Injection molding is a fascinating process that relies heavily on the remarkable versatility of plastics.
Plastics are ideal for injection molding due to their plasticity, fluidity, thermal stability, and cooling shrinkage properties. These characteristics enable plastics to be easily molded into complex shapes and maintain their integrity throughout the process.
While understanding these properties provides a foundational answer, delving deeper reveals how different plastics perform under varying conditions. Let’s explore these properties in detail and see how they impact the manufacturing process.
Plastics are ideal for injection molding due to plasticity.True
Plasticity allows plastics to be molded into complex shapes under heat and pressure.
How Does Plasticity Influence the Injection Molding Process?
Plasticity plays a pivotal role in transforming plastics into versatile products through injection molding.
Plasticity enables plastics to deform under heat and pressure, allowing them to be molded into various shapes. This characteristic is crucial in the injection molding process, as it permits the plastic material to flow into the mold cavity, forming intricate and precise designs upon cooling.
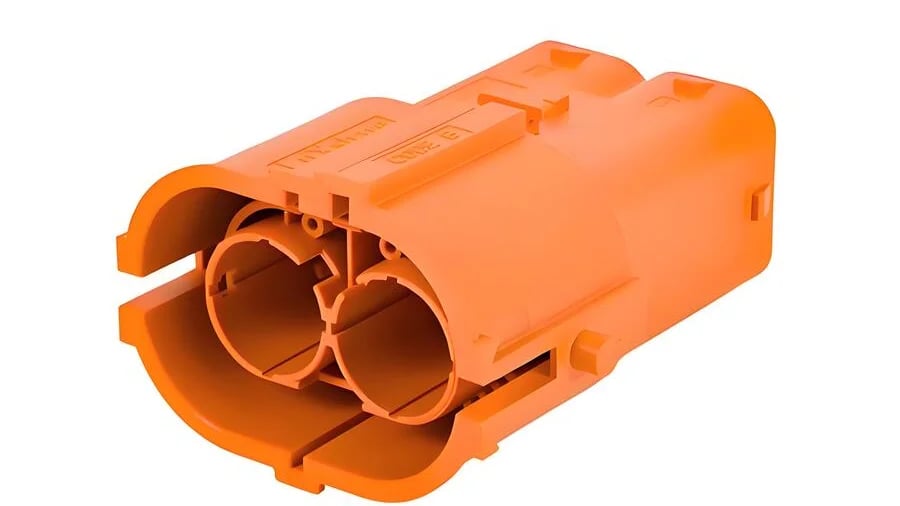
Understanding Plasticity in Injection Molding
Plasticity refers to the ability of materials to undergo permanent deformation when subjected to stress, specifically heat and pressure in the context of injection molding. This property is essential because it allows plastics to be heated, melted, and then molded into new shapes.
The Role of Temperature and Pressure
During the injection molding process1, plastics are heated in the machine’s barrel until they reach a molten state. This is where plasticity truly comes into play. Materials like polyethylene and polypropylene are perfect examples; they can soften under high temperatures and become pliable enough to flow into a mold. Once cooled, they harden, retaining the shape of the mold cavity.
Comparison of Thermoplastics
Thermoplastic | Softening Point | Plasticity Characteristics |
---|---|---|
Polyethylene | Low | Highly plastic, excellent for everyday items |
Polypropylene | Medium | Moderate plasticity, ideal for complex shapes |
The table above shows how different thermoplastics exhibit varying degrees of plasticity, affecting their use in injection molding.
Challenges and Considerations
While plasticity is beneficial, it also presents challenges. For instance, if the material is too plastic, it may lead to deformations or defects in the final product. Engineers must carefully control temperature and pressure settings to ensure optimal plasticity levels are maintained throughout the process.
Plasticity not only influences how easily a material can fill a mold but also affects the precision and quality of the final product. By understanding these dynamics, manufacturers can optimize their processes, leading to better efficiency and product quality.
For more insights on how different types of plastics behave under specific conditions, exploring detailed guides and case studies can be beneficial.
