Ever wondered how a simple cavity in a mold shapes the objects we use daily?
In injection molding, the cavity is the mold’s hollow section shaping molten plastic. It determines the product’s final appearance and precision, essential for manufacturing accuracy.
I remember when I first learned about cavities in molds; it was like discovering a hidden art form. These spaces might seem just empty hollows, but they’re the unsung heroes in creating everything from tiny toy cars to sleek plastic bottles. Imagine the cavity as the sculptor’s chisel, defining each contour and detail with precision. Whether we’re talking about a single-cavity mold for a custom piece or a multi-cavity mold for mass production, each type has its charm and efficiency. This understanding not only refines our designs but also boosts our production efficiency, ensuring that what we envision is exactly what we get.
Cavity defines the outer structure in injection molding.True
The cavity shapes the external features of the molded part.
Cavities have no impact on manufacturing efficiency.False
Cavity design influences precision, affecting production speed and quality.
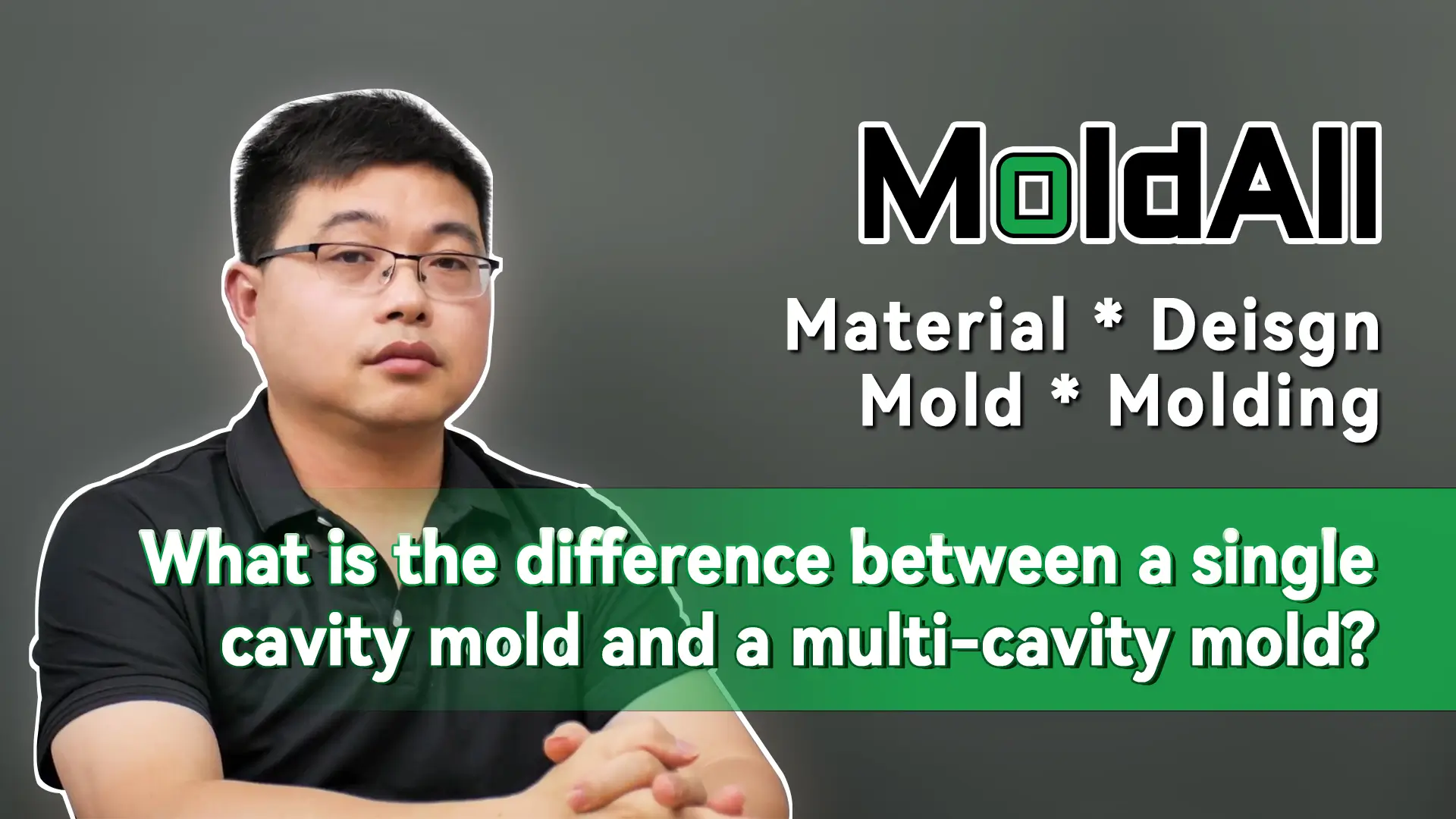
What is a Single-Cavity Mold and When Should You Use It?
