Overheating in the gate area of injection molding can wreak havoc on production quality. As someone who has navigated this challenge, I understand the urgency to find effective solutions that lead to excellence in manufacturing.
To prevent overheating in the gate area of injection molding, focus on optimizing mold design, controlling process parameters, selecting suitable materials, and maintaining equipment regularly. This comprehensive approach minimizes defects and enhances production efficiency.
While these initial strategies provide a solid foundation, diving deeper into each aspect will reveal more nuanced insights and practical tips that are vital for mastering the injection molding process.
Optimizing mold design prevents gate area overheating.True
Proper mold design enhances heat dissipation, reducing overheating risk.
What Role Does Mold Design Play in Preventing Overheating?
Mold design is critical in injection molding, especially for preventing overheating that can compromise product quality and process efficiency.
In injection molding, mold design is pivotal in preventing overheating by optimizing gate size and shape and enhancing the cooling system. Proper design ensures efficient heat dissipation, reducing the risk of defects and ensuring consistent product quality.
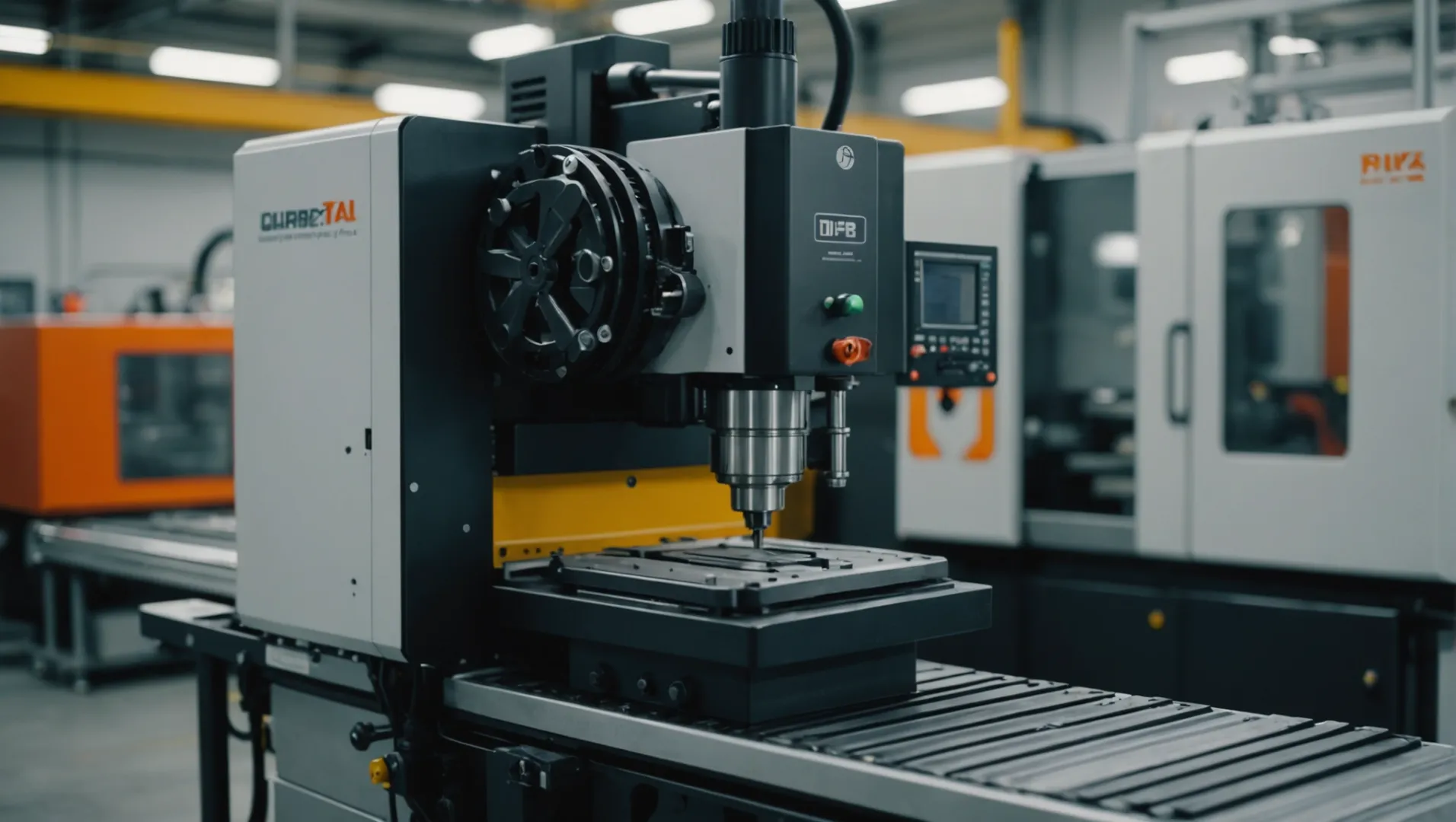
Understanding the Importance of Gate Design
The gate is where the plastic melt enters the mold cavity, making its design crucial for temperature control. Gate Size and Shape play an integral role. An appropriately sized gate1 ensures a balanced flow rate, minimizing residence time and reducing overheating risks. Smaller gates can increase shear forces leading to heat, while larger gates slow flow and extend heat exposure.
Choosing the right gate shape also impacts heat distribution. Options like point gates or side gates each have unique advantages. For instance, a latent gate can stabilize melt flow, reducing overheating by dispersing heat more evenly throughout the cavity.