Plasticity allows plastics to fill mold cavities.True
Plasticity enables materials to flow and fill molds under heat and pressure.
Polypropylene has a higher plasticity than polyethylene.False
Polypropylene has moderate plasticity compared to polyethylene's high plasticity.
What Role Does Fluidity Play in Mold Filling?
Fluidity is a crucial factor in the injection molding process, determining how well the molten plastic fills the mold.
Fluidity in mold filling ensures that molten plastic can reach every part of the mold cavity, forming complex shapes accurately. Controlling fluidity through temperature, pressure, and speed adjustments ensures optimal mold filling and product quality.
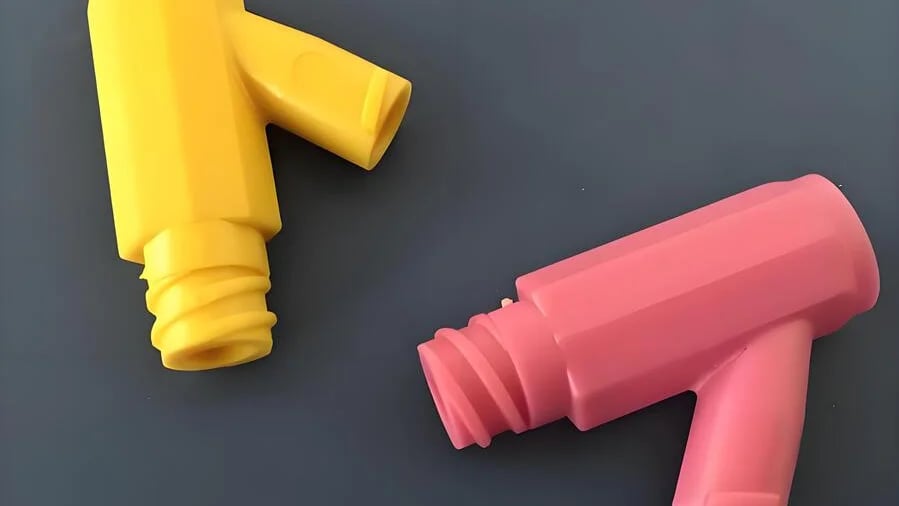
Understanding Fluidity in Plastics
Fluidity is the ability of a molten material to flow into intricate mold shapes, significantly impacting the outcome of injection molding processes2. Different types of plastics exhibit varying levels of fluidity. For instance, polystyrene is known for its excellent flow characteristics, making it suitable for detailed mold designs, while polycarbonate tends to have lower fluidity, requiring specific adjustments during molding.
Factors Influencing Fluidity
-
Temperature:
The temperature of the molten plastic is a primary factor influencing fluidity. Higher temperatures generally improve fluidity by reducing viscosity. However, excessively high temperatures can lead to degradation of the plastic, affecting the final product’s properties.
-
Pressure:
Adequate pressure is essential for pushing the molten plastic into every crevice of the mold. Adjusting pressure helps in managing the flow characteristics of plastics with different viscosities.
-
Injection Speed:
The speed at which the molten plastic is injected plays a critical role. High injection speeds can improve fluidity but may also cause defects like warping or incomplete fills if not carefully managed.
Controlling Fluidity for Optimal Results
Manufacturers often adjust these parameters to optimize fluidity according to the specific plastic being used and the complexity of the mold design. For example, when dealing with engineering plastics3 that possess good thermal stability but varying fluidity, precise control over temperature and pressure can ensure successful mold filling.
Case Study: Fluidity in Complex Mold Designs
Consider a scenario where a manufacturer is using ABS plastic to produce a component with intricate details. ABS has moderate fluidity and requires careful parameter adjustments:
- Temperature: Set slightly higher than average to enhance flow without risking thermal degradation.
- Pressure: Apply sufficient force to aid in reaching all mold areas.
- Speed: Moderate injection speed helps avoid surface defects while ensuring complete cavity fill.
