Residual stress can feel like a lurking menace in the injection molding world, impacting everything from product strength to appearance. Let’s tackle this issue head-on!
Preventing residual stress in injection molding involves optimizing process parameters, designing efficient molds, and implementing post-processing techniques. These strategies help reduce warping, brittleness, and instability, ensuring high-quality plastic products.
Though tackling residual stress may seem daunting, grasping its root causes and effective prevention strategies can dramatically elevate product quality. Join me as we explore actionable steps and expert insights to refine your injection molding practices.
Faster cooling reduces residual stress in injection molding.False
Faster cooling often increases residual stress due to uneven shrinkage.
What Role Does Material Selection Play in Reducing Residual Stress?
Material selection is pivotal in minimizing residual stress in injection molding, affecting both production efficiency and product quality.
Choosing the right material for injection molding can significantly reduce residual stress. Factors such as thermal expansion, flow properties, and molecular weight influence stress levels. Opting for materials with balanced thermal and mechanical properties helps in achieving uniform cooling and minimizing stress-induced defects.
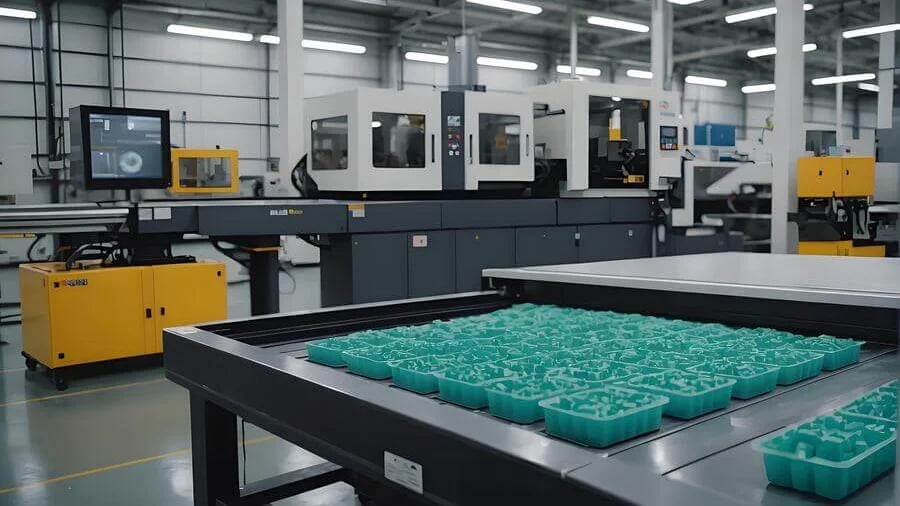
Understanding Material Properties
When it comes to reducing residual stress1 in injection molding, material properties play a critical role. Different plastics have varying thermal expansion coefficients, which dictate how they shrink during cooling. Materials with lower thermal expansion tend to cool more evenly, reducing stress. Additionally, the molecular weight and distribution can influence the degree of molecular orientation, impacting internal stress.
For example, materials like polycarbonate or polyamide often exhibit lower residual stress due to their intrinsic properties. These materials allow for consistent flow and cooling, reducing uneven shrinkage that typically leads to internal stress.
Thermal Conductivity and Flow Characteristics
The thermal conductivity of a material affects how heat is dissipated during molding. Materials with higher thermal conductivity enable more uniform cooling, crucial for reducing residual stress. Flow characteristics2 also matter; materials that flow easily can fill molds more evenly, avoiding pressure points and shear forces that contribute to stress.
Choosing a material with a suitable melt flow index (MFI) can lead to better mold filling and reduced risk of short shots or unbalanced flows. This approach minimizes the potential for stress concentration areas.
Balancing Mechanical and Optical Properties
In some cases, balancing mechanical strength with optical clarity is necessary. Transparent plastics used in lenses or covers require careful material selection to ensure that optical properties are not compromised by residual stress. Utilizing additives or blends can sometimes help achieve this balance, providing strength without sacrificing clarity.
Environmental Considerations
Material selection should also consider environmental factors like temperature fluctuations during use. Selecting materials that maintain dimensional stability across a wide temperature range can prevent residual stress from developing over time.
