Injection molding is a fascinating process, a true marvel of modern manufacturing. However, it does come with its fair share of challenges. One of the most frustrating issues I’ve encountered is edge fracture in molded products—something that can really compromise quality.
To prevent product edge fractures in injection molding, adjust injection parameters, optimize mold design, choose suitable materials, and maintain equipment. Key strategies include reducing injection speed, increasing mold temperature, and ensuring material quality.
But let’s not stop here! Exploring the specifics of each strategy can truly transform your production process. Join me as we delve into effective practices that can help you avoid common pitfalls.
Reducing injection speed prevents edge fractures.True
Lowering injection speed reduces impact force on edges, minimizing stress.
What Are the Common Causes of Edge Fractures in Injection Molding?
Edge fractures in injection molding can be a persistent problem, impacting the integrity and functionality of products. Understanding their causes is key to prevention.
Edge fractures in injection molding often result from improper process parameters, suboptimal mold design, material inadequacies, and poor maintenance. Addressing these areas is crucial for quality improvement.
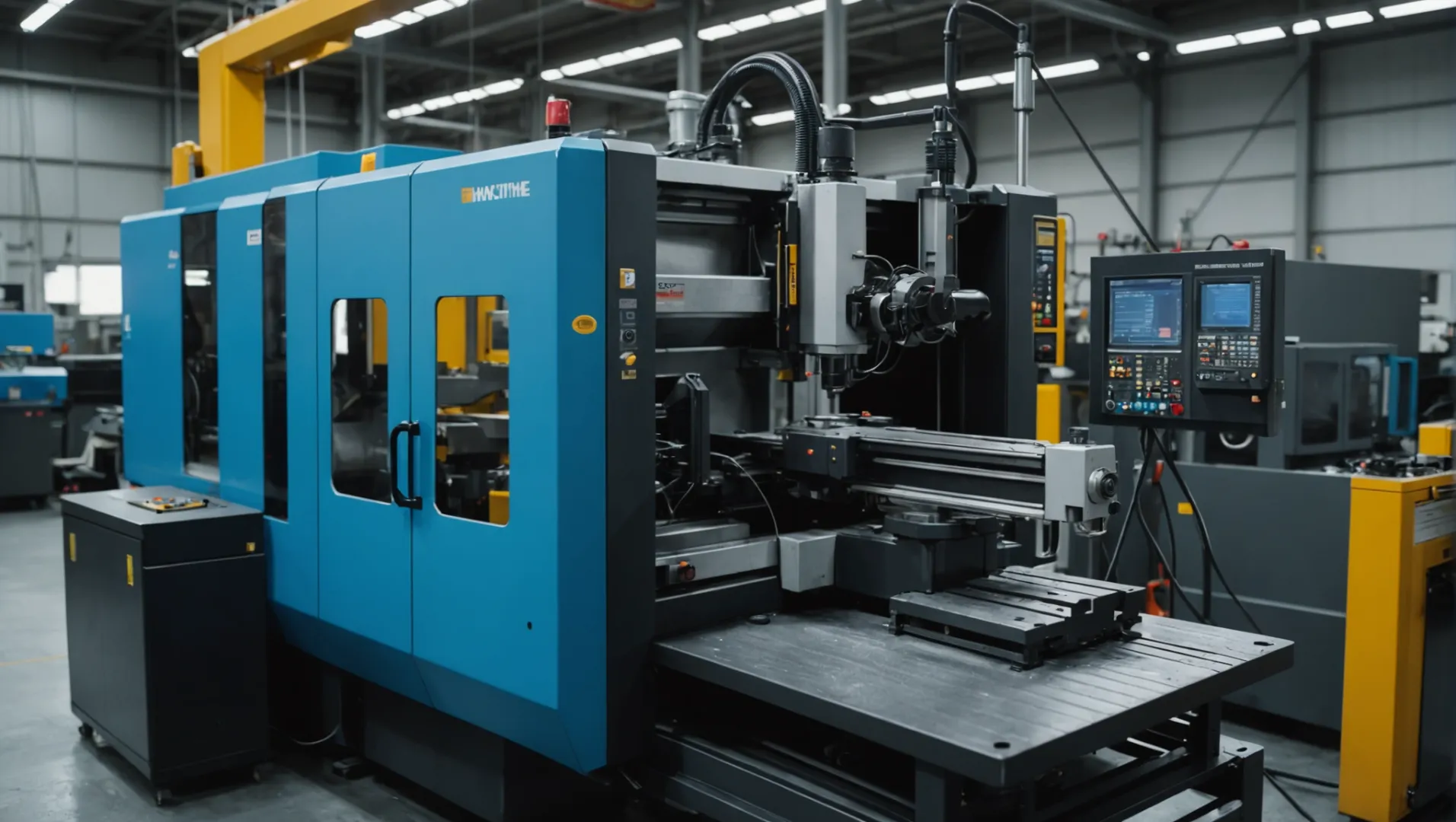
Process Parameters
In injection molding, the control of process parameters is vital. Injection speed and holding pressure are two critical factors:
-
Injection Speed: Excessive speed can lead to a high impact force on the edges, causing fractures. Adjusting the injection speed1 allows the melt to fill the mold more smoothly, minimizing stress.
