In the world of manufacturing, creating flawless transparent injection molded products is both an art and a science.
The key points of process control for transparent injection molded products involve selecting high-purity raw materials, optimizing mold design, precisely controlling injection molding parameters, and implementing effective post-processing techniques.
While these foundational strategies provide a clear pathway to success, delving deeper into each element can unveil nuanced techniques that significantly impact the final product quality. Understanding the intricate balance of these factors will elevate your manufacturing prowess.
High-purity raw materials ensure product transparency.True
Impurities scatter light, reducing clarity in transparent products.
How Does Raw Material Purity Affect Transparency?
In the realm of transparent injection molding, the purity of raw materials is pivotal in determining product clarity and quality.
High-purity raw materials minimize impurities that can scatter light, ensuring the transparency and integrity of injection molded products. Selecting optical-grade materials like polycarbonate with minimal impurity content is essential for achieving superior transparency.
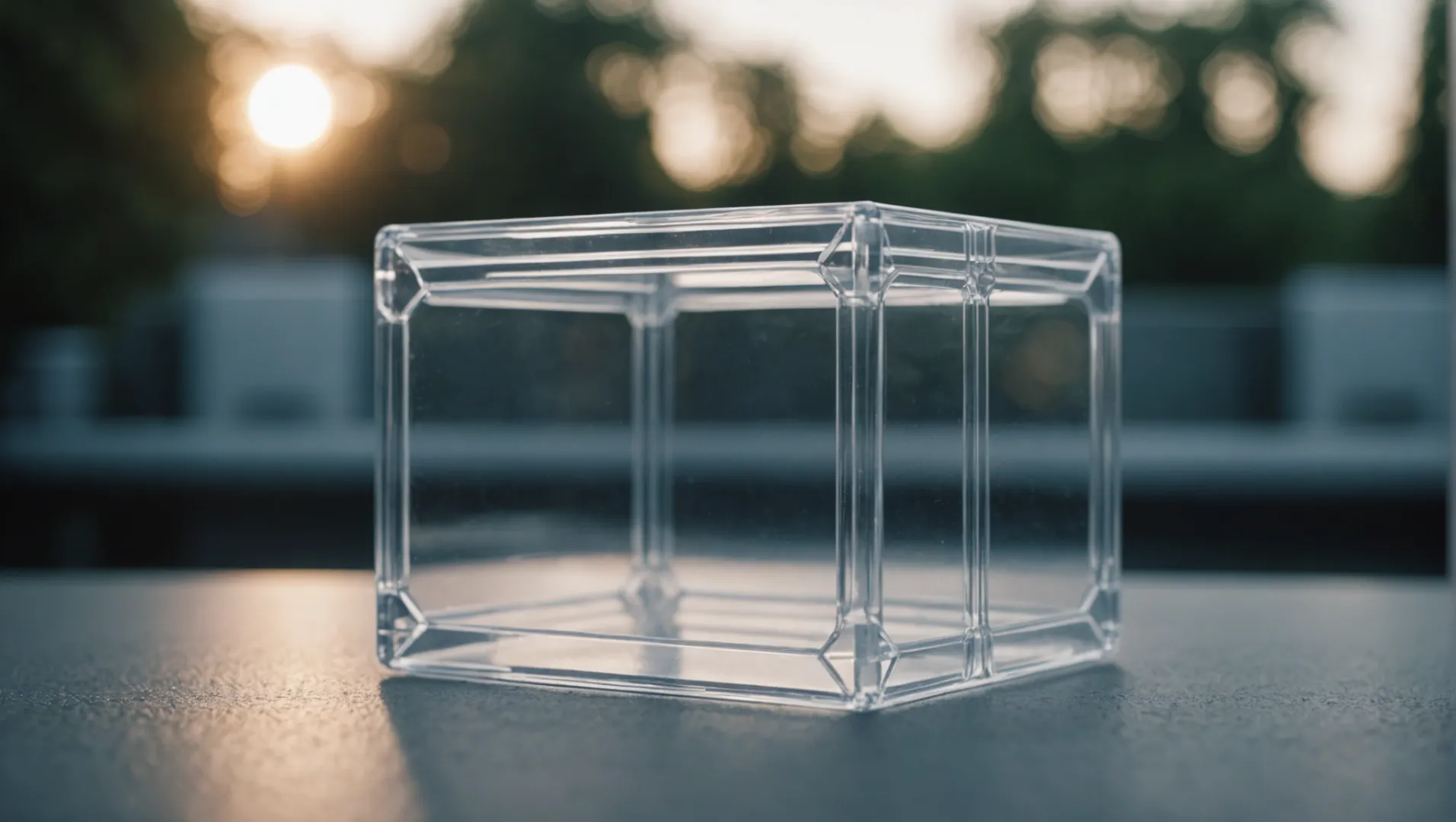
The Critical Role of Purity in Material Selection
When it comes to producing transparent injection molded products, the selection of high-purity raw materials cannot be overstated. Impurities within raw materials are notorious for scattering light and creating undesirable effects such as cloudiness or visible defects. For instance, optical-grade polycarbonate (PC), known for its transparency and durability, should contain impurity levels lower than one part per million.