In summary, thoughtful material selection tailored to the specific application can significantly mitigate residual stress in injection molding processes. By understanding and leveraging the intrinsic properties of materials, manufacturers can enhance product quality and performance. This strategic approach3 not only addresses immediate production challenges but also anticipates long-term performance needs.
Materials with lower thermal expansion reduce stress.True
Lower thermal expansion leads to more even cooling, reducing stress.
High MFI materials increase the risk of residual stress.False
High MFI materials fill molds evenly, reducing stress concentrations.
How Does Cooling Rate Affect Residual Stress in Injection Molding?
The cooling rate in injection molding plays a pivotal role in determining the residual stress within plastic products, influencing their overall quality.
Cooling rate directly impacts residual stress in injection molding by affecting thermal shrinkage and molecular orientation. Faster cooling may lead to higher residual stresses due to uneven shrinkage and increased molecular orientation, while slower cooling allows for more uniform stress distribution.
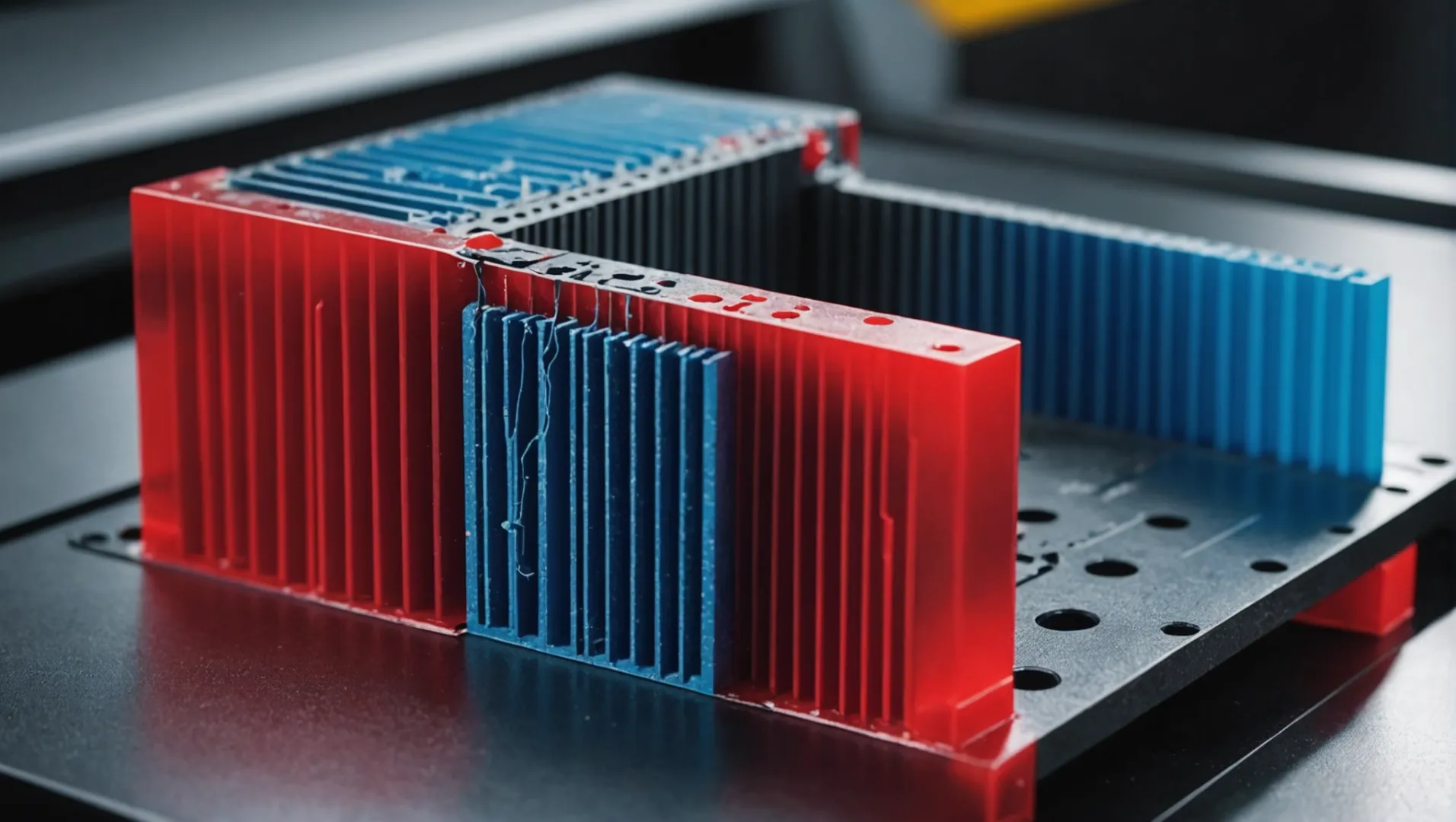
The Basics of Cooling Rate and Its Impact
In the injection molding process4, molten plastic is injected into a mold where it cools and solidifies. The rate at which this cooling occurs is crucial, as it can lead to uneven shrinkage if not controlled properly. This unevenness results in residual stress, which can degrade the mechanical and dimensional properties of the final product.