This approach ensures that the mold is completely filled without defects, maintaining high product quality while leveraging the specific fluidity characteristics4 of ABS plastic.
Higher temperature improves fluidity in molding.True
Increased temperature reduces viscosity, enhancing flow of molten plastic.
Polycarbonate has higher fluidity than polystyrene.False
Polystyrene flows better than polycarbonate, suitable for detailed molds.
Why Is Thermal Stability Important in Injection Molding?
Thermal stability is crucial in injection molding, ensuring plastics maintain integrity under high temperatures.
Thermal stability in injection molding prevents plastics from decomposing, discoloring, or altering properties at high temperatures, ensuring product quality and consistency.

Understanding Thermal Stability in Plastics
During injection molding5, plastics undergo a series of temperature changes—being heated, melted, and then cooled. For the material to sustain these processes without degradation, thermal stability is paramount. It determines a plastic’s ability to withstand high temperatures without experiencing decomposition or discoloration.
For instance, engineering plastics like polyamide (nylon) and polyoxymethylene are known for their excellent thermal stability, enabling them to be molded at higher temperatures. This attribute is essential for producing parts that must endure harsh environments, such as automotive components or electronics.
Why Thermal Stability Matters
Thermal stability ensures that the chemical structure of the plastic remains unchanged throughout the molding process. This is vital for maintaining the physical properties and aesthetic appeal of the final product. A lack of thermal stability can lead to defects such as:
- Decomposition: Breakdown of the polymer chain, resulting in weak or unusable products.
- Discoloration: Aesthetic flaws that affect the appearance and marketability.
- Volatile Emissions: Release of gases that could affect health and safety standards.
Case Studies: Practical Implications
Automotive Industry
In automotive manufacturing, components such as under-the-hood parts require materials that can tolerate high temperatures without losing integrity. Using thermally stable plastics ensures reliability and longevity.
Electronics Manufacturing
For electronic devices, especially those that generate heat like power supplies or connectors, plastics need to resist melting or deforming. Materials with high thermal stability prevent short circuits and enhance safety.
How to Enhance Thermal Stability
Manufacturers can improve a plastic’s thermal stability by:
- Blending with Stabilizers: Adding stabilizers that boost resistance to thermal degradation.
- Optimizing Process Parameters: Adjusting temperature and pressure settings to minimize stress on the material.
- Selecting Appropriate Materials: Choosing plastics with inherent thermal resilience based on the application’s requirements.
In conclusion, understanding and optimizing thermal stability is crucial for achieving high-quality injection molded products across various industries.
Thermal stability prevents plastic decomposition in molding.True
Thermal stability ensures plastics don't decompose under high temperatures.
All plastics have excellent thermal stability for injection molding.False
Not all plastics have high thermal stability; some degrade easily.
How Does Cooling Shrinkage Affect Mold Design?
Cooling shrinkage is a crucial factor in mold design, impacting the final dimensions of molded products.
Cooling shrinkage affects mold design by necessitating adjustments to compensate for material contraction. Mold designers must account for different shrinkage rates to ensure precise product dimensions and quality.
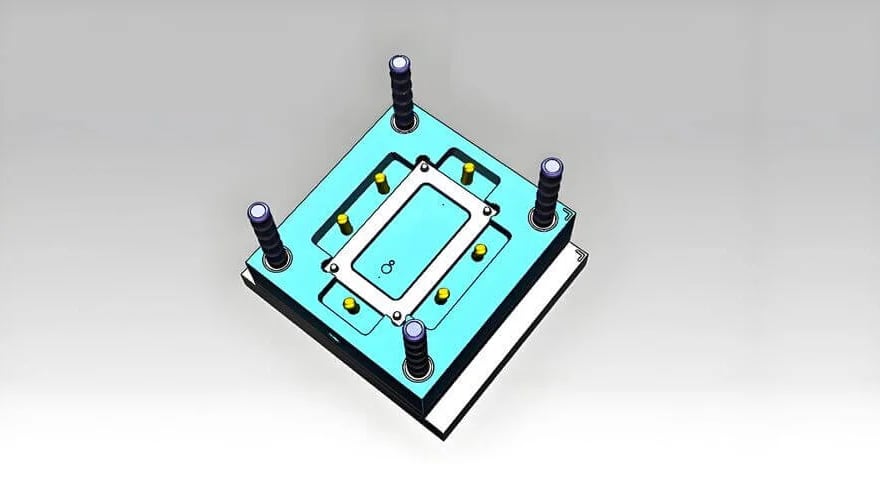
Understanding Cooling Shrinkage
Cooling shrinkage refers to the reduction in volume that occurs when plastics transition from a molten to a solid state during the cooling phase of injection molding. As plastics cool, they contract, and this contraction can significantly influence the final dimensions of the molded part.
