Jet marks can be an unwelcome surprise in the world of injection molding—like a sudden rain on a picnic day!
To prevent jet marks on injection molded parts, focus on optimizing mold design, adjusting molding process conditions, and selecting appropriate materials. These strategies ensure smoother plastic flow, reducing shear stress and improving overall part quality.
While these initial techniques lay the groundwork for improvement, the real magic lies in diving deeper into each strategy to refine your injection molding process further.
Adjusting mold design can reduce jet marks.True
Optimizing gate placement and size ensures smoother plastic flow, reducing defects.
How Does Mold Design Influence Jet Marks?
Mold design is crucial in preventing jet marks, which compromise injection molded parts.
Mold design significantly influences jet marks by ensuring smooth plastic flow, minimizing shear stress, and optimizing gate placement and size.
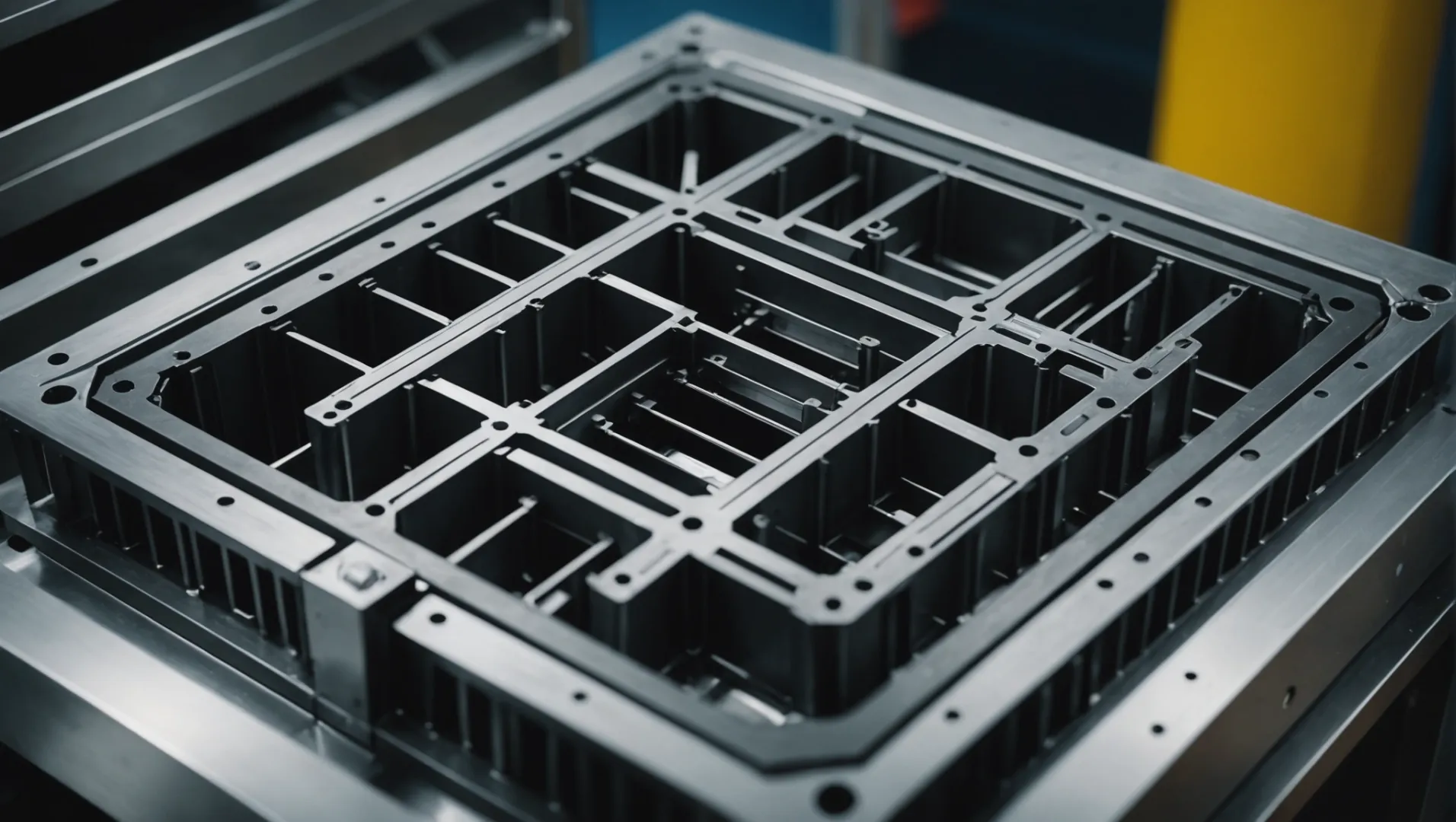
Understanding the Impact of Mold Design
Jet marks are caused by uneven flow and sudden changes in pressure as molten plastic enters the mold cavity. A well-thought-out mold design addresses these issues, reducing or eliminating jet marks. By focusing on key design elements, manufacturers can ensure the production of high-quality parts.