-
Holding Pressure: Overpressure during the holding phase can increase the risk of edge fractures. Properly reducing it prevents over-extrusion during cooling.
Additionally, extending the cooling time ensures full stabilization of the product within the mold, reducing deformation risks.
Mold Design
The design of the mold plays a pivotal role in preventing edge fractures:
-
Gate Location and Number: Placing gates in thicker sections or increasing their number for larger products helps distribute melt evenly and reduces localized stress.
-
Mold Structure: Incorporating larger fillet radii at edges and corners lowers stress concentration. An optimized demoulding mechanism prevents damage during product removal.
Material Selection
Selecting the right material is essential for durability:
-
Material Toughness: Choosing materials with higher toughness and strength, such as those reinforced with fibers, can significantly reduce edge fracture occurrences.
-
Material Quality: Ensuring that materials are dry and free from impurities prevents stress and defects during the molding process.
Equipment Maintenance
Regular maintenance of both machinery and molds is crucial:
-
Injection Molding Machine: Regular checks and maintenance of components like screws, barrels, and nozzles ensure consistent performance.
-
Mold Maintenance: Regular cleaning and wear checks can prevent defects arising from equipment failure.
Strengthening employee training2 ensures operators are skilled in adjusting parameters and addressing common issues, further preventing edge fractures.
Excessive injection speed causes edge fractures.True
High injection speed increases impact force, leading to fractures.
Ignoring mold maintenance has no effect on edge fractures.False
Neglecting maintenance can cause defects, increasing fracture risk.
How Does Mold Design Influence Edge Fracture Prevention?
The design of the mold in injection molding is pivotal in preventing edge fractures, a frequent defect that undermines product integrity.
Mold design significantly impacts edge fracture prevention by optimizing gate location, increasing fillet radii, and ensuring uniform mold temperature. These adjustments reduce stress concentration and enhance product durability.
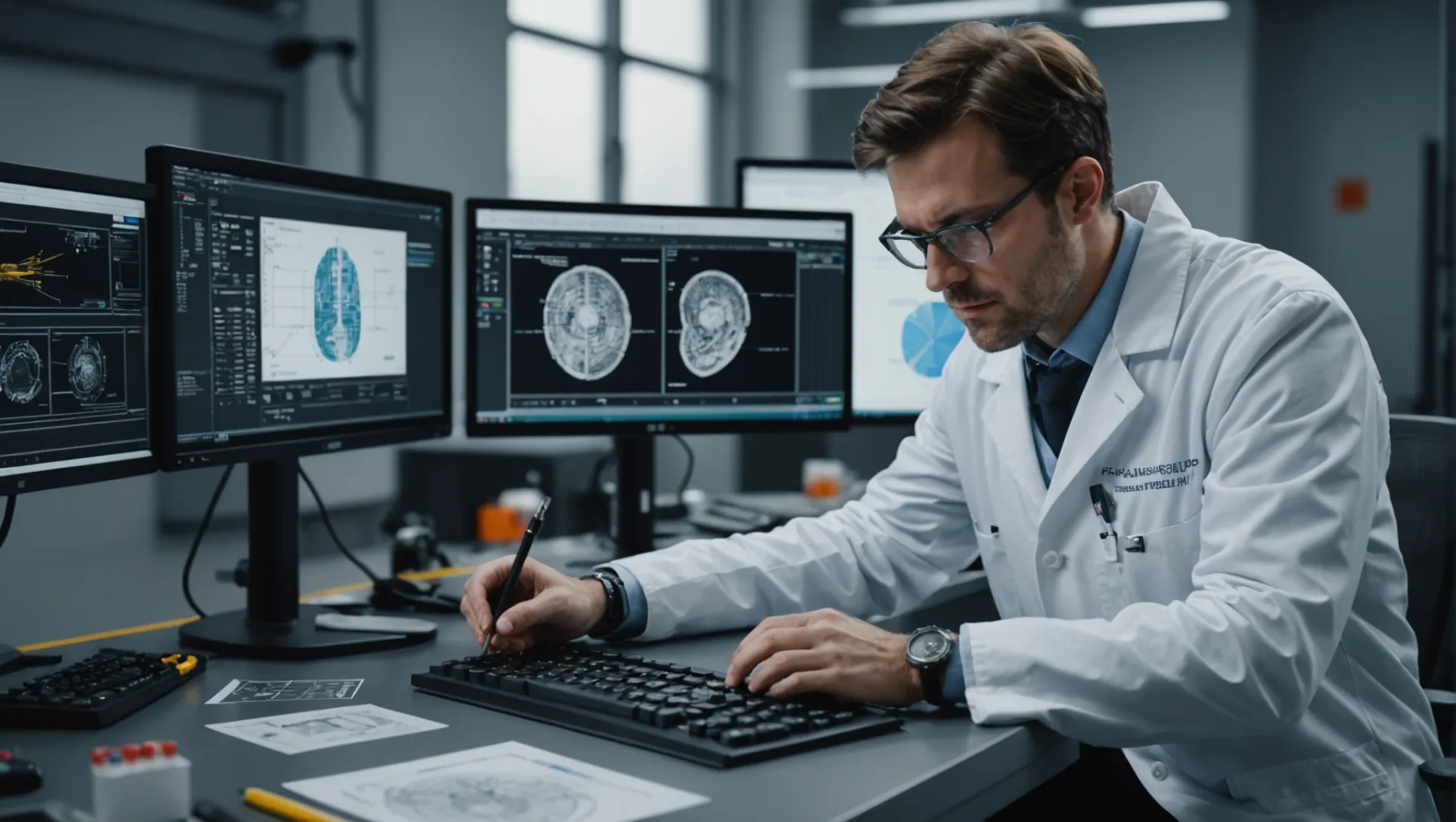
Optimizing Gate Locations and Numbers