The Impact of Different Plastics
Each type of plastic exhibits unique shrinkage characteristics. For instance, ABS plastic generally has a smaller shrinkage rate compared to polyethylene, which can experience more considerable contraction. Therefore, understanding the specific shrinkage rate of different materials6 is vital when designing molds, as it directly affects the dimensional accuracy and quality of the final product.
Mold Design Adjustments
Mold designers must incorporate allowances for shrinkage within their designs to achieve precise product specifications. This often involves:
- Compensating for Shrinkage: By adjusting the mold cavity size to accommodate expected shrinkage, designers ensure that the final product meets dimensional tolerances.
- Material-Specific Design: Using the plastic’s shrinkage rate data to tailor the mold design to specific materials. For example, with higher-shrinkage materials like polyethylene, molds might require larger cavity dimensions.
Plastic Type | Shrinkage Rate |
---|---|
ABS | Low |
Polyethylene | High |
Polypropylene | Moderate |
Process Control in Reducing Shrinkage Impact
Controlling the injection molding process parameters—such as temperature, pressure, and cooling rate—can mitigate the effects of shrinkage. By fine-tuning these variables, manufacturers can enhance the consistency and quality of molded products.
Adjusting these parameters not only compensates for shrinkage but also optimizes fluidity and thermal stability, ensuring that the overall molding process is efficient and yields high-quality results.
Understanding these dynamics enables product designers and engineers to make informed decisions, ultimately leading to better-performing products and more cost-effective manufacturing processes. To delve deeper into mold design strategies, explore how temperature control influences mold performance7.
ABS plastic has a higher shrinkage rate than polyethylene.False
ABS has a lower shrinkage rate compared to polyethylene.
Mold designers adjust cavity size for shrinkage compensation.True
Designers modify mold cavities to ensure dimensional accuracy post-shrinkage.
Conclusion
Grasping the properties of plastics such as plasticity, fluidity, and thermal stability is crucial in optimizing injection molding processes.
-
Gain insights into how plasticity shapes modern manufacturing techniques.: Injection molding is a method to obtain molded products by injecting plastic materials molten by heat into a mold, and then cooling and solidifying them. ↩
-
Learn about the basic principles and steps involved in injection molding.: With injection molding, molten plastic is injected into a mold cavity under high pressure, creating a part all at once. Both processes are … ↩
-
Explore types and properties of engineering plastics used in manufacturing.: Engineering plastics are a group of plastic materials that have better mechanical or thermal properties than the more widely used commodity plastics (such as … ↩
-
Understand how ABS plastic’s fluidity affects its use in complex designs.: It offers significantly enhanced fluidity and good moldability, making it ideal for applications in painting, thin-wall injection molding, and industrial … ↩
-
Learn why thermal stability is critical for high-quality molded products.: Stable mold temperature reduces fluctuations in molding shrinkage, improving dimensional stability. For crystalline plastics, high mold … ↩
-
Learn about specific shrinkage rates to tailor mold designs effectively.: The shrinkage of molded plastic parts can be as much as 20% by volume when measured at the processing and ambient temperature. ↩
-
Discover how temperature adjustments enhance mold performance.: The coolant absorbs heat from the mold (which has absorbed heat from the hot plastic) and keeps the mold at proper temperature to solidify the plastic. ↩