Faster cooling rates can cause the outer layers of the plastic to solidify more quickly than the inner layers, leading to differential shrinkage. This can create tensile stress on the outer layers while compressing the inner layers, resulting in a product that is prone to warping or cracking over time.
Influence of Thermal Conductivity and Mold Design
The thermal conductivity of the plastic material used is another factor that affects how quickly a product cools. Materials with higher thermal conductivity will cool more evenly, reducing the risk of residual stress. However, the mold design is equally important. A well-designed mold ensures uniform cooling by maintaining consistent temperature across all parts, thereby minimizing differential shrinkage.
Example Table: Cooling Rate Effects
Cooling Rate | Shrinkage Effect | Residual Stress Level |
---|---|---|
Slow | Even Shrinkage | Low |
Moderate | Balanced | Medium |
Fast | Uneven Shrinkage | High |
Strategies to Control Cooling Rate
Mold Temperature Control: Implementing a precise mold temperature control system can help manage the cooling rate effectively. Techniques such as using heating rods or hot oil circulation ensure that the mold maintains a consistent temperature throughout the process.
Cycle Time Adjustment: Adjusting the cycle time to allow for slower cooling can also be beneficial. This approach reduces residual stress by giving the material more time to solidify uniformly.
Material Selection: Opting for materials with appropriate thermal properties can also aid in achieving a desired cooling rate. Selecting materials that naturally exhibit lower shrinkage rates can prevent residual stresses from developing.
Understanding and controlling the cooling rate is essential for reducing residual stress in injection molding. By optimizing both material choice and mold design, manufacturers can improve product quality and performance significantly.
Faster cooling increases residual stress in molded plastics.True
Faster cooling causes uneven shrinkage, raising residual stress.
High thermal conductivity materials cool unevenly.False
Materials with high thermal conductivity cool more evenly.
Can Advanced Simulation Tools Help Predict and Mitigate Residual Stress?
Advanced simulation tools are transforming the way we address residual stress in manufacturing. But how effective are they really?
Advanced simulation tools offer predictive insights into residual stress formation, allowing manufacturers to optimize processes and materials. By simulating thermal and mechanical behaviors, these tools help mitigate stress, enhancing product quality.