The strategic placement and number of gates are crucial in distributing the molten material evenly across the mold. By setting gates in thicker product sections or away from vulnerable edges, the impact force on these edges during filling is minimized. Increasing the number of gates can also ensure a more uniform fill, reducing localized stress. For instance, in large or complex designs, multiple gates can help balance the flow and prevent fractures.
Enhancing Mold Structure
One effective way to mitigate stress concentrations at edges and corners is by increasing the fillet radius. Sharp corners are stress concentrators and can be prone to fractures. A larger fillet radius distributes the stress more evenly, enhancing overall product strength. Furthermore, an optimized demoulding mechanism3 is essential. Properly designed demoulding slopes and methods prevent damage during release, maintaining edge integrity.
Ensuring Uniform Mold Temperature
Maintaining a consistent mold temperature across all areas helps avoid uneven shrinkage, a common cause of stress concentration leading to edge fractures. This can be achieved by refining the mold cooling system to ensure even temperature distribution. For materials that are particularly hard or brittle, a slight increase in mold temperature can improve melt fluidity, thus reducing stress.
Case Study: Implementing Mold Design Strategies
Consider a manufacturer facing recurrent edge fractures in their plastic housings. By reassessing their mold design, they moved the gate away from thinner sections and incorporated a larger fillet radius in critical areas. Additionally, they adjusted the cooling channels to maintain uniform mold temperatures. The result was a significant decrease in defects, showcasing how targeted mold design4 strategies can effectively prevent edge fractures.
Optimizing gate location reduces edge fractures.True
Strategically placed gates distribute molten material evenly, minimizing stress.
Increasing fillet radii increases stress concentration.False
Larger fillet radii distribute stress more evenly, reducing concentration.
What Role Does Material Selection Play in Reducing Edge Fractures?
Material selection is crucial in minimizing edge fractures during injection molding, impacting product quality significantly.
Selecting materials with high toughness and appropriate fluidity reduces stress and prevents edge fractures in injection molding. Consider modified plastics and reinforcing fibers to enhance material properties.
