Have you ever considered how tiny details in mold design might affect your budget? Small features often have a huge impact. Sometimes they even ruin financial plans. These minute aspects in the mold’s blueprint might surprise you with their significance. Details are truly important. They deserve attention.
The design of main and branch channels in molds impacts production costs. It does this by changing how much material gets used. It also affects how complex the processing is and how often maintenance is needed. A clever design finds a good balance. It lowers costs but keeps high quality. Quality must not suffer.
Starting with mold design was really surprising for me. Tiny changes led to big savings. Take the main channel. High-quality steel is very necessary to handle hot plastic and pressure. But a channel too long or wide uses more materials. It needs special care for durability. This is not just about numbers; it’s about smart design. Effective design saves money and works efficiently.
Runner design was something I underestimated. Its length and shape decide steel use. A long or uneven runner might seem minor but raises costs. Shape affects processing. Complex shapes need special tools, increasing expenses. Every choice – channel length or runner shape – balances quality and cost.
I learned this during a project where designs looked good. Once we checked the numbers, we saw long-term costs. Smart changes were needed. Adjusting these parts saved money and made production smoother. It really improved efficiency. Such experiences show the value of smart design in making molds.
Main channel design affects material consumption in molds.True
Main channel design determines the amount of material needed, impacting costs.
Branch channels have no impact on mold maintenance needs.False
Branch channel design influences maintenance due to complexity and wear.
What are the key material cost factors in channel design?
Have you ever asked why certain channel designs cost more than others? Some designs require more resources and specialized skills. Others use high-quality materials that increase expenses. Different design elements can add complexity, raising costs even further. High demand for specific styles may impact price, too. Popular or trendy designs could be more expensive.
Key costs in channel design involve the materials’ quality, design complexity and needed treatments. High-quality materials often raise costs. Intricate designs also bring extra costs. But these factors increase strength and performance. Good materials last long. Good designs work well.
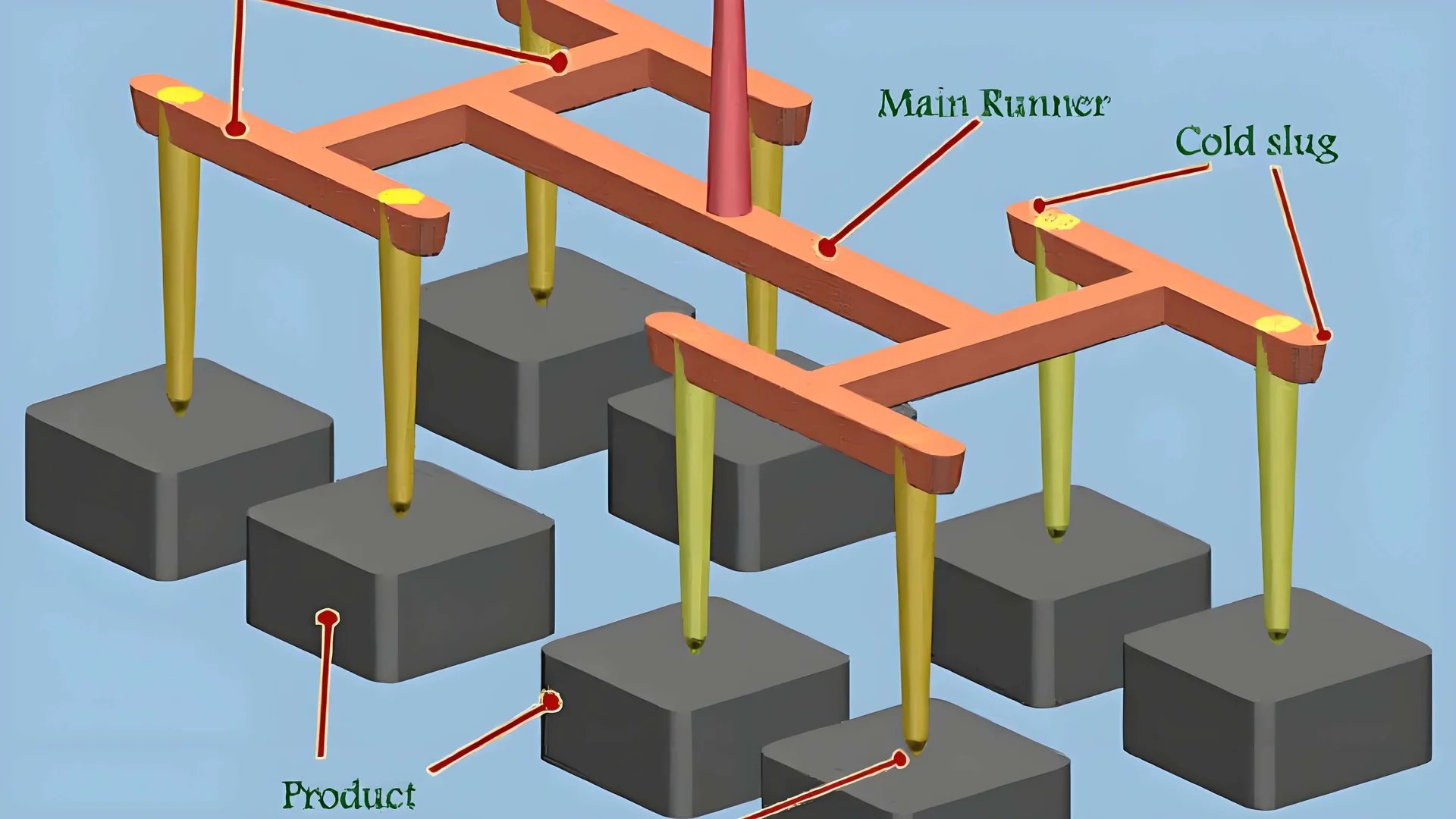
Quality of Materials Used