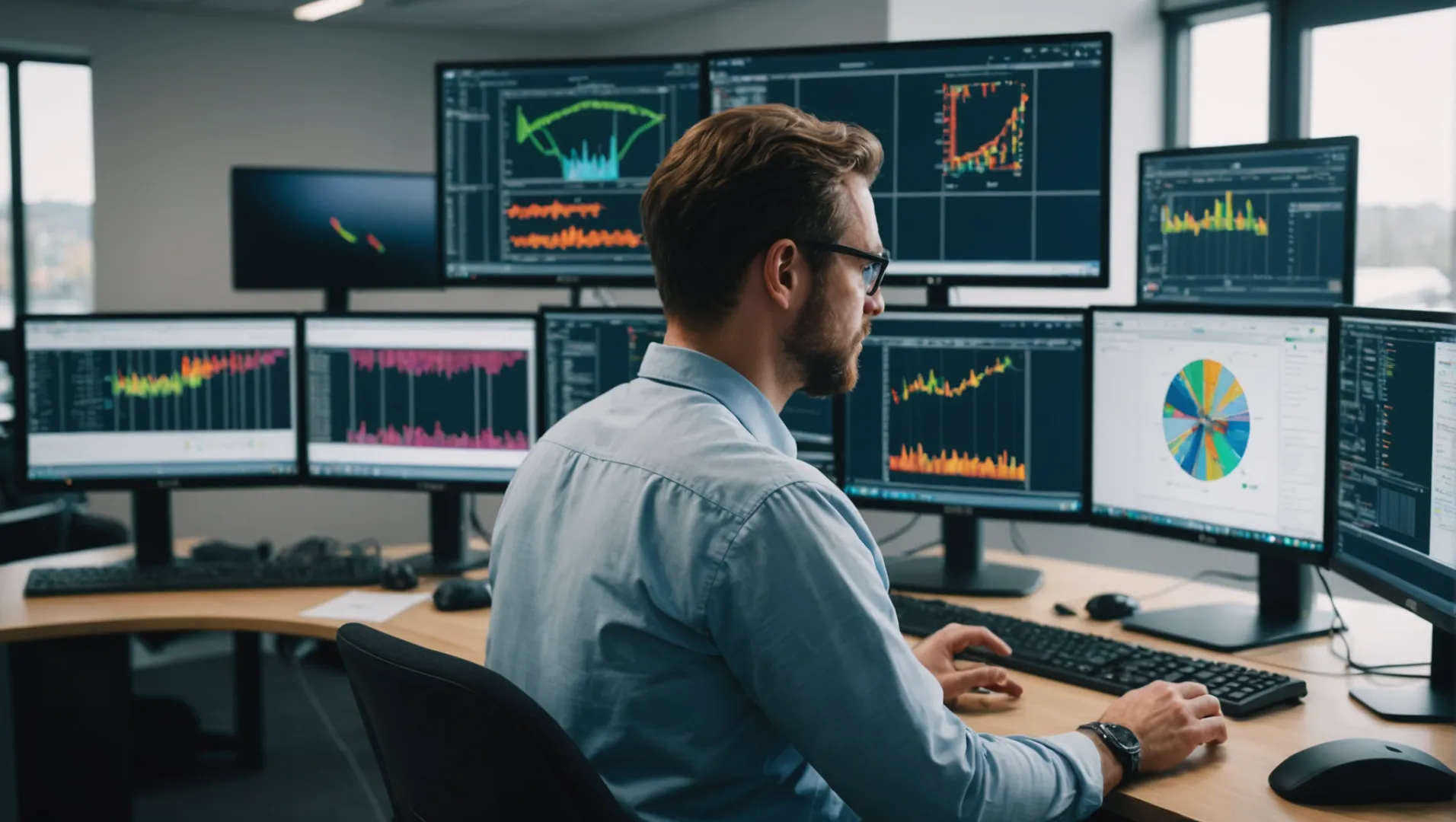
Understanding the Function of Advanced Simulation Tools
Advanced simulation tools, like finite element analysis (FEA) and computational fluid dynamics (CFD), play a pivotal role in understanding and predicting residual stress. These tools simulate the thermal and mechanical behaviors of materials during the injection molding process5, providing valuable insights into how different parameters affect stress formation.
For instance, FEA can model the cooling and solidification phases of plastic products, revealing how temperature gradients lead to uneven shrinkage and stress. By adjusting variables within the simulation, manufacturers can test various scenarios to identify optimal conditions that minimize stress.
How Simulation Tools Predict Residual Stress
Simulation tools use mathematical models to represent physical phenomena. In the context of residual stress, these tools consider factors such as:
- Material properties: Understanding the plastic’s thermal expansion coefficient and mechanical properties helps predict how it reacts to temperature changes.
- Processing conditions: Simulations can adjust parameters like injection speed, mold temperature, and cooling rate to observe their impact on stress levels.
- Geometry and design: The shape and complexity of the mold design can influence the flow and cooling patterns, affecting stress distribution.
By inputting these variables into a simulation, engineers can visualize potential stress points and assess different strategies to mitigate them before actual production.
The Benefits of Mitigating Residual Stress with Simulations
Using advanced simulations offers several advantages:
- Cost-effectiveness: By predicting and addressing issues virtually, manufacturers can reduce the need for physical prototypes, saving time and resources.
