Explore the interesting world of polystyrene (PS) and its part in injection molding. If you ever thought about how those daily plastic items come to life, you are in the correct spot.
The injection molding process for PS material involves melting polystyrene resin, injecting it into a mold, cooling, and then ejecting the finished product. Key parameters like temperature and pressure must be precisely controlled to accommodate PS‘s unique properties, including its brittleness and heat sensitivity.
This short summary shows the main steps, but learning PS injection molding needs deep knowledge of the material’s details, best conditions and possible problems. Read further to find detailed information that will grow your knowledge and use of this flexible material.
PS requires drying before injection molding.False
PS often does not need drying unless wet, then dry at 70°C-80°C.
What Are the Key Steps in the Injection Molding Process for PS?
Learning the injection molding process for polystyrene (PS) needs several important steps to get the best results.
The injection molding process for PS includes material preparation, melting, injection, cooling, and ejection. Each step is crucial to address PS‘s brittleness, low impact strength, and heat sensitivity, ensuring a high-quality final product.
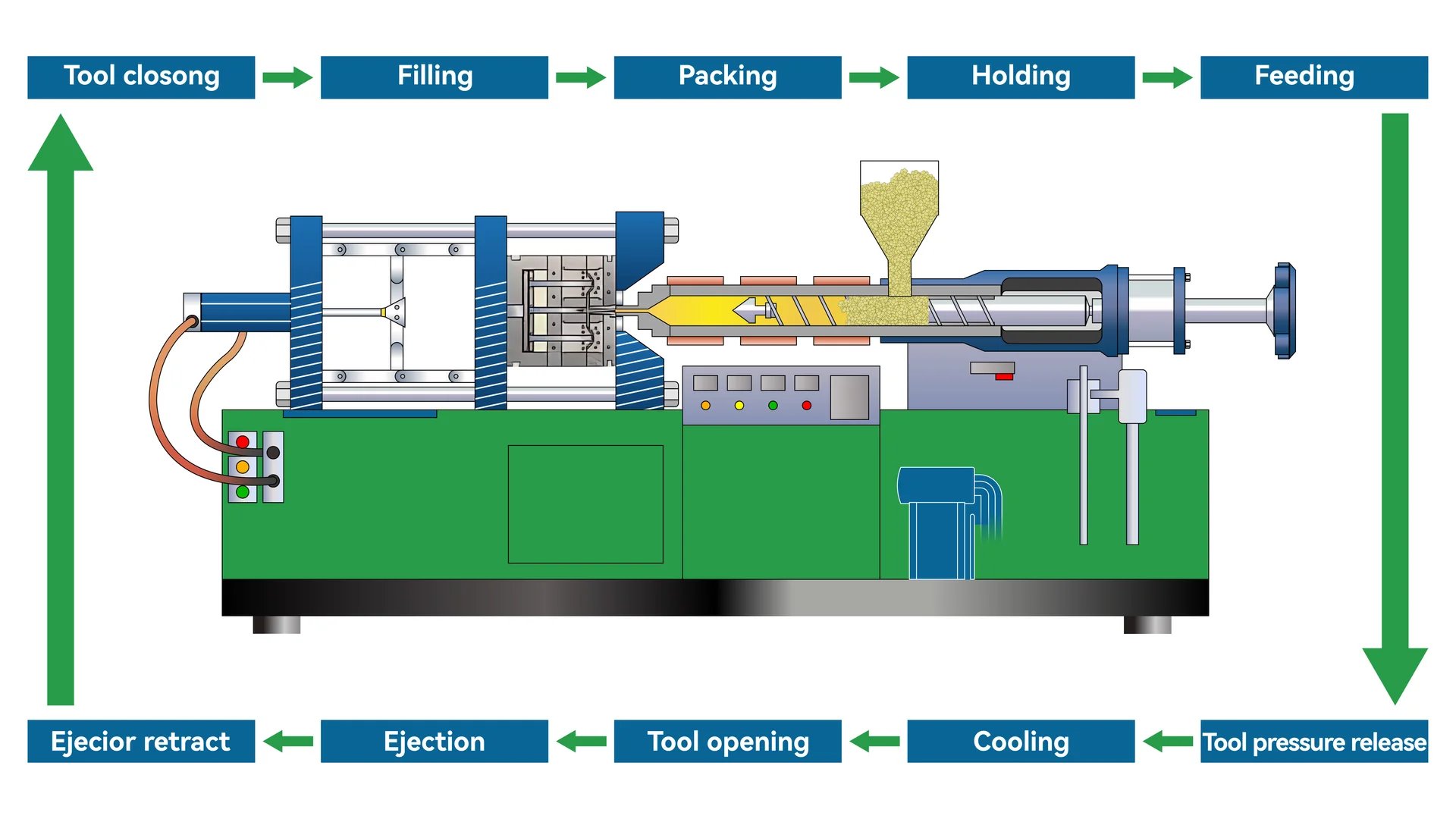
Material Preparation
Before starting the injection molding process1 for polystyrene (PS), prepare the material with care. PS has different kinds like ordinary polystyrene, expanded polystyrene (EPS), and high impact polystyrene (HIPS). Each kind has special features that change how it is processed.