Impact of Impurities on Light Transmission
Impurities within raw materials can cause disruptions in light transmission. These disruptions often manifest as distortions or visual imperfections, thereby affecting the overall transparency of the finished product.
Consider the example of polycarbonate: even minute impurities can lead to defects like haze, which is detrimental in applications demanding clear visibility, such as lenses or protective shields.
Case Study: Polycarbonate in Optical Applications
In industries where transparency is critical, such as optics or electronics, selecting raw materials with impeccable purity is non-negotiable. For example, optical lenses made from polycarbonate must maintain clarity and precision. Any deviation due to impurities could compromise functionality and performance.
Material | Impurity Level | Application | Impact of Impurities |
---|---|---|---|
Polycarbonate (PC) | <1 ppm | Lenses, Shields | Haze, Reduced Clarity |
Achieving Optimal Transparency Through Controlled Processes
Beyond selecting high-purity materials, maintaining transparency during the injection molding process involves precise control over processing parameters. Ensuring a seamless flow and adequate filling without introducing additional impurities is crucial.
- Fluidity Control: By adjusting temperature and pressure, manufacturers can influence the fluidity of the material, thereby reducing the likelihood of defects.
- Exhaust Systems: Properly designed molds with efficient exhaust systems prevent air entrapment, which can lead to bubbles or streaks impacting transparency.
Concluding Thoughts on Material Purity
Understanding and implementing stringent controls over raw material purity not only impacts the visual quality but also enhances the structural integrity of transparent products. By committing to high standards in material selection and process control, manufacturers can achieve exceptional clarity and performance in their products. To explore more about achieving optimal material purity standards, consider consulting industry-specific guidelines or expert recommendations here1.
High-purity materials reduce light scattering in products.True
Impurities scatter light, affecting transparency. High-purity minimizes this.
Impurities in polycarbonate improve transparency.False
Impurities cause haze, reducing clarity in transparent applications.
What Role Does Mold Design Play in Quality Control?
Mold design is crucial in ensuring the quality and precision of transparent injection molded products.
Mold design significantly influences quality control by dictating the product’s surface finish, transparency, and structural integrity. Key elements such as gate design and exhaust systems are essential to minimize defects like bubbles and silver streaks.
