Injection molding technology is racing ahead, revolutionizing industries with its game-changing advances. Are you caught up on these latest innovations?
Cutting-edge injection molding trends include automation, sustainability, and novel materials, enhancing manufacturing efficiency, reducing environmental impact, and opening new design possibilities globally.
When I first started in mold design, the pace of innovation seemed daunting. But over time, I realized that understanding these trends isn’t just about keeping up; it’s about unlocking potential. By exploring how automation can streamline production or how new materials can inspire novel designs, I’ve seen firsthand how staying informed can provide a significant edge. Let’s delve deeper into these trends and see how they can transform our design processes and drive business success.
Automation is the most significant trend in injection molding.True
Automation enhances efficiency and precision, reducing costs and errors.
Sustainability practices in injection molding increase waste production.False
Sustainability practices aim to reduce waste and environmental impact.
- 1. How Is Automation Revolutionizing Injection Molding?
- 2. How Does Sustainability Transform Modern Injection Molding?
- 3. What New Materials Are Emerging in Injection Molding?
- 4. How Are Smart Technologies Enhancing Molding Processes?
- 5. How Are Emerging Trends Shaping Design and Production?
- 6. Where Is the Future of Injection Molding Heading?
- 7. Conclusion
How Is Automation Revolutionizing Injection Molding?
When I first stepped into the world of injection molding, automation felt like science fiction. Now, it’s the heartbeat of innovation, shaping how we design and produce. From tireless robots to smart sensors, these technologies are reshaping everything.
Automation in injection molding uses robotics and sensors to boost precision, efficiency, and quality control, reducing human error and production time, ultimately leading to cost savings and a transformed manufacturing process.
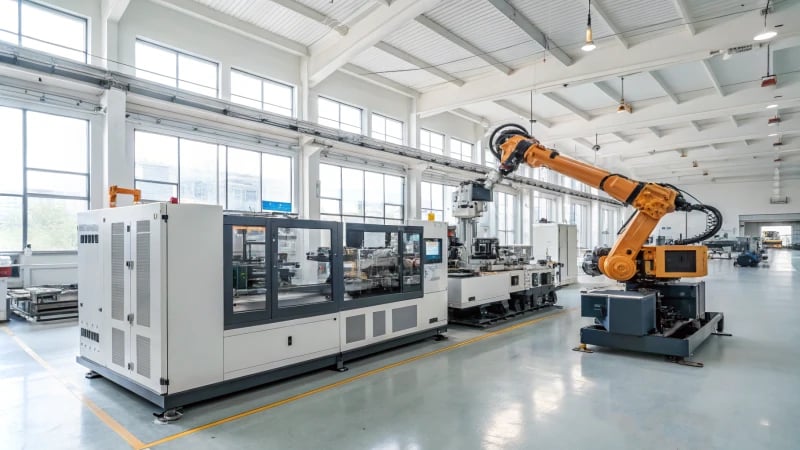
The Role of Robotics in Injection Molding
I remember the first time I saw a robot in action on the factory floor. It was mesmerizing to watch it swiftly move between tasks, seamlessly picking parts from the mold with a precision that seemed almost human. Robotics has become integral to modern injection molding processes, performing tasks such as part removal, assembly, and packaging. These robots enhance efficiency1 by operating continuously without the need for breaks or lunch hours, ensuring consistent cycle times and slashing labor costs.
Take articulated robots, for instance. They can reach deep into molds to extract parts quickly and accurately, reducing the risk of damaging delicate components. And then there are collaborative robots, or cobots, which are designed to work side-by-side with human operators. By taking over repetitive tasks, these cobots free us up to focus on more complex and creative activities.
Sensor Integration for Enhanced Precision
Sensors are like the unsung heroes of injection molding. They quietly monitor parameters like temperature, pressure, and material flow in real-time, ensuring everything runs smoothly. Imagine cooking without a timer or thermometer; sensors are just as crucial in maintaining precision here. This real-time data helps adjust process parameters dynamically, improving product consistency and reducing waste.
Thanks to advanced sensor systems, manufacturers can now detect defects early in the production process. This means fewer costly errors and a smoother path to meeting strict industry standards. It’s like having a quality control2 team working 24/7 without ever needing a break.