- Enhanced product quality: Identifying stress points early allows for design modifications that improve durability and performance.
- Process optimization: Simulations help in refining process parameters, leading to more efficient production cycles with reduced risk of defects.
Real-World Application of Simulation Tools
A case study involving a high-stress automotive component illustrates the power of simulation tools. Engineers used CFD simulations to optimize the mold design and processing conditions. The result was a significant reduction in residual stress, improving the part’s mechanical properties and longevity.
Challenges and Future Directions
While simulations offer substantial benefits, they also have limitations. Accurate predictions rely on precise input data and sophisticated models. As technology advances, integrating artificial intelligence with simulation tools could further enhance their predictive capabilities, making them indispensable in modern manufacturing processes6.
Simulation tools reduce need for physical prototypes.True
Simulations predict stress issues virtually, saving time and resources.
Residual stress predictions rely on AI exclusively.False
Predictions currently depend on precise data and mathematical models.
What Are Common Signs of Residual Stress in Finished Products?
Residual stress often manifests in various forms, compromising the integrity and performance of finished plastic products. Identifying these signs early is crucial for quality assurance.
Common signs of residual stress in finished products include warping, cracking, optical distortions, and compromised mechanical properties. These indicators suggest internal stress imbalances resulting from manufacturing processes, especially in plastics.
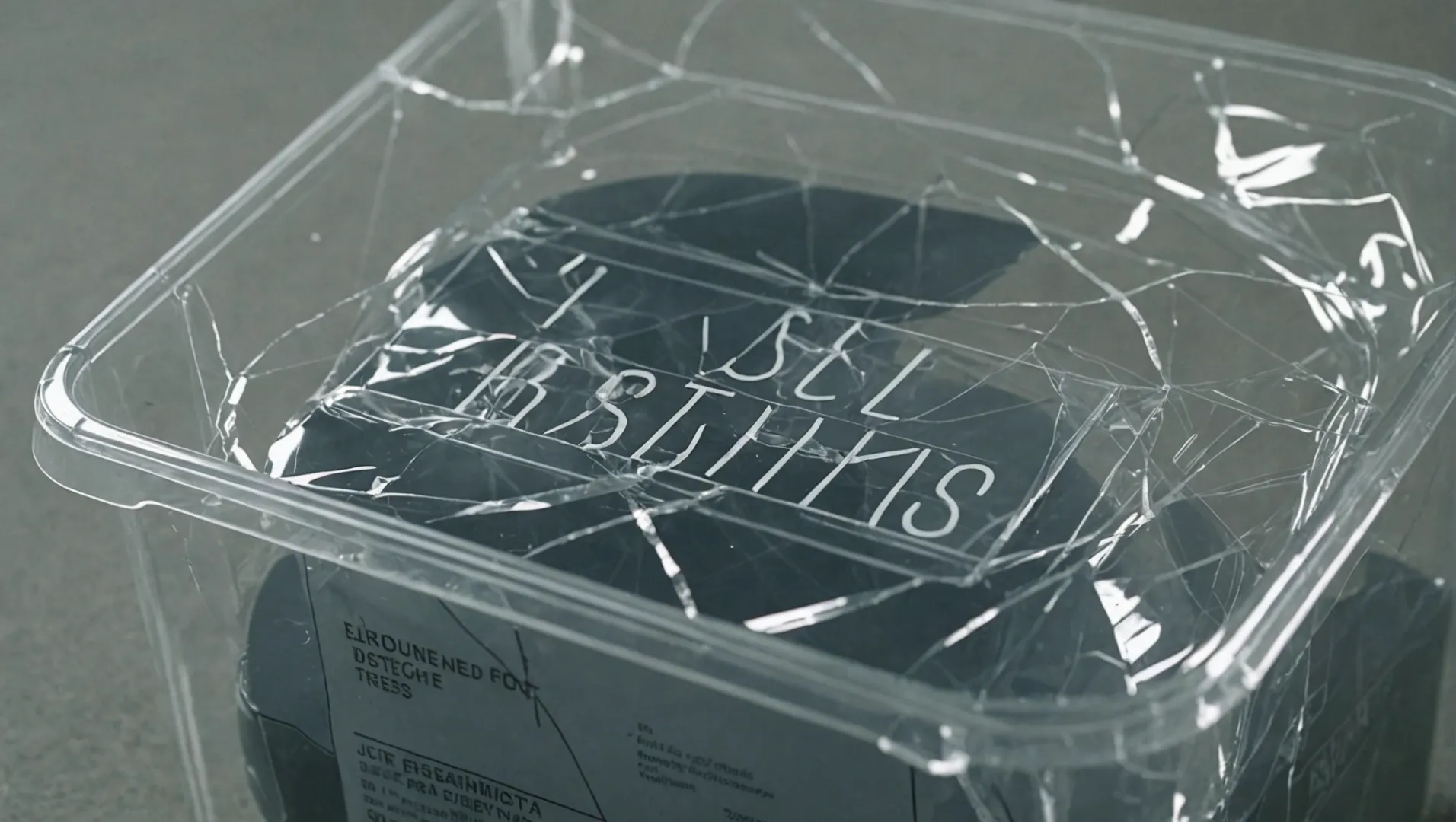
Identifying Warping and Deformation
Warping is a telltale sign of residual stress7 in finished products. It occurs when parts of the plastic product cool and shrink unevenly, leading to dimensional instability. This deformation can affect assembly accuracy and product function, becoming evident soon after demolding or during use.
