Ever wonder what makes plastics such a go-to in manufacturing? Let’s dive into their remarkable properties that allow them to shine in injection molding.
Plastics are suitable for injection molding primarily due to their plasticity, fluidity, thermal stability, and cooling shrinkage. These properties allow plastics to be easily molded into complex shapes, maintain structural integrity at high temperatures, and ensure dimensional accuracy post-cooling.
While these fundamental properties enable the injection molding process, each characteristic contributes uniquely to manufacturing. Join me as we explore these fascinating aspects and their impact on material selection and product quality.
Plastics' thermal stability prevents decomposition during molding.True
Thermal stability ensures plastics maintain integrity under high temperatures, crucial for injection molding.
How Does Plasticity Affect Injection Molding?
Discover how plasticity plays a crucial role in shaping products through injection molding.
Plasticity in injection molding allows materials to flow and form intricate shapes under specific temperature and pressure, crucial for creating diverse products efficiently.
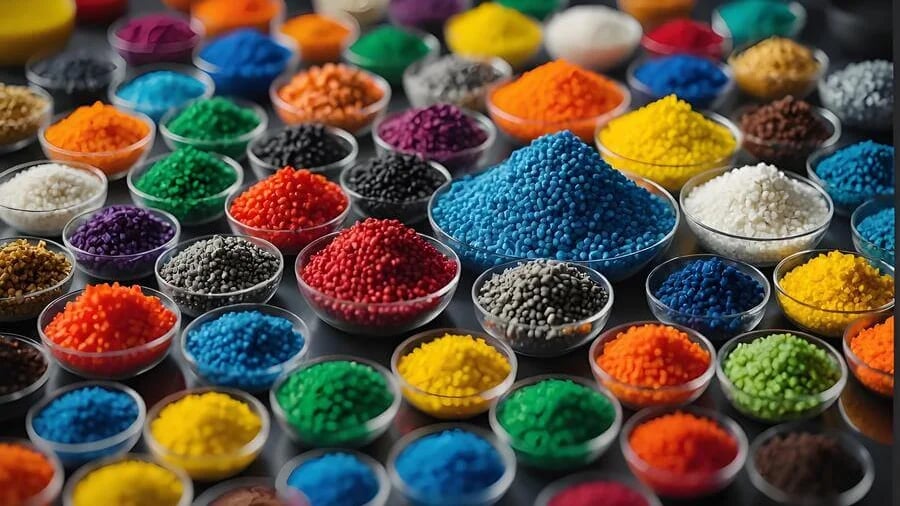
Understanding Plasticity in Plastics
Plasticity refers to a material’s ability to undergo permanent deformation without breaking when subjected to external forces. In the context of injection molding1, plasticity enables plastics to flow into molds, capturing even the most intricate details.
The Role of Temperature and Pressure
During the injection molding process, plastics are heated to a temperature where they transition from solid to a malleable state. This heating is critical, as it allows the material to exhibit plasticity, becoming pliable enough to be shaped. The application of pressure ensures the molten plastic fills all areas of the mold, forming the desired product shape.
- Example: Thermoplastics like polyethylene soften significantly when heated, allowing them to flow into the mold under pressure. Once cooled, they solidify and retain the molded shape.
Benefits of Plasticity in Manufacturing
Plasticity provides several advantages in the manufacturing process:
- Versatility: Allows for the creation of complex shapes and intricate designs.
- Efficiency: Speeds up production by enabling rapid filling and cooling cycles.
- Material Utilization: Minimizes waste by ensuring precise filling of molds.
Plasticity vs. Elasticity
It’s important to distinguish between plasticity and elasticity. While elasticity refers to a material’s ability to return to its original shape after deformation, plasticity involves a permanent change. In injection molding, this permanent deformation is desirable to produce stable and durable products.
Material Selection Based on Plasticity
Selecting the right plastic material is critical. Factors such as molecular structure and weight can affect plasticity. For instance, high-density polyethylene exhibits excellent plasticity, making it ideal for injection molding applications requiring robust performance under varying conditions.
Understanding the nuances of plasticity not only aids in material selection but also helps optimize production processes2 and enhance product quality.
Plasticity allows plastics to flow in molds.True
Plasticity enables materials to fill molds, forming intricate shapes.
Elasticity is more important than plasticity in molding.False
Plasticity, not elasticity, is crucial for permanent shape formation.
What Role Does Fluidity Play in the Injection Molding Process?
Fluidity is crucial in the injection molding process, influencing the ease and precision of shaping plastics.
Fluidity in plastics determines their ability to flow into mold cavities during injection molding. This property ensures even filling, reducing defects and achieving complex shapes with precision. Different plastics exhibit varying fluidity based on molecular weight, structure, and additives.