- Selection of Material: Pick the right type of PS that fits the product needs. Ordinary PS is very clear and insulates well for electricity, but it breaks easily and is not strong against impacts.
- Storage Conditions: Keep PS materials in a dry and airy place to stop moisture from getting in. Store them at temperatures below 25°C.
- Drying: PS usually stays dry, but any wetness must be removed by drying at 70°C-80°C for 2-4 hours, so moisture levels drop below 0.05%.
Melting and Injection
The melting and injection stage changes PS granules into a molten state and pushes them into a mold.
- Melting: Heat the PS to its melting point, around 240°C. This needs careful control of temperature to avoid damage from too much heat.
- Injection: Push the melted material into a carefully shaped mold. Manage injection pressure to handle PS‘s tendency to break and its low strength against impacts.
Cooling and Solidification
After injection, the material must cool to harden into its final form.
- Cooling System Design: Set up an efficient cooling system with evenly spread channels to keep cooling even. This prevents problems like shrink marks or warping.
- Solidification: Let the product harden without issues by keeping stable temperature conditions inside the mold.
Ejection of the Product
After cooling enough, the product is released from the mold.
- Ejection System: Use a well-made ejector system to remove the product smoothly without harm. Options might include push rod ejectors or push plate ejectors.
- Inspection: After ejection, check the product for any flaws or defects, like bubbles or changes in shape, and adjust in future cycles if needed.
Understanding these steps2 well probably reduces common problems like cracking or defect due to stress. When done properly, these steps create strong, high-quality polystyrene products usable for many things.
PS requires drying before injection molding.False
Polystyrene typically does not need drying, but moisture should be considered.
Melting temperature for PS is around 240°C.True
PS becomes warm at roughly 240°C, turning it into a liquid form.
How Do Temperature and Pressure Affect PS Injection Molding?
Temperature and pressure are crucial for successful polystyrene (PS) injection molding. These factors influence how the material behaves and decide the quality of the final product.
Temperature and pressure significantly influence the injection molding of polystyrene (PS) by affecting its melt flow, cooling rate, and dimensional stability. Proper control ensures optimal product quality by minimizing defects such as warping, shrinkage, and stress cracking.

Understanding Temperature’s Role
In PS injection molding, controlling temperature is key because PS has special qualities. Its glass transition point lies between 80 to 105°C, where it starts to bend. After this, reaching about 240°C is essential so the material flows into molds. But, too much heat causes damage, affecting PS‘s clarity and electrical block3.
Cooling Steps
After injection, PS needs careful cooling. Quick cooling causes cracks and makes it break easier since PS doesn’t resist heat well. A good cooling system with balanced channels helps keep even temperatures, stopping warping.
Pressure Importance
Pressure helps fill molds fully and evenly. High pressure lessens empty spots and improves surface smoothness. But too much pressure might cause problems like thin edges.
Pressure Changes
Changes should consider mold complexity and PS type – common PS, high-impact PS or expanded PS. Different types need various pressure levels as their flow and strength differ.