Key Elements of Mold Design
1. Gate Design:
- Utilize overlapping gates, ear gates, or fan gates to allow for a smoother transition of molten plastic into the mold cavity. This reduces shear stress and minimizes jet marks.
- Adjust gate positions to prevent plastic from hitting wide areas directly, thus reducing abrupt changes in flow.
2. Gate and Runner Size:
- Increase the size of gates and runners to lower the flow rate and pressure of plastic entering the cavity.
- Shortening gate length can also contribute to reducing shear stress, aiding in minimizing jet marks.
Element | Suggested Design Change |
---|---|
Gate Design | Use overlapping, ear, or fan gates |
Gate Position | Prevent direct flow to wide areas |
Gate and Runner Size | Increase size, shorten gate length |
3. Mold Exhaust System:
- Proper venting is essential to ensure gases are expelled smoothly. An optimized exhaust system prevents pressure build-up that can lead to defects such as jet marks.
Practical Application
Implementing these mold design strategies requires collaboration between designers and engineers to tailor solutions specific to the material and product requirements. Regular testing and adjustments are vital to adapt to different materials and achieve desired outcomes.
For further insights into how effective mold design can transform your manufacturing process, explore related resources such as optimizing mold design strategies1 or advanced techniques in injection molding2.
Gate design can minimize jet marks.True
Proper gate design reduces shear stress, minimizing jet marks.
Smaller gates increase plastic flow rate.False
Larger gates reduce flow rate, minimizing pressure and defects.
What Role Does Material Selection Play in Preventing Jet Marks?
Choosing the right material is crucial in minimizing jet marks during injection molding, influencing both flow and finish.
Material selection impacts jet mark prevention by affecting plastic flow and fluidity. Opt for materials with good fluidity or add lubricants to minimize these defects.
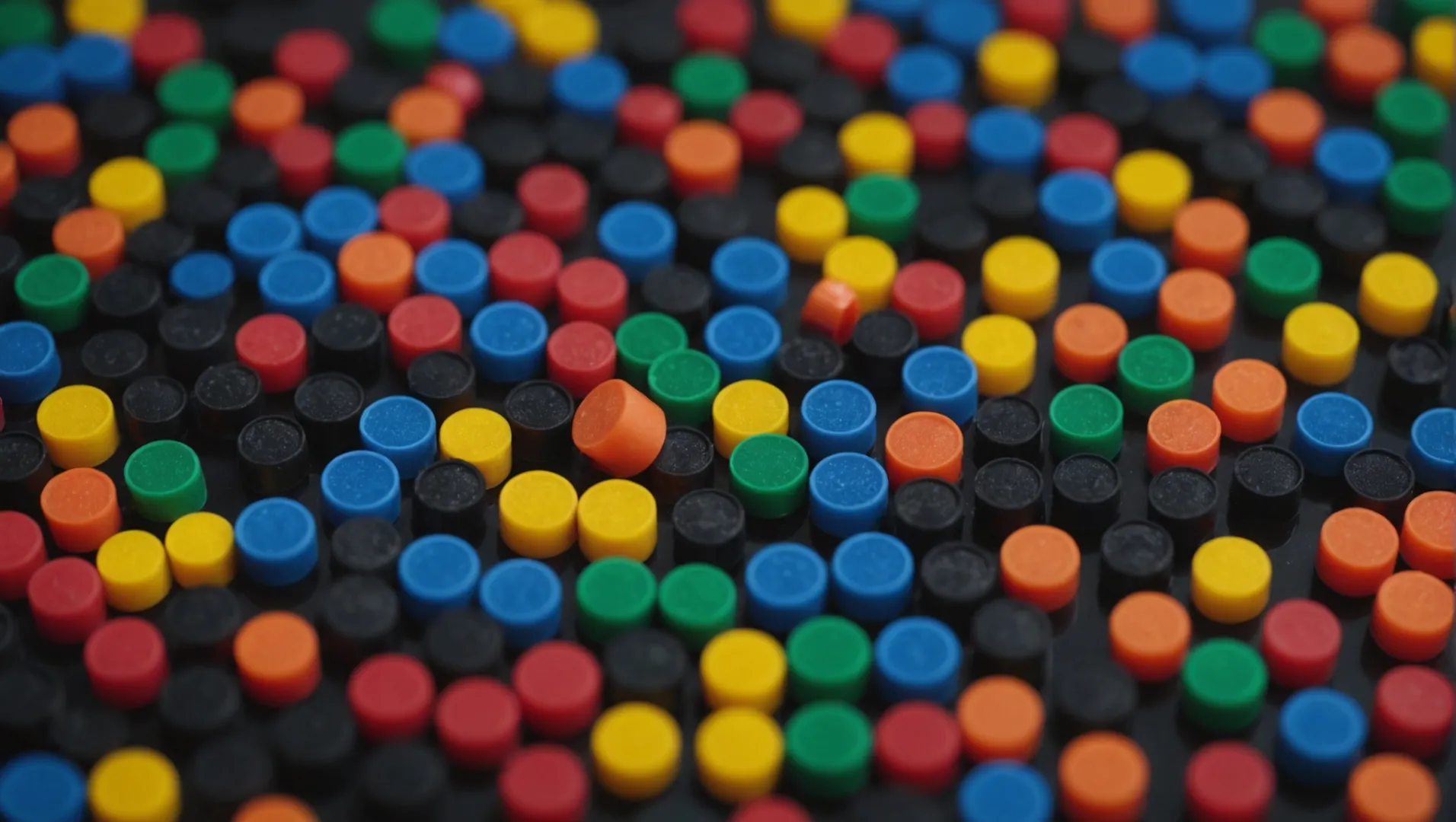
Importance of Material Fluidity
In the world of injection molding, the choice of material plays a pivotal role in ensuring the quality of the final product. Materials with good fluidity can significantly reduce the appearance of jet marks. This is because they flow more smoothly through the mold, decreasing shear stress and avoiding abrupt changes in velocity that often lead to defects.
