Have you ever marveled at the sleek finish of a well-made product? That perfect surface isn’t just luck; it’s the result of careful planning and execution in injection molding.
To prevent surface scratches on injection molded parts, optimize mold design and maintenance, adjust injection molding parameters, and ensure a clean production environment. These strategies help enhance product durability and aesthetic quality.
While the initial answer provides a solid foundation, delving deeper into each strategy reveals valuable insights that can further refine your manufacturing process. Continue reading to explore comprehensive solutions tailored for reducing surface scratches effectively.
Mold design impacts surface quality of injection molded parts.True
Mold design affects demoulding angles and mold finish, reducing scratches.
How Does Mold Design Influence Surface Quality?
Mold design plays a pivotal role in determining the surface quality of injection molded parts. By focusing on optimal design parameters and maintenance practices, manufacturers can minimize surface defects, including scratches.
Mold design influences surface quality through factors like demoulding angles, mold finish, and ejection systems. Optimizing these elements reduces friction and uneven forces, preventing scratches and improving product aesthetics.
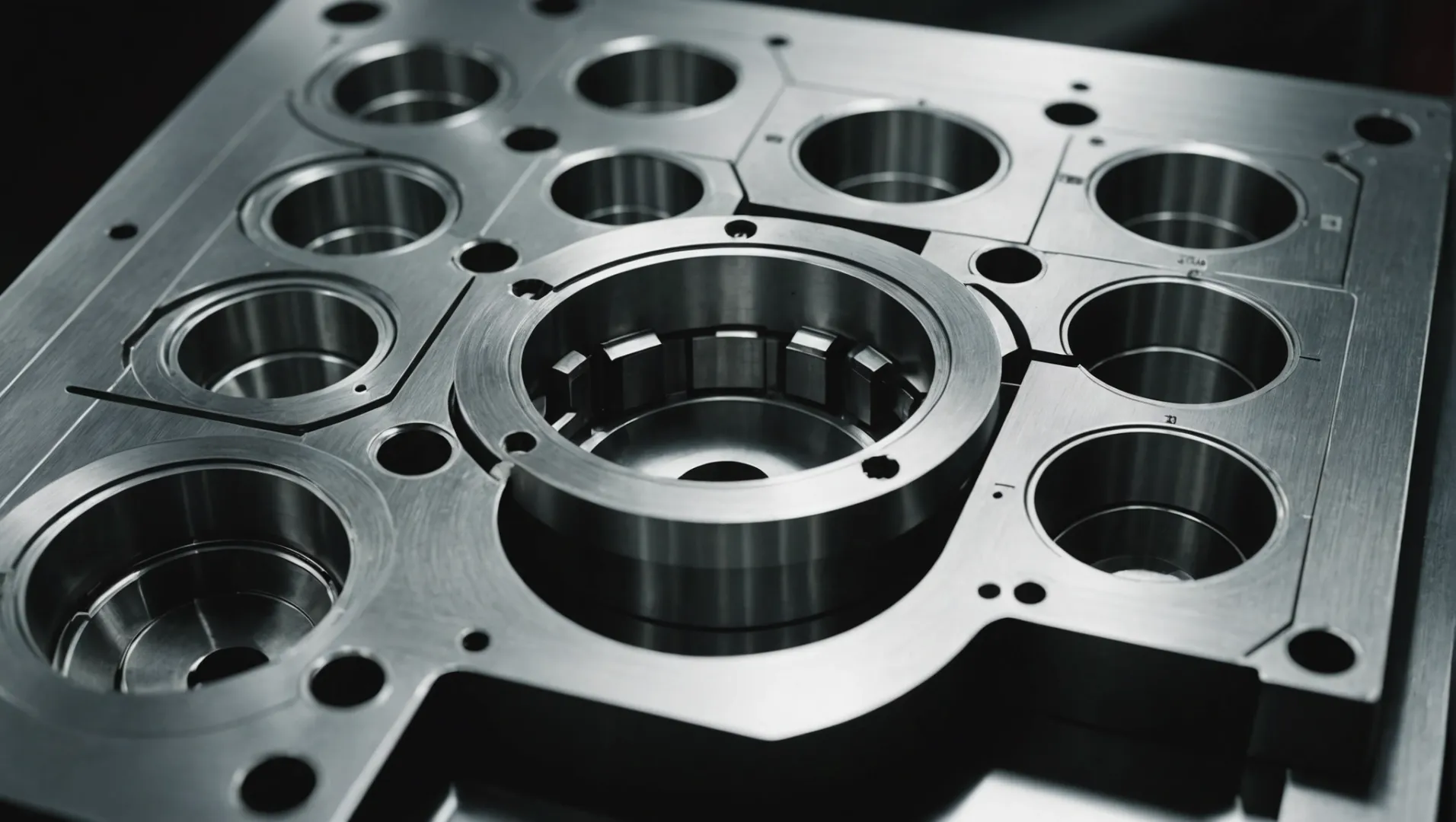
The Importance of Demoulding Angle
One of the most critical aspects of mold design1 is the demoulding angle. A well-designed angle ensures the smooth ejection of parts from the mold, minimizing friction and potential scratches. For instance, a demoulding angle typically ranges between 1° and 3° depending on part shape and size. Insufficient angles can cause excessive contact, while too steep angles may lead to warping or distortion.