Temperature and Pressure Together
Temperature and pressure must balance for PS injection molding. High temperature with the right pressure enhances flow, allowing complex shapes while maintaining strength. Wrong balance causes problems like shrink marks or bubbles4. So, operators need to watch these factors often to match current conditions and keep high quality.
Monitoring Systems
Modern machines have advanced systems to watch temperature and pressure instantly. They adjust quickly for outside changes, such as heat shifts or material issues, helping avoid problems and improving work speed.
PS melts at 240°C for optimal flow in molds.True
Polystyrene melts at 240°C, allowing it to flow correctly in the mold.
Excessive pressure reduces voids in PS molding.True
High pressure assists in filling mold cavities fully, lowering empty spaces.
What Challenges Might You Face When Molding PS, and How Can They Be Overcome?
Polystyrene (PS) is a common option for injection molding because of its good traits, but it brings certain difficulties.
When molding polystyrene, challenges such as brittleness, low impact strength, and heat sensitivity are common. These can be addressed by optimizing wall thickness, improving mold cooling systems, and adjusting injection parameters like pressure and speed. Proper material preparation and storage are also crucial in overcoming these obstacles.
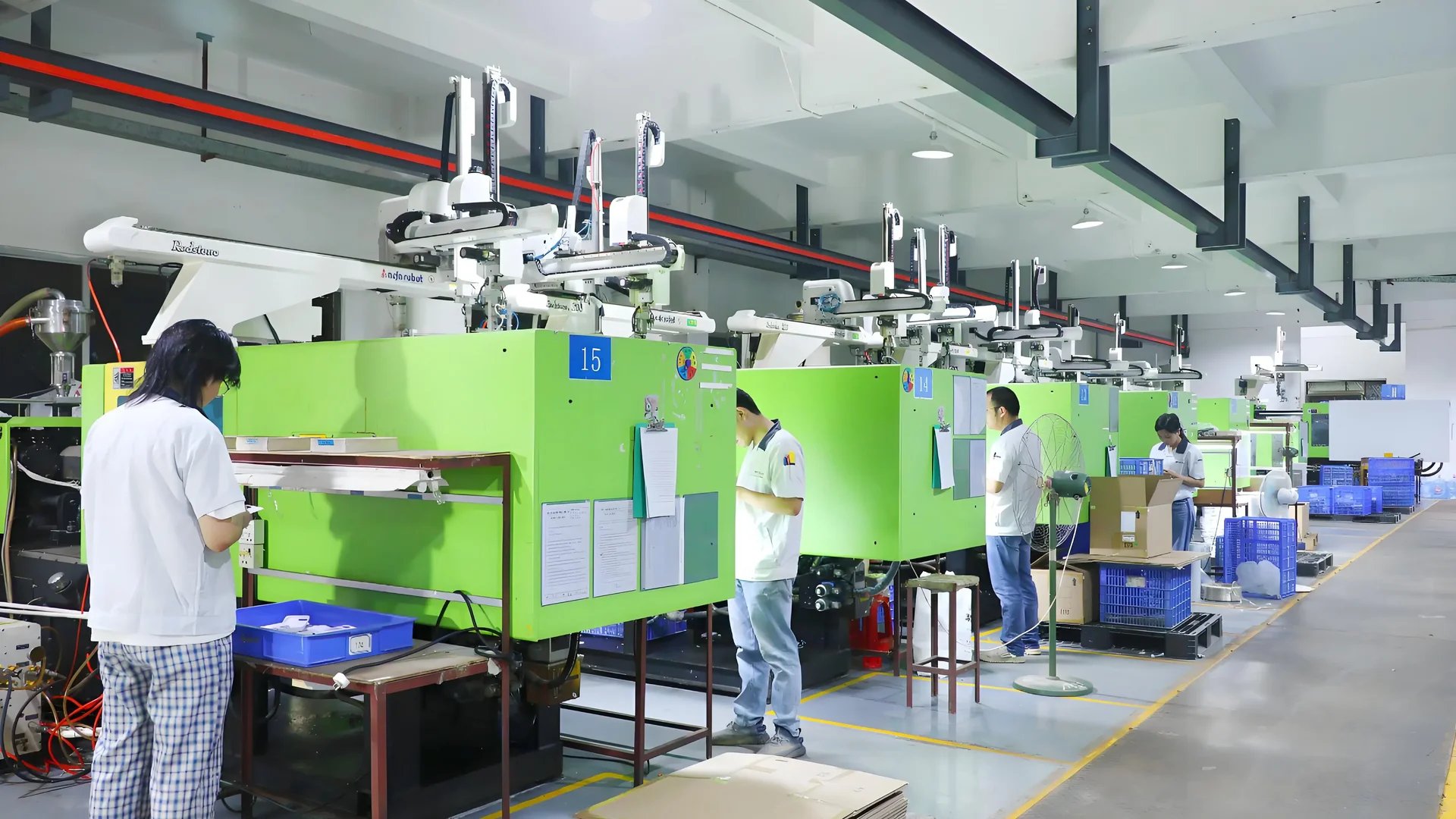
Understanding the Material Properties
Polystyrene (PS) includes types like ordinary polystyrene, expanded polystyrene (EPS), high impact polystyrene (HIPS), and integrated polystyrene (SPS). Each type provides unique advantages, such as high clarity and good electrical insulation. But they also share problems like breaking easily and weak heat resistance.
