material spreads. Higher pressure fills the cavity completely. This reduces mistakes like short shots. However, too much pressure may lead to flash and reduce material quality. It is crucial to find the right balance. Balance is key for great results.
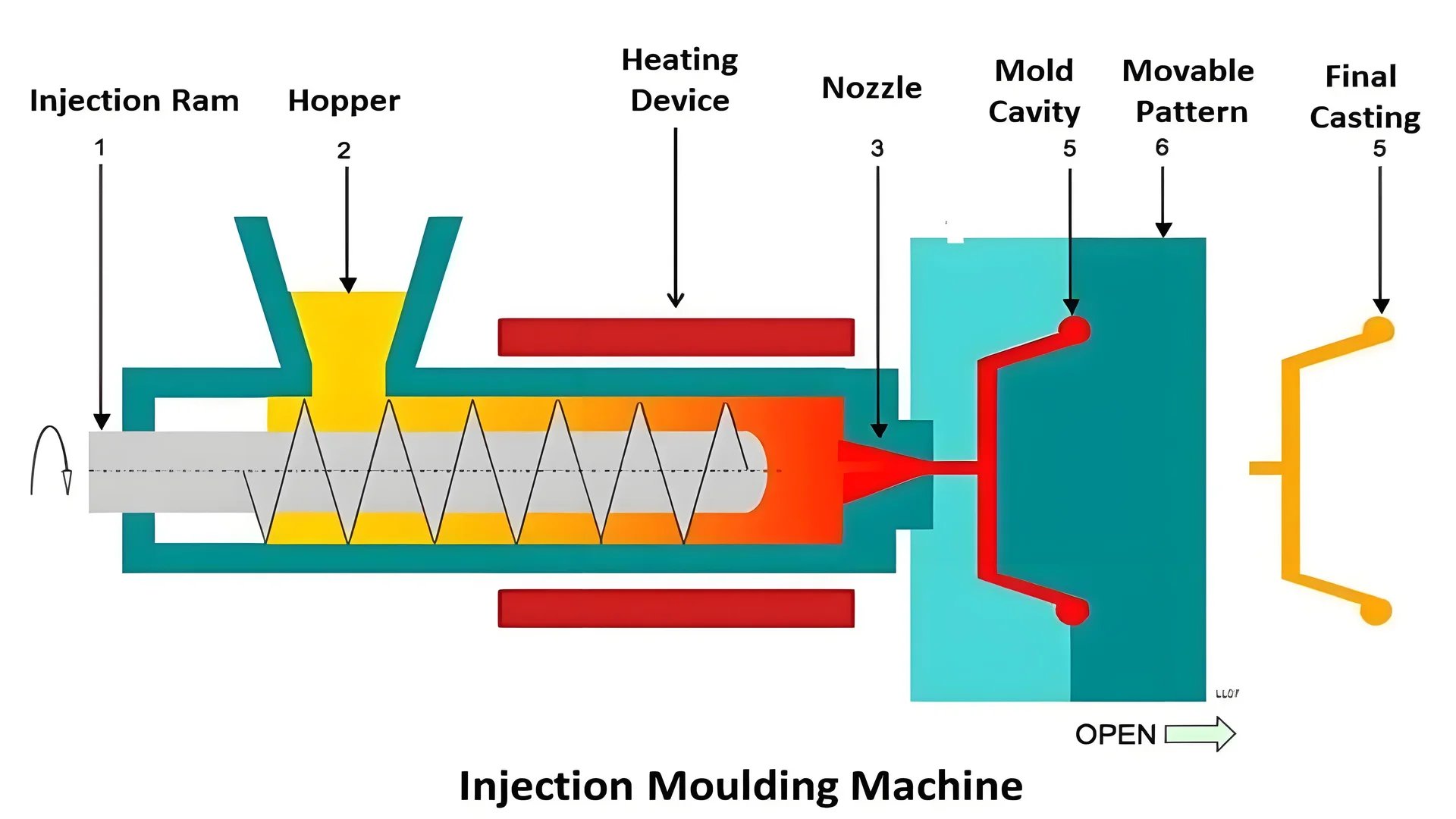
Influence on Dimensional Accuracy
Injection pressure was crucial in my early days in manufacturing. We had a project with products that had unwanted flashes along the edges. It was annoying! A seasoned expert told me that too much pressure caused this issue, as the material was squeezing out of the mold. Controlling pressure helps maintain precise dimensions and does more than avoid short shots or incomplete items.
The product’s size often affects the needed pressure. For instance, selecting the tonnage of the injection molding machine depends on the product’s area. The formula (F = p\times A\times S) calculates the clamping force needed based on injection pressure and other factors8. This calculation helps keep quality high.
Effect on Surface Finish
The surface finish is important; it’s like a bow on a gift. Even small imperfections were not okay in one project I worked on. We needed the right injection pressure to avoid flow lines or streaks. Too much pressure caused sink marks or warping, making balancing pressure really tricky.
Picking the correct mold size and matching it with the injection machine was key. Larger products required a machine with enough space for both the mold and rods for optimal results9.
Relationship with Material Properties
Weight is another important factor. Heavy products need more pressure to fill the mold, which I learned during a project with thick-walled items where uniform density was essential. The melt had to spread evenly without gaps.
Understanding this was eye-opening. Calculating volume using weight and material density helped select a suitable machine to meet specific needs10. This step let us adjust settings for better material spread, reducing defects and always improving product quality.
Higher injection pressure improves product surface quality.True
Increased pressure ensures complete mold filling, enhancing surface finish.
Larger molds require smaller injection machines.False
Larger molds need machines with sufficient template size and tie rod spacing.
Conclusion
Choosing the right injection molding machine involves matching product size, weight, and required clamping force to ensure efficient production and high-quality results.
-
Learn how mold sizing affects machine compatibility and production efficiency. ↩
-
Discover key factors for selecting an efficient injection molding machine. ↩
-
Discover suitable dimensions for accommodating larger molds. ↩
-
Understand how to match machine capacity with product volume. ↩
-
Explore how size influences machine selection and material usage. ↩
-
Gain a comprehensive understanding of this essential manufacturing technique. ↩
-
Explore how size influences machine selection and material usage. ↩
-
Learn about calculations ensuring machine capability for optimal product quality. ↩
-
Discover how proper matching improves molding efficiency and product quality. ↩
-
Find methods to determine suitable machine capacity for effective molding. ↩