Advanced Process Automation Systems
One of the most exciting parts of automation is seeing how software platforms integrate seamlessly with existing machinery to optimize operations. These systems manage scheduling, monitor equipment health, and predict maintenance needs using AI algorithms.
Picture this: analyzing historical data to optimize mold design and production strategies. These systems don’t just work in isolation—they integrate with CAD tools, allowing designers3 like Jacky to simulate production scenarios before actual implementation. This ensures fewer surprises and more efficient production runs.
Benefits of Automation | Description |
---|---|
Increased Efficiency | Robots work 24/7 without breaks. |
Improved Precision | Sensors adjust processes in real-time. |
Cost Reduction | Lower labor costs and waste minimization. |
Enhanced Quality | Real-time monitoring ensures defect-free products. |
The Future of Automation in Injection Molding
Looking ahead, I’m thrilled about the possibilities as technology continues to evolve. Imagine factories where advanced AI capabilities handle most processes, leaving us humans to focus on strategic oversight rather than manual operations.
Exploring these trends can help manufacturers4 stay competitive and adaptable in a rapidly changing industry landscape. It’s an exciting time to be involved in this field as we stand on the brink of even more profound changes.
Robots in injection molding reduce labor costs.True
Robots operate continuously without fatigue, minimizing the need for human labor.
Sensors in injection molding cannot adjust processes in real-time.False
Sensors monitor parameters and adjust processes dynamically to maintain precision.
How Does Sustainability Transform Modern Injection Molding?
The journey towards sustainable injection molding is not just about materials; it’s about reimagining how we create the future, balancing innovation with environmental responsibility. Join me as I dive into the world of eco-friendly molding and discover its transformative impact.
Sustainability in injection molding involves using eco-friendly materials, reducing waste, and optimizing energy use to enhance environmental efficiency in manufacturing, paving the way for a greener future.

Embracing Eco-Friendly Materials
Imagine this: the same old packaging, but now it’s made from biodegradable polymers5. As someone who’s spent countless hours pondering product designs, the shift towards using recycled and biodegradable materials in injection molding feels like a personal victory. Not only do these materials lessen our dependency on non-renewable resources, but they also help reduce landfill waste—a win-win for both designers and the environment. This change is especially significant in industries like packaging, where every little bit counts towards minimizing environmental impact.
Minimizing Waste
Every designer knows the frustration of dealing with excess material. It’s like watching your efforts and resources go to waste—literally. But modern injection molding is changing that narrative. By optimizing mold designs and refining production processes, we’re able to significantly cut down on waste. Techniques such as closed-loop recycling systems6 mean that scrap materials aren’t just discarded; they’re reused, giving them a second life in new products.
Waste Reduction Strategies | Description |
---|---|
Design Optimization | Creating molds with minimal excess material |
Process Efficiency | Streamlining production to reduce scrap |
Material Recycling | Reusing waste material in new products |
Energy Efficiency
Energy consumption is another major concern I’ve grappled with in my career. The hum of machinery often comes with the nagging thought of energy bills and environmental costs. But with innovations like electric injection molding machines7, those concerns are starting to fade. These machines promise lower energy consumption, reduced noise levels, and enhanced precision and control—making them a dream for anyone committed to sustainable manufacturing.
- Benefits of Electric Machines:
- Lower energy consumption
- Reduced noise levels
- Enhanced precision and control
Sustainable Design Practices
I’ve always believed that good design starts from the ground up. Sustainable design practices involve looking at the entire product lifecycle—from the materials we choose to how we dispose of them responsibly. Concepts like Design for Environment (DfE)8 guide us in crafting products that are not just functional but also easier to recycle or dispose of responsibly.
Innovations in Sustainable Molding
There’s an exciting wave of innovations transforming our industry. From plant-based polymers to advanced recycling technologies, these developments are paving the way for a more sustainable future. They align perfectly with global environmental goals and promise to further integrate sustainability into injection molding practices9.
- Emerging Trends:
- Bio-based materials
- Smart recycling technologies
- Lifecycle analysis tools
As I continue my journey in product and mold design, these sustainable practices remind me that innovation isn’t just about the latest tech or sleekest design—it’s about building a better world for future generations.