Imagine building your dream model car with just one mold! That’s the magic of single-cavity molds in manufacturing.
A single-cavity mold, ideal for low-volume production and precision tasks, is used for prototyping or making large, intricate parts by shaping molten plastic in one cavity.
Understanding Single-Cavity Molds
You know that feeling when you’re about to create something unique and special, like crafting a personalized gift? That’s what using a single-cavity mold1 is all about. This mold has just one cavity, acting as a negative impression of the final product. Imagine you’re working on a custom toy car—the cavity mirrors every detail of that car, from the sleek body lines to the tiny wheels.
When to Use Single-Cavity Molds?
- Low Volume Production: Sometimes, you’re not looking to mass-produce; you need just enough to test the waters. For those small runs where precision is key, single-cavity molds are your best friend.
- Complex Parts: Remember that time I tried to make an intricate chess set for a friend? It needed precision just like when crafting custom prototypes or intricate designs.
- Large Parts: If you’re working on something big, like a large component that requires careful cooling, single-cavity molds help minimize shrinkage and ensure quality.
Use Case | Description |
---|---|
Prototyping | Ensures precision and quality in small batches |
Custom Products | Suitable for unique, high-value components |
Large Components | Handles significant size with detailed features |
Comparing with Multi-Cavity Molds
While single-cavity molds are like that one-of-a-kind handcrafted item, multi-cavity molds2 are your go-to for mass production. They churn out multiple parts in one cycle, speeding up the process but sometimes sacrificing those delicate details.
Key Differences:
- Production Speed: It’s like having multiple pairs of hands working simultaneously; multi-cavity molds give you faster cycles by casting several parts at once.
- Cost Efficiency: When demand is high, these molds reduce costs by producing more in less time.
- Part Consistency: Like a master craftsman focusing on one piece at a time, single-cavity molds deliver consistent quality and finish.
For those of us in manufacturing and design, understanding these nuances helps us decide how to balance precision and volume effectively. Delve deeper into mold design considerations3 to see how these choices impact everything from production outcomes to product quality.
Single-cavity molds are ideal for high-volume production.False
Single-cavity molds are best for low-volume production due to precision.
Multi-cavity molds offer faster production cycles than single-cavity molds.True
Multi-cavity molds produce multiple parts per cycle, increasing speed.
How Do Multi-Cavity Molds Boost Production Efficiency?
Imagine doubling your output without doubling your work! That’s the magic of multi-cavity molds.
Multi-cavity molds enhance production efficiency by molding multiple parts at once, significantly cutting cycle time and per-unit costs, and increasing overall output compared to single-cavity molds.
Understanding Multi-Cavity Molds
I still remember the first time I encountered a multi-cavity mold. It was like witnessing a well-choreographed ballet, where each cavity in the mold danced perfectly with molten plastic, creating identical parts in one elegant cycle. In essence, these molds house multiple cavities within a single base, letting you mold several parts simultaneously.