Enhancing Mold Surface Finish
The surface finish of the mold directly impacts the friction between the part and the mold. Techniques such as polishing or chrome plating can significantly improve mold smoothness, which in turn reduces scratch risks. A smoother mold surface enables easier ejection, enhancing both the functional and aesthetic quality of the part.
Regular Maintenance and Repairs
Routine maintenance checks are vital to address wear and tear on mold surfaces. Any scratches or irregularities should be promptly repaired to maintain optimal working conditions. Regular inspections help ensure that the mold remains in peak condition, thereby safeguarding against unexpected defects.
Designing an Effective Ejection System
An evenly distributed ejection force is crucial to preventing surface scratches during part removal. Multi-point ejection systems or nitrogen springs can be employed to ensure balance. This approach avoids localized pressure that can lead to imperfections on the part surface.
Optimizing Mold Structure for Better Ventilation
Proper ventilation through exhaust grooves helps manage trapped gases during molding. These grooves must be carefully designed to prevent gas marks or scratches. By ensuring effective gas escape, manufacturers can maintain the integrity of the part’s surface finish.
Incorporating these strategies within mold design not only enhances surface quality but also contributes to the overall durability and appeal of injection molded parts.
Demoulding angles reduce mold friction.True
Correct demoulding angles minimize friction, preventing scratches.
Chrome plating increases mold surface roughness.False
Chrome plating smoothens the mold, reducing surface roughness.
What Role Does Material Selection Play in Scratch Prevention?
Material selection is crucial in minimizing scratches on injection molded parts, enhancing both durability and aesthetics. Choosing the right material can significantly impact the product’s resistance to scratches.
Selecting appropriate materials for injection molding reduces surface scratches by leveraging properties like wear resistance and fluidity. By considering the use conditions and environmental factors, manufacturers can enhance product quality.
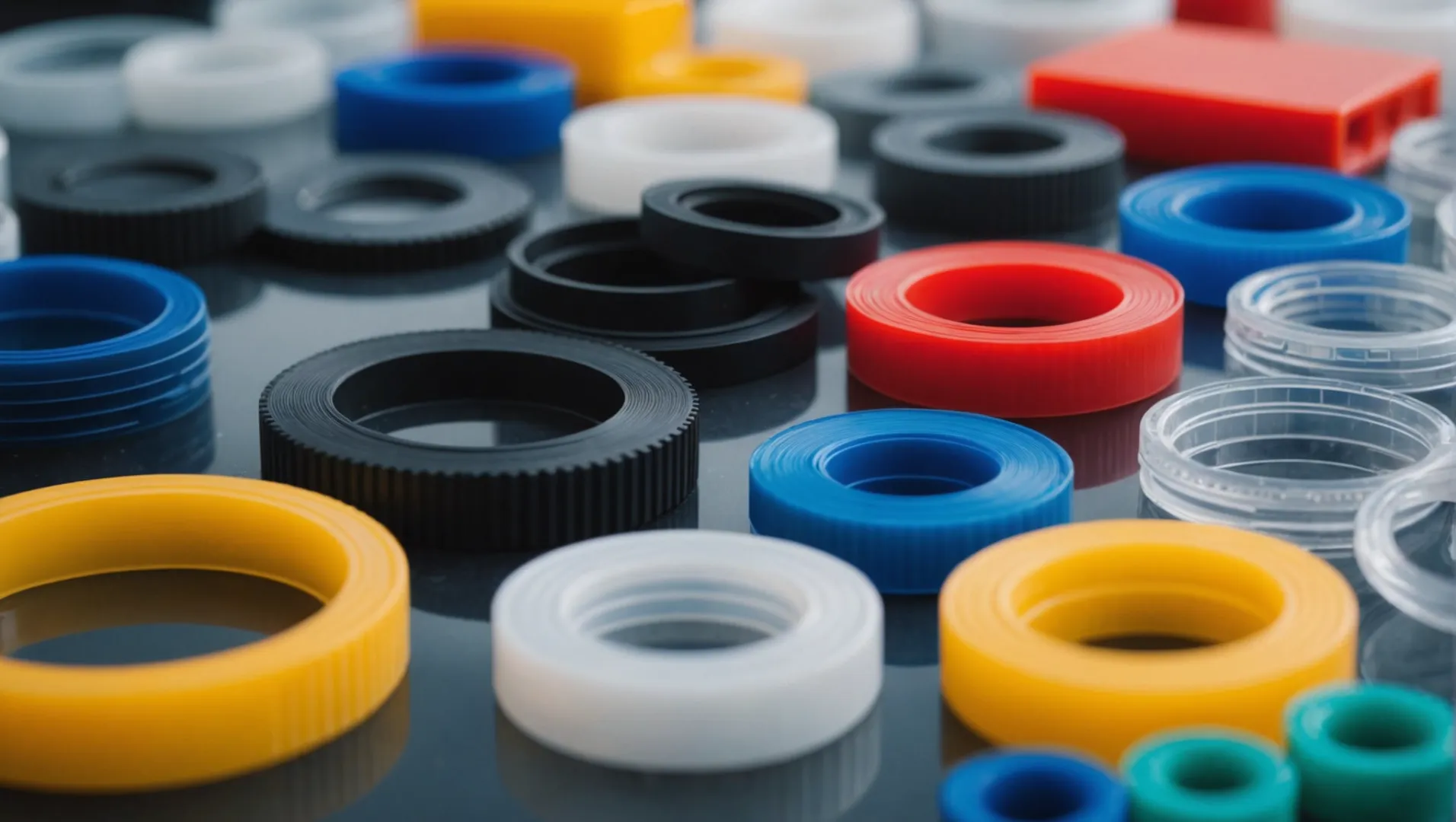
Understanding Material Properties
The selection of materials in injection molding2 plays a pivotal role in scratch prevention. Different materials exhibit varying degrees of hardness, elasticity, and chemical resistance, which directly influence their susceptibility to surface damage. For instance, polycarbonate (PC) and poly(methyl methacrylate) (PMMA) are often chosen for applications requiring high clarity and scratch resistance due to their excellent optical properties and durability.