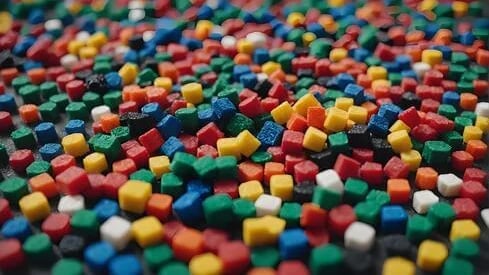
Understanding Fluidity in Plastics
Fluidity refers to the ability of a material to flow and fill a mold, which is essential for achieving the desired shape in injection molding. In the molten state, plastics need to exhibit optimal fluidity to ensure that every intricate detail of the mold is captured, reducing the risk of defects such as voids or incomplete fillings.
Factors Influencing Fluidity
-
Molecular Structure and Weight: Plastics with a more regular molecular structure and lower molecular weight generally show better fluidity. For instance, polystyrene3 is known for its superior fluidity, making it ideal for producing complex and dimensionally accurate items.
-
Additives: The addition of certain substances can enhance or reduce fluidity. Additives are often used to tailor the flow characteristics of plastics for specific applications.
Practical Implications
The selection of plastic materials based on their fluidity is critical in injection molding. A material with high fluidity will not only fill the mold faster but also do so more uniformly, which is crucial for maintaining the quality of the final product.
Plastic Type | Typical Uses | Fluidity Characteristics |
---|---|---|
Polystyrene | Electronics, toys | High fluidity, suitable for complex shapes |
Polypropylene | Packaging, automotive components | Moderate fluidity, good for various applications |
ABS | Consumer goods, automotive parts | Lower fluidity, but offers strength and stability |
Challenges and Considerations
While high fluidity is desirable for complex molds, it can pose challenges in terms of controlling shrinkage and maintaining dimensional accuracy during cooling. Engineers must carefully balance these aspects when designing products and selecting materials.
In conclusion, understanding the role of fluidity allows manufacturers to optimize the injection molding process, ensuring that plastics can be shaped effectively while maintaining high quality standards. For more on how molecular structure impacts plastic properties4, further exploration can provide deeper insights into material science.
Polystyrene exhibits high fluidity in injection molding.True
Polystyrene's regular molecular structure allows it to flow easily into molds.
Higher molecular weight always increases plastic fluidity.False
Higher molecular weight often decreases fluidity, making plastics less flowable.
Why Is Thermal Stability Important in Injection Molding?
Thermal stability is crucial for ensuring the quality and safety of injection molded products.
Thermal stability in injection molding prevents plastics from decomposing, discoloring, or emitting harmful gases under high temperatures, maintaining product integrity and safety.
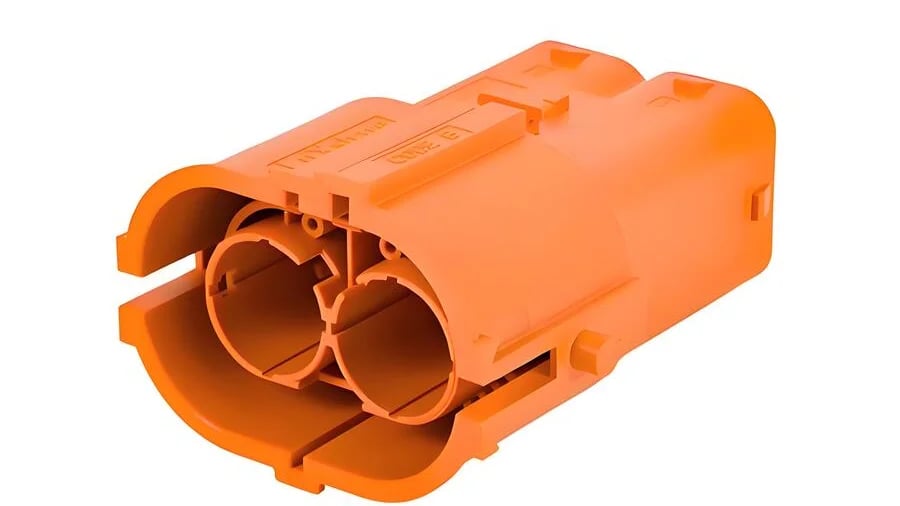
The Role of Thermal Stability in Injection Molding
Thermal stability refers to a material’s ability to maintain its properties and resist degradation at high temperatures. In injection molding, where materials are subjected to intense heat to transform them into a molten state, thermal stability is a critical factor5.
Preventing Decomposition and Discoloration
High thermal stability ensures that plastics do not decompose or discolor during the heating phase of injection molding. For example, polycarbonate is a material known for its excellent thermal stability, allowing it to withstand higher molding temperatures without losing its aesthetic or structural qualities.