Biodegradable polymers are used in packaging industries.True
Biodegradable polymers are popular in packaging due to environmental concerns.
Electric machines increase energy consumption in molding.False
Electric machines reduce energy consumption, not increase it, in molding.
What New Materials Are Emerging in Injection Molding?
Have you ever wondered what materials are shaking up the injection molding world? Let me take you on a journey through some of the latest innovations.
Emerging injection molding materials like bio-based polymers, reinforced composites, and high-performance thermoplastics boost sustainability, strength, and thermal resistance, revolutionizing the industry.
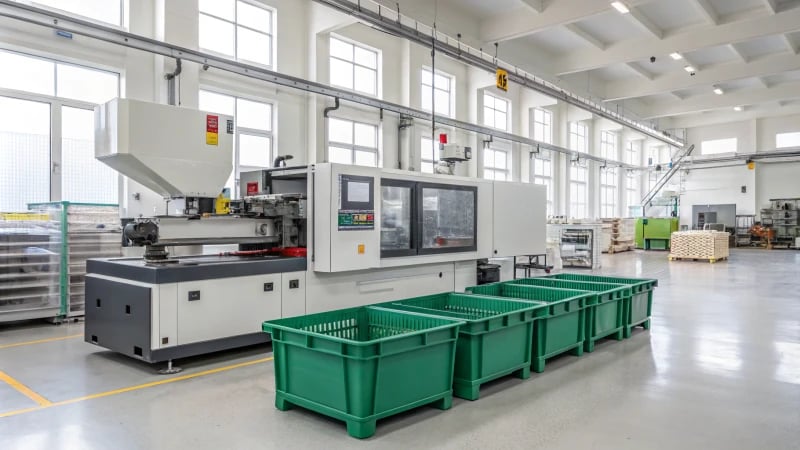
Bio-based Polymers: A Sustainable Shift
I remember when I first stumbled upon bio-based polymers at a trade show. The idea of using materials made from corn starch and cellulose was fascinating, especially knowing they are biodegradable and less dependent on fossil fuels. These polymers are not just a trend; they’re a sustainable10 alternative that makes me feel hopeful about reducing our environmental footprint.
Reinforced Composites: Strength Meets Versatility
Reinforced composites remind me of a project I once tackled where weight and strength11 were non-negotiable. By combining polymers with glass or carbon fibers, these composites provide the ideal balance—lightweight yet robust. They’re perfect for applications like automotive parts or aerospace components where every ounce counts.
High-Performance Thermoplastics: Pushing Boundaries
High-performance thermoplastics such as PEEK and PPS are like the superheroes of the material world. Their ability to withstand extreme temperatures and harsh environments makes them indispensable for industrial applications12 requiring utmost reliability and durability. I find them particularly exciting because they expand what’s possible in engineering and design.
Material | Key Benefits |
---|---|
Bio-based Polymers | Eco-friendly, biodegradable |
Reinforced Composites | Enhanced strength, lightweight |
High-Performance | Thermal resistance, durability |
Innovations Driving Material Development
The push for innovation in injection molding materials reminds me of the constant quest for better solutions in our field. It’s driven by the need for cost-efficiency, performance optimization, and meeting regulatory demands. As we all strive to meet stricter environmental standards and consumer expectations, these new materials don’t just improve product quality—they’re also paving the way for more sustainable manufacturing practices. It’s an exciting time to be part of this evolving industry.
Bio-based polymers reduce reliance on fossil fuels.True
Bio-based polymers are derived from renewable resources, decreasing fossil fuel dependence.
Reinforced composites are unsuitable for aerospace use.False
Reinforced composites are ideal for aerospace due to their strength and light weight.
How Are Smart Technologies Enhancing Molding Processes?
Imagine if your molding processes could think for themselves, adapting and optimizing without constant oversight. Welcome to the world of smart technologies revolutionizing manufacturing.
Smart technologies, including IoT, AI, and automation, enhance molding processes by improving precision, reducing waste, and optimizing production efficiency through real-time monitoring and adaptive process control.