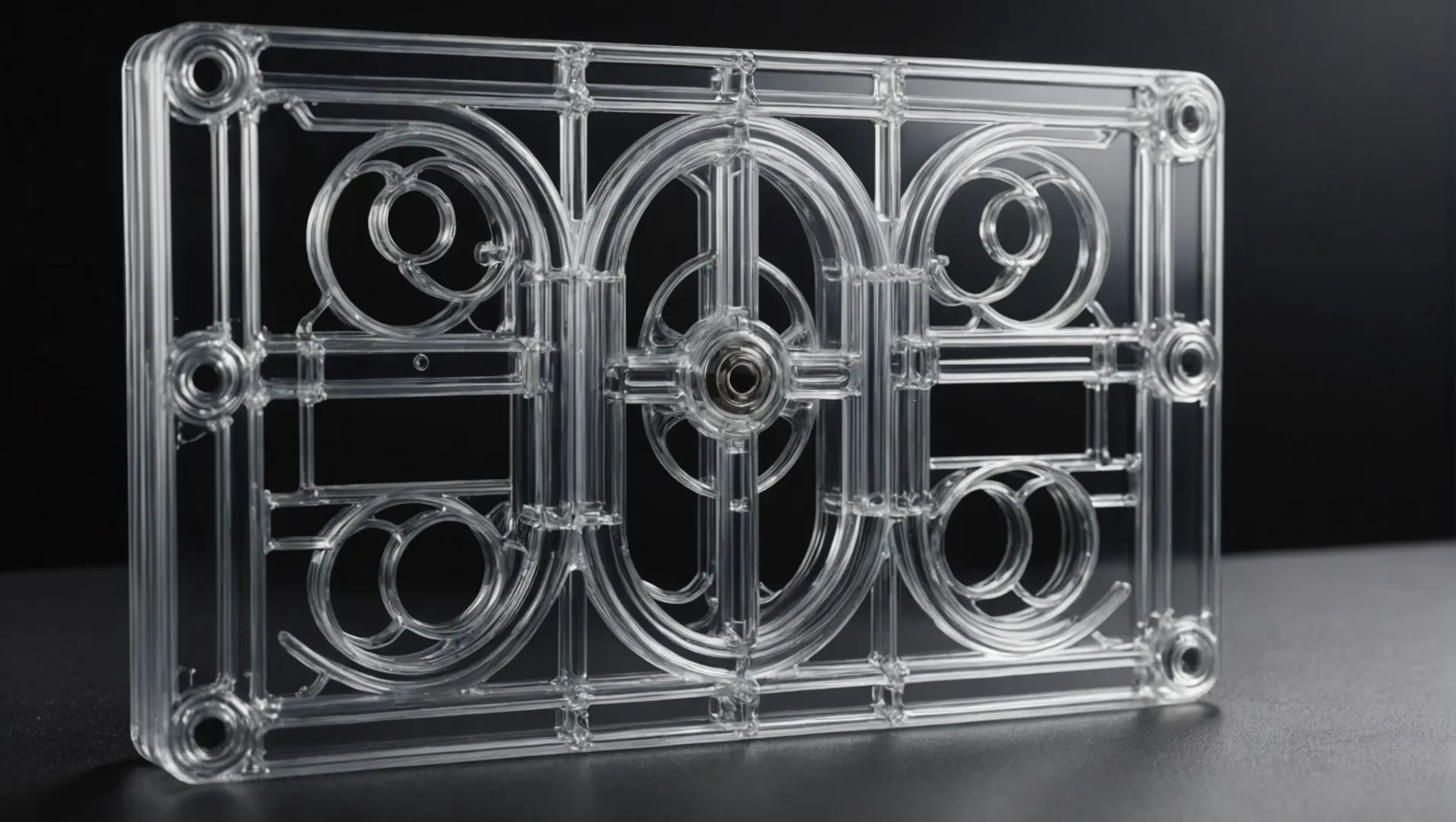
The Importance of Gate Design
In mold design, the location and size of the gate are pivotal in determining the final product’s appearance and quality. For transparent injection molded products, it’s essential to select a gate position that minimizes visual imperfections. For instance, utilizing a latent or point gate can substantially reduce the impact of gate marks on the product’s surface, thus enhancing transparency.
These designs ensure that the material flows smoothly and uniformly into the mold cavity, which is particularly important for maintaining clarity in transparent products. A well-placed gate also aids in distributing the pressure evenly, reducing the risk of warping or stress concentrations.
The Role of Exhaust Systems
Efficient exhaust systems within a mold are critical for maintaining product quality. Without proper ventilation, air trapped inside the mold can lead to defects like bubbles or silver streaks, which severely compromise transparency. Designing molds with effective exhaust grooves on parting surfaces or sliders ensures that air can escape swiftly and without hindrance.
An effective exhaust system not only preserves the aesthetic qualities of the product but also enhances its structural integrity by preventing voids and weak points. Understanding proper exhaust system design2 can drastically reduce production errors and improve overall product quality.
Integrating Mold Design with Process Parameters
Mold design does not operate in isolation; it must be integrated with other process control parameters to achieve optimal results. Factors such as injection temperature, pressure, and speed must align with the mold’s specifications to ensure consistent quality control.
For example, a mold designed for high-speed injection should accommodate rapid material flow without causing turbulence or unwanted stress. Similarly, pressure settings need to match the gate design to prevent issues like shrinkage or distortion. Exploring these integrations3 provides deeper insights into achieving superior quality control through holistic design approaches.
Gate design affects the transparency of molded products.True
Proper gate design reduces visual imperfections, enhancing transparency.
Exhaust systems are irrelevant to product quality.False
Efficient exhaust systems prevent defects like bubbles and silver streaks.
Why Are Injection Molding Parameters Crucial for Success?
In the realm of transparent injection molding, precision is paramount to success.
Injection molding parameters are crucial for success because they dictate the material’s flow, cooling rate, and final product quality, significantly impacting transparency and mechanical properties.