Optimizing the Cooling System
A well-designed cooling system is essential to manage heat effectively. Positioning the cooling channels strategically close to the gate area enhances heat extraction efficiency. Utilize a mix of cooling media2 such as water or oil, and methods like straight-through or circulating cooling. This not only maintains optimal temperatures but also improves cycle times, resulting in increased productivity.
The Role of Material Selection and Process Parameters
While mold design is foundational, it interacts with material selection and process parameters to minimize overheating. Selecting materials with suitable thermal properties complements mold design, ensuring stability during processing. Additionally, adjusting process parameters like injection pressure and speed can further optimize temperature control.
For a holistic approach, manufacturers should also focus on equipment maintenance3, ensuring that systems function correctly to support mold design efforts. Regular checks prevent anomalies that could negate effective design strategies.
Gate size affects overheating in injection molding.True
Gate size influences melt flow and heat distribution, reducing overheating.
Cooling channels should be far from the gate area.False
Cooling channels close to the gate enhance heat extraction efficiency.
How Can Process Parameters Be Adjusted to Minimize Heat?
Adjusting process parameters is key to minimizing heat during injection molding, ensuring quality and efficiency.
To minimize heat in the injection molding process, adjust the injection pressure, speed, temperature, and holding time. These parameters directly impact the heat generated during molding, and optimizing them is essential for reducing overheating in the gate area.