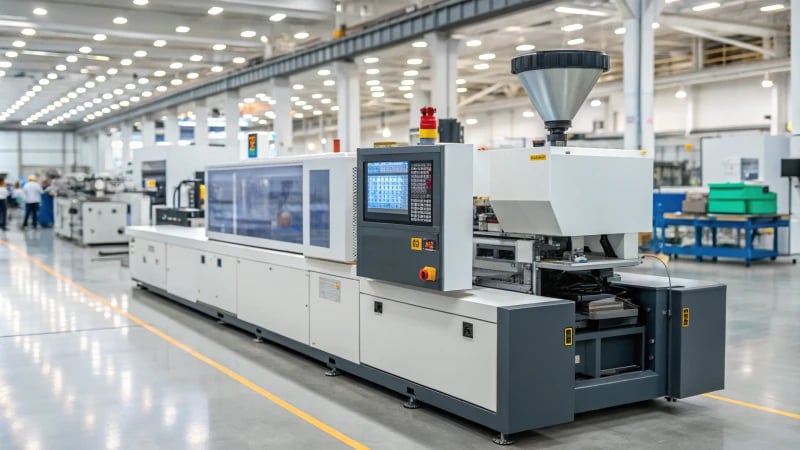
Real-time Monitoring with IoT
I still remember the first time I witnessed the power of IoT in molding. It was like watching a symphony of technology play out seamlessly. Sensors were everywhere, gathering data on temperature, pressure, and humidity as if they were the conductors of this intricate orchestra. This Internet of Things (IoT)13 system allowed for instantaneous adjustments, making sure everything was just right. I was amazed at how it minimized human error and reduced downtime by predicting maintenance needs before they became issues.
Technology | Application | Benefits |
---|---|---|
IoT Sensors | Real-time data collection | Improved precision, reduced errors |
Artificial Intelligence and Predictive Maintenance
Artificial Intelligence in molding isn’t just about flashy new gadgets—it’s about peace of mind. Imagine knowing your machines so well that you could predict when they’d need a little TLC before they even gave a hint of trouble. That’s exactly what AI offers with predictive maintenance. It felt like having a crystal ball for machinery health; no more unexpected breakdowns or costly downtimes.
Predictive maintenance not only enhances machine longevity but also ensures consistent production quality. The productivity boost and cost savings were not just numbers on a spreadsheet—they were tangible changes I experienced in my day-to-day operations.
Technology | Application | Benefits |
---|---|---|
AI Systems | Predictive maintenance | Enhanced efficiency, reduced downtime |
Automation for Efficiency
Automation was the game-changer I didn’t know I needed until I saw it in action. Watching robotic arms manage injection molding14 tasks with tireless precision felt like witnessing a glimpse of the future. These machines handled repetitive tasks flawlessly, freeing up valuable human resources for more complex challenges.
This technology also allows human operators to focus on more complex tasks, thus improving overall workflow efficiency. The consistency they brought to every production run was unmatched, aligning perfectly with our lean manufacturing goals.
Incorporating these smart technologies not only enhances the efficiency of molding processes but also ensures that companies remain competitive in a rapidly evolving manufacturing industry.
Explore more about smart manufacturing trends15 to stay ahead in the game.
IoT reduces human error in molding processes.True
IoT sensors provide real-time data, allowing automatic adjustments, minimizing human error.
AI systems increase downtime in molding operations.False
AI predicts failures, enabling proactive maintenance, thus reducing downtime.
How Are Emerging Trends Shaping Design and Production?
Have you ever wondered how the latest trends are shaping the way we design and produce things? Whether it’s automation or sustainability, these changes are making waves.
Emerging trends in automation, sustainability, and digitalization are transforming design and production, enhancing efficiency and promoting eco-friendly practices throughout the process.