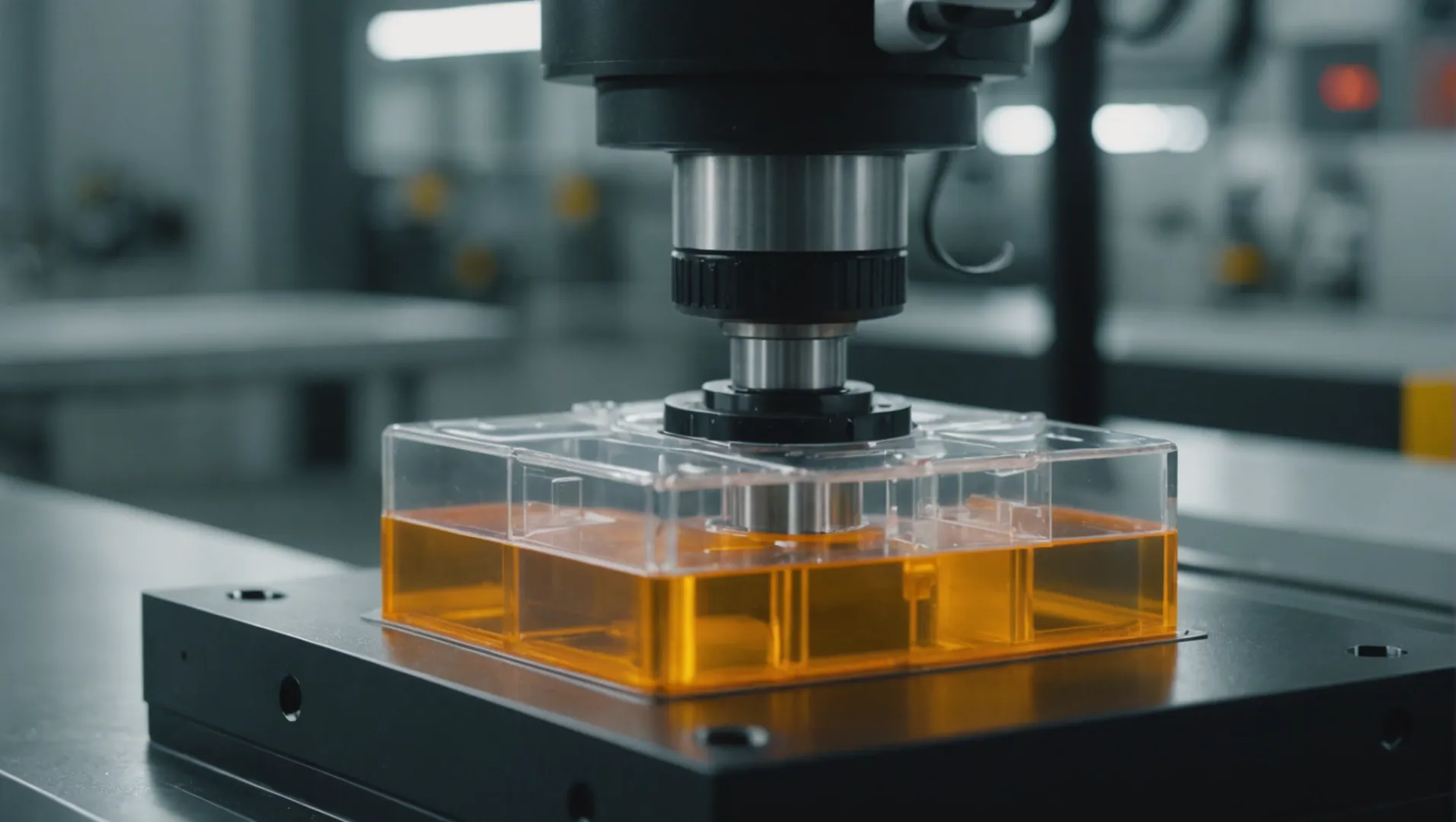
Understanding Injection Molding Parameters
The parameters of injection molding, including temperature, pressure, and speed, are pivotal in determining the outcome of the process. Each parameter must be meticulously controlled to ensure optimal results.
Temperature Control
- Injection Molding Temperature: The temperature must be precisely managed to ensure raw materials are sufficiently melted for proper mold filling. While transparent products often require higher temperatures, excessive heat can lead to decomposition, compromising transparency and quality.
Pressure Regulation
-
Injection Pressure: This refers to the force applied to the molten material during molding. High pressure is necessary to prevent defects like shrinkage and bubbles but must be balanced to avoid internal stress that can affect product clarity.