Importance of Material Compatibility
When selecting materials, it is vital to consider compatibility with the intended application. Materials that are not well-suited to the operating environment can lead to increased wear and scratching. For example, nylon3 is often used in mechanical components due to its strength and low friction properties, which help in reducing surface scratches caused by mechanical interactions.
Material Type | Key Property | Application Example |
---|---|---|
Polycarbonate | High clarity | Optical lenses |
Nylon | Low friction | Mechanical gears |
PMMA | Scratch resistance | Display screens |
Considering Environmental Factors
Environmental factors such as temperature, humidity, and exposure to chemicals can affect the material’s performance in preventing scratches. For instance, thermoplastic elastomers (TPEs) are often selected for outdoor applications due to their ability to withstand varying temperatures without compromising surface integrity.
Choosing the right material involves balancing these factors to ensure that the final product maintains its aesthetic and functional qualities throughout its lifecycle. This requires a comprehensive understanding of both the material properties and the operational demands of the application.
Processing Techniques and Material Performance
The interaction between material selection and processing techniques also affects scratch prevention. For instance, properly drying materials like polyethylene terephthalate4 (PET) before processing can prevent hydrolysis, reducing the risk of surface defects. Additionally, selecting materials with suitable flow characteristics can ensure a smoother finish by reducing internal stresses during molding.
By carefully considering these aspects of material selection, manufacturers can significantly minimize surface scratches and improve overall product quality. This not only enhances the aesthetic appeal but also prolongs the product’s lifespan.
Polycarbonate is chosen for scratch-resistant lenses.True
Polycarbonate's high clarity and durability make it ideal for optical lenses.
Nylon increases surface scratches in mechanical parts.False
Nylon's low friction reduces surface scratches in mechanical applications.
Why Is a Clean Production Environment Essential?
A clean production environment is crucial for ensuring the quality and longevity of injection molded parts. Dust and contaminants can easily mar the surface, leading to scratches that compromise both aesthetics and function.