For example, materials like polypropylene (PP) and polyethylene (PE) are known for their excellent fluidity. These materials not only fill the mold cavities more evenly but also require less pressure to inject, thereby reducing the potential for jet marks.
Lubricants: A Useful Addition
Adding lubricants to the material can further enhance its flow properties. Lubricants work by reducing the friction between the plastic molecules, allowing them to move more freely and fill the mold more uniformly. This is particularly beneficial when working with materials that inherently have lower fluidity.
Commonly used lubricants include fatty acids, esters, and metal stearates. By incorporating these additives, manufacturers can improve not only the surface finish of their products but also enhance the ease of processing.
Comparative Table: Material Properties and Their Impact on Jet Marks
Material Type | Fluidity | Jet Mark Resistance | Typical Applications |
---|---|---|---|
Polypropylene | High | Excellent | Consumer goods, automotive |
Polyethylene | High | Excellent | Packaging, containers |
Polystyrene | Moderate | Good | Toys, household appliances |
ABS | Low | Fair | Electronics, automotive |
Selecting the Right Material for Your Needs
The decision on material selection should not only consider the fluidity and resistance to jet marks but also other factors such as mechanical strength, heat resistance, and cost-effectiveness. For instance, while ABS may have lower fluidity compared to PP or PE, it offers superior impact resistance and aesthetic qualities, making it suitable for certain high-demand applications.
When selecting a material, it’s crucial to balance these attributes to ensure that the final product meets both functional and visual requirements. Consulting with material suppliers or using specialized software can aid in making an informed decision tailored to your specific application needs.
By understanding material properties3 and their implications on the molding process, manufacturers can better tailor their choices to reduce defects such as jet marks.
Polypropylene has excellent fluidity for molding.True
Polypropylene is known for its high fluidity, aiding in smooth mold filling.
ABS offers high fluidity in injection molding.False
ABS has lower fluidity compared to materials like PP or PE.
How Can Adjusting Process Conditions Reduce Jet Marks?
Adjusting process conditions is key to minimizing jet marks, ensuring superior quality in molded parts.
To reduce jet marks, adjust filling speed, mold and melt temperatures, injection speed, and holding time. These tweaks enhance plastic flow and minimize defects.