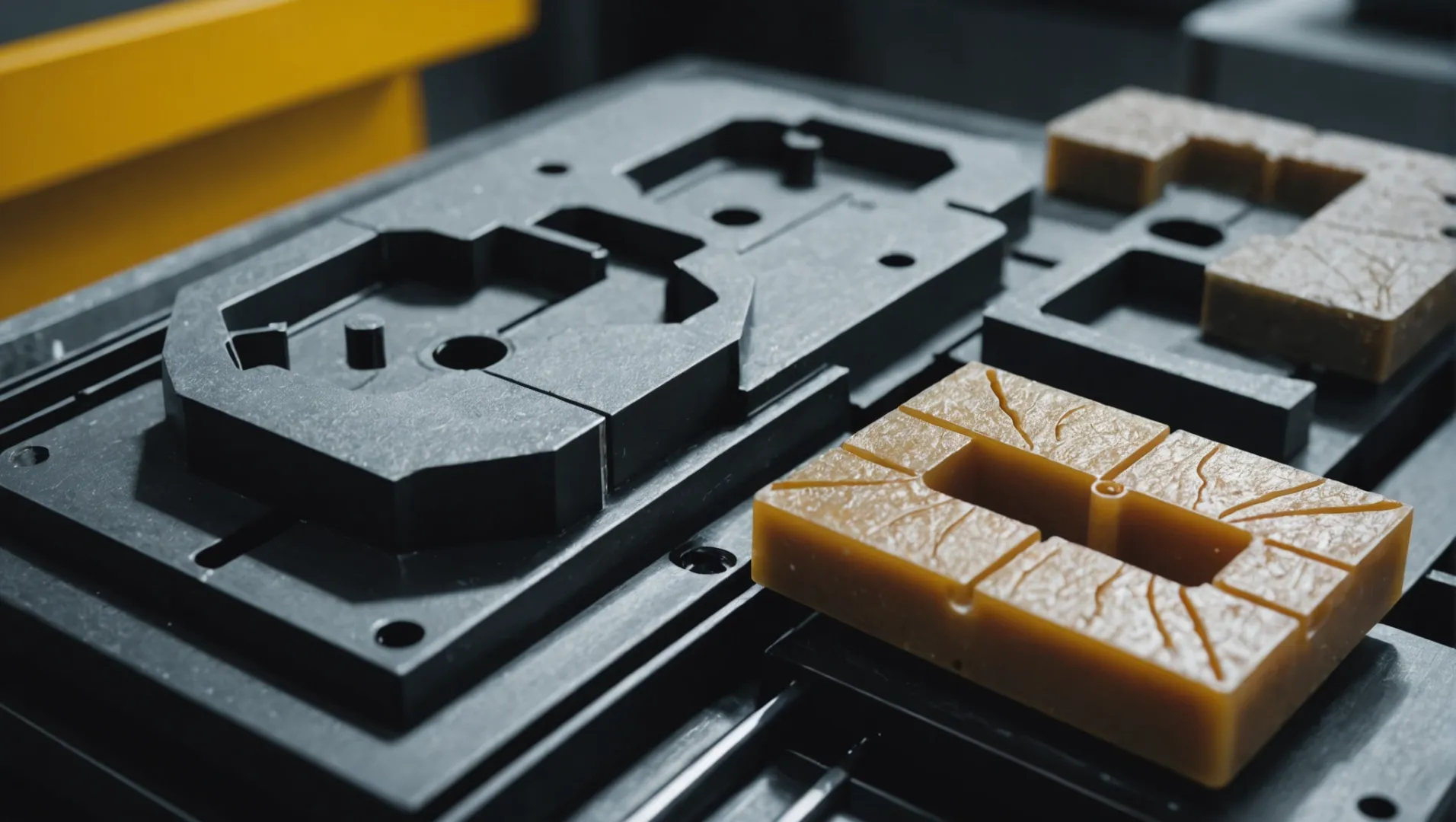
Importance of Material Toughness
When selecting materials for injection molding, one of the primary considerations should be their toughness. Materials with higher toughness can absorb impact better and are less likely to fracture under stress. For instance, using modified plastics5 or those with added reinforcing fibers can dramatically reduce the incidence of edge fractures by distributing stress more evenly across the product.
Materials such as polycarbonate or certain grades of polypropylene are often preferred for applications that require higher impact resistance. These materials can withstand the mechanical stress exerted during the injection molding process, making them ideal for products prone to edge fractures.
The Role of Material Fluidity
Fluidity is another critical factor in material selection. Materials with good fluidity can fill molds more uniformly, reducing the likelihood of stress concentrations that lead to fractures. Ensuring adequate material flow within the mold minimizes sharp edges and thin sections that are prone to breaking.
To improve fluidity, manufacturers may choose materials that have been modified with plasticizers or other additives. This allows the melt to fill intricate molds smoothly, decreasing the risk of defects.
Controlling Material Quality
Beyond choosing the right material, controlling its quality is equally important. Moisture content and impurities can significantly affect the performance of materials during injection molding. Moisture can lead to bubbles forming within the melt, increasing internal stress and fracture risk. Thus, ensuring materials are thoroughly dried before use is crucial.
Additionally, screening for impurities helps prevent defects that could weaken the product structure. Using materials from reputable suppliers who adhere to strict quality control measures is a proactive approach to maintaining consistent product quality.