Maintaining a clean production environment minimizes contaminants that can cause surface scratches on injection molded parts, preserving their integrity and appearance.
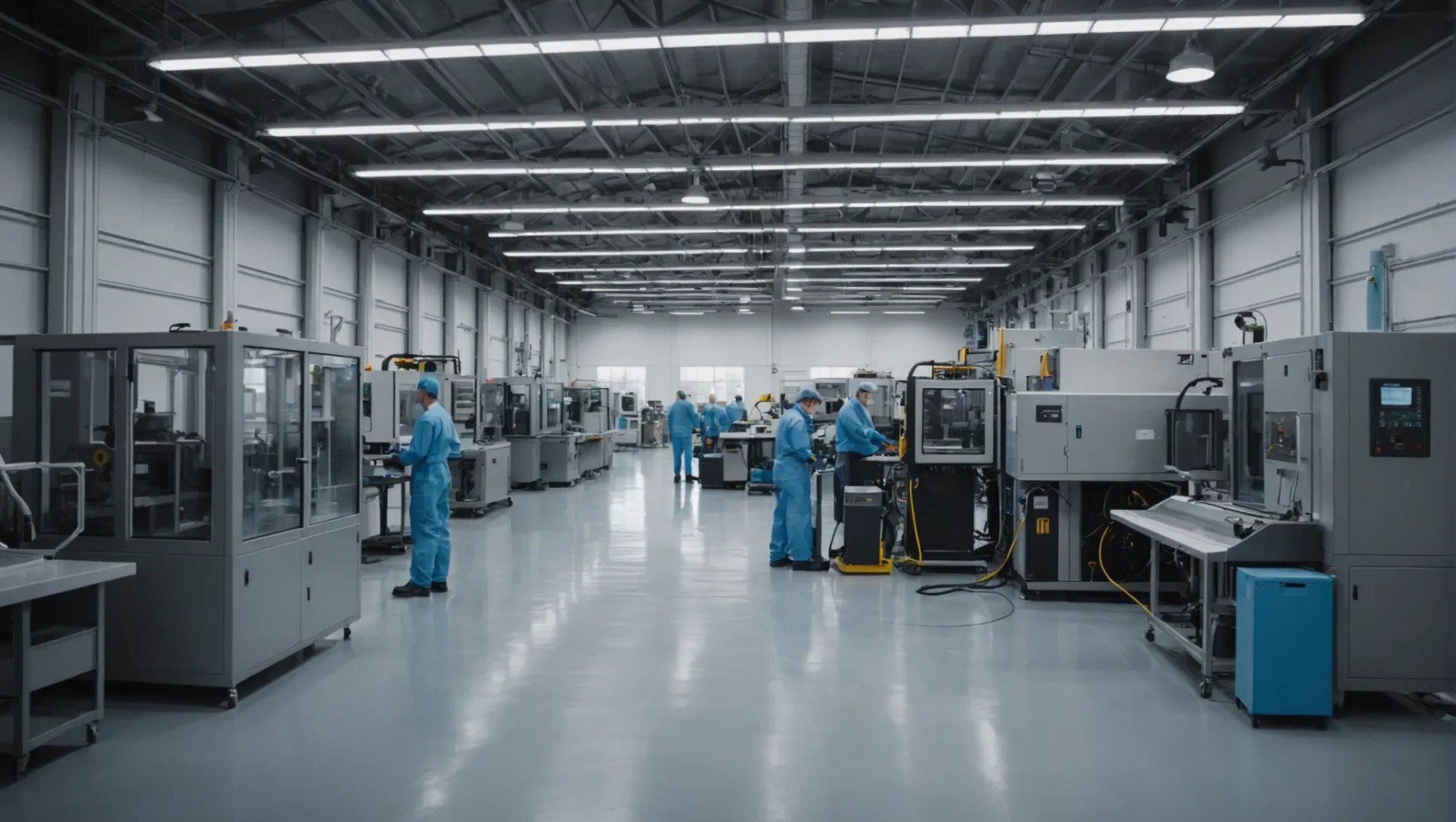
The Role of Cleanliness in Production
A clean production environment is not just about aesthetics; it directly impacts the quality of injection molded parts. Dust and other airborne particles can settle on the mold or the part itself during the molding process, creating blemishes or scratches. By maintaining cleanliness, manufacturers can significantly reduce these risks.