Ensuring Safety and Environmental Compliance
Materials that lack thermal stability can emit harmful gases when heated. By selecting plastics with high thermal stability, manufacturers ensure that the molding process does not produce volatile compounds that could harm workers or the environment. This makes thermal stability a key consideration in maintaining workplace safety and meeting environmental regulations.
Impact on Product Quality and Dimensional Stability
Thermal stability directly influences the dimensional stability of the final product. A plastic that maintains its form at elevated temperatures will cool into a precise shape without unexpected shrinkage or warping, ensuring high product quality.
Consider the following table illustrating the thermal stability of different plastics:
Plastic Type | Thermal Stability | Common Uses |
---|---|---|
Polycarbonate | High | Optical discs, automotive parts |
ABS | Moderate | Electronic housings, toys |
PVC | Low | Pipes, vinyl flooring |
Materials with high thermal stability are preferred for applications requiring tight tolerances and complex geometries.
Choosing the Right Material
When selecting a plastic for injection molding, it is essential to consider the required thermal stability based on the intended application. For instance, materials like polycarbonate6 offer superior thermal performance for demanding uses such as electronics and automotive components.
Understanding these aspects allows manufacturers to optimize their processes and enhance the overall quality of their products.
Thermal stability prevents plastic decomposition.True
High thermal stability ensures plastics do not break down at molding temperatures.
Polycarbonate has low thermal stability.False
Polycarbonate is known for its excellent thermal stability, enduring high temperatures.
How Does Cooling Shrinkage Influence Product Design?
Cooling shrinkage is a critical factor in injection molding, affecting both product design and quality.
Cooling shrinkage in plastics affects product design by influencing dimensional accuracy and potential for warping. Designers must consider shrinkage rates, which vary by material, to ensure optimal fit and function. Strategies include choosing materials with predictable shrinkage and designing molds that compensate for expected changes.
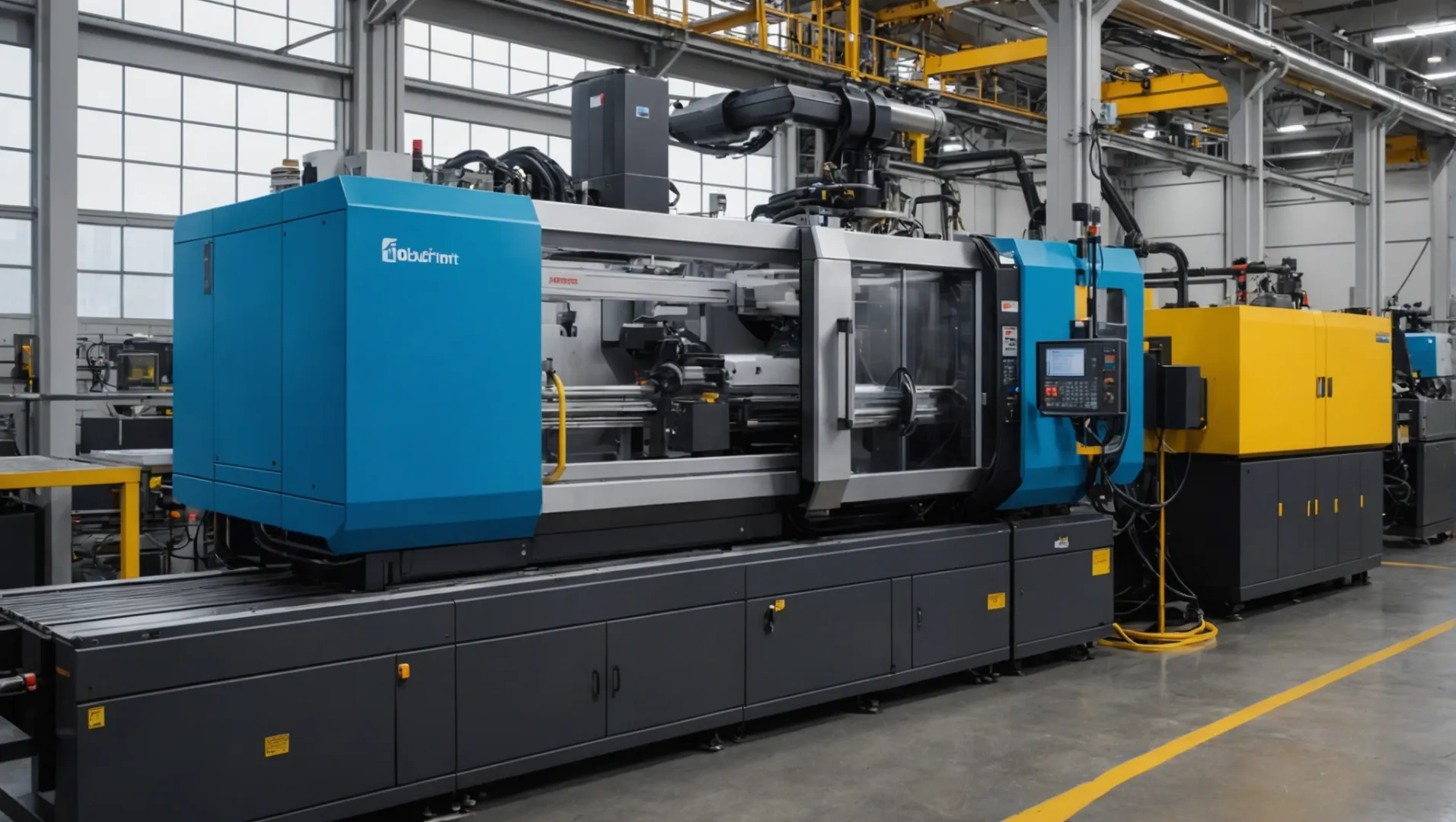
Understanding Cooling Shrinkage
Cooling shrinkage occurs as plastics transition from a molten to a solid state during the cooling phase of injection molding. As the material cools, it contracts, leading to a reduction in volume. This physical change can impact the final dimensions of the product, potentially causing issues like warping or deformation if not properly managed.