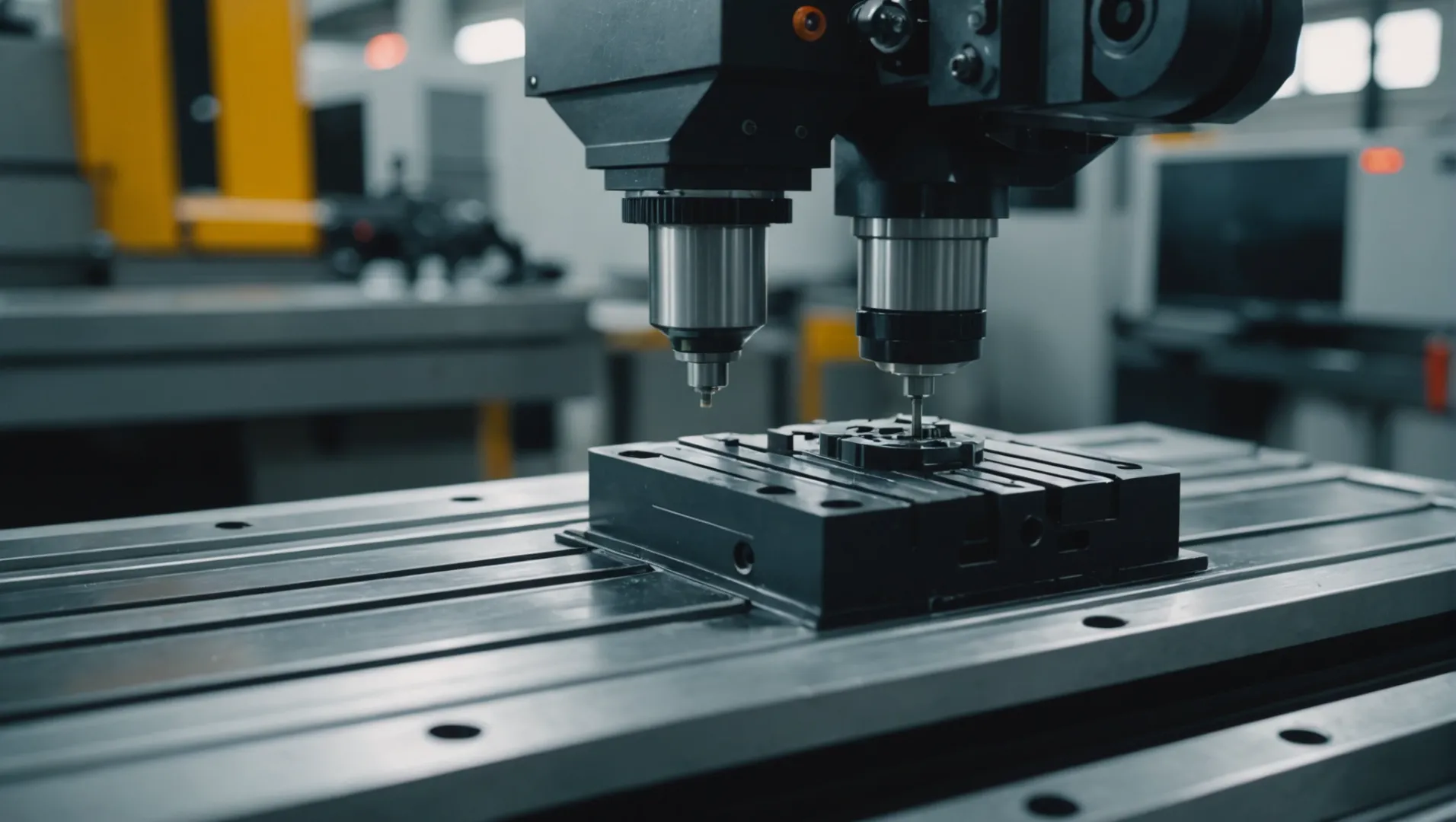
Optimizing Filling Speed
Adjusting the filling speed curve is crucial to preventing jet marks. By allowing the front end of the molten plastic to pass through the gate at a lower speed, you can minimize turbulence and shear stress. Once the plastic enters the cavity, increase the shooting speed to ensure proper filling without the formation of jet marks.
Controlling Temperature Settings
-
Mold Temperature: Increasing the mold temperature can help improve surface finish and reduce cooling disparities that contribute to jet marks. A warmer mold allows for better plastic flow, leading to smoother finishes.
-
Melt Temperature: Raising the melt temperature reduces viscosity, enhancing the fluidity of the plastic. This adjustment is particularly effective when combined with optimized filling speed.