Implementing Effective Cleaning Protocols
Keeping the production area free from dust and debris involves several steps. Regular cleaning schedules should be established, ensuring that all equipment and surfaces are wiped down frequently. Utilizing air filters can also help remove particulates from the environment, reducing contamination risks. Effective cleaning protocols5 are critical in this respect.
Choosing Appropriate Packaging Materials
Once the parts are molded, choosing the right packaging materials becomes vital. Soft and non-abrasive materials should be used to prevent any scratches during handling and transportation. This practice not only protects the product but also maintains its quality until it reaches the customer. Soft packaging materials6 can be beneficial in this regard.
Packaging Material | Properties | Benefit |
---|---|---|
Foam | Cushions and absorbs impact | Reduces friction |
Bubble wrap | Provides a protective barrier | Prevents scratches |
Plastic film | Smooth surface, non-abrasive | Avoids direct contact |
Training Personnel for Optimal Handling
Operators play a crucial role in maintaining a clean environment. Training them to understand the importance of cleanliness and how to properly handle injection molded parts can make a significant difference. Knowledgeable staff are less likely to introduce contaminants during production.
In summary, maintaining a clean production environment involves regular cleaning schedules, appropriate packaging materials, and well-trained personnel. These measures collectively ensure that injection molded parts remain free from surface scratches, thus preserving their quality and longevity.
Clean environments prevent scratches on molded parts.True
Dust and contaminants cause scratches, affecting quality.
Air filters are unnecessary in production areas.False
Air filters remove particulates, reducing contamination risks.
How Can Operator Training Reduce Surface Defects?
Operator training is a critical factor in minimizing surface defects during injection molding, enhancing both efficiency and quality.
Effective operator training reduces surface defects by improving handling skills, promoting adherence to operational guidelines, and boosting quality awareness. This leads to fewer errors and enhanced product quality.
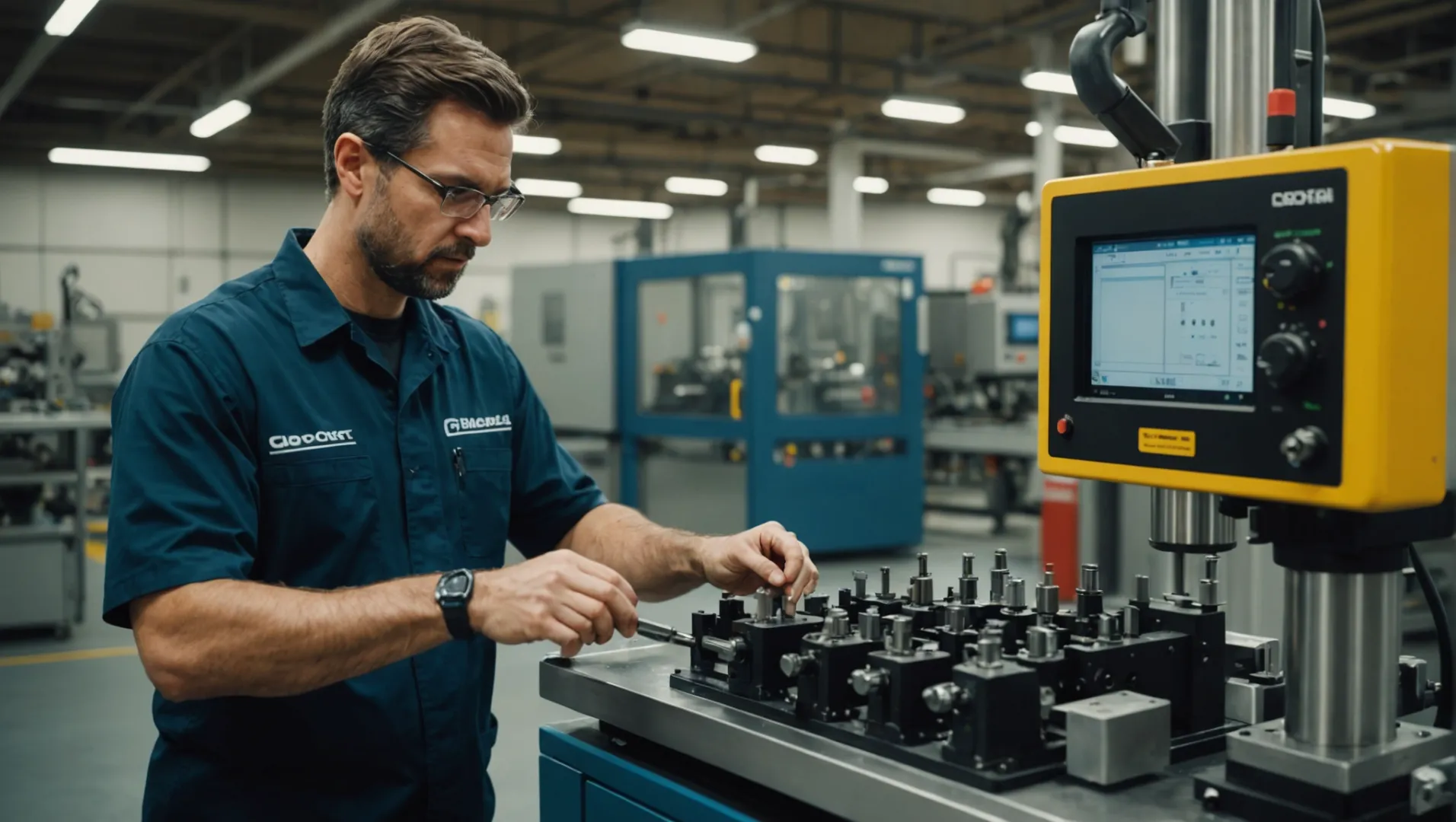
The Importance of Comprehensive Training Programs
Comprehensive training programs equip operators with the necessary skills to handle machinery and materials with precision. This includes understanding the nuances of injection molding7 processes, recognizing the importance of maintaining consistent operational standards, and effectively communicating with team members.
Operators must be trained to follow strict operating procedures, ensuring consistency and reducing the likelihood of errors. Through hands-on practice and theoretical learning, operators can develop a keen eye for detail, allowing them to identify potential issues before they become significant problems.
Hands-On Skill Development
Incorporating hands-on skill development into training programs is crucial. Practical exercises help operators become familiar with the machines they will use daily. This familiarity leads to smoother operation and less downtime due to mishandling.