Benefits Over Single-Cavity Molds
- Increased Output: Imagine using a 6-cavity mold—it’s like having six sets of hands working at once, multiplying your output without any extra effort. Multi-cavity molds4 are truly a marvel when it comes to cranking up production rates.
- Cost Efficiency: Each cycle gives you more parts, which means your cost per part drops significantly. It’s a win-win situation, saving on labor, machine time, and energy.
Factors to Consider
- Part Uniformity: Ensuring every part is just like the next can be tricky. It’s like baking cookies—consistent oven temperature and dough distribution are key to getting perfect cookies every time.
- Mold Design: A well-thought-out design reduces cycle time and minimizes defects, much like having a reliable recipe that delivers perfect results every bake.
Feature | Single-Cavity Mold | Multi-Cavity Mold |
---|---|---|
Production Rate | Low | High |
Cost Efficiency | Moderate | High |
Complexity | Simple | Complex |
Application Scenarios
These molds shine in high-volume production settings like packaging or automotive components. Imagine producing plastic bottle caps5—a multi-cavity mold can churn out thousands of caps an hour, effortlessly keeping up with demand.
Challenges in Using Multi-Cavity Molds
While they’re fantastic tools, they do need a bit of finesse. Precise calibration is crucial, as even slight variations can cause inconsistencies, much like how a slight misstep can lead to burnt cookies. Plus, the initial cost of creating multi-cavity molds6 can be steep, but the efficiency and long-term savings make it worthwhile.
Multi-cavity molds increase production rates sixfold.True
A 6-cavity mold produces six times more parts per cycle than a single-cavity.
Single-cavity molds are more cost-efficient than multi-cavity molds.False
Multi-cavity molds reduce the cost per part due to higher output efficiency.
Why is Temperature Control Crucial for Cavity Performance?
Ever wondered why some plastic products hold their shape while others warp? It all comes down to temperature control during molding.
Temperature control is vital in injection molding to ensure uniform cooling of plastic, which minimizes defects like warping and shrinkage, thereby maintaining the shape and quality of the molded parts.
Understanding Cavity in Injection Molding
Think of a mold cavity as a blueprint or a skeleton of the final product. It’s like when I tried baking my first intricate cake, and I realized how the details in the cake pan made all the difference. The cavity is where molten plastic is injected, taking on the intricate details of the design. If you’re crafting something like a toy car, every little bump and groove has to be just right.
The Role of Temperature Control
When it comes to molding, temperature control is the unsung hero. Imagine trying to bake bread without regulating your oven’s temperature—you’d end up with a crusty outside and a gooey inside. The same concept applies here. Temperature control ensures that as the molten plastic fills the cavity, it cools evenly, reducing imperfections like warping and shrinkage.
Benefits of Temperature Control | Impact on Cavity Performance |
---|---|
Reduces Warping | Maintains shape integrity |
Minimizes Shrinkage | Ensures dimensional accuracy |
Improves Surface Finish | Enhances aesthetic appeal |
Types of Cavities and Temperature Control
Depending on what you’re making, different molds require different approaches:
- Single-Cavity Mold: This is like a bespoke tailor-made suit—perfect for precision and detail but not for mass production. Every detail matters, so temperature has to be spot-on.
- Multi-Cavity Mold: Think of this like a cupcake tin where you want every cupcake to come out exactly the same. Uniform temperature across all cavities is vital for consistency.
Learn more about cavity types7 and their specific needs in manufacturing.
Real-World Application Examples
In my work with consumer electronics, I’ve seen how precise temperature control can mean the difference between a perfect fit and a misshapen disaster. In pharmaceuticals, it’s even more critical—imagine the stakes when molding medical devices or packaging. Temperature regulation ensures safety and efficacy by keeping dimensions exact.
Explore how temperature influences pharmaceutical manufacturing8 to maintain high standards in product quality.
Uniform cooling prevents warping in injection molding.True
Uniform cooling helps maintain the shape integrity of molded parts.