Table: Key Properties of PS Types
Type | Transparency | Impact Strength | Heat Resistance |
---|---|---|---|
Ordinary PS | High | Low | Poor |
EPS | Moderate | Moderate | Poor |
HIPS | Lower | High | Moderate |
SPS | Variable | Variable | Variable |
Addressing Brittleness and Low Impact Strength
A main problem with PS is breaking easily and low impact strength. This issue can be reduced through:
- Adjusting Wall Thickness: Ensure that the product plan includes correct wall thickness. Thin walls may result in weak strength, while thick walls possibly cause uneven cooling and shrinking.
- Using High Impact Polystyrene (HIPS): For uses needing stronger impact resistance, HIPS serves as a better choice.
Managing Heat Sensitivity
The heat sensitivity of PS presents another challenge. Its glass transition temperature ranges from 80°C to 105°C, with a melting temperature near 240°C. Hence, exact control over injection settings is critical.
- Temperature Control: A well-planned cooling system in the mold stabilizes temperature. Cooling water channels need to be well spread to secure even product cooling.
- Pressure Adjustments: Adjust injection pressure and speed to avoid defects like shrink marks or bubbles. Raising the injection pressure or lengthening holding time delivers better outcomes.
Solving Material Preparation Issues
Proper preparation is vital to avoid defects during injection molding:
- Storage: Store PS materials in a dry, ventilated space away from sunlight to avoid moisture absorption.
- Drying: If the material feels damp, dry it at 70°C-80°C for 2-4 hours until moisture content decreases below 0.05%.
Designing Effective Molds
Mold design plays a key role in overcoming issues:
- Material Selection: Use mold materials like P20 or 718 steel for hardness and wear resistance.
- Glue Feeding Design: Select suitable glue feeding methods based on product complexity; side gates or sprue gates may be needed for harder shapes.
By solving these problems with careful plans and actions, manufacturers can take advantage of PS while reducing its natural limits.
HIPS offers the highest impact strength among PS types.True
HIPS is specially created to raise impact strength compared to other PS varieties.
Polystyrene has a melting temperature of around 150°C.False
Polystyrene softens at around 240°C, not 150°C.
Why Choose PS for Your Injection Molding Projects?
Find the convincing reasons to choose polystyrene (PS) for your upcoming injection molding project. Highlight its special advantages and uses.
Polystyrene (PS) is an ideal choice for injection molding projects due to its affordability, excellent transparency, and ease of processing. It offers versatility across various industries, from packaging to electronics, making it a popular material in manufacturing diverse products.