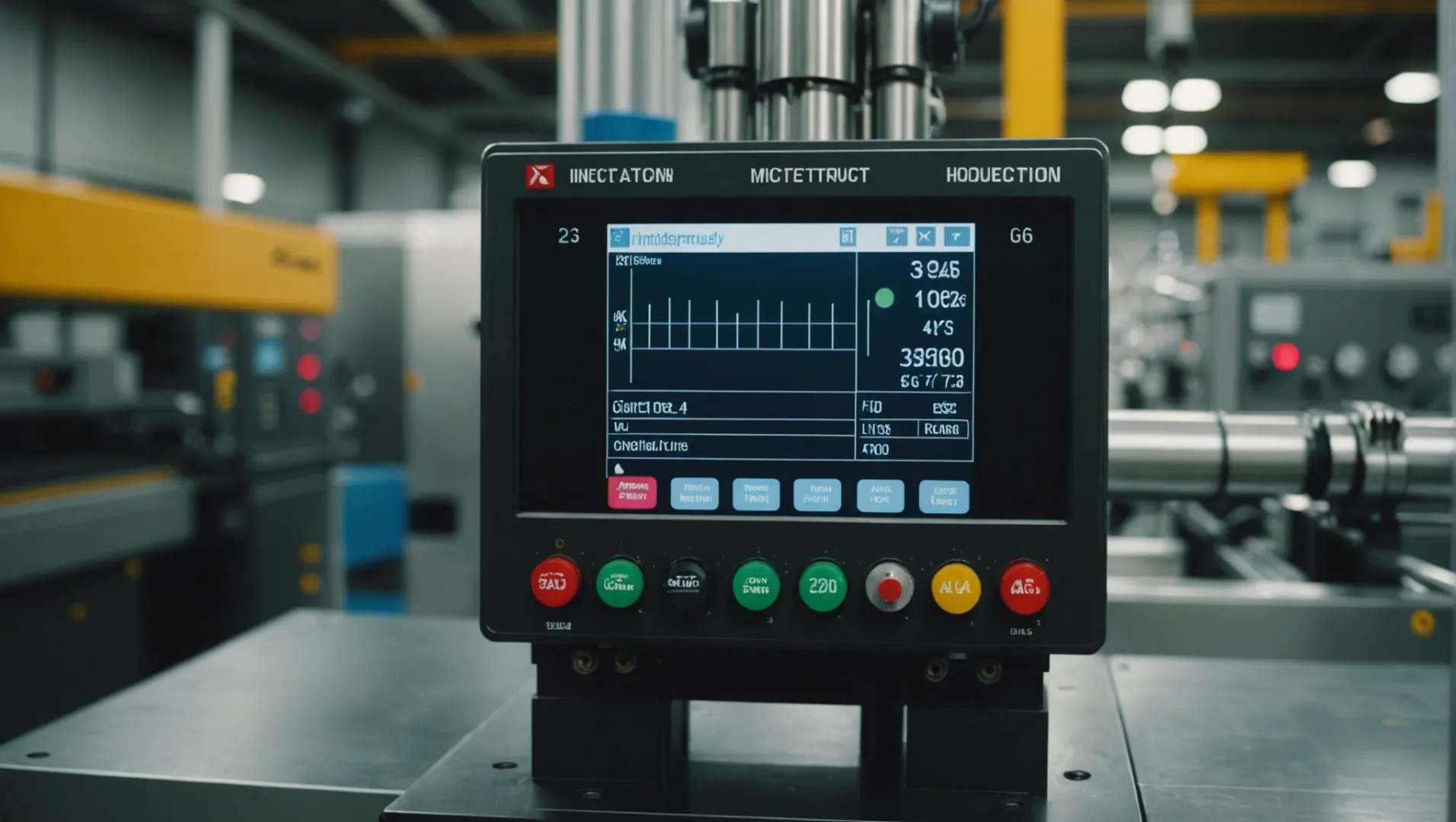
Understanding Injection Pressure and Speed
One of the primary ways to control heat in the injection molding process is by adjusting the injection pressure and speed4. High injection pressure can cause increased shear forces at the gate, which in turn raises the temperature. By carefully reducing the injection pressure and speed, the shear force can be minimized, leading to less heat generation.
Example:
- Reduced Pressure: Lowering the pressure by 10% can decrease temperature by approximately 5°C.
- Slower Speed: Decreasing speed by 15% results in a significant reduction in shear forces.
Controlling Injection Temperature
The temperature of the plastic melt5 is crucial in preventing overheating. It’s essential to maintain the barrel and nozzle temperatures within an optimal range that suits the specific plastic material being used. Different materials have varying thermal properties, so understanding these characteristics is vital.
Example:
- Material-Specific Temperatures: For a thermoplastic like Polypropylene, maintaining a barrel temperature of 230°C is ideal.