When I started mold design, I found that picking the right materials is very important. Think of it like building a house. You wouldn’t use weak wood for the base, right? In channel design, using strong steel1 really helps, especially for parts like the gate sleeve that face big heat and pressure. These materials cost more at first but last longer, saving money over time.
Material Type | Application | Cost Impact |
---|---|---|
High-quality steel | Gate sleeve | Higher initial cost but increases durability |
Design Complexity
Remember a time when putting something together felt tricky with too many screws and pieces? Channel design can feel similar. Complex designs increase costs because they need more material and accurate making. If the main channel is too long or wide, it uses more material. Special shapes might need unique ways to process.
- Complex shapes: Increase processing time2 and need special tools.
- Length and size: Bigger sizes mean more material.
Required Treatments
Important treatments like heat or surface changes increase channel durability. My first try taught me this was very important. I skipped it to save money but got a product that didn’t last. These methods cost upfront but help by resisting rust and wear.
- Heat treatment: Increases hardness3 and strength.
- Surface treatment: Guards against erosion, making the mold last longer.
Balancing Cost with Performance
Choosing between cost and performance feels like picking a fancy car or a trusty old one. Quality materials and complex designs cost more but often work better and need less repair later. In my mold design journey, looking at these factors closely kept initial costs low and efficiency high over time.
Discovering more about cutting mold production costs4 involves considering material choice, design, and needed treatments. It’s crucial to learn how these affect each other to find a balance between saving money and keeping product quality high.
High-quality steel increases gate sleeve cost.True
High-quality steel is used for its durability, increasing initial costs.
Complex designs decrease material costs.False
Complex designs require more material and precision, raising costs.
How Does Channel Shape Affect Processing Costs?
Have you ever thought about how the form of a channel could decide your production costs?
Channel shape is very important in deciding costs linked to processing. It affects how the material is used. It also influences precision needs and maintenance tasks. Good channel designs really use resources wisely. Costs stay low with good designs. On the other hand, bad shapes probably raise expenses a lot.