For example, an operator trained in the proper calibration of molding machines can ensure that settings are optimal for the materials used, reducing surface defects like scratches or blemishes. They learn to adjust settings such as temperature and pressure appropriately, which can be critical in maintaining product quality.
Emphasizing Quality Awareness
Quality awareness is another vital component of operator training. Educating operators on the impact of their work on overall product quality fosters a sense of responsibility and care in their daily tasks. This awareness can lead to more careful handling of materials and finished products, reducing the risk of surface defects.
Continuous Learning and Feedback
A culture of continuous learning and feedback is essential for sustained improvement. Regular workshops and refresher courses can keep operators updated on the latest techniques and technologies in injection molding. Feedback sessions allow operators to share their experiences, leading to collective learning and process optimization.
By investing in robust operator training programs, companies can significantly reduce the incidence of surface defects in injection molded parts. This investment not only enhances product quality but also boosts operational efficiency, leading to long-term benefits for the business.
Operator training reduces injection molding defects.True
Training improves skills and adherence to guidelines, reducing errors.
Hands-on training is unnecessary for reducing defects.False
Practical exercises are crucial for familiarity and error reduction.
Conclusion
By implementing these strategies, you can minimize surface scratches on injection molded parts, ensuring high-quality outputs. Consider integrating these practices into your production process to enhance product durability and customer satisfaction.
-
Learn why correct demoulding angles are essential for reducing friction.: By applying a degree of draft, the part is allowed to move a short distance before the mold shrink is able to clear the micro undercuts, and ultimately the … ↩
-
Explore how material properties affect scratch resistance.: Learn how to select the right material for your injection molding design with this technical overview of thermoplastic resins. ↩
-
Discover why nylon is favored for low friction applications.: Nylon is a commonly used injection molding material because of its advantageous physical properties, mechanical properties, and moldability. ↩
-
Learn how drying PET affects its scratch resistance.: Water molecules bond strongly to the PET polymer chain. · Hot drying air loosens the bonds between moisture and the resin, allowing the molecules … ↩
-
Discover comprehensive cleaning strategies to maintain optimal production conditions.: Clean the surface using a product containing soap, detergent, or other type of cleaner appropriate for use on these surfaces. · Launder items if … ↩
-
Learn about materials that minimize damage during shipping and storage.: Plastic materials for injection molding range from commonly used polymers to specialty plastics and polymer blends. ↩
-
Learn why training is crucial for reducing defects in molded parts.: Operators work with injection molding machines in both the automatic and semi-automatic modes. In the automatic mode, the molded parts drop out of the mold as … ↩