Adjusting Injection Speed
Reducing the injection speed prevents the molten plastic from traveling too quickly through gates and runners, which can otherwise lead to jet marks due to high shear rates. This control allows for a more uniform flow into the mold cavity.
Enhancing Holding Time
Increasing holding time after injection ensures that the molten plastic completely fills the mold cavity and compensates for any shrinkage during cooling. This results in fewer imperfections and a reduction in jet marks.
Implementing Process Control Strategies
Maintaining a consistent production environment is vital. Regular monitoring and adjustments based on real-time data can significantly improve outcomes. Consider implementing a closed-loop control system4 to automate these adjustments, thus ensuring optimal conditions are maintained consistently.
Each of these adjustments not only minimizes jet marks but also contributes to an overall improvement in part quality and production efficiency. Explore specific process optimization techniques5 that align with your production needs for enhanced results.
Increasing mold temperature reduces jet marks.True
A warmer mold improves plastic flow, reducing cooling disparities.
Reducing injection speed increases jet marks.False
Lower injection speed reduces shear rates, minimizing jet marks.
Why Is Regular Maintenance Important for Mold Longevity and Quality?
Regular maintenance of molds is crucial for ensuring their longevity and the quality of the molded parts produced.
Regular maintenance of molds prevents wear and tear, reduces downtime, and ensures consistent product quality. By maintaining optimal mold conditions, manufacturers can extend mold life, prevent defects like injection marks, and improve efficiency, leading to better end products and reduced costs.
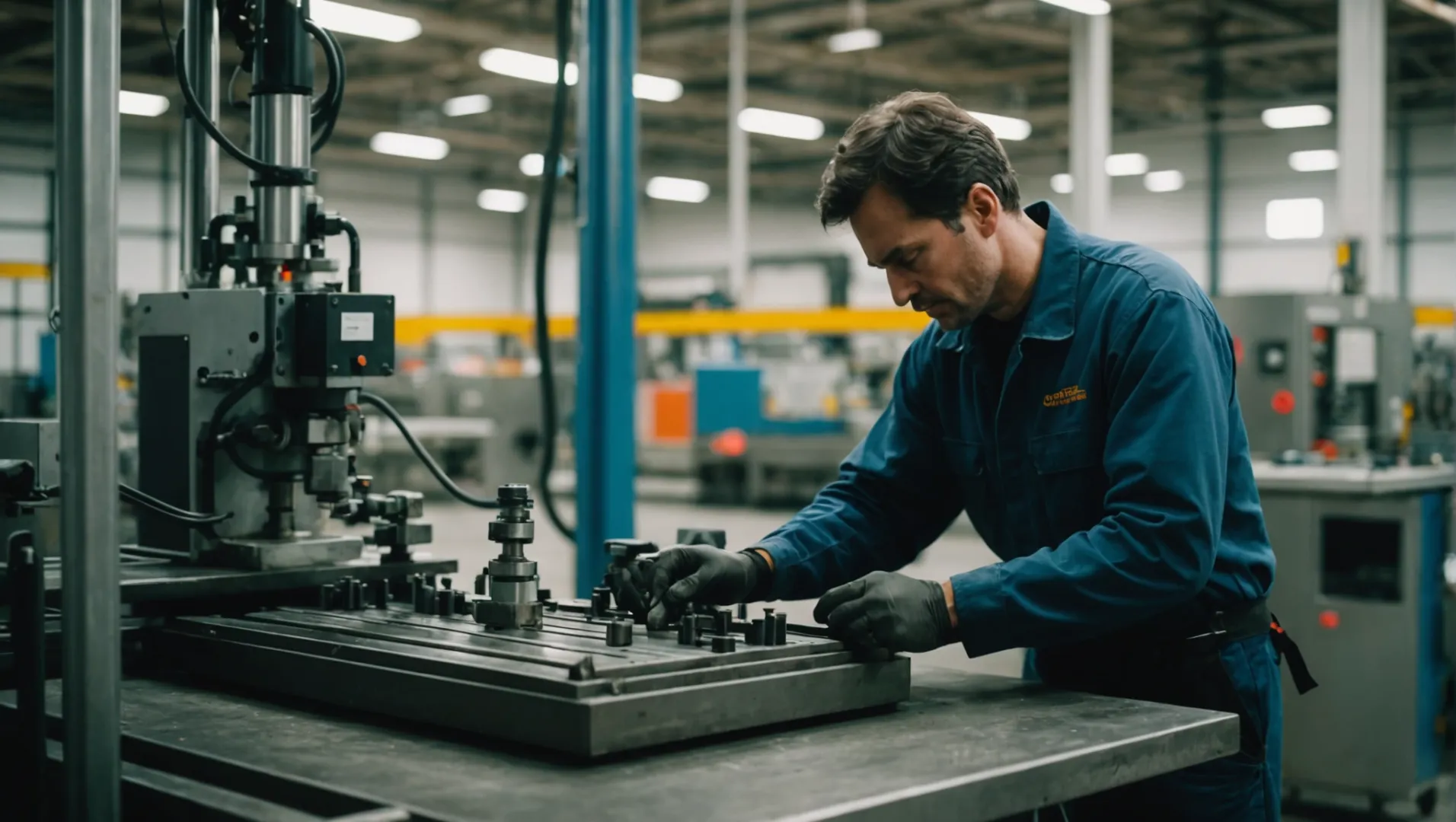
Understanding Mold Maintenance
Regular maintenance of molds6 involves several critical activities like cleaning, inspection, and timely repairs. These processes help in identifying and addressing issues before they escalate into significant problems that affect the production quality or result in costly downtimes.