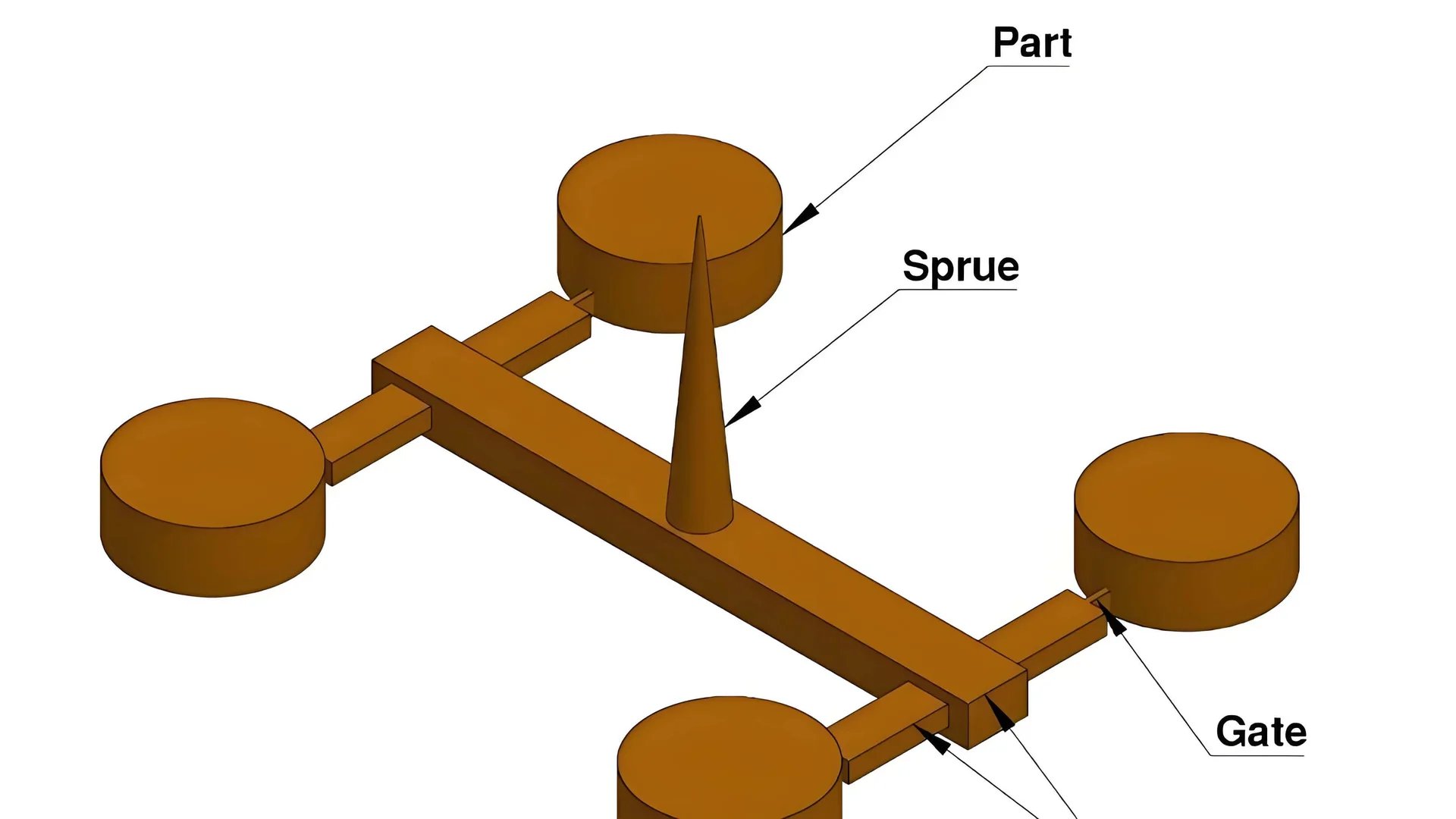
The Role of Main Channel Design in Mold Production
The design of the main channel is critical in mold production. An improperly designed main channel5 can escalate material costs due to excessive steel usage. High-quality steel is essential to endure high temperatures and pressures. If channels are too long or large, the cost increases.
Additionally, processing costs rise with high-precision requirements. For instance, a cone-shaped channel demands strict accuracy in cone angles and surface roughness. Inadequate processing accuracy necessitates rework or advanced CNC equipment use, increasing expenses.
Cost Factor | Impact on Processing Costs |
---|---|
Material Cost | High-quality steel requirement |
Processing Cost | Precision equipment needed |
Maintenance Cost | Frequent replacements |
Runner Design’s Impact on Production Costs
The runner’s design also plays a pivotal role. Length and size directly affect material consumption. Long or unbalanced runners require more materials, increasing costs. Complex shapes like non-circular runners might need special technologies, further hiking expenses.
The cross-sectional shape influences processing difficulty; circular runners are efficient but complex to process, necessitating special tools. Trapezoidal or U-shaped runners are easier to process, thus potentially reducing costs.
Surface roughness requirements (e.g., Ra = 1.6μm) also demand precise processing, with additional polishing needed for lower roughness levels.
Maintenance costs arise from poor design causing wear or blockage. Repairs or replacements can affect efficiency, indirectly boosting production costs.
Design Aspect | Processing Challenge |
---|---|
Cross-sectional Shape | Processing complexity |
Surface Roughness | Polishing requirements |
Maintenance Needs | Repair and replacement costs |
Implications for Other Industries
Beyond mold production, channel shape impacts other fields like hydrology and civil engineering. In hydrology, river channel shapes influence water flow and velocity, affecting erosion6 and sediment transport. Understanding these dynamics helps manage water resources efficiently.