Multi-cavity molds don't need temperature control.False
Even temperature distribution is crucial for consistent multi-cavity mold output.
How Do Cavity Surface Finishes Affect Product Quality?
Ever wonder how the finish on a mold cavity can make or break your product’s quality?
Cavity surface finishes influence product quality by affecting aesthetics, functionality, and durability. Smooth finishes enhance appearance and reduce defects, whereas rough surfaces may cause imperfections.
The Role of Cavity Surface Finishes
When I first started diving into the world of injection molding, it felt like stepping into a whole new universe. I remember walking into a factory, the hum of machines all around me, and seeing a mold for the first time. A mold is like the unsung hero in the manufacturing process, especially the cavity part, which is the hollow space9 that shapes the final product. It’s like when you make a sandcastle using a bucket—the bucket’s shape determines what your castle looks like.
The surface finish of this cavity isn’t just about looks—it’s about performance too:
- Aesthetic Appeal: If you’re like me and love a good-looking gadget, you’ll know how much a smooth finish can add to the allure. It’s crucial for things like electronics casings.
- Functional Performance: I once had a project where the parts just wouldn’t fit right because of a rough finish causing friction.
- Durability: A smoother finish helps avoid stress points that can lead to cracks or breaks.
Types of Cavity Surfaces
Getting the right finish type can feel like choosing the perfect wallpaper for your living room—each has its vibe:
Finish Type | Characteristics | Use Cases |
---|---|---|
Polished | Ultra-smooth, reflective | High-end products needing visual precision |
Matte | Non-reflective, textured | Products requiring minimal glare |
Textured | Deliberate pattern for grip or aesthetics | Handles or ergonomic designs |
Impact on Manufacturing Processes
You wouldn’t believe how much these finishes can affect efficiency:
- Cycle Time: A smooth surface can be like greasing a slide, making everything faster and more efficient.
- Tool Wear: I learned this the hard way when rough surfaces increased tool wear, leading to unexpected downtime and costs.
Considerations for Designers
As designers, we have to juggle a lot—precision, environment, aesthetics. It’s about finding that sweet spot where everything clicks together.
Challenges and Solutions
Rough finishes can be a nightmare with defects like sink marks. I’ve found that ensuring uniform cooling and utilizing multi-cavity molds can be game changers.
Understanding these nuances has been pivotal in my journey as a designer10, ensuring that my products not only meet but exceed expectations.
Further Reading
Curious to delve deeper into how cavity design impacts molding processes? Check out more resources on mold design optimization11. It’s fascinating stuff!
Smoother finishes reduce stress concentrations.True
Smoother surfaces distribute stress evenly, minimizing potential failure points.
Textured surfaces increase cycle time in molding.False
Textured surfaces can slow material flow, but do not inherently increase cycle time.
Conclusion
Cavities in injection molding are essential for shaping molten plastic into precise forms, influencing product quality, production efficiency, and surface finishes in manufacturing processes.
-
Learn more about the fundamental aspects of single-cavity molds and their applications. ↩
-
Understand how single-cavity molds differ from multi-cavity molds in terms of production and efficiency. ↩
-
Discover critical factors in mold design that affect production quality and efficiency. ↩
-
Discover how multi-cavity molds enhance production rates by increasing output and lowering costs in manufacturing. ↩
-
Explore how multi-cavity molds efficiently produce large quantities of plastic bottle caps. ↩
-
Learn about the initial investment required for multi-cavity mold development and its long-term benefits. ↩
-
Knowing various mold cavity types aids in selecting the right approach for efficient production. ↩
-
Temperature control ensures product safety and efficacy in pharmaceutical manufacturing. ↩
-
Clicking this link provides a detailed understanding of cavity definitions, crucial for grasping mold design basics. ↩
-
Explore this link to learn how top designers approach mold creation, enhancing your design skills. ↩
-
This link offers advanced strategies to improve mold efficiency and product quality through design tweaks. ↩