-
Holding Pressure and Time: After initial molding, holding pressure ensures dimensional stability. This must be adjusted according to material properties to prevent internal stress while maintaining transparency.
Speed and Timing Adjustments
-
Injection Speed: A slower speed is generally preferred for transparent products to minimize flow marks and silver streaks. However, too slow can also result in defects such as shrinkage, necessitating a balanced approach.
-
Cooling Rate: Fast cooling might lead to warping or uneven surfaces, while slow cooling helps in stress relaxation, improving transparency.
The Interplay of Parameters
The success of transparent injection molded products lies in the delicate balance of these parameters. Changes in one parameter often necessitate adjustments in others. For instance, increasing the injection speed might require a temperature increase to maintain material fluidity.
Example Parameter Table
Parameter | Transparent Product Requirement |
---|---|
Temperature | Higher than standard; avoid too high |
Pressure | Higher with careful stress control |
Speed | Slower to avoid defects |
Cooling | Balanced to prevent warping |
By understanding and controlling these parameters, manufacturers can produce high-quality transparent products with the desired clarity and strength. For detailed guidelines on setting optimal injection molding conditions4, refer to expert resources.
Conclusion
While perfecting these parameters requires careful experimentation and adjustment, mastering them ensures a seamless production process and superior product quality. This balance is a critical component of successful transparent injection molding.
Higher temperatures improve transparency in molding.True
Higher temperatures melt materials better, enhancing transparency.
Fast cooling always improves product clarity.False
Fast cooling can warp products, reducing clarity.
How Can Post-Processing Improve Product Quality?
Unlocking the full potential of transparent injection molded products hinges on effective post-processing techniques.
Post-processing techniques such as annealing and polishing are crucial in enhancing the mechanical properties, transparency, and overall quality of transparent injection molded products.
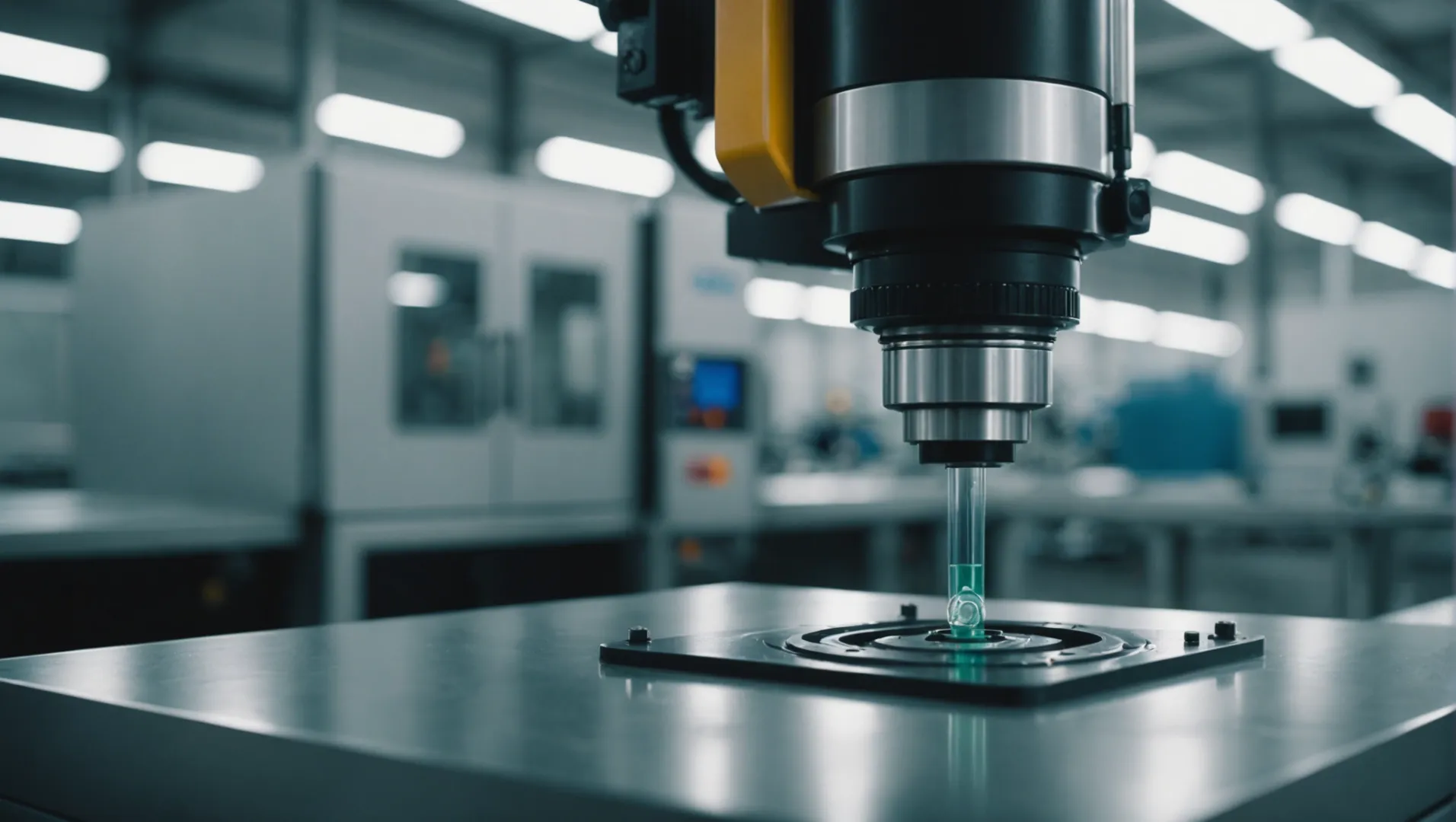
The Significance of Annealing in Product Quality
Annealing is a vital post-processing method that involves heating a product to a specific temperature to relieve internal stresses. This process not only enhances the transparency of the product but also improves its mechanical properties. For instance, when annealing polycarbonate (PC) products, the temperature should exceed the product’s use temperature but be carefully monitored to avoid deformation. The time spent at this temperature varies based on the product’s thickness and size, ensuring that the stress is adequately relieved.
The benefits of annealing extend beyond stress relief. By optimizing the annealing process, manufacturers can reduce the likelihood of defects like cracks and warping, resulting in a more robust final product.
Polishing: A Path to Transparency and Smoothness