In semiconductor manufacturing, channel shape affects material flow in microfabrication processes. Channel efficiency can enhance productivity and reduce waste.
For engineers like Jacky, optimizing channel shapes is vital for maintaining production efficiency and cost-effectiveness. By leveraging advanced design tools and techniques, he can improve component performance while controlling expenses. CAD tools7 are instrumental in achieving these goals, allowing for precise simulations and adjustments before physical production begins.
Overall, the impact of channel shape on processing costs highlights the necessity for thoughtful design and strategic planning across various industries. By focusing on these aspects, businesses can significantly enhance their operational efficiency and cost management strategies.
Cone-shaped channels increase processing costs.True
Cone-shaped channels require precision in angles and surface roughness, raising costs.
Circular runners are the easiest to process.False
Circular runners are efficient but complex, requiring special tools for processing.
What Challenges Do We Face with Poor Channel Design?
Had a project where everything felt stuck and messy? Bad channel design in mold production often brings surprise maintenance problems.
Poorly designed mold channels often cause more wear, corrosion and clogs. This situation requires frequent repairs and new parts. Costs rise. Efficiency drops. Proper channel size and the right materials probably reduce these problems.
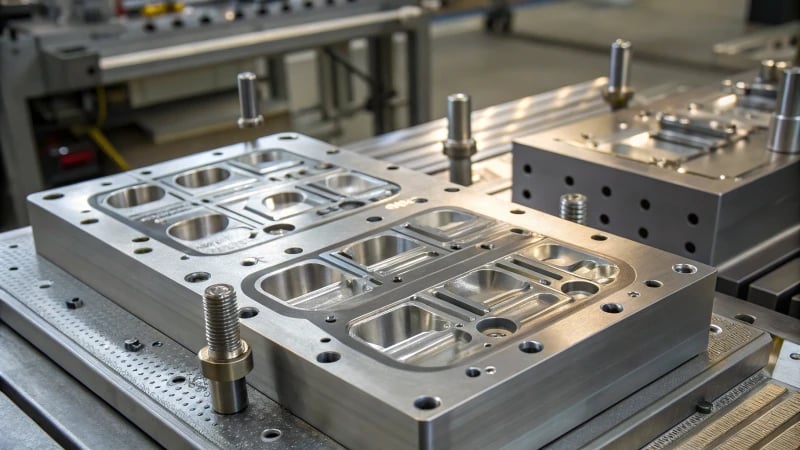
Impact on Wear and Corrosion
I remember working on a big project where everything seemed to go wrong. The channels were very narrow. The plastic melt rubbed against the sides, wearing them down quickly. This friction felt like running a marathon in shoes that are too tight.
Solutions:
- Use strong materials: Investing in materials that resist wear and corrosion is like buying an insurance policy. It saves you trouble in the future.
- Regular checks: Routine inspections revealed issues early. It’s like seeing a doctor regularly; you catch problems before they turn into crises.
Blockages and Flow Issues
Once, our production line stopped because of a blockage. It felt like trying to drink a smoothie through a bent straw! It showed me the need for well-designed channels for smooth flow.
Solutions:
- Proper channel sizes: Correct channel sizing is like having roads that handle busy traffic without jams.
- Regular cleaning: Frequent cleaning was crucial. It prevented problems from starting.
Issue | Cause | Impact |
---|---|---|
Wear | Narrow channels increasing friction | Frequent replacements |
Corrosion | Material not resistant to high temperature | Increased maintenance |
Blockages | Poor channel alignment | Production delays |
Increased Costs from Frequent Maintenance
Frequent maintenance was like keeping a leaky boat from sinking. Fix one leak, another appears. This happened because we used materials that couldn’t take the high pressure and heat.
- Choose the right materials: Using materials for high temperatures was vital – like wearing the right gear to climb a mountain.
- Design reviews: We started regular design reviews. This was like having a map for a hike; it helped spot weak points before they caused trouble.
For more insights into how material selection8 impacts mold life, industry experts can offer specific advice tailored to your needs.
Narrow channels increase friction and wear.True
Narrow channels cause higher friction, leading to faster wear of channel walls.
Poor channel design reduces maintenance frequency.False
Improper design increases maintenance needs due to wear, corrosion, and blockages.
How Can Proper Channel Design Improve Production Efficiency?
Picture cutting through inefficiencies as smoothly as slicing butter with a well-designed channel in your production process.