Adjusting Holding Time and Pressure
Holding time and pressure play a significant role in how much heat is generated at the gate area. Long holding times and high pressures can exacerbate overheating issues. Therefore, these parameters should be finely tuned based on product requirements and material properties6.
Example:
- Optimized Holding Pressure: Reducing holding pressure by 20% can decrease residual heat substantially.
Parameter | Recommended Adjustment | Impact on Heat |
---|---|---|
Injection Pressure | Reduce by 10-20% | Lowers shear force |
Injection Speed | Decrease by 15% | Minimizes heat |
Holding Time | Optimize as needed | Reduces heat build-up |
Barrel Temperature | Material-specific | Controls melt temp |
Implementing these strategies will not only help reduce heat but also improve overall product quality and production efficiency.
Reducing injection pressure by 10% lowers temperature by 5°C.True
Lowering injection pressure reduces shear forces, decreasing heat.
Increasing holding time decreases heat in the gate area.False
Longer holding times increase residual heat at the gate.
Why Is Material Selection Crucial for Controlling Temperature?
Choosing the right materials can make or break the efficiency and quality of injection molding processes. Discover why material selection is key to temperature management.
Material selection is crucial for controlling temperature in injection molding as different materials have unique thermal properties. Using materials with good thermal stability and suitable fluidity minimizes overheating risks, enhancing product quality and process efficiency.
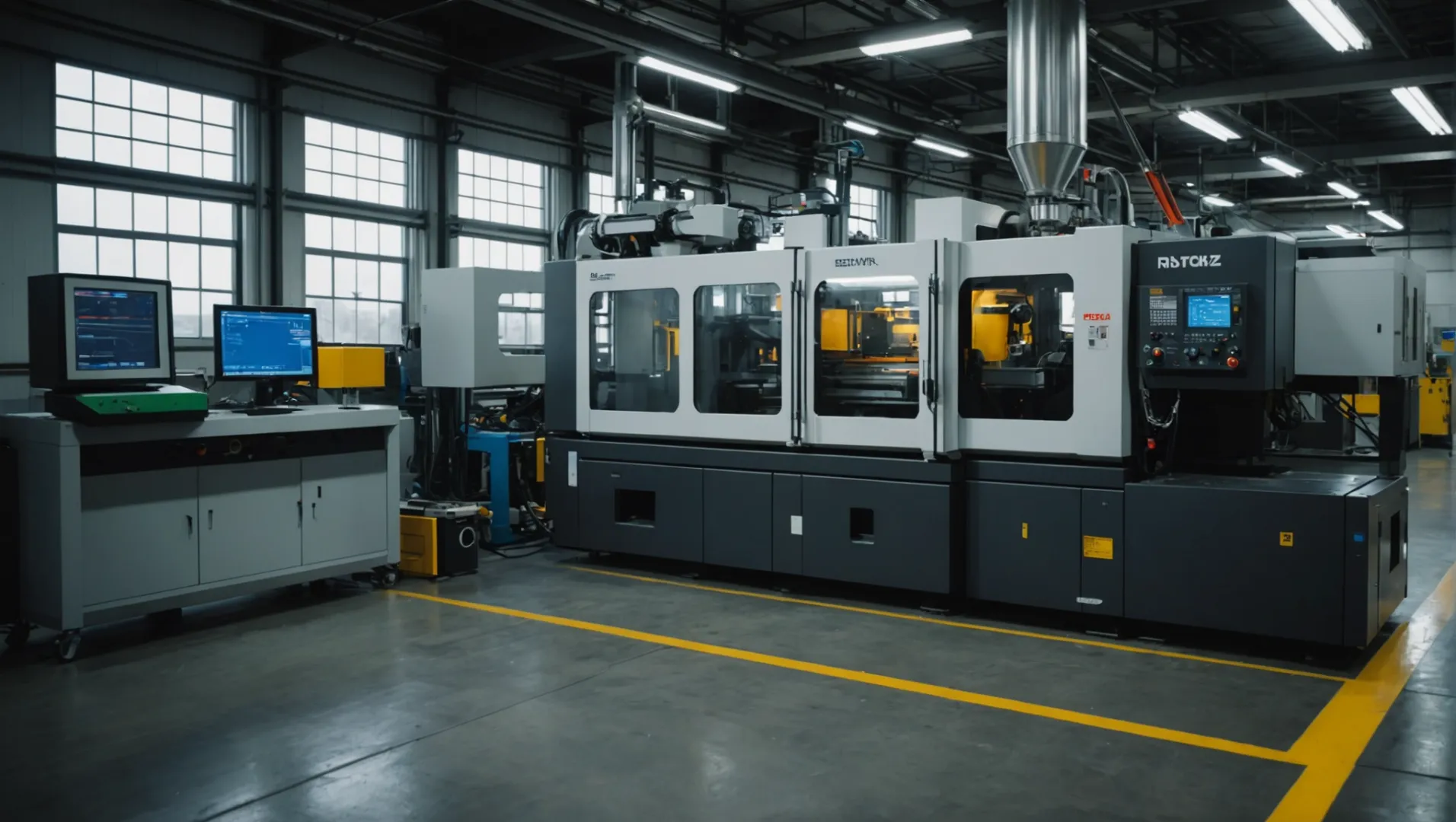
Understanding Thermal Properties
In the context of injection molding7, the thermal properties of materials significantly impact the heat distribution during production. Some plastics, like polycarbonate and polypropylene, have higher heat resistance and are less prone to overheating. By understanding these properties, manufacturers can choose materials that inherently reduce the risk of overheating in critical areas such as gates.
Selecting Plastics with Optimal Fluidity