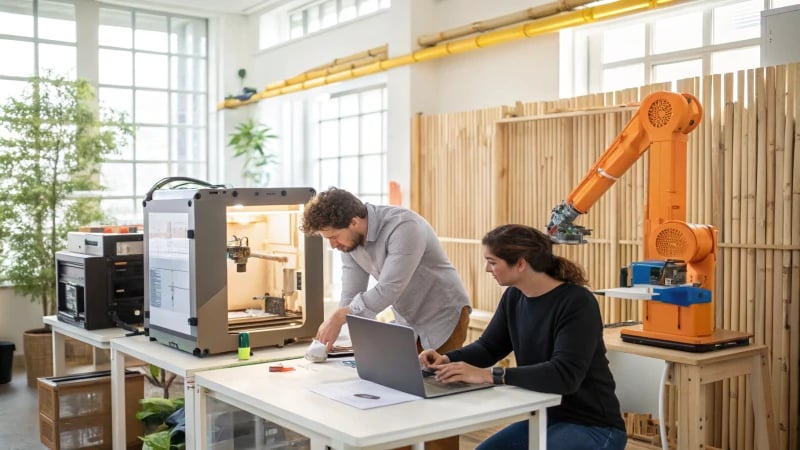
The Rise of Automation in Design and Production
I remember the first time I saw automation in action at a trade show. It was mesmerizing—machines seamlessly creating intricate designs with a precision that seemed almost magical. Today, automation has become a game-changer in design and production. With CAD software integrated with AI, I can whip up complex models16 that balance beauty and function with just a few clicks.
Automation Benefits | Impact on Production |
---|---|
Increased Efficiency | Faster turnaround times for product launches |
Cost Reduction | Lower operational costs due to reduced labor |
Enhanced Precision | Improved quality control and less wastage |
Embracing Sustainability
Back in my early days as a designer, I used to think sustainability meant just recycling. But oh, how times have changed! Now, it’s about weaving eco-friendly materials and processes into every part of production. For instance, using biodegradable plastics doesn’t just help the planet—it ensures our products hold up to high standards of quality while maintaining product integrity17.
- Materials: Switching to renewable resources like bamboo
- Processes: Implementing energy-efficient manufacturing techniques
The Role of Digitalization
I once tried a VR headset at a colleague’s studio, and it blew my mind. These digital tools are not just sci-fi gadgets; they are changing how we create. With VR and AR, I can walk through a design before it’s even built, tweaking things on the fly for better results.
- VR/AR: Allows for immersive design experiences
- Digital Twins: Provides a virtual replica of physical assets for testing
And let’s not forget digitalization’s role in mass customization—making personalized products is now a breeze without sacrificing efficiency.
Consumer-Driven Design Trends
Today’s consumers want products that feel tailor-made for them and don’t harm the planet—a challenge I relish as it pushes my creativity. By incorporating feedback right into the design process18, I can create something that hits all the right notes.
- Customization: Offering bespoke options to cater to individual preferences
- User-Centric Design: Prioritizing user experience and functionality
These trends require us to stay nimble, constantly innovating to keep pace with what’s next in design strategies. It’s an exciting time to be in this field!
Automation reduces manual labor in production.True
Automation replaces repetitive tasks, enhancing efficiency and precision.
Sustainability is not a focus in modern design.False
Eco-friendly practices are central to contemporary design strategies.
Where Is the Future of Injection Molding Heading?
Imagine a world where machines know exactly what you need before you do. That’s the future of injection molding, driven by cutting-edge technology and green innovations.
The future of injection molding focuses on automation, advanced materials, and sustainability to boost efficiency, reduce costs, and support eco-friendly initiatives, driving major industry advancements.
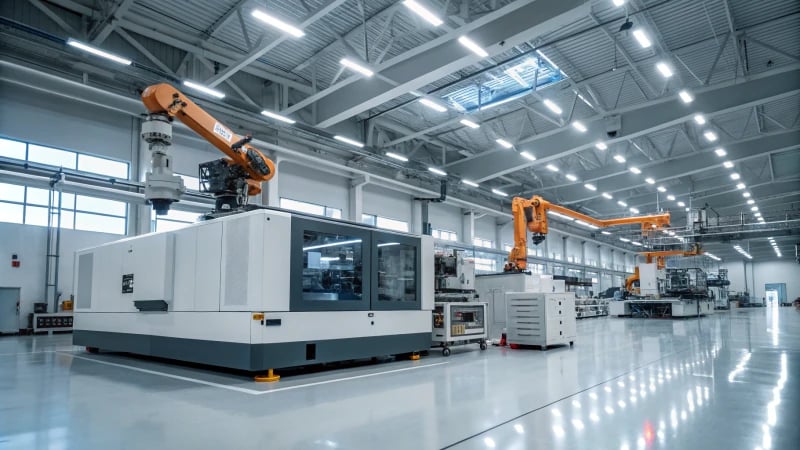
Automation and Robotics in Injection Molding
I still remember the first time I saw a robot arm in action at a factory. It was mesmerizing. Today, automation is more than just a fancy tool—it’s revolutionizing the injection molding industry. Picture robots gracefully handling tasks like part removal and quality inspection. This isn’t just about speed; it’s about precision, reducing human error, and upping safety standards. With artificial intelligence19 in the mix, we’re talking real-time monitoring and predictive maintenance, meaning less downtime and more uptime.