For instance, a warped plastic component may not fit properly with other parts, causing issues in assembly lines or reducing the aesthetic appeal of consumer goods.
Cracking and Breakage
Another significant indicator is cracking or breakage under stress. Areas with concentrated residual stress are prone to failure when subjected to mechanical loads. During quality checks, look for hairline cracks or fractures along the edges or junctions of the product.
These defects not only compromise structural integrity but also pose safety risks in applications requiring high strength and durability.
Optical Distortions in Transparent Products
In transparent plastics like polycarbonate or acrylic, residual stress can manifest as optical distortions. This includes birefringence or rainbow-like patterns that distort light passing through the material.
Such optical imperfections can degrade the clarity and performance of lenses, screens, and protective covers, impacting their effectiveness in visual applications.
Mechanical Property Deterioration
Residual stress adversely affects mechanical properties such as toughness and fatigue resistance. Products may exhibit reduced performance over time due to stress-induced molecular alignment changes.
Monitoring mechanical properties through tests like tensile strength can reveal underlying stress issues. This is crucial in industries where product reliability and longevity are paramount.
How to Monitor These Signs Effectively
Regular inspections and testing protocols can help identify residual stress manifestations early. Employing tools like polarized light for optical products or conducting stress relaxation tests can pinpoint areas of concern.
Incorporating advanced monitoring techniques into production workflows enhances early detection, allowing for timely interventions to mitigate residual stress effects.
Warping indicates residual stress in plastics.True
Warping results from uneven cooling and shrinking, leading to instability.
Optical distortions are unrelated to residual stress.False
Residual stress causes birefringence, affecting optical clarity in plastics.
Conclusion
By mastering these strategies, we can significantly enhance plastic product quality and performance while reducing residual stress.
-
Learn about how residual stresses develop during molding.: So, what is residual stress? It is defined as the byproduct of the manufacturing process, which is a part of the internal makeup of a part. A corresponding term … ↩
-
Understand the impact of MFI on mold filling efficiency.: High melt flow can cause flashing, leading to increased waste and potential damage to equipment like hot runner molds. Conversely, low melt flow might result in … ↩
-
Explore comprehensive strategies to minimize residual stress.: 4. High mold temperatures usually provide less residual stress. Lower mold temperatures provide more residual stress. ↩
-
Explore detailed insights on how injection molding works.: Injection molding is a method to obtain molded products by injecting plastic materials molten by heat into a mold, and then cooling and solidifying them. ↩
-
Discover how FEA enhances understanding of stress in molding processes.: Finite element analysis is available to assess the amount of metal needed around mold cavities for example, and could seamlessly be coupled … ↩
-
Explore upcoming advancements in simulation technology for better stress prediction.: 2. Artificial Intelligence and Machine Learning · 3. Model-Based Systems Engineering · 4. Additive Manufacturing and Generative Design · 5. ↩
-
Understand warping causes to improve product design and manufacturing.: Material shrinkage during and after manufacturing plays an important role in why injection molded plastic parts warp. ↩