Fluidity plays a pivotal role in how materials flow and distribute heat. Plastics with moderate fluidity ensure smooth flow, minimizing friction and reducing temperature spikes. This prevents hotspots in the gate area, which can lead to defects. For instance, materials like ABS offer a balance between fluidity and strength, making them ideal for precision parts where temperature control is paramount.
Role of Additives
Incorporating additives like coolants or lubricants can enhance a material’s performance by lowering its viscosity. This adjustment decreases shear forces during the molding process, thus preventing unnecessary heat buildup. However, it’s crucial to maintain an optimal additive balance to avoid compromising the final product’s quality.
Additive Type | Effect on Material | Caution |
---|---|---|
Coolant | Lowers viscosity | Overuse may weaken product integrity |
Lubricant | Reduces shear force | Excess may cause surface defects |
Collaborating with Suppliers
Manufacturers should actively engage with material suppliers to access technical information about different plastic materials. This collaboration ensures informed decisions are made based on accurate data regarding thermal stability and fluidity. Suppliers can provide valuable insights into how specific materials perform under various conditions, allowing for better material selection.
By aligning material selection with these strategic considerations, manufacturers can effectively manage temperature, leading to enhanced production efficiency8 and quality outcomes.
Polycarbonate has high heat resistance in molding.True
Polycarbonate is known for its high thermal stability, reducing overheating risks.
Excess lubricant always improves molding quality.False
Too much lubricant can cause surface defects, compromising product quality.
What Maintenance Practices Help Avoid Overheating Issues?
Proper maintenance is key to avoiding overheating issues in injection molding, particularly in the gate area. By focusing on equipment upkeep, manufacturers can prevent costly downtime and defects.
To avoid overheating issues, regularly maintain injection molding equipment, check systems for optimal functionality, and ensure cleanliness to promote efficient heat dissipation.