- Key Benefits:
- Increased production speed
- Reduced human error
- Enhanced safety standards
Advanced Materials
When I first heard about bioplastics, I was intrigued by their promise. Now, high-performance polymers and these eco-friendly materials are changing the game in injection molding. Imagine materials that are lightweight yet strong or ones that reduce our carbon footprint—it’s not just sci-fi anymore. These innovations offer a superior strength-to-weight ratio and environmental benefits that make them incredibly appealing.
Material Type | Benefits |
---|---|
High-performance | Lightweight yet strong |
Bioplastics | Eco-friendly and renewable |
Sustainability Practices
I’ve always believed sustainability isn’t just a trend; it’s essential for our future. In the world of injection molding, this means recycling and using renewable energy sources have become standard practice. Companies are now embracing circular economy principles20 to reduce waste and minimize their environmental impact.
- Strategies for Sustainability:
- Use of recycled materials
- Energy-efficient machinery
- Waste minimization techniques
Digital Transformation
The concept of Industry 4.0 still excites me—it’s like living in the future. By harnessing digital twin technology21, manufacturers can create virtual models to simulate, predict, and optimize processes before they even begin on the production floor. It’s about making smarter decisions in real-time, boosting accuracy, and cutting costs in prototyping.
Automation reduces human error in injection molding.True
Automation enhances precision and consistency, minimizing errors.
Bioplastics are less eco-friendly than traditional plastics.False
Bioplastics are more eco-friendly due to biodegradability.
Conclusion
Injection molding technology is advancing through automation, sustainability, and innovative materials, enhancing efficiency and reducing environmental impact while transforming manufacturing processes for designers and engineers.
-
Discover how robotics enhance operational efficiency by reducing manual labor and increasing production speed. ↩
-
Learn how sensors ensure product quality by providing real-time feedback on process variables. ↩
-
Understand the synergy between automated systems and CAD tools in optimizing design workflows. ↩
-
Explore future trends and implications of automation on manufacturing industries. ↩
-
Explore biodegradable polymers’ applications and benefits in molding, highlighting their environmental advantages. ↩
-
Learn how closed-loop systems enhance sustainability by reusing waste materials, reducing environmental impact. ↩
-
Discover how electric machines boost efficiency and sustainability with lower energy use and improved precision. ↩
-
Understand how DfE principles promote sustainability by integrating eco-friendly strategies throughout the product lifecycle. ↩
-
Stay updated on cutting-edge sustainable practices that transform injection molding towards greener solutions. ↩
-
Explore how bio-based polymers are reshaping the injection molding industry by offering sustainable alternatives to conventional plastics. ↩
-
Discover the benefits of using reinforced composites for enhanced strength and lightweight solutions in various industries. ↩
-
Learn about the diverse applications of high-performance thermoplastics in industrial settings where durability is crucial. ↩
-
Learn how IoT facilitates real-time monitoring and process optimization in molding industries. ↩
-
Discover how robotic arms enhance precision and efficiency in injection molding tasks. ↩
-
Stay updated on the latest smart manufacturing trends to keep your business competitive. ↩
-
Explore how automation enhances precision and efficiency in CAD modeling, crucial for modern designers. ↩
-
Learn about the environmental advantages and functional integrity of using biodegradable plastics. ↩
-
Understand the importance of integrating user feedback to meet consumer demands. ↩
-
Explore how AI optimizes injection molding processes through enhanced precision and reduced downtime. ↩
-
Understand how these principles minimize waste and enhance resource efficiency. ↩
-
Discover how digital twins improve production accuracy and efficiency. ↩