For instance, when designing products using thermoplastics7 such as polyethylene, understanding the specific shrinkage rate is crucial. This rate typically ranges between 0.5% and 3%, depending on the polymer’s properties. Plastics like ABS exhibit lower shrinkage, offering better dimensional stability.
Designing for Shrinkage
To counteract the effects of cooling shrinkage, designers must adopt strategies that account for expected changes:
-
Material Selection: Choose plastics with consistent shrinkage rates to predict dimensional outcomes more accurately. Polycarbonate, known for its thermal stability8, offers reliable performance with minimal warping.
-
Mold Design: Modify mold dimensions to accommodate shrinkage. For example, molds for polystyrene should be slightly larger to allow for its higher shrinkage rate, ensuring the final product meets specifications.
Material | Typical Shrinkage Rate (%) |
---|---|
Polyethylene | 1.5 – 3.0 |
ABS | 0.5 – 1.0 |
Polystyrene | 2.0 – 3.0 |
Impact on Product Design
Effective management of cooling shrinkage is crucial in industries where precision is vital, such as automotive and aerospace sectors. Designers often use simulation software to predict how a part will behave post-molding, allowing them to adjust designs proactively.
Moreover, understanding how different plastics respond to cooling can help in developing products that require high dimensional accuracy and surface quality, like medical devices or consumer electronics. By considering these factors early in the design process, companies can enhance product reliability and customer satisfaction.
In conclusion, while cooling shrinkage poses challenges, understanding its impact allows designers to create more accurate and reliable products.
ABS has a shrinkage rate between 0.5% and 1.0%.True
ABS is known for its low shrinkage, providing dimensional stability.
Polycarbonate exhibits high shrinkage and warping.False
Polycarbonate offers thermal stability, reducing shrinkage and warping.
Conclusion
The unique properties of plastics make them indispensable in injection molding, driving innovation across industries. Understanding these characteristics is crucial for optimal material selection and product design.
-
Explores how plasticity impacts molding efficiency and product quality.: Plastic injection molding is an extremely versatile method of producing plastic parts and has multiple advantages over other methods of plastic molding. ↩
-
Learn strategies for enhancing efficiency using plastic materials.: Get an overview of manufacturing processes for producing different types of plastic parts and learn how to select the best option for your application. ↩
-
Explore why polystyrene’s fluidity makes it ideal for detailed molds.: It also has good electrical insulation, is easy to color, has good processing fluidity, and is resistant to chemical corrosion. Polystyrene plastic. Request a … ↩
-
Understand how molecular structure affects plastic’s physical properties.: Plastics are polymers of very high molecular mass. To enhance their properties, they often contain additives, such as fillers and reinforcements. ↩
-
Learn how thermal stability impacts product quality and safety.: Mold temperature is the most significant factor that influences a molded product’s appearance, structure, and functionality. ↩
-
Discover why polycarbonate is ideal for high-temperature applications.: Polycarbonates are strong, stiff, hard, tough, transparent engineering thermoplastics that can maintain rigidity up to 140°C and toughness down to -20°C or … ↩
-
Explore specific shrinkage rates of common thermoplastics for informed material selection.: The shrinkage of molded plastic parts can be as much as 20% by volume when measured at the processing and ambient temperature. ↩
-
Learn how thermal stability influences plastic performance in injection molding.: Thus, thermal and chemical stability are among the most important limiting factors in the tribological application of plastics at high temperatures. ↩