Practical Application: A Case Study
Consider a manufacturer producing automotive components using injection molding. Initially, they faced frequent edge fractures due to the use of a brittle polymer. By switching to a high-toughness material reinforced with glass fibers, they observed a marked reduction in defects. This change, coupled with optimized injection parameters6, led to improved product durability and reduced waste.
By focusing on the strategic selection of materials, manufacturers can not only reduce edge fractures but also enhance overall production efficiency and product longevity.
High-toughness materials prevent edge fractures.True
Materials with high toughness absorb impact better, reducing fracture risk.
Fluidity is irrelevant in injection molding.False
Good fluidity ensures uniform mold filling, reducing stress and fractures.
How Can Regular Maintenance Prevent Edge Fractures in Injection Molding?
Regular maintenance of injection molding equipment is crucial to prevent edge fractures and ensure consistent product quality. Learn how routine checks and upkeep can mitigate defects.
Regular maintenance prevents edge fractures by ensuring equipment operates smoothly, avoiding stress and defects. Key actions include cleaning, lubrication, and part inspections.

Importance of Equipment Maintenance
Ensuring the injection molding machine is in optimal condition is fundamental to preventing edge fractures. Regular maintenance helps identify issues such as wear and tear that could contribute to defects. For instance, worn screws or nozzles can lead to uneven pressure during molding, increasing the risk of fractures at the product’s edges.
Routine Maintenance Checklist
- Cleaning: Regular cleaning of molds and machine parts prevents residue build-up that can affect the material flow, leading to stress concentration at product edges.
- Lubrication: Proper lubrication of moving parts reduces friction and wear, ensuring smooth operation and preventing potential points of failure.
- Inspection of Wear and Tear: Consistent inspection allows for timely identification of worn components. Replace these parts before they lead to operational inefficiencies or defects.
Maintenance Activity | Frequency | Benefits |
---|---|---|
Cleaning | Weekly | Reduces residue build-up |
Lubrication | Bi-weekly | Minimizes friction and wear |
Inspection | Monthly | Identifies wear before failure |
Mold Maintenance
Proper mold care is equally essential. Molds must be cleaned and checked for wear regularly. A damaged mold can create uneven pressure distribution during the injection process, leading to localized stress at the edges.
- Mold Cleaning: Regularly clean molds to avoid residue that can affect the quality and integrity of the molded product.
- Wear Inspection: Inspect mold surfaces for signs of wear or damage that could lead to uneven pressure application.
- Lubrication: Ensure mold parts are properly lubricated to avoid unnecessary friction and damage during the molding process.
Training and Awareness
Equally important is the role of trained personnel in maintaining equipment. Operators should be well-versed in equipment handling and maintenance procedures to preemptively address potential issues. Training programs should focus on:
- Understanding the impact of equipment conditions on product quality.
- Learning how to adjust parameters to compensate for any minor discrepancies identified during routine checks.
By implementing a comprehensive maintenance strategy, you not only extend the lifespan of your equipment but also consistently produce high-quality products with minimal defects. Such proactive measures are crucial in an industry where precision and reliability are paramount.
Regular cleaning reduces edge fractures in injection molding.True
Cleaning prevents residue build-up, reducing stress at product edges.
Skipping lubrication has no effect on injection molding quality.False
Lack of lubrication increases friction, causing wear and potential defects.
Conclusion
By adopting these strategies, I can significantly reduce edge fractures in my injection molding process, leading to better product quality and efficiency.
-
Learn to fine-tune injection speed to reduce edge fractures.: First Step: Start by setting V1, V2, and V3 at the same speed, then gradually increase the injection speed by 5% increments from about 5%, … ↩
-
Understand why skilled operators are key to quality control.: Continued training helps moldmakers make tooling decisions and properly use the latest cutting tool to efficiently machine high-quality molds. ↩
-
Explore various demoulding techniques that protect product edges.: Explore key factors in mold design for efficient demolding mechanisms in injection molding, including part geometry, material properties, and production … ↩
-
Discover how specific design changes can decrease stress risks.: Fillets reduce stress concentration at corners or changes of sections because they transmit applied stresses across larger surface areas. ↩
-
Explore how modified plastics enhance toughness and reduce fracture risks.: Injection molding can handle highly complex parts, provides uniformity, and offers the ability to make millions of virtually identical parts. ↩
-
Learn techniques for refining injection parameters to prevent fractures.: 1. Temperature Control: · 2. Injection Speed: · 3. Cooling Time: · 4. Plastic Material Selection: · 5. Screw Speed and Back Pressure: · 6. Injection … ↩