Good channel design in mold manufacturing helps production run better by lowering material and processing costs. It improves quality and cuts down on maintenance needs. Operations become smoother. This leads to higher overall productivity.
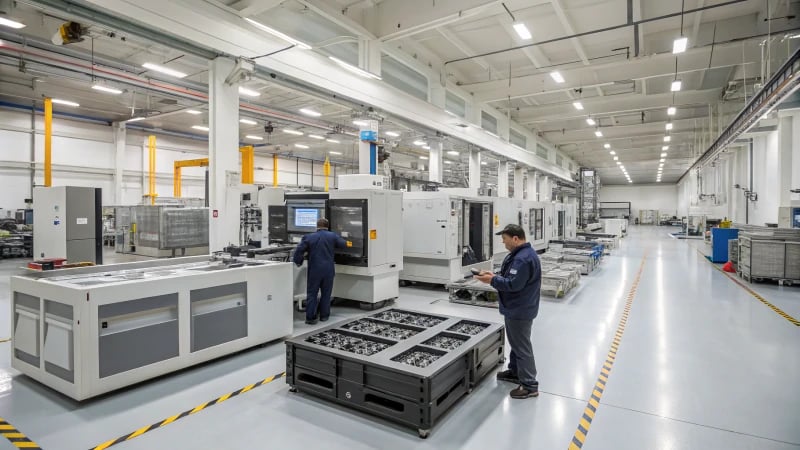
Main Channel Design’s Role in Efficiency
Main channel design is like building the backbone of mold production. The right shape is important, but smart use of materials matters too. Using high-quality steel for the gate sleeve is really essential. This steel handles the tough conditions like high-temperature plastic melt and injection pressure that designs often face. A long or wide main channel design means more steel costs, which everyone wants to avoid.
Precision is very critical. Once, I tried to save money on CNC equipment for a cone-shaped channel. The rework costs were a real lesson! Precise cone angles and smooth surfaces are like a perfectly tuned guitar; anything less may disturb the entire process. Precision cannot be ignored.
Maintenance is another key factor. A poor design leads to more wear and tear. This results in frequent replacements and increased downtime. I’ve adjusted timelines many times due to frequent part swaps. Trust me, productivity suffers a lot.
Runner Design’s Influence on Cost and Quality
Runner design plays a big role in mold efficiency. Mistakes here cause wasted material and higher costs. I’ve seen molds with unbalanced runners that waste material like there’s no tomorrow, adding extra expenses.
Circular runners work well but are tricky to process. It’s like walking a tightrope – hard but rewarding if done correctly. On the other hand, trapezoidal or U-shaped runners make processing easier but may not always fit the task.
A balanced runner is like a well-conducted orchestra, bringing even flow and high product quality. When I got this balance right, defects dropped and yield rates improved. Achieving smooth surfaces does cost more in polishing, but the quality improvement is worth every penny.
Visualizing Design Impact: A Table Overview
Aspect | Impact on Cost | Efficiency Gain |
---|---|---|
Main Channel | High material use if oversized | Precision reduces rework |
Runner Design | Complex shapes increase cost | Balanced flow enhances quality |
Focusing on these elements has greatly increased production efficiency through optimized channel designs. Like tuning an engine, every adjustment leads to smoother operations and better output. For those interested in understanding more, exploring more on mold production strategies9 could be a beneficial next step.
Poor channel design increases material costs.True
Inefficient designs require more high-quality steel, raising costs.
Complex runner shapes decrease processing expenses.False
Complex shapes need special processing, increasing costs.
Conclusion
The design of main and branch channels in molds significantly influences production costs by affecting material usage, processing complexity, and maintenance needs, ultimately impacting efficiency and quality.
-
High-quality steel ensures durability under high temperatures and pressures, minimizing long-term maintenance costs. ↩
-
Complex designs can increase production time and require specialized tools, affecting overall costs. ↩
-
Heat treatment enhances steel’s hardness and durability, reducing wear and extending the mold’s lifespan. ↩
-
Effective strategies balance material quality, design complexity, and necessary treatments to manage costs efficiently. ↩
-
Explore how main channel design affects mold production costs and efficiency. ↩
-
Learn about how river channel shapes impact erosion and sediment flow. ↩
-
Discover how CAD tools help in designing cost-effective components. ↩
-
Learn about materials that withstand high temperatures, essential for reducing wear and maintenance costs in molds. ↩
-
Discover advanced strategies for enhancing production efficiency in molds. ↩