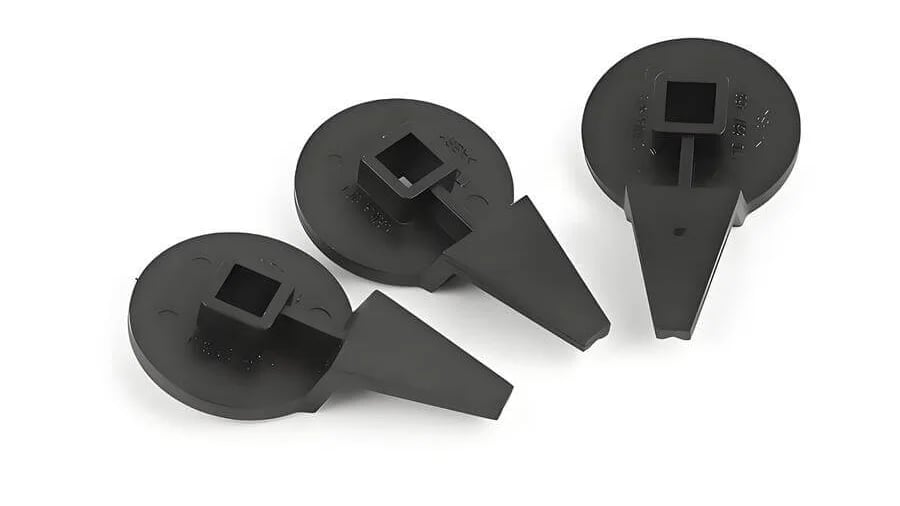
Benefits of Using PS in Injection Molding
Polystyrene (PS) is a much-praised material in the injection molding world because of its special traits. Lightweight, it is simple to carry and lift. The density lies between 1.04 to 1.06 g/cm³, helping in easy handling.
PS is very clear, with light passing through over 90%, fitting for items needing clear sight, like packaging and displays. This feature is different from materials like PVC, which are less clear.
PS has top electrical insulation, making it a favorite for shells and parts in electronics. It resists many chemicals, useful across different fields.
Comparisons with Other Materials
When placed against other plastics, PS gives a unique deal of price and workability. Though not as weatherproof as PVC, PS is clearer and harder. Compared to PP (Polypropylene), PS is stiffer but less able to take hits and heat. Price-wise, PS costs less than ABS (Acrylonitrile Butadiene Styrene), though ABS usually works better overall.
Material | Transparency | Hardness | Impact Resistance | Cost |
---|---|---|---|---|
PS | High | High | Low | Low |
PVC | Medium | Medium | Medium | Medium |
PP | Low | Medium | High | Low |
ABS | Medium | High | High | High |
Key Ideas in Design and Processing
Creating with PS means looking at wall thickness and mold matter. Wall thickness needs fine-tuning to stop problems like uneven cooling or weak spots. Bigger products might need thicker walls for strength, while smaller pieces might reduce thickness to save resources.
For molds, P20 or 718 steel is often chosen due to being strong and long-lasting. A smart cooling design is vital with PS’s high mold temperature, making sure cooling is even and flaws like shrink marks or bending don’t happen.
Areas Where PS is Used
PS finds a place in many industries. In packaging, it shapes boxes, trays and holders. Its insulating nature suits making cases for electronic goods. Also, PS is liked in toys and household items like plastic dishes.
In building, PS helps with heat and sound barriers, showing its wide use.
Knowing how to use PS fully and handling problems like brittleness or poor heat handling helps in getting better results in projects, leading to top-notch work and quality items.
PS offers over 90% light transmittance.True
Polystyrene has excellent transparency, making it perfect for see-through items.
PS is more weather-resistant than PVC.False
PS has weaker weather resistance than PVC.
Conclusion
Learning PS injection molding improves product quality and efficiency. Knowing its material properties and adjusting molding conditions lead to better outcomes. Think about these ideas when you adjust your processes or start new projects.
-
Explore detailed guidance on each step of the injection process.: In this blog post, we will provide a detailed introduction to the characteristics of PS materials, the specific process and molding conditions of PS injection … ↩
-
Learn effective cooling strategies to prevent defects.: The heat input is the molten polymer injected at regular intervals. Sufficient heat must be removed from the mold so parts are cooled to a safe … ↩
-
Learn about PS’s unique properties that benefit various applications.: The advantages of polystyrene plastic injection molding are low shrinkage, moldability, and the flexibility to be used in blended and foam form. ↩
-
Discover how to identify and address common molding defects.: Some of the most common defects in plastic molding include warping, sink marks, flash, voids, and contamination. Factors such as the injection … ↩