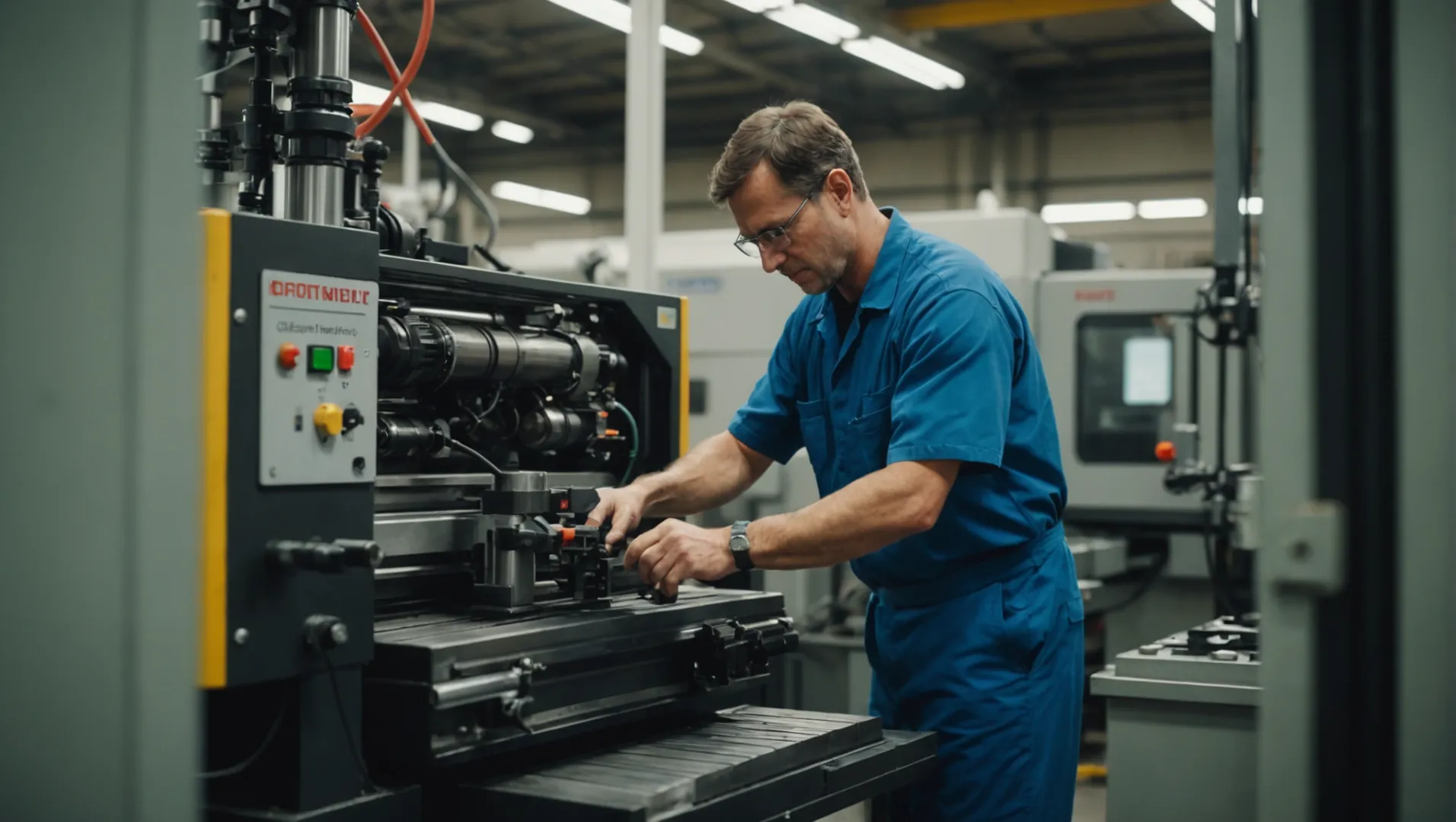
Importance of Regular Equipment Checks
Maintaining an injection molding machine requires consistent checks of several key systems to ensure they function optimally. A regular inspection schedule9 can help detect and rectify potential problems before they escalate into significant issues.