Benefits of Mold Longevity
-
Cost Efficiency: By extending the lifespan of molds, companies can significantly reduce replacement costs. This efficiency is not only financial but also operational, as less frequent mold changes mean fewer interruptions in production.
-
Consistent Quality: A well-maintained mold ensures that every part produced meets quality standards. This consistency reduces the chances of defects such as jet marks or other surface imperfections that might occur due to worn or damaged molds.
-
Reduced Downtime: Scheduled maintenance minimizes unexpected breakdowns. Unplanned downtimes can severely impact production schedules and lead to delays in delivering products to the market.
Maintenance Activity | Benefits |
---|---|
Regular Cleaning | Removes residues that cause defects |
Inspection & Repairs | Detects wear early, prevents failure |
Lubrication | Ensures smooth operation |
Calibration | Maintains precision in part creation |
How Maintenance Impacts Quality
Regular maintenance directly impacts the quality of the molded parts. By keeping the mold surfaces clean and free from residues, manufacturers can avoid many common defects. Additionally, regular inspections allow for the early detection of issues such as small cracks or other wear-related damages that could lead to quality problems if left unchecked.
Expert Insights: Techniques to Enhance Maintenance
-
Documentation: Keeping detailed records of maintenance activities helps in tracking mold performance over time and in making informed decisions about when major refurbishments or replacements might be necessary.
-
Training: Providing staff with the right training on maintenance procedures ensures that tasks are carried out efficiently and effectively, further safeguarding mold longevity.
-
Use of Technology: Implementing advanced monitoring systems can provide real-time data on mold conditions, enabling predictive maintenance and reducing the risk of unexpected failures.
By integrating these practices, manufacturers can ensure that their molds operate efficiently and produce high-quality parts consistently. This approach not only enhances productivity but also fosters a reputation for reliability and excellence in the competitive manufacturing landscape.
Regular maintenance prevents mold defects.True
Maintenance removes residues and detects issues early, preventing defects.
Ignoring mold maintenance reduces production costs.False
Neglecting maintenance leads to defects and downtime, increasing costs.
Conclusion
Implementing these strategies will help you effectively reduce jet marks, enhancing product quality. Reflect on your current processes and consider adopting these best practices for optimal results.
-
Discover advanced mold design strategies to minimize defects effectively.: The injection molding process can be broken into three steps: 1. Product Design Determining product objectives such as function, aesthetics, assembly, etc. ↩
-
Learn about cutting-edge techniques for superior injection molding results.: A review of current advancements in high surface quality injection molding: Measurement, influencing factors, prediction, and control. ↩
-
Explore how different material properties affect injection molding outcomes.: Other Material Properties. Properties other than thermal and mechanical can be important in specific applications. These include electrical properties such … ↩
-
Learn how automation improves consistency in injection molding processes.: Software closed loop is to directly detect system pressure through pressure sensor installed in motion actuator (cylinder, etc.), monitor system … ↩
-
Discover advanced methods to refine injection molding processes.: 1. Temperature Control: · 2. Injection Speed: · 3. Cooling Time: · 4. Plastic Material Selection: · 5. Screw Speed and Back Pressure: · 6. Injection … ↩
-
Explores detailed benefits of regular mold maintenance in manufacturing processes.: You need to carry out preventive maintenance daily, monthly, or weekly. It ensures the smooth operation of molds. It comprises mold cleaning, inspection, and … ↩