Polishing is another essential post-processing technique that significantly impacts the surface quality of transparent injection molded products. It can be achieved through mechanical polishing5 or chemical polishing.
-
Mechanical Polishing: This method involves using abrasive materials like sandpaper or grinding wheels to smoothen the product surface. It’s crucial for removing minor imperfections that could impact the product’s visual appeal and performance.
-
Chemical Polishing: This approach uses chemical solutions to erode and polish the surface, offering a finer finish. It’s particularly useful for achieving a high level of transparency and smoothness, which is often required in optical-grade products.
Both methods are instrumental in eliminating surface defects that may have been introduced during molding, thereby enhancing the product’s overall appearance and functionality.
Enhancing Product Durability Through Post-Processing
Post-processing not only improves aesthetic aspects but also plays a crucial role in boosting the durability of injection molded products. For example, during polishing, minor scratches that could become fracture points under stress are removed, thereby extending the product’s lifespan.
Moreover, these techniques help in maintaining dimensional stability by ensuring that the product retains its shape and size over time. Such stability is critical in applications where precision and reliability are non-negotiable.
Conclusion: Integrating Post-Processing into Manufacturing Protocols
Incorporating annealing and polishing into the manufacturing process allows for the production of high-quality transparent injection molded products that meet stringent industry standards. By understanding and applying these techniques, manufacturers can achieve not only superior transparency and aesthetics but also enhanced durability and performance.
Annealing improves transparency in molded products.True
Annealing relieves internal stresses, enhancing transparency.
Chemical polishing uses abrasive materials for smoothing.False
Chemical polishing uses solutions, not abrasives, for smoothing.
Conclusion
By mastering these key points, manufacturers can achieve superior transparency and product integrity, setting a benchmark for quality.
-
Explore guidelines for achieving high material purity in manufacturing.: Learn how to select the right material for your injection molding design with this technical overview of thermoplastic resins. ↩
-
Understand how effective exhaust systems prevent common molding defects.: 5. The presence of a large amount of gas in the cavity can reduce the filling speed, affecting the molding cycle and reducing production … ↩
-
Learn how aligning design with parameters improves product quality.: The 8 Key Parameters in Injection Molding Process Optimization to Avoid Defects · 1. Temperature Control: · 2. Injection Speed: · 3. Cooling Time:. ↩
-
Explore detailed guidelines on setting precise molding conditions.: Popular materials for clear plastic injection molding include: Acrylic, HDPE, Polycarbonate, and PEI · SPI-A2 is the best surface finish for … ↩
-
Discover effective methods for enhancing surface smoothness and transparency.: The polishing can be done in a number of ways, such as through chemical, mechanical fluid, electrolytic, or even abrasive polishing. ↩