- Heating System: Ensure the heating elements are functioning correctly to avoid overheating. Any irregularities should be addressed immediately.
- Cooling System: The cooling channels must be free from blockages to allow efficient heat removal from the gate area. This system plays a critical role in preventing temperature spikes.
- Hydraulic System: Proper lubrication and hydraulic fluid levels are essential for maintaining pressure and reducing heat generation during operation.
Cleaning and Maintenance of Molds
Clean molds facilitate better heat dissipation and prevent overheating. It’s important to clean molds regularly using appropriate cleaning agents and tools.
- Surface Cleanliness: Dirt and residues can act as insulators, trapping heat. Using specialized cleaning solutions helps maintain mold surface integrity without causing damage.
- Residual Removal: Residual plastic from previous runs can obstruct the gate area, leading to overheating. A thorough cleaning regimen ensures that these residues do not impede heat flow.
Scheduled Preventative Maintenance
Implementing a preventative maintenance program10 is vital for preventing overheating issues. This approach involves:
- Routine Inspections: These should be scheduled at regular intervals based on the machine’s usage intensity. This helps in timely identification of potential failures.
- Component Replacement: Worn-out parts, especially those affecting temperature control, should be replaced promptly to maintain efficiency.
Keeping the Environment Optimal
The surrounding environment can significantly impact the machine’s performance. Ensure that:
- Ambient Temperature Control: The room where injection molding occurs should be climate-controlled to aid in consistent temperature regulation.
- Ventilation Systems: Proper ventilation helps dissipate excess heat generated during operations, reducing the risk of overheating.
By integrating these maintenance practices, manufacturers can significantly reduce the risk of overheating in the gate area, thus ensuring smoother production processes and better product quality.
Regular equipment checks prevent overheating.True
Regular checks detect issues early, preventing overheating and costly downtime.
Ignoring mold cleanliness doesn't affect heat dissipation.False
Dirty molds trap heat, hindering dissipation and increasing overheating risk.
Conclusion
By taking a strategic approach to design, processes, materials, and maintenance, manufacturers can significantly reduce overheating risks and enhance product quality.
-
Discover how gate size influences temperature control in molding.: A good starting point is to make the last runner diameter 1.5 times the wall thickness of the part where it is gated into. This may seem like an … ↩
-
Explore cooling media options to optimize mold performance.: Standard cooling channel design is best suited for parts with relatively simple geometries to help ensure the entire part is cooled effectively … ↩
-
Learn why maintenance supports effective mold design.: Injection molding tool maintenance includes cleaning and repairing components to maintain a functioning injection mold. An injection mold’s condition influences … ↩
-
Explore how pressure impacts heat generation and strategies for optimization.: Temperature affects the fluidity of the molten material, while pressure affects its flow rate and packing. ↩
-
Find guidelines for setting optimal temperatures for various materials.: The table below demonstrates the optimal melt and mould temperature ranges of various plastic materials, to ensure product quality and manufacturing efficiency. ↩
-
Learn techniques for optimizing holding parameters to reduce heat.: Classic Steps for Setting Holding Time: · Set the melt temperature to the mid-range of the manufacturer’s recommended values. · Set the filling … ↩
-
Explores why thermal properties are critical in injection molding.: The heat capacity and thermal conductivity have important implications during heat transfer in injection moulding. Conduction out of the melt and shear heating … ↩
-
Learn how choosing the right materials boosts production efficiency.: The cost of materials significantly influences the overall cost efficiency of the manufacturing process. Materials that are readily available … ↩
-
Learn how regular checks prevent costly machine failures.: Your inspections should regularly check the mold for any condensation, as well as the nearby parts for any signs of deformity caused due to … ↩
-
Discover how proactive maintenance improves efficiency and reduces downtime.: In summary, maintenance of injection molds is critical for maintaining product quality, reducing costs, minimizing downtime